본 소개 자료는 "[SAE International]"에서 발행한 논문 "[The Application of Magnesium Die Casting to Vehicle Closures]"을 기반으로 작성되었습니다.
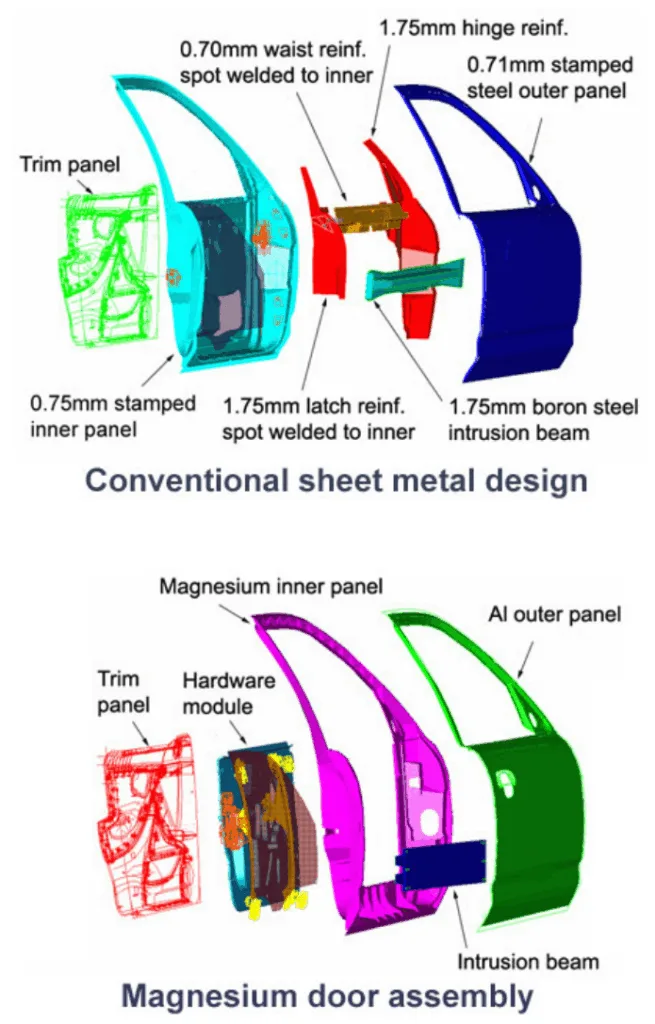
1. 개요:
- 제목: The Application of Magnesium Die Casting to Vehicle Closures (마그네슘 다이캐스팅의 차량 클로저 적용)
- 저자: Patrick J. Blanchard, Gregory T. Bretz, Saravanan Subramanian and James E. deVries (Ford Motor Company); Andrew Syvret, Andrew MacDonald and Peter Jolley (Aston Martin)
- 발행 연도: 2005
- 발행 학술지/학회: SAE International
- 키워드: 논문에 명시되지 않음.
2. 초록:
지난 10년간 마그네슘 다이캐스팅 기술의 발전으로 대형 경량 박벽 다이캐스팅 부품 생산이 가능해졌으며, 이는 저투자 차체 구조 기술에 새로운 접근법을 제시합니다. 그 결과, 많은 OEM 업체들이 투자 절감 기회와 최대 50%의 잠재적 중량 절감 효과로 인해 마그네슘 도어 클로저 시스템에 관심을 표명해 왔습니다. 그러나 이러한 적용 분야에서 제품 엔지니어들은 단련 판재 제품에 비해 탄성 계수와 연성이 낮은 재료를 사용하여 충돌이 중요한 응용 분야에서 강성과 강도를 위한 설계라는 과제에 직면합니다. 사이드 도어 시스템에 대한 개념 설계가 문헌에 제시되었으며, 구조적 성능 목표를 달성할 수 있음을 나타냅니다. 그러나 현재까지 양산 설계는 구조적 하중을 처리하기 위해 다이캐스팅에 부착된 다수의 보조 판금 보강재를 특징으로 합니다. 이 접근 방식은 여전히 성능상의 이점을 제공할 수 있지만, 추가적인 툴링 및 조립 비용은 전체 중량과 사업 타당성 모두에 부정적인 영향을 미칩니다. 반대로, 본 논문에 제시된 마그네슘 도어 개념은 단일 마그네슘 다이캐스팅으로 판금 스탬핑 부품의 대부분을 대체하도록 설계된 사이드 도어 시스템 개발을 설명합니다. 설계, 분석, 프로토타이핑 및 테스트 단계 요약과 함께 2004년형 차량용 양산 도어 시스템 개발이 보고됩니다. 제조 및 테스트 결과 검토는 마그네슘이 저투자 경량 차량 클로저 제조에 효과적으로 사용될 수 있음을 보여줍니다.
