본 소개 자료는 "Mälardalen University Press Licentiate Theses"에서 발행된 "OPTIMIZATION PRODUCT PARTS IN HIGH PRESSURE DIE CASTING PROCESS" 논문을 기반으로 합니다.
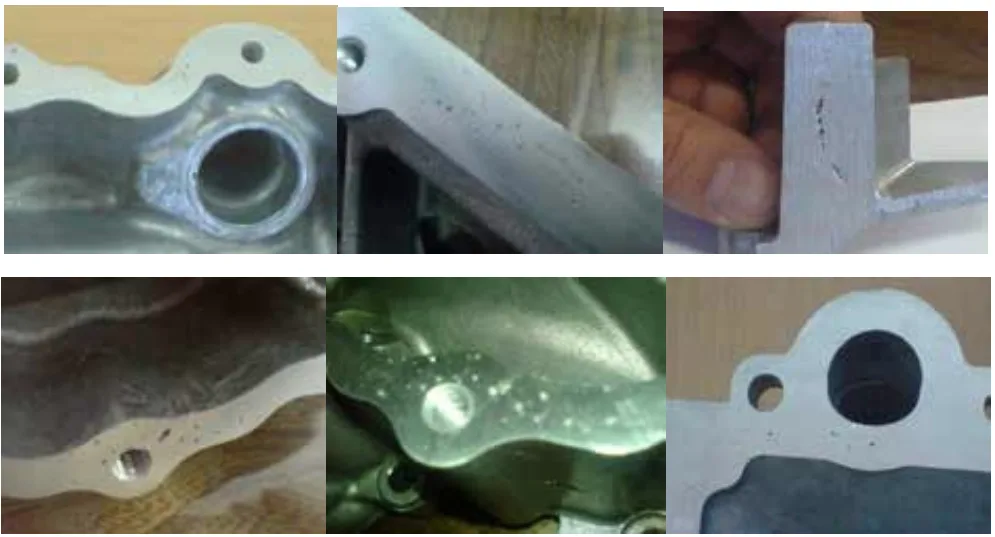
1. 개요:
- 제목: 고압 다이캐스팅 공정에서의 제품 부품 최적화 (OPTIMIZATION PRODUCT PARTS IN HIGH PRESSURE DIE CASTING PROCESS)
- 저자: Mohammad Sadeghi
- 발행 연도: 2015
- 발행 학술지/학회: Mälardalen University Press Licentiate Theses, No. 197
- 키워드: 고압 다이캐스팅 (HPDC), 금형 온도 최적화, A380 알루미늄 합금, 수치 시뮬레이션, 실험적 관찰, 결함 최소화
2. 초록:
본 학위 논문은 통계적 도구를 사용하여 A380 합금의 고압 다이캐스팅(HPDC)에서 실험적 관찰 및 수치 시뮬레이션을 통해 금형 온도를 최적화하는 방법을 기술합니다. 본 연구의 목표는 이러한 결함 발생을 최소화하고 결함 없는 부품 생산을 극대화하기 위한 최적의 금형 온도를 결정하는 것입니다.
HPDC 공정에서는 용탕이 고속(알루미늄 합금의 경우 40-60 m/s)으로 금형에 사출됩니다. 금형 온도는 불량 부품 발생률에 중요한 역할을 합니다. 따라서 매우 복잡한 형상(EF7 모터의 래더 프레임)을 가진 자동차 부품의 HPDC에서 용탕의 유동 패턴을 검토하여 최적의 금형 온도를 결정하였습니다.
생산 공정에서의 결함은 표면 결함, 내부 결함 및 치수 결함의 세 가지 범주로 나뉩니다. 실험에서 생산된 샘플은 존재하는 결함에 따라 분류되었습니다.
주조 결함에 영향을 미치는 또 다른 중요한 파라미터는 냉각 속도입니다. 금형 온도는 초기 단계와 최종 충전 위치에서 측정되었습니다. 실험은 150°C에서 250°C 범위의 금형 온도로 수행되었습니다. 그 결과, 초기 단계와 최종 충전 위치 사이의 금형 내 용탕 온도 차이는 20~25°C였습니다.
회귀 분석, 관계, 최대값, 최소값, 상관 관계, ANOVA, T-검정, 주성분 분석(PCA) 및 기술 통계와 같은 통계적 도구를 사용하여 다이캐스팅 실험 데이터를 쉽게 해석할 수 있도록 하였습니다.
