본 기사에서는 [UNIVERSITÀ DEGLI STUDI DI PADOVA 및 AALEN HOCHSCHULE FÜR TECHNIK UND WIRTSCHAFT]에서 발행한 논문 ["INVESTIGATION ON THE EFFECTS OF INNOVATIVE MELT TREATMENTS ON MICROSTRUCTURE AND MECHANICAL BEHAVIOUR OF DIECAST AL ALLOYS"]를 소개합니다.
1. 개요:
- 제목: INVESTIGATION ON THE EFFECTS OF INNOVATIVE MELT TREATMENTS ON MICROSTRUCTURE AND MECHANICAL BEHAVIOUR OF DIECAST AL ALLOYS
- 저자: Alberto Dal Maso, Prof. Dr. Ing. Lothar H. Kallien, Prof. Ing. Franco Bonollo
- 발행 연도: Academic year 2011 – 2012
- 발행 저널/학회: UNIVERSITÀ DEGLI STUDI DI PADOVA, CORSO DI LAUREA MAGISTRALE IN INGEGNERIA DELL’INNOVAZIONE DEL PRODOTTO
- 키워드: 다이캐스팅, 알루미늄 합금, 용융 처리, 미세 구조, 기계적 거동, Al2O3 입자, 현장 공정
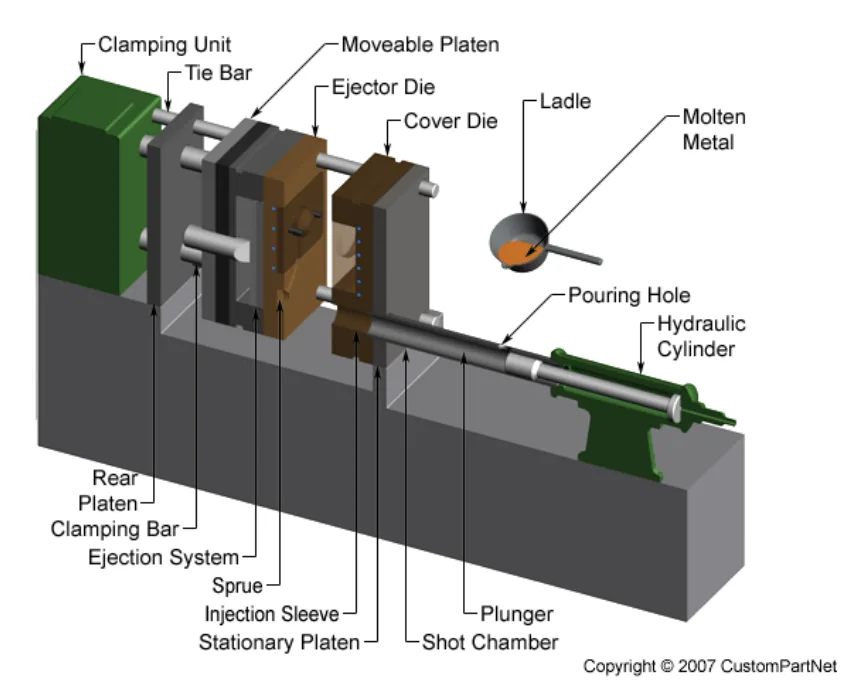
2. 초록 또는 서론
더 나은 성능을 가진 혁신적인 재료에 대한 연구는 여러 분야의 발전에 핵심적인 역할을 합니다. 재료 특성 개선을 위해 가장 흔히 채택되는 전략 중 하나는 상호 작용을 통해 더 나은 성능을 달성하는 상보적인 재료를 결합하는 것이며, 이는 복합 재료 연구의 기본 원리입니다.
금속 매트릭스 복합재료(MMC)는 성능과 다양한 공정 적용 가능성으로 인해 특히 흥미롭습니다. 본 연구에서는 용융 알루미늄에 대한 혁신적인 용융 처리를 조사하여 용융물 내에 분산시키고 응고된 금속에 통합하는 것을 목표로 현장에서 산화알루미늄(Al2O3) 입자를 생성하는 것을 목표로 합니다.
Al2O3를 강화재로 사용하는 것은 알루미늄 합금의 경도, 강도 및 탄성 계수를 향상시키는 기계적 강화재로서, 그리고 더 미세한 미세 구조를 통해 합금 성능을 향상시키는 결정립 미세화제로서의 두 가지 이점을 위해 탐구됩니다. 본 연구에서는 순수 알루미늄과 Al-Cu 합금에 대한 처리 효과를 영구 금형 및 고압 다이캐스팅(HPDC) 모두에서 시험했습니다.
Al, Mg 및 Zn 합금 부품 생산에 중요한 HPDC 공정은 강철 다이에 용융 합금을 고압으로 주입하는 것을 포함합니다. 진공 및 반용융 금속 주조와 같은 HPDC의 최근 발전은 주조 품질을 향상시켰습니다. 강도와 연성으로 알려진 Al-Cu 합금은 석출 경화의 이점을 활용하여 단조 및 주조 형태로 널리 사용됩니다.
그러나 열간 균열 감수성 및 부식 문제가 있습니다. 용융 알루미늄에 아르곤과 산소 주입을 포함하는 용융 처리는 합금 특성과 미세 구조를 향상시키기 위해 Al2O3 입자를 형성하고 분산시키는 것을 목표로 합니다.
