융용 용접의 한계를 넘어서: 고강도, 저결함 접합을 위한 FSW의 모든 것
이 기술 브리핑은 Verma, S. M. & Misra, J.P.가 DAAAM International Scientific Book 2015에 발표한 학술 논문 "A Critical Review of Friction Stir Welding Process"를 기반으로 합니다. 주식회사 에스티아이씨앤디(STI C&D)의 전문가들이 제조 산업 전문가들을 위해 핵심 내용을 요약하고 분석했습니다.
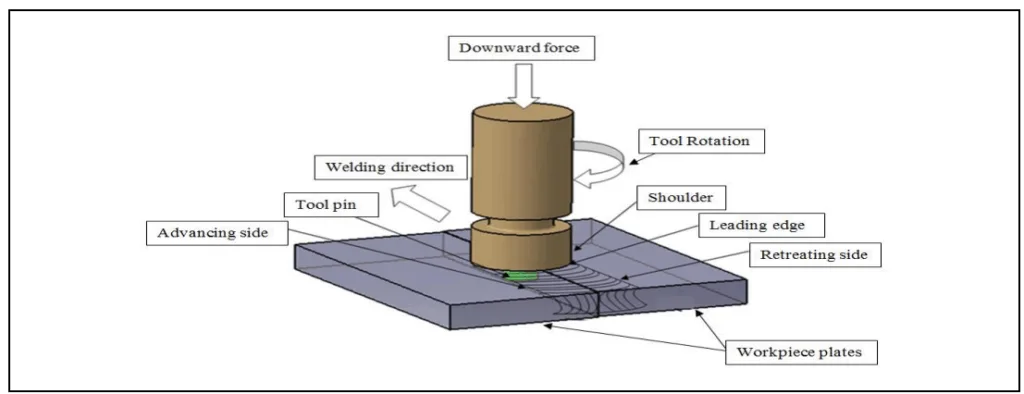
키워드
- 주요 키워드: 마찰 교반 용접 (Friction Stir Welding, FSW)
- 보조 키워드: 고상 용접(Solid-state welding), 알루미늄 용접(Aluminum welding), 이종 금속 접합(Dissimilar metal joining), 용접 공정 변수(Welding process parameters), 미세조직 분석(Microstructure analysis), 기계적 특성(Mechanical properties)
Executive Summary
- 도전 과제: 항공우주, 자동차 산업에서 널리 쓰이는 알루미늄과 같은 경량 합금은 기존의 융용 용접 시 기공, 넓은 열영향부(HAZ), 변형 등의 결함이 발생하기 쉽습니다.
- 연구 방법: 본 논문은 고상 접합 공정인 마찰 교반 용접(FSW)에 대한 광범위한 기존 연구들을 비판적으로 검토하고 종합하여, 공정 원리, 핵심 변수, 재료별 적용 사례 및 최신 기술 동향을 분석했습니다.
- 핵심 성과: FSW는 재료를 녹이지 않고 접합하여 기공과 같은 용융 결함을 원천적으로 제거하고, 좁은 열영향부와 우수한 기계적 특성을 가진 고품질의 접합부를 생성합니다. 이는 알루미늄, 강철, 구리, 이종 금속 등 다양한 재료에 효과적으로 적용될 수 있습니다.
- 결론: FSW는 기존 융용 용접의 한계를 극복하는 검증된 대안 기술이며, 예열 및 나노 입자 첨가와 같은 부가 기술을 통해 성능을 더욱 향상시킬 수 있는 잠재력을 가지고 있습니다.
도전 과제: 왜 이 연구가 제조 전문가들에게 중요한가?
