본 문서는 "Taguchi 방법을 이용한 새로운 부분 응고 고압 알루미늄 다이캐스팅 최적화" 연구 논문을 요약하여 다이캐스팅 기술 전문가 및 관심 있는 분들을 위해 주요 내용을 포괄적으로 제공합니다.
1. 개요:
- 제목: Taguchi 방법을 이용한 새로운 부분 응고 고압 알루미늄 다이캐스팅 최적화 (Optimization in Novel Partial-Solid High Pressure Aluminum Die Casting by Taguchi Method)
- 저자: 예크타 베르크 수슬루 (Yekta Berk Suslu), 메흐메트 시락 아카르 (Mehmet Sirac Acar), 미트하트 세놀 (Mithat Senol), 무아메르 무틀루 (Muammer Mutlu), 오즈굴 켈레스 (Ozgul Keles)
- 발행 연도: 2018년
- 발행 저널/학회: 광물, 금속 및 재료 학회 (The Minerals, Metals & Materials Society (TMS)) - Light Metals 2018 컨퍼런스 Proceedings
- 키워드: 고압 다이캐스팅 (High pressure die casting), 부분 응고 가공 (Partial-solid processing), 알루미늄 (Aluminum), Taguchi 방법 (Taguchi method), 최적화 (Optimization)
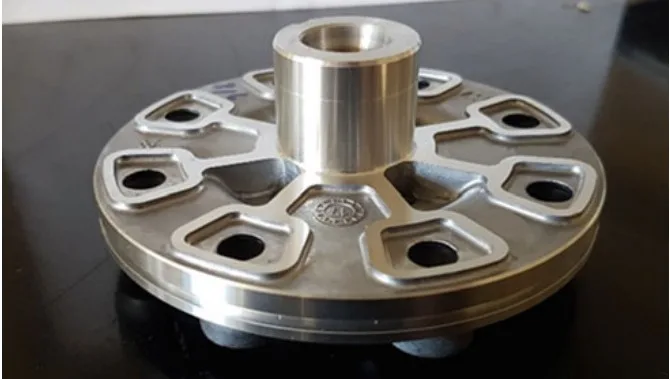
2. 연구 배경:
- 연구 주제의 사회적/학문적 맥락:
- 고압 다이캐스팅 (HPDC)은 자동차, 항공, 가전 산업과 같은 필수 산업에서 부품 생산에 필수적인 제조 공정입니다.
- HPDC의 장점은 빠른 응고로 인한 낮은 사이클 시간으로 대량 생산을 가능하게 합니다.
- 그러나 기공 및 수축은 HPDC에서 효율성과 품질을 저하시키는 주요 결함입니다.
- 기존 연구의 한계:
- 기존의 HPDC 방법은 종종 기공 및 수축 결함을 최소화하는데 어려움을 겪습니다.
- 진공, 냉각 벤트 및 사출 속도 조정과 같은 기술이 도움이 될 수 있지만 이러한 문제를 완전히 제거하지 못할 수 있습니다.
- 기존의 주조 방법, 특히 HPDC는 기공, 수축 및 냉각 슬러그 결함과 같은 결함에 취약합니다.
- 연구의 필요성:
- 기존 HPDC의 한계를 극복하고 부품 품질을 향상시키기 위해 부분 응고 주조가 해결책으로 모색됩니다.
- 부분 응고 주조, 특히 GISS (Gas Induced Semi-Solid) 기술을 사용하면 미세 구조를 수정하고 기계적 특성을 개선할 수 있습니다.
- GISS-HPDC 공정을 최적화하는 것은 고품질 부품을 결함 감소와 함께 생산할 수 있는 잠재력을 최대한 실현하는 데 필요합니다.
- 실험 계획법 접근 방식인 Taguchi 방법은 GISS-HPDC와 관련된 복잡한 매개변수를 최적화하는 데 유용한 도구로 확인되었습니다.
3. 연구 목적 및 연구 질문:
- 연구 목적:
- "A" 등급 품질의 부분 응고 알루미늄 자동차 부품 생산을 위해 고압 다이캐스팅 (HPDC)과 통합된 GISS (Gas Induced Semi-Solid) 기술의 매개변수를 최적화합니다.
- GISS-HPDC에서 기공 수준 및 미세 구조적 특성에 대한 주요 공정 매개변수의 영향을 결정합니다.
- 주요 연구 질문:
- 용융 온도, 가스 취입 시간, 2차 속도 및 게이트 두께는 GISS 기술을 사용한 부분 응고 HPDC에서 기공률에 어떤 영향을 미칩니까?
- 기공을 최소화하고 GISS-HPDC로 생산된 알루미늄 자동차 부품에서 "A" 등급 품질을 달성하기 위한 용융 온도, 가스 취입 시간, 2차 속도 및 게이트 두께의 최적 수준은 무엇입니까?
- GISS 기술은 HPDC 알루미늄 부품의 미세 구조, 특히 구상 구조 형성 및 금속간 화합물상의 분포에 어떤 영향을 미칩니까?