공정 거동을 연구하고, 영향 파라미터에 대한 더 나은 지식을 얻고, 필요한 파라미터를 측정하기 위해 몇 가지 사례 연구를 수행합니다. 수집된 데이터는 다음을 위해 활용됩니다:
- 모델 설정
- 모델 검증/확인
ProCast 소프트웨어를 사용하여 유체 유동 및 응고 단계를 시뮬레이션했으며, 그 결과는 실험적 측정을 통해 검증되었습니다. 이 합금에 대한 최적의 금형 온도는 200°C 이상인 것으로 밝혀졌습니다.
실험 결과의 통계적 분석에 따르면, 래더 프레임의 HPDC에서 210°C에서 215°C 범위의 금형 온도에서 결함이 최소화되고 양품 부품이 극대화되는 것으로 나타났습니다.
3. 서론:
고압 다이캐스팅(HPDC) 공정은 알루미늄, 마그네슘, 구리 및 아연 부품 생산에 널리 사용되는 제조 방법으로, 정확한 금형 일치성, 우수한 기계적 특성, 저렴한 비용 및 복잡한 형상 부품 생산 능력과 같은 장점을 제공합니다. 이 공정은 자동차 및 항공 우주 산업을 포함한 다양한 산업에 필수적입니다. 그러나 HPDC 부품의 품질은 용탕 온도, 사출 압력, 금형 온도, 부품 복잡성 및 사출 속도 등 수많은 파라미터의 영향을 받습니다. 본 연구는 생산된 부품의 결함에 대한 금형 온도의 영향 조사에 중점을 둡니다. 부품의 복잡성이 증가하고 최적화의 필요성이 대두됨에 따라, 수치 해석 방법은 생산 공정과 관련된 물리적 문제를 해결하는 데 필수적인 도구가 되고 있으며, 전통적인 시행착오 방식에 비해 시간과 비용을 크게 절감할 수 있습니다. 본 학위 논문은 특히 다이캐스팅 알루미늄 합금과 자동차 산업에서의 응용을 다루며, 주조 형상, 생산 파라미터 및 다이캐스팅 공정 구성 요소 간의 관계를 이해하고 최적화하여 폐기물을 줄이고 결함을 최소화하는 것을 목표로 합니다.
4. 연구 요약:
연구 주제의 배경:
고압 다이캐스팅(HPDC)은 A380 알루미늄과 같은 합금을 사용하여 복잡한 금속 부품, 특히 자동차 분야에서 중요한 제조 공정입니다. 이 공정은 용융된 금속을 고속 및 고압으로 금형에 사출하는 것을 포함합니다. HPDC는 정밀형상에 가까운 생산 및 우수한 기계적 특성과 같은 장점을 제공하지만, 최종 부품 품질은 공정 파라미터에 매우 민감합니다. 최적이 아닌 조건에서는 결함이 발생하여 비용 증가 및 폐기물 발생으로 이어질 수 있습니다. 이러한 파라미터, 특히 금형 온도를 최적화하는 것은 건전한 주물을 보장하는 데 중요합니다. 이러한 파라미터들의 복잡한 상호 작용을 이해하고 최적화하기 위해 수치 시뮬레이션 도구가 점점 더 많이 사용되고 있습니다.
선행 연구 현황:
본 연구는 HPDC 공정 물리학, 응고 이론 및 결함 형성 메커니즘에 관한 기존 지식 체계를 기반으로 합니다. 핵 생성 이론(예: 고전적 Gibbs 모델, 비고전적 모델) 및 응고 미세조직 발달에 대한 확립된 이론이 연구의 과학적 토대를 형성합니다. 주조 공정에서 유체 유동, 열 전달 및 응고를 시뮬레이션하기 위한 ProCast와 같은 계산 도구의 사용은 잘 개발된 분야입니다. 본 연구는 이러한 확립된 원리 및 도구를 적용하여 새로 설계된 복잡한 자동차 부품(EF7 엔진용 래더 프레임)의 금형 온도를 최적화하여 결함을 최소화하는 특정 과제를 해결합니다.
