이 소개 자료는 "[IOP Conference Series: Materials Science and Engineering]"에 게재된 "Multi-scale simulation of hybrid light metal structures produced by high pressure die casting" 논문을 기반으로 합니다.
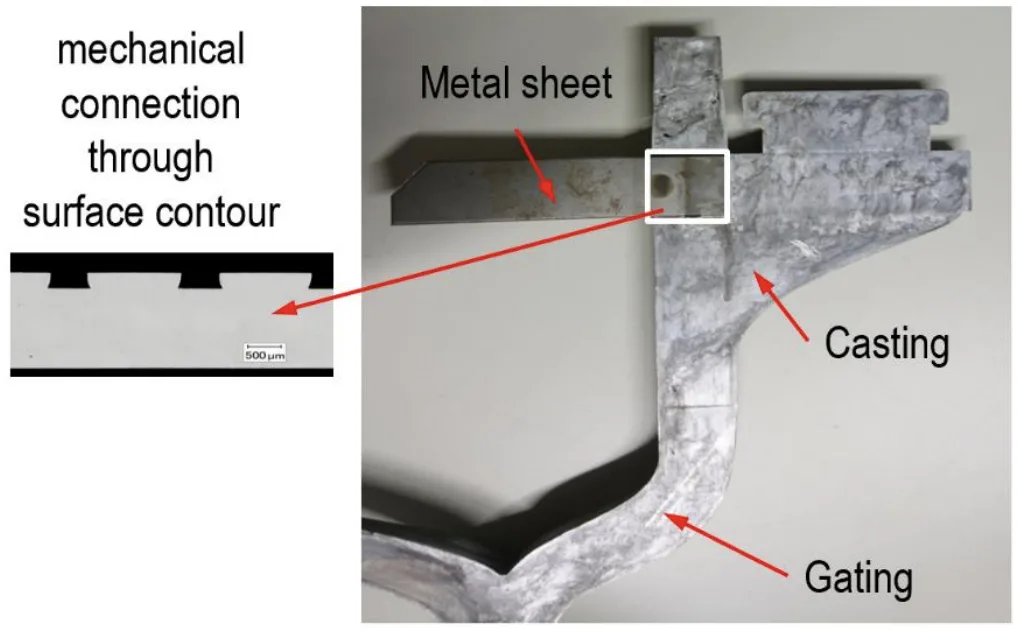
1. 개요:
- 논문 제목: Multi-scale simulation of hybrid light metal structures produced by high pressure die casting
- 저자: J Jakumeit¹, H Behnken¹, R Laqua¹, J Eiken¹ and J Brachmann²
- 발행 연도: 2020
- 게재 학술지/학회: IOP Conference Series: Materials Science and Engineering
- 키워드: 논문에 명시되지 않음
2. 초록:
최신 자동차 구조 부품에서는 경량이면서 기계적으로 안정적인 구조를 구현하기 위해 금속 판재와 주조 부품을 결합합니다. 본 연구에서는 강철 판재와 알루미늄 주조 부품 간의 접합이 고압 다이캐스팅(HPDC) 공정의 일부로 수행됩니다. 이러한 방식으로 용접과 같은 추가적인 접합 단계를 생략할 수 있어 시간과 에너지를 절약할 수 있습니다. 판재와 주물의 결합은 판재의 구조화된 표면(rib)을 통해 이루어지며, 이는 주조 공정 중 액상 알루미늄 합금으로 채워져 응고 후 기계적 연결을 형성합니다. 결합된 유동 및 응고 시뮬레이션을 사용하여 하이브리드 주조 공정을 분석하며, 특히 rib 내부의 급속 응고에 초점을 맞춥니다. 판재와 알루미늄 합금 사이 계면의 고해상도(mesoscale) 충진 및 응고 시뮬레이션은 용탕 유동 및 급속 응고의 세부 사항을 포착할 수 있습니다. Mesoscale 유동 및 응고 시뮬레이션을 microscale에서의 다상장(multiphase field) 시뮬레이션과 연계함으로써 결과적인 미세조직을 계산할 수 있습니다. Mesoscale 시뮬레이션 결과로서 rib 내부의 응고 조건은 콜드챔버 HPDC 장비에서 수행된 실제 주조품에서 발견된 실험 결과와 계산된 미세조직을 비교함으로써 검증될 수 있습니다.
