본 자료는 ['CINDAS LLC']에서 발행한 ['Aerospace and High Performance Alloys Database Ferrous • FeUH H-13 August 2008'] 자료를 기반으로 작성되었습니다.
1. 개요:
- 제목: Aerospace and High Performance Alloys Database Ferrous • FeUH H-13 (항공우주 및 고성능 합금 데이터베이스: 철강 • FeUH H-13)
- 저자: J. C. Benedyk
- 발행년도: 2008년 8월
- 발행 학술지/학회: CINDAS LLC
- 키워드: H-13 강, AISI/UNS (T20813), 조성 한계, 열간 금형강, 고급 등급, 최상급 등급, 인성, 열 피로 저항, 합금 원소, 미세 조직, 탄화물 크기, 탄화물 분포, 마르텐사이트강, 공랭 경화, 초고강도강, 열처리, 기계적 성질, 항공기 구조, 착륙 장치 응용, 극한 인장 강도, 열충격 저항, 오스테나이트화, 템퍼링, 2차 경화, 파괴 인성, 피로 강도, 고온, 수소 취성, 내식 코팅, 산화, 바나듐 함량, 바나듐 탄화물, 내마모성, 균질화, 분말 야금, 잉곳 야금, 열간 금형, 금형 재료, 비철 주조, 철강 주조, 열간 성형 작업, 플라스틱 성형, 다이캐스팅 금형, 알루미늄 다이캐스팅, 마그네슘 다이캐스팅, 압출 다이, 컨테이너, 열간 단조 다이, 스탬핑 다이, 열간 전단 블레이드, 플라스틱 금형, 열 피로, 열 침식, 열간 경도, 열충격 저항, 수냉식 다이, 질화, 경질 코팅, 상업적 명칭, 사양, 열처리, 미세 조직, 어닐링, 노멀라이징, 응력 제거, 경화, 오스테나이트화, 퀜칭, 템퍼링, 안정화, 잔류 오스테나이트, 질화, 경도, 상온 경도, 열간 경도, 질화 케이스 경도, 형태 및 사용 조건, 용해 및 주조 공정, 물리적 성질, 열적 성질, 용융 범위, 상변태, 열전도율, 열팽창, 비열, 열 확산율, 밀도, 비중, 전기적 성질, 자기적 성질, 방사율, 감쇠능, 화학적 환경, 일반 부식, 응력 부식, 산화 저항, 수소 저항, 용융 금속에 의한 부식/침식, 액체 금속 유발 취성 저항, 고체 금속 유발 취성 저항, 핵 환경, 기계적 성질, 특정 기계적 성질, NADCA H-13 207-97 H-13 강 합격 기준, 기타 H-13 강 합격 기준, 상온에서의 기계적 성질, 인장 응력-변형률 선도 및 인장 성질, 압축 응력-변형률 선도 및 압축 성질, 충격, 노치 성질, 파괴 인성, 평면 변형률 파괴 인성, 다양한 온도에서의 기계적 성질, 인장 성질, 압축 응력-변형률 선도, 압축 성질, 충격, 굽힘, 비틀림 및 전단, 베어링, 응력 집중, 노치 성질, 파괴 인성, 복합 하중, 연성-취성 천이 온도, 크리프 및 크리프 파단 성질, 피로 성질, 고주기 피로, 저주기 피로, 탄성 성질, 포아송 비, 탄성 계수, 강성률, 접선 계수, 시컨트 계수, 열 피로 성질, CWRU 열 피로 시험, IITRI 열 피로 시험, H-13 강 공급업체의 열 피로 시험, 가공, 성형, 열간 가공, 단조, 기계 가공 및 연삭, 접합, 표면 처리.
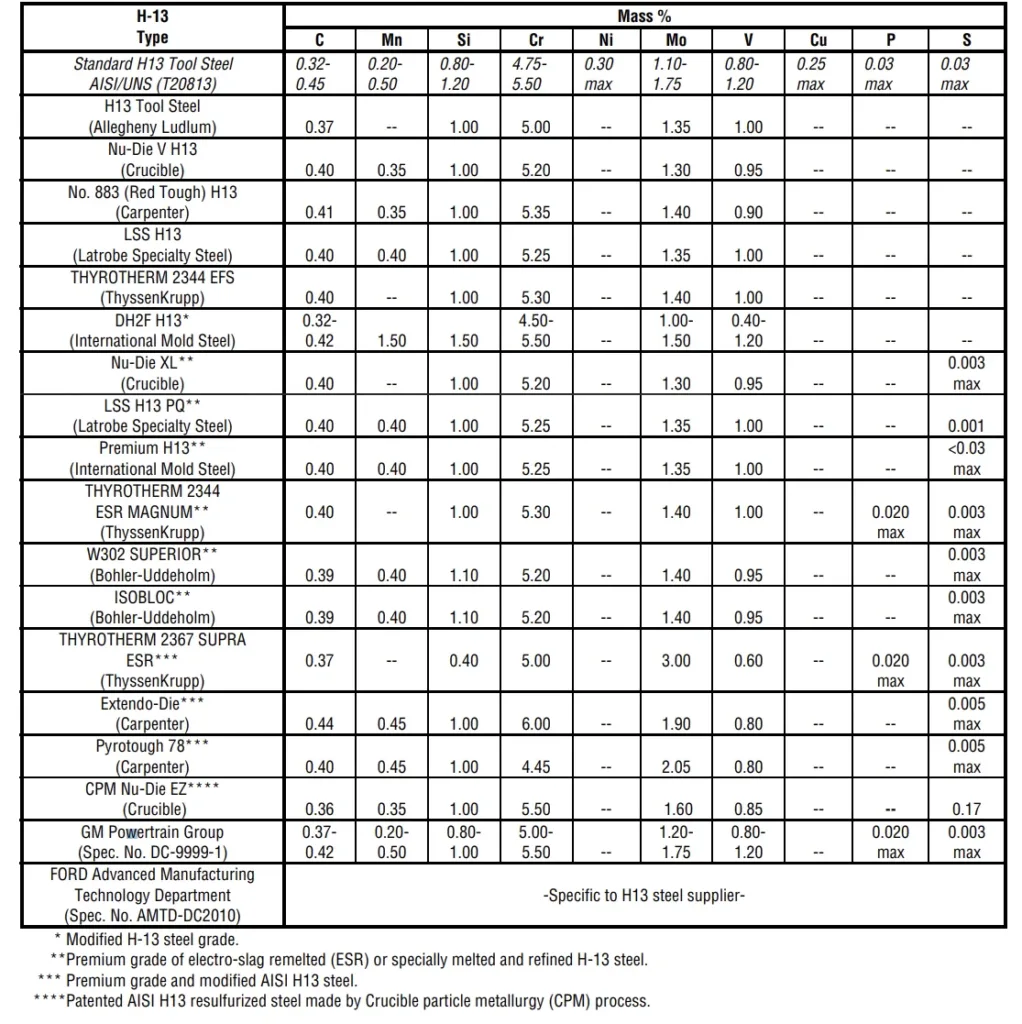
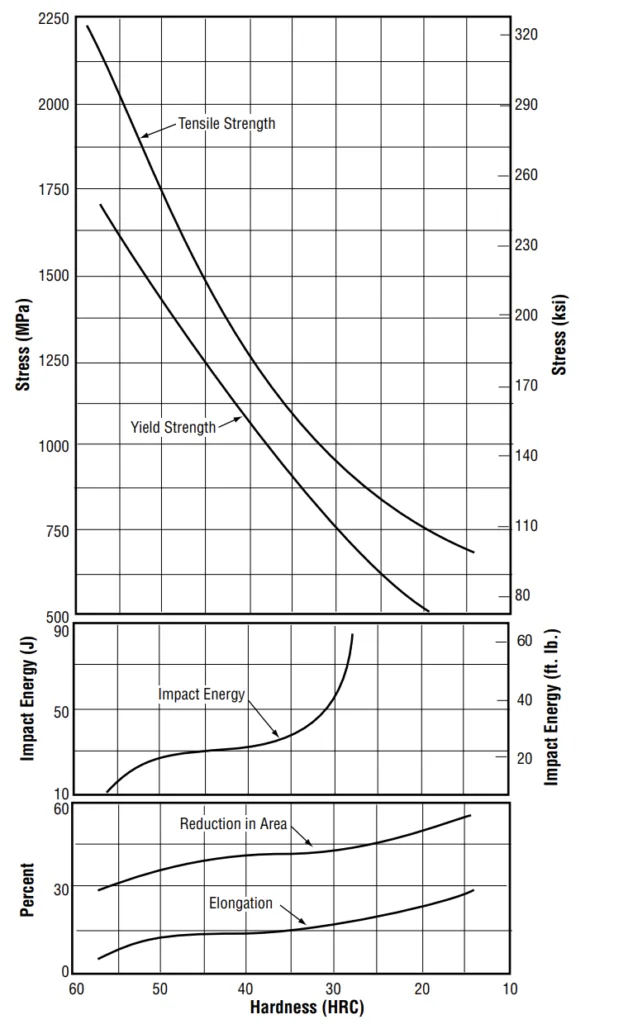

2. 초록 또는 서론
1.0 일반
본 중합금, 마르텐사이트계, 공랭 경화형, 초고강도강은 조성, 열처리 및 여러 성질에서 H-11 및 H-11 Mod 강과 유사합니다. H-11, H-11 Mod 및 H-13 강은 항공기 구조 및 착륙 장치 응용 분야에서 중요한 여러 특성을 나타내는데, 그 중 하나는 뛰어난 열충격 저항성을 유지하면서 300 ksi의 극한 인장 강도로 열처리할 수 있다는 것입니다. 이러한 강종은 일반적으로 오스테나이트화 후 공기, 불활성 기체, 오일 또는 열욕조에서 냉각하여 경화됩니다. 템퍼링 시 템퍼링 곡선에서 2차 경도 최대값을 나타내며, 1050-1100F에서 2회 또는 3회 템퍼링하면 일반적으로 높은 경도(44-48 Rc)와 우수한 파괴 인성 및 상온 및 고온에서 최대 피로 강도와 결합된 높은 상온 극한 인장 강도(220-250 ksi)의 조합을 나타냅니다.