항공우주, 자동차, 해양 산업의 발전에 따라 경량 고강도 합금의 사용이 급증하고 있습니다. 하지만 알루미늄, 마그네슘과 같은 소재들은 기존의 아크 용접이나 가스 용접과 같은 융용 용접(fusion welding) 기법으로 접합할 때 여러 문제에 직면합니다. 높은 에너지 밀도로 인해 넓은 열영향부(HAZ)가 형성되고, 이로 인해 재료의 기계적 특성(연성, 인장 강도 등)이 저하됩니다. 또한, 응고 과정에서 발생하는 기공, 균열, 심각한 변형 등의 결함은 제품의 신뢰성을 떨어뜨리는 주된 원인이 됩니다.
이러한 문제들을 해결하기 위해 재료의 용융점 이하 온도에서 접합이 이루어지는 고상 용접(solid-state welding) 기술이 주목받게 되었습니다. 그중에서도 1991년 TWI(The Welding Institute)에서 발명한 마찰 교반 용접(FSW)은 획기적인 대안으로 떠올랐습니다. FSW는 소모성 용가재나 보호 가스가 필요 없고, 용융으로 인한 결함이 없으며, 친환경적이라는 독보적인 장점들을 바탕으로 기존 용접 기술을 빠르게 대체하고 있습니다. 본 논문은 FSW 기술의 핵심적인 측면들을 심층적으로 검토하여, 현장의 엔지니어와 연구자들이 이 기술을 더 깊이 이해하고 활용할 수 있는 지침을 제공합니다.
접근 방식: 연구 방법론 분석
본 연구는 새로운 실험을 수행한 것이 아니라, 마찰 교반 용접(FSW) 분야에서 발표된 수많은 선행 연구들을 체계적으로 수집하고 비판적으로 분석한 리뷰 논문(review paper)입니다. 저자들은 FSW 기술을 여러 핵심적인 관점에서 종합적으로 평가했습니다.
- 공정 원리 및 미세조직: FSW의 기본적인 작동 원리(Figure 1)와 접합 후 형성되는 독특한 미세조직 영역(Figure 2)에 대한 연구들을 분석했습니다.
- 공정 변수 분석: 용접 품질에 영향을 미치는 다양한 변수들을 툴링 관련, 장비 관련, 기타 변수로 분류하고, 이들의 상호 관계를 인과관계 다이어그램(Figure 3)으로 정리하여 체계적으로 고찰했습니다.
- 재료별 적용 사례: 연구가 가장 활발히 이루어진 알루미늄 합금(Figure 5)을 시작으로 강철, 구리, 마그네슘, 티타늄, 심지어 이종 금속과 폴리머에 대한 FSW 적용 연구 결과들을 종합하여 각 재료의 접합 특성을 비교 분석했습니다.
- 최신 기술 동향: 접합부 성능을 더욱 향상시키기 위한 예열(preheating), 나노 입자 첨가(nanoparticle inclusion), 퀜칭(quenching)과 같은 최신 보조 기술들의 효과와 가능성을 탐구했습니다.
이러한 포괄적인 접근을 통해, 본 논문은 FSW 기술의 현주소를 조망하고 미래 연구가 나아가야 할 방향을 제시하는 중요한 가이드라인 역할을 합니다.
핵심 성과: 주요 발견 및 데이터
본 리뷰 논문은 FSW 기술의 우수성과 잠재력을 입증하는 다양한 연구 결과들을 종합하여 다음과 같은 핵심적인 발견들을 제시합니다.