3. 서론:
차량 질량이 연비에 미치는 영향은 잘 알려져 있으며 기업 평균 연비 향상을 위한 중요한 요소로 간주됩니다. 실제로 1980년대 초 차량 연석 중량이 평균 20% 감소하면서 상당한 개선이 보고되었습니다 [1]. 그러나 차량 모델에 새로운 기능과 편의성을 추가하는 추세가 계속되면서 중량 목표는 이제 더 큰 압박을 받고 있습니다. 결과적으로 OEM 업체들은 비용을 통제하면서 소비자 요구를 충족시키기 위해 광범위한 재료와 공정을 검토해 왔습니다. 경우에 따라 강철을 알루미늄으로 단순 대체하기도 했습니다 [2]. 그러나 알루미늄 합금의 성형 한계는 종종 그 적용을 제한합니다. 이를 극복하기 위해 스탬핑, 압출 및 주조를 결합한 하이브리드 도어 시스템이 개발되었습니다. 그러나 최종 중량 이점은 조립 복잡성 및 가변 비용 증가로 쉽게 상쇄될 수 있습니다.
반면, 마그네슘은 많은 자동차 응용 분야에서 성공적으로 사용되어 왔습니다. 낮은 밀도와 높은 강도 대 중량비를 포함한 특성은 마그네슘을 부품 질량 감소에 매력적인 재료로 만듭니다. 결과적으로 지난 10년 동안 여러 구조용 주물이 보고되었으며, 더 크고 복잡한 다이캐스팅이 시연됨에 따라 적용 범위가 증가하고 있습니다 [3,4]. 여러 프로그램의 초점이 되어온 특정 응용 분야 중 하나는 다이캐스트 차량 클로저 패널 개발입니다 [5,6,7]. 이러한 제안 중 다수는 개념으로 남아 있지만, 리프트게이트 및 사이드 도어의 생산 버전이 등장했습니다 [6]. 이 중 가장 주목할 만한 것은 메르세데스가 CL 및 SL 모델에 구현한 것입니다. 그러나 마그네슘 주물의 하중을 제한하고 구조적 요구 사항을 충족시키기 위해 도어 어셈블리에 보조 보강재를 고정하는 일반적인 추세는 여전히 남아 있습니다. 이는 다시 전체 중량 및 조립 비용에 부정적인 영향을 미칠 수 있습니다.
본 논문은 주요 보강재를 다이캐스팅에 통합하여 보조 스탬핑을 제거하도록 설계된 새로운 마그네슘 도어 내부 패널 개발에 중점을 둡니다. 따라서 마그네슘 패널은 도어 구조의 필수적인 부분이 되어 차량의 정적 및 동적 충돌 성능에 기여합니다. 초기 개념에 대한 설계, 분석 및 테스트 요약이 제시되고, 이어서 MY2004 애스턴 마틴 DB9에 구현된 생산 의도 도어 시스템 개발이 이어집니다. 두 설계 모두에 대한 최종 중량 평가와 함께 기존 강철 스탬핑 대비 기술 비용을 파악하기 위한 경제성 분석이 제공됩니다.
