본 논문 요약은 Journal of Manufacturing Processes에 게재된 "A complete computer aided engineering (CAE) modelling and optimization of high pressure die casting (HPDC) process" 논문을 기반으로 작성되었습니다.
1. 개요:
- 제목: 완전한 전산 유체 역학(CAE) 모델링 및 고압 다이캐스팅(HPDC) 공정의 최적화 (A complete computer aided engineering (CAE) modelling and optimization of high pressure die casting (HPDC) process)
- 저자: K. Dou, E. Lordan, Y.J. Zhang, A. Jacot, Z.Y. Fan
- 발행 연도: 2020년
- 발행 저널/학회: Journal of Manufacturing Processes, Elsevier Ltd. / The Society of Manufacturing Engineers
- 키워드: CAE 시뮬레이션, 유한 요소법, HPDC, 공정 최적화, CFD, 기계적 특성 (CAE simulation, finite element method, HPDC, Process optimization, CFD, Mechanical property)
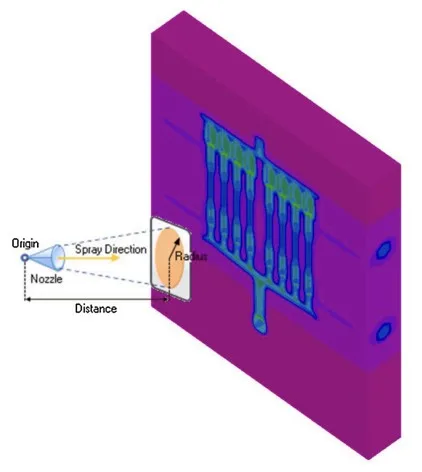
2. 연구 배경:
- 연구 주제의 사회적/학문적 맥락: 전산 유체 역학(CAE)의 응용은 효율성과 신뢰성으로 인해 제조 산업에서 점점 더 보편화되고 있습니다. 주조 산업에서 CAE 기반 수치 모델링은 기존의 시행착오식 연구 개발(R&D) 절차를 여러 측면에서 대체했습니다. 고급 병렬 컴퓨팅 기술과 정교한 계산 모델을 통해 다양한 주조 조건에서 유체 흐름, 열 전달, 응고 및 결함 형성 거동을 자세히 조사할 수 있습니다. 이는 원하는 미세 구조 및 기계적 특성을 달성하기 위한 부품 설계 및 주조 매개변수 최적화를 용이하게 합니다. 공정 조건, 주조 품질 및 기계적 특성 간의 직접적인 상관 관계를 설정하는 것은 중력 다이캐스팅, 고압 다이캐스팅(HPDC) 및 연속 주조와 같은 공정에 매우 중요하며, 실용적이고 경제적이며 에너지 효율적인 솔루션을 제공합니다.
- 기존 연구의 한계: HPDC 공정의 수치 시뮬레이션이 새로운 것은 아니지만, 이전 연구는 종종 공정에 영향을 미치는 개별 현상에 초점을 맞추었습니다. 여기에는 게이팅 시스템 설계, 잉게이트에서의 액체 제트 최적화, 용융 흐름 특성, 재산화 공정 및 샷 슬리브 충전 효과에 대한 연구가 포함됩니다. 기존 연구는 종종 다이캐스팅 기계 매개변수, 플런저 속도 또는 러너 설계와 같은 단일 측면을 개별적으로 조사했습니다. 상류 하위 공정을 포함하여 전체 HPDC 사이클을 고려하는 포괄적인 접근 방식이 부족했습니다.
- 연구의 필요성: 본 논문은 전체 HPDC 공정을 단일 수학적 모델로 통합하는 전체론적 시뮬레이션 접근 방식의 필요성을 강조합니다. 여기에는 다이 가열, 열 다이 사이클링, 샷 슬리브 예비 충전, 저속/고속 사출, 다이 충전/응고 및 가압이 포함됩니다. 이러한 완전한 모델은 이러한 하위 공정의 복잡한 상호 작용을 이해하고 주조 품질 및 기계적 특성을 효과적으로 개선하기 위해 HPDC 공정을 최적화하는 데 필수적입니다. 본 연구는 HPDC에 대한 포괄적인 CAE 모델을 개발하고 검증하여 단편적인 연구의 한계를 해결하는 것을 목표로 합니다.