3. 연구 배경:
연구 주제 배경:
혁신적인 재료 개발은 공학 분야에서 매우 중요하며, 금속 매트릭스 복합재료(MMC)는 향상된 특성과 다양한 가공성으로 인해 중요성이 커지고 있습니다. 알루미늄 합금, 특히 Al-Cu 합금은 높은 강도와 인성으로 단조 및 주조 응용 분야 모두에서 필수적입니다. 고압 다이캐스팅(HPDC)은 특히 자동차 및 기타 대량 생산 산업에서 Al, Mg 또는 Zn 기반 합금 부품 생산에 필수적인 공정입니다. 다이캐스트 알루미늄 합금의 기계적 특성을 개선하고 결함을 줄이는 것은 지속적인 연구 분야입니다.
기존 연구 현황:
재료 과학 분야의 기존 연구는 복합재료에서 재료를 결합하는 것과 같은 방법을 통해 재료 특성을 향상시키는 데 중점을 두고 있습니다. 세라믹 상, 특히 Al2O3로 강화된 금속 매트릭스 복합재료는 향상된 강도, 경도 및 고온 성능으로 잘 알려져 있습니다. 선행 연구에서는 현장 및 외부 방법을 통해 생산된 Al2O3 강화 MMC를 탐구했습니다. 연구에 따르면 Al2O3 입자는 Al-Cu 합금에서 결정립 미세화제 역할을 하여 열간 균열을 줄일 수 있습니다. 진공 보조 및 반용융 HPDC와 같은 HPDC의 혁신은 결함을 줄이고 부품 품질을 향상시키는 것을 목표로 합니다. 그러나 금속 매트릭스 내에 나노 스케일 강화재를 생성하고 분산시키는 비용 효율적이고 산업적으로 확장 가능한 방법을 생산하는 데에는 여전히 어려움이 있습니다.
연구의 필요성:
HPDC 및 Al-Cu 합금의 발전에도 불구하고 열간 균열 감수성, 기공률 및 내식성과 같은 제한 사항이 지속적으로 존재합니다. 기계적 특성이 향상된 금속 매트릭스 나노 복합재료(MMNC)를 생산하고 낮은 파괴 인성 및 가공성과 같은 한계를 극복하는 것이 주요 연구 분야입니다. 기존의 많은 MMC 생산 방법은 비용이 많이 들고 기존 생산 환경에서 적용하기 복잡합니다. 특히 강도를 개선하고 미세 구조를 개선하며 HPDC와 같은 공정에서 열간 균열 감수성을 잠재적으로 줄일 수 있는 Al2O3와 같은 강화 입자의 현장 생성 및 분산을 통해 다이캐스트 알루미늄 합금의 특성을 향상시키는 저렴하고 효과적인 방법이 필요합니다. 본 연구는 보다 까다로운 구조적 응용 분야에 적합하도록 다이캐스트 알루미늄 합금의 성능을 개선하기 위한 혁신적이고 비용 효율적인 용융 처리의 필요성을 해결합니다.
4. 연구 목적 및 연구 질문:
연구 목적:
주요 연구 목적은 용융 알루미늄 내에서 Al2O3 입자를 현장에서 생성하는 혁신적인 용융 처리의 타당성을 조사하고, 다이캐스트 알루미늄 합금의 미세 구조 및 기계적 거동에 대한 이러한 처리의 효과를 평가하는 것입니다. 여기에는 생성된 Al2O3 입자가 응고된 금속에 유지되는지 여부와 기계적 특성에 미치는 영향 평가가 포함됩니다.
핵심 연구 질문:
- 용융 알루미늄에 아르곤과 산소 가스 혼합물을 주입하는 혁신적인 용융 처리가 Al2O3 입자를 현장에서 효과적으로 생성할 수 있는가?
- 이 용융 처리는 응고 시 유지되는 용융 알루미늄 내 Al2O3 입자의 분산을 유도하는가?
- 이 현장 용융 처리는 순수 알루미늄 및 Al-Cu 합금의 미세 구조에 어떤 영향을 미치는가?
- 용융 처리는 영구 금형 및 HPDC 모두에서 생산된 다이캐스트 순수 알루미늄 및 Al-Cu 합금의 기계적 특성(인장 강도, 항복 강도, 연신율)에 어떤 영향을 미치는가?
- 이 용융 처리는 생산 비용이나 복잡성을 크게 증가시키지 않고 다이캐스트 알루미늄 합금의 특성을 향상시키는 데 실행 가능한 방법이 될 수 있는가?
5. 연구 방법론
연구 설계:
본 연구에서는 혁신적인 용융 처리가 알루미늄 합금에 미치는 영향을 평가하기 위해 실험적 설계를 채택했습니다. 용융 처리에는 교반하면서 용융 알루미늄에 아르곤과 산소 가스 혼합물을 주입하는 것이 포함되었습니다. 실험은 유도 용해로와 탈기 장치를 활용하여 소규모 및 대규모 설정으로 수행되었습니다. 다양한 처리 시간, 가스 유량, 임펠러 크기 및 주조 방법(영구 금형 및 HPDC)을 체계적으로 변화시켜 그 영향을 평가했습니다.
자료 수집 방법:
- 기계적 시험: 영구 금형에서 주조하고 다이캐스트 판에서 가공한 시편에 대해 인장 시험을 수행하여 극한 인장 강도(UTS), 항복 강도(YS) 및 연신율(A)을 평가했습니다.
- 현미경 관찰: 광학 현미경을 사용하여 합금의 미세 구조를 분석하고 결정립 구조와 상 분포를 조사했습니다.
- 컴퓨터 단층 촬영(CT): CT 스캔을 사용하여 주조 시편 내의 기공률 함량 및 분포를 평가했습니다.
- 밀도 측정: 아르키메데스 저울을 사용하여 시편의 밀도를 측정하여 기공률에 대한 또 다른 척도를 제공했습니다.