3. 서론:
고압 다이캐스팅(HPDC)은 특히 자동차 산업에서 크고 얇은 벽의 구조 부품을 위한 중요한 제조 공정입니다. HPDC는 복잡한 대형 알루미늄 또는 마그네슘 부품의 제조를 가능하게 하며, 이는 여러 개의 단조 금속 판재를 용접하여 결합하는 것보다 더 효율적일 수 있습니다. 흥미로운 새로운 응용 분야는 하나의 하이브리드 주조 공정 단계에서 알루미늄 주물과 금속 판재를 결합하는 것입니다. 이러한 방식으로 용접과 같은 추가적인 접합 단계를 생략할 수 있어 시간과 에너지를 절약할 수 있습니다. 판재와 주물의 결합은 판재의 구조화된 표면(rib)을 통해 이루어지며, 이는 주조 공정 중 액상 알루미늄 합금으로 채워져 응고 후 기계적 연결을 형성합니다. 기계적 연결은 접착 연결보다 강하지만 용접 연결보다는 약합니다. 연결 강도에 중요한 것은 금속 판재의 구조화된 표면이 완전히 채워지는 것입니다.
HPDC 충진 공정의 시뮬레이션은 상당한 양의 공기 혼입과 함께 캐비티의 매우 빠르고 혼란스러운 충진 때문에 어렵습니다. 대부분의 상용 시뮬레이션 프로그램은 잔류 공기의 영향을 근사화하기 위해 일부 특수 모델을 사용하여 주조 공정을 설명하는 단상(one-phase) 접근법을 사용합니다[1-4]. 본 연구에서는 공기, 용탕 및 고상(solid phase)을 포함하는 주조 공정의 3상(three-phase) 시뮬레이션이 사용됩니다. 용탕과 공기 모두 압축성 유체로 간주되며, 계면을 선명하게 유지하기 위한 특별한 처리를 포함하는 Volume-of-Fluid(VoF) 접근법으로 분리됩니다. 응고 과정 중 용탕 유동성 감소는 덴드라이트 네트워크를 통한 유동을 설명하기 위해 다공성 매질(porous media) 접근법으로 처리됩니다. 임계 고상 분율 값에서 용탕은 완전히 멈춥니다. 이 접근법은 상용 주조 시뮬레이션 패키지 STAR-CCM+[5]에 구현되어 있습니다. 미충진(misrun)을 유발할 수 있는 공기의 정확한 처리와 빠른 응고는 하이브리드 주조 연구에 중요하다고 여겨지는데, 이는 공기 혼입과 구조화된 금속 판재 표면이 완전히 채워지기 전의 용탕 응고가 판재와 주물 사이의 기계적 결합을 약화시킬 수 있기 때문입니다.
4. 연구 요약:
연구 주제의 배경:
최신 자동차 부품은 경량이면서도 기계적으로 안정적인 구조를 요구합니다. 금속 판재(예: 강철)와 주조 경금속 부품(예: 알루미늄)을 단일 고압 다이캐스팅(HPDC) 공정에서 결합하는 하이브리드 주조는 용접과 같은 전통적인 조립 방법에 비해 시간과 에너지를 절약함으로써 잠재적인 이점을 제공합니다. 이러한 하이브리드 구조의 기계적 연결은 금속 판재에 설계된 구조화된 표면(rib)을 통해 이루어지며, 이는 주조 중 용융 합금에 의해 채워집니다.
이전 연구 현황:
복잡한 HPDC 공정, 특히 급속 충진 및 잠재적인 공기 혼입을 시뮬레이션하는 것은 어렵습니다. 많은 상용 코드는 단상 근사치를 사용하지만, 공기, 용탕 및 고상을 고려하는 다상 접근법은 더 상세한 설명을 제공합니다. Volume-of-Fluid(VoF) 방법과 같은 기술은 자유 표면 추적에 사용되며, 다공성 매질 모델과 유동 정지 기준을 결합하여 응고가 유체 유동에 미치는 영향을 시뮬레이션합니다.
