본 기사에서는 Linköping University에서 발행한 논문 ["CAE modelling of cast aluminium in automotive structures"]를 소개합니다.
1. Overview:
- Title: CAE modelling of cast aluminium in automotive structures
- Author: Sreehari Veditherakal Shreedhara & Subrat Raman Singh
- Publication Year: 2019
- Publishing Journal/Academic Society: Master Thesis in Division of Solid Mechanics, Department of Management and Engineering, Linköping University
- Keywords: Cast aluminium, Explicit FEA, LS-DYNA, Drop tower, Spring tower, FEM, CrachFEM, MFGenYld
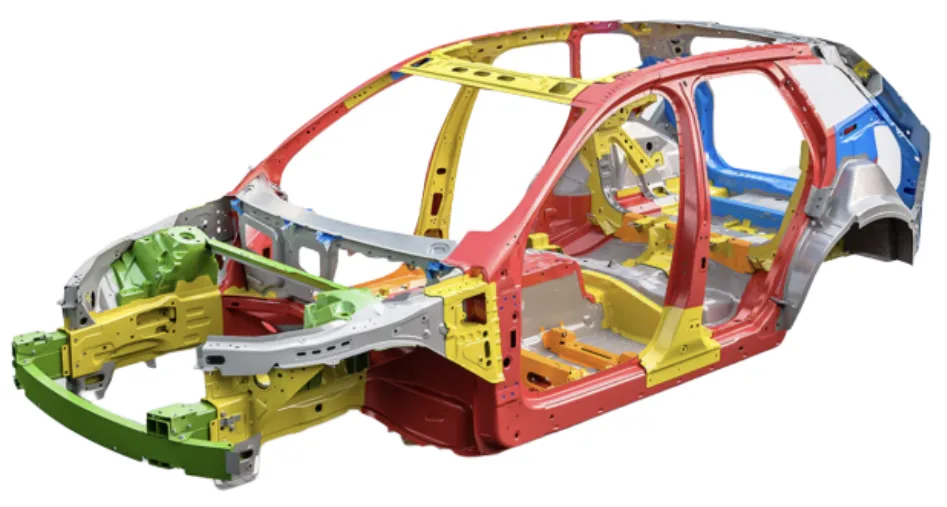
2. Abstracts or Introduction
자동차 산업에서는 CAE(Computer Aided Engineering) 솔루션 결과를 기반으로 엔지니어링 의사 결정을 내리고, 비용이 많이 드는 반복적인 프로세스인 프로토타입 제작 및 테스트를 최종 검증 및 유효성 확인 단계로 전환하려는 움직임이 크다. 부품 재료 속성 및 환경 조건의 가변성과 복잡한 시스템의 기본 물리학에 대한 지식 부족으로 인해 결정론적 CAE 모델만으로는 신뢰할 수 있는 예측을 하기 어려운 경우가 많다. 이러한 영역 중 하나가 주조 알루미늄 부품의 CAE 모델링이다. 이러한 주조 알루미늄 부품은 뛰어난 기계적 특성으로 인해 자동차 산업에서 큰 관련성을 얻고 있다. 주조 알루미늄 합금의 장점은 제조 공정에서 잘 확립된 합금 시스템, 기능적 무결성 및 상대적으로 낮은 무게이다. 그러나 제조 공정 중에 얻어지는 기공 및 미세 기공의 존재는 특정한 재료 거동을 구성하고 주조 재료 모델링에 어려움을 야기한다. 또한 재료의 낮은 연성은 파괴를 예측하기 위한 고급 수치 모델을 필요로 한다.
본 석사 학위 논문의 주요 초점은 드롭 타워 테스트를 위한 주조 알루미늄 합금 부품인 스프링 타워의 모델링 기술을 조사하고 물리적 테스트 결과와 예측된 거동을 검증하는 것이다. Volvo Car Corporation은 현재 MATFEM에서 제공하는 주조 알루미늄 부품용 재료 모델을 사용하고 있으며, 이 논문에서는 부품 수준 테스트를 위한 재료 모델을 검증하기 위해 이 모델을 탐구한다.
이 목표를 달성하기 위해 사용된 방법론은 드롭 타워에서 부품 수준 테스트를 수행하고 명시적 솔버 LS-DYNA에서 다양한 모델링 기술을 사용하여 얻은 결과와 이러한 결과를 연관시키는 경계 조건을 개발하는 것이었다. 따라서 시뮬레이션 결과가 주요 설계 변경에 의해 영향을 받을 수 있기 때문에 드롭 타워의 정확하고 현실적인 모델링이 중요하다. 물리적 테스트 중 관찰된 결과를 바탕으로 스프링 타워에 대한 상세한 유한 요소 모델이 개발되었다. 개선된 모델은 스프링 타워에 대한 기존 모델 및 물리적 테스트 관찰 결과와 양호한 일치를 보였다.
3. Research Background:
Background of the Research Topic:
자동차 산업은 전기 자동차의 수요 증가와 함께 차량 무게 감량의 필요성이 커지고 있다. 탄소 섬유 강화 플라스틱과 같은 재료는 차량 무게를 줄이는 데 효과적이지만 생산 및 제조 비용이 비싸다. 반면에 알루미늄과 같은 재료는 낮은 밀도와 잘 확립된 제조 공정으로 인해 많은 관련성을 확보했다 [1]. 강도와 연성의 조합은 자동차 응용 분야에서 핵심 성능 파라미터이다. 그러나 재료 속성, 강도, 강성 및 부품 무게 간의 관계는 매우 복잡하며 형상 및 제조 공정에 의해 크게 영향을 받을 수 있다.