- 화학 조성 분석: 스파크 광학 방출 분광법(S-OES)을 사용하여 합금의 화학 조성을 검증했습니다.
분석 방법:
- 정량적 분석: 인장 시험 데이터를 통계적으로 분석하여 용융 처리 및 주조 방법이 기계적 특성에 미치는 영향을 결정했습니다. CT 스캔 및 밀도 시험에서 얻은 기공률 측정값을 기계적 특성 데이터와 상관 관계를 분석했습니다.
- 정성적 분석: 광학 현미경 및 CT 이미지의 미세 구조 분석을 사용하여 용융 처리가 결정립 미세화, 상 분포 및 기공률 형태에 미치는 영향을 정성적으로 평가했습니다.
- 비교 분석: 처리된 합금과 처리되지 않은 합금, 그리고 다양한 방법(영구 금형 대 HPDC)을 사용하여 주조된 합금의 기계적 특성을 비교하여 용융 처리 및 주조 공정의 효과를 평가했습니다. 결과는 EN AC-21100 및 AA 206.0 T4와 같은 표준 합금의 사양과도 비교했습니다.
연구 대상 및 범위:
연구 대상은 4가지 알루미늄 합금이었습니다.
- 합금 1: 상업용 순수 알루미늄.
- 합금 2: AlCu4.6 (Al-4.6Cu).
- 합금 3: AlCu5MnMg (Al-5Cu-0.45Mn-0.37Mg).
- 합금 4: Zn 및 Ti 첨가 AlCu5MnMg (Al-5Cu-0.42Mn-0.27Mg-0.1Zn-0.023Ti).
연구 범위는 다음을 포함했습니다.
- 용융 처리: 아르곤 및 산소 가스 주입을 사용하여 용융 알루미늄에서 Al2O3 입자를 현장에서 생성.
- 주조 방법: 영구 금형 주조 및 고압 다이캐스팅(HPDC).
- 열처리: 합금 4 HPDC 시편에 대한 용체화 열처리 및 자연 시효.
- 기계적 특성: 인장 강도, 항복 강도 및 연신율.
- 미세 구조 특성 분석: 광학 현미경 및 CT 기공률 분석.
6. 주요 연구 결과:
핵심 연구 결과:
- 용융 처리 및 Al2O3 형성: 용융 처리 공정은 용융 표면에 거품 슬래그를 지속적으로 생성하여 산화물, 즉 Al2O3의 형성을 나타냅니다. 그러나 미세 구조 분석 결과 모든 합금에서 알루미늄 매트릭스 내에 분산된 Al2O3 입자는 나타나지 않았습니다.
- 합금 1(순수 알루미늄)의 기계적 특성: Ar 또는 Ar + O2를 사용한 용융 처리는 순수 알루미늄의 기계적 특성을 크게 변경하지 않았습니다. 인장 강도와 연신율의 변화는 용융 처리 자체가 아니라 기공률 및 금형 온도 변동에 기인한 것으로 보입니다.
- 합금 2(AlCu4.6)의 기계적 특성: 구리 첨가는 합금 1에 비해 합금 2의 강도를 크게 증가시켰습니다. HPDC 합금 2는 영구 금형 주조물보다 강도와 연신율이 더 높았으며, 이는 더 빠른 냉각으로 인한 더 미세한 미세 구조에 기인합니다. 두 주조 방법 모두 "톱니 모양" 응력-변형 곡선을 나타냈으며, 이는 CuAl2 상 때문일 수 있습니다.
- 합금 3(AlCu5MnMg)의 기계적 특성: 합금 3은 합금 2에 비해 강도가 더욱 증가했지만 연신율은 감소했습니다. HPDC 합금 3은 영구 금형 주조물보다 강도가 약간 더 높았습니다. "톱니 모양" 거동은 합금 3에서 관찰되지 않았습니다.
- 합금 4(Zn 및 Ti 첨가 AlCu5MnMg)의 기계적 특성: 합금 4는 주조 HPDC 조건에서 안정적인 항복 강도와 영구 금형 주조물보다 높은 UTS를 나타냈습니다. 열처리(T4)는 HPDC 합금 4의 강도를 크게 향상시켜 AA 206.0 T4 합금과 유사한 특성을 달성했지만 연신율은 여전히 낮았습니다.
- 기공률: 기공률은 모든 합금 및 주조 방법에서 기계적 특성에 영향을 미치는 중요한 요소였습니다. CT 분석 결과 다양한 기공률 수준과 분포가 나타났으며, 이는 인장 강도와 연신율에 영향을 미쳤습니다.
제시된 데이터 분석:
- 그림 5.1, 5.2, 5.3, 5.4, 5.5, 5.6, 5.7: 이 그림은 시간 경과에 따른 다양한 용융 처리(Ar, Ar+O2) 및 임펠러 크기(Ø 72 mm, Ø 185 mm) 하에서 합금 1의 기계적 특성(Rm, Ag)을 보여줍니다. 데이터는 용융 처리로 인한 유의미한 강화 효과가 없음을 나타내며, 변화는 기공률 및 금형 조건 때문일 가능성이 높습니다.
- 그림 5.8, 5.9, 5.10: 이 그림은 합금 1에 대한 CT 이미지와 기공률 측정을 제시하여 기공률 변화를 보여주고 기공률과 기계적 특성 가변성 간의 상관 관계를 시사합니다.
- 그림 5.16, 5.20, 5.21: 이 그림은 영구 금형 및 HPDC에서 주조된 합금 2의 기계적 특성을 비교합니다. HPDC 샘플은 더 높은 강도와 연신율을 보여줍니다. 그림 5.21은 합금 2에 대한 주조 공정을 비교하여 HPDC의 향상된 특성을 강조합니다.
