본 논문 요약은 ['INTERNATIONAL JOURNAL OF RESEARCH IN ADVANCED ENGINEERING TECHNOLOGIES']에서 발행한 ['DESIGN AND WEIGHT OPTIMIZATION OF OIL PAN BY FE ANALYSIS'] 논문을 기반으로 작성되었습니다.
1. 개요:
- 제목: DESIGN AND WEIGHT OPTIMIZATION OF OIL PAN BY FE ANALYSIS (FE 해석을 이용한 오일 팬의 설계 및 무게 최적화)
- 저자: SINGATHI SHARATH KUMAR, P. SUBRAMANYAM
- 발행 연도: 2015년
- 발행 학술지/학회: INTERNATIONAL JOURNAL OF RESEARCH IN ADVANCED ENGINEERING TECHNOLOGIES (국제 첨단 공학 기술 연구 저널)
- 키워드: Oil pan (오일 팬), Manufacturing Methods (제조 방법), Cost Analysis (원가 분석), Design (설계), Analysis (해석)
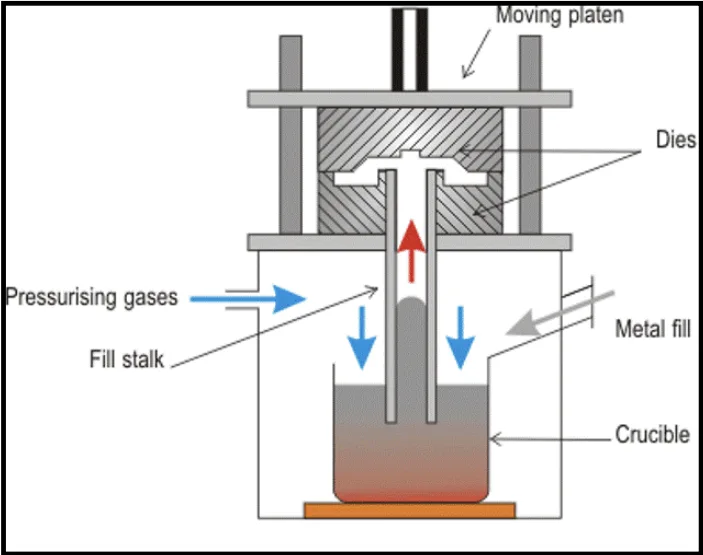
2. 초록 또는 서론
초록 - 왕복 운동형 내연 기관에서 오일 팬은 크랭크축 하우징 역할을 합니다. 이 밀폐 구조는 엔진에서 가장 큰 공동을 형성하며, 멀티 실린더 엔진에서는 일반적으로 하나 또는 여러 개의 실린더 블록에 통합되어 실린더 하단에 위치합니다. 오일 팬은 엔진 하단에 위치하며 엔진 오일을 저장하는 데 사용됩니다. 필요할 때 오일 팬에서 엔진으로 오일이 펌핑됩니다.
본 프로젝트에서는 잠수함 엔진에 사용되는 오일 팬 모델링을 수행합니다. 본 프로젝트의 목표는 CAD 소프트웨어를 사용하여 오일 팬을 모델링하고, 적합한 주조 제조 공정을 선택하여 주조 금형을 설계하고, CAM 소프트웨어를 사용하여 CNC 프로그램을 생성하며, 주조 금형의 불필요한 영역에서 무게를 줄이는 것입니다.
초기에는 금형 설계 및 해석 조건에 대한 데이터를 수집합니다. 다음 단계에서는 추가 연구를 위해 Pro-Engineer를 사용하여 모델을 생성합니다. 금형 조립 모델링을 위해 금형 설계 계산을 수행합니다. 금형 준비 후, 오일 팬에 적합한 재료를 선택하여 금형 구조를 최적화하고 무게를 줄이기 위해 구조 해석을 수행합니다. 모델링, 금형 설계 및 제조(CNC)는 Pro/Engineer 소프트웨어를 사용하여 수행됩니다.
