이 소개 자료는 "[학술지/학회]"에서 발행한 논문 "[Examples of Practical Solutions for Aluminium Castings using Quiescent Running Systems and Computer Modelling]"을 기반으로 작성되었습니다.
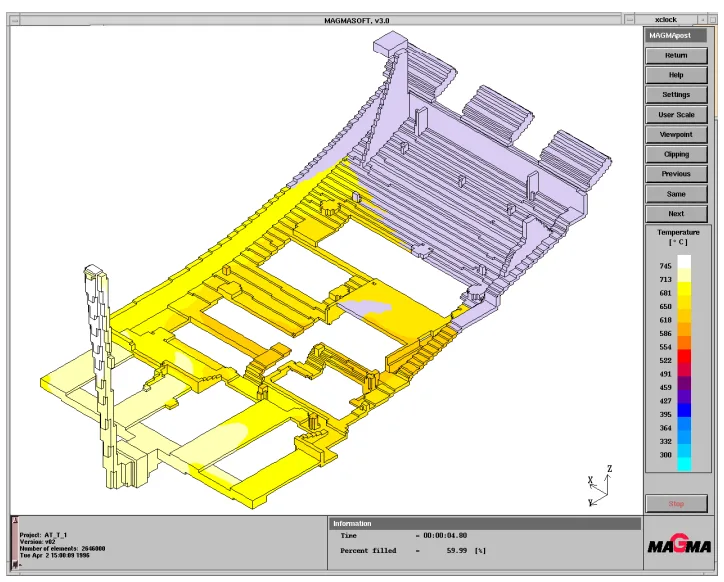
1. 개요:
- 제목: Examples of Practical Solutions for Aluminium Castings using Quiescent Running Systems and Computer Modelling (정온 주행 시스템과 컴퓨터 모델링을 이용한 알루미늄 주조의 실제적 해결 방안 예시)
- 저자: Mark R Jolly, PhD.
- 발행 연도: 1999년
- 발행 학술지/학회: Conference Paper
- 키워드: Aluminium Castings, Quiescent Running Systems, Computer Modelling, Gravity Die-Casting, Low-Pressure Die-Casting, Sand Casting (알루미늄 주물, 정온 주행 시스템, 컴퓨터 모델링, 금형 주조, 저압 주조, 사형 주조)
2. 초록:
영국 버밍엄 대학교의 주조 센터는 지난 5년간 실제적인 규칙과 컴퓨터 시뮬레이션의 조합을 사용하여 업계에 주행 시스템 솔루션을 제공해왔습니다. 이 실제적 규칙들은 존 캠벨 교수가 이끄는 주조 연구 그룹이 실제 충전 시스템을 관찰하기 위해 실시간 X-ray 기술을 사용하여 수행한 연구 결과에서 추출된 것입니다. 컴퓨터 시뮬레이션은 다양한 상용 소프트웨어 패키지를 사용하여 사형, 금형(영구 주형) 및 저압 다이캐스팅에 대해 수행되었습니다. 본 논문에서는 채택된 접근 방식의 효과를 입증하기 위해 자동차 및 비자동차 분야를 아우르는 다양한 사례들을 제시합니다.
3. 서론:
용탕이 주형 캐비티로 처리되고 분배되는 방식은 아마도 주물의 품질과 특성에 영향을 미치는 가장 중요한 단일 요소일 것입니다. 따라서 주조 산업의 많은 사람들과 그 고객들이 이를 주물 및 관련 제조 공정 설계에서 가장 마지막에 고려해야 할 사항으로 여기는 것은 놀라운 일입니다. 버밍엄 대학교 주조 연구 그룹과 주조 센터가 산업계와 협력하여 수행한 연구는 유체 역학의 세부 사항에 주의를 기울임으로써 주물 품질에 상당한 개선이 이루어질 수 있음을 보여주었습니다. 주물의 충전이 올바르게 해결되면, 수많은 글이 쓰이고 모든 주조인이 의견을 가진 주물의 압탕 공급은 부차적인 문제가 됩니다. 본 논문은 이론적 규칙, 시뮬레이션 및 이 둘의 실제적 적용을 통해 상업적으로 실행 가능한 해결책을 제시하는 세 가지 사례 연구를 보여줍니다.
