본 논문 요약은 ['다이캐스팅 공정에서 시뮬레이션 기반 주조 제품 결함 예측'] 논문을 기반으로 작성되었으며, ['International Journal of Production Research']에 게재되었습니다.
1. 개요:
- 제목: 다이캐스팅 공정에서 시뮬레이션 기반 주조 제품 결함 예측 (Simulation-enabled casting product defect prediction in die casting process)
- 저자: M.W. Fu & M.S. Yong
- 출판 연도: 2009년
- 출판 저널/학회: International Journal of Production Research
- 키워드: CAE 시뮬레이션 (CAE simulation); 고압 다이캐스팅 (high pressure die casting); 제품 품질 보증 (product quality assurance); 결함 예측 (defect prediction)
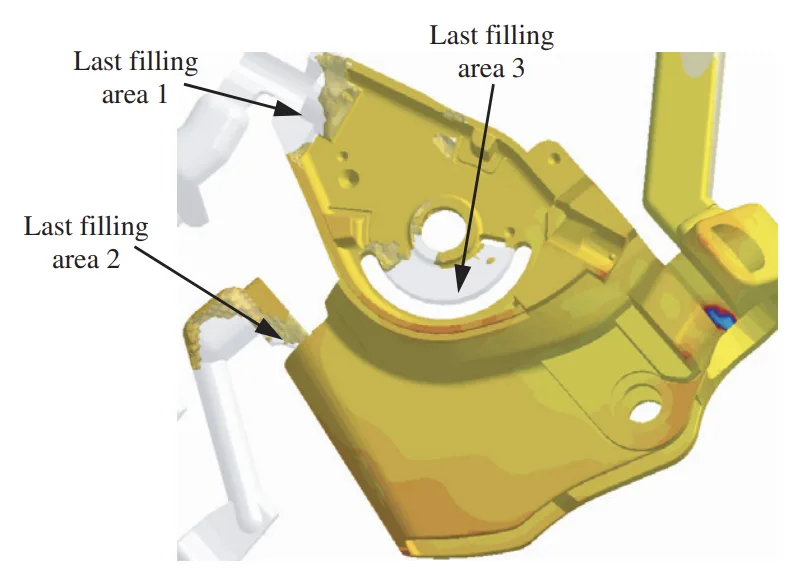
2. 연구 배경:
연구 주제 배경:
최근 주조 산업에서는 제품 개발 패러다임이 기존의 작업장 내 시행착오 방식에서 CAE (Computer-Aided Engineering) 기반 시뮬레이션 및 컴퓨터를 이용한 '개념 증명 (proof-of-concept)' 방식으로 전환되고 있습니다. 이러한 제품 개발 패러다임의 변화는 경험적 노하우와 숙련된 기술 중심에서 보다 과학적인 시뮬레이션, 평가, 분석 및 계산 중심으로 이동하는 것을 의미합니다. CAE 시뮬레이션은 전체 주조 공정을 모델링하고 실제 작동 조건에서 주조 시스템의 동적 거동을 파악하는 데 중요한 역할을 수행합니다. 또한, 시뮬레이션을 통해 제품 품질 현황과 제품 결함을 탐색하여 주조 결함의 근본 원인을 정확히 파악하고 이를 방지하기 위한 해결책을 모색할 수 있습니다. 현재, 특히 고압 다이캐스팅 (HPDC) 제품은 정밀 형상 (near-net shape 또는 net shape) 특성, 높은 생산성 및 복잡한 형상과 특징으로 인해 많은 산업 분야에서 널리 사용되고 있습니다. 시장에서 설계 및 제조 리드 타임 단축, 우수한 치수 정확도, 전반적인 제품 품질 및 신속한 제품 설계 변경에 대한 요구가 증가함에 따라 기존의 제품 개발 패러다임은 경쟁적인 시장 환경에서 분명히 한계에 직면하게 되었습니다.
기존 연구 현황:
기존의 CAD (Computer-Aided Design) 및 CAM (Computer-Aided Manufacturing) 기술은 설계 의도를 표현하고 물리적 구현을 돕는 효율적인 지원 기술로서 중요한 역할을 수행해 왔습니다. 이러한 기술은 설계 품질을 크게 향상시키고 설계 및 제조 리드 타임을 단축시키는 데 기여합니다. 그러나 CAD/CAM 기술만으로는 주조 공정 설계, 금형 구조, 제품 속성 구성 및 품질 관리 및 보증과 같은 중요한 문제들을 해결하기에는 어려움이 있습니다. 기존의 주조 시뮬레이션 연구는 주로 단편적인 접근 방식을 취했으며, 시뮬레이션 기반 제품 결함 예측 패러다임을 체계적으로 제시하지 못했습니다. 또한, CAE 시뮬레이션이 결함 예측 및 방지에 어떻게 도움이 되는지, CAE 시뮬레이션을 통해 어떤 정보를 얻을 수 있는지, 어떤 종류의 정보가 해당 결함을 식별하는 데 필요한지, 충전 및 응고 과정에서 어떤 결함이 발생할 수 있는지, 시뮬레이션 정보를 기반으로 제품 결함 방지 대책을 어떻게 수립할 수 있는지에 대한 구체적인 내용이 부족했습니다.
