본 요약은 ['The Future of Structural Components in HPDC.'] 문서를 기반으로 작성되었으며, 발행처는 ['Bühler AG'] 입니다.
1. 개요:
- 제목: HPDC 구조 부품의 미래 (The Future of Structural Components in HPDC.)
- 저자: 헤르만 야콥 루스 (Hermann Jacob Roos), 마틴 래글러 (Martin Lagler), 루이스 퀸타나 (Luis Quintana)
- 발행 연도: 논문 내 명시되지 않음.
- 발행 저널/학회: 뷔흘러 AG (Bühler AG)
- 키워드: 구조 부품 (structural components), HPDC, 다이캐스팅 (die casting), 자동차 산업 (automotive industry), 경량화 (weight reduction), 열 관리 (thermal management), 합금 선택 (alloy selection), 경량 설계 (lightweight design), 비용 절감 (cost reduction).
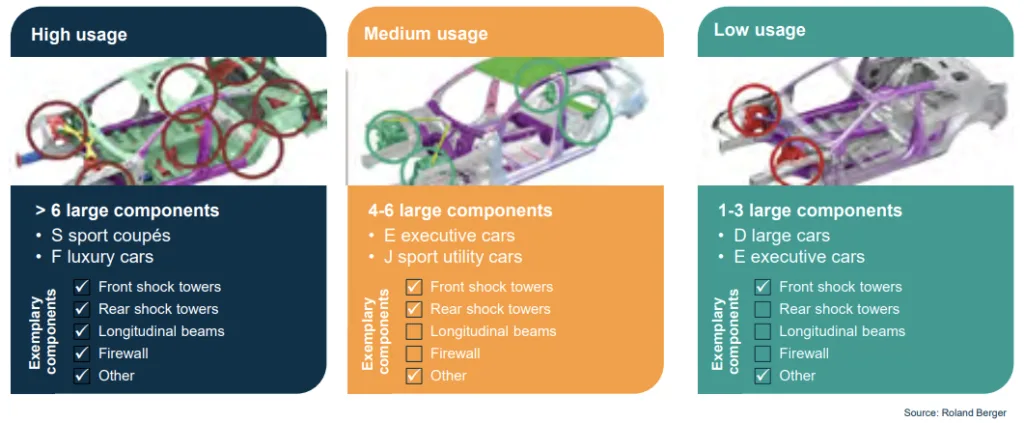
2. 초록 (Abstracts)
자동차 산업에서 경량 부품에 대한 지속적인 요구는 다이캐스팅 분야에서 새로운 수익성 있는 시장, 즉 구조 부품의 출현을 가져왔습니다. 쇼크 타워 (shock towers) 및 롱지튜디널 빔 (longitudinal beams)과 같은 크고 복잡한 부품에 대한 수요는 2018년에 6백만 대 미만의 자동차를 대상으로 하는 것으로 추정되었으며, 많은 자동차가 여러 개의 구조 부품을 포함하고 있습니다. 현재 사용량은 2025년까지 거의 9백만 대로 증가할 것으로 예측됩니다³. 그러나 이러한 구조 부품은 자동차 제조업체가 원하는 더 견고하고 가벼운 솔루션을 제공하지만, 긴 생산 실행에 대한 비용은 지금까지 스포츠카, 고급차, SUV 및 소량 생산이 경제적으로 합리적인 D 세그먼트 살롱 (D segment saloons)으로 채택을 제한했습니다. 그러나 다이캐스팅의 경제성은 변화하고 있습니다. 지난 몇 년 동안 구조 부품의 비용은 최대 20%까지 감소했습니다. 본 논문은 첨단 열 관리 (advanced thermal management), 새로운 합금 (new alloys)의 사용 및 신중한 제품 설계 (careful product design)의 조합이 생산 비용을 더욱 낮출 수 있는 방법을 보여줍니다. 이를 통해 다이캐스팅 구조 부품은 대량 자동차 시장 (mass car market)에 더욱 비용 효율적으로 접근할 수 있습니다. 2023년¹에 새로운 자동차 생산량이 1억 1천만 대를 기록할 것으로 예상되고, 자동차당 2~6개의 구조 부품이 사용될 것으로 예상됨에 따라, 이러한 기술 발전은 전 세계 다이캐스터 (die casters)에게 기회를 잠재적으로 변화시킬 수 있습니다. 다이캐스팅 기계 제조업체에서 파운드리 (foundries) 및 OEM에 이르기까지 제조 체인 (manufacturing chain)이 협력한다면 가능할 것입니다.