4. 연구 요약:
연구 주제의 배경:
자동차 산업은 연비 향상과 성능 개선을 위해 차량 질량 감소에 대한 지속적인 압박에 직면해 있습니다. 마그네슘 다이캐스팅 기술은 특히 차량 클로저용으로 대형, 경량, 박벽 부품을 생산할 수 있는 유망한 방법을 제공하며, 투자 절감 및 상당한 중량 절감 가능성을 가지고 있습니다. 그러나 충돌이 중요한 응용 분야에 마그네슘을 설계하려면 기존 강철에 비해 낮은 탄성 계수와 연성을 해결해야 합니다.
이전 연구 현황:
이전 연구에는 달성 가능한 구조적 성능을 나타내는 마그네슘 사이드 도어 시스템에 대한 개념 설계가 포함됩니다. 그러나 기존의 양산 설계는 종종 구조적 하중을 관리하기 위해 다이캐스팅에 부착된 수많은 보조 판금 보강재를 통합합니다. 이 접근 방식은 일부 이점을 제공하지만 비용, 복잡성 및 중량을 추가하여 전반적인 이점을 감소시킵니다. 마그네슘 클로저의 주목할 만한 예로는 메르세데스 CL 및 SL 모델의 클로저가 있으며, 이들 역시 보강재를 사용하는 경향이 있습니다.
연구 목적:
본 연구의 주요 목적은 주요 보강재를 다이캐스팅 자체에 통합하여 보조 스탬핑의 필요성을 제거하는 새로운 마그네슘 도어 내부 패널을 개발하는 것이었습니다. 본 연구는 마그네슘 패널이 도어 구조의 필수적인 부분으로 작용하여 정적 및 동적 충돌 성능에 기여할 수 있음을 입증하는 것을 목표로 했습니다. 구체적인 목표는 다음과 같습니다.
- 초기 개념의 설계, 분석, 프로토타이핑 및 테스트 요약.
- MY2004 애스턴 마틴 DB9용 양산 도어 시스템 개발 상세 설명.
- 두 설계 모두에 대한 중량 평가 제공.
- 기존 강철 스탬핑 대비 기술 비용을 파악하기 위한 경제성 분석 수행.
핵심 연구:
본 연구는 두 가지 주요 단계로 수행되었습니다.
- 개념 검증 (포드 컨투어 기반): 이 단계에서는 MY2000 포드 컨투어를 기반으로 한 마그네슘 도어 아키텍처를 개발하고 평가했습니다. 여기에는 CAE를 사용한 설계, 중력 사형 주조를 통한 프로토타입 제작, 정적 내구성 테스트, 생산을 위한 고압 다이캐스팅을 가정한 사업 타당성 개발이 포함되었습니다.
- 생산 구현 (애스턴 마틴 DB9): 개념 평가 후, MY2004 애스턴 마틴 DB9용 생산 의도 도어 설계가 개발되었습니다. 이 단계는 충돌 성능과 부식 방지에 중점을 두었습니다. 생산 다이캐스팅 금형이 제작되었고, 제조 검증 및 주기적 부식 테스트를 포함한 포괄적인 테스트를 위해 부품이 생산되었습니다.
5. 연구 방법론
연구 설계:
본 연구는 두 단계의 개발 접근 방식을 따랐습니다.
- 1단계: 개념 검증 (포드 컨투어):
- 완전 프레임형 사이드 도어 어셈블리(MY2000 포드 컨투어) 기반 설계.
- 중력 사형 주조를 사용한 프로토타입 제작.
- 정적 내구성에 대한 CAE와 프로토타입 테스트 조합을 통한 기술 평가.
- 고압 다이캐스팅을 위한 사업 타당성 개발.
- 2단계: 구현 (애스턴 마틴 DB9):
- MY2004 애스턴 마틴 DB9용 생산 의도 도어 설계 개발.
- 충돌 성능 및 부식 방지에 중점.
- 생산 다이캐스팅 금형을 사용한 부품 제조.
- 보호 시스템 평가를 위한 주기적 부식 테스트.
데이터 수집 및 분석 방법:
- 컴퓨터 지원 공학 (CAE): 유한 요소 모델을 사용하여 강성(비틀림, 측면 강성, 처짐, 드롭오프) 및 비선형 충돌 분석(예: FMVSS-214 측면 충돌)을 포함한 주요 하중 조건에 대한 시스템 응답을 시뮬레이션했습니다.