- 발견 1: 월등한 접합 품질과 결함 최소화
FSW는 재료를 녹이지 않고 고체 상태에서 소성 변형시켜 접합하므로, 융용 용접에서 흔히 발생하는 기공, 응고 균열, 스패터 등의 결함이 없습니다. Figure 2에서 보듯이, 접합부는 미세하고 균일한 재결정립으로 구성된 너겟존(nugget zone)을 형성하여 모재보다 우수하거나 동등한 기계적 강도를 나타냅니다. - 발견 2: 광범위한 재료 적용성
FSW는 다양한 재료에 성공적으로 적용되었습니다. Figure 5에 따르면, 전체 연구의 76%가 알루미늄에 집중되어 있으며, 이는 FSW가 알루미늄 접합의 어려움을 해결하는 데 매우 효과적임을 시사합니다. 이 외에도 고강도 강철의 부식 및 인성 저하 문제를 해결하고, 열전도율이 높은 구리의 접합을 가능하게 하며, 서로 다른 물성을 가진 이종 금속(예: 알루미늄-강철, 알루미늄-구리)의 접합에도 성공적인 결과를 보여주었습니다. - 발견 3: 공정 변수의 결정적 역할
용접 품질은 공정 변수에 의해 크게 좌우됩니다. 특히 회전하는 툴의 형상(Figure 4)은 재료의 유동 및 혼합에 직접적인 영향을 미칩니다. 예를 들어, 나사산이 있는 테이퍼형 핀은 재료의 수직 유동을 촉진하여 결함 없는 강한 접합부를 만드는 데 유리합니다. 또한 툴의 회전 속도와 이송 속도는 가해지는 열의 양과 소성 변형 정도를 결정하여, 최종 접합부의 미세조직과 기계적 특성을 제어하는 핵심 요소임이 여러 연구를 통해 확인되었습니다. - 발견 4: 첨단 기술을 통한 성능 향상
FSW 공정의 성능을 극대화하기 위한 새로운 시도들이 활발히 연구되고 있습니다. 접합 전 예열(preheating)은 소재를 부드럽게 하여 재료 유동성을 높이고 용접에 필요한 힘을 줄여줍니다. 또한, SiC나 ZrB2 같은 나노 입자를 첨가하면 접합부 내에서 강화재 역할을 하여 재결정립 성장을 억제하고 인장 강도를 획기적으로 향상시킬 수 있음이 밝혀졌습니다.
귀사의 운영을 위한 실질적 시사점
본 논문의 연구 결과들은 실제 제조 현장에서 다음과 같은 실질적인 개선을 이끌어낼 수 있습니다.
- 공정 엔지니어: 논문에서 제시된 다양한 툴 형상(Figure 4)과 공정 변수(회전 속도, 이송 속도 등)에 대한 분석 결과는 특정 소재와 두께에 맞는 최적의 용접 조건을 설정하는 데 중요한 근거를 제공합니다. 이를 통해 '키싱 본드(kissing bond)'와 같은 내부 결함을 최소화하고 일관된 품질의 접합부를 확보할 수 있습니다.
- 품질 관리: Figure 2에 나타난 너겟존(Nugget), 열-기계적 영향부(TMAZ), 열영향부(HAZ) 등 FSW 접합부의 특징적인 미세조직 영역은 품질 평가의 명확한 기준이 됩니다. 각 영역에 걸친 경도 분포를 측정하고 분석함으로써 접합부의 건전성을 비파괴적으로 예측하고 관리할 수 있습니다.
- R&D 및 소재 개발: 본 논문은 이종 금속 접합, 금속기 복합재료(MMC), 폴리머 등 아직 연구가 부족한 분야에서 FSW의 엄청난 잠재력을 보여줍니다. 특히 나노 입자 강화 FSW에 대한 연구 결과는 기존 소재의 한계를 뛰어넘는 차세대 고성능 접합 기술 개발에 대한 새로운 아이디어를 제공할 수 있습니다.
논문 상세 정보
A Critical Review of Friction Stir Welding Process
1. 개요:
- 논문 제목: A Critical Review of Friction Stir Welding Process
- 저자: Verma, S. M. & Misra, J.P.