- 그림 5.19, 5.22: 이 그림은 합금 2에 대한 응력-변형 곡선을 보여주며, "톱니 모양" 거동을 보여주며, 영구 금형 주조물에서 더 두드러집니다.
- 그림 5.26, 5.30: 이 그림은 영구 금형 및 HPDC에서 주조된 합금 3의 기계적 특성을 제시합니다. 합금 3은 합금 2보다 강도가 높지만 연신율은 낮습니다.
- 그림 5.35, 5.36, 5.38, 5.39: 이 그림은 영구 금형, 주조 HPDC 및 열처리된 HPDC 조건에서 합금 4의 기계적 특성을 보여줍니다. 열처리는 HPDC 합금 4의 강도를 크게 향상시킵니다.
그림 목록:
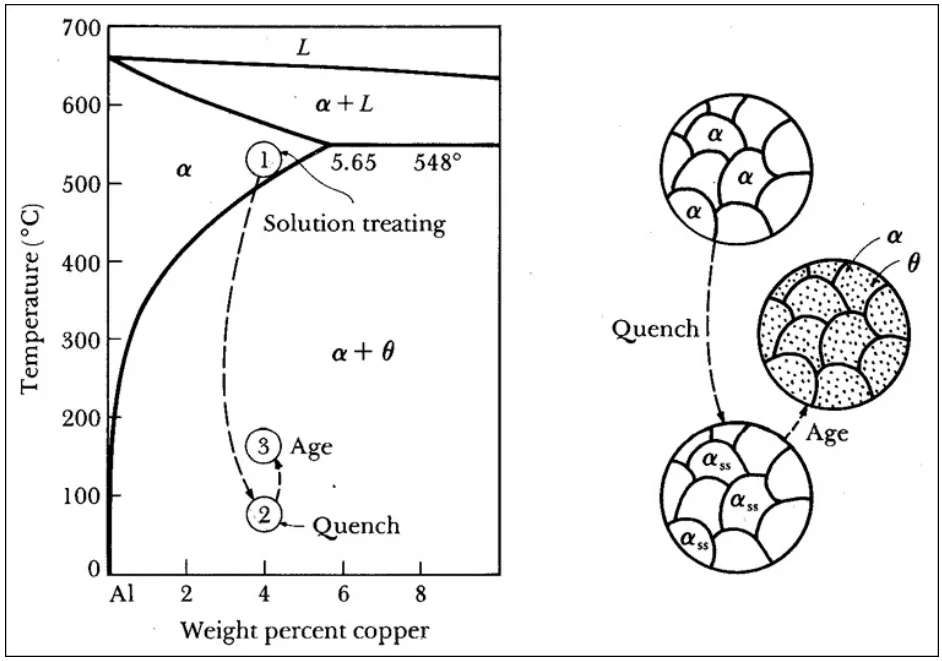
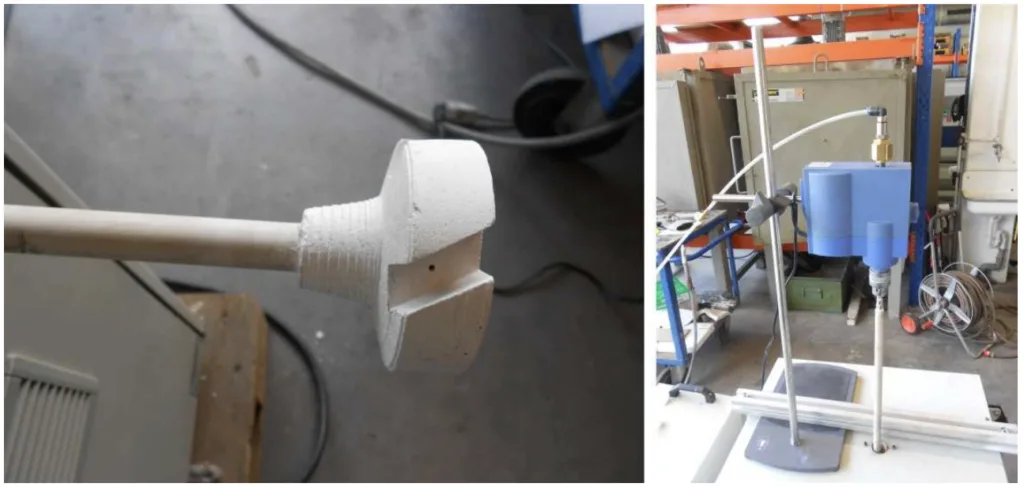
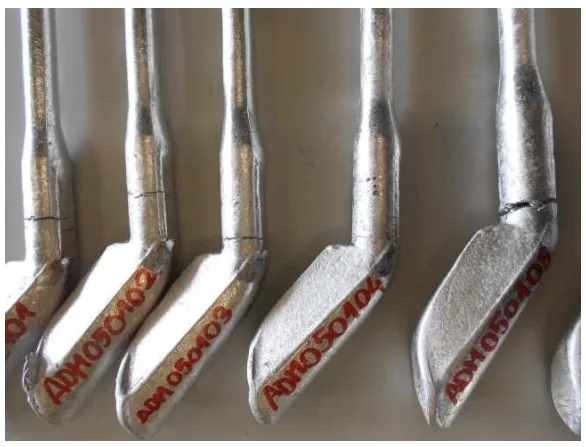
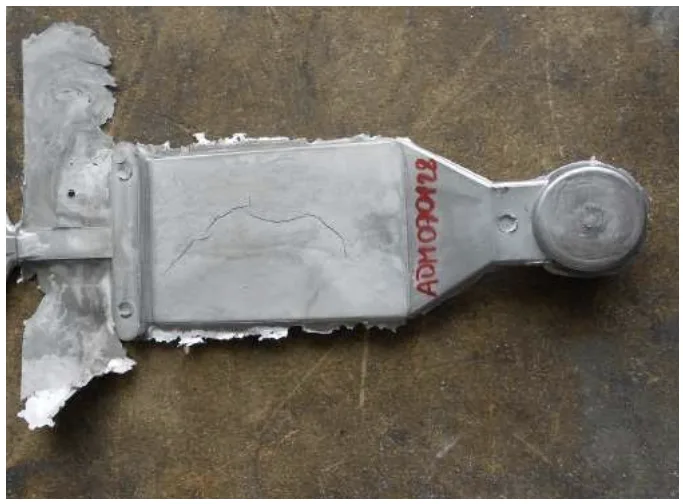
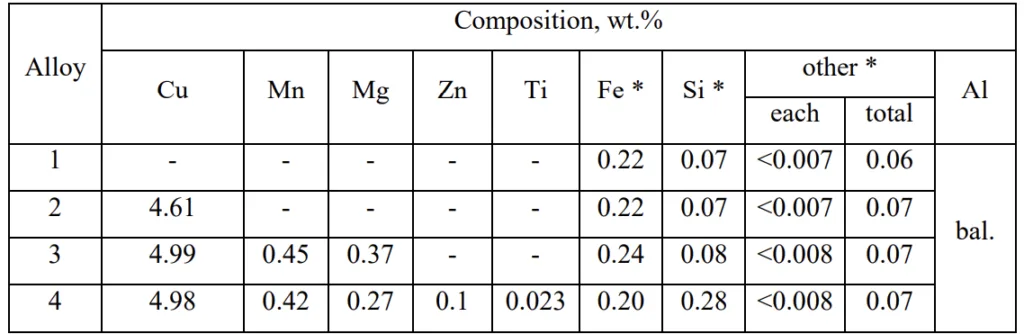
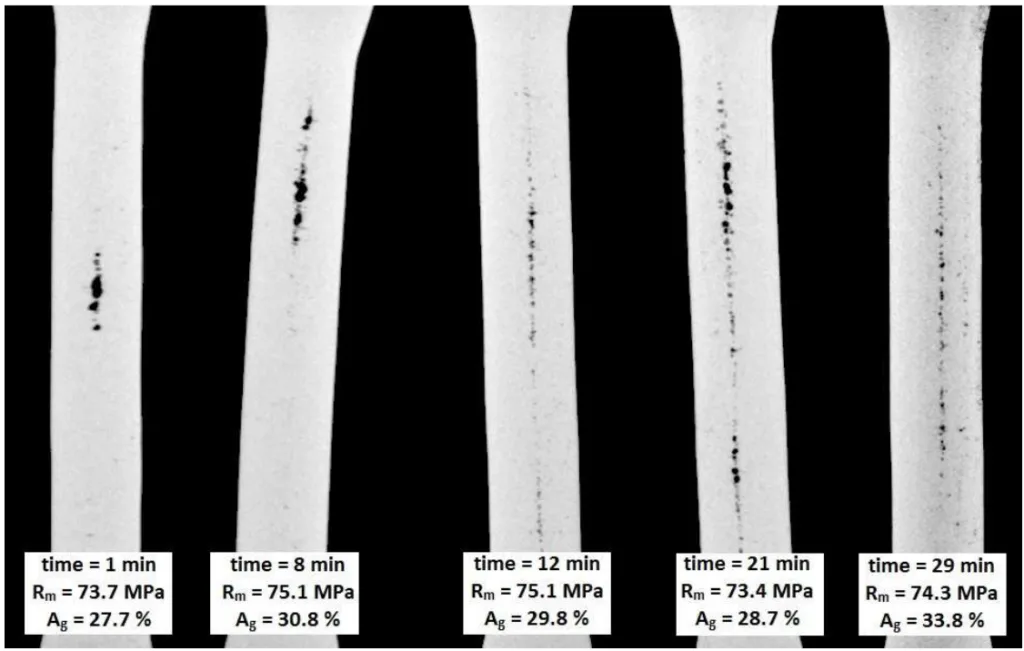
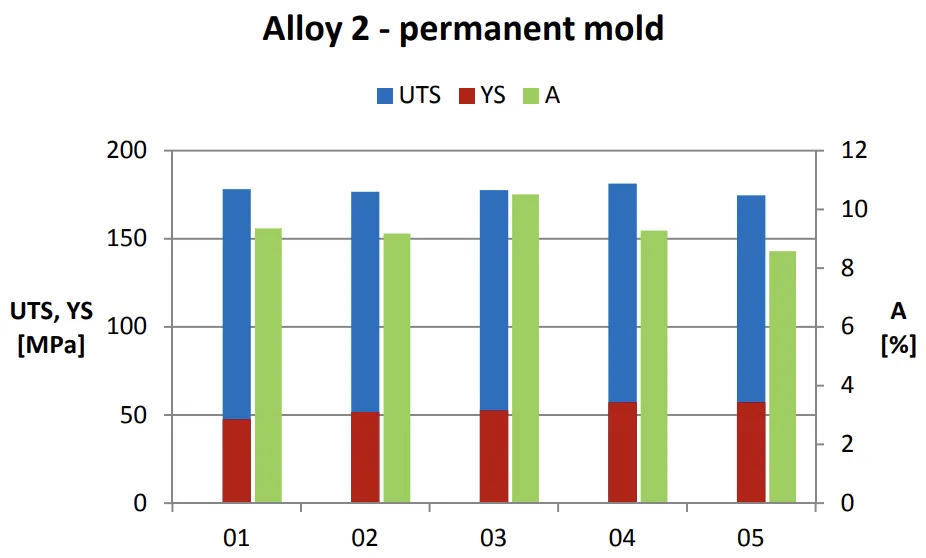
- Figure 1: rappresentazione in sezione di una macchina da pressocolata
- Figure 2: illustrazione del processo di rafforzamento per precipitazione
- Figure 3: girante e miscelatore utilizzati nell'impianto più piccolo
- Figure 4: scoria formatasi sulla superficie del bagno fuso di alluminio fuso
- Figure 5: piasta ottenuta per pressocolata con evidenti segni di criccatura a caldo
- Figure 6: proprietà meccaniche della lega 1 - iniezione di Ar + O2 - girante da Ø 72 mm
- Figure 7: proprietà miccaniche della lega 1 - iniezione di Ar + O2 - girante da Ø 185 mm
- Figure 8: microstruttura della lega 1 dopo trattamento con iniezione di Ar + O2
- Figure 9: distribuzione dei punti di rottura dei provini di lega 2 pressocolata
- Figure 10: proprietà meccaniche della lega 4 dopo invecchiamento
- Figure 2.1: parts produced with HPDC: a dental chair component (a), a medical imager side wall (b), an engine base bracket (c) and a transaxle housing (d).