연구 목적:
본 연구는 멀티스케일 시뮬레이션 접근법을 사용하여 하이브리드 HPDC 공정을 분석하는 것을 목표로 하며, 특히 금속 판재 표면의 작은 스케일 rib 내에서 발생하는 용탕 유동, 충진 동역학 및 급속 응고에 초점을 맞춥니다. 주요 목표는 하이브리드 접합부의 기계적 무결성에 중요한 rib의 완전한 충진에 영향을 미치는 요인을 이해하는 것입니다. 또한, 이 연구는 rib 내에서 예측된 미세조직을 실제 주조품의 실험적 관찰 결과와 비교하여 시뮬레이션 결과를 검증하고자 합니다.
핵심 연구:
연구의 핵심은 멀티스케일 시뮬레이션 전략을 포함합니다. 먼저, 전체 HPDC 공정의 macroscale 시뮬레이션은 후속 고해상도 mesoscale 시뮬레이션을 위한 현실적인 경계 조건(용탕 속도 및 온도)을 제공합니다. 이 mesoscale 시뮬레이션은 강철 판재와 알루미늄 합금(Al-5wt%Mg-1.8wt%Si) 사이의 rib이 있는 계면 영역에 특히 초점을 맞춥니다. 0.2 x 0.2 mm rib 내의 상세한 충진 및 응고 거동을 포착하기 위해 3상(공기, 용탕, 고상) VoF 모델을 사용합니다. Mesoscale 시뮬레이션에서 예측된 열 조건(냉각 속도)은 예상되는 미세조직을 계산하기 위해 microscale 상-장(phase-field) 시뮬레이션(MICRESS® 소프트웨어 사용)의 입력으로 사용됩니다. 이 연구는 다양한 공정 변수(유동에 대한 rib 방향, rib 위의 캐비티 두께, 용탕 속도) 및 응고 모델(Scheil 근사 대 상-장 유도 고상 분율 곡선)이 rib 충진 공정에 미치는 영향을 체계적으로 조사합니다. 마지막으로, 시뮬레이션된 미세조직은 검증을 위해 콜드챔버 HPDC 기계에서 생산된 하이브리드 주조품의 실험 결과와 비교됩니다.
5. 연구 방법론
연구 설계:
본 연구는 실험적 검증과 결합된 멀티스케일 시뮬레이션 접근법을 사용했습니다. 전체 HPDC 공정의 macroscale 시뮬레이션은 중요한 rib이 있는 계면의 상세한 mesoscale 시뮬레이션을 위한 경계 조건을 제공했습니다. Mesoscale 시뮬레이션 결과(특히, 국소 응고 조건)는 결과적인 미세조직을 예측하기 위해 microscale 상-장 시뮬레이션의 입력으로 사용되었습니다. 이러한 시뮬레이션 예측은 정의된 조건 하에서 생산된 실험적 하이브리드 주조품에서 관찰된 미세조직과 비교하여 검증되었습니다.
데이터 수집 및 분석 방법:
- 시뮬레이션:
- Macroscale 및 Mesoscale: STAR-CCM+에 구현된 유한 체적법(finite-volume method)이 사용되었습니다. 이는 고해상도 계면 포착(HRIC) 기법을 사용한 3상(공기, 용탕, 고상) Volume-of-Fluid(VoF) 모델을 사용하여 질량, 운동량 및 에너지에 대한 수송 방정식을 푸는 것을 포함합니다. 표면 장력은 Continuum Surface Force(CSF) 모델을 통해 처리되었습니다. 응고는 잠열(L*d(fs(T))/dT)을 방출하기 위해 표로 만들어진 고상 분율 대 온도 곡선(fs(T))을 사용하여 모델링되었습니다. 머시 영역(mushy zone)에서의 유동 저항은 2차 덴드라이트 암 간격(SDAS, λ2)을 통합한 Kozeny-Carman 방정식에 기반한 다공성 매질 접근법을 사용하여 모델링되었습니다. 임계 고상 분율 임계값 이상에서 용탕 유동을 멈추는 유동 정지(flow-stop) 기능이 구현되었습니다. 재료 데이터는 STAR-CCM+ 야금 데이터베이스 및 열역학 계산에서 가져왔습니다.