- 발표 연도: 2015
- 게재 학술지/학회: DAAAM INTERNATIONAL SCIENTIFIC BOOK 2015
- 키워드: Solid-state welding, friction stir welding, preheating, quenching, nano-particle inclusion
2. 초록:
마찰 교반 용접(FSW)은 영구적인 고상 접합 공정으로, 특히 항공우주, 해양, 우주선, 자동차 등 제조 산업에서 다양한 금속 합금 및 비금속을 접합하는 데 빠르게 증가하고 있습니다. 현재 시나리오에서 금속 합금의 용접은 FSW의 독특한 특징, 즉 기공 결함 감소, 열영향부(HAZ) 감소, 보호 가스 불필요, 친환경성, 변형 감소 등으로 인해 융용 용접 공정을 대체하고 있습니다. 이 장에서는 마찰 교반 용접의 공정 원리, 야금학적 및 기계적 측면, 예열 및 나노 입자 포함의 효과와 같은 중요한 측면에 대한 비판적 평가가 논의되었습니다. FSW와 관련된 어려움 및 기타 문제들도 다루어져 전 세계 연구 커뮤니티가 이 분야에서 광범위한 연구를 수행할 수 있도록 지침을 제공합니다.
3. 서론 요약:
19세기 중반에 등장한 용접 기술, 특히 융용 용접은 높은 에너지 밀도로 인해 넓은 열영향부(HAZ)를 형성하고, 이는 변형, 기계적 특성 저하, 불완전 용입 등의 결함을 유발한다. 알루미늄, 마그네슘과 같은 반응성 금속에는 부적합하다. 이러한 단점들은 필러나 보호 가스 없이 모재의 용융점 이하에서 접합하는 고상 용접 기술의 필요성을 대두시켰다. 1991년 TWI에서 발명된 마찰 교반 용접(FSW)은 기존 용접의 어려움을 극복하는 독특하고 새로운 기술로, 결함이 거의 없고 친환경적이며 에너지 효율적인 공정으로 자리매김했다.
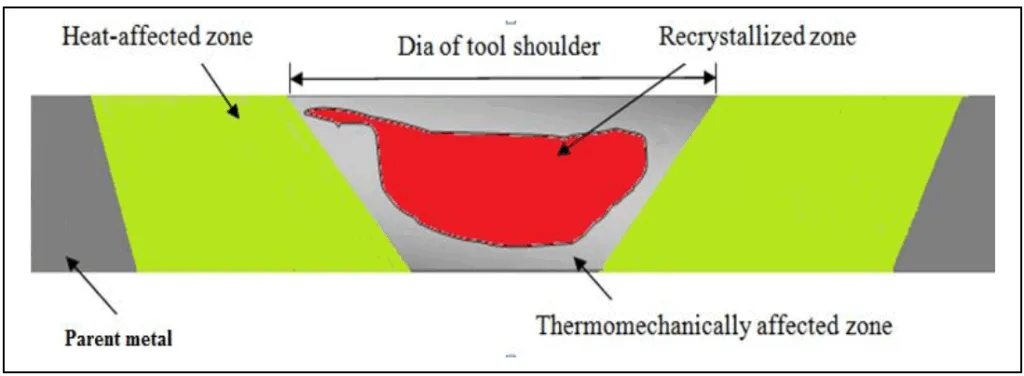
4. 연구 요약:
연구 주제의 배경:
FSW는 비소모성 회전 툴을 사용하여 마찰열과 소성 변형을 통해 재료를 접합하는 고상 용접 기술이다. 툴은 핀(pin)과 숄더(shoulder)로 구성되며, 접합할 부재에 삽입되어 회전하면서 전진한다. 이 과정에서 재료는 녹지 않고 부드러워지며, 툴의 교반 작용에 의해 혼합되어 고상으로 접합된다.
이전 연구 현황:
본 논문은 리뷰 논문으로서, FSW에 대한 수많은 이전 연구들을 종합하고 분석한다. 특히 알루미늄 합금에 대한 연구가 가장 활발했으며(전체의 76%), 그 외 강철, 구리, 마그네슘, 이종 금속, 폴리머 등 다양한 재료에 대한 FSW 적용 연구 결과들이 검토되었다. 각 연구는 공정 변수(툴 형상, 회전 속도 등)가 미세조직과 기계적 특성에 미치는 영향을 주로 다루었다.