- 프로토타입 테스트:
- 포드 컨투어 프로토타입에 대한 정적 내구성 테스트: 비틀림 강성, 프레임 측면 강성, 도어 드롭오프, 도어 처짐 및 도어 슬램(84,000 사이클).
- 실험적 검증 (애스턴 마틴 DB9):
- 특정 위치에서 채취한 서브사이즈 인장 시험편(ASTM E8)을 사용하여 다이캐스트 도어 내부 패널에서 국부 변형률 데이터 획득.
- 실차 측면 충돌 테스트(정적 FMVSS-214).
- 부식 테스트: 알루미늄 쿠폰에 접합된 주조 마그네슘 샘플에 대한 주기적 부식 테스트(포드 테스트 방법 BI123-01, 100 사이클)를 통해 다양한 표면 전처리 및 코팅 평가.
- 치수 분석: 공정 개발 중 생산된 다이캐스팅 측정하여 공차 준수 여부 평가.
- 경제성 평가: 다양한 생산량 시나리오(저 자동화/투자 및 고 자동화/투자)에 대해 마그네슘 도어 어셈블리의 총 비용과 기존 강철 스탬핑 비교.
연구 주제 및 범위:
- 주요 주제: 차량 클로저, 특히 사이드 도어에 대한 마그네슘 다이캐스팅 기술 적용.
- 주요 조사 분야:
- 강성, 강도 및 충돌 내구성을 위한 마그네슘 다이캐스트 도어 내부 패널 설계.
- 부품 수 및 조립 복잡성 감소를 위한 다이캐스팅에 보강재 통합.
- 기존 강철 도어 대비 달성 가능한 중량 감소.
- 대형 박벽 마그네슘 다이캐스팅의 제조 가능성 및 과제.
- 이종 금속 어셈블리에서 마그네슘에 적합한 부식 방지 시스템 평가 및 선택.
- 다양한 생산량에서 마그네슘 다이캐스트 도어의 경제적 실행 가능성.
- 범위: 본 연구는 초기 개념(포드 컨투어 기반)에서부터 소량 생산 고급 차량(애스턴 마틴 DB9)에 구현된 생산 의도 설계까지의 개발 과정을 포괄했습니다.
6. 주요 결과:
주요 결과:
포드 컨투어 개념 단계:
- 중량 감소: 마그네슘 도어 어셈블리(9.62kg)는 기존 스탬핑 강철 설계(15.56kg)에 비해 5.94kg(38%)의 중량 감소를 달성했습니다 (Table 1). 마그네슘 내부 패널과 하드웨어 모듈은 5.83kg으로, 모든 보강재를 포함한 8.09kg의 강철 내부 패널보다 28% 가벼웠습니다.
- 강성 이점: 마그네슘 내부 패널의 높은 강성 덕분에 외부 패널에 저밀도 알루미늄/플라스틱 라미네이트를 사용할 수 있었으며, 이는 중량 절감에 크게 기여했습니다 (강철 외부 패널 대비 3.67kg).
- 성능 테스트 (Table 2):
- CAE 예측은 5가지 주요 테스트 사양을 모두 준수함을 나타냈습니다.
- 실험 테스트 결과 비틀림 강성에서 실패(실제 5.7mm vs. 요구사항 <4mm)하고 예측보다 높은 도어 처짐(실제 13.3mm vs. CAE 5.4mm)이 나타났지만, 여전히 사양(<38mm) 내였습니다. 이러한 불일치는 프로토타입 힌지 핀 간극과 프로토타입 힌지의 소성 변형 때문인 것으로 분석되었습니다.
- 도어 슬램 내구성 테스트는 성공적이었으며, 84,000 사이클(수명 3배) 후 손상이 없었습니다.
- 경제성 분석 (Figure 4 & 5):
- 낮은 생산량(예: 연간 10,000대)에서 마그네슘 도어 어셈블리는 주로 부품 통합 및 툴링 투자 감소로 인해 강철 대응 부품보다 13% 저렴했습니다.