H-13 강은 초고강도 응용 분야의 구조용 강재로서 H-11 Mod 강만큼 일반적으로 사용되지는 않지만, 가용성 또는 약간 더 나은 내마모성 및 기타 H-13 강의 특징이 장점을 제공하는 경우 H-11 Mod 강을 대체할 수 있습니다.
3. 연구 배경:
연구 주제 배경:
- H-13과 같은 열간 금형강은 고온에서 경도와 강도를 유지하는 능력 때문에 다이캐스팅 및 열간 성형에 매우 중요합니다.
- H-13은 알루미늄 및 마그네슘 다이캐스팅 금형, 압출 다이, 열간 단조 및 스탬핑 다이, 열간 전단 블레이드 및 플라스틱 금형에 선호됩니다.
- 주요 특성으로는 열 피로, 열 침식, 내마모성 및 1000F 이상의 온도에서 열간 경도 유지가 있습니다.
- 우수한 열충격 저항성으로 인해 다이와 공구를 내부적으로 수냉식으로 사용할 수 있습니다.
- 내마모성을 향상시키기 위해 질화 또는 경질 코팅과 같은 표면 처리가 사용됩니다.
기존 연구 현황:
- 프리미엄 및 슈페리어 등급의 H-13은 향상된 인성 및 열 피로 저항성을 위해 제어된 조성과 정제된 미세 조직으로 제공됩니다.
- 분말/입자 야금 등급은 기존 잉곳 야금 H-13 강에 비해 향상된 특성을 위해 탄화물 및 황화물 분포가 크게 개선되었습니다.
- 연구에서는 열 응력 순환 조건에서 연화 저항 증가로 인해 열 피로 저항성을 크게 향상시키는 오스테나이트화 온도(1950F 및 2050F)의 효과를 탐구했습니다.
- NADCA는 다이캐스팅 다이에 사용되는 프리미엄 및 슈페리어 등급 H-13에 대한 조성 및 미세 청정도 한계를 지정했습니다.
연구의 필요성:
- 다양한 응용 분야에서 비용 효율적인 H-13 강종을 선택하는 것이 중요합니다.
- H-13의 열처리 및 미세 조직을 이해하는 것은 다이캐스팅 및 열간 성형과 같은 까다로운 응용 분야에서 성능을 최적화하는 데 필수적입니다.
- 상온 및 고온에서 H-13의 기계적 및 물리적 특성을 특성화하는 것은 적절한 재료 선택 및 응용 분야 설계를 위해 필요합니다.
- 질화 및 코팅과 같은 표면 처리를 조사하는 것은 내마모성 및 내식성을 향상시키고 H-13 다이 및 공구의 수명을 연장하는 데 중요합니다.
4. 연구 목적 및 연구 질문:
연구 목적:
본 논문은 주로 다이캐스팅 및 열간 가공 공구 응용 분야를 위해 H-13 다이강에 대한 포괄적인 핸드북 수준의 개요를 제공하는 것을 목표로 하며, 그 특성, 열처리, 제조 및 성능 특성을 다룹니다.
주요 연구:
- H-13 강종의 화학 조성, 상업적 명칭 및 사양.
- 어닐링, 응력 제거, 경화, 템퍼링 및 안정화를 포함한 열처리 절차와 미세 조직 및 경도에 미치는 영향.
- 열전도율, 열팽창, 비열, 밀도 및 탄성률과 같은 물리적 특성.
- 상온 및 고온에서의 기계적 성질, 즉 인장 강도, 항복 강도, 경도, 충격 인성, 파괴 인성, 피로 특성 및 크리프 저항.
- 성형, 기계 가공, 연삭, 용접 및 표면 처리를 포함한 제조 측면.
- 일반 부식, 응력 부식, 산화, 용융 금속 접촉 및 열 피로를 포함한 다양한 환경에서의 성능.
연구 가설:
- 더 높은 오스테나이트화 온도(1950F-2050F)는 기존의 1850F 오스테나이트화에 비해 H-13 강의 열 피로 저항성을 향상시킵니다.
- 제어된 조성과 정제된 미세 조직을 가진 프리미엄 및 슈페리어 등급의 H-13 강은 향상된 인성 및 열 피로 저항성을 나타냅니다.
- 질화 및 PVD 코팅과 같은 표면 처리는 H-13 다이 및 공구의 내마모성, 내식성 및 열 피로 수명을 향상시킵니다.
- 응력 가속 템퍼링은 고온 및 응력이 관련된 사용 조건에서 H-13 강의 경도 및 성능에 영향을 미칩니다.
5. 연구 방법론
연구 설계:
본 논문은 H-13 다이강에 대한 기존 문헌, 사양 및 연구 결과를 편집하고 요약한 설명적 검토입니다. 핸드북, 기술 논문, 재료 사양 및 연구 보고서의 데이터를 기반으로 합니다.
자료 수집 방법:
다음 자료에서 데이터를 수집했습니다.