연구의 필요성:
기존 방법론과 단편적인 연구의 한계를 극복하기 위해서는 CAE 시뮬레이션 기술에 기반한 효율적인 제품 개발 패러다임이 절실히 필요합니다. 이는 공정 구성 및 제품 품질에 대한 요구 증가로 인해 주조 생산 산업에서 발생하는 병목 현상을 해결하는 데 매우 중요합니다. CAE 시뮬레이션 기술은 주조 제품 품질 및 결함 분석, 예측 및 평가를 위한 기술적으로 효율적이고 비용 효과적인 솔루션으로 부상하고 있으며, 물리적인 시행착오에 대한 의존도를 줄이고 제품 개발 주기를 단축하는 데 기여할 수 있습니다.
3. 연구 목적 및 연구 질문:
연구 목적:
본 연구의 주된 목적은 다이캐스팅 공정에서 CAE 기술이 주조 공정 시뮬레이션 및 제품 결함 예측을 위한 핵심 도구임을 제시하는 것입니다. 본 연구는 주조 공정 모델링을 명확히 하고, 중요한 시뮬레이션 문제들을 상세히 설명하며, CAE 시뮬레이션이 충전, 응고 및 이젝션 후 거동과 관련된 정보를 어떻게 밝혀내는지 설명하고자 합니다. 산업 사례 연구를 통해 CAE 시뮬레이션이 공정 관련 결함을 식별하고 예측하는 데 효과적임을 입증하고, 제품 품질 보증을 향상시키는 데 있어 CAE 시뮬레이션의 전반적인 효율성을 검증하는 것을 목표로 합니다.
핵심 연구 질문:
본 연구는 다음과 같은 핵심 질문에 집중합니다:
- 수치 해석 방법을 사용하여 주조 공정을 모델링하고 실제 공정, 모델링, 시뮬레이션 및 출력 변수 간의 연관성을 확립하는 방법은 무엇인가?
- 시뮬레이션 과정과 솔루션 생성 주기 내 정보 흐름을 명확히 설명하는 방법은 무엇인가?
- 주조 결함 예측을 위한 공정 기반 시뮬레이션 패러다임을 제안하는 방법은 무엇인가?
- 시뮬레이션을 통해 얻을 수 있는 정보와 이 정보를 기반으로 예측할 수 있는 결함 범주를 분류하는 방법은 무엇인가?
- 사례 연구를 통해 시뮬레이션 과정, 절차 및 식별된 시뮬레이션 매개변수를 기반으로 주조 공정에서 결함이 발생하는 메커니즘을 분석하는 방법은 무엇인가?
연구 가설:
본 연구의 중심 가설은 CAE 시뮬레이션 기술이 다이캐스팅 공정에서 주조 제품 결함을 예측하는 데 강력하고 효과적인 방법론을 제공한다는 것입니다. 주조 공정을 정확하게 모델링하고 시뮬레이션 결과를 분석함으로써 공정 관련 결함을 식별, 이해 및 궁극적으로 방지할 수 있으며, 이는 제품 품질 향상과 제조 비용 절감으로 이어진다고 가정합니다. 또한, 체계적인 공정 기반 시뮬레이션 패러다임이 다이캐스팅에서 결함 예측 및 공정 최적화를 용이하게 하기 위해 개발 및 검증될 수 있다고 가설을 설정합니다.
4. 연구 방법론
연구 설계:
본 연구는 주조 결함 예측을 위한 공정 기반 시뮬레이션 프레임워크를 채택합니다. 이 프레임워크는 제품 설계 사양과 CAE 시뮬레이션을 통합하여 주조 공정을 분석하고 최적화하는 데 중점을 둡니다. 연구 설계는 CAE 환경 내에서 주조 형상, 공정 경로 및 매개변수 결정을 포함한 전체 주조 시스템을 모델링하는 것을 포함합니다. 방법론은 고압 다이캐스팅 (HPDC) 공정에 초점을 맞춘 산업 사례 연구를 통해 검증됩니다.
자료 수집 방법:
본 연구의 자료는 주로 상용 주조 시뮬레이션 소프트웨어인 Magmasoft를 사용하여 수행된 CAE 시뮬레이션에서 얻습니다. 시뮬레이션 입력 자료에는 주조 형상의 CAD STL 모델, 주조 합금 (AlSi9Cu3) 및 금형 재료 (X38CrMoV5)의 물성치, HPDC 관련 공정 매개변수가 포함됩니다. 산업 사례 연구는 시뮬레이션 결과에 대한 실제적인 맥락과 검증을 제공합니다. 용융 금속 흐름 패턴, 온도 분포, 응고 순서 및 응력-변형 분석과 같은 시뮬레이션 결과는 결함 예측을 위해 수집된 주요 자료를 구성합니다.