- Microscale: 상-장 시뮬레이션은 MICRESS® 소프트웨어를 사용하여 박막 계면(thin-interface) 한계에서 수행되었으며, 반-트래핑(anti-trapping) 항과 FD-보정(FD-correction)을 통합했습니다. 액상, fcc-Al 및 Mg2Si 상에 대한 재료 데이터는 TQ-인터페이스를 통해 열역학 데이터베이스 TCA15를 사용하여 평가되었습니다. 공정(eutectic)은 유효 상(effective phase)으로 처리되었습니다.
- 실험: 하이브리드 주조품은 rib 구조 표면을 가진 강철 판재 위에 Al-5wt%Mg-1.8wt%Si 합금을 주조하여 생산되었습니다. Buehler H630-SC HPDC 기계가 특정 공정 변수(주조 온도 680 °C, 최대 피스톤 속도 1 m/s, 금형 예열 200 °C, 증압 압력 200 bar)와 함께 사용되었습니다. 결과 주조품의 rib 영역 미세조직은 시뮬레이션과의 비교를 위해 실험적으로 분석되었습니다.
연구 주제 및 범위:
본 연구는 하이브리드 HPDC 공정 중 강철 판재 위의 0.2 x 0.2 mm rib 내에서 Al-Si-Mg 합금의 충진 및 응고를 시뮬레이션하는 데 중점을 두었습니다. 범위는 다음을 포함합니다:
- 멀티스케일 시뮬레이션 워크플로우(macro-meso-micro) 개발 및 적용.
- Mesoscale 시뮬레이션을 사용하여 rib 내의 용탕 유동 동역학, 온도 변화 및 응고 순서 분석.
- Rib 충진에 대한 공정 변화의 영향 조사, 구체적으로:
- 용탕 유동에 대한 rib의 방향 (평행 대 수직).
- Rib 위의 주조 캐비티 두께 (2 mm 대 5 mm).
- 용탕 유입 속도 (표준 대 4 m/s).
- 응고 모델 (Scheil 근사 대 상-장 시뮬레이션에서 파생된 fs(T) 곡선).
- Mesoscale 결과에 기반한 상-장 시뮬레이션을 사용하여 rib 내 미세조직 예측.
- 시뮬레이션된 미세조직과 실험적 미세조직을 비교하여 mesoscale 시뮬레이션의 예측된 응고 조건 검증.
6. 주요 결과:
주요 결과:
- Mesoscale 시뮬레이션은 차가운 금형 및 판재와의 접촉으로 인해 rib 내부에서 매우 빠른 냉각 속도(~5000 K/s)와 응고를 나타냈으며, rib 바로 위의 용탕은 훨씬 느리게(~200 K/s) 냉각되었습니다.
- Rib의 완전한 충진은 공정 후반부에, 주로 주 캐비티가 대부분 채워진 후 압력 상승 단계(시뮬레이션된 경우 약 60 ms)에 의해 구동되는 것으로 밝혀졌습니다.
- 상-장 시뮬레이션에서 파생된 더 현실적인 고상 분율 곡선(20 K 과냉각 포함)을 사용하면, 더 간단한 Scheil 근사법을 사용하는 것에 비해 응고 시작이 늦어지고 rib 충진이 약간 느려졌습니다.
- 공정 변수는 rib 충진 효율에 상당한 영향을 미쳤습니다(압력 상승 전환 시점에서 비교):
- 주 용탕 유동에 수직(crosswise)으로 배향된 rib은 유동에 평행하게 배향된 rib(98-99%)에 비해 훨씬 덜 효과적으로 채워졌습니다(89%).
- Rib 위의 주조 캐비티 두께를 2 mm에서 5 mm로 늘리면 rib 충진이 급격히 감소하여(16%까지), 두꺼운 섹션에서는 압력 상승이 덜 효과적임을 나타냅니다.
- 용탕 유입 속도를 증가시키면(4 m/s로) rib 충진이 감소했는데(79%까지), 이는 더 빠른 유동이 rib을 채우기보다는 위로 지나가는 경향이 있기 때문입니다.