- 금속 핸드북
- 열처리 지침서
- NADCA 표준
- 강철 제조업체의 재료 데이터 시트(Allegheny Ludlum, Assab Steels, Bohler-Uddeholm, Carpenter, Crucible, Latrobe, ThyssenKrupp, International Mold Steel, MetalTek, Osprey Metals, GM Powertrain Group, FORD)
- 연구 출판물 및 보고서(박사 학위 논문, SDCE 국제 다이캐스팅 회의 논문, 다이캐스팅 연구 재단 보고서, IIT 연구소 보고서, TPTC 기밀 보고서, 저널 논문).
분석 방법:
본 논문은 H-13 강에 대한 포괄적인 개요를 제공하기 위해 다양한 출처의 정보를 종합하고 체계화합니다. 표, 그림 및 설명 텍스트를 사용하여 조성, 특성, 열처리 및 성능에 대한 데이터를 제시합니다. 분석은 주로 질적이며 보고된 데이터와 추세를 요약하고 설명하는 데 중점을 둡니다. 정량적 분석은 속성 값 및 그림의 그래픽 데이터와 같이 인용된 출처에서 직접 데이터를 제시하는 것으로 제한됩니다.
연구 대상 및 범위:
본 논문의 주제는 H-13 열간 금형강입니다. 범위는 다음을 포함합니다.
- 화학 조성, 명칭 및 사양.
- 열처리 및 미세 조직.
- 물리적, 기계적 및 환경적 특성.
- 제조 및 접합 방법.
- 다이캐스팅 및 열간 가공 공구 응용 분야에서의 성능.
6. 주요 연구 결과:
주요 연구 결과:
- 조성 및 등급: 표준 및 프리미엄/슈페리어 등급의 H-13 강은 AISI/UNS (T20813) 및 제어된 불순물(P, S) 및 합금 원소를 가진 수정된 조성으로 정의됩니다. 표 1.4.1, 1.4.2 및 1.4.3은 이러한 조성 및 개재물 한계를 자세히 설명합니다.
- 열처리: 어닐링, 응력 제거, 경화(오스테나이트화 및 퀜칭), 템퍼링 절차는 원하는 특성을 얻는 데 매우 중요합니다. 그림 1.5.4.1, 1.5.5.1, 1.5.5.2, 1.5.5.3, 1.5.5.8, 1.5.8.1, 1.5.8.2, 1.5.8.3, 1.5.8.4, 1.5.8.6 및 1.5.8.7, 그리고 표 1.6.1.1, 1.6.1.2, 1.6.1.3, 1.6.1.4, 1.5.11.2, 1.6.3.1은 열처리 사이클, 상변태 다이어그램, 템퍼링 곡선 및 질화 케이스 특성을 보여줍니다.
- 미세 조직: 어닐링된 미세 조직은 구상화된 탄화물이 있는 페라이트 기질로 구성됩니다(그림 1.5.2.1). 경화 및 템퍼링된 미세 조직은 미세 탄화물이 있는 템퍼드 마르텐사이트입니다(그림 1.5.8.7, 1.5.8.8).
- 경도: 상온 경도는 열처리 및 등급에 따라 다릅니다(표 1.6.1.1, 1.6.1.2, 1.6.1.3, 1.6.1.4, 1.6.3.1). 열간 경도 및 질화 케이스 경도도 특징지어집니다(그림 1.6.2.1, 1.6.2.4, 표 1.6.2.2, 1.6.2.3, 1.6.3.1).
- 기계적 성질: 인장 특성, 충격 인성 및 파괴 인성은 상온 및 고온에서 제시됩니다(표 3.2.1.1, 3.2.1.2, 3.2.1.4, 3.2.3.1, 3.2.3.2, 3.2.3.3, 3.3.1.4, 3.3.3.1, 그림 3.2.1.3, 3.2.7.1.1, 3.2.7.2.2, 3.2.7.2.3, 3.2.7.2.4, 3.2.7.2.5, 3.2.7.2.6, 3.3.1.1, 3.3.1.2, 3.3.1.3, 3.3.3.2, 3.3.3.3, 3.3.3.4, 3.3.3.5, 3.3.7.2.2, 3.3.7.2.4, 3.3.7.2.5, 3.3.9.1).
- 열 피로: CWRU 및 IITRI 열 피로 시험은 오스테나이트화 온도, 강종 및 열처리가 열 피로 저항성에 미치는 영향을 보여줍니다(그림 3.7.1.3, 3.7.1.4, 3.7.2.5, 3.7.3.1, 3.7.3.4, 3.7.3.5, 표 3.7.1.5, 3.7.3.2).
- 부식 및 마모: 질화 및 PVD 코팅은 특히 용융 알루미늄에 대한 내식성 및 내마모성을 향상시킵니다(그림 2.3.1.1, 2.3.3.1, 2.3.3.2, 2.3.5.1, 2.3.5.5, 표 1.5.11.2, 1.6.3.1).
- 물리적 성질: 열전도율 및 열팽창 데이터는 표 2.1.3.1, 2.1.3.2, 2.1.4.1, 2.1.4.2, 2.1.4.3, 2.1.4.4에, 밀도는 표 2.2.1.1에 제공됩니다.
제시된 데이터 분석:
- 열처리 최적화: 더 높은 오스테나이트화 온도(1950-2050F)는 일반적으로 열 피로 및 열간 경도를 향상시키지만, 결정립 크기가 증가할 수 있습니다(그림 1.5.5.4, 1.5.5.5, 1.5.5.6, 3.7.1.3). 최적의 인성 및 치수 안정성을 얻으려면 2회 또는 3회 템퍼링이 중요합니다(그림 1.5.4.1, 1.5.8.4, 표 1.5.8.10).
- 등급 선택: 프리미엄 및 슈페리어 등급은 제어된 조성 및 정제 공정으로 인해 향상된 특성을 제공하므로 다이캐스팅 다이와 같은 중요한 응용 분야에서 사용을 정당화합니다(표 1.4.2, 1.4.3, 그림 3.3.9.1, 3.7.3.1, 3.7.3.4, 3.7.3.5).
- 표면 처리 이점: 질화 및 PVD 코팅은 표면 경도, 내마모성 및 내식성을 크게 향상시켜 특히 용융 알루미늄과 접촉하는 H-13 다이 및 공구의 수명을 연장합니다(그림 1.5.11.1, 2.3.5.1, 2.3.5.5, 표 1.5.11.2, 1.6.3.1).
- 응력 및 온도 효과: 응력 가속 템퍼링 및 열 피로는 열간 가공 응용 분야에서 중요한 고려 사항이며, 경도 및 파손 메커니즘에 영향을 미칩니다(그림 1.5.9.3, 1.5.9.4, 1.5.9.5, 3.7.2.5).