서론 - 오일 팬 소개
오일 팬은 일반적으로 자동차 및 기타 유사한 응용 분야의 4행정 내연 기관의 하단을 밀봉하는 부품입니다. 미국에서는 오일 팬으로 알려져 있지만, 세계 다른 지역에서는 오일 섬프라고 부를 수 있습니다. 주요 목적은 크랭크 케이스의 최하단 부분을 형성하고 엔진 오일이 엔진을 순환하기 전후에 오일을 담는 것입니다. 오일 팬을 제거하면 일반적으로 크랭크축, 오일 픽업 및 딥스틱 하단부가 드러납니다.
정상적인 엔진 작동 중에는 오일 펌프가 팬에서 오일을 끌어와 엔진을 순환시키며, 여기서 오일은 다양한 부품을 윤활하는 데 사용됩니다. 오일이 엔진을 통과한 후에는 오일 팬으로 되돌아갑니다. 이러한 습식 섬프 시스템에서 엔진이 담을 수 있는 오일의 양은 오일 팬의 크기와 직접적인 관련이 있습니다. 엔진은 크랭크축이 잠기면 오일이 공기를 흡입하여 오일 펌프가 엔진을 순환시키기 어렵거나 불가능해지므로 팬에 들어갈 수 있는 양 이상의 오일을 담을 수 없습니다.
엔진 오일을 교환하는 데 사용되는 드레인 플러그는 일반적으로 오일 팬의 어딘가에 위치합니다. 오일 드레인 플러그를 쉽게 찾는 방법은 팬을 찾은 다음 가장 낮은 지점을 찾는 것입니다. 팬은 기울어져 있거나, 한쪽 끝이 불룩하거나, 엔진 위치 때문에 약간 기울어져 있을 수 있습니다. 이 낮은 지점은 일반적으로 드레인 플러그가 위치하여 팬의 오일을 거의 모두 배출할 수 있는 곳입니다.
레이스 또는 고성능 자동차와 같은 특정 엔진은 드라이 섬프 시스템으로 알려진 것을 사용할 수 있습니다. 크랭크 케이스에 모든 오일을 저장하는 대신, 이러한 엔진에는 펌핑되는 분리된 저장소가 있습니다. 이러한 엔진의 오일 팬은 일반적으로 습식 섬프 시스템의 오일 팬보다 훨씬 작습니다. 오일은 윤활에 사용된 후 저장소로 되돌아가기 때문입니다.
3. 연구 배경:
연구 주제 배경:
왕복 운동형 내연 기관에서 오일 팬은 크랭크축 하우징 역할을 합니다. 이 밀폐 구조는 엔진에서 가장 큰 공동을 형성하며 실린더 하단에 위치합니다. 오일 팬은 엔진 하단에 위치하며 엔진 오일을 저장하는 데 사용됩니다.
기존 연구 현황:
본 섹션에서는 명시적으로 언급되지 않았습니다.
연구의 필요성:
본 프로젝트에서는 잠수함 엔진에 사용되는 오일 팬 모델링을 수행합니다. 본 프로젝트의 목표는 CAD 소프트웨어를 사용하여 오일 팬을 모델링하고, 적합한 주조 제조 공정을 선택하여 주조 금형을 설계하고, CAM 소프트웨어를 사용하여 CNC 프로그램을 생성하며, 주조 금형의 불필요한 영역에서 무게를 줄이는 것입니다. 초기에는 금형 설계 및 해석 조건에 대한 데이터를 수집합니다. 다음 단계에서는 추가 연구를 위해 Pro-Engineer를 사용하여 모델을 생성합니다. 금형 조립 모델링을 위해 금형 설계 계산을 수행합니다. 금형 준비 후, 오일 팬에 적합한 재료를 선택하여 금형 구조를 최적화하고 무게를 줄이기 위해 구조 해석을 수행합니다. 모델링, 금형 설계 및 제조(CNC)는 Pro/Engineer 소프트웨어를 사용하여 수행됩니다.