연구 목적:
본 연구의 주요 목표는 A380 알루미늄 합금의 고압 다이캐스팅(HPDC)에서 결함 발생을 최소화하고 이를 통해 양품 부품 생산을 극대화하기 위한 최적의 금형 온도를 결정하는 것입니다. 구체적인 목표는 다음과 같습니다:
- 생산 공정에 영향을 미치는 파라미터와 다이캐스팅 방법의 설계 파라미터를 이해합니다.
- 다이캐스팅 설계 구성 요소, 탕도 및 오버플로우 위치, 부품의 기하학적 복잡성 간의 관계를 결정합니다.
- 설계 파라미터와 제조 파라미터 간의 관계를 조사하고 결함 및 불량 부품 수를 줄이기 위해 최적화합니다.
핵심 연구:
본 연구의 핵심은 HPDC 공정으로 생산되는 A380 알루미늄 합금 자동차 부품(EF7 모터의 래더 프레임)에 대한 금형 온도 최적화에 대한 포괄적인 조사입니다. 이는 실험적 관찰과 수치 시뮬레이션의 조합을 통해 달성되었습니다. 금형 온도(150°C ~ 250°C)와 용탕 온도를 체계적으로 변경하면서 결함 형성을 모니터링하는 실험이 수행되었습니다. 복잡한 형상 때문에 선택된 래더 프레임이 시험 부품으로 사용되었습니다. ProCast 소프트웨어를 사용한 수치 시뮬레이션을 통해 유체 유동 및 응고 단계를 모델링했으며, 그 결과는 실험적 측정을 통해 검증되었습니다. 회귀 분석, ANOVA 및 PCA를 포함한 통계적 도구를 사용하여 실험 데이터를 분석하고 최적의 공정 조건을 식별했습니다.
5. 연구 방법론
연구 설계:
본 연구는 실험과 수치 시뮬레이션을 결합한 접근 방식을 사용했습니다. 실험은 산업용 HPDC 장비(IDRA1600)에서 A380 알루미늄 합금을 사용하여 복잡한 자동차 부품인 EF7 모터의 "래더 프레임"을 생산하는 방식으로 수행되었습니다. 주요 조사 변수는 150°C에서 250°C 범위의 금형 온도였으며, 용탕 온도도 모니터링되고 제어되었습니다. ProCast 소프트웨어를 사용하여 다양한 조건에서 금형 충전 및 응고 과정을 모델링하는 수치 시뮬레이션이 수행되었습니다. 그런 다음 시뮬레이션 결과는 정확성과 신뢰성을 보장하기 위해 실험적 측정을 통해 검증되었습니다.
데이터 수집 및 분석 방법:
데이터 수집에는 초기 단계와 최종 충전 위치에서의 금형 온도 측정, 그리고 다이 입구(사출 시작)와 다이 끝(사출 종료)에서의 용탕 온도 측정이 포함되었습니다. 각 조건에 대해 3회 반복 실행하여 신뢰성을 확보했으며, 총 800회의 실험이 수행되었습니다. 결함 부품을 식별하고 X-선 검사, 3차원 측정기(CMM), 금속 조직 검사 및 육안 검사를 포함한 다양한 분석 기법을 사용하여 결함 유형(표면, 내부, 치수)을 결정했습니다.
데이터 분석은 회귀 분석, 관계, 최대값, 최소값, 상관 관계, ANOVA, T-검정, 주성분 분석(PCA) 및 기술 통계와 같은 일련의 통계적 도구를 사용하여 수행되었습니다. ProCast 소프트웨어는 유체 유동 및 응고 시뮬레이션에 사용되어 온도 분포, 충전 패턴 및 잠재적 결함 위치에 대한 통찰력을 제공했습니다.
연구 주제 및 범위:
본 학위 논문의 범위는 고압 다이캐스팅 방법을 사용하여 복잡한 형상과 최소한의 결함을 가진 A380 알루미늄 합금 부품 생산에 중점을 둡니다. 핵심 연구 주제는 주조 결함을 최소화하기 위한 금형 온도의 최적화입니다. 본 연구는 매우 복잡한 형상을 가진 특정 자동차 부품(래더 프레임)의 품질에 대한 금형 온도의 영향을 조사합니다. 연구는 실험 결과를 모델링하고 시뮬레이션 결과를 경험적으로 확인하기 위해 Engineering ProCast 소프트웨어를 사용한 수치 시뮬레이션과 실험 작업을 결합합니다. 또한 탕도 및 오버플로우 위치와 같은 설계 파라미터와 금형 및 용탕 온도와 같은 제조 파라미터 간의 관계도 탐구합니다.