연구 목적:
본 논문의 목적은 FSW 공정의 다양한 중요 측면(공정 원리, 야금학적/기계적 특성, 예열 및 나노 입자 첨가 효과 등)을 비판적으로 평가하고, 현재까지의 연구 성과를 종합하여 제시하는 것이다. 또한, 아직 해결되지 않은 과제와 이슈들을 조명함으로써 향후 연구자들에게 이 분야의 심층 연구를 위한 가이드라인을 제공하고자 한다.
핵심 연구 내용:
논문은 FSW의 핵심을 다음과 같이 나누어 심층적으로 분석했다:
- 공정 원리 및 미세조직: FSW의 기본 메커니즘과 접합 후 형성되는 너겟존, TMAZ, HAZ 등의 미세조직적 특징을 설명했다.
- 공정 변수: 툴링, 장비, 기타 변수들이 용접 품질에 미치는 영향을 인과관계 다이어그램을 통해 체계적으로 분석했다.
- 재료별 적용: 알루미늄, 강철, 구리, 마그네슘, 티타늄, 이종 금속, 폴리머 등 다양한 재료에 대한 FSW 연구 결과를 요약하고 특성을 비교했다.
- 부가 공정의 효과: 예열, 퀜칭, 나노 입자 첨가와 같은 부가 공정이 접합부의 기계적 특성을 어떻게 향상시키는지에 대한 연구들을 검토했다.
5. 연구 방법론
연구 설계:
본 연구는 특정 실험을 설계한 것이 아닌, 기존에 발표된 학술 논문, 기술 보고서 등을 종합적으로 검토하는 문헌 연구(Literature Review) 방식으로 설계되었다.
데이터 수집 및 분석 방법:
저자들은 FSW와 관련된 광범위한 학술 데이터베이스를 통해 자료를 수집했다. 수집된 자료들은 공정 원리, 재료별 적용, 공정 변수의 영향, 최신 기술 동향 등의 주제별로 분류되었다. 각 주제에 대해 발표된 연구 결과들을 비교하고, 일관된 경향과 상충하는 결과들을 비판적으로 분석하여 FSW 기술에 대한 종합적인 결론을 도출했다.
연구 주제 및 범위:
연구 범위는 FSW 공정의 전반을 아우른다.
- 기초: FSW의 원리, 공정 변수, 실험 장비 구성.
- 재료: 알루미늄, 강철, 구리, 마그네슘, 티타늄, 황동, 플라스틱 등 유사 및 이종 재료 접합.
- 심화: 나노 입자 첨가, 예열, 퀜칭이 접합부 특성에 미치는 영향.
- 미래 연구 방향: 아직 연구가 부족한 영역과 해결해야 할 과제 제시.
6. 주요 결과:
주요 결과 요약:
본 리뷰를 통해 도출된 주요 결과는 다음과 같다:
- FSW는 융용 용접 대비 변형, 수축, HAZ, 기공 결함이 현저히 적은 우수한 접합 기술이다.
- FSW는 알루미늄, 마그네슘, 구리, 강철, 아연, 니켈 및 그 합금, 플라스틱 등 다양한 유사/이종 재료 접합에 적합하다.
- 툴 회전 속도, 이송 속도, 틸트 각도와 같은 공정 변수는 접합부의 기계적 및 야금학적 거동에 결정적인 영향을 미친다.
- 툴의 핀과 숄더 형상은 교반되는 재료의 양과 마찰열을 조절하므로 건전한 용접부를 얻기 위한 핵심 설계 요소이다.
- 알루미늄, 구리, 마그네슘에 대한 연구가 주를 이루었으며, 합금, 플라스틱, 복합재료 등에 대한 연구는 향후 큰 잠재력을 가진다.
- 예열, 나노 입자 첨가, 퀜칭과 같은 부가 공정은 FSW 접합부의 기계적/야금학적 특성을 향상시키는 데 효과적이며, 이에 대한 심층 연구가 필요하다.