Status of Existing Research:
알루미늄 주조 부품은 자동차 산업에서 점점 더 중요해지고 있다. Volvo는 2025년까지 판매량의 50%를 전기 자동차로 목표하고 있으며 [2], 차량의 충돌 안전성을 저하시키지 않으면서 무게를 줄여 장거리 내구성을 목표로 하고 있다. 이는 주조 알루미늄을 현재 시점에서 좋은 선택으로 만든다. 따라서 특정 하중 조건에서 각 주조 알루미늄 부품의 거동을 연구하는 것이 필수적이다.
Necessity of the Research:
주조 알루미늄 부품은 동일 부품 내에서도 다른 영역에서 다른 속성을 나타낼 수 있으며, 부품 내에 가변적인 결함이 존재할 수 있고, 주조 알루미늄에 대한 CAE 방법 및 경험이 제한적이다. 또한 주조 알루미늄 합금은 기공과 미세 기공을 포함할 수 있으며, 이는 외부 하중에 노출될 때 미세 균열 시작 및 전파로 이어질 수 있다 [3]. 따라서 차량 안전에 영향을 미치지 않도록 주조 알루미늄 부품의 거동을 이해하는 것이 중요하다.
4. Research Purpose and Research Questions:
Research Purpose:
본 논문의 주요 목적은 자동차의 주조 알루미늄 구조물에 대한 CAE(Computer Aided Engineering) 모델링 방법을 연구, 검증 및 개선하는 것이다. 이는 스웨덴 예테보리의 Volvo Cars에서 사용되는 현재 모델링 및 시뮬레이션 기술을 조사하여 수행된다. 상용 유한 요소(FE) 프로그램은 부품의 파손을 예측하기 위해 하중 조건을 시뮬레이션하고 분석하는 데 사용된다. 본 연구에서는 스프링 타워라는 부품을 분석한다. VCC(Volvo Cars Corporation)는 FE 소프트웨어에 통합된 MATFEM에서 개발한 재료 파손 모델인 MFGenYld+CrachFEM을 사용한다. 이러한 재료 카드에는 수많은 쿠폰 테스트에서 정의된 파라미터가 있지만 VCC의 주조 알루미늄 부품에 대해서만 독점적으로 검증되지는 않았다. 따라서 재료 파손 카드가 FE 시뮬레이션의 주조 알루미늄 부품에 적용 가능한지 확인하기 위해 재료 검증을 수행해야 한다.
Key Research:
본 논문의 범위는 다음과 같다.
- 물리적 드롭 타워 테스트 중에 부품을 고정할 수 있을 만큼 견고한 테스트 설정을 결정한다.
- 부품에 대한 물리적 테스트를 수행하고 결과를 얻는다.
- 다양한 모델링 방법을 평가하여 CAE를 통해 물리적 결과를 연관시킨다.
Research Hypotheses:
본 논문에서는 문제 설명 및 목적을 바탕으로 다음과 같은 연구 질문에 대한 답변을 분석 및 결론 과정에서 제시한다.
- 현재의 계산 능력에 기반하여 주조 알루미늄에 대한 최적의 파손 예측 방법은 무엇인가?
- 쉘 및 솔리드 요소는 상대적으로 얇은 벽 구조물에 대해 정확한 결과를 제공할 수 있는가?
5. Research Methodology
Research Design:
본 연구에서는 CAE 시뮬레이션과 물리적 드롭 타워 테스트를 병행하여 주조 알루미늄 부품의 파손 거동을 분석하고 모델링 방법을 검증하는 실험적 연구 설계를 채택하였다.
Data Collection Method:
- CAE 시뮬레이션 데이터: LS-DYNA를 사용하여 다양한 요소 유형(쉘 및 솔리드), 요소 크기, 재료 모델 파라미터 및 경계 조건에서 시뮬레이션을 수행하고, 힘-변위 곡선, 플라스틱 변형률 분포, 요소 삭제 등의 데이터를 수집하였다.
- 물리적 테스트 데이터: 드롭 타워 테스트를 통해 스프링 타워 부품의 파손 거동을 측정하였다. 힘 센서 및 가속도계 데이터를 수집하여 힘-변위 곡선을 얻고, 파손 모드 및 균열 위치를 관찰하였다.
Analysis Method:
- CAE 시뮬레이션 분석: METApost를 사용하여 시뮬레이션 결과를 후처리하고, 힘-변위 곡선, 플라스틱 변형률 분포, 요소 삭제 등을 분석하였다.
- 물리적 테스트 데이터 분석: METApost를 사용하여 가속도계 데이터를 필터링하고, 힘-변위 곡선을 계산하고, 흡수 에너지를 평가하였다.
- CAE-물리적 테스트 결과 비교: CAE 시뮬레이션 결과와 물리적 테스트 결과를 힘-변위 곡선, 최대 하중, 파손 모드 및 균열 위치 측면에서 비교하고, 모델링 방법의 정확성을 평가하였다.
Research Subjects and Scope:
본 연구의 대상은 자동차 구조물에 사용되는 주조 알루미늄 합금 스프링 타워 부품이다. 연구 범위는 다음과 같다.
- 재료: 주조 알루미늄 합금
- 부품: 스프링 타워
- 하중 조건: 드롭 타워 충격 하중 (Load case 1, Load case 2)
- 모델링 방법: 쉘 요소 및 솔리드 요소 모델링, 다양한 요소 크기 및 요소 공식, MFGenYld+CrachFEM 재료 모델
- 해석 도구: LS-DYNA, ANSA, METApost
6. Main Research Results:
Key Research Results:
- 경계 조건 개선: 초기 rigid impactor 모델에서 elastic material properties를 부여하고, rollers, guide rail, mass 등을 포함한 improved boundary condition 모델을 개발하여 물리적 테스트 설정을 더욱 정확하게 모사하였다.