- Mesoscale 시뮬레이션에서 추출한 열 조건(열 추출률 2x10¹¹ W/m³)을 사용한 Microscale 상-장 시뮬레이션은 핵 생성 밀도 5x10¹⁶ m⁻³를 가정했을 때 실험적 미세조직과 잘 일치하는 미세조직(fcc-Al 및 공정)을 생성했습니다. 이 일치는 mesoscale 모델에 의해 예측된 응고 조건을 검증합니다.
- Figure 2. Simulation of the HPDC process coupling flow, temperature and solidification. After ~0.1 s (b) the critical region below the metal sheet is filled. After 0.2 s (c) the melt in the metal sheet area starts to solidify (green line = points at liquidus temperature).
- Figure 3. (a) Mesoscale geometry of the region below the metal sheet with 0.2 x 0.2 mm ribs and (b) the trimmed fine mesh. The round shape of the region with ribs gives possibility to use different orientations towards the melt flow direction.
- Figure 4. Streamlines showing the movement of the ribs and the temperature of the melt during the filling process after 25 ms.
- Figure 5. Cooling curves at different points inside (negative position) and above the ribs (positive position). The small sketch at the right shows the positions of the data recording points.
- Figure 6. Volume fraction of melt (red) or air (blue) during filling.
- Figure 7. Filling of ribs using different fraction-solid curves, process parameters or geometries (broken lines use Scheil approximation).
- Figure 8. Fraction solid curves from Scheil approximation and phase-field simulation using MICRESS®.
- Figure 9. A series of phase-field simulations were performed under systematic variation of cooling and nucleation conditions. Good agreement between (a) experimental microstructure and (b) simulated microstructure was obtained for an extraction rate of 2×1011 W/m3 and a nucleation density of 5×1016 m-3 .
그림 목록:
- Figure 1. Hybrid HPDC casting with gating system, casting and metal sheet. The metal sheet is connected to the casting by the surface contour of the metal sheet (ribs), which is filled by the melt.
- Figure 2. Simulation of the HPDC process coupling flow, temperature and solidification. After ~0.1 s (b) the critical region below the metal sheet is filled. After 0.2 s (c) the melt in the metal sheet area starts to solidify (green line = points at liquidus temperature).
- Figure 3. (a) Mesoscale geometry of the region below the metal sheet with 0.2 x 0.2 mm ribs and (b) the trimmed fine mesh. The round shape of the region with ribs gives possibility to use different orientations towards the melt flow direction.
- Figure 4. Streamlines showing the movement of the ribs and the temperature of the melt during the filling process after 25 ms.
- Figure 5. Cooling curves at different points inside (negative position) and above the ribs (positive position). The small sketch at the right shows the positions of the data recording points.
- Figure 6. Volume fraction of melt (red) or air (blue) during filling.
- Figure 7. Filling of ribs using different fraction-solid curves, process parameters or geometries (broken lines use Scheil approximation).
- Figure 8. Fraction solid curves from Scheil approximation and phase-field simulation using MICRESS®.
- Figure 9. A series of phase-field simulations were performed under systematic variation of cooling and nucleation conditions. Good agreement between (a) experimental microstructure and (b) simulated microstructure was obtained for an extraction rate of 2x10¹¹ W/m³ and a nucleation density of 5x10¹⁶ m⁻³.
- Table 1. Filling of ribs using different fraction solid curves or process parameter
7. 결론:
3상 결합 유동 및 응고 시뮬레이션은 금속 판재와 주물을 결합하는 하이브리드 고압 다이캐스팅 공정을 분석하는 데 성공적으로 사용되었으며, 기계적 결합에 중요한 rib 내부의 급속 응고에 초점을 맞췄습니다. 고해상도(mesoscale) 시뮬레이션은 macroscale 시뮬레이션의 경계 조건을 사용하여 계면에서의 용탕 유동 및 응고의 세부 사항을 포착했습니다. Mesoscale 시뮬레이션 결과를 다상장 미세조직 시뮬레이션(microscale)과 결합하여 결과적인 미세조직을 계산할 수 있었습니다. 계산된 미세조직과 실험적 분석 간의 양호한 일치는 mesoscale 시뮬레이션이 rib 내부의 응고 조건을 정확하게 예측함을 입증했습니다.