그림 제목 목록:
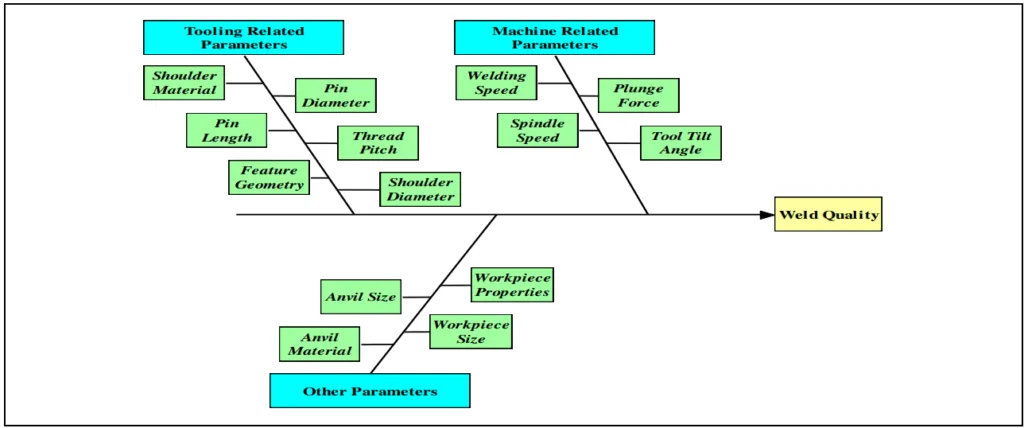
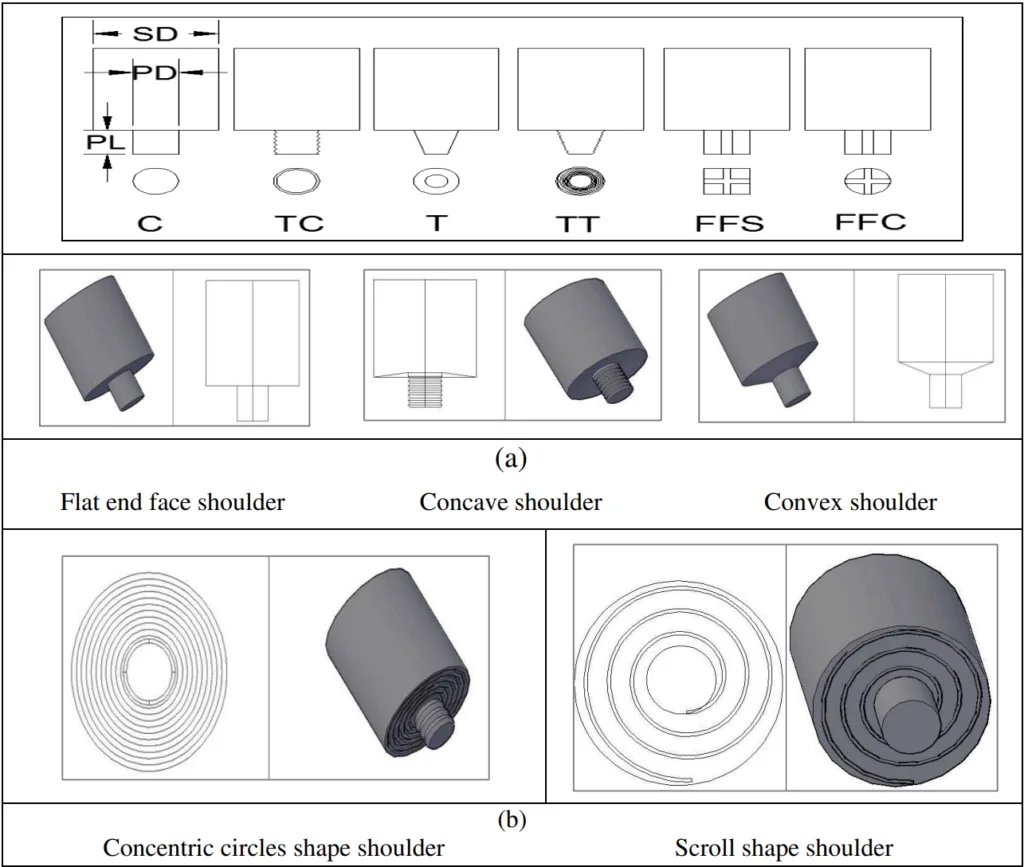
- Fig. 1. Principle of friction stir welding (Backer and Bolmsjo, 2014)
- Fig. 2. Microstructural regions of friction stir welding (Mahoney et al., 1998)
- Fig. 3. Cause and effect diagram for friction stir welding process
- Fig. 4. (a) FSW tool with different pin geometry (C: Cylindrical; TC: Threaded cylindrical; T: Tapered; TT: Threaded taper; FFS: Four flute square; FFC: Four flute cylindrical)(b) FSW tools with different shoulder geometry
- Fig. 5. Comparative study of published research work on FSW
7. 결론:
본 논문은 FSW 기술의 다양한 측면을 비판적으로 검토하고 주요 발견 사항들을 제시했다. 결론적으로 FSW는 낮은 변형, 아크 및 용가재 불필요, 낮은 HAZ, 무결점 등의 독특한 특성으로 인해 융용 용접의 강력한 대안으로 부상하고 있다. 이 기술은 다양한 금속, 합금, 플라스틱의 접합에 적합하며, 기존 용접 대비 인장 강도, 연성, 피로 수명 등에서 상당한 향상을 보인다. 툴 형상과 공정 변수가 품질에 결정적인 역할을 하지만, 아직 재료 유동 메커니즘, 툴 마모, 공정 모델링 등 심층 연구가 필요한 분야가 많다. 특히 예열, 나노 입자 첨가, 퀜칭의 효과에 대한 상세한 연구와 다양한 재료(합금, 플라스틱, 복합재료)로의 확대 적용은 FSW 기술의 미래 발전에 있어 중요한 연구 과제로 남아있다.
8. 참고문헌:
- Backer, J. D. & Bolmsjö, G. (2014).Temperature control of robotic friction stir welding using the thermoelectric effect. Int. J. of Adv. Manuf. Technol., 70, 375-383.
- Elangovan, K.; Balasubramanian, V. & Valliappan, M. (2008). Influences of tool pin profile and axial force on the formation of friction stir processing zone in AA6061 aluminium alloy. Int. J. Adv. Manuf. Technol, 38, 285-295
- Lohwasser, D. & Chen, Z. (2010). Friction stir welding: from basics to applications, Woodhead Publishing limited, New Delhi