- 쉘 요소 모델 vs. 솔리드 요소 모델: 쉘 요소 모델(ELFORM16)과 솔리드 요소 모델(ELFORM16, ELFORM13) 모두 파손 예측에 유효했지만, 솔리드 요소 모델이 메쉬 의존성이 더 강하게 나타났다. coarse mesh의 솔리드 요소 모델은 stiff behaviour를 보이며 peak force를 과대 예측하는 경향이 있었다.
- 요소 크기 영향: 솔리드 요소 모델에서 요소 크기를 줄일수록 결과가 개선되었지만, 시뮬레이션 시간이 크게 증가하였다. 쉘 요소 모델에서는 요소 크기 변화에 따른 결과 변화가 상대적으로 작았다.
- 마찰 계수 영향: 마찰 계수(static friction fs, dynamic frictional coefficient fd)는 CAE 시뮬레이션 결과에 중요한 영향을 미쳤다. 실험적으로 측정되지 않은 마찰 계수는 추정값을 사용하였으며, static friction fs 값을 0.2에서 0.25로 증가시켰을 때 물리적 테스트 결과와 더 나은 상관관계를 얻을 수 있었다.
- 파손 위치 예측: 솔리드 요소 모델이 쉘 요소 모델보다 파손 위치 예측 정확도가 더 높았다. 특히 solid model은 flange가 접히면서 재료 skinning 현상을 더 잘 나타냈지만, 쉘 모델은 파손 위치 예측에서 다소 차이를 보였다.
- Selective mass scaling 효과: Selective mass scaling은 explicit finite element 해석에서 시뮬레이션 시간을 단축하는 데 효과적이었다.
Analysis of presented data:
- Figure 5.1: Physical test compared to CAE model with rigid impactor at 6m/s. Rigid impactor 모델에서 CAE 모델과 물리적 테스트 간의 파손 위치 예측이 불일치함을 보여준다.
- Figure 5.2: Incorrect failure prediction in FE model with rigid impactor compared to physical test at 6m/s. Rigid impactor 모델에서 CAE 모델과 물리적 테스트 간의 파손 위치 예측이 불일치함을 시각적으로 보여준다.
- Figure 5.3: Force vs displacement curve of physical and original FE model at 6m/s. Rigid impactor 모델에서 CAE 모델과 물리적 테스트 간의 힘-변위 곡선이 잘 일치하지 않음을 보여준다.
- Figure 5.4: Force-displacement curve of physical test with simulations pf shell model at 6 m/s. Improved boundary condition 모델과 쉘 요소(ELFORM16)를 사용했을 때 CAE 모델과 물리적 테스트 간의 힘-변위 곡선이 개선되었음을 보여준다.
- Figure 5.5: Failure in FE shell model after impact at 6 m/s with different mesh size. 쉘 요소 모델에서 요소 크기에 따른 파손 형상 변화를 보여준다.
- Figure 5.6: Force-displacement curve of physical test with simulations of solid model at 6m/s. 솔리드 요소 모델(ELFORM16, ELFORM13)을 사용했을 때 CAE 모델과 물리적 테스트 간의 힘-변위 곡선을 비교한다.
- Figure 5.7: Failure in the FE model with different element size using ELFORM16 at 6 m/s. 솔리드 요소 모델(ELFORM16)에서 요소 크기에 따른 파손 형상 변화를 보여준다.
- Figure 5.8: Failure in the FE model with different element size using ELFORM13 at 6 m/s. 솔리드 요소 모델(ELFORM13)에서 요소 크기에 따른 파손 형상 변화를 보여준다.
- Figure 5.9: Force-displacement curve with shell model at 9 m/s. 쉘 요소 모델(ELFORM16)을 사용하여 9 m/s 충격 속도에서 CAE 모델과 물리적 테스트 간의 힘-변위 곡선을 비교한다.
- Figure 5.10: Force-displacement curve with solid model at 9 m/s. 솔리드 요소 모델(ELFORM16)을 사용하여 9 m/s 충격 속도에서 CAE 모델과 물리적 테스트 간의 힘-변위 곡선을 비교한다.
- Figure 5.11: Failure in the physical and the FE model with different element size at 9 m/s. 9 m/s 충격 속도에서 CAE 모델(쉘 및 솔리드 요소, 다양한 요소 크기)과 물리적 테스트 간의 파손 형상 비교를 보여준다.
- Figure 5.12: Force-displacement curve with the shell model at 4 m/s. 쉘 요소 모델(ELFORM16)을 사용하여 4 m/s 충격 속도에서 CAE 모델과 물리적 테스트 간의 힘-변위 곡선을 비교한다.
- Figure 5.13: Force-displacement curve with the solid model at 4 m/s. 솔리드 요소 모델(ELFORM16)을 사용하여 4 m/s 충격 속도에서 CAE 모델과 물리적 테스트 간의 힘-변위 곡선을 비교한다.
- Figure 5.14: Comparison of physical and FE model with different elements size at 4 m/s. 4 m/s 충격 속도에서 CAE 모델(쉘 및 솔리드 요소, 다양한 요소 크기)과 물리적 테스트 간의 파손 형상 비교를 보여준다.
- Figure 5.15: Comparison of physical and FE simulation of load case 2 at 5 m/s. Load case 2 조건에서 CAE 모델(쉘 요소, ELFORM16)과 물리적 테스트 간의 파손 형상 비교를 보여준다.
- Figure 5.16: Comparison of physical and FE model at 5 m/s. Load case 2 조건에서 CAE 모델(쉘 요소, ELFORM16)과 물리적 테스트 간의 파손 형상 비교를 보여준다.