4. 연구 목적 및 연구 질문:
연구 목적:
본 프로젝트의 목표는 CAD 소프트웨어를 사용하여 오일 팬을 모델링하고, 적합한 주조 제조 공정을 선택하여 주조 금형을 설계하고, CAM 소프트웨어를 사용하여 CNC 프로그램을 생성하며, 주조 금형의 불필요한 영역에서 무게를 줄이는 것입니다. 또한 오일 팬에 적합한 재료를 선택하여 금형 구조를 최적화하고 무게를 줄이는 것입니다.
핵심 연구:
- CAD 소프트웨어(Pro-Engineer)를 사용한 오일 팬 모델링.
- 주조 금형 설계.
- 적합한 주조 제조 공정 선택.
- CAM 소프트웨어를 사용한 CNC 프로그램 생성.
- 주조 금형의 불필요한 영역에서 무게 감소.
- 오일 팬에 적합한 재료 선택을 비교하여 금형 구조를 최적화하고 무게를 줄이기 위한 구조 해석.
연구 가설:
본 섹션에서는 명시적으로 언급되지 않았습니다. 본 연구는 가설 중심이라기보다는 탐색적이고 설계 중심입니다.
5. 연구 방법론
연구 설계:
연구 설계는 소프트웨어 도구를 사용한 모델링, 설계, 해석 및 최적화를 포함합니다. 초기에는 금형 설계 및 해석 조건에 대한 데이터를 수집합니다. 다음 단계에서는 추가 연구를 위해 Pro-Engineer를 사용하여 모델을 생성합니다. 금형 조립 모델링을 위해 금형 설계 계산을 수행합니다. 금형 준비 후, 오일 팬에 적합한 재료를 선택하여 금형 구조를 최적화하고 무게를 줄이기 위해 구조 해석을 수행합니다. 모델링, 금형 설계 및 제조(CNC)는 Pro/Engineer 소프트웨어를 사용하여 수행됩니다.
자료 수집 방법:
초기에는 금형 설계 및 해석 조건에 대한 데이터를 수집합니다.
분석 방법:
FE 해석을 사용하여 오일 팬에 적합한 재료 선택을 비교하여 금형 구조를 최적화하고 무게를 줄이기 위해 구조 해석을 수행합니다.
연구 대상 및 범위:
잠수함 엔진에 사용되는 오일 팬 모델링. 오일 팬 재료 선택. 주조 금형 설계 및 제조.
6. 주요 연구 결과:
핵심 연구 결과:
- M.S. F26의 변위 값: 최대 0.24694 mm
- M.S. F26의 변형률 값: 최대 0.0069591
- M.S. F26의 폰 미세스 응력 값: 133.38 N/mm²
- 알루미늄 A360의 변위 값: 최대 0.66136 mm
- 알루미늄 A360의 변형률 값: 최대 0.0018799
- 알루미늄 A360의 폰 미세스 응력 값: 132.43 N/mm²
- M.S. F26의 안전 계수: 2.186
- 알루미늄 A360의 안전 계수: 2.12
- 기존 모델과 수정 모델 간의 비용 차이: 2,82,377 루피
- 최적화된 금형 사용으로 인한 가공 시간 절약: 약 68시간.
- 알루미늄 사용으로 인한 부품 비용 절감: 약 40%.
제시된 데이터 분석:
분석 결과, 안전 계수가 2보다 크므로 연강 F26과 알루미늄 A360 모두 적합한 재료임을 보여줍니다. 그러나 알루미늄 A360은 연강 F26과 비슷한 폰 미세스 응력 값을 가지면서 더 높은 변위를 나타냅니다. 알루미늄 A360을 사용하면 상당한 비용 절감 및 무게 최적화를 달성할 수 있습니다. 최적화된 금형 설계 또한 제조 비용 및 시간 절감에 기여합니다.
그림 목록:
- 그림 3.4 냉간 챔버 기술 원리 (Fig. 3.4 Principle of Cold Chamber Technologies)
- 그림 5-2 중력 다이캐스팅용 고전 금형을 구성하는 주요 부품 (Fig. 5-2 the main parts constituting a classical mould for gravity die-casting)
- 조립 지침을 위해 선택된 설계 (Selected design for assembly guidelines.)