6. 주요 결과:
주요 결과:
본 연구는 복잡한 래더 프레임 부품에 대해 결함을 최소화하고 A380 알루미늄 합금의 HPDC에서 양품 부품 생산을 극대화하기 위한 최적의 금형 온도 범위를 성공적으로 식별했습니다.
- 이 합금에 대한 최적의 금형 온도는 200°C 이상인 것으로 밝혀졌습니다.
- 실험 결과의 통계적 분석에 따르면, 금형 온도가 210°C에서 215°C 범위일 때 결함이 최소화되고 양품 부품이 극대화되었습니다. 따라서 이상적인 금형 온도 범위는 212.5±2.5°C입니다.
- 기술 통계에 따르면, 210°C의 금형 온도가 95% 신뢰 수준에서 가장 높은 양품률(99.45%)을 나타냈습니다.
- 분산 분석(ANOVA) 결과, 210°C의 금형 온도가 가장 큰 분산을 나타내어 양품 및 최소 결함에 대한 유의미한 영향을 보여주었습니다.
- 주성분 분석(PCA)은 210°C의 금형 온도가 부품 품질에 최적이며, 테스트된 온도 중 가장 큰 영향을 미친다는 것을 추가로 확인했습니다.
- 210°C의 금형 온도와 668°C에서 680°C의 주입 온도로 진행된 실험이 금형 품질 측면에서 최적인 것으로 나타났습니다.
- 다양한 금형 온도에서 서로 다른 결함 유형이 우세하게 나타났습니다: 금형 온도가 200°C 미만일 때는 유형 1(표면 결함)이 가장 빈번했고, 금형 온도가 200°C 이상일 때는 유형 2(내부 결함) 및 유형 3(치수 결함)이 더 빈번했습니다.
- ProCast 소프트웨어를 사용한 수치 시뮬레이션은 거시적 및 미시적 결함의 예상 위치와 유동 패턴을 효과적으로 예측했습니다. 금형 내부의 세 개의 구멍을 제거하는 것과 같은 수정은 유동 패턴을 개선하는 것으로 나타났습니다.
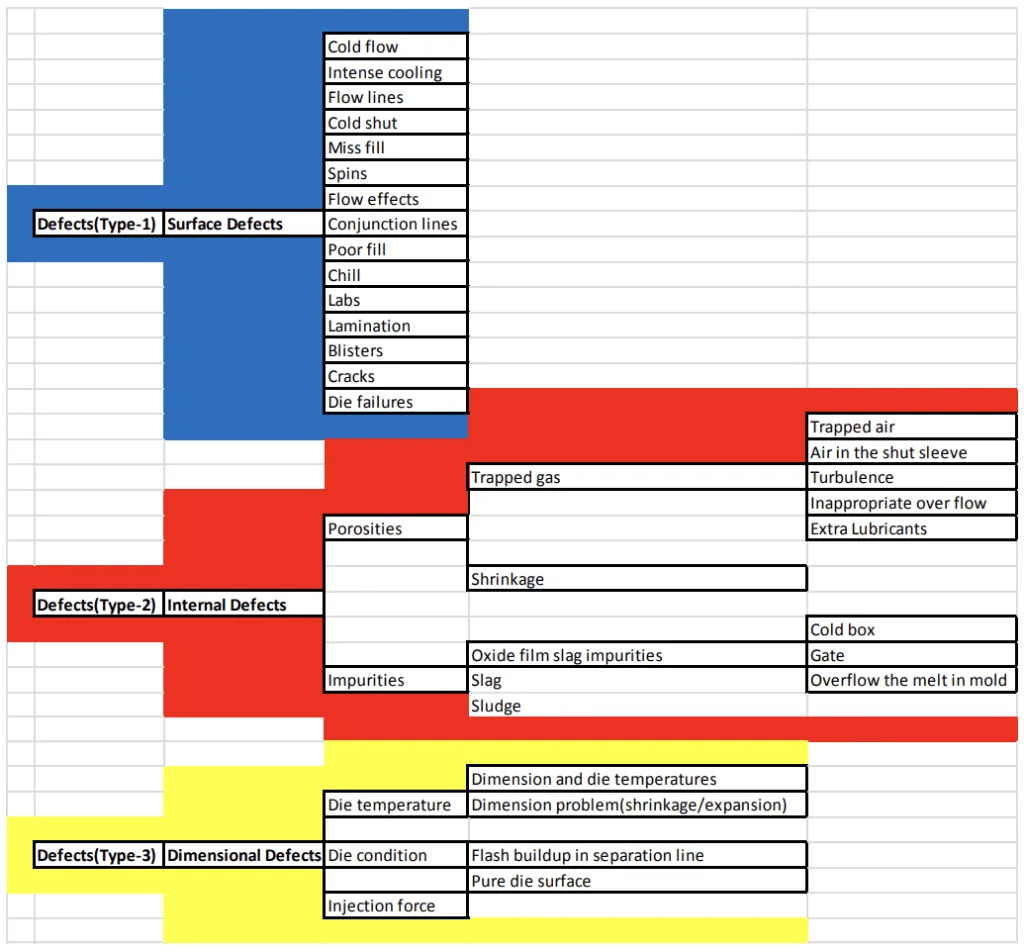
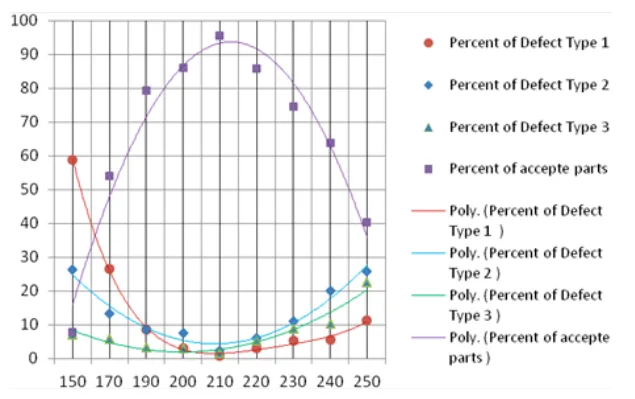
그림 이름 목록:
- FIGURE 2.1: AL-SI BINARY PHASE DIAGRAM