3. 연구 목적 및 연구 질문:
- 연구 목적: 주요 연구 목적은 고압 다이캐스팅(HPDC) 공정에 대한 완전한 전산 유체 역학(CAE) 모델을 개발하고 검증하는 것입니다. 이 모델은 ProCAST 소프트웨어를 사용하여 다이 가열부터 응고 및 가압까지 전체 HPDC 사이클을 시뮬레이션하는 것을 목표로 합니다. 궁극적으로 목표는 이 포괄적인 CAE 접근 방식을 공정 최적화에 사용하여 주조 품질과 기계적 특성을 개선하는 방법을 입증하는 것입니다.
- 주요 연구 질문:
- 모든 관련 하위 공정 및 상호 작용을 포함하여 전체 HPDC 공정을 정확하게 시뮬레이션하기 위해 완전한 CAE 모델을 개발할 수 있는가?
- 용융물과 다이/샷 슬리브 사이의 계면 열전달 계수(iHTC)를 정확하게 결정하고 CAE 모델에 통합하는 방법은 무엇인가?
- 동적 정상 상태 다이 온도를 달성하고 일관된 주조 품질을 보장하는 데 필요한 최적의 열 다이 사이클 수는 얼마인가?
- 사출 단계에서 결함 형성을 최소화하기 위해 CAE 모델을 사용하여 피스톤 샷 프로파일을 최적화하는 방법은 무엇인가?
- CAE 시뮬레이션에서 파생된 최적화된 공정 매개변수가 HPDC 부품의 기계적 특성을 눈에 띄게 개선할 수 있는가?
- 연구 가설: (논문에 명시적으로 언급되지는 않았지만 추론 가능)
- 조정된 iHTC를 통합하고 전체 HPDC 사이클을 시뮬레이션하는 포괄적인 CAE 모델은 공정 조건과 주조 품질을 정확하게 예측할 것이다.
- CAE 시뮬레이션을 통한 열 다이 사이클 최적화는 보다 안정적인 다이 온도와 향상된 주조 일관성으로 이어질 것이다.
- CAE 시뮬레이션을 기반으로 피스톤 샷 프로파일을 조정하면 다이 충전 중 결함 형성(예: 공기 혼입)이 감소할 것이다.
- CAE 최적화된 공정 매개변수를 사용하여 주조된 HPDC 부품은 최적화되지 않은 매개변수로 생산된 부품에 비해 향상된 기계적 특성(항복 강도, 인장 강도 및 연신율)을 나타낼 것이다.
4. 연구 방법론:
- 연구 설계: 본 연구는 시뮬레이션 기반 실험 설계를 채택합니다. ProCAST 소프트웨어 내에서 유한 요소법(FEM)을 사용하여 HPDC 공정의 완전한 CAE 모델을 개발했습니다. 그런 다음 모델을 사용하여 HPDC 공정을 시뮬레이션하고 최적화했습니다. 최적화된 매개변수를 사용하여 인장 막대를 주조하고 기계적 특성을 테스트하여 실험적 검증을 수행했습니다.
- 자료 수집 방법:
- 열전대 측정 및 적외선 이미징: 이러한 방법은 다이 표면 온도 분포를 측정하고 CAE 모델 내에서 계면 열전달 계수(iHTC)를 조정하는 데 사용되었습니다. 시간 종속 iHTC는 이러한 측정에서 파생되어 시뮬레이션에 통합되었습니다.
- 기계적 특성 시험: 항복 강도, 인장 강도(UTS) 및 연신율을 평가하기 위해 주조된 인장 막대에 대한 인장 시험을 수행했습니다. 이러한 실험 결과는 CAE 최적화된 공정 매개변수의 효과를 평가하는 데 사용되었습니다.
- 공정 매개변수 데이터: 다이 가열, 열 다이 사이클링, 샷 슬리브 예비 충전, 사출, 가압, 부품 배출, 다이 분사 및 공기 블로잉과 같은 다양한 HPDC 단계의 시간 지속 시간과 순서를 실제 HPDC 실험에서 기록하고 CAE 모델의 입력으로 사용했습니다.