- Figure 5.17: Force-displacement curve with shell model at 5 m/s. Load case 2 조건에서 쉘 요소 모델(ELFORM16)을 사용하여 CAE 모델과 물리적 테스트 간의 힘-변위 곡선을 비교한다.
- Figure 5.18: Comparison of solid FE model at 5 m/s. Load case 2 조건에서 솔리드 요소 모델(ELFORM16)을 사용하여 CAE 모델과 물리적 테스트 간의 파손 형상 비교를 보여준다.
- Figure 5.19: Force-displacement curve with solid model at 5 m/s. Load case 2 조건에서 솔리드 요소 모델(ELFORM16)을 사용하여 CAE 모델과 물리적 테스트 간의 힘-변위 곡선을 비교한다.
- Figure A.1: Failure with rigid impactor at 6 m/s. Rigid impactor 모델에서 CAE 모델의 파손 형상을 보여준다.
- Figure A.2: Force-displacement curve with shell model at 7.5m/s. 쉘 요소 모델(ELFORM16)을 사용하여 7.5 m/s 충격 속도에서 CAE 모델과 물리적 테스트 간의 힘-변위 곡선을 비교한다.
- Figure A.3: Force-displacement curve with solid model at 7.5 m/s. 솔리드 요소 모델(ELFORM16)을 사용하여 7.5 m/s 충격 속도에서 CAE 모델과 물리적 테스트 간의 힘-변위 곡선을 비교한다.
- Figure A.4: Failure in the physical and the FE model with different element size at 7.5 m/s. 7.5 m/s 충격 속도에서 CAE 모델(쉘 및 솔리드 요소, 다양한 요소 크기)과 물리적 테스트 간의 파손 형상 비교를 보여준다.
- Figure A.5: Comparison of Force-displacement curve with shell model at 5 m/s. 쉘 요소 모델(ELFORM16)을 사용하여 5 m/s 충격 속도에서 CAE 모델과 물리적 테스트 간의 힘-변위 곡선을 비교한다.
- Figure A.6: Comparison of Force-displacement curve with solid model at 5 m/s. 솔리드 요소 모델(ELFORM16)을 사용하여 5 m/s 충격 속도에서 CAE 모델과 물리적 테스트 간의 힘-변위 곡선을 비교한다.
- Figure A.7: Crack initiation in physical and FE model with different elements size at 5 m/s. 5 m/s 충격 속도에서 CAE 모델(쉘 및 솔리드 요소, 다양한 요소 크기)과 물리적 테스트 간의 균열 시작 형상 비교를 보여준다.