분석 방법:
분석 방법은 CAE 시뮬레이션 결과를 해석하여 주조 결함을 예측하고 이해하는 데 중점을 둡니다. CAE 소프트웨어 내에서 유한 요소법 (FEM) 및 유한 차분법 (FDM)과 같은 수치 해석 방법이 활용되어 주조 시스템의 물리적 거동을 정량적으로 나타냅니다. 분석에는 다음이 포함됩니다:
- 용융 금속 선단 진행 (MFA) 분석을 통해 잠재적인 공기 혼입 및 충전 불균형을 식별합니다.
- 응고 시 온도 분포 분석을 통해 수축 기공 및 고온점 (hot spot) 발생 가능성을 예측합니다.
- 이젝션 후 응력 및 변형 분포 평가를 통해 변형 및 잔류 응력을 평가합니다.
- 시뮬레이션 예측 결함과 산업 사례 연구에서 관찰된 실제 결함을 비교하여 시뮬레이션 방법론을 검증합니다.
연구 대상 및 범위:
연구 대상은 산업 현장의 고압 다이캐스팅 (HPDC) 공정이며, 특히 4구멍 (four-cavity) 다이캐스팅 구성에 초점을 맞춥니다. 두 가지 산업 사례가 자세히 제시됩니다. 연구 범위는 충전, 응고 및 열응력으로 인해 발생하는 결함을 포함하여 HPDC의 공정 관련 결함으로 제한됩니다. 연구 대상 재료는 주조 재료로 AlSi9Cu3, 금형 재료로 X38CrMoV5이며, 이는 다이캐스팅 응용 분야에서 흔히 사용되는 재료를 대표합니다. 시뮬레이션 분석은 금형 충전, 응고 및 냉각, 그리고 이젝션 후 주조품의 응력 및 변형 분포를 포함합니다.
5. 주요 연구 결과:
핵심 연구 결과:
본 연구는 CAE 시뮬레이션이 다이캐스팅 공정에 대한 중요한 정보를 효과적으로 밝혀내어 제품 결함 예측을 가능하게 함을 입증합니다. 주요 연구 결과는 다음과 같습니다:
- 충전 공정 시뮬레이션: CAE 시뮬레이션은 용융 금속 선단 위치, 난류 및 충전 매끄러움을 정확하게 묘사합니다. 잠재적인 공기 혼입 영역을 식별하고 통풍 (venting) 요구 사항을 평가합니다. 또한, 시뮬레이션은 열적 거동, 온도 분포, 충전 순서 및 용융 금속 속도 분포를 보여주며, 이는 금형 침식 및 표면 조도 품질을 예측하는 데 중요합니다. 분할 용융 흐름 (split melt stream) 및 미충전 (misrun)과 같은 바람직하지 않은 충전 거동도 식별할 수 있습니다.
- 응고 공정 시뮬레이션: 시뮬레이션은 응고 순서, 주조품 및 금형의 온도 분포를 명확히 하고, 최종 응고 영역 및 잠재적인 고온점을 식별합니다. 냉각 시스템 설계, 런너 시스템 설계 평가 및 수축 기공 및 다공성 분포 예측에 도움이 됩니다. CAE 시뮬레이션은 또한 기공 없는 주조품을 위한 피더 크기 및 위치 결정을 지원합니다.
- 주조품 응력 해석: CAE 시뮬레이션은 이젝션 후 온도 분포 및 변형, 잔류 응력 분포 및 응력 관련 잠재적 제품 결함을 예측합니다. 주조 시스템 설계 최적화 및 금형 수명 및 주조 정확도 향상을 위한 금형 응력 해석을 지원합니다.
자료 해석:
시뮬레이션 결과는 특정 시뮬레이션 출력과 잠재적인 주조 결함을 연관시키기 위해 해석됩니다. 예를 들어, 불균형한 MFA 패턴은 불균일한 충전 및 공기 혼입으로 인한 결함과 관련이 있습니다. 응고 시뮬레이션에서 식별된 고온점은 잠재적인 수축 기공 및 오렌지 스킨 결함을 나타냅니다. 응력 해석에서 예측된 높은 응력 집중은 변형 또는 피로 파괴가 발생하기 쉬운 영역을 시사합니다. 사례 연구는 시뮬레이션 예측 결함과 산업 주조품에서 관찰된 실제 결함 간의 강력한 상관관계를 보여줌으로써 이러한 해석을 검증합니다. 예를 들어, 사례 I에서 MFA 분석은 보스 형상에서 공기 혼입을 예측했으며, 이는 주조품 분석에서 확인되었습니다. 사례 II에서 시뮬레이션은 비합리적인 흐름 및 온도 분포가 오렌지 스킨 및 파단 결함으로 이어질 것이라고 예측했으며, 이는 실제 부품에서도 관찰되었습니다.