- FIGURE 2.2: GRAIN MICROSTRUCTURE AFTER SOLIDIFICATION OF CASTING PART SCHEMATIC (LEFT), AND MICROSTRUCTURE OF AL-4%CU BILLET (RIGHT) [1]
- FIGURE 2.3: RELATIONSHIP BETWEEN PHASE DIAGRAM WITH DISTRIBUTION COEFFICIENT K, AND DEVELOPMENT OF CONSTITUTIONAL UNDER COOLING [1]
- FIGURE 2.4: FORMATION OF DIFFERENT PHASE BOUNDARY STRUCTURES ACCORDING TO CONSTITUTIONAL UNDER COOLING: PLANAR (LEFT), CELLULAR (MIDDLE), AND DENDRITIC (RIGHT). THERMAL GRADIENT AND MELTING TEMPERATURE (TOP GRAPHS) AND RESULTING MICROSTRUCTURE (BOTTOM GRAPHS)
- FIGURE 2.5: EFFECT OF GL AND VS ON THE SOLIDIFIED MICROSTRUCTURE [1].
- FIGURE 2.6: VARIATION OF INTERNAL ENERGY OF THE SINGLE-PHASE SYSTEM VERSUS RADIUS OF FORMED NUCLEUS
- FIGURE 2.7: CATEGORIES OF DEFECTS OCCURRING IN THE PRODUCTION OF ALUMINUM PARTS THROUGH HPDC.
- FIGURE 2.8: (A) SCHEMATIC OF A SMALL SOLIDIFYING VOLUME ELEMENT OF UNIFORM TEMPERATURE WITHIN WHICH NUCLEATION AND GROWTH CAN OCCUR FROM THE MOLD WALL AND IN BULK;(B) SCHEMATICS OF THE CELLULAR AUTOMATON USED TO PREDICT MICROSTRUCTURE FORMATION IN THE SMALL SOLIDIFYING SPECIMEN SHOWN IN(A).