- Figure A.8: Force-displacement curve with shell model at 4 m/s. 쉘 요소 모델(ELFORM16)을 사용하여 4 m/s 충격 속도에서 CAE 모델과 물리적 테스트 간의 힘-변위 곡선을 비교한다.
- Figure A.9: Force-displacement curve with solid model at 4 m/s. 솔리드 요소 모델(ELFORM16)을 사용하여 4 m/s 충격 속도에서 CAE 모델과 물리적 테스트 간의 힘-변위 곡선을 비교한다.
- Figure A.10: Comparison of the physical and the FE model with various element sizes at 4 m/s. 4 m/s 충격 속도에서 CAE 모델(쉘 및 솔리드 요소, 다양한 요소 크기)과 물리적 테스트 간의 파손 형상 비교를 보여준다.
Figure Name List:
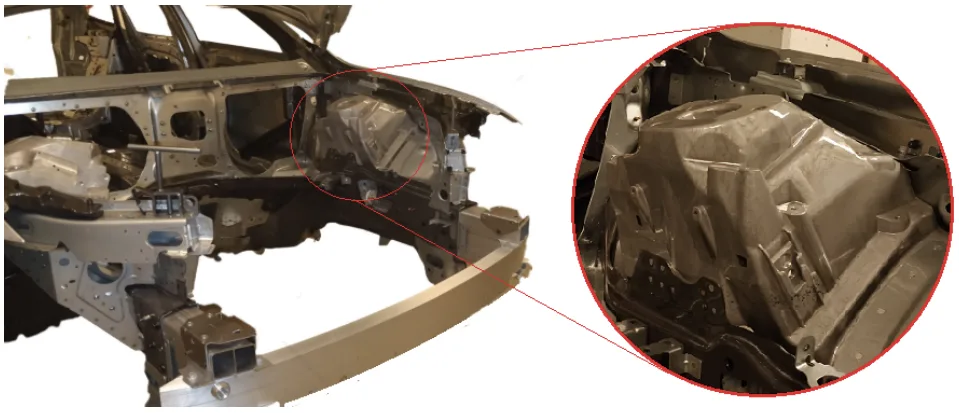
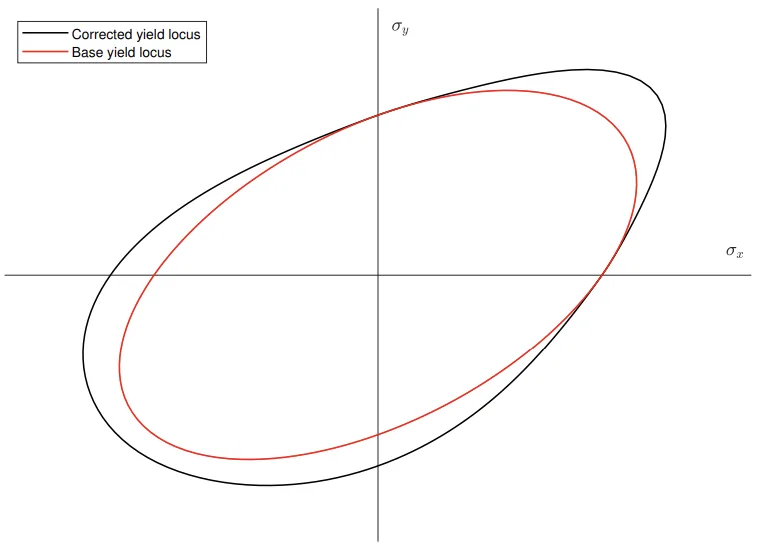
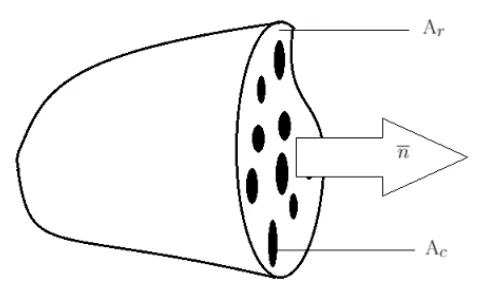
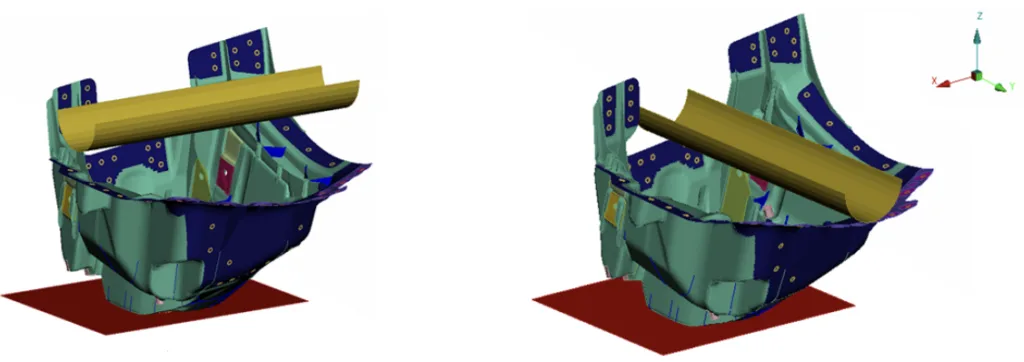
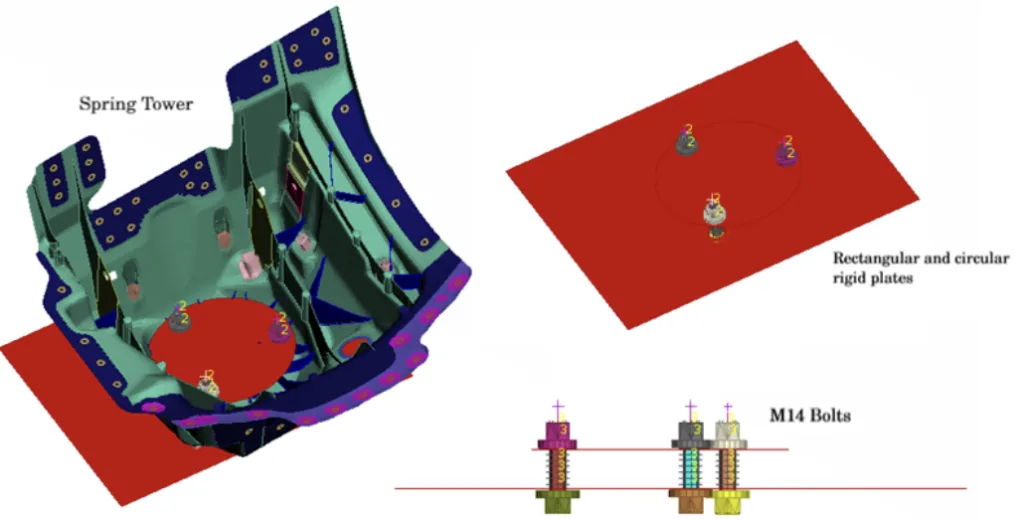
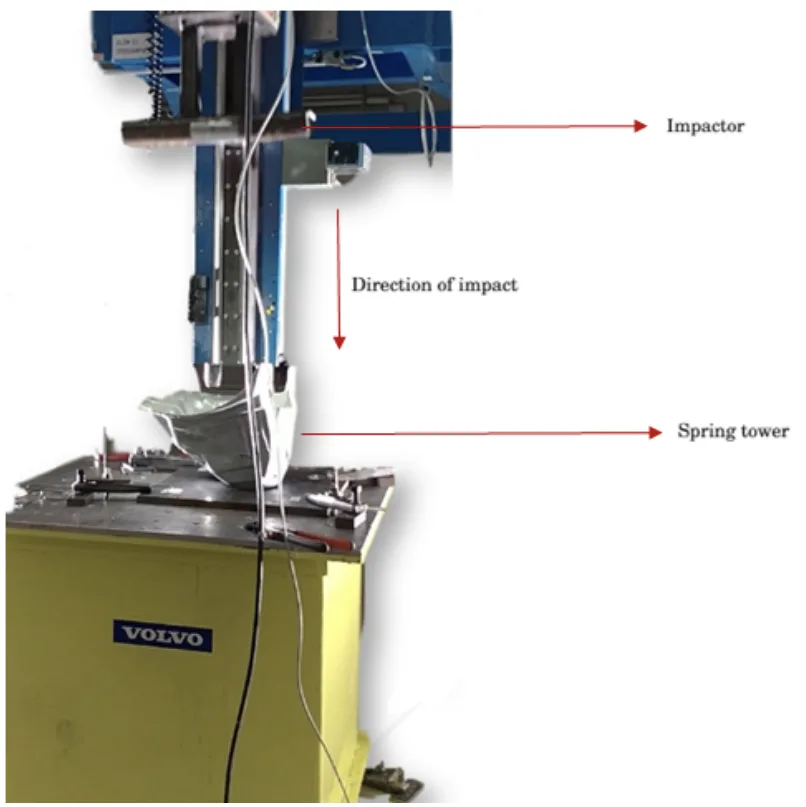
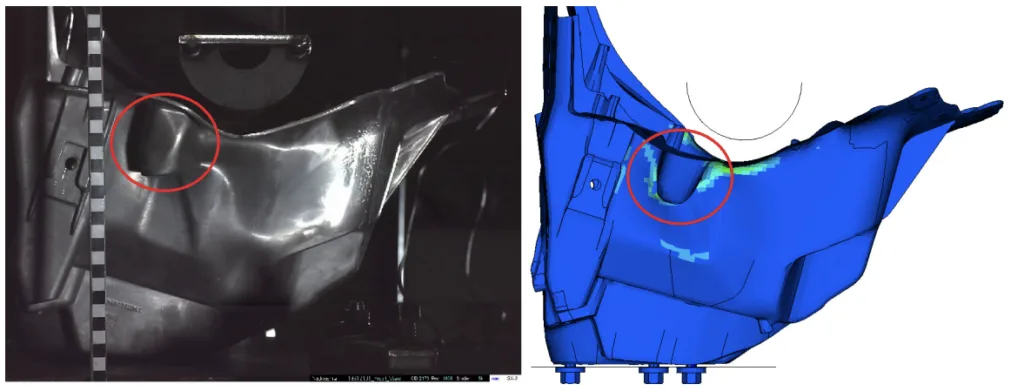
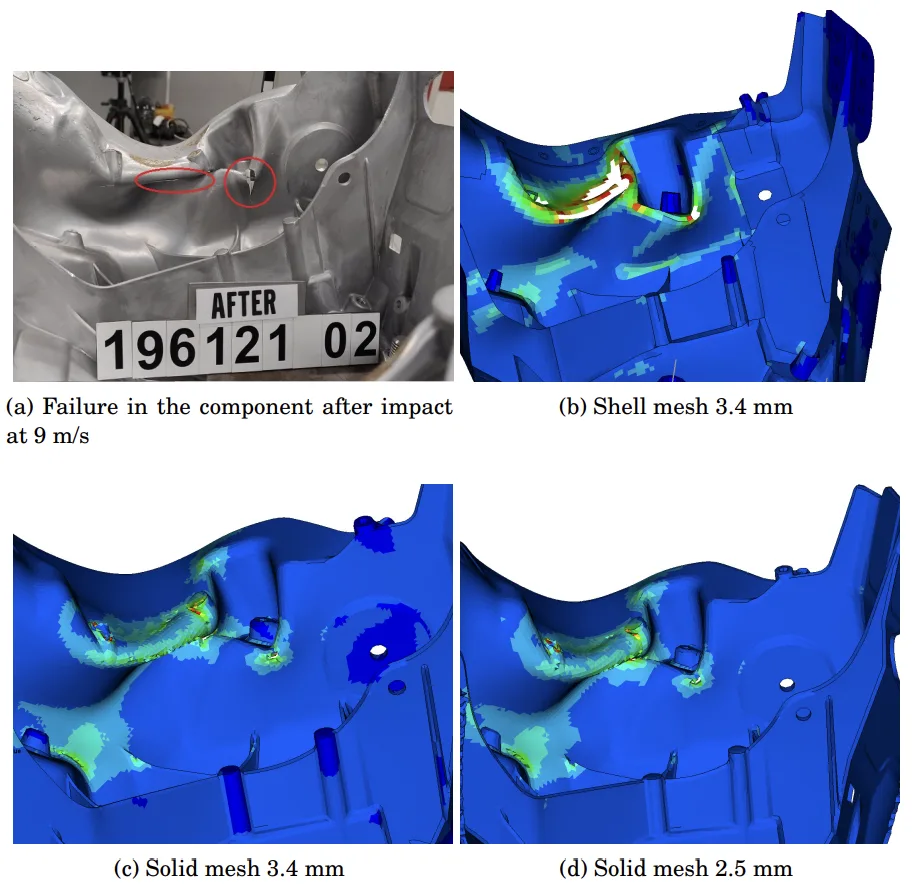
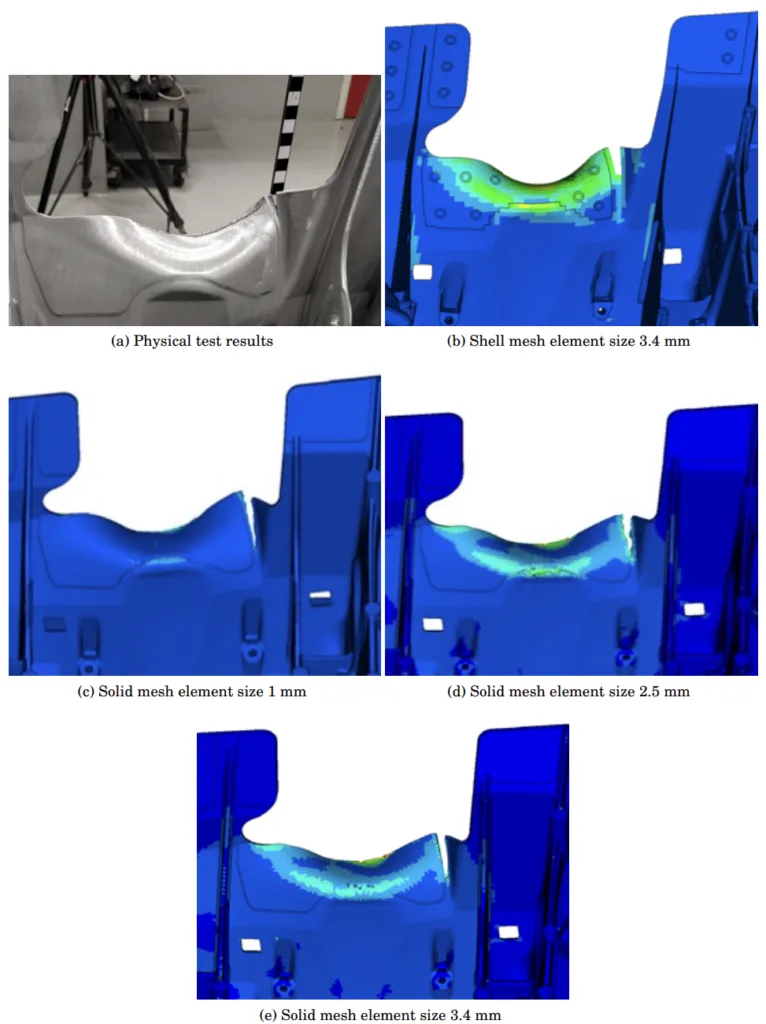
- Figure 5.1: Physical test compared to CAE model with rigid impactor at 6m/s
- Figure 5.2: Incorrect failure prediction in FE model with rigid impactor compared to physical test at 6m/s
- Figure 5.3: Force vs displacement curve of physical and original FE model at 6m/s
- Figure 5.4: Force-displacement curve of physical test with simulations pf shell model at 6 m/s
- Figure 5.5: Failure in FE shell model after impact at 6 m/s with different mesh size
- Figure 5.6: Force-displacement curve of physical test with simulations of solid model at 6m/s
- Figure 5.7: Failure in the FE model with different element size using ELFORM16 at 6 m/s
- Figure 5.8: Failure in the FE model with different element size using ELFORM13 at 6 m/s