- 연구 가설: (연구 설계에 내재됨)
- Taguchi 방법을 적용하면 GISS-HPDC 알루미늄 자동차 부품에서 기공을 최소화하기 위한 용융 온도, 가스 취입 시간, 2차 속도 및 게이트 두께의 최적 조합을 식별할 수 있습니다.
- GISS 기술은 HPDC 알루미늄 부품에서 구상 미세 구조 형성을 촉진하여 기존 HPDC에 비해 기계적 특성 향상 및 기공 감소를 가져올 것입니다.
- 게이트 두께, 용융 온도, 2차 속도 및 가스 취입 시간은 GISS-HPDC의 기공 수준에 다양한 정도로 영향을 미치며, Taguchi 분석을 통해 상대적 중요성을 결정할 수 있습니다.
4. 연구 방법론:
- 연구 설계:
- Taguchi L9 직교 배열을 사용한 실험 계획법 (DOE) 접근 방식.
- GISS-HPDC 공정을 최적화하기 위해 각각 3단계의 4가지 매개변수를 조사했습니다.
- L9 직교 배열을 통해 4가지 매개변수를 단 9번의 실험 실행으로 연구할 수 있었으며, 이는 완전 요인 설계에 비해 실험 횟수를 크게 줄였습니다.
- 데이터 수집 방법:
- 실험 주조: L9 직교 배열에 따라 총 9회의 주조 실험을 수행했습니다. EN AC 48000 (AlSi12CuNiMg) 알루미늄 합금을 사용했습니다. 7700 kN 클램핑 힘을 가진 냉간 챔버 HPDC 기계를 사용하여 각 실험마다 15개의 시편을 생산했습니다. 주조 후 부품을 가공했습니다.
- 방사선 투과 검사 (비파괴): Bosello 산업용 X선 스캐너 (115 kV, 1.5 mA)를 사용하여 각 실험에서 5번째, 10번째 및 15번째 시편의 기공 수준을 평가했습니다. 기공은 4 (최고 - A 등급)에서 1 (최악 - D 등급)까지 등급이 매겨졌습니다.
- 미세 구조 특성 분석 (파괴): 각 실험에서 15번째 시편을 미세 구조 검사에 사용했습니다.
- 광학 현미경: Nikon Eclipse LV100ND 광학 현미경을 사용하여 금속 조직학적 준비 (연마, 연삭, Keller 시약으로 10초 동안 에칭) 후 미세 구조를 관찰했습니다.
- 주사 전자 현미경 (SEM) 및 에너지 분산 분광법 (EDS): FESEM, JSM 7000 F를 형태학적 분석 및 금속간 화합물상 식별에 활용했습니다.
- 분석 방법:
- 방사선 투과 검사 품질 점수: 각 실험에서 5번째, 10번째 및 15번째 시편의 방사선 투과 검사 등급에서 평균 품질 점수를 계산했습니다.
- 신호 대 잡음비 (S/N) 분석: "Larger is better" 품질 특성을 기반으로 S/N비를 계산했습니다. 방정식은 다음과 같습니다.
-10 log₁₀ (Σ(1/Yᵢ²)/n)
여기서 Yᵢ는 실험에서 각 시편의 품질 점수이고, n은 시편 수입니다 (이 경우 n=3, 실험당 3개의 시편을 등급 매김). Minitab 18 소프트웨어를 S/N비 분석에 사용했습니다.- S/N비의 주 효과 그림: 각 매개변수 수준이 S/N비에 미치는 영향을 시각화하고 최적 수준을 식별하기 위해 생성되었습니다.
- 확인 실험: Taguchi 분석에서 식별된 최적 매개변수 조합을 사용하여 결과를 검증하기 위한 확인 주조 실험을 수행했습니다.
- 연구 대상 및 범위:
- 재료: 상용 EN AC 48000 (AlSi12CuNiMg) 알루미늄 주조 합금. 화학 조성은 표 2에 제공됩니다: Si (12%), Fe (0.21%), Mn (1.2%), Cu (0.9%), Ni (0.81%), Mg (0.74%), Al (나머지).
- 부품 유형: 자동차 부품 (특정 형상은 그림 1에 표시, "생산된 부품, 주조 및 가공"으로 설명).
- 공정: 부분 응고 고압 다이캐스팅 (GISS-HPDC).
- 조사된 매개변수:
- A: 용융 온도 (°C): 수준: 1 (650±5), 2 (670±5), 3 (690±5)
- B: 가스 취입 시간 (s): 수준: 1 (0), 2 (5), 3 (10)
- C: 2차 속도 (m/s): 수준: 1 (4), 2 (4.5), 3 (5)
- D: 게이트 두께 (mm): 수준: 1 (1.8), 2 (2.4), 3 (3.5)
- 품질 특성: 기공 수준 (최소화).
5. 주요 연구 결과:
- 주요 연구 결과:
- 최적 매개변수 조합: S/N비 분석을 기반으로 최적 매개변수 조합은 A3B3C2D1로 결정되었으며, 이는 다음을 의미합니다.