- FIGURE 2.9: DETAILS OF THE GROWTH OF ACELLULAR AUTOMATON CELL CORRECTION APPLIED TO ADENDRITE TIP
- FIGURE3.1: GEOMETRY OF LADDER FRAME PART
- FIGURE 3.2: THE INFLUENCE GRAPH
- FIGURE 3.3: THE LOADING GRAPH
- FIGURE 3.4: EFFECT OF DIE TEMPERATURE ON THE PERCENTAGE OF ACCEPTED PARTS AND THE THREE DEFECT TYPES OF THE DIE-CASTING PARTS.
- FIGURE 3.5: EFFECT OF DIE TEMPERATURE ON THE PERCENTAGE OF ACCEPTED PARTS AND THE THREE TYPES OF DEFECT IN THE DIE-CASTING PARTS
- FIGURE 3.6: MELT TEMPERATURES AT DIE ENTRANCE AND START INJECTION VERSUS DIE TEMPERATURES.
- FIGURE 3.7: MELT TEMPERATURES AT THE END OF THE DIE AND END INJECTION VERSUS DIE TEMPERATURES.
- FIGURE 3.8: REDUCTION OF MELT TEMPERATURE AT VARIOUS DIE TEMPERATURES AT THE INITIAL AND THE END OF INJECTION
- FIGURE 3.9: GEOMETRY OF LADDER FRAME PRODUCT
- FIGURE 3.10: TEMPERATURE FIELD IN THE PART DURING FILLING AT DIE TEMPERATURE OF 150°C.
- FIGURE 3.11: TEMPERATURE FIELD IN THE PART DURING FILLING AT DIE TEMPERATURE OF 200°C.
- FIGURE 3.12: TEMPERATURE FIELD IN THE PART DURING FILLING AT DIE TEMPERATURE OF 250°C.
- FIGURE 3.13: FILLING AND SOLIDIFICATION PATTERN AT DIE TEMPERATURE 200°C, MELT TEMPERATURE 680°CAND PISTON VELOCITY3 M/S.
- FIGURE 3.14: RESULT OF EXPERIMENT IN SIMILAR CONDITIONS TO SIMULATION
- FIGURE 3.15: OVERFLOWS LOCATIONS IN THE DIE
- FIGURE 3.16: TEMPERATURE DISTRIBUTION AND FILLING SEQUENCE OF THE MOLD AT200°C
- FIGURE 3.17: FINAL SOLIDIFICATION POSITIONS.
- FIGURE 3.18: GAS AND SHRINKAGE DEFECTS IN THE SECTION SURFACE
- FIGURE 3.19: EFFECT OF THE HOLES ON THE FLOW PATTERN AND SOLIDIFICATION.
- FIGURE 3.20: EFFECT OF THE HOLES LOCATED ON THE VELOCITY VECTORS OF THE MELT
7. 결론:
주물 형상과 금형 설계 간에는 수치 및 통계적 방법을 사용하여 최적화할 수 있는 명백한 관계가 있습니다. 연구 결과는 금형 설계 변경, 특히 세 개의 구멍 제거가 유익하다는 것을 시사했으며, 이는 빠른 응고 및 압력 전달 부족으로 인한 얇은 단면의 수축과 같은 문제를 방지하여 주물 품질을 향상시킬 수 있습니다.
실험을 통해 210°C의 금형 온도와 668°C에서 680°C 사이의 주입 온도가 금형 품질에 최적임을 확인했습니다. 본 연구는 시뮬레이션을 통해 예측된 유동 패턴으로부터 오버플로우 위치를 효과적으로 결정할 수 있음을 보여주었습니다. PCA 및 ANOVA와 같은 통계 도구의 적용은 다이캐스팅 실험 데이터 분석을 크게 용이하게 하여 더 쉽고 정확하게 만듭니다.
금형 온도는 결함의 수와 유형에 명확한 영향을 미치는 것으로 나타났습니다. 금형 온도가 200°C 미만일 때 유형 1 결함(표면)이 가장 빈번했습니다. 반대로, 금형 온도가 200°C 이상일 때 유형 2(내부) 및 유형 3(치수) 결함이 더 빈번했습니다. 전체 결함을 최소화하기 위한 최적의 금형 온도 범위는 210-215°C로 결정되었습니다. 따라서 연구된 A380 합금 및 부품 형상에 대한 이상적인 금형 온도 범위는 212.5±2.5°C입니다.
8. 참고문헌:
- [1- W. Kurz and D.J. Fisher. Fundamentals of Solidification. Switzerland: Trans Tech Pub., 4th edition, 1998.]