- 조립 지침을 위해 선택된 설계 (Selected design for assembly guidelines.)
- 중력 다이캐스팅 (Gravity die casting)
- 요약된 다이캐스팅 공정 (Die casting processes, as summarized)
- 냉간 챔버 기술 원리 (Principle of Cold Chamber Technologies)
- 캐비티 부품 제도 (Drafting for cavity part)
- 코어 부품 제도 (Drafting for Core part)
- 이젝터 플레이트 제도 (Drafting for Ejector plate)
- 리테이너 플레이트 및 핀 제도 (Drafting for Retainer plate and pins)
- 워터 인렛 노브, 25mm 볼트 제도 (Drafting for Water inlet knob, 25mm Bolts)
- 가이드 필러, 가이드 슬리브 제도 (Drafting for Guide Pillar, Guide Sleeve)
- 백 플레이트 제도 (Drafting for Back plate)
- 이젝터 핀 제도 (Drafting for Ejector pins)
- 하우징 제도 (Drafting for Housing)
- 코어 부품 모델 (Model of Core part)
- 리테이너 플레이트 모델 (Model of Retainer plate)
- 이젝터 플레이트 모델 (Model of Ejector plate)
- 백 플레이트 모델 (Model of Back plate)
- 완전한 금형 조립 (Complete Mould Assembly)
- 분해 도면 (Exploded View)
- 캐비티용 분할면 (Parting surface for Cavity)
- 추출된 코어 부품 (Extracted Core part)
- 추출된 캐비티 부품 (Extracted Cavity part)
- 캐비티 준비 (CAVITY PREPARATION)
- 캐비티 모델 (Model of Cavity)
- 금형 준비를 위한 공급 시스템이 있는 오일 팬 (Oil pan with feed system for the preparation of mould)
- 코어용 분할면 (Parting surface for Core)
- 형상 (Geometry)
- 모델 메시 (Meshing for model)