3. 연구 배경:
연구 주제 배경:
자동차 산업은 연비 향상, 배터리 주행 거리 연장 및 배기가스 감소를 위해 지속적으로 경량 부품을 추구하고 있습니다. 이러한 추세는 구조 부품에 대한 상당한 수요로 이어져 다이캐스팅에 수익성 있는 시장을 창출했습니다. 전기 자동차 (electric mobility)는 빠르게 확장되고 있으며, 전 세계 판매량은 2017년 약 2백만 대에서 2018년 510만 대로 두 배 이상 증가했습니다². 모든 자동차 제조업체는 더 낮은 비용으로 더 지속 가능한 차량을 생산하는 데 주력하고 있으며, 경량화는 핵심 요소입니다. 알루미늄 합금 다이캐스팅으로 대형 구조 부품을 만드는 것은 기존 강철 구조물보다 뛰어난 강도와 성형성을 제공하면서 차량 중량 감소를 위한 입증된 방법입니다.
기존 연구 현황:
독일 고급차 시장에서 개척된 다이캐스팅 구조 부품은 현재 다양한 차량 범주에서 활용되고 있습니다. 그림 1은 자동차 시장에서 구조 부품의 현재 사용량을 차량 유형 (고사용량, 중간 사용량, 저사용량) 및 예시 부품 (전방 쇼크 타워, 후방 쇼크 타워, 롱지튜디널 빔, 방화벽)별로 분류하여 보여줍니다. S 스포츠 쿠페 (S sport coupés) 및 F 고급차 (F luxury cars)는 현재 충돌 에너지 소산 (crash energy dissipation)을 위해 설계된 부품을 포함하여 가장 높은 사용량을 보입니다. E 세그먼트 임원 차량 (E segment executive cars) 및 J 세그먼트 스포츠 유틸리티 차량 (J segment sport utility vehicles)은 쇼크 타워 및 로커 강화재 (rocker rein enforcements)에 다이캐스팅 부품을 활용합니다. D 세그먼트 대형차 (D-segment large cars)는 전방 쇼크 타워 및 터널 보강재 (tunnel reinforcement)에 다이캐스팅 부품을 사용합니다.
연구의 필요성:
이러한 장점에도 불구하고, 다이캐스팅 구조 부품의 대량 시장 차량 (mass-market vehicles) 채택은 긴 생산 실행과 관련된 비용 문제로 인해 제한되었습니다. 툴링 (tooling)에 대한 투자 비용은 상대적으로 낮지만, 툴 마모 증가로 인해 유지 보수 비용이 증가하여 C 세그먼트 중형차 시장 (C segment medium car market) 및 소형 대량 시장 자동차 (smaller mass market cars)에 대한 전체 단위 비용이 너무 높아집니다. 그러나 다이캐스팅의 경제성은 진화하고 있으며, 구조 부품의 비용은 최근 몇 년 동안 최대 20%까지 감소했습니다. 생산 비용을 더욱 절감하여 다이캐스팅 구조 부품을 대량 자동차 시장 채택에 더욱 비용 효율적으로 만들고 전 세계 다이캐스터의 잠재력을 여는 기술 발전을 모색할 필요가 있습니다.
4. 연구 목적 및 연구 질문:
연구 목적:
본 논문의 목적은 열 관리, 합금 선택 및 제품 설계의 발전을 통해 다이캐스팅 구조 부품의 생산 비용을 더욱 절감하여 대량 자동차 시장에서 더 광범위하게 채택될 수 있도록 하는 방법을 입증하는 것입니다. 궁극적인 목적은 다이캐스팅이 비용 장벽을 극복하고 대량 생산 차량의 구조 부품에 대한 실행 가능한 솔루션이 될 수 있는 경로를 식별하는 것입니다.
핵심 연구 질문:
핵심 연구 질문은 "현재 기술로 지금 당장 적용할 수 있는 발전과 기술은 무엇이며, 다이캐스팅이 대량 시장 채택에 대한 비용 장벽을 깰 수 있도록 할 수 있는가?" 입니다. 본 논문은 세 가지 기술 영역을 조사합니다.
- 열 관리를 통한 생산성 향상 (Improving productivity through thermal management).
- 공정 단계를 줄이기 위한 새로운 합금 활용 (Utilizing new alloys to reduce process steps).
- 제품 설계에 의한 경량 구조 (Lightweight construction by product design).