- 강철 스탬핑이 더 비용 효율적이 되는 손익분기점은 연간 약 30,000대였습니다.
- 재료 가격(기준 $2.90/kg)과 기계 가동률이 비용에 영향을 미치는 주요 요인으로 파악되었습니다.
애스턴 마틴 DB9 구현 단계:
- 설계: 모듈식 아키텍처가 아닌 프레임리스 도어 시스템이 개발되었습니다. 외부 벨트 보강재를 포함한 주요 보강재가 다이캐스트 내부 패널에 통합되었습니다.
- 중량 절감:
- 프로토타입 애스턴 마틴 DB9 도어 내부 패널은 3.711kg이었으며(Table 3), 이는 총 도어-인-화이트 어셈블리 중량 9.749kg에 기여했습니다.
- 다이 충진을 위한 추가 분석으로 국부적인 두께 증가가 이루어져 최종 마그네슘 내부 패널 중량은 4.32kg이 되었습니다.
- 최종 DB9 도어 어셈블리는 동등한 스탬핑 강철 어셈블리 대비 43%의 중량 절감을 제공할 것으로 예상되었습니다.
- 정적 내구성 (Figure 8): 벽 두께는 CAE 및 다이캐스팅 충진 시뮬레이션을 기반으로 최적화되었습니다. 예를 들어, 상부 힌지 부착 영역(섹션 5)에서 벽 두께를 20% 증가시키면 도어 드롭 변형에 대한 강성이 36.4% 증가했습니다.
- 충돌 성능 (AM50 합금):
- CAE 시뮬레이션(FMVSS-214) 결과 도어 어셈블리가 요구 사항을 훨씬 초과할 것으로 나타났습니다 (Figure 10).
- 다이캐스트 샘플에 대한 실험적 인장 테스트 결과 평균 파단 변형률이 요구 사항을 초과했습니다: 래치, 빔 부착 및 웨이스트 레일 영역에서 >15%, 힌지 영역에서 최대 28%. 로커 영역은 평균 8%를 보였습니다 (Figure 11).
- 실차 정적 FMVSS-214 측면 충돌 테스트 결과 6인치 램 변위에서 97%, 12인치에서 87%, 18인치에서 60%로 요구 사항을 초과하는 성능을 보였습니다 (Figure 12). 연성 거동이 관찰되었습니다.
- 치수 관리 (Figure 13): 전반적인 공차는 일반적으로 +/- 0.5mm로 유지되었습니다. 양산 전 내부 패널의 경우 측정된 22개 지점 중 21개가 사양을 충족했습니다. 한 위치는 0.039mm 벗어났으며, 이는 추가적인 다이캐스팅 공정 조정을 통해 해결되었습니다.
- 부식 방지:
- 상도 코팅된 양극 산화 처리 기본층이 가장 효과적인 보호 기능을 제공했습니다.
- 에폭시-폴리에스터 분체 도료와 결합된 크롬 기반 전환 코팅은 거의 비슷한 성능을 보였으며 비용 고려 사항으로 인해 사용하도록 선택되었고, 크롬 프리 시스템으로의 계획된 전환이 예정되어 있었습니다.