- M.S. F26의 변위 값 (Displacement value for M.S. F26)
- M.S. F26의 변형률 값 0.0069591 최대 (Strain Value 0.0069591 Max for M.S. F26)
- 알루미늄 A360의 변형률 값 0.0018799 최대 (Strain value 0.0018799 for Aluminum A360)
- M.S. F26의 폰 미세스 응력 값 133.38 N/mm² (Von-misses stress value 133.38 N/mm² for M.S. F26)
- 알루미늄 A360의 폰 미세스 응력 값 132.43 N/mm² (Von-misses stress value 132.43 N/mm² for Aluminum A360)
- 알루미늄 A360의 변위 값 (Displacement value for Aluminum A360)
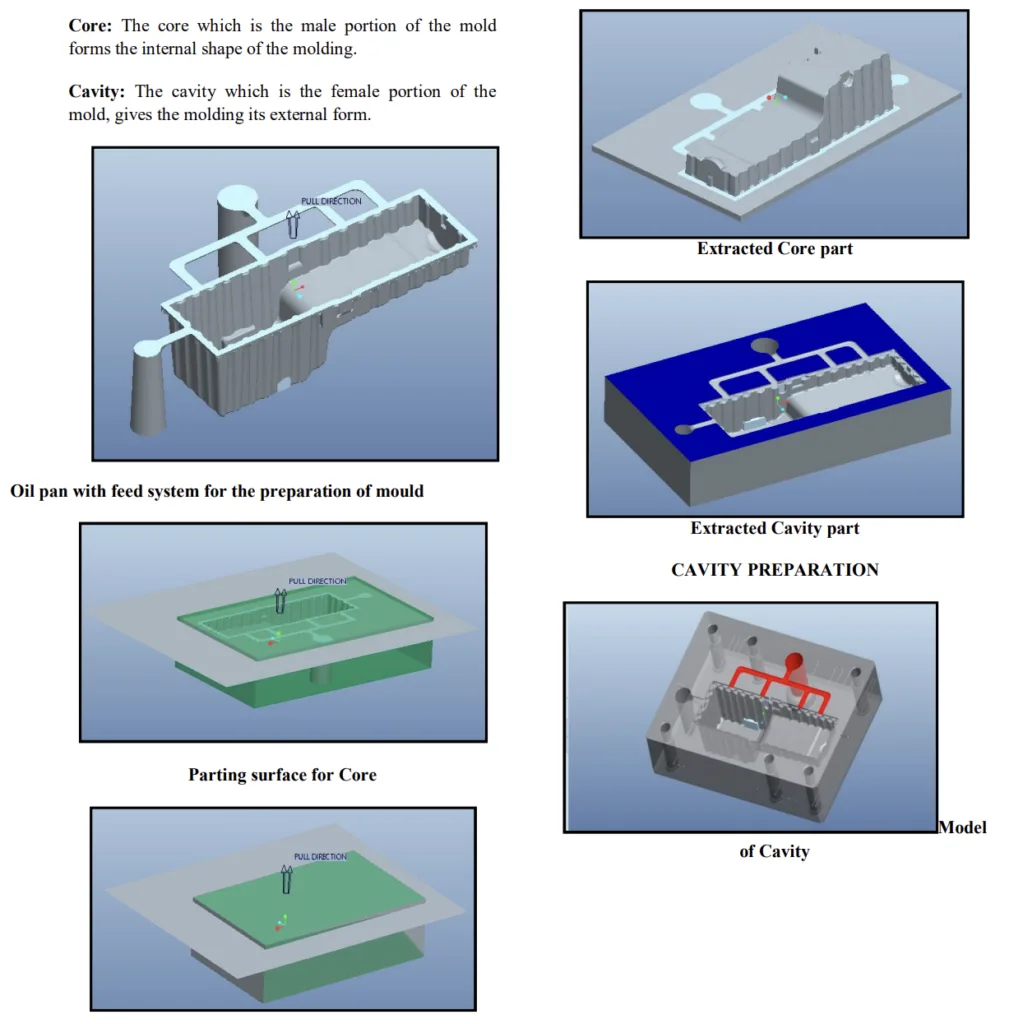
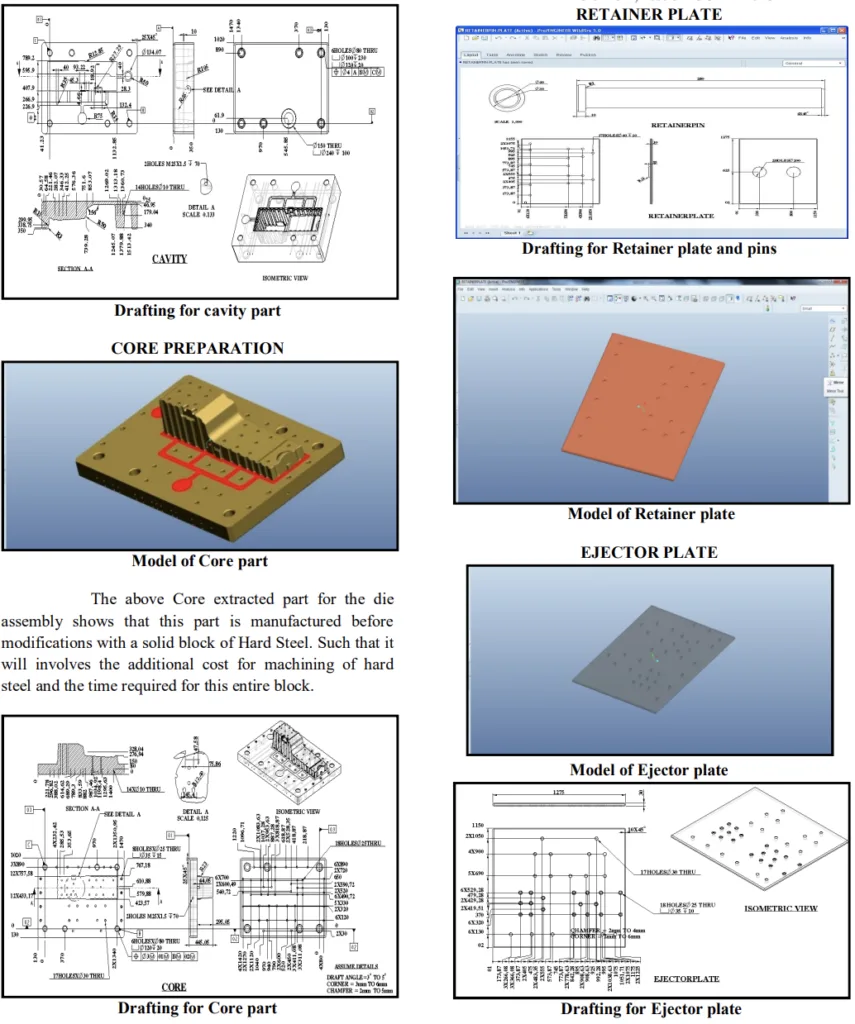
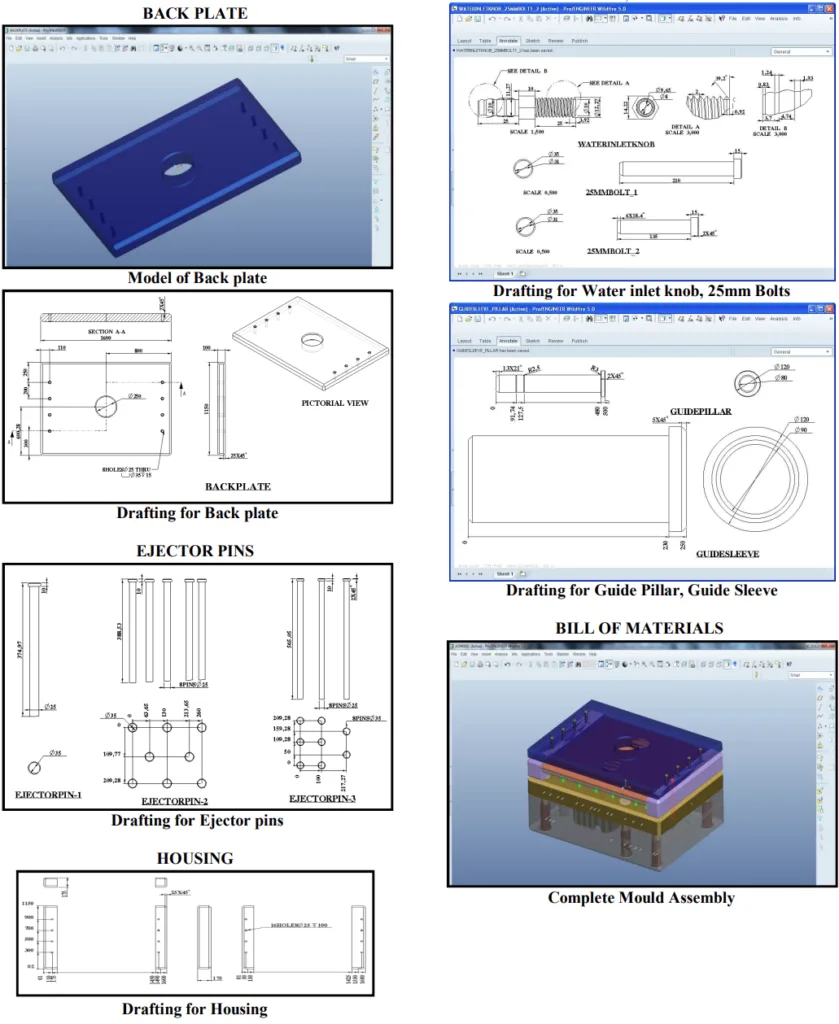
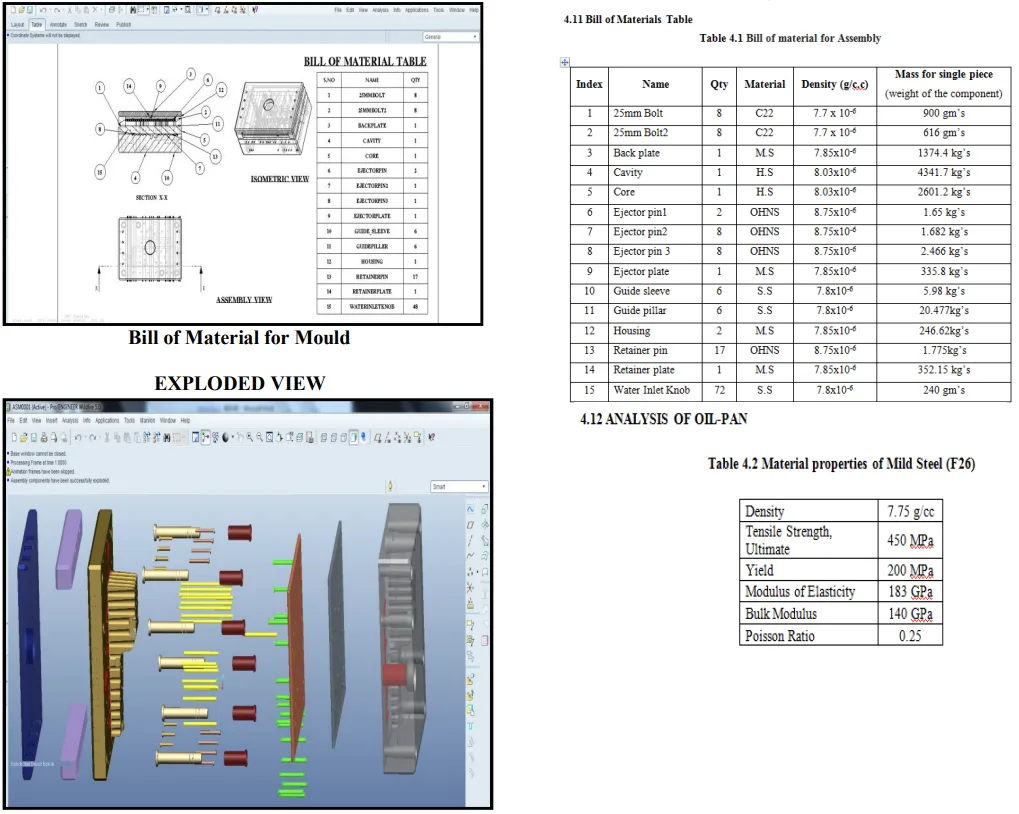