연구 가설:
중심 가설은 첨단 열 관리 (advanced thermal management)를 구현하고, 열처리 (heat treatment)를 최소화하거나 제거하기 위해 새로운 합금을 활용하고, 경량 제품 설계 (lightweight product design)를 적용함으로써 다이캐스팅 구조 부품의 생산 비용을 크게 절감하여 대량 시장 자동차 응용 분야에 경제적으로 실현 가능하게 만들 수 있다는 것입니다. 특히, 본 논문은 이러한 접근 방식의 조합이 일반적인 쇼크 타워에 대한 이론적 비용 절감 프로그램에서 입증된 바와 같이 23%를 초과하는 비용 절감을 달성할 수 있다고 가정합니다.
5. 연구 방법론
연구 설계:
본 논문은 뷔흘러의 응용 지식과 롤랜드 버거 (Roland Berger)가 수행한 시장 분석을 활용하여 분석적 및 설명적 접근 방식을 채택합니다. 경험적 실험보다는 계산 및 업계 모범 사례를 기반으로 이론적 비용 절감 프로그램을 제시합니다. 설계는 특정 기술 발전이 다이캐스팅 구조 부품의 비용 효율성에 미치는 잠재적 영향을 보여주는 데 중점을 둡니다.
자료 수집 방법:
분석은 유럽, 중국 및 북미 전역에서 얻은 뷔흘러의 산업 경험 및 응용 지식을 기반으로 합니다. 시장 데이터 및 예측은 기존, 알려진 및 예상되는 차량 아키텍처 (vehicle architectures), 학회 발표 및 업계 전문가 인터뷰를 고려하는 롤랜드 버거 연구 (그림 2)에서 파생됩니다. 비용 절감 계산은 일반적인 쇼크 타워 부품을 기준으로 4,400톤 기계와 2 캐비티 (cavity), 3 플레이트 툴 (plate tool) 설정을 활용하여 제시됩니다.
분석 방법:
본 논문은 열 관리, 새로운 합금 및 경량 설계가 단위 생산 비용에 미치는 영향을 평가하기 위해 비용-편익 분석 (cost-benefit analysis) 접근 방식을 활용합니다. 사이클 시간 단축 (cycle time reduction), 다이 수명 연장 (die lifetime extension) 및 스크랩률 감소 (scrap rate reduction)를 수량화하여 개선된 열 관리를 통해 달성한 비용 절감을 입증합니다 (그림 4 및 5). 열처리 (heat treatment)를 줄이거나 제거하는 새로운 합금 활용으로 인한 잠재적인 비용 절감도 분석합니다 (그림 7). 마지막으로, 경량 설계로 인한 비용 절감을 평가합니다 (그림 8). 이러한 세 가지 영역에서 누적된 비용 절감을 계산하여 다이캐스팅 구조 부품을 더욱 경쟁력 있게 만들 수 있는 전반적인 잠재력을 입증합니다.
연구 대상 및 범위:
본 연구는 다이캐스팅 구조 부품에 초점을 맞추고 있으며, 특히 일반적인 자동차 쇼크 타워를 사례 연구로 사용합니다. 범위는 고압 다이캐스팅 (High Pressure Die Casting, HPDC) 기술과 자동차 산업에서의 응용으로 제한됩니다. 분석은 고급차에서 대량 시장 차량에 이르기까지 다양한 차량 세그먼트를 고려하고 비용 장벽을 해결하여 이러한 세그먼트 전반에 걸쳐 다이캐스팅 구조 부품의 사용을 확대할 가능성을 조사합니다.
6. 주요 연구 결과:
핵심 연구 결과:
본 논문은 다이캐스팅 구조 부품의 생산 비용을 크게 절감할 수 있는 세 가지 주요 기술 발전을 확인합니다.
- 개선된 열 관리 (Improved Thermal Management): 열 균형 (thermal balance) 최적화 및 표적 마이크로 스프레이 (targeted micro-spraying) 통합은 사이클 시간을 약 33% (일반적인 쇼크 타워의 경우 90초에서 60초로) 단축하고, 다이 수명을 50% 이상 (80,000 사이클에서 최소 120,000 사이클로) 연장하고, 스크랩률을 5%에서 3%로 줄일 수 있습니다. 이러한 조합은 단위 생산 비용을 10% 절감할 수 있습니다 (그림 5).