4. 연구 요약:
연구 주제의 배경:
본 연구는 고품질 금속 주물을 생산해야 하는 산업적 과제를 배경으로 합니다. 주조 부품의 품질은 용융된 금속이 주형에 어떻게 주입되는지와 근본적으로 연결되어 있습니다. 난류 충전 과정은 불량품과 신뢰할 수 없는 최종 제품을 초래하는 결함의 주요 원인입니다.
기존 연구 현황:
이 연구는 버밍엄 대학교의 주조 연구 그룹이 존 캠벨 교수의 지도하에 수행한 연구에 기반을 두고 있습니다. 이 그룹은 주조 공정의 실시간 X-ray 이미징 관찰을 기반으로 충전 시스템 설계를 위한 일련의 실제적인 규칙을 개발했습니다. 현재 논문은 이러한 규칙들을 상용 컴퓨터 시뮬레이션 소프트웨어와 통합함으로써 이를 발전시킵니다.
연구 목적:
본 연구의 목적은 실제 설계 규칙과 컴퓨터 시뮬레이션을 결합한 접근 방식이 산업 주조 공정의 문제 해결에 얼마나 효과적인지를 입증하는 것입니다. 이 방법론이 자동차 및 비자동차 부품의 복잡한 충전 및 응고 문제를 어떻게 해결할 수 있는지를 보여줍니다.
핵심 연구:
연구의 핵심은 세 가지 상세한 산업 사례 연구로 구성됩니다:
- 금형 주조 ATM 하우징: NCR 자동 현금 인출기(ATM)용 크고 복잡한 알루미늄 하우징의 주행 시스템 설계.
- 금형 주조 히트 싱크 주물: 선박 기어박스용 스테인리스 스틸 튜브가 내장된 히트 싱크의 제조 공정 개발.
- 저압 자동차 휠 주조: Compomotive Ltd.를 위한 저압 다이캐스팅 알루미늄 합금 휠의 기공 결함 해결.
5. 연구 방법론
연구 설계:
연구 방법론은 이론적 원리와 컴퓨터 분석을 결합합니다. 주조 연구 그룹(CRG)이 개발한 설계 규칙을 사용하여 초기 충전 시스템을 만듭니다. 이 설계는 컴퓨터 시뮬레이션을 통해 구현되고 테스트되어 주형 충전 및 응고 과정을 예측하고 시각화함으로써 생산 전에 반복적인 개선을 가능하게 합니다.
데이터 수집 및 분석 방법:
이 연구는 상용 시뮬레이션 소프트웨어 패키지를 사용하여 유체 흐름과 응고를 모델링합니다. 금속 속도, 온도 분포(Figure 17 참조), 기공 예측(Figure 9 및 Figure 12 참조)과 같은 시뮬레이션 결과 분석이 잠재적 결함을 식별하는 주요 방법입니다. 이러한 예측은 Figure 2에서 보여주듯이 실제 주조 시험 결과와 비교하여 검증됩니다.
연구 주제 및 범위:
이 연구는 금형 주조(영구 주형), 사형 주조, 저압 다이캐스팅을 포함한 다양한 일반적인 주조 공정을 다룹니다. 적용 분야는 비자동차(ATM 하우징) 및 자동차(히트 싱크, 휠) 부품을 아우르며, 이 방법들의 광범위한 적용 가능성을 보여줍니다.
6. 주요 결과:
주요 결과:
본 논문은 정온 주행 시스템과 컴퓨터 모델링의 성공적인 적용을 보여주는 세 가지 사례 연구를 제시합니다.