- 분석 방법:
- 유한 요소법(FEM) 시뮬레이션: 전체 HPDC 공정은 ProCAST 내에서 FEM을 사용하여 시뮬레이션되었습니다. Visual-Mesh, Visual-Cast 및 Visual-Viewer 모듈은 메쉬 생성, 모델 계산 및 결과 분석에 각각 활용되었습니다. 효율적인 계산을 위해 병렬 컴퓨팅 기술을 사용했습니다.
- 지배 방정식: 용융물 사출, 다이 충전 및 응고는 엔탈피 방법을 기반으로 3D FEM을 사용하여 모델링되었습니다. 용융물 난류는 표준 k-ε 난류 모델을 사용하여 설명되었습니다. VOF(Volume of Fluid) 방법은 용융물 자유 표면을 추적하는 데 사용되었습니다. 연속성 및 운동량 방정식이 해결되었습니다(단순화된 버전이 논문에 제시됨).
- 최적화 방법론: HPDC 공정 최적화는 두 단계로 수행되었습니다.
- 열 다이 사이클 최적화: 동적 정상 상태 다이 온도를 달성하기 위한 최적의 열 다이 사이클 수를 결정합니다.
- 피스톤 샷 프로파일 최적화: 사출 중 결함 형성, 특히 공기 혼입을 최소화하기 위해 피스톤 샷 프로파일을 조정합니다.
- 통계 분석: 인장 시험에서 얻은 기계적 특성 데이터를 분석하여 최적화된 매개변수와 최적화되지 않은 매개변수로 생산된 주조물의 성능을 비교했습니다. 항복 강도(YS), 인장 강도(UTS) 및 연신율(El)에 대한 평균 및 표준 편차를 계산했습니다.
- 연구 대상 및 범위:
- 재료: 알루미늄 합금 A356이 시뮬레이션 및 실험에 사용되었습니다. 온도 의존적 재료 특성은 ProCAST 데이터베이스에서 얻었습니다.
- 공정: 콜드 챔버 HPDC 기계를 사용한 고압 다이캐스팅(HPDC) 공정.
- 시뮬레이션 범위: 다이 가열, 열 다이 사이클링, 샷 슬리브 예비 충전, 저속/고속 사출, 다이 충전/응고 및 가압을 포함한 전체 HPDC 사이클.
- 실험 범위: 표준 및 CAE 최적화된 피스톤 샷 프로파일을 모두 사용하여 인장 막대를 주조한 후 기계적 특성 시험을 수행합니다.
5. 주요 연구 결과:
- 주요 연구 결과:
- 최적 열 다이 사이클: CAE 시뮬레이션 결과 6~7회의 열 사이클 후 다이 표면 온도 분포가 준정상 상태에 도달하는 것으로 나타났습니다. 따라서 7번째 사이클 후의 온도 분포를 후속 다이 충전 시뮬레이션에 사용했습니다.
- 최적화된 피스톤 샷 프로파일: 다양한 피스톤 저속 샷 가속 위치를 사용한 시뮬레이션 결과 초기 위치에서 10mm 떨어진 가속 위치가 주조물에서 가장 적고 가장 균일한 공기 혼입을 초래하는 것으로 나타났습니다.
- 향상된 기계적 특성: 최적화된 피스톤 샷 프로파일(10mm 가속 위치, 0.4-0.6m/s의 저속 샷 속도)을 사용하여 주조된 인장 막대는 향상된 기계적 특성을 나타냈습니다. 특히 UTS 및 연신율 값은 가장 높았고 표준 편차는 테스트된 다른 프로파일에 비해 이 최적화된 프로파일로 생산된 샘플에서 가장 낮았습니다.
- 통계적/정성적 분석 결과:
- 기계적 특성 데이터 (표 3): 인장 시험 결과 0.4-0.6m/s의 피스톤 속도 프로파일이 가장 높은 평균 UTS 및 연신율 값과 이러한 특성에 대한 가장 낮은 표준 편차를 나타내어 향상되고 보다 일관된 기계적 성능을 나타내는 것으로 나타났습니다.
- 공기 혼입 시뮬레이션 (그림 17): 공기 혼입 분포에 대한 정성적 분석 결과 10mm 피스톤 저속 샷 가속 위치가 다른 위치에 비해 더 적고 더 균일하게 분포된 공기 혼입으로 이어지는 것으로 나타났습니다.