- Mahoney, M. W.; Rohdes, C. G.; Flintoff, J. G.; Surling,R. A. & Bingel, W. H. (1998). Properties of friction-stir-welded 7075 T651 aluminum. Metallurgical and Materials Transactions, 29,1955-1964
- Reynolds, A. P.; Tang, W.; Gnaupel-Herold, T. & Prask, H. (2003). Structure, properties, and residual stress of 304L stainless steel friction stir welds. Scripta Materialia, 48, 1289-1294
- Rodrigues, D. M.; Loureiro, A.; Leitao, C.; Leal, R. M.; Chaparro, B. M. &Vilaça, P. (2009). Influence of friction stir welding parameters on the microstructural and mechanical properties of AA 6016-T4 thin welds. Materials & Design, 30
- Sinclair, P. C.; Longhurst, W. R.; Cox, C. D.; Lammlein, D. H.; Alvin, M. & Cook, G.E. (2010). Materials and manufacturing processes heated friction stir welding: an experimental and theoretical investigation into how preheating influences process
- Takehiko, W.; Hirofumi, T. & Yanagisawa, A. (2006). Joining of aluminum alloy to steel by friction stir welding. Science and Technology of Welding and Joining, 4, 365-372
- Thomas, W. M.; Nicholas, E. D.; Needham, J. C.; Murch, M. G.; Templesmith, P. & Dawes, C. J. (1991). Patent 9125978.8
Conclusion & Next Steps
This research provides a valuable roadmap for enhancing component joining through Friction Stir Welding. The findings offer a clear, data-driven path toward improving quality, reducing defects, and optimizing production for a variety of materials.