- 사례 연구 1에서는 복잡한 금형 주조 ATM 하우징을 위해 정온 충전 시스템이 설계되었습니다. 주조 연구 그룹(CRG)의 설계 규칙을 사용한 시뮬레이션은 8초의 충전 시간을 달성하여 미성형을 방지하는 데 필수적이었습니다. 시뮬레이션은 주물의 평평한 영역에서 발생할 수 있는 충전 결함과 공기 혼입을 정확하게 예측했으며(Figure 2a), 이는 실제 주물에서 확인되었고(Figure 2b) 이후 브리지와 벤트를 추가하여 설계(Figure 3)를 수정함으로써 해결되었습니다.
- 사례 연구 2에서는 내장된 강철 튜브가 있는 히트 싱크에 대한 초기 금형 주조 방식이 실패하여 난류 충전으로 인해 큰 기포가 있는 주물이 생산되었습니다. 시뮬레이션 결과, 강철 튜브가 충전 중에 가열되어 중앙에 고온점을 형성하고 이로 인해 적절한 압탕 공급이 방해받아 기공이 발생함이 밝혀졌습니다(Figure 9, Figure 11). 추가 분석을 통해 도출된 해결책은 사형 주조로 공정을 변경하는 것이었고, 이를 통해 더 느리고 제어된 충전이 가능해져 불량 없이 3등급 이상의 품질을 가진 주물을 생산할 수 있었습니다(Figure 12, Figure 13).
- 사례 연구 3에서는 저압 다이캐스팅 자동차 휠이 스포크-림 접합부의 기공으로 인해 불량품이 발생했습니다. 시뮬레이션은 이 심각한 기공을 정확하게 예측했을 뿐만 아니라, 주조 공장에서 이전에 식별하지 못했던 중앙 허브의 미세 기공도 발견했습니다(Figure 18b). 시뮬레이션 기반의 목표 솔루션을 적용하여 문제를 완화했습니다. 허브 기공은 스프레더 설계를 변경하여 줄였고, 스포크-림 기공은 냉각 핀을 추가하여 극적으로 감소시켰습니다(Figure 19).
그림 이름 목록:
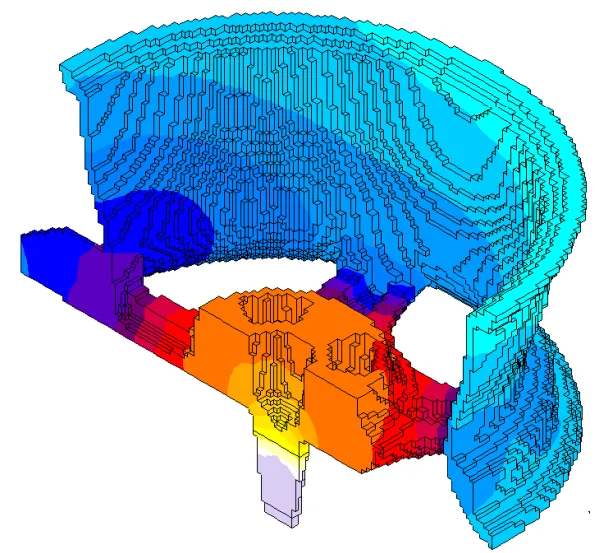
- Figure 1: Isometric, top and side views of ATM module interface castings and rigging.
- Figure 2a): Filling simulation showing potential filling problem and air entrapment.
- Figure 2b): Casting showing problem predicted in figure 2a).
- Figure 3: a) Simulation of module filling with wide bridges b) Simulation of module filling with narrow bridges.
- Figure 4: Simulations of flow off junctions a) & b) foundry preferred methods – 10 mm and 15mm thickness respectively with witness c) Castings Centre preferred method 15 mm no witness.
- Figure 5: ATM housing castings in product.
- Figure 6: Diagram of the 150 mm wide heat sink casting.
- Figure 7: Die-cast heat sink component first running system.
- Figure 8: Cross sections through first heat sink simulation showing the low level turbulence problem at a) 40 % full and no turbulence at b) 80% full.