그림 목록:
- 그림 1.5.2.1 NADCA에 따른 어닐링된 H-13 강에 대한 "AS" 품질 미세 조직 차트(허용 가능(AS1-AS9) 및 허용 불가능(AS10-AS18) 미세 조직 표시)—모든 미세 조직은 500배 확대 및 5% Nital로 에칭됨(참조 4)
- 그림 1.5.2.2 NADCA에 따른 어닐링된 H-13 강 블록에 대한 밴딩 미세 분리 차트(허용 가능 및 허용 불가능 미세 조직 표시)—모든 미세 조직은 50배 확대 및 Villella 시약으로 에칭됨(참조 4)
- 그림 1.5.4.1 NADCA 권장 오스테나이트화, 퀜칭 및 템퍼링 열처리 사이클 개략도(H-13 강용)(참조 4)
- 그림 1.5.5.1 H-13 강(0.40 C, 1.05 Si, 5.00 Cr, 1.35 Mo, 1.10V)의 등온 상변태 다이어그램(1850F에서 오스테나이트화)(참조 3)
- 그림 1.5.5.2 프리미엄 등급 H-13 강(Thyrotherm 2344 ESR Magnum, ThyssenKrupp Specialty Steels, Inc.)의 시간-온도 변태 다이어그램(1870–1920F에서 오스테나이트화)(참조 17, 18)
- 그림 1.5.5.3 주어진 오스테나이트화 온도에서 H-13 및 H-11 강의 베이나이트 변태 속도 비교(참조 29)
- 그림 1.5.5.4 H-13 강 및 0.5인치 큐브 시편의 ASTM 결정립 크기 대 오스테나이트화 온도(25–80분 동안 온도에서 유지 후 공랭)(참조 28)
- 그림 1.5.5.5 공랭(AC) 소형 단면 및 더 큰 6인치 및 12인치 원형 H-13 강의 퀜칭 상태에서 탄화물 부피 %(95% 신뢰 구간)(주어진 유지 시간 동안 오스테나이트화 온도 함수)(참조 28)
- 그림 1.5.5.6 공랭(AC) 소형 단면 및 더 큰 6인치 및 12인치 원형 H-13 강의 오스테나이트화 온도 함수로서의 퀜칭 경도(주어진 유지 시간 동안)(참조 28)
- 그림 1.5.5.7 결정립계에서 중간 정도의 탄화물 석출 및 기질에 미세하게 분산된 탄화물을 나타내는 H-13 강의 퀜칭 미세 조직(참조 30)
- 그림 1.5.5.8 1970F에서 오스테나이트화된 H-13 강의 연속 냉각 변태 다이어그램(냉각 곡선 A~E 표시)(참조 30)
- 그림 1.5.8.1 1875F에서 공랭되고 온도에서 2시간 템퍼링된 H-13 강의 템퍼링 온도에 따른 경도 변화(참조 1)
- 그림 1.5.8.2 1850F 및 1800F에서 오스테나이트화되고 공랭되고 2회 템퍼링된 H-13 강의 템퍼링 온도 함수로서의 경도(참조 3)
- 그림 1.5.8.3 1950F 및 1800F에서 오스테나이트화되고 공랭되고 2시간 템퍼링된 H-13 강의 템퍼링 온도 함수로서의 경도(참조 3)
- 그림 1.5.8.4 공랭(AC) 후 H-13 강에 대한 템퍼링 곡선(2회 템퍼링 2시간 + 2시간)(1875, 1950 및 2050F에서 0.5인치 정사각형 시편)(참조 28)
- 그림 1.5.8.5 1750–1950F에서 오스테나이트화 및 퀜칭하여 경화된 H-13 강의 마스터 템퍼링 파라미터 곡선(참조 4)
- 그림 1.5.8.6 1875F에서 오스테나이트화하여 경화된 H-13 강의 시간-온도 템퍼링 다이어그램(참조 32)
- 그림 1.5.8.7 NADCA 합격 기준에 따라 오스테나이트화, 퀜칭 및 템퍼링하여 적절하게 열처리된 H-13 강의 허용 가능한 미세 조직(500배, 5% Nital 에칭)(번호 HS1-HS9는 품질 순위를 나타내지 않으며 모두 허용 가능)(참조 4)
- 그림 1.5.8.8 1850F의 진공로에서 상업적으로 경화되고 2회 템퍼링된(1050F에서 2시간 + 1100F에서 2시간) 6인치 두께 H-13 강 다이 중앙의 일반적인 미세 조직(참조 30)
- 그림 1.5.8.9 1 x 2 x 6인치 블록에서 H13 강의 치수 변화 대 템퍼링 온도(참조 3)
- 그림 1.5.9.1 그림 1.5.9.2–1.5.9.5에 보고된 H-13 강의 응력 가속 템퍼링 연구에 사용된 가변 단면 크리프 시편(참조 25)
- 그림 1.5.9.2 그림 1.5.9.1에 표시된 시험편의 비응력 단면에서 구성된 H-13 강에 대한 템퍼링 곡선(참조 25)
- 그림 1.5.9.3 1000F에서 응력 가속 템퍼링으로 인한 그림 1.5.9.1에 표시된 가변 단면 크리프 시험편을 따라 측정한 H-13 강의 경도 변화(마이크로 경도 조사에서 로크웰 C로 변환)(참조 25)
- 그림 1.5.9.4 1050F에서 응력 가속 템퍼링으로 인한 그림 1.5.9.1에 표시된 가변 단면 크리프 시험편을 따라 측정한 H-13 강의 경도 변화(마이크로 경도 조사에서 로크웰 C로 변환)(참조 25)
- 그림 1.5.9.5 1100F에서 응력 가속 템퍼링으로 인한 그림 1.5.9.1에 표시된 가변 단면 크리프 시험편을 따라 측정한 H-13 강의 경도 변화(마이크로 경도 조사에서 로크웰 C로 변환)(참조 25)
- 그림 1.5.11.1 1890F에서 오스테나이트화 및 3회 템퍼링 후 가스 질화, 이온 질화 및 염욕 질화 H-13 강의 단면 광학 현미경 사진(70배 확대)(참조 34)
- 그림 1.5.11.3 1890F에서 오스테나이트화되고 950F에서 3회 템퍼링되고 망간 인산염으로 표면 활성화된 H-13 강에서 생성된 가스 질화 케이스(975F에서 24시간)(300배 확대)(참조 35)
- 그림 1.6.1.5 4-100시간 동안 고온에 노출된 후 표시된 대로 경화 및 템퍼링된 H-13 강의 상온 경도 또는 "적색 경도"(참조 36)
- 그림 1.6.1.6 1750, 1850 및 2050F에서 오스테나이트화 후 공랭된 H-13 강의 템퍼링 곡선(1100F의 템퍼링 온도에서 시간 함수로서의 경도(Rc 또는 HRC) 표시)(참조 22)
- 그림 1.6.1.7 1750, 1850 및 2050F에서 오스테나이트화 후 공랭된 H-13 강의 템퍼링 곡선(45 HRC로 템퍼링, 1000F의 템퍼링 온도에서 시간 함수로서의 경도(Rc 또는 HRC) 표시)(참조 22)
- 그림 1.6.2.1 1850F에서 오일 퀜칭되고 표시된 템퍼링 온도에서 2 + 2시간 2회 템퍼링된 시편에 대한 H-13 강의 일반적인 열간 경도(참조 37)
- 그림 1.6.2.4 경화된(오스테나이트화 및 퀜칭, 템퍼링되지 않은) H-13 강의 열간 브리넬 경도(HB)에 대한 온도 영향(참조 44)
- 그림 2.3.1.1 pH = 6에서 3.5% NaCl 용액에서 측정한 AISI H-13 강의 동전위 분극 곡선(…) 미처리 시편, (----) 질소 플라즈마 이온 주입(PIII) 처리된 시편(T=300C, t=12시간), (—) 질소 PIII 처리된 시편(T=450C, t=9시간)(참조 45)