- 산화물 형성 시뮬레이션 (그림 19): 산화물 지표 시뮬레이션 결과 0.4-0.6m/s의 저속 샷 속도가 다른 속도에 비해 상대적으로 균일한 산화물 분포와 낮은 전체 산화물 경향을 초래하는 것으로 나타났습니다.
- 데이터 해석: 결과는 CAE 시뮬레이션이 HPDC 공정을 효과적으로 모델링하고 최적화할 수 있음을 보여줍니다. 열 다이 사이클을 최적화하면 열 안정성이 보장되고 CAE 통찰력을 기반으로 피스톤 샷 프로파일을 조정하면 결함 형성을 최소화하고 기계적 특성을 개선할 수 있습니다. 인장 시험을 통한 실험적 검증은 CAE 예측을 뒷받침하며, 최적화된 공정 매개변수와 향상된 주조 성능 간의 명확한 연관성을 보여줍니다.
- 그림 목록:
- 그림 1. 전체 HPDC 공정의 모델링 워크플로우.
- 그림 2. 전체 사이클 동안의 일반적인 HPDC 절차.
- 그림 3. 계산에 사용된 구성 및 하이브리드 FEM 메쉬 (½ 대칭).
- 그림 4. A356 합금 열물리적 특성.
- 그림 5. 본 연구에서 사용된 시간 종속 iHTC.
- 그림 6. 대기에서 가열 후 다이 표면의 온도 분포.
- 그림 7. 6번째 HPDC 사이클 동안 다이 표면의 온도 분포.
- 그림 8. 부품 배출 후 분사/블로잉의 개략도.
- 그림 9. HPDC 중 얻은 적외선 이미지와 예측된 다이 표면 온도 분포 비교.
- 그림 10. 다중 열 사이클에서 다이 표면의 샘플링 위치에서 계산된 온도 곡선.