7. 결론:
주요 결과 요약:
본 프로젝트에서는 FE 해석 및 설계 수정을 통해 오일 팬과 다이캐스팅 금형의 설계를 성공적으로 최적화했습니다. 본 연구에서는 재료로 연강 F26과 알루미늄 A360을 비교하여 알루미늄 A360이 2.12의 안전 계수로 구조적 무결성을 유지하면서 무게 및 비용 이점을 제공하는 적합한 대안임을 발견했습니다. 분할 코어를 통합한 최적화된 금형 설계는 재료 사용량, 가공 시간(약 68시간) 및 전체 제조 비용(2,82,377 루피 절감)을 줄이며, 알루미늄 사용으로 인한 부품 비용 절감 효과는 거의 40%에 달합니다.
연구의 학문적 의의:
본 연구는 다이캐스팅에서 무게 및 비용 절감을 위한 FE 해석 및 최적화된 설계 방법론의 적용을 보여줍니다. 오일 팬과 같은 자동차 부품 제조에서 재료 선택 및 금형 설계 최적화에 대한 사례 연구를 제공합니다.
실용적 의미:
본 연구 결과는 다이캐스팅 제조업체가 오일 팬 생산에서 재료 비용, 가공 시간 및 부품 무게를 줄이기 위한 실용적인 지침을 제공합니다. 최적화된 금형 설계 및 재료 선택(알루미늄 A360)은 제조 효율성 및 제품 성능을 개선하기 위해 직접 구현할 수 있습니다.