- 그림 2.3.3.1 1000F에서 H-13 강과 마레이징강의 비교 산화 저항성(참조 46)
- 그림 2.3.3.2 경화된 H-13 강 시편의 열 피로 균열에서 산화물 축적의 단면도: (a) 50배, 니탈 에칭 및 (b) 500배, 니탈 에칭(참조 22)
- 그림 2.3.5.1 용융 Al-Si-Cu(KS ALDC) 알루미늄 합금에서 1300F에서 43시간 동안 유지된 가스 또는 이온 질화에 의해 별도로 질화되고 기계 가공 및 열처리된 경화 및 템퍼링된 H-13 강 침지 시험편의 부식/침식 깊이 변화(참조 47)
- 그림 2.3.5.2 케이스 웨스턴 리저브 대학교(CWRU)의 가속 세척 시험 장치의 개략도(다이 캐비티에 ~70 in/s로 주입된 용융 알루미늄 합금 사용)(참조 48)
- 그림 2.3.5.3 그림 2.3.5.2에 표시된 CWRU 가속 세척 시험 장치의 다이 캐비티 내 시험 핀 설계 및 위치(참조 48)
- 그림 2.3.5.4 그림 2.3.5.2에 표시된 CWRU 가속 세척 장치에서 시험된 PVD 코팅된 핀 시편의 미세 조직 단면(500배)(참조 48)
- 그림 2.3.5.5 그림 2.3.5.4에 표시된 다양한 유형의 PVD 코팅이 그림 2.3.5.2 및 2.3.5.3에 표시된 CWRU 가속 세척 시험에서 H-13 강 다이캐스팅 코어 핀의 세척 저항성에 미치는 영향(참조 48)
- 그림 2.3.6.1 TPTC U-벤드 액체 아연 취성 시험 절차의 개략도(H-13 강판 시편에 대해 수행): 원래 어닐링된 시편을 U자 모양으로 구부리고, 열처리하고, Δd 변위(왼쪽)에서 초기 소성 흐름 조건으로 구부리고, 패스너로 변위를 유지하고, 용융 아연 욕조에 담금(오른쪽)(참조 50)
- 그림 2.3.6.2 액체 아연 취성 TPTC U-벤드 시험 데이터(Y축: 시간 대 파단 시간(시간); X축: 그림 2.3.6.1에 표시된 시험 조건) H-13 강판 시편에 대해 수행(참조 50)
- 그림 3.2.7.1.1 48 로크웰 C로 열처리되고 상온에서 시험된 H-13 강 Izod 유형 시편의 충격 강도에 대한 노치 반경의 영향(참조 61)
- 그림 3.2.7.2.2 H-13 강 소형 및 대형 시편의 상온 평면 변형률 파괴 인성(KIc) 대 오스테나이트화 온도(a) 및 템퍼링 경도(b)(모든 시편은 오스테나이트화 유지 시간 및 주어진 냉각 조건에 대해 1100F(2 + 2시간)에서 2회 템퍼링됨)(소형 시편의 경우 25분 유지 및 공랭, 6인치 및 12인치 원형의 경우 50분 및 60분 유지 및 시뮬레이션된 실험실 퀜칭)(참조 28)
- 그림 3.2.7.2.3 열처리된 H13 강의 상온 평면 변형률 파괴 인성 KIc 변화(1870F에서 30분 동안 오스테나이트화, 다양한 속도로 퀜칭, 44 HRC로 템퍼링)(퀜칭 속도 함수)(참조 76)
- 그림 3.2.7.2.4 H-13 강 샤르피 V-노치(CVN) 충격 값(1870F에서 30분 동안 오스테나이트화 후 다양한 속도로 퀜칭 및 44 HRC로 템퍼링)(참조 76)
- 그림 3.2.7.2.5 H13/H11 강에 대한 상온에서 (KIc/σys)2와 CVN/σys 간의 상관 관계(참조 77)
- 그림 3.2.7.2.6 상온에서 CVN 및 HRC 데이터에서 계산된 KIc 값과 비교한 상온에서 KIc의 실험값(H13 및 H11 강에 대한 3.2.7.2의 선형 회귀 관계 참조)(참조 77)
- 그림 3.3.1.1 상온 로크웰 C(HRC) 경도 값으로 열처리된 H-13 강의 인장 강도에 대한 고온 영향(참조 44)
- 그림 3.3.1.2 고온(C x 1.8 + 32 = F)이 H-13 강 인장 및 0.2 항복(크리프 한계) 강도(N/mm2 x 0.145 = ksi) 및 단면 수축률에 미치는 영향(상온 강도 수준으로 열처리된 H-13 강)(참조 17)
- 그림 3.3.1.3 H-13 강의 유동 응력(수정된 Johnson-Cook 유동 응력 모델에서 결정 및 OXCUT 컴퓨터 프로그램 및 선반 가공 실험의 실험 데이터로 조정)(800–1200C(1472-2192F) 온도 및 6 x 103 – 9 x 105 1/s 변형률)(원래 46 로크웰 C(HRC) 경도)(MPa x 0.145 = ksi)(참조 57)
- 그림 3.3.3.2 오스테나이트화 온도에 따른 세로 샤르피 V-노치 충격 저항성(H-13 강 시편)(주어진 유지 시간 동안 오스테나이트화, 공랭(소형 시편) 또는 6인치 및 12인치 원형 시편의 시뮬레이션된 퀜칭으로 냉각, 1000F(2 + 2시간)에서 2회 템퍼링, 이후 상온 및 800F에서 시험)(참조 28)
- 그림 3.3.3.3 오스테나이트화 온도에 따른 세로 샤르피 V-노치 충격 저항성(H-13 강 시편)(주어진 유지 시간 동안 오스테나이트화, 공랭(소형 시편) 또는 6인치 및 12인치 원형 시편의 시뮬레이션된 퀜칭으로 냉각, 1100F(2 + 2시간)에서 2회 템퍼링, 이후 상온 및 800F에서 시험)(참조 28)
- 그림 3.3.3.4 오스테나이트화 온도에 따른 세로 샤르피 V-노치 충격 저항성(H-13 강 시편)(주어진 유지 시간 동안 오스테나이트화, 공랭(소형 시편) 또는 6인치 및 12인치 원형 시편의 시뮬레이션된 퀜칭으로 냉각, 1150F(2 + 2시간)에서 2회 템퍼링, 이후 상온 및 800F에서 시험)(참조 28)
- 그림 3.3.3.5 템퍼링 경도에 따른 세로 샤르피 V-노치 충격 저항성(H-13 강 시편)(주어진 유지 시간 동안 1875, 1950 및 2025F에서 오스테나이트화, 공랭(소형 시편) 또는 6인치 및 12인치 원형 시편의 시뮬레이션된 퀜칭으로 냉각, 템퍼링, 이후 상온 및 800F에서 시험)(참조 28)
- 그림 3.3.7.2.1 [그림] 그림 3.3.7.2.2에 표시된 데이터를 얻기 위해 사용된 단간(셰브론 노치) 파괴 인성 시험편(음영 영역은 균열 진전 증가량 표시)(참조 78, 79)
- 그림 3.3.7.2.2 [그림] H13 강, VASCO MA 초고강도강, M 50 고온 베어링강 및 드릴 비트 베어링에 사용되는 S 2 공구강의 KIc(K-Iv ~ KIc)의 온도 의존성(SOLAR STEEL)(이러한 강철에 대한 열처리 및 상온 특성 데이터는 표 3.3.7.2.3에 제시)(참조 78)
- 그림 3.3.9.1 샤르피 V-노치(CVN) 시험을 기반으로 한 DBTT 곡선 표현(저품질 및 고품질 H-13 공구강)(NADCA 207-97(3.1.1)에 따라 열처리됨)(참조 60)
- 그림 3.4.1 H-13 강 크리프 특성(216 ksi 상온 인장 강도로 열처리됨(~44–46 HRC)): 시간 대 변형률(1% 크리프 한계 – 왼쪽 또는 크리프 파단 – 오른쪽)(응력 함수)(표시된 온도에서 N/mm2 x 0.145 = ksi)(참조 17)