그림 목록:
- Figure 1. Modelling of the casting process from physical and mathematical perspectives: action-behaviour-property relationship.
- Figure 2. Association among the process, modelling, simulation and output variables.
- Figure 3. The process-based simulation paradigm for prediction of casting defects.
- Figure 4. The layout of the casting filling system in Case I.
- Figure 5. The MFA positions in the filling process. (a) Filling at 85% of the whole process; (b) filling at 90% of the whole process.
- Figure 6. The layout of the casting filling system in Case II.
- Figure 7. The melt-front advancement position in filling process.
- Figure 8. Unreasonable filling pattern and the defect caused. (a) Simulation predicted irrational flow; (b) the real defect revealed by experiment.
- Figure 9. Defect caused by the unreasonable temperature distribution in the solidification process. (a) Simulation result; (b) real part.
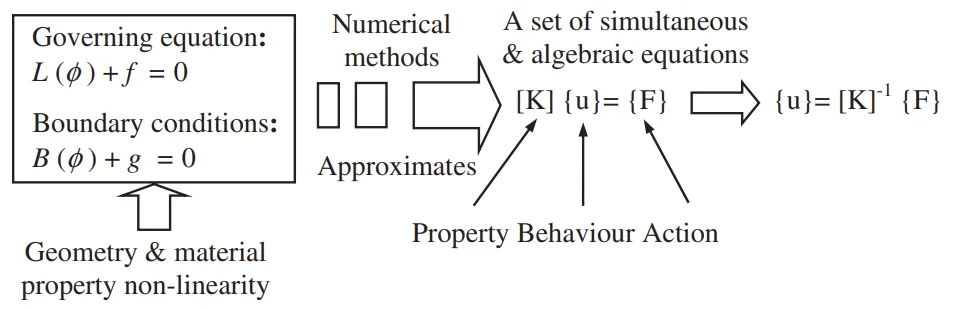
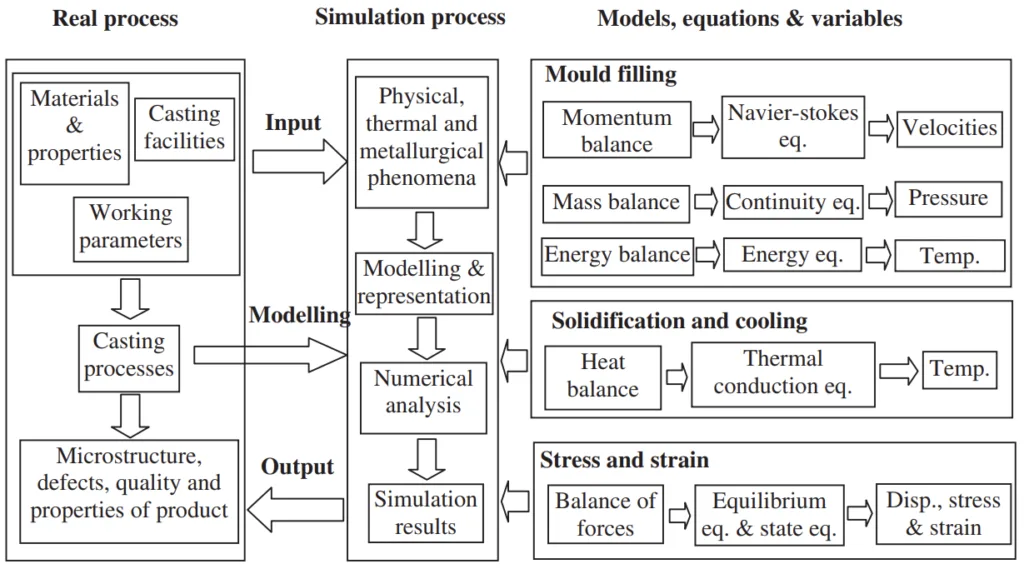