- 그림 11. 샷 슬리브 충전 중 사용된 유량 곡선.
- 그림 12. 피스톤 사출 전 샷 슬리브 충전 중 용융물의 흐름 및 온도 진화, 두 개의 시점에서 본 이미지.
- 그림 13. 샷 슬리브를 따라 외부에서 응고된 결정의 분포.
- 그림 14. 다이 캐비티에서 용융물의 충전 순서 및 공기 분포.
- 그림 15. 응고 시간이 0.7초 미만인 위치에 대한 단면 컷오프.
- 그림 16. 저속 샷 가속 위치가 다른 피스톤 샷 곡선.
- 그림 17. 저속 샷 가속 위치가 다른 주조물에서 공기 혼입의 모델링 결과.
- 그림 18. 저속 샷 속도가 다른 피스톤 샷 곡선.
- 그림 19. 저속 샷 속도 크기가 다른 모델링 결과 비교.
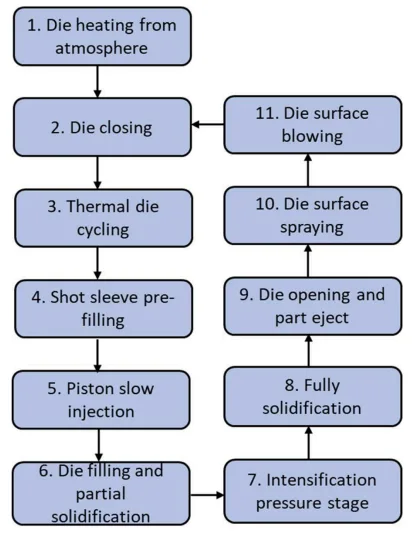
6. Conclusion and Discussion:
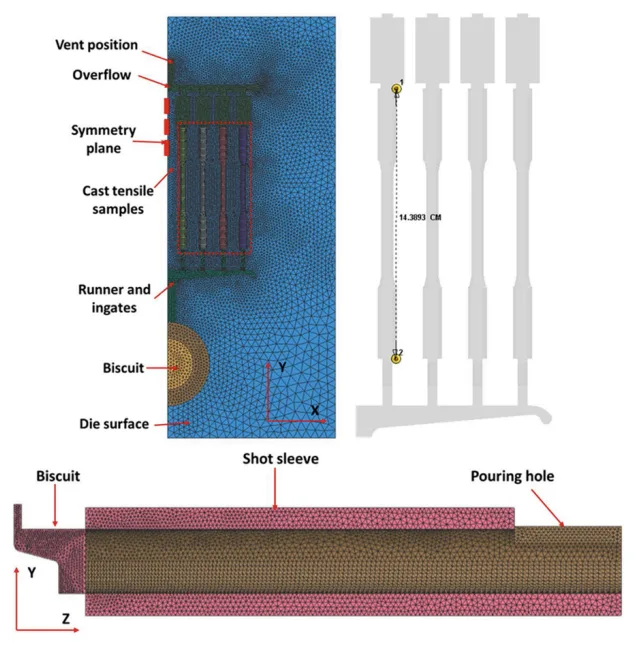
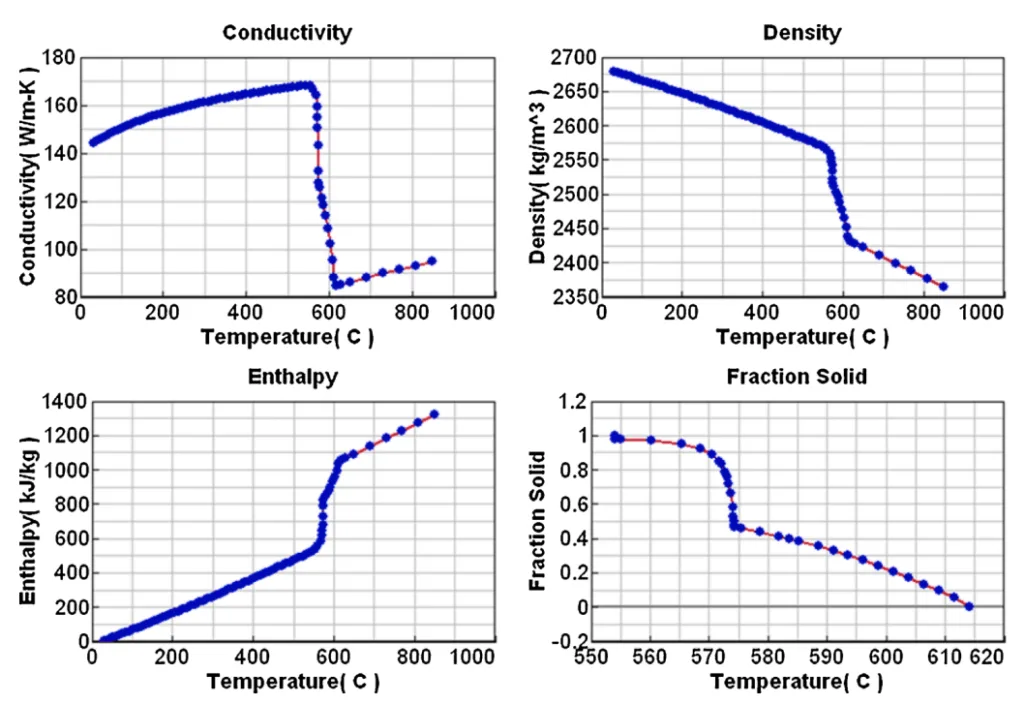
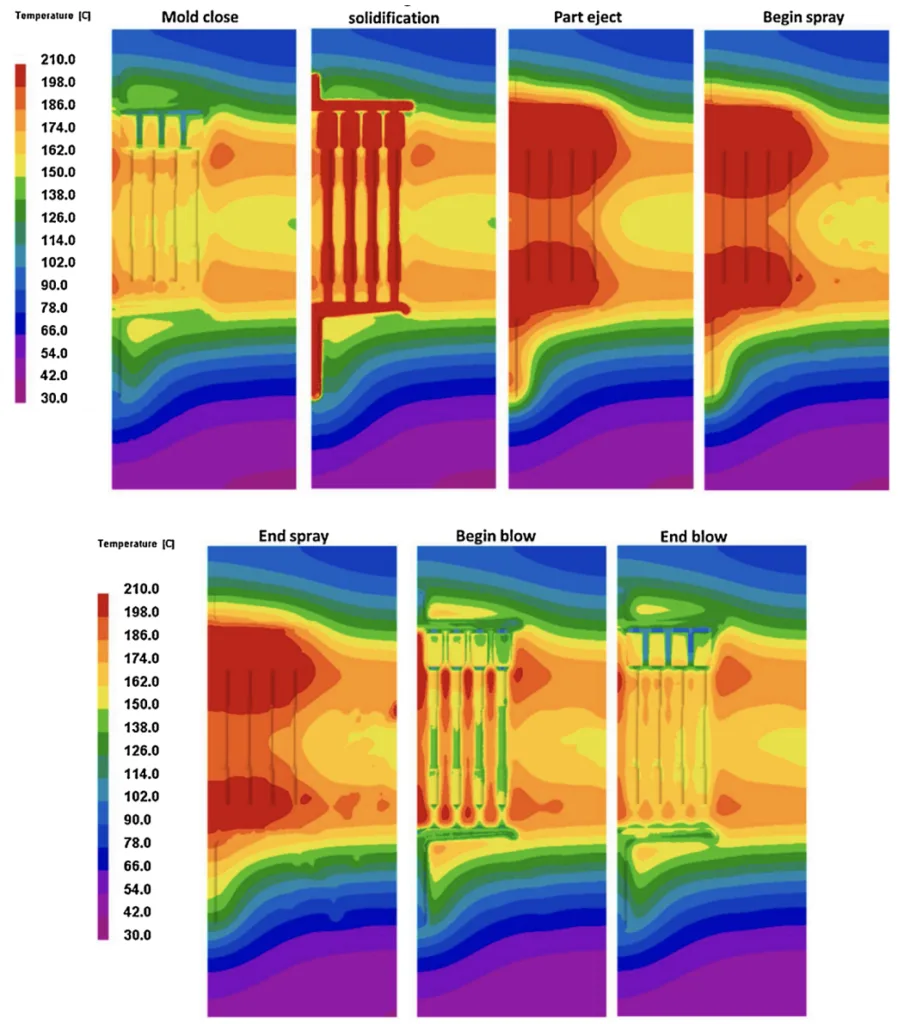
6. 결론 및 논의:
- 주요 결과 요약: 본 연구에서는 ProCAST 플랫폼을 사용하여 콜드 챔버 HPDC에 대한 완전한 CAE 시뮬레이션 접근 방식을 성공적으로 구축했습니다. 이 모델은 다이 가열, 열 다이 사이클링, 샷 슬리브 예비 충전, 사출 및 응고를 통합합니다. 