- Figure 5.9: Force-displacement curve with shell model at 9 m/s
- Figure 5.10: Force-displacement curve with solid model at 9 m/s
- Figure 5.11: Failure in the physical and the FE model with different element size at 9 m/s
- Figure 5.12: Force-displacement curve with the shell model at 4 m/s
- Figure 5.13: Force-displacement curve with the solid model at 4 m/s
- Figure 5.14: Comparison of physical and FE model with different elements size at 4 m/s
- Figure 5.15: Comparison of physical and FE simulation of load case 2 at 5 m/s
- Figure 5.16: Comparison of physical and FE model at 5 m/s
- Figure 5.17: Force-displacement curve with shell model at 5 m/s
- Figure 5.18: Comparison of solid FE model at 5 m/s
- Figure 5.19: Force-displacement curve with solid model at 5 m/s
- Figure A.1: Failure with rigid impactor at 6 m/s
- Figure A.2: Force-displacement curve with shell model at 7.5m/s
- Figure A.3: Force-displacement curve with solid model at 7.5 m/s
- Figure A.4: Failure in the physical and the FE model with different element size at 7.5 m/s
- Figure A.5: Comparison of Force-displacement curve with shell model at 5 m/s
- Figure A.6: Comparison of Force-displacement curve with solid model at 5 m/s
- Figure A.7: Crack initiation in physical and FE model with different elements size at 5 m/s
- Figure A.8: Force-displacement curve with shell model at 4 m/s
- Figure A.9: Force-displacement curve with solid model at 4 m/s