- 새로운 합금 시스템 (New Alloy Systems): AlMg4Fe2 또는 AlMg6Si2MnZr과 같은 새로운 합금 시스템을 활용하면 열처리 (HT) 및 교정 (straightening) 공정의 필요성을 잠재적으로 제거하여 생산 비용을 더욱 절감할 수 있습니다. 새로운 합금으로 전환하면 추가적으로 10%의 비용 절감을 얻을 수 있습니다 (그림 7). 표 1은 표준 구조 합금 시스템 (Standard Structural Alloy Systems, AlSi10MnMg)과 새로운 합금 (New Alloys, AlMg4Fe2) 및 고강도 합금 시스템 (High Strength Alloy Systems, AlMg6Si2MnZr)의 특성을 자세히 설명합니다. 그림 6: 구조 부품을 위한 다양한 합금 시스템의 가능성 (Figure 6: Possibilities of different alloy systems for Structural components.) 합금 시스템 (Alloy System) AlSi10MnMg AlMg4Fe2 AlMg6Si2MnZr 열처리 (HT) T7 F T5 UTM Rm[MPa] 200-240 240-260 350-380 항복 강도 Rp0,2% [MPa] (Yield strength Rp0,2% [MPa]) 120-140 120-140 230-250 연신율 A [%] (Elongation A [%]) 10-20 10-22 8-12
- 경량 제품 설계 (Lightweight Product Design): 지능형 제품 설계 (intelligent product design) (예: 벽 두께를 2.5mm에서 1.8mm로 줄이는 것)는 최대 20%의 중량 절감을 달성할 수 있습니다. 쇼크 타워 예시에서 중량 감소 (4,000g에서 3,600g으로, 10% 감소)는 생산 비용을 추가로 4% 절감할 수 있습니다 (그림 8).
데이터 해석:
그림 5, 7, 8에 제시된 데이터는 개선된 열 관리, 새로운 합금 활용 및 경량 설계를 결합하여 23% 이상의 누적 비용 절감 잠재력을 보여줍니다. 그림 2는 구조 부품 시장의 예상 성장률을 보여주며, 수요 증가를 강조합니다. 그림 3은 생산 비용 절감에 따른 잠재적인 시장 성장을 강조하며, 약 6백만 대에서 2030년까지 2,500만 대로 크게 확장될 수 있음을 시사합니다. 그림 4는 개선된 열 관리를 통해 달성한 사이클 시간 단축을 시각적으로 나타냅니다.
그림 목록:
- 그림 1: 자동차 시장에서 구조 부품의 현재 사용량 (Figure 1: Current usage for structural components in the automotive market)
- 그림 2: 현재 구조 부품의 예상 성장률, 2015년~2025년 (Figure 2: Predicted growth in current structural components, 2015 to 2025)
- 그림 3: 생산 비용 절감에 따른 잠재적인 구조 부품 시장 성장 (Figure 3: Potential structural component market growth with production cost savings)
- 그림 4: 더 나은 열 관리가 사이클 시간을 최대 1/3까지 줄일 수 있는 방법 (Figure 4: How better thermal management can reduce cycle times by up to a third)
- 그림 5: 개선된 열 관리를 사용한 비용 절감 (Figure 5: Cost reduction using improved thermal management)
- 그림 6: 구조 부품을 위한 다양한 합금 시스템의 가능성 (Figure 6: Possibilities of different alloy systems for Structural components.)