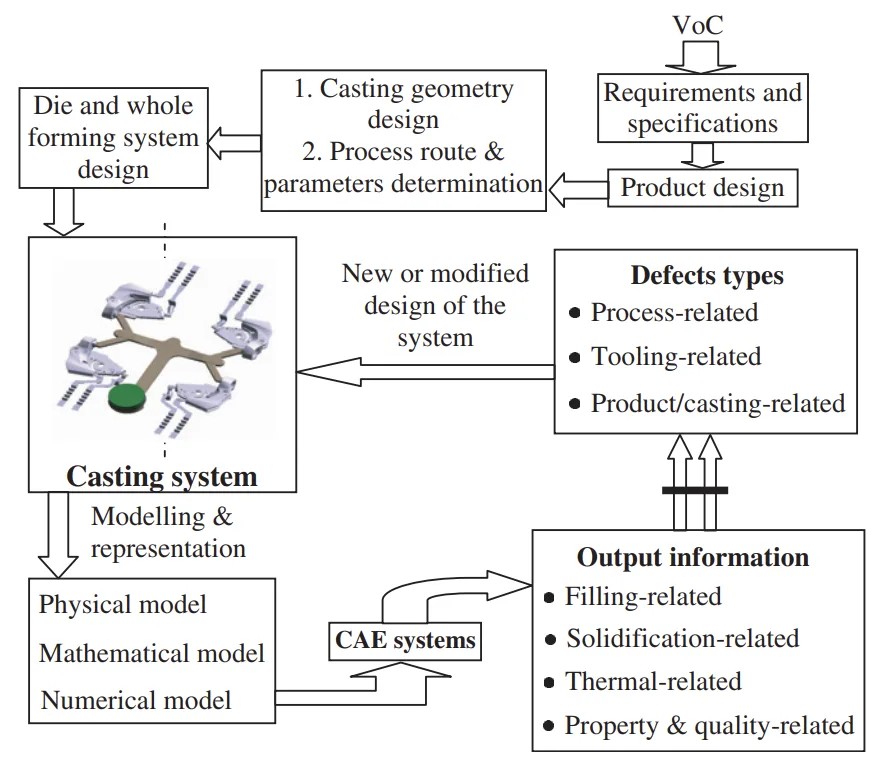
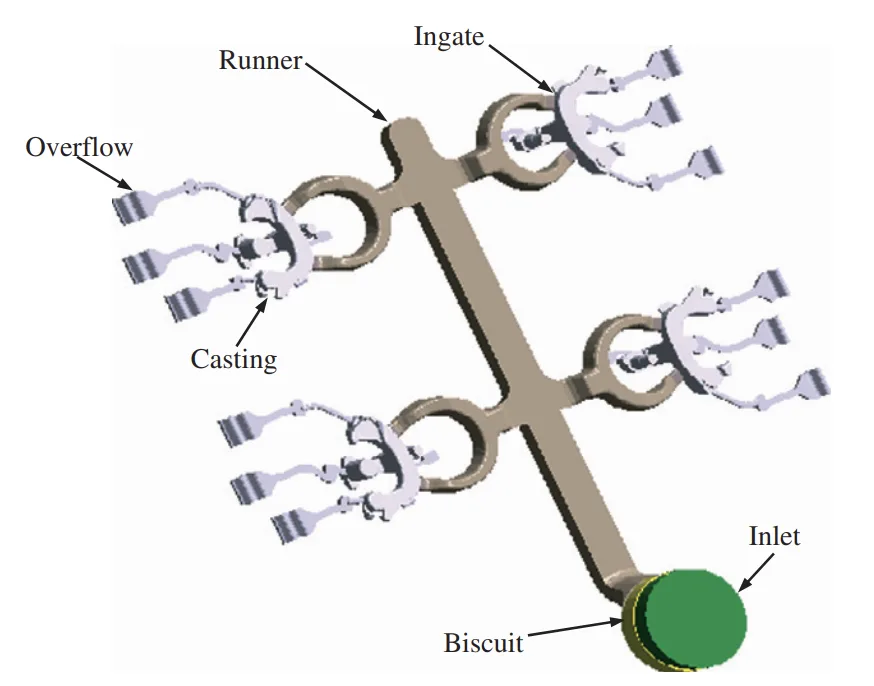
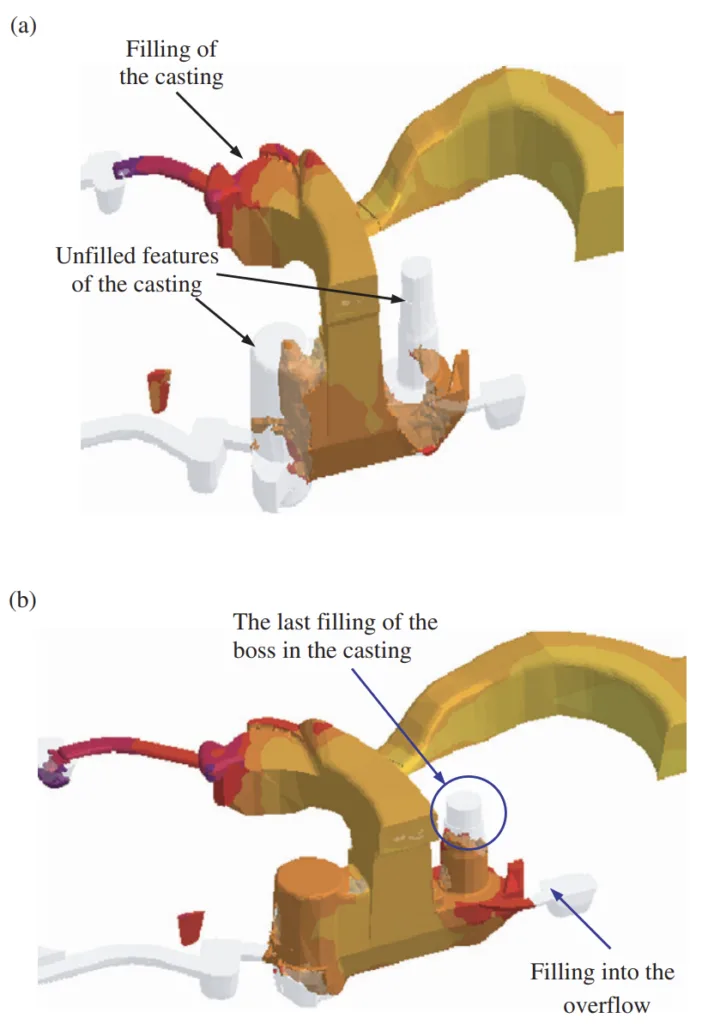
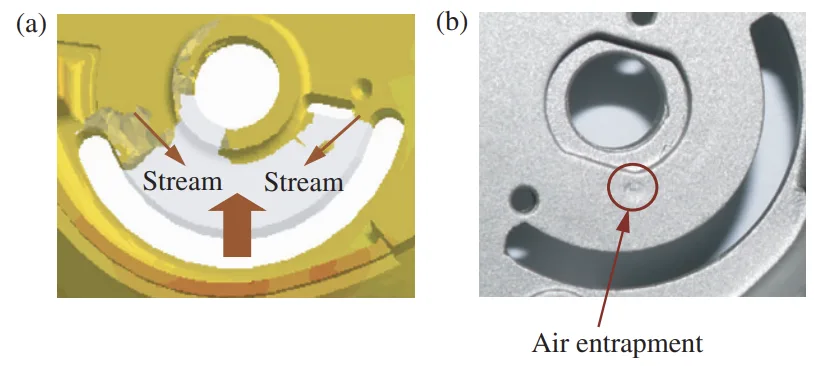
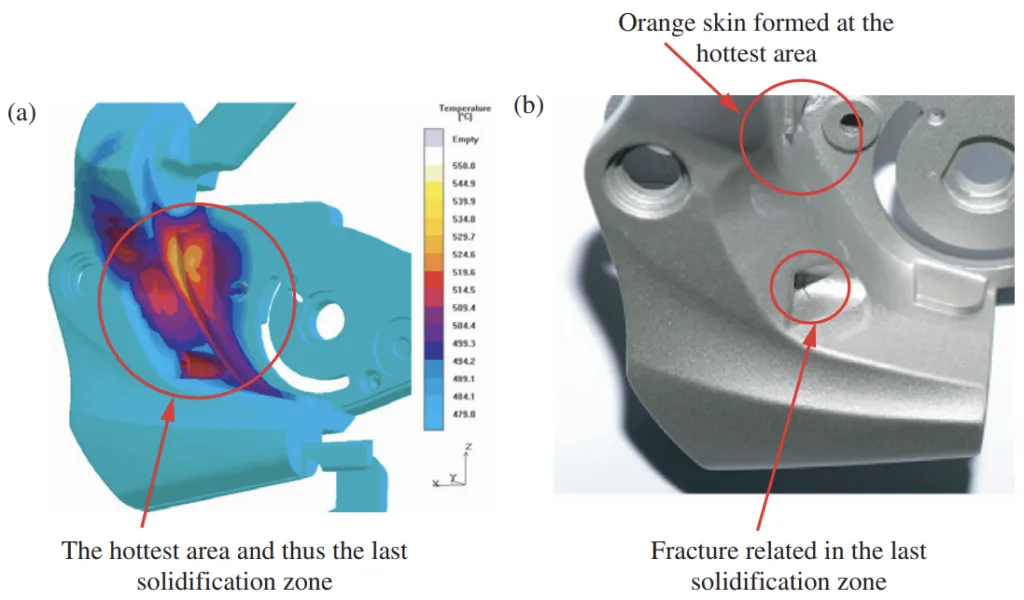
6. 결론:
주요 결과 요약:
본 연구는 다이캐스팅 공정에서 시뮬레이션 기반 주조 제품 결함 예측의 효과를 결정적으로 입증합니다. CAE 시뮬레이션을 활용함으로써 충전, 응고 및 이젝션 후 거동을 포함한 복잡한 주조 공정을 가상으로 구현하고 분석할 수 있습니다. 본 연구는 산업 사례 연구를 통해 검증된 시뮬레이션 기반 결함 예측을 위한 포괄적인 프레임워크, 절차 및 공정을 명확히 제시합니다. 연구 결과는 CAE 시뮬레이션이 공정 관련 결함을 식별하고 예측하는 강력한 도구임을 확인시켜 주며, 이는 주조 제품 개발에서 기존의 시행착오 방법에 대한 의존도를 줄여줍니다.