- [2- J.W. Gibbs, H.A. Bumstead, and W.R. Longley. The Collected Works of J. Willard Gibbs. Longmans,Green and Co, 1928.]
- [3- J.D. Van der Waals. Translation of J. D. van der Waals' "The thermodynamic theory of capillarity under the hypothesis of a continuous variation of density”. Journal of Statistical Physics, 20(2):200–244, 1979]
- [4- J.W. Cahn and J.E. Hilliard. Free energy of a nonuniform system. I. Interfacialfreeenergy. The Journal ofChemicalPhysics, 28:258, 1958.]
- [5- J.W. Cahn. Free energy of a nonuniform system. II. Thermodynamic basis. The Journal of Chemical Physics, 30:1121, 1959.]
- [6- J.W. Cahn and J.E. Hilliard. Free energy of a nonuniform system. III. Nucleation in a twocomponent incompressible fluid. The Journal of Chemical Physics, 31:688, 1959.]
- [7- D.W. Oxtoby and R. Evans. Nonclassical nucleation theory for the gas-liquid transition. The Journal ofChemicalPhysics, 89:7521, 1988.]
- [8- D.W. Oxtoby. Density functional methods in the statistical mechanics of materials. Annual Review of Materials Research, 32(1):39–52, 2002.]
- [9- S.F. Jones, G.M. Evans, and K.P. Galvin. Bubble nucleation from gas cavities a review. Advances in colloid and interface science, 80(1):27–50, 1999.]
- [10- E.N. Harvey, W.D. McElroy, and AH Whiteley. On cavity formation in water. Journal ofAppliedPhysics, 18:162, 1947.]
- [11- R.A. Outlaw, D.T. Peterson, and F.A. Schmidt. Hydrogen partitioning in pure cast aluminum as determined by dynamic evolution rate measurements. Metallurgical and Materials Transactions A, 12(10):1809–1816, 1981.]
- [12- J. Campbell. Castings. Butterworth-Heinemann, 2003.]
- [13- R.B. Dean. The formation of bubbles. Journal ofAppliedPhysics, 15:446, 1944.]
- [14- R. Sasikumar, M.J. Walker, S. Savithri, and S. Sundarraj. Initiation of microporosity from preexisting bubbles: a computational study. Modelling and Simulation in Materials Science and Engineering, 16(3):35009, 2008.]
- [15- D. Dispinar and J. Campbell. Critical assessment of reduced pressure test. Part 1: Porosityphenomena. International Journal ofCastMetals Research, 17(5):280–286, 2004.]
- [16- D. Dispinar and J. Campbell. Use of bifilm index as an assessment of liquid metal quality. International Journal ofCastMetals Research, 19(1):5–17, 2006.]
- [17- Z.W. Chen, M.Z. Jahedi., Die erosion and its effect on soldering formation in high pressure die casting of aluminum alloys,Materials and Design ,1999, vol.20,pp.303-309.]
- [18- P.W. Cleary, J. Ha, M. Prakash, T. Nguyen,∃3D SPH flow predictions and validation for high pressure die casting of automotive components∃,Applied Mathematical Modeling,2006, vol.30, pp. 1406–1427.]
- [19- Laws, K.J., Gun, B., Ferry, M.,∃Effect of die-casting parameters on the production of high quality bulk metallic glass samples∃,Mater. Sci. Eng., 2006, A425, pp.114–120.]
- [20- NADCA product specification standards for die castings/1997]
- [21- http://www.ewp.rpi.edu]
- [22- http://www.wtm.uni-erlangen.de]
- [23- ProCAST 2011.User's Manual]
- [24- M. Rappaz,Ch. A. Gandin, “Probabilistic Modelling of Microstructure Formation in Solidification Processes”, Actametallmater,Vol. 41 . No.2, pp.345-360, 1993]
9. 저작권:
- 본 자료는 "Mohammad Sadeghi"의 논문입니다. "OPTIMIZATION PRODUCT PARTS IN HIGH PRESSURE DIE CASTING PROCESS"를 기반으로 합니다.
- 논문 출처: http://www.diva-portal.org/smash/record.jsf?pid=diva2:804075
본 자료는 상기 논문을 기반으로 요약되었으며, 상업적 목적의 무단 사용을 금합니다.
Copyright © 2025 CASTMAN. All rights reserved.