- Figure 2.2: layout of a hot-chamber HPDC machine
- Figure 2.3: layout of a cold-chamber HPDC machine
- Figure 2.4: main components of a die assembly
- Figure 2.5: a vacuum system for extracting air both from the shot sleeve and the die cavity
- Figure 2.6: StatVac equipment by Electronics GmbH
- Figure 2.7: layout of a Vacural HPDC machine
- Figure 2.8: microstructure comparison between a convetional and a semi solid die cast alloy
- Figure 3.1: Alfred Wilm (1869–1937)
- Figure 3.2: Duralumin was adopted in airplanes and airships for its stength, toughtness and lightness
- Figure 3.3: Al-CuAl2 phase diagram
- Figure 3.4: solidification of an Al-Cu alloy
- Figure 3.5: the precipitation hardening process
- Figure 3.6: two mechanisms of overcoming precipitates
- Figure 3.7: influence of precipitate radius on the stress σy
- Figure 3.8: changes in behaviour due to different age hardening conditions
- Figure 3.9: solvuses of Al-Cu phases
- Figure 3.10: a hot crack originate on a die cast component
- Figure 4.1: a block of boron nitride and the impeller machined
- Figure 4.2: two phases of the gluing process
- Figure 4.3: the stirrer installed on the furnace
- Figure 4.4: scheme of the gas mixing circuit
- Figure 4.5: the big scale setup during the treatment
- Figure 4.6: the Ø 185 mm impeller
- Figure 4.7: slag solidified around the impeller and the oxide powder on the crucible
- Figure 4.8: slag wrapped around the graphite tube
- Figure 4.9: slag removed from the surface of melt
- Figure 4.10: permanent mold cast tensile specimens
- Figure 4.11: Weingarten GDK 200 HPDC machine
- Figure 4.12: die employed for the production of die cast plates
- Figure 4.13: hot cracks in permanent mold cast specimens
- Figure 4.14: hot cracks on a die cast plate
- Figure 4.15: mark of the ejector pin on the overflow of a die cast plate
- Figure 4.16: blisters on the surface of a heat treated die cast plate
- Figure 4.7: slag solidified around the impeller and the oxide powder on the crucible
- Figure 5.1: mechanical properties of alloy 1 – melt treatment with Ar + O2 – Ø 72 mm impeller setup
- Figure 5.2: ultimate tensile strength of alloy 1 − melt treatment with Ar − Ø185 mm impeller setup
- Figure 5.3: permanent elongation at maximum load of alloy 1 − melt treatment with Ar – Ø 185 mm impeller setup
- Figure 5.4: ultimate tensile strength of alloy 1 − melt treatment with Ar and O2 – Ø 185 mm impeller
- Figure 5.5: elongation at maximum load of alloy 1 − melt treatment with Ar and O2 – Ø 185 mm impeller
- Figure 5.6: Rm comparison between alloy 1 treated with Ar and alloy 1 treated with Ar + O2
- Figure 5.7: comparison of Rm and Ag variability in alloy 1 after trend-filtering of Ag values − melt treatment with Ar + O2 – Ø 185 mm impeller
- Figure 5.8: CT images showing the internal porosity of some of the tensile specimens of alloy 1
- Figure 5.9: porosity content of tensile specimens of alloy 1 − melt treatment with Ar + O2 – Ø 185 mm impeller
- Figure 5.10: CT images of the grip sections of tensile specimens of alloy 1 − melt treatment with Ar + O2 – Ø 185 mm impeller
- Figure 5.11: microstructure of alloy 1 − no melt treatment − 100x
- Figure 5.12: microstructure of alloy 1 − no melt treatment − 1000x
- Figure 5.13: microstructure of alloy 1 − melt treatment with Ar + O2 – Ø 72 mm impeller setup − 1000x
- Figure 5.14: microstructure of alloy 1 − melt treatment with Ar + O2 – Ø 185 mm impeller – 100x
- Figure 5.15: microstructure of alloy 1 − melt treatment with Ar + O2 – Ø 185 mm impeller − 1000x
- Figure 5.16: mechanical properties of permanent mold cast alloy 2