- Figure 9: Porosity levels in the die-cast heat sink a) complete casting and rigging b) zoom in on region between tubes.
- Figure 10: a) CAD drawing of 5th version of rigging showing bubble trap, filter placed at 45° and shaped feeder b) Solidification results showing porosity distribution demonstrating that the change of alloy has no effect and feeder does not work.
- Figure 11: a) and b) showing progression of recalescence up the casting between the tubes c) and d) showing temperature rise between the tubes as the casting fills.
- Figure 12: a) Complete sand cast heat sink showing the redistribution of porosity compared with die-casting. b) Temperature distribution across the casting after filling showing no recalescence.
- Figure 13: Final configuration of rigging for heat sink component for sand casting.
- Figure 14: Low-pressure die-cast automotive wheel.
- Figure 15: Process pressure cycle for LPDC auto wheel.
- Figure 16a: Finite difference mesh for LPDC wheel casting.
- Figure 16b: Finite difference mesh of dies for LPDC wheel casting.
- Figure 17: Simulated warming cycles showing increases in die temperature.
- Figure 18a): Solidification time contour plot showing thermal isolations.
- Figure 18b): Porosity prediction showing macro- and micro-graphs confirming the predictions.
- Figure 19a): Solidification time contours for LPDC after modification showing better directional solidification and no thermal isolations.
- Figure 19b): Porosity prediction in LPDC after modification showing substantial reduction of porosity in hub and spoke rim junction.
7. 결론:
본 논문은 설계 규칙이 난류 없는 충전 시스템을 설계하는 데 중요한 출발점을 제공하지만, 모든 주조 시나리오에 대한 최종적인 "규칙집"은 아니라고 결론 내립니다. 정교한 주조 시뮬레이션 도구의 사용은 매우 가치 있으며, 비싼 실제 금형으로 주조 현장에서 시행착오를 겪는 대신 컴퓨터상에서 이를 수행할 수 있게 해줍니다. 이 접근 방식은 주행 시스템을 개선하는 데 도움이 될 뿐만 아니라, 수용 가능한 품질을 보장하기 위해 올바르고 가장 실행 가능한 제조 경로를 결정하는 데 필수적임이 입증되었습니다. 사례 연구들은 적절하고 정온한 충전 설계를 통해 난류 관련 결함이 제거되면, 응고 과정에서 다시 나타나지 않아 최종 제품에서 탐지 불가능한 "암적 존재"가 되는 것을 방지함을 보여줍니다.
8. 참고 문헌:
본 논문에는 공식적인 번호가 매겨진 참고 문헌 목록이 포함되어 있지 않습니다. 다음 기관들이 지원에 대해 감사를 받았습니다:
- NCR (Scotland)
- Johnston Engineering & Castings
- CEGELEC
- Barton Aluminium
- Compomotive 73
9. 저작권:
- 이 자료는 "Mark R Jolly"의 논문입니다. "[Examples of Practical Solutions for Aluminium Castings using Quiescent Running Systems and Computer Modelling]"을 기반으로 합니다.
- 논문 출처: https://www.researchgate.net/publication/281816640_Examples_of_Practical_Solutions_for_Aluminium_Castings_using_Quiescent_Running_Systems_and_Computer_Modelling (DOI: 10.13140/RG.2.1.4121.3529)
이 자료는 위 논문을 바탕으로 요약되었으며, 상업적 목적의 무단 사용을 금지합니다.
Copyright © 2025 CASTMAN. All rights reserved.
논문 요약:
연구에 대한 핵심 질문과 답변:
이 연구는 실제 설계 규칙과 컴퓨터 시뮬레이션을 결합하는 것이 고품질 알루미늄 주물을 생산하기 위한 효과적인 해결책을 어떻게 제공하는지 보여줍니다. ATM 하우징, 히트 싱크, 자동차 휠 등 세 가지 산업 사례 연구를 통해 이 접근 방식이 난류, 기공, 충전 문제와 같은 결함을 예측하고 해결할 수 있음을 입증합니다. 핵심 결론은 시뮬레이션으로 검증된 적절하고 정온한 충전 시스템 설계가 중요하며, 종종 압탕 공급 고려 사항보다 더 중요하다는 것입니다.