시뮬레이션을 통해 열 다이 사이클 및 피스톤 샷 프로파일의 최적화를 달성했습니다. 실험적 검증을 통해 CAE 최적화된 매개변수로 생산된 주조물이 향상된 기계적 특성을 나타내는 것으로 확인되었습니다. 최적의 피스톤 저속 샷 가속 위치는 10mm이고, 최적의 저속 샷 속도 범위는 연구된 조건에서 0.4-0.6m/s였습니다.
- 연구의 학문적 의의: 본 연구는 고립된 측면에 초점을 맞춘 이전 연구의 한계를 해결하면서 전체 HPDC 공정을 시뮬레이션하기 위한 포괄적인 방법론을 제공합니다. 실험 데이터(iHTC)를 CAE 모델에 통합하면 정확성과 예측 능력이 향상됩니다. 본 연구는 HPDC 공정 내의 복잡한 상호 작용을 이해하고 공정 매개변수를 최적화하기 위한 전체론적 CAE 접근 방식의 가치를 입증합니다.
- 실용적 의미: 개발된 CAE 방법론은 HPDC 엔지니어에게 광범위하고 비용이 많이 드는 경험적 시험 없이 주조 매개변수와 HPDC 셀 내의 작동 조건을 최적화할 수 있는 체계적이고 비용 효율적인 경로를 제공합니다. 이 가상 엔지니어링 접근 방식을 사용함으로써 제조업체는 결함을 줄이고, 주조 품질을 개선하고, 기계적 특성을 향상시키며, 잠재적으로 HPDC 공정에서 재료 및 에너지 소비를 줄일 수 있습니다. 최적의 피스톤 샷 프로파일 매개변수에 대한 연구 결과는 공정 설정에 대한 실용적인 지침을 제공합니다.