- 그림 3.5.1.1 매끄럽고 노치된 시편의 피로 강도(N/mm2 x 0.145 = ksi)(상온에서 완전 역전 인장-압축(R = -1)으로 시험)(경화된 H-13 강)(전기 아크 공기 용융, ESR 및 특수 처리(특허 받은 Isodisc 공정)로 달성된 미세 조직 균질성과 관련)(참조 38)
- 그림 3.5.1.2 [그림] 인장-인장(R = +0.2) 피로 곡선(60Hz에서 측정)(공랭() 및 ESR() H-13 강 열처리 강재 시편)(경화 조건(1850F에서 오스테나이트화, 오일 퀜칭, 1090F에서 2 + 2시간 2회 템퍼링, 48 HRC 경도))(참조 62)
- 그림 3.5.1.3 [그림] 완전 역전 인장-압축(R = -1) 피로 곡선(60Hz에서 측정)(세로( – ESR, – 공랭) 및 가로( – ESR, – 공랭) H-13 강)(경화 조건(1850F에서 오스테나이트화, 오일 퀜칭, 1090F에서 2 + 2시간 2회 템퍼링, 48 HRC 경도))(참조 62)
- 그림 3.7.1.1 [그림] CWRU 열 피로 시험의 개략도(H-13 열 피로 및 내열 균열성 연구에 사용)(용융 A380 알루미늄 1300F(상단)에 시편을 담그고 수냉식 H-13 강 시험편(하단)에 사용된 장치 표시)(참조 22–24, 48)
- 그림 3.7.1.2 [그림] CWRU 시험에서 H-13 강의 열 피로 저항성을 결정하는 데 사용된 열 사이클(다양한 오스테나이트화 온도(그림 3.7.1.3) 및 다양한 유형 및 등급의 H-13 강(그림 3.7.1.4))(참조 22–24)
- 그림 3.7.1.3 [그림] CWRU 시험(그림 3.7.1.1)에서 H-13 강의 열 피로 거동(1750, 1850, 1950 및 2050F에서 오스테나이트화, 공랭, 45 Rc(HRC)로 템퍼링)(평균 최대 균열 길이(미크론(μ))(상단) 및 총 균열 면적 합계(하단)를 사이클 수의 함수로 표시)(참조 22–24)
- 그림 3.7.1.4 [그림] CWRU 시험(그림 3.7.1.1)에서 다양한 유형 및 등급의 H-13 강의 열 피로 거동(1850F에서 오스테나이트화, 공랭, 1100F에서 45 Rc(HRC)로 템퍼링)(평균 최대 균열 길이(미크론(μ))(상단) 및 총 균열 면적 합계(하단)를 사이클 수의 함수로 표시)(참조 22–24)
- 그림 3.7.2.1 [그림] IITRI 열 피로 시험에서 1100~400F 사이의 짧은 열 사이클 동안 H-13 강의 가열 및 냉각 곡선(참조 25, 66)
- 그림 3.7.2.3 [그림] IITRI 열 피로 시험에서 H-13 강의 균열 시작 사이클 수(그림 3.7.2.1에 표시된 사이클에 따름)(강철 청결도 함수)(40개의 임의 필드에서 320배 확대에서 +4mm 산화물 개재물 수로 평가)(참조 66)
- 그림 3.7.2.4 [그림] IITRI 열 피로 시험에서 1100~400F 사이의 긴 사이클 동안 H-13 강의 가열 및 냉각 곡선(참조 25)
- 그림 3.7.2.5 [그림] IITRI 열 피로 핀의 템퍼링(짧고 긴 열 사이클 동안 250–16,000 사이클 동안 핀에 기록된 HRC 경도)(참조 25)
- 그림 3.7.3.1 [그림] Crucible Steel Co. 시험의 열 피로 데이터(1250F에서 용융 A380 알루미늄에 정사각형 시편을 교대로 침지하고 200F의 수조에서 퀜칭)(10,000 사이클마다 균열 검사)(참조 43)
- 그림 3.7.3.3 [그림] EWK/Thyssen Krupp Specialty Steel의 열 피로 시험 장치: 부식 방지를 위한 Ar 분위기, 1200F까지 유도 가열, 상온 또는 상온 근처에서 유지되고 pH = 10.5로 습윤성을 개선하기 위한 수조, 30 x 8인치 단조 슬래브에서 가로 방향으로 절단되고 거칠게 가공된 2 x 2 x 0.40인치 H-13 강 시편, 시편은 44-46 HRC로 경화 및 템퍼링되고 미세하게 연마됨(참조 68)
- 그림 3.7.3.4 [그림] 총 균열 길이 측정값(우수한 등급의 AISI H-13(Thyrotherm 2344 EFS Supra) 및 수정된 등급의 H-13(Thyrotherm 2367 EFS Supra) 시편)(44–46 HRC로 열처리되고 그림 3.7.3.3에 표시된 EWK/Thyssen Krupp Specialty Steel 열 피로 장치에서 시험됨)(참조 68)
- 그림 3.7.3.5 [그림] 샘플에서 개발된 일부 열 피로 균열의 200배 현미경 평가(그림 3.7.3.4)(EWK/Thyssen Krupp Specialty Steel 열 피로 시험(그림 3.7.3.3)에서)(참조 68)
7. 결론:
주요 결과 요약:
- H-13 강은 우수한 템퍼 저항성, 열간 경도 및 열충격 저항성으로 인해 다이캐스팅 및 열간 성형에 널리 사용되는 다용도 열간 금형강입니다.
- 최적의 열처리, 특히 오스테나이트화 및 템퍼링은 원하는 기계적 성질과 성능을 달성하는 데 매우 중요합니다. 더 높은 오스테나이트화 온도는 열 피로 저항성을 향상시킬 수 있습니다.
- 프리미엄 및 슈페리어 등급은 분말 야금 경로와 함께 기존 H-13 강에 비해 향상된 특성을 제공합니다.
- 질화 및 PVD 코팅과 같은 표면 처리는 내마모성 및 내식성을 향상시켜 공구 수명을 연장하는 데 효과적입니다.
- 응력 가속 템퍼링 및 열 피로 거동을 이해하는 것은 까다로운 응용 분야에서 H-13 부품의 수명을 예측하고 개선하는 데 필수적입니다.
연구의 학문적 중요성:
- 본 논문은 H-13 강에 대한 데이터와 연구 결과를 포괄적으로 편집하여 재료 과학 및 제조 엔지니어링 분야의 전문가와 연구원에게 귀중한 자료를 제공합니다.
- 조성, 열처리, 미세 조직, 특성 및 H-13 강의 성능 간의 복잡한 상호 작용을 강조하여 열간 금형강 기술의 추가 연구 개발에 대한 통찰력을 제공합니다.
- 열 피로 시험 방법론(CWRU, IITRI 및 공급업체별 시험)에 대한 자세한 검토는 다이 재료에 대한 열 피로 평가의 이해 및 표준화에 기여합니다.
실용적 의미:
- 제시된 정보는 H-13 강 공구에 대한 정보에 입각한 재료 선택 및 열처리 설계를 지원하여 다이캐스팅, 단조, 압출 및 성형 응용 분야에서 성능을 최적화하고 수명을 연장합니다.
- 오스테나이트화 온도 및 퀜칭 속도와 같은 가공 매개변수의 영향을 이해하면 특정 응용 분야 요구 사항을 충족하기 위해 맞춤형 열처리가 가능합니다.
- 표면 처리 검토는 내마모성 및 내식성을 향상시키고 제조 공정에서 가동 중지 시간을 줄이고 생산성을 향상시키는 데 지침을 제공합니다.
- 다양한 온도에서의 기계적 및 물리적 특성에 대한 데이터는 H-13 공구 및 부품의 정확한 설계 및 시뮬레이션에 매우 중요합니다.