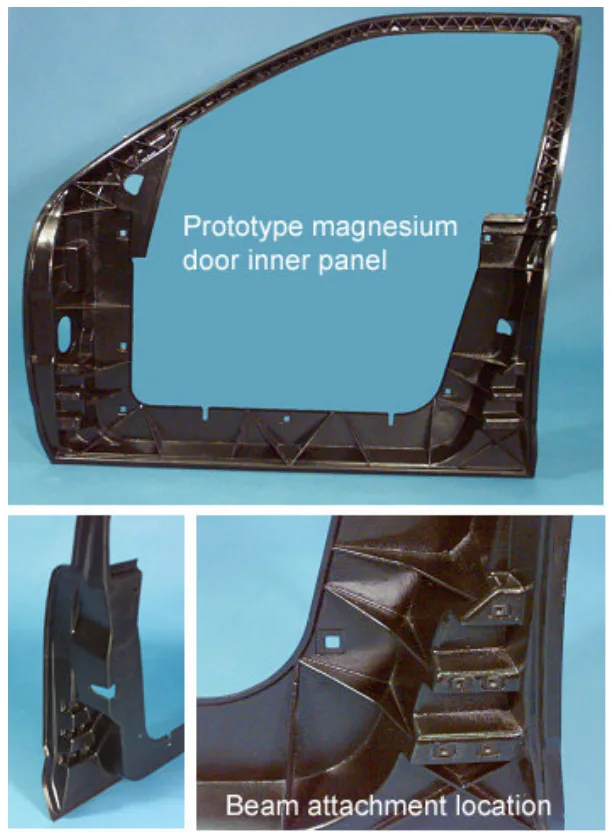
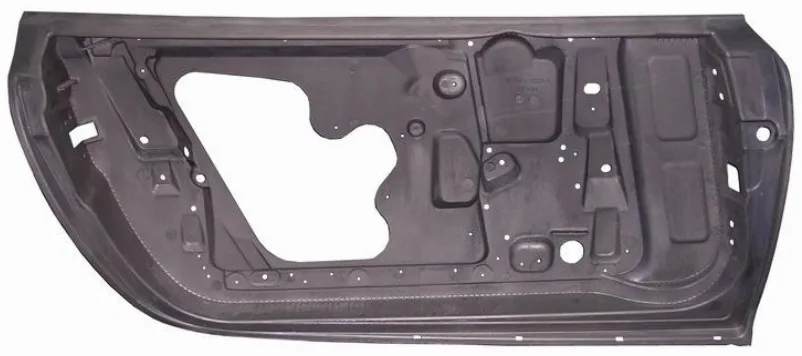
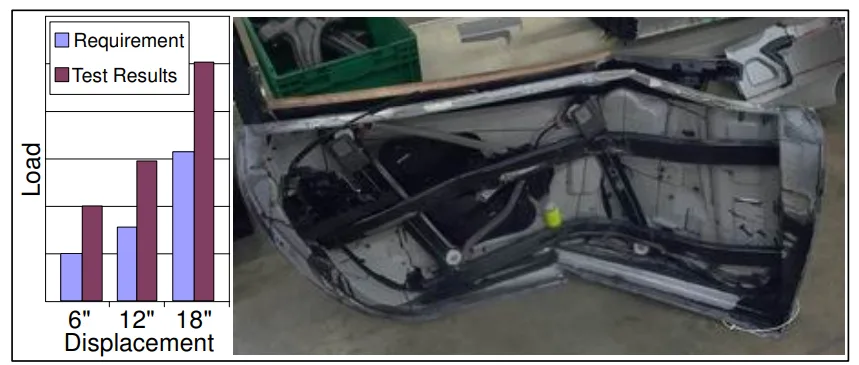
그림 이름 목록:
- Figure 1. Lightweight magnesium door architecture.
- Figure 2. Casting section thickness variations magnesium door inner panel.
- Figure 3. Magnesium door inner panel prototype based upon the MY2000 Ford Contour
- Figure 4. Economic comparison of conventional and magnesium door assemblies for the MY2000 Ford Contour.
- Figure 5. Sensitivity analysis of piece cost to model input data.
- Figure 6. Aston Martin DB9 magnesium door assembly.
- Figure 7. Aston Martin DB9 magnesium door inner panel.
- Figure 8. The effect of wall thickness on door drop off.
- Figure 9. FMVSS 214 test setup.
- Figure 10. Strain map of a preliminary magnesium door inner panel design following static FMVSS-214 testing.
- Figure 11. Mean tensile failure strains of castings by location (see Figure 10).
- Figure 12. FMVSS-214 side impact results for the DB9 magnesium door assembly.
- Figure 13. Dimensional data for a pre-production DB9 magnesium die cast door inner panel.