- Figure 5.17: CT images of permanent mold cast specimens of alloy 2
- Figure 5.18: porosity content of alloy 2 specimens cast in permanent mold
- Figure 5.19: a stress-strain curve of permanent mold cast alloy 2, showing the "saw-tooth" behaviour
- Figure 5.20: distribution of failure points of die cast alloy 2 specimens
- Figure 5.21: mechanical properties of alloy 2 - comparison of casting processes
- Figure 5.22: stress-strain curve of die cast alloy 2, showing the same “saw-tooth” behaviour as for permanent mold cast specimens
- Figure 5.23: microstructure of alloy 2 − permanent mold casting − 100x
- Figure 5.24: microstructure of alloy 2 − permanent mold casting − 500x
- Figure 5.25: microstructure alloy 2 – HPDC − 100x
- Figure 5.26: mechanical properties of permanent mold cast alloy 3
- Figure 5.27: CT images of permanent mold cast alloy 3
- Figure 5.28: porosity content of the specimens of permanent mold cast alloy 3
- Figure 5.29: x-ray images of die cast alloy 3 specimens, showing hot cracks inside the two samples in the middle
- Figure 5.30: mechanical properties of die cast alloy 3
- Figure 5.31: comparison of the yielding behaviour of permanent mold and die cast alloy 3
- Figure 5.32: microstructure of alloy 3 − permanent mold casting − 100x
- Figure 5.33: microstructure of alloy 3 − permanent mold casting − 1000x
- Figure 5.34: microstructure of alloy 3 – HPDC − 100x
- Figure 5.35: mechanical properties of permanent mold cast alloy 4
- Figure 5.36: mechanical properties of HPDC alloy 4 without heat treatment
- Figure 5.37: comparison of the yielding behaviour of permanent mold and die cast alloy 4
- Figure 5.38: mechanical properties of die cast alloy 4 after HT1
- Figure 5.39: mechanical properties of die cast alloy 4 after HT2
- Figure 5.40: microstructure of alloy 4 − permanent mold casting − 100x
- Figure 5.41: microstructure of alloy 4 - permanent mold casting - 1000x
- Figure 5.42: microstructure of alloy 4 − HPDC − no heat treatment − 100x
- Figure 5.43: microstructure of alloy 4 − HPDC − no heat treatment − 500x
- Figure 5.44: microstructure of alloy 4 − HPDC − HT1 − 100x
- Figure 5.45: microstructure of alloy 4 - HPDC - HT2 - 100x
7. 결론:
주요 연구 결과 요약:
본 실험은 다양한 조건과 매개변수에서 수행되었습니다. 모든 상황에서 용융 처리는 용융 표면에 떠 다니는 거품 슬래그를 생성했습니다. 슬래그는 낮은 비중과 내부에 갇힌 가스로 인해 떠 다니는 산화된 알루미늄의 응집에서 유래합니다. 아르곤 및 아르곤 + O2를 사용한 용융 처리 후 합금 1이 도달한 기계적 특성은 관련성 있는 차이를 나타내지 않습니다. 아르곤 + O2로 처리하는 동안 주조된 시편에서 연신율의 긍정적인 진화가 관찰되었지만, 도달한 값은 아르곤으로만 처리된 동일한 합금의 값과 비슷합니다. 금형 크기, 온도, 기공률 함량 및 분포의 영향이 합금의 기계적 특성에 미치는 것으로 나타났습니다. 합금 1의 미세 구조는 결정립계 및 결정립 내의 둥근 영역에서 응고된 Al/Al3Fe 공정상의 존재가 특징입니다. 용융 처리하지 않은 합금, 아르곤으로 처리한 합금, 아르곤 + O2로 처리한 합금 간에 눈에 띄는 변화는 발견되지 않았습니다. 임펠러 크기는 미세 구조에 영향을 미치지 않았습니다. 합금 2에 대한 시험에서는 첨가 원소로서 Cu 첨가의 강화 효과를 보여주었습니다. UTS와 YS는 연신율을 희생하면서 향상되었습니다. 영구 금형 주조 시편의 측정된 UTS 및 A 값은 EN AC-21100 합금의 사양과 일치하지만 YS는 더 낮습니다. 다이캐스트 시편은 더 높은 강도와 연신율에 도달하지만 많은 결함, 특히 실제 강도에 강하게 영향을 미치는 열간 균열의 존재로 인해 어려움을 겪습니다. 영구 금형 및 다이캐스트 합금 2 모두 "톱니 모양" 응력-변형 곡선을 보여줍니다. CuAl2 상의 손상 메커니즘이 원인일 수 있습니다. 합금 2의 미세 구조는 수지상이며 CuAl2는 Al/Al3Fe 상과 함께 수지상 간 공간에서 응고됩니다. HPDC는 더 높은 냉각 속도로 인해 더 미세한 미세 구조를 갖습니다. 합금 3은 합금 2에 비해 더 높은 강도에 도달했지만 연신율은 더 낮습니다. Mn과 Mg의 첨가와 더 높은 Cu 함량은 합금의 강도를 현저히 증가시켰습니다.
연구의 학문적 중요성:
본 연구는 알루미늄 합금에서 Al2O3 입자를 현장에서 생성하기 위한 혁신적인 용융 처리에 대한 포괄적인 조사를 제공합니다. 연구 결과에 따르면 이 처리는 슬래그 형성에 의해 입증된 바와 같이 산화물을 효과적으로 생성하지만 테스트된 매개변수를 사용하여 알루미늄 매트릭스 내에 Al2O3 강화재의 원하는 분산을 달성하지는 못합니다. 본 연구는 용융 처리의 한계와 다이캐스트 알루미늄 합금, 특히 Al-Cu 기반 합금에서 공정 매개변수, 미세 구조 및 기계적 특성 간의 복잡한 상호 작용에 대한 이해에 기여합니다. 이는 기존 다이캐스팅 공정에서 현장 강화 전략을 구현하는 데 따르는 어려움을 강조합니다.