연구의 한계 및 향후 연구 분야:
- 본 논문은 기존 문헌 및 데이터의 요약이며 독창적인 실험 연구가 아닙니다.
- 분석 깊이는 검토된 문서의 범위에 의해 제한됩니다.
- 추가 연구가 필요합니다.
- 산업 다이캐스팅 및 열간 성형 환경에서 고급 H-13 등급 및 표면 처리의 장기 성능을 조사합니다.
- H-13 강에서 열 피로 및 응력 가속 템퍼링에 대한 보다 정확한 예측 모델을 개발합니다.
- 향상된 H-13 강 특성을 위한 분말 야금 공정 및 합금 전략을 최적화합니다.
- 다양한 연구 및 공급업체 간의 데이터 비교 가능성을 개선하기 위해 열 피로 시험 방법을 표준화합니다.
8. 참고 문헌:
- 1. Metals Handbook Ninth Edition. Volume 1. Properties and Selection: Irons and Steels, American Society for Metals (now ASM International), 1978, pp. 437–39.
- 2. Metals Handbook Ninth Edition. Volume 3. Properties and Selection: Stainless Steels, Tool Materials and Special-Purpose Metals, American Society for Metals (now ASM International), 1980, pp. 421–69.
- 3. HEAT TREATER’S GUIDE: Practices and Procedures for Irons and Steels, ASM International, 2nd Ed., 1998, pp. 600-605.
- 4. Premium and Superior Quality H-13 Steel and Heat Treatment Acceptance Criteria for Pressure Die Casting Dies: NADCA #207-2003, North American Die Casting Association (NADCA), River Grove, Illinois, 2003.
- 5. Allegheny Ludlum H-13 Tool Steel, UNS T20813, DATA SHEET.
- 6. Assab Steels 8407 SUPREME Hot Work Steel, DATA SHEET.
- 7. Bohler-Uddeholm ORVAR H-13 Hot Work Tool Steel, DATA SHEET.
- 8. Bohler-Uddeholm SUPERIOR H-13 Hot Work Tool Steel, DATA SHEET.
- 9. Bohler-Uddeholm ISOBLOC H-13 Hot Work Tool Steel, DATA SHEET.
- Carpenter Pyrotough® 78 Hot Work Die Steel. DATA SHEET.
- Carpenter No. 883® Hot Work Die Steel (Red-Tough) (AISI H-13), DATA SHEET.
- Crucible Nu-Die® XL (Premium Quality AISI H-13) Tool Steel, DATA SHEET.
- International Mold Steel DH2F Pre-Hardened H-13-Type Mold Steel, DATA SHEET.
- International Mold Steel Premium H-13 Hot Work Die and Mold Steel, DATA SHEET.
- Latrobe LSS® H-13 Tool Steel, DATA SHEET.
- Latrobe VDC® H-13 Tool Steel, DATA SHEET.
- ThyssenKrupp Specialty Steels THYROTHERM 2344, DATA SHEET.
- ThyssenKrupp Specialty Steels THYROTHERM 2344 ESR MAGNUM, DATA SHEET.
- ThyssenKrupp Specialty Steels THYROTHERM 2367 SUPRA ESR, DATA SHEET.
- Premium Grade H-13/Hot Work Tool Material Standard Specification: Die Insert and Heat Treating Specification, Spec. No. DC-9999-1, GM Powertrain Group, 6-29-2001.
- Die Insert Material and Heat Treatment Performance Requirements: General Applications, Spec. No. AMTD DC2010, FORD Advanced Manufacturing Technology Development, 17 February 2003.
- Benedyk, J. C., Thermal Fatigue Behavior of H-13 Die Steels, Ph.D. Thesis, Case Western Reserve University, January, 1969.
- Benedyk, J. C., Moracz, D. J., and Wallace, J. F., “Thermal Fatigue Behavior of Die Materials for Aluminum Die Casting, ” Paper No. 111, 6th SDCE (Society of Die Casting Engineers) International Die Casting Congress, November 16–19, 1970.
- Dunn, R. P., “Thermal Fatigue Behavior of H-13 Steel & Other Die Materials for Aluminum Die Casting, ” Report of the Task Group on Materials & Surface Treatments for Dies, Die Casting Research Foundation 1969 Annual Meeting, October 8, 1969.
- Nolen, R. K., Benedyk, J. C., and Howes, M. A. H., Investigation of Strain Softening Occurring during Thermal Fatigue, Internal Research and Development Project Final Report on Project B1051, IIT Research Institute, October 23, 1969.
- Purohit, S. and Tszeng, C., “Carbide Dissolution in H-13 Tool Steel during Austenitization, ” TPTC (Thermal Processing Technology Center, Illinois Institute of Technology) Project Review, 2003.
- Pacyna, J. and Mazur, A., “The Influence of Grain Size upon the Fracture Toughness of the Hot-Work Tool Steel, ” Scandinavian J. of Metallurgy, No. 12, 1983, pp. 22–28.
- Schmidt, M. L., “Effect of Austenitizing Temperature on the Structure and Mechanical Property Behavior of Laboratory Treated Specimens and Large Section Sizes of H-13 Tool Steel, ” Paper No. G-T87-006, 14th SDCE (Society of Die Casting Engineers) International Die Casting Congress, May 11–14, 1987.
- Stuhl, J. H. and Schindler, A. M., “New Materials Study of 5% Chromium Type Steels for Use in Die Casting Dies, ” Paper No. G-T75-053, 8th SDCE (Society of Die Casting Engineers) International Die Casting Congress, May 17–20, 1975.
- Conybear, J. A., “Vacuum Hardening of H-13 Die Steels: Experience with Convective Assisted Heating and Isothermal Holding in Regard to Distortion and Metallurgical Properties, ” reprinted from Industrial Heating, August, 1993.
- Alloy Tool Steel SPEC FACTS A.I.S.I. H-13, DATA SHEET.
- Thelning, K. E., “How Far Can H-13 Die Casting Die Steel Be Improved, ” Paper No. 114, 6th SDCE (Society of Die Casting Engineers) International Die Casting Congress, November 16–19, 1970.
- Huffman, D. D. “Avoiding Retained Austenite in Tool Steels, ” Source Book on Heat Treating: Vol. II – Production and Engineering Practices, American Society for Metals (now ASM International), December, 1974, pp. 276–79.
- Y.-M. Rhyim, et al., “Effect of Surface Treatment on the Life of AISI H-13 Steel Core Pin for Die Casting, ” Key Engineering Materials, Vols. 326–28, 2006, pp. 1181–84.
- Metals Handbook Ninth Edition. Volume 9: Metallography and Microstructures, American Society for Metals (now ASM International), 1985, p. 228.
- Cremisio, R. S., Pridgeon, J. W., and Mills, D. W, Hot Work Materials Processing and Metallurgy for Hot Extrusion Applications, AJAX Forging and Casting Co., Allegheny Ludlum Industries Co., Ferndale, MI, 1977, pp. 24–25.
- Metals Handbook Ninth Edition. Volume 1. Properties and Selection: Irons and Steels, American Society for Metals (now ASM International), 1978, p. 440.
- Schindler, A. M., Kulmberg, A., and Stuhl, J. H., “Thermal Fatigue of H-13 in Die Casting Applications, ” Paper No. G-T77-065, 9th SDCE (Society of Die Casting Engineers) International Die Casting Congress, June 6–9, 1977.
- Metals Handbook Ninth Edition. Volume 9: Metallography and Microstructures, American Society for Metals (now ASM International), 1985, p. 271.
- MetalTek MTek T90813 H-13 Tool Steel, DATA SHEET.