- Figure A.10: Comparison of the physical and the FE model with various element sizes at 4 m/s
7. Conclusion:
Summary of Key Findings:
Load case 1과 Load case 2의 결과는 올바른 테스트 설정 개발이 결과 상관관계에 중요한 역할을 한다는 것을 보여준다. MATFEM의 제공된 재료 모델(MFGenYld + CrachFEM)은 주조 알루미늄 부품에 대해 물리적 테스트와 유한 요소 결과 간에 양호한 상관관계를 보여준다. Load case 1은 두 번째 Load case에 비해 더 나은 테스트 설정 선택이었다. Load case 2와 마찬가지로 부품에 대한 각 충격으로 인해 플랜지가 구부러지고 나중에 추가 테스트를 위해 테스트 장비에서 부품을 제거하는 것이 지루한 작업이었다. 또한 이 보고서에 제시된 결과는 부품 및 개발된 테스트 설정에만 해당된다. 따라서 차량 차체의 다른 주조 알루미늄 부품도 재료 파손 모델을 검증하기 위해 유사한 방식으로 분석해야 한다.
수행된 시뮬레이션에서 다양한 솔리드 및 쉘 모델의 결과를 비교하면 쉘 요소와 솔리드 요소 모두 부품의 파손에 대한 양호한 예측을 제공할 만큼 충분히 정확하다는 것을 알 수 있다. 솔리드 요소를 사용한 시뮬레이션이 더 정확한 결과를 제공하는 것으로 관찰되었지만 메쉬 의존성이 강했다. coarse mesh를 사용한 이러한 솔리드 요소는 stiff behaviour를 보여 peak force를 과대 평가했다. 솔리드 tetrahedron 메쉬를 개선하면 결과가 더욱 향상되지만 시뮬레이션 시간이 크게 늘어난다. 이를 보상하기 위해 본 연구에서는 explicit finite element 해석에서 selective mass scaling을 적용하여 결과에 거의 또는 전혀 변화 없이 계산 속도를 높일 수 있음을 보여주었다.
explicit dynamic 해석에서 reduced integration element는 fully integrated element와 대조적으로 낮은 계산 비용으로 인해 유리하다. 그러나 fully integrated element formulation은 물리적 테스트와의 비교를 통해 관찰된 바와 같이 파손 예측에 더 적합하다. ELFORM16은 moderate strain에만 적합하고, ELFORM13은 finer mesh에서 large strain에 더 효과적인 것으로 알려져 있지만 [11], 본 연구 결과에서는 finer mesh에서도 ELFORM13을 사용하면 ELFORM16에 비해 결과가 좋지 않았다. 본 연구에서는 moderate strain이 있었고 따라서 ELFORM16이 더 나은 결과를 보였을 가능성이 있다. 따라서 이러한 시나리오에 어떤 요소 formulation이 적합한지 결론을 내리기 위해서는 추가 연구가 필요하다. 이 외에도 본 논문에서 사용된 마찰 값은 추정치이며, 주조 알루미늄 부품의 추가 검증 전에 마찰 계수를 실험적으로 결정해야 한다.