Q1. 논문에서 주물 품질에 가장 중요한 영향을 미치는 요인으로 무엇을 꼽았습니까?
A1. 논문은 용탕이 주형 캐비티로 처리되고 분배되는 방식을 "주물의 품질과 특성에 영향을 미치는 가장 중요한 단일 요소"로 식별합니다. (출처: "Examples of Practical Solutions for Aluminium Castings using Quiescent Running Systems and Computer Modelling", 서론).
Q2. 고품질 주물에 정온(난류 없는) 충전이 필수적인 이유는 무엇입니까?
A2. 정온 충전은 고품질 주물의 전제 조건입니다. 왜냐하면 난류 충전은 사용되는 합금에 관계없이 슬래그 결함, 광택 탄소막, 혼입된 기포, 모래 혼입과 같은 대부분의 결함의 원인이기 때문입니다. (출처: "Examples of Practical Solutions for Aluminium Castings using Quiescent Running Systems and Computer Modelling", 서론).
Q3. 사례 연구 2(히트 싱크 주물)에서 초기 금형 주조 방식이 실패한 이유는 무엇입니까?
A3. 초기 방식은 난류 충전으로 인해 공기가 혼입되었고, 주물 내의 스테인리스 스틸 튜브가 가열되어 단열재 역할을 하며 중앙에 "거대한 고온점"을 형성했기 때문에 실패했습니다. 이는 적절한 압탕 공급을 방해하여 큰 기포와 허용할 수 없는 수준의 기공을 초래했습니다. (출처: "Examples of Practical Solutions for Aluminium Castings using Quiescent Running Systems and Computer Modelling", 사례 연구 2).
Q4. 히트 싱크 주물의 기공 문제에 대한 해결책은 무엇이었습니까?
A4. 해결책은 제조 공정을 금형 주조에서 사형 주조로 변경하는 것이었습니다. 이를 통해 더 긴 충전 시간을 확보하고 더 유리한 온도 구배를 형성하여 방향성 응고를 가능하게 하고 주물에 적절한 압탕 공급이 이루어지게 하여 기공을 제거할 수 있었습니다. (출처: "Examples of Practical Solutions for Aluminium Castings using Quiescent Running Systems and Computer Modelling", 사례 연구 2).
Q5. 사례 연구 3에서 컴퓨터 시뮬레이션은 저압 자동차 휠을 개선하는 데 어떻게 도움이 되었습니까?
A5. 시뮬레이션은 불량의 원인이었던 스포크-림 접합부의 수축 기공과 허브의 미세 기공을 정확하게 예측했습니다. 시뮬레이션을 바탕으로 스포크-림 기공은 냉각 핀을 추가하여 줄였고, 허브 기공은 약간의 형상 변경을 통해 감소시켰습니다. (출처: "Examples of Practical Solutions for Aluminium Castings using Quiescent Running Systems and Computer Modelling", 사례 연구 3).
Q6. "처음부터 올바른" 주조 공정을 개발하는 것에 대한 논문의 주된 결론은 무엇입니까?
A6. 논문은 최종적인 "규칙집"은 존재하지 않지만, 정교한 주조 시뮬레이션 도구를 사용하면 컴퓨터 상에서 시행착오를 수행할 수 있다고 결론 내립니다. 이는 비싼 금형을 제작하기 전에 올바른 제조 경로와 난류 없는 충진 시스템 설계를 결정하는 데 도움이 되어 공정을 처음부터 올바르게 수행할 수 있게 합니다. (출처: "Examples of Practical Solutions for Aluminium Castings using Quiescent Running Systems and Computer Modelling", 결론).