- Osprey Metals H-13 Tool Steel Powder Grades, DATA SHEETS.
- Cremisio, R. S., Pridgeon, J. W., and Mills, D. W, Hot Work Materials Processing and Metallurgy for Hot Extrusion Applications, AJAX Forging and Casting Co., Allegheny Ludlum Industries Co., Ferndale, MI, 1977, pp. 4–13.
- Crucible CPM® Nu-Die® EZ, DATA SHEET, Issue #2.
- Engineering Properties of Steel: Hot Work Tool Steels, ASM International, 1982, pp. 457–62.
- da Silva, L. L. G., Ueda, M., and Nakazato, R. Z., “Enhanced Corrosion Resistance of AISI H13 Steel Treated by Nitrogen Plasma Immersion Ion Implantation, ” Surf. Coat. Techn., 201, 2007, pp. 8291–94.
- Hamaker, J. C. and Yates, D. H., “A Forward Look at the New Die Steels, ” Paper No. 1201, 4th SDCE (Society of Die Casting Engineers) International Die Casting Congress, November 14–17, 1966.
- Youn, K.-T., et al., “An Evaluation of Thermal Fatigue Cracking and Chemical Reaction in Die Casting Mould, ”Key Engineering Materials, Vols. 345-346, 2007, pp. 701–04.
- Test data and review of latest research on H-13 steel kindly provided by Prof. J. Wallace of CWRU.
- Kamdar, M. H., “Liquid-Metal Embrittlement, ” Metals Handbook. Volume 11. Failure Analysis and Prevention, ASM International, 1986, pp. 225–38.
- Kim, T., et al., “Liquid Zinc Embrittlement Study of H 13 Steel in Various Austenitized and Tempered Conditions, ” TPTC Confidential Report for Industrial Client (data kindly provided with permission), 2008.
- Kamdar, M. H., “Embrittlement by Solid-Metal Environments, ” Metals Handbook. Volume 11. Failure Analysis and Prevention, ASM International, 1986, pp. 239–44.
- Takao, et al., “Crack Initiation and Propagation Mechanism of Die for Extruding 7000 Series Alloy, ” Keikinzoku Fakkai Koen Gaiyo, 1993, Vol. 84, pp. 275–76 (in Japanese).
- Benedyk, J., et al., “Literature Survey on H-13 Extrusion Die Failure (I), ” TPTC Confidential Report for Industrial Client, 2003.
- Gordon, P., “Metal-Induced Embrittlement of Metals – An Evaluation of Embrittler Transport Mechanisms, ” Met. Trans. A, V. 9A, Feb., 1978, pp. 267–73.
- Kim, C. D, “Hydrogen-Damage Failures, ” Metals Handbook. Volume 11. Failure Analysis and Prevention, ASM International, 1986, pp. 245–51.
- Rosenfield, A. R. and Marshall, C. W., “Ductile-to Brittle Fracture Transition, ” Metals Handbook. Volume 11. Failure Analysis and Prevention, ASM International, 1986, pp.69, 100.
- Shatla, M., Kerk, C., and Altan, T., “Process Modeling in Machining. Part I: Determination of Flow Stress Data, ” International J. of Machine Tools & Manufacture, Vol. 41, 2001, pp. 1511–34.
- Crucible Nu-Die® V (AISI H-13) Tool Steel, Issue #13, DATA SHEET.
- Plane Strain Fracture Toughness (KIc) Data Handbook for Metals, Army Materials and Mechanics Research Center, Watertown, MA, December, 1973.
- Brada, G., “Effects of Quench Rate and Impact Test Temperature on the Toughness and Microstructure of H13, ” Die Casting Engineer, May, 2002, pp. 22–24.
- Huffman, D. D., “Aluminum Extrusion Tooling: Where Do We Stand?, ” International Extrusion Technology Seminar, 1969, paper no. 23.
- Philip, T.V., “ESR: A Means of Improving Transverse Mechanical Properties in Tool and Die Steels, ” Metals Technology, Dec., 1975, p. 554.
- Manson, S. S., Thermal Stress and Low-Cycle Fatigue, McGraw-Hill, 1966, pp. 125–91.
- Manson, S. S. and Halford, G., “A Method of Estimating High-Temperature Low-Cycle Fatigue Behavior of Materials, ” NASA Lewis Research Center, Cleveland, Ohio, January, 1967.
- Barrow, B. J., “The Thermal Fatigue Resistance of H-13 Die Steel for Aluminum Die Casting Dies, ” NASA Technical Memorandum 83331, NASA Lewis Research Center, Cleveland, Ohio, August, 1982.
- Rostoker, W., et al., The Metallurgy of Thermal Fatigue: Summary Report IV on Thermal Fatigue Resistance of Martensitic Steels, IITRI-B879-20, July 17, 1967.
- Alloy Tool Steel SPEC FACTS Premium Grade H-13, DATA SHEET.
- Ehrhardt, R., et al., “Improving the Heat Checking Characteristics of AISI H13 by Modification of the Chemical Composition, ” Die Casting Engineer, Nov., 2003, pp. 30–37.
- Metals Handbook Ninth Edition. Vol. 16. Machining, ASM International, 1989, pp. 712–26.
- Metals Handbook Ninth Edition. Vol. 16. Machining, ASM International, 1989, pp. 557–64)
- Bosheh, S. S. and Mativenga, P. T., “White Layer Formation in Hard Turning of H13 Tool Steel at high Cutting Speeds Using CBN Tooling, ” International J. of Machine Tools & Manufacture, Vol. 46, 2006, pp. 225–33.
- Metals Handbook Ninth Edition. Vol. 16. Machining, ASM International, 1989, pp. 514–19)
- Extrusion Dies & Tooling Manual: Recommended Handling and Maintenance, Aluminum Extruders Council, pp. 16-17.
- Björk, T., Westergård, R., and Hogmark, S., “Wear of Surface Treated Dies for Aluminium Extrusion – A Case Study, ” Wear, Vol. 249, 2001, pp. 316–23.
- Müller, K. B., “Deposition of Hard Films on Hot Working Steel Dies for Aluminium, ” J. of Materials Processing Technology, Vols. 130-131, 2002, pp. 423–37.
- Okuno, T., “Effect of Microstructure on the Toughness of Hot Work Tool Steels, H13, H10, H19,” Tran. ISIJ, Research Article, Vol. 27, 1987, pp. 51–59.
- Leskovšek, V., “Correlation Between the KIc,the HRC and the Charpy V-Notch Test Results for H11/H13 Hot work Tool Steels at Room Temperature,” Steel Research Int., Vol. 79, No. 4, 2008, pp. 306–13.
- Barker, L. M. and Leslie, W. C.,” Short Rod KIc Tests of Several Steels at Temperatures to 700K,” Fracture 1977, Vol. 2, ICF4, Waterloo, Canada, June 19–24, 1977, MS311, pp. 305–11.
- ASTM E 1304: Standard Test Method for Plane-Strain (Chevron-Notch) Fracture Toughness of Metallic Materials.
- Qamar, S. Z., et al., “Regression-based CVN-K-Ic Models for Hot Work Tool Steels,” Mater. Sci. and Eng., Vol. A 430, 2006, pp. 208–15.
9. 저작권:
- 본 자료는 "[저자: J. C. Benedyk]"의 논문: "[Aerospace and High Performance Alloys Database Ferrous • FeUH H-13 August 2008]"을 기반으로 합니다.
- 논문 출처: [문서에서 사용 불가]
본 자료는 상기 논문을 기반으로 요약되었으며, 상업적 목적으로 무단 사용하는 것을 금지합니다.
Copyright © 2025 CASTMAN. All rights reserved.