연구의 학문적 의의:
본 연구의 학문적 의의는 CAE 시뮬레이션을 다이캐스팅 제품 개발 패러다임에 통합하는 체계적인 접근 방식에 있습니다. 단편적인 접근 방식을 넘어 주조 공정에 대한 전체적인 시각을 제공하는 구조화된 결함 예측 방법론을 제시합니다. 본 연구는 CAE 시뮬레이션이 중요한 공정 매개변수와 다이캐스팅의 결함 형성과의 관계를 밝히는 데 어떻게 효과적으로 활용될 수 있는지에 대한 이론적 이해를 높입니다. 시뮬레이션 출력을 분류하고 특정 결함 유형과 연관시킴으로써 본 연구는 주조 공정 최적화 및 품질 보증을 위한 과학적 기반을 강화합니다.
실용적 의미:
본 연구의 실용적 의미는 다이캐스팅 산업에 상당한 영향을 미칩니다. 본 연구에서 제시된 CAE 시뮬레이션 기술의 적용은 다음과 같은 경로를 제공합니다:
- 시행착오 감소: 주조 공정을 가상으로 시뮬레이션함으로써 제조업체는 작업장에서 비용이 많이 들고 시간이 오래 걸리는 물리적 실험을 최소화할 수 있습니다.
- 제품 개발 비용 절감: 시뮬레이션을 통한 잠재적 결함의 조기 발견 및 완화는 다운스트림 재작업, 불량률 및 전반적인 생산 비용을 크게 줄일 수 있습니다.
- 제품 출시 시간 단축: CAE 기반 설계 최적화로 촉진된 간소화된 제품 개발 주기는 주조 제품을 시장에 더 빠르게 출시할 수 있도록 합니다.
- 주조 품질 향상: 시뮬레이션을 통한 결함 메커니즘 및 공정 매개변수에 대한 향상된 이해는 제품 품질, 치수 정확도 및 기능적 성능 향상으로 이어집니다.
- 주조 설계 및 공정 최적화: CAE 시뮬레이션은 주조 형상, 금형 설계, 공정 매개변수 및 냉각 전략을 최적화하기 위한 실행 가능한 통찰력을 제공하여 보다 효율적이고 견고한 주조 공정을 구현할 수 있도록 합니다.
연구의 한계점
본 연구는 CAE 시뮬레이션의 능력을 효과적으로 입증하지만, 잠재적인 한계점을 언급하는 것이 중요합니다. 사례 연구는 주로 4구멍 HPDC 공정 및 특정 재료 (AlSi9Cu3 및 X38CrMoV5)에 초점을 맞추고 있습니다. 연구 결과의 일반화 가능성을 다른 주조 공정 (예: 중력 다이캐스팅, 저압 다이캐스팅) 및 더 넓은 범위의 재료에 적용하려면 추가 연구가 필요할 수 있습니다. 또한, 시뮬레이션 결과의 정확도는 재료 물성치 및 공정 매개변수를 포함한 입력 데이터의 충실도에 따라 달라집니다. 이러한 한계에도 불구하고 본 연구는 다이캐스팅 결함 예측에 CAE 시뮬레이션을 광범위하게 적용하기 위한 강력한 기반을 제공합니다.
7. 향후 후속 연구:
- 후속 연구 방향
향후 연구는 HPDC 외에 중력 다이캐스팅 및 저압 다이캐스팅을 포함하여 더 넓은 범위의 주조 공정에 제시된 CAE 시뮬레이션 프레임워크의 적용을 확대하는 데 초점을 맞춰야 합니다. 철 및 비철 합금을 포함한 다양한 주조 재료에 대한 방법론의 효과를 조사하는 것도 중요합니다. 추가 연구에서는 실시간 공정 모니터링 및 제어 시스템과 CAE 시뮬레이션을 통합하여 생산 중 적응형 공정 최적화를 가능하게 하는 방안을 모색할 수 있습니다. - 추가 탐구가 필요한 영역
추가 탐구가 필요한 영역에는 CAE 소프트웨어 내에서 보다 정교하고 예측 가능한 결함 모델 개발, 특히 열간 균열 및 피로 관련 파괴와 같은 복잡한 결함 유형에 대한 모델 개발이 포함됩니다. 더 빠른 처리 시간과 신속한 제품 개발 주기 통합을 가능하게 하기 위해 시뮬레이션의 계산 효율성을 향상시키는 것도 필수적입니다. 결함 예측 정확도 및 공정 최적화 기능을 향상시키기 위해 다중 물리 시뮬레이션 및 머신 러닝 알고리즘과 같은 고급 시뮬레이션 기술을 사용하는 것을 조사하는 것은 미래 연구를 위한 유망한 방향을 제시합니다.