다양한 공정 구성에 대한 체계적인 조사를 통해 다음과 같은 주요 결과를 도출했습니다:
- Rib 위의 압력 상승 단계는 용탕이 rib 안으로 완전히 채워지는 데 중요합니다.
- 용탕의 과냉각(약 20 K, 상-장 결과에 의해 시사됨)은 응고 시작을 늦추고 점도를 증가시켜, Scheil 근사법을 사용한 시뮬레이션에 비해 rib의 빠른 충진을 약간 방해합니다.
- Rib을 용탕 유동에 수직으로 배향하면 평행 배향에 비해 충진이 늦어지는데, 이는 용탕이 rib 안으로 흘러 들어갈 가능성이 적기 때문입니다.
- Rib 위의 주조 캐비티 두께를 늘리면 필요한 압력 상승을 방해하고 rib 충진을 크게 감소시킵니다. 이는 얇은 주물이 두꺼운 부품보다 하이브리드 주조 응용에 더 유리함을 시사합니다.
- 더 높은 용탕 속도 또한 rib 충진을 감소시키는데, 이는 용탕이 rib 안으로 방향을 바꾸기보다는 더 빠른 속도로 rib 위를 흐르는 경향이 있기 때문입니다.
8. 참고 문헌:
- [1] The aluminum automotive manual 2002 (European Aluminium Association) https://www.european-aluminium.eu/media/1526/aam-manufacturing-1-casting-methods.pdf
- [2] Beckermann C and Monroe A 2009 Porosity simulation for high pressure die castings Die Casting Engineer (The North American Die Casting Association) ISSN 0012-25JX
- [3] Bodhayana M R and Ramesha N 2014 Int. J. Res. Eng. Tech. 03 (11) 1163
- [4] Zhu J et al. 2009 MCWASP XII (Warrendale: The Minerals, Metals & Materials Society TMS) 361-8
- [5] Jana S, Kättlitz O, Hediger F, Jakumeit J and Aguilar J 2012 IOP Conf. Ser.: Mater. Sci. Eng. 33 012007
- [6] Ferziger J H and Peric M 2002 Computational Methods for Fluid Dynamics (McGraw-Hill) ISBN 2-540-42074-6.
- [7] Teskeredzic A, Demirdzic I and Muzaferija S 2002 Num. Heat Trans. B 42 43
- [8] Demirdzic I and Muzaferija S 1995 Comput. Method Appl. Mech. Eng. 125 235-55
- [9] Muzaferija S and Peric M 1999 Computation of free surface flows using interface-tracking and interface-capturing methods. In Nonlinear Water Wave Interaction, ed Mahrenholtz O et al. (Southampton: WIP Press) pp 59-100
- [10] Brackbill J U, Kothe D B and Zemach C 1992 J. Comput. Physics 100 335
- [11] Sabau S and Viswanath S 2002 Met. Mat. Trans. B 33B 131
- [12] Poirier D R, Yeum K and Mapples A L 1987 Metall. Mater. Trans. A 18 1979
- [13] MICRESS®, multicomponent multi-phase-field software, www.micress.de
- [14] Eiken J, Böttger B and Steinbach I 2006 Phys. Rev. E 73 066122
- [15] Carré A, Böttger B and Apel M 2013 J. Cryst. Growth 380 5
- [16] Eiken J 2012 Mater. Sci. Eng. 33 012105
- [17] Thermo-Calc Software: http://www.thermocalc.com
9. 저작권:
- 본 자료는 "J Jakumeit 외"의 논문입니다. "Multi-scale simulation of hybrid light metal structures produced by high pressure die casting"을 기반으로 합니다.
- 논문 출처: https://doi.org/10.1088/1757-899X/861/1/012035
본 자료는 상기 논문을 바탕으로 요약된 자료이며, 상업적 목적의 무단 사용을 금합니다.
Copyright © 2025 CASTMAN. All rights reserved.