연구의 실제적 의미:
결과에 따르면 조사된 용융 처리는 현재 형태로 Al2O3 입자 강화를 통해 다이캐스트 알루미늄 합금의 기계적 특성을 향상시키는 실용적으로 실행 가능한 방법이 아닙니다. 본 연구는 특히 Al-Cu 합금에서 기공률과 열간 균열을 관리하기 위해 금형 온도 및 냉각 속도와 같은 주조 매개변수를 최적화하는 것의 중요성을 강조합니다. 연구 결과는 열처리, 특히 T4 열처리가 HPDC Al-Cu 합금과 같은 합금 4의 강도를 크게 향상시켜 AA 206.0 T4와 같은 기존의 고성능 합금과 견줄 수 있게 만드는 데 효과적임을 강조합니다.
연구의 한계 및 향후 연구 분야:
주요 한계는 산화물 형성에도 불구하고 알루미늄 매트릭스 내에 현장 Al2O3 입자 분산을 달성하지 못한 것입니다. 향후 연구에서는 다음과 같은 용융 처리 공정의 수정 사항을 탐구해야 합니다.
- 가스 주입 매개변수 최적화: Al2O3 핵 생성 및 분산을 촉진하기 위해 가스 혼합 비율, 유량 및 주입 방법을 다양하게 변경합니다.
- 임펠러 설계 및 교반 조건: 슬래그 형성 및 용융 표면 파괴를 최소화하면서 난류 및 산화물 입자 분포를 향상시키기 위해 임펠러 형상 및 교반 속도를 개선합니다.
- 대체 현장 반응: Al2O3 형성 및 분산을 보다 효과적으로 촉진할 수 있는 다양한 반응성 가스 혼합물 또는 전구체를 조사합니다.
- 나노 입자 안정화: 용융 처리 및 주조 중 Al2O3 나노 입자의 응집을 안정화하고 방지하는 방법을 탐구합니다.
- 공정 확장성 및 비용 효율성: 강화된 다이캐스트 부품의 대량 생산에 산업적으로 확장 가능하고 경제적으로 실현 가능한 용융 처리 방법 개발에 중점을 둡니다.
- 열간 균열에 대한 추가 조사: Al-Cu 합금의 열간 균열 메커니즘을 이해하고 미세 구조 제어 또는 합금 수정을 통해 HPDC에서 열간 균열을 완화하기 위한 효과적인 전략을 개발하기 위한 추가 연구가 필요합니다.
8. 참고 문헌:
- [1] K.U. Kainer, Basics of Metal Matrix Composites
- [2] C. Borgonovo, Aluminum Nano-composites for Elevated Temperature Applications, Worcester Polytechnic Institute, Worcester, USA
- [3] C. Borgonovo, Makhlouf M. Makhlouf, Synthesis of die-castable nano-particle reinforced aluminium matrix composite materials by in-situ gas-liquid reactions, Worcester Polytechnic Institute, Worcester, USA
- [4] A.A. Hamid, P.K. Ghosh, S.C. Jain, S. Ray, Processing, Microstructure, and Mechanical Properties of Cast In-Situ Al(Mg,Ti)-Al2O3(TiO2) Composite, Metallurgical and Materials Transactions A, vol. 37A, Feb. 2006
- [5] North American Die Casting Association - www.diecasting.org
- [6] CustomPartNet – www.custompartnet.com/wu/die-casting#equipment
- [7] ASM Handbook, ASM International, vol. 2
- [8] UC RUSAL – www.aluminiumleader.com/en/around/transport
- [9] I. J. Polmear, Aluminium Alloys - A century of age hardening, Materials Forum Vol. 28 – 2004
- [10] J.R. Greer, Handout AlCu, www.jrgreer.caltech.edu
- [11] Prof. F. Bonollo, Leghe di alluminio: approfondimenti metallurgici – Trattamenti termici, Dipartimento di Tecnica e Gestione dei Sistemi Industriali - Università di Padova, Vicenza, Italy
- [12] Alcan AA206 Primary Foundry Alloys, Alcan Primary Products Corporation Inc.
- [13] S. Li, Hot Tearing in Cast Aluminium Alloys: Measures and Effects of Process Variables, Worcester Polytechnic Institute, Worcester, USA
- [14] S. Bao, K. Tang, A. Kvithyld, M. Tangstad, Wettability of Aluminum on Alumina, Metallurgical and Materials Transactions B, vol. 42B, Dec. 2011
- [15] E.G. Fuchs, A Roósz, TTD-Diagrams for the Homogenization of As-Cast Structures, Z. Metallkunde, Vol. 63, pp. 211-214 (1972)
- [16] Prof. F. Bonollo, Prodotti Metallurgici Innovativi e Multifunzionali, Dipartimento di Tecnica e Gestione dei Sistemi Industriali - Università di Padova, Vicenza, Italy
- [17] www.matweb.com
- [18] www.keytometals.com
- [19] www.aviometal.com
- [20] www.wikipedia.org
9. 저작권:
- 본 자료는 "Alberto Dal Maso"의 논문: "[Paper Title]"을 기반으로 합니다.
- 논문 출처: [문서에 DOI 없음]
본 자료는 위 논문을 소개하기 위해 제작되었으며, 상업적 목적으로 무단 사용하는 것을 금지합니다.
Copyright © 2025 CASTMAN. All rights reserved.