7. 결론:
이 두 단계 개발 프로그램의 결과는 마그네슘 다이캐스팅이 사이드 도어 어셈블리 내에서 완전한 구조 부재로 효과적으로 사용될 수 있음을 보여줍니다. 주요 기능을 통합한 단일 마그네슘 주물로 여러 금속 스탬핑 부품을 대체함으로써 상당한 이점을 얻을 수 있었습니다. 여기에는 부품 수 감소로 인한 하위 어셈블리 공정 단순화와 툴링 투자 감소가 포함됩니다. 또한 이 접근 방식은 성능과 중량 모두에 대해 설계를 최적화할 수 있는 기회를 제공합니다. 애스턴 마틴 DB9 도어 인 화이트 어셈블리의 예상 중량 절감 효과는 43%였습니다.
경제성 평가는 중저 생산량의 파생 프로그램의 경우 이 마그네슘 다이캐스팅 기술이 비용 불이익 없이 이점을 제공할 수 있음을 나타냈습니다. 그러나 대량 생산 차량의 경우 기존의 스탬핑 강철 어셈블리가 가장 비용 효율적인 제조 경로로 남아 있습니다. 두 제조 기술의 정확한 손익분기점을 결정하려면 특정 대상 응용 분야에 대한 상세한 분석이 필요합니다.
8. 참고문헌:
- [1] http://www.nhtsa.dot.gov/cars/rules/cafe/NewPassengerCarFleet.htm.
- [2] Seksaria, D.C. and R.K. Patel. "An Ultra-Light Thin Sliding Door Design - A Multi Product Multi Material Solution." SAE Technical Paper Series, 2002-01-0391.
- [3] Balzer, J., et al. "Structural Magnesium Front End Support Assembly." SAE Technical Paper Series, 2003-01-0186.
- [4] Friedrich, H. and S. Schumann, "Research for a "new age in magnesium" in the automotive industry." Journal of Materials Processing Technology, 2001. 117(3): p. 276-281.
- [5] Jonason, P., et al. "MAGDOOR- Magnesium in Structural Application." SAE Technical Paper Series,1999-01-3198.
- [6] Schreckenberger, H., M. Papke, and S. Eisenberg. "The Magnesium Hatchback of the 3-Liter Car: Processing and Corrosion Protection." SAE Technical Paper Series, 2000-01-1123.
- [7] "Design of a magnesium/aluminum door frame", Automotive Engineering, 1993, Vol 101, 5,pp 57-60.
- [8] Federal Motor Vehicle Safety Standard 214, Side Impact Protection.
- [9] Ames, W. and W. Altenhof. "Observations of the Relative Performance of Magnesium and Aluminum Steering Wheel Skeletons with Identical Geometry." SAE Technical Paper Series, 2000-01-0784.
- [10] Aune, T. and L. Riopelle. "An Evaluation of the Mechanical Properties Critical to the Design of Interior Magnesium Components." SAE Technical Paper Series, 960415.
- [11] Alain, R. et al. "Robustness of Large Thin Wall Magnesium Die Castings for Crash Applications." SAE Technical Paper Series, 2004-01-0131.
- [12] Ford Laboratory Test Method BI 123-01. "Painted Sheet Metal Corrosion Test (Laboratory Simulated Arizona Proving Ground Test)", 2001.
- [13] Bretz, G.T., et al. "Adhesive Bonding and Corrosion Protection of a Die Cast Magnesium Automotive Door." The Minerals, Metals and Materials Society. 2004: Magnesium Technology 2004.
- [14] Blanchard, P.J., et al. "Evaluation of Corrosion Protection Methods for Magnesium Alloys in Automotive Applications." The Minerals, Metals and Materials Society, Magnesium Technology 2005.
9. 저작권:
- 본 자료는 "[Patrick J. Blanchard, Gregory T. Bretz, Saravanan Subramanian, James E. deVries, Andrew Syvret, Andrew MacDonald and Peter Jolley]"의 논문입니다. "[The Application of Magnesium Die Casting to Vehicle Closures]"을 기반으로 합니다.
- 논문 출처: [https://doi.org/10.4271/2005-01-0338]
본 자료는 위 논문을 바탕으로 요약되었으며, 상업적 목적의 무단 사용을 금합니다.
Copyright © 2025 CASTMAN. All rights reserved.