- 연구의 한계: ProCAST에서 공기 혼입 예측은 정성적인 것으로 언급됩니다. 유용한 지침을 제공하지만 공기 혼입 수준에 대한 정확한 정량적 예측을 제공하지 못할 수 있습니다. 공기 혼입 모델을 추가로 개선하고 검증하는 것이 유익할 수 있습니다. 본 연구는 A356 합금과 특정 HPDC 설정에 초점을 맞추었습니다. 최적화된 매개변수의 다른 합금 및 주조 시스템으로의 일반화 가능성은 추가 조사가 필요합니다.
7. 향후 후속 연구:
- 후속 연구 방향:
- 개발된 CAE 모델을 사용하여 HPDC에서 용융 흐름, 응고 및 결함 형성에 대한 다양한 공정 매개변수(피스톤 샷 프로파일 및 열 다이 사이클 외)의 영향을 추가로 조사합니다.
- HPDC 공정에서 결함 형성을 억제하기 위한 새로운 기술을 탐색하고 검증하며, 잠재적으로 CAE 시뮬레이션을 사용하여 물리적 구현 전에 이러한 기술을 설계하고 최적화합니다.
- 특히 결함 예측(예: 기공, 공기 혼입, 산화물)에 대해 CAE 모델의 보다 자세한 정량적 검증을 수행하여 시뮬레이션 결과를 실험 측정과 비교합니다.
- 추가 탐구가 필요한 영역:
- HPDC에서 용융 흐름 특성, 응고 거동 및 결함 형성 메커니즘 간의 복잡한 상호 작용에 대한 심층적인 조사.
- 포괄적인 CAE 모델의 적용을 더 넓은 범위의 알루미늄 합금 및 기타 다이캐스팅 합금(예: 마그네슘 합금)으로 확장합니다.
- HPDC 시뮬레이션에서 결함 형성, 특히 공기 혼입 및 산화물 생성을 예측하기 위한 보다 정교하고 정량적으로 정확한 모델을 개발합니다.
- HPDC에서 동적 공정 제어 및 최적화를 위해 실시간 공정 모니터링 데이터를 CAE 모델과 통합합니다.
8. 참고 문헌:
- [1] Zhou Y, Guo Z, Xiong SM. Effect of runner design on the externally solidified crystals in vacuum die-cast Mg-3.0Nd-0.3Zn-0.6Zr alloy. J. Mater. Process. Technol. 2019;267:366-75. https://doi.org/10.1016/j.jmatprotec.2018.12.032.
- [2] Gunasegaram DR, Givord M, O'Donnell RG, Finnin BR. Improvements engineered in UTS and elongation of aluminum alloy high pressure die castings through the alteration of runner geometry and plunger velocity. Mater. Sci. Eng. A. 2013;559: 276-86. https://doi.org/10.1016/j.msea.2012.08.09
- [3] Tsoukalas VD. The effect of die casting machine parameters on porosity of aluminium die castings. Int. J. Cast Met. Res. 2003;15:581-8. https://doi.org/ 10.1080/13640461.2003.11819544.
- [4] wu Wu M, bo Li X, peng Guo Z, mei Xiong S. Effects of process parameters on morphology and distribution of externally solidified crystals in microstructure of magnesium alloy die castings. China Foundry. 2018;15:139-44. https://doi.org/ 10.1007/s41230-018-7242-z.
- [5] Kwon HJ, Kwon HK. Computer aided engineering (CAE) simulation for the design optimization of gate system on high pressure die casting (HPDC) process. Robot. Comput. Integr. Manuf. 2019;55:147-53. https://doi.org/10.1016/j. rcim.2018.01.003.
- [6] Pereira GG, Cleary PW, Serizawa Y. Prediction of fluid flow through and jet formation from a high pressure nozzle using Smoothed Particle Hydrodynamics. Chem. Eng. Sci. 2018;178:12-26. https://doi.org/10.1016/j.ces.2017.1
- [7] Cleary PW, Ha J, Prakash M, Nguyen T. Short shots and industrial case studies: Understanding fluid flow and solidification in high pressure die casting. Appl. Math. Model. 2010. https://doi.org/10.1016/j.apm.2009.10.015.