8. 참고 문헌:
- Barriere, T., Liu, B., and Gelin, J.C., 2003. Determination of the optimal process parameters in metal injection molding from experiments and numerical modeling. Journal of Materials Processing Technology, 143–144 (December), 636-644.
- Bird, R.B., Stewart, W.E., and Lightfoot, E.N., 1960. Transport Phenomena. New York: J. Wiley & Sons.
- Cleary, P., et al., 2002. Flow modeling in casting processes. Applied Mathematical Modeling, 26, 171-190.
- Dai, X., et al., 2003. Effects of runner system design on the mechanical strength of Al-7Si-Mg alloy castings. Materials Science and Engineering: A, 354 (1), 315–325.
- Fuh, J.Y.H., et al., 2004. Computer-aided Injection Mould Design and Manufacture. New York: Marcel Dekker.
- Guo, Z., et al., 2005. Modelling of materials properties and behavior critical to casting simulation. Materials Science and Engineering: A, 413-414, 465-469.
- Hsu, Y.L. and Yu, C.C., 2006. Computer simulation of casting process of aluminum wheels a case study. Proceedings of the I MECH E Part B Journal of Engineering Manufacture, 220 (2), 203-211.
- Hu, B.H., et al., 2000. Design and optimization of runner and gating systems for the die casting of thin-walled magnesium telecommunication parts through numerical simulation. Journal of Materials Processing Technology, 105 (1), 128-133.
- Krimpenis, A., et al., 2006. Simulation-based selection of optimum pressure die-casting process parameters using neural nets and genetic algorithms. International Journal of Advanced Manufanuring Technology, 27 (5–6), 509–517.
- Lewis, R.W. and Ravindran, K., 2000. Finite element simulation of metal casting. International Journal for Numerical Methods in Engineering, 47 (1–3), 29–59.
- Louvo, A., 1997. Casting simulation as a tool in concurrent engineering. In: International ADI and simulation conference, 28–30 May, Espoo, Finland.
- McMillin, T., Hartmann, G., and Egner-Walter, A., 2002. CAE opens new frontier in casting design. Engineered Casting Solutions, Spring 2002, 29–31.
- Midea, A., et al., 2000. Using computer modeling to optimize casting processes. Modern Casting, 90, May 2000, 4-10.
- Mirbagheri, S.M.H., et al., 2002. Simulation of melt flow in coated mould cavity in the casting process. Journal of Materials Processing Technology, 142 (2), 493–507.
- Mochnacki, B., Lara, S., and Pawlak, E., 2005. Multiscale model of segregation process. Journal of Materials Processing Technology, 162–163, May 2005, 766–769.
- Monroe, C. and Beckermann, C., 2005. Development of a hot tear indicator for steel castings. Materials Science and Engineering: A, 413-414, 30-36.
- Naher, S., Brabazon, D., and Looney, L., 2003. Simulation of the stir casting process. Journal of Materials Processing Technology, 143-144, 567–571.
- Neumann, L., et al., 2005. Prediction of texture induced anisotropy by through-process modelling. Materials Science Forum, 495–497, 1657–1662.
- Peng, Y.H., et al., 2005. Numerical study on the low pressure die casting of AZ91D wheel hub. Materials Science Forum, 488-489, 393-396.
- Sequeira, W., et al., 2001. Optimization of die casting part design, process parameters and process control using newly die casting simulation tool. In: proceedings of die casting in the 21th century, Cincinnati, Ohio.
- Sturm, J.C., et al., 2001. Optimized development for castings and casting processes. In: 19th CAD-FEM users' meeting 2001, international congress on FEM technology, 17–19 October, Postdam, Germany.
- Ulysse, P., 1999. Optimal extrusion die design to achieve flow balance. International Journal of Machine Tools and Manufacture, 39 (7), 1047–1064.
- Venkatesan, A., Gopinath, V.M., and Rajadurai, A., 2005. Simulation of casting solidification and its grain structure prediction using FEM. Journal of Materials Processing Technology, 168 (1), 10-15.
- Zhang, X.P., Xiong, S.M., and Xu, Q.Y., 2006. Numerical methods to improve the computational efficiency of solidification simulation for the investment casting process. Journal of Materials Processing Technology, 173 (1), 70–74.
9. 저작권:
- 본 자료는 "M.W. Fu & M.S. Yong"의 논문: "다이캐스팅 공정에서 시뮬레이션 기반 주조 제품 결함 예측"을 기반으로 작성되었습니다.
- 논문 출처: http://dx.doi.org/10.1080/00207540801935616
본 자료는 상기 논문을 기반으로 요약되었으며, 상업적 목적으로 무단 사용하는 것을 금지합니다.
Copyright © 2025 CASTMAN. All rights reserved.