결론적으로 현재 사용 가능한 리소스를 사용하여 주조 알루미늄 부품인 스프링 타워, 평균 요소 크기 3.4 mm의 쉘 메쉬 또는 fine mesh(2.5mm)의 솔리드 모델에 대한 제안된 모델링 기술은 상당히 정확한 것으로 입증되었다. Selective mass scaling은 단순성으로 인해 매력적인 기술이며 모델의 작은 부분만 mass scaling해야 하는 상황에서 계산 시간을 줄이면서 사용할 수 있다.
Academic Significance of the Study:
본 연구는 자동차 산업에서 주조 알루미늄 부품의 CAE 모델링에 대한 핸드북 수준의 심층적인 지침을 제공한다. 특히, 다양한 요소 유형, 요소 크기, 재료 모델 파라미터 및 경계 조건이 CAE 시뮬레이션 결과에 미치는 영향을 체계적으로 분석하여 최적의 모델링 전략을 제시한다. 또한, explicit dynamic 해석에서 selective mass scaling의 효과를 입증하고, 주조 알루미늄 부품의 파손 예측에 적합한 요소 formulation을 비교 분석하여 학문적 가치를 높였다.
Practical Implications:
본 연구의 결과는 자동차 제조업체가 주조 알루미늄 부품을 설계하고 CAE 시뮬레이션을 통해 성능을 예측하는 데 실질적인 도움을 줄 수 있다. 최적의 모델링 기법과 파라미터에 대한 지침은 CAE 시뮬레이션의 정확성과 효율성을 향상시켜 제품 개발 시간과 비용을 절감하는 데 기여할 수 있다. 또한, 드롭 타워 테스트 설정 및 데이터 분석 방법은 주조 알루미늄 부품의 물리적 성능 평가에 대한 표준 절차를 제시할 수 있다.
Limitations of the Study and Areas for Future Research:
본 연구는 특정 주조 알루미늄 합금 스프링 타워 부품 및 특정 하중 조건에 국한되어 있다. 다양한 형상 및 재료의 주조 알루미늄 부품, 다양한 하중 조건에 대한 추가 연구가 필요하다. 또한, 본 연구에서 사용된 마찰 계수는 추정값을 사용하였으므로, 실험적 측정을 통해 마찰 계수를 정확하게 결정하고 CAE 모델에 반영하는 것이 필요하다. 향후 연구에서는 온도, 주조 결함, 미세 조직 등 CAE 모델링에 영향을 미치는 다른 요인들을 고려하여 모델의 정확성을 더욱 향상시킬 수 있을 것이다.
8. References:
- [1] Djukanovic G. Aluminium vs. steel in electric vehicles : the battle goes on. Aluminium insider; 2018. https://aluminiuminsider.com/aluminium-vs-steel-in-electric-vehicles-the-battle-goes-on/.
- [2] Lambert F. Volvo clarifies electrification plan, aims for 50 percent of sales to be fully electric by 2025. electrek; 2018. https://electrek.co/2018/04/25/volvo-electrification-plan-fully-electric/.
- [3] Dharwadkar N, Adivi KP. Modelling of Engine suspension components for crash simulation. Division of Vehicle safety, Department of Applied mechanics, Chalmers University of technology; 2014.
- [4] Dell H, Gese H, Oberhofer G. MF GenYID + CrachFEM User's theory Manual. 2014;.
- [5] Stouffer DC, Dame LT. Inelastic deformation of metals. 1st ed. John Wiley and Sons; 1996.
- [6] Björklund O. Ductile failure in High Strength Steel Sheets. Linköping University; 2014.
- [7] Xue L. Damage accumulation and fracture initiation in uncracked ductile solids subject to triaxial loading. 2006;.
- [8] Brenner F, Buckley M, Gese H, Oberhofer G. Influence of discretisation on stiffness and failure prediction in crashworthiness simulation of automotive high pressure die cast components. 9th European LS-DYNA Conference. 2013 Feb; Available from: https://www.dynalook.com/conferences/9th-european-ls-dyna-conference.
- [9] Hallquist J. LS-DYNA theory manual. Livermore Software Technology Corporation, California; 2006.
- [10] Olovsson L, Simonsson K, Unosson M. Selective mass scaling for explicit finite element analyses. 2005;.
- [11] Erhart T. Review of solid element formulations in LS-DYNA. LS-DYNA forum 2011; 2011.
- [12] Cook RD, Malkus DS, Plesha ME. Concepts and Applications of Finite Element Analysis, 3rd Edition. 3rd ed. Wiley Student Edition; 2004.
9. Copyright:
- This material is "SHREEHARI VEDITHERAKAL SHREEDHARA, SUBRAT RAMAN SINGH"'s paper: Based on "CAE modelling of cast aluminium in automotive structures".
- Paper Source: [DOI URL] (DOI URL 정보가 논문에 명시되어 있지 않아 생략)
This material was created to introduce the above paper, and unauthorized use for commercial purposes is prohibited.
Copyright © 2025 CASTMAN. All rights reserved.