- [8] Brůna M, Bolibruchová D, Pastirčák R. Reoxidation Processes Prediction in Gating System by Numerical Simulation for Aluminium Alloys. Arch. Foundry Eng. 2017; 17:23-6. https://doi.org/10.1515/afe-2017-0084.
- [9] Korti AIN, Abboudi S. Effects of shot sleeve filling on evolution of the free surface and solidification in the high-pressure die casting machine. Int. J. Met. 2017;11: 223-39. https://doi.org/10.1007/s40962-016-0051-5.
- [10] Dou K, Lordan E, Zhang YJ, Jacot A, Fan ZY. Numerical simulation of fluid flow, solidification and defects in high pressure die casting (HPDC) process, IOP Conf. Ser. Mater. Sci. Eng. 2019;529:012058. https://doi.org/10.1088/1757-899X/529/ 1/012058.
- [11] Gleeson J, Gourlay CM, Schaffer PL, Laukli HI. Gate microstructure in an AlSi9MgMn High-Pressure Die Casting. Proc. 12th Int. Conf. Alum. Alloy 2010: 751-6.
- [12] Cao H, Wessén M. Characteristics of microstructure and banded defects in die cast AM50 magnesium components. Int. J. Cast Met. Res. 2005;18:377-84. https://doi. org/10.1179/136404605225023216.
- [13] Hong Hai N. Effect of Pressure on Solidification Process and Mechanical Properties During Semi-Solid Casting by Computational Fluid Dynamics (CFD). Adv. Mater. 2019;7. https://doi.org/10.11648/j.am.20180702.15. 44.
- [14] Yuan Z, Guo Z, Xiong SM. Skin layer of A380 aluminium alloy die castings and its blistering during solution treatment. J. Mater. Sci. Technol. 2019;35:1906–16. https://doi.org/10.1016/j.jmst.2019.05.011.
- [15] Otarawanna S, Gourlay CM, Laukli HI, Dahle AK. Agglomeration and bending of equiaxed crystals during solidification of hypoeutectic Al and Mg alloys. Acta Mater. 2010;58:261-71. https://doi.org/10.1016/j.actamat.2009.09.002.
- [16] Wang BS, Xiong SM. Effects of shot speed and biscuit thickness on externaly solidified crystals of high-pressure diet cast AM60B magnesium alloy. Trans. Nonferrous Met. Soc. China (English Ed. 2011;21:767-72. https://doi.org/ 10.1016/S1003-6326(11)60778-4.
- [17] Jiao XY, Wang J, Liu C, Guo Z, Wang J, Wang Z, Gao J, Xiong SM. Influence of slow-shot speed on PSPs and porosity of AlSi 17 Cu 2.5 alloy during high pressure die casting. J. Mater. Process. Technol. 2019;268:63-9. https://doi.org/10.1016/j. jmatprotec.2019.01.008.
- [18] Yuan L, Xiong S, Liu B, Masayuki M, Yoshihide M, Shingo I. Numerical simulation and optimization of liquid metal flow in the shot sleeve of cold chamber die casting process. MCWASP Conf. Model. Cast. Welding, Adv. Solidif. Process. Opio, Fr. Miner. Met. Mater. Soc. 2006:111-8.
- [19] Wang QL, Xiong SM. Effect of multi-step slow shot speed on microstructure of vacuum die cast AZ91D magnesium alloy. Trans. Nonferrous Met. Soc. China (English Ed. 2015;25:375-80. https://doi.org/10.1016/S1003-6326(15)63613-5.
9. 저작권:
- 본 자료는 "K. Dou, E. Lordan, Y.J. Zhang, A. Jacot, Z.Y. Fan"의 논문: "A complete computer aided engineering (CAE) modelling and optimization of high pressure die casting (HPDC) process"를 기반으로 합니다.
- 논문 출처: https://doi.org/10.1016/j.jmapro.2020.10.062
본 자료는 상기 논문을 기반으로 요약되었으며, 상업적 목적으로 무단 사용하는 것을 금지합니다.
Copyright © 2025 CASTMAN. All rights reserved.