연구의 한계 및 향후 연구 분야:
본 연구는 잠수함 엔진용 특정 오일 팬 설계에 초점을 맞추고 있습니다. 향후 연구에서는 이러한 최적화 기술의 일반화 가능성을 다른 유형의 오일 팬 및 다이캐스팅 부품으로 확장할 수 있습니다. 해석을 열 해석 및 피로 해석을 포함하도록 확장하여 보다 포괄적인 평가를 수행할 수 있습니다. 다양한 알루미늄 합금 및 주조 매개변수에 대한 추가 조사도 유익할 수 있습니다.
8. 참고 문헌:
- [1] Kennedy J, Eberhart RC (1995) "Particle swarm optimization". In: Proceedings of the 1995 IEEE International Conference on Neural Networks (ICNN'95), Perth, Australia, November/December 1995, vol 4, pp 1942-1948
- [2] Jerald J, Asokan P, Prabaharan G, Saravanan R (2005) "Scheduling optimisation of flexible manufacturing systems using particle swarm optimisation algorithm". International Journal Advance Manufacturing Technology 25:964-971
- [3] K. Vidyarthi and M.K. Tiwari “Machine loading problem of FMS: a fuzzy-based heuristic approach", International Journal of Production Research, 2001, 39(5), 953-979
- [4] M. K. Tiwari, B. Hazarika “Heuristic solution approach to the machine loading problem of an FMS and its Petri net model", International Journal of Production Research, 1997, 35(8), 2269-2284
- [5] Swarnkar R, Tiwari MK (2004) Modeling machine loading problem of FMSs and its solution methodology using a hybrid tabu search and simulated annealing-based heuristic approach. Robot Computer-Integrated Manufacturing 20(3):199–209
- [6] Nagarjuna N, Mahesh O, Rajagopal K (2006) A heuristic based on multi-stage programming approach for machine-loading problem in a flexible manufacturing system. Robot Computer-Integrated Manufacturing 22:342-352
- [7] S. G. Ponnambalam and Low Seng Kiat (2008) "Solving Machine Loading Problem in Flexible Manufacturing Systems Using Particle Swarm Optimization" World Academy of Science, Engineering and Technology 39
- [8] Sandhyarani Biswas, S. S. Mahapatra "Machine loading in Flexible manufacturing System: A swarm optimization approach" Eighth Int. Conference on Opers. & Quant. Management, 2007, NITR, 621-628
- [9] Kathryn E. Stecke, (1986), “A hierarchical approach to solving machine grouping and loading problems of FMS'S", European journal of operational research, 24, 369-378
- [10] M. K. Tiwari& N.K. Vidyarthi (2000): Solving machine loading problems in a flexible manufacturing system using a genetic algorithm based heuristic approach, International Journal of Production Research, 38:14, 3357-3384
- [11] Paul S. Andrews, An Investigation into Mutation Operators for Particle Swarm Optimization
- [12] Akhilesh kumar, prakash, MK Tiwari (2006), "Solving machine loading problem of a FMS with constraint based Genetic Algorithm”, European Journal of Operational Research (2006) 1043-1069 175
- [13] Sandhyarani Biswas, S. S. Mahapatra, “Modified particle swarm optimization for solving machine-loading problems in flexible manufacturing systems”. International Journal of Advanced Manufacturing Technology (2008) 39:931-942
9. 저작권:
- 본 자료는 "[SINGATHI SHARATH KUMAR, P. SUBRAMANYAM]"의 논문: "[DESIGN AND WEIGHT OPTIMIZATION OF OIL PAN BY FE ANALYSIS]"를 기반으로 합니다.
- 논문 출처: https://www.ijraet.com/wp-content/uploads/2024/01/IJRAET_2178.pdf
본 자료는 상기 논문을 요약한 것으로, 상업적 목적으로 무단 사용하는 것을 금지합니다.
Copyright © 2025 CASTMAN. All rights reserved.