STI C&D is committed to applying cutting-edge industry research to solve our customers’ most challenging technical problems. If the challenges discussed in this paper align with your goals, please contact our engineering team to discuss how we can help you apply advanced simulation principles to your FSW process development.
Expert Q&A:
Q1: What are the main advantages of Friction Stir Welding (FSW) over traditional fusion welding?
A1: According to the paper, FSW offers several unique advantages, including low distortion and shrinkage, no need for filler metal or shielding gas, a reduced heat-affected zone (HAZ), and freedom from porosity defects. This makes it an eco-friendly and highly effective alternative for joining materials like aluminum, magnesium, and copper. (Source: "A Critical Review of Friction Stir Welding Process", Abstract & Section 4).Q2: How important is the FSW tool design for the quality of the weld?
A2: The tool design is a deciding factor for obtaining sound welds. The paper states that the FSW tool, specifically the geometry of the pin and shoulder, regulates the amount of material stirred and the frictional heat generated. Different geometries, as shown in Fig. 4, directly impact material flow and the final mechanical and metallurgical properties of the joint. (Source: "A Critical Review of Friction Stir Welding Process", Section 4 & Section 2).Q3: Can FSW be used to join dissimilar materials, like aluminum and steel?
A3: Yes, the review indicates that FSW is capable of joining dissimilar metals, which is a significant challenge for fusion welding. For example, Takehiko et al. (2006) successfully joined aluminum alloy to steel, finding that joint strength was optimized when the tool pin was slightly offset toward the steel side. This capability makes FSW highly valuable for many industrial applications. (Source: "A Critical Review of Friction Stir Welding Process", Section 3.5).Q4: What are the key process parameters that need to be controlled in FSW?
A4: The paper identifies three broad categories of parameters, as shown in the cause-and-effect diagram in Fig. 3. The most critical machine-related parameters are tool rotational speed, welding (traverse) speed, plunge force/depth, and tool tilt angle. These parameters directly influence the heat input, material flow, and ultimately, the final weld quality. (Source: "A Critical Review of Friction Stir Welding Process", Section 1.2).Q5: Does adding nanoparticles to the joint improve the FSW process?
A5: Yes, the inclusion of hard ceramic nanoparticles (like SiC or ZrB₂) into the joint can significantly enhance the mechanical properties of FSW joints. The paper notes that these particles act as barriers against recrystallization during the process, leading to improved strength. In some cases, the joint becomes so strong that fracture during testing occurs in the base metal, not the weld. (Source: "A Critical Review of Friction Stir Welding Process", Section 3.6).Q6: What are the main areas where more research on FSW is needed?
A6: The review concludes by identifying several areas for future research. These include a deeper understanding of the material flow mechanism, tool geometry design and wear, the corrosion behavior of FSW joints, and the effect of process enhancements like preheating and quenching. Crucially, the paper calls for the development of mathematical/theoretical models to predict weld performance based on input parameters. (Source: "A Critical Review of Friction Stir Welding Process", Section 4).
Copyright
- This material is an analysis of the paper "A Critical Review of Friction Stir Welding Process" by Verma, S. M. & Misra, J.P.
- Source of the paper: DOI: 10.2507/daaam.scibook.2015.22
- This material is for informational purposes only. Unauthorized commercial use is prohibited.
- Copyright © 2025 STI C&D. All rights reserved.