- 그림 7: 새로운 합금으로 인한 잠재적인 비용 절감 (Figure 7: Potential cost savings from new alloys)
- 그림 8: 경량 설계에 의한 잠재적인 비용 절감 (Figure 8: Cost saving potential by light weight design)
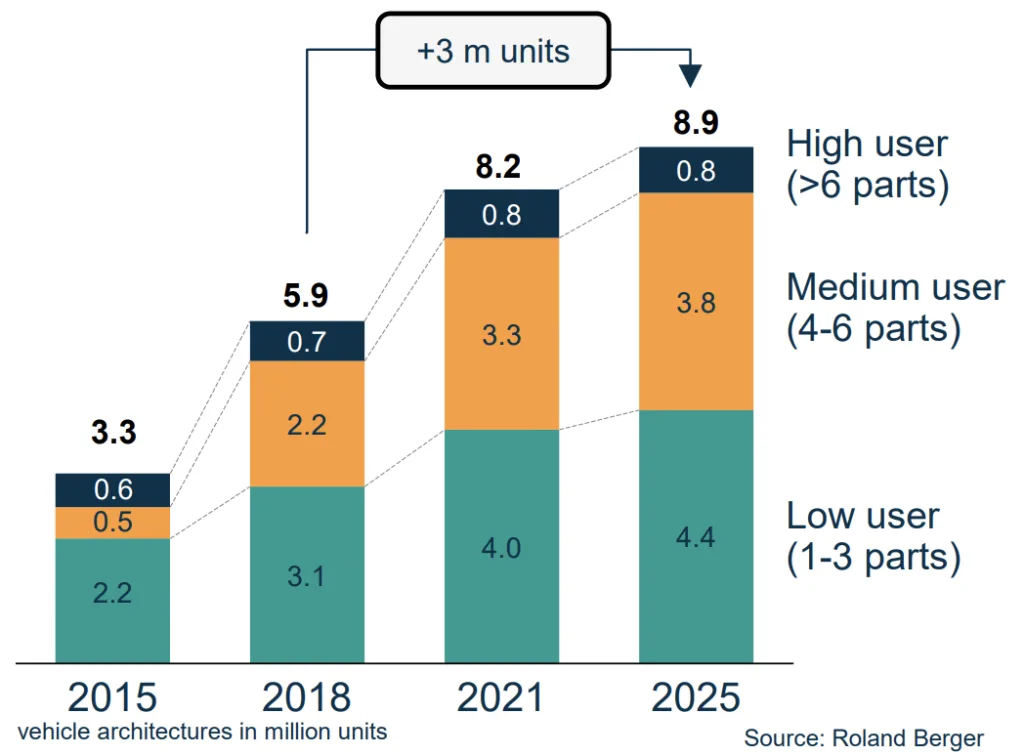
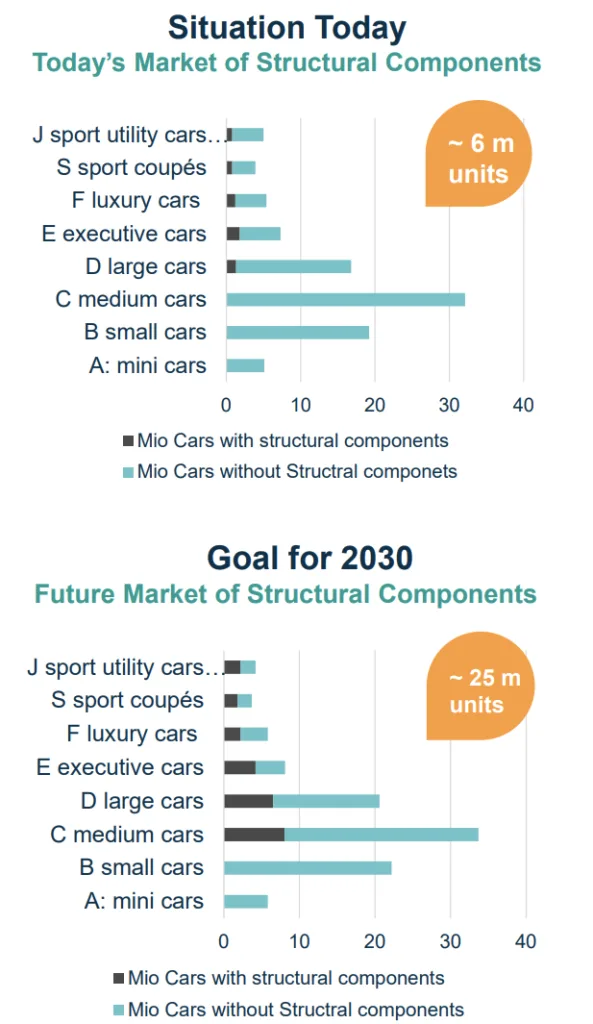
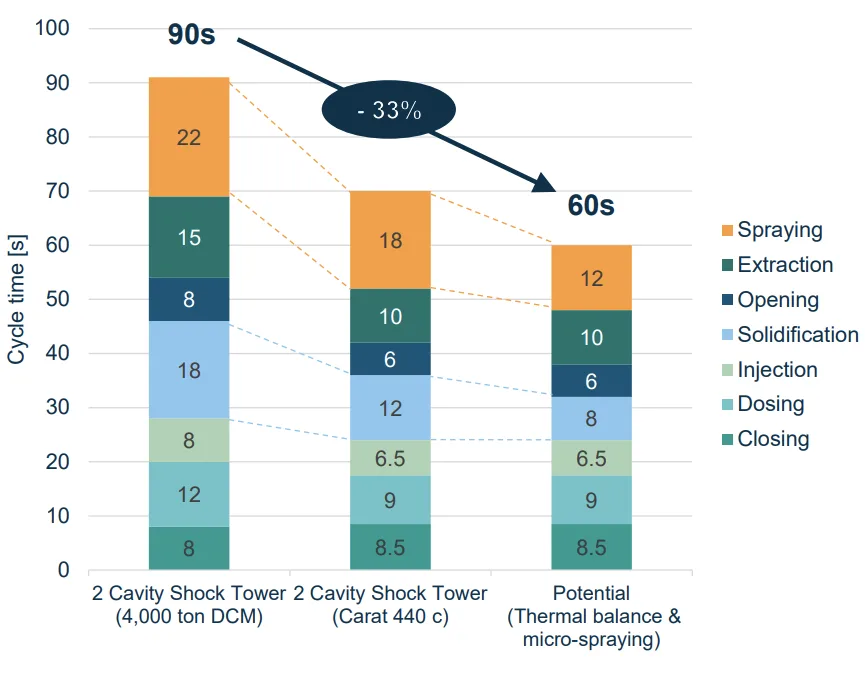
7. 결론:
주요 연구 결과 요약:
본 논문은 다이캐스팅 구조 부품이 비용 장벽을 해결함으로써 대량 자동차 시장 채택에 상당한 잠재력을 가지고 있다고 결론 내립니다. 첨단 열 관리, 새로운 합금 시스템 및 경량 제품 설계의 조합은 23% 이상의 상당한 비용 절감을 달성할 수 있습니다. 이러한 비용 절감은 주로 사이클 시간 개선, 다이 수명 연장, 스크랩 감소 및 열처리 및 교정과 같은 후처리 공정 제거에 의해 주도됩니다.
연구의 학문적 의의:
본 연구는 자동차 산업의 진화하는 요구 사항을 충족하기 위한 다이캐스팅 기술의 지속적인 혁신의 중요성을 강조합니다. 특정 기술 발전이 대량 생산에서 다이캐스팅 구조 부품의 경제적 타당성에 어떻게 기여할 수 있는지 이해하기 위한 프레임워크를 제공합니다. 분석은 HPDC가 차량 경량화 및 지속 가능성 목표에 기여할 수 있는 잠재력을 강조합니다.
실용적 의미:
본 연구 결과는 다이캐스팅 파운드리, 자동차 OEM 및 다이캐스팅 기계 제조업체에 중요한 실용적 의미를 갖습니다. 제안된 기술 발전을 구현하면 다이캐스터가 대량 시장에 진출할 수 있으며, OEM은 비용 효율적인 경량화 솔루션의 혜택을 누릴 수 있습니다. 본 논문은 이러한 이점을 실현하기 위해 제조 체인 전반에 걸친 협력의 필요성을 강조합니다.
연구의 한계 및 향후 연구 분야:
본 논문은 계산 및 산업 경험을 기반으로 한 이론적 비용 절감 프로그램을 제시합니다. 향후 연구에서는 파일럿 생산 연구 및 실제 사례 연구를 통해 이러한 결과의 경험적 검증을 포함할 수 있습니다. 분석은 일반적인 쇼크 타워에 초점을 맞추고 있습니다. 향후 연구에서는 이러한 비용 절감 전략의 적용 가능성을 더 넓은 범위의 구조 부품 및 다양한 다이캐스팅 공정에 대해 탐구할 수 있습니다. 또한, 새로운 합금 및 경량 설계로 생산된 구조 부품의 장기적인 성능 및 내구성을 조사하는 것이 가치가 있을 것입니다.
8. 참고 문헌:
- Wagner, Statistica, available at: https://www.statista.com/
statistics/266813/growth-of-the-global-vehicle-production-
since-2009/ - IEA (2019), "Global EV Outlook 2019", IEA, Paris, www.iea.
org/publications/reports/globalevoutlook2019/ - Roland Berger (2019), Independent research for Bühler
AG: Considers existing, known and projected architectures,
congress presentations and interviews with industry experts. - DGS award-winning casting: https://www.dgs-druckguss.
com/en/technology-and-innovation/awards
9. 저작권:
- 본 자료는 "헤르만 야콥 루스, 마틴 래글러, 루이스 퀸타나"의 논문: "The Future of Structural Components in HPDC."를 기반으로 작성되었습니다.
- 논문 출처: 논문 내 명시되지 않음.
본 자료는 위 논문을 기반으로 요약되었으며, 상업적 목적으로 무단 사용하는 것을 금지합니다.
Copyright © 2025 CASTMAN. All rights reserved.