- 용융 온도: 수준 3 (690 ± 5 °C)
- 가스 취입 시간: 수준 3 (10 s)
- 2차 속도: 수준 2 (4.5 m/s)
- 게이트 두께: 수준 1 (1.8 mm)
- 매개변수 중요도: 게이트 두께가 기공 감소에 가장 효과적인 매개변수로 확인되었으며, 그 다음으로 용융 온도, 2차 속도 및 가스 취입 시간 순으로 영향력이 감소했습니다 (그림 4에서 최소값과 최대값 S/N 값 사이의 간격을 기준으로).
- 기공 감소 및 "A" 등급 품질: 최적 매개변수 (A3B3C2D1)를 사용한 확인 실험 결과 "A" 등급 품질 부품이 생산되었으며, 5번째, 10번째 및 15번째 시편에 대한 방사선 투과 검사 점수는 각각 4, 4, 4였습니다. 이는 Taguchi 최적화를 검증하고 고품질 부품의 성공적인 생산을 입증했습니다.
- 미세 구조 변화: GISS 적용 시편은 기존 HPDC에 비해 더 미세하고 구상인 1차 α-Al 상 분포를 나타냈습니다. 비수지상 미세 구조가 달성되었습니다.
- 금속간 화합물상 식별: SEM-EDS 분석을 통해 α-Al 기지, Al-Cu-Ni 혼합물, Al₃FeSi, Al₁₅Si₂(FeMn)₃, Al₂Cu 및 Al₅(FeMn)Si₁.₅와 같은 금속간 화합물상을 식별했습니다.
- 최적 매개변수 조합: S/N비 분석을 기반으로 최적 매개변수 조합은 A3B3C2D1로 결정되었으며, 이는 다음을 의미합니다.
- 통계적/정성적 분석 결과:
- 표 4: 9개 실험 각각에 대한 5번째, 10번째 및 15번째 시편의 방사선 투과 검사 등급 (Y₁, Y₂, Y₃), 평균 품질 점수 (Ỹ) 및 계산된 S/N비를 제시합니다. 가장 높은 평균 품질 점수 (4.00) 및 S/N비 (12.04)를 가진 실험 9는 L9 실험 중 가장 좋은 결과를 나타냅니다.
- 그림 3: "A" 등급 (최고) 및 "D" 등급 (최악) 품질 부품의 방사선 투과 이미지를 보여주어 기공 수준의 차이를 시각적으로 보여줍니다. 그림 3a는 거의 기공이 없는 ("A" 등급) 반면, 그림 3b는 흰색 원형 점으로 기공을 보여줍니다 ("D" 등급).
- 그림 4: S/N비의 주 효과 그림은 각 매개변수 및 수준이 S/N비에 미치는 영향을 보여줍니다. 게이트 두께가 가장 영향력 있는 매개변수임을 시각적으로 확인시켜줍니다.
- 그림 5: 확인 실험 시편 (5번째, 10번째 및 15번째)에 대한 방사선 투과 검사 결과는 일관되게 높은 품질 (모두 방사선 투과 검사 점수 4)을 보여줍니다.
- 그림 6: 모든 9개 실험에서 15번째 시편의 광학 현미경 이미지를 보여주며, 다양한 매개변수 조합에 따른 미세 구조 변화를 보여줍니다. GISS 적용 시편에서 구상 미세 구조가 분명히 나타납니다.
- 그림 7: Taguchi 확인 실험 시편의 미세 구조는 부러진 수지상 결정과 구상 α-Al 입자를 보여줍니다.
- 그림 8: Taguchi 신뢰성 테스트 시편의 SEM 분석 BSE 이미지는 다양한 금속간 화합물상 (중국 문자 모양, 바늘 모양) 및 EDS 분석 영역을 보여줍니다.
- 표 5: 그림 8d의 다른 영역에 대한 EDS 분석 결과 (wt%)는 원소 조성 및 문헌 비교를 기반으로 가능한 금속간 화합물상을 식별합니다.
- 데이터 해석:
- S/N비 분석은 GISS-HPDC에서 기공을 최소화하기 위한 최적 매개변수 설정을 효과적으로 식별했습니다.
- 확인 실험은 Taguchi 방법이 공정 최적화에 효과적임을 검증했습니다.
- GISS 기술은 기계적 특성을 향상시키는 것으로 알려진 구상 미세 구조를 성공적으로 촉진했습니다.
- 게이트 두께는 이 특정 GISS-HPDC 응용 분야에서 기공 감소에 가장 중요한 매개변수로 나타났습니다.
- 가스 취입 시간은 중요하지만 과도한 취입 시간은 용융 특성에 부정적인 영향을 미치고 잠재적으로 결함을 유발할 수 있으므로 최적화해야 합니다. 선택된 10초 취입 시간은 부작용 없이 생산 사이클 시간을 안정화하는 데 이상적인 것으로 간주되었습니다.
- 그림 목록:
- 그림 1 생산된 부품, 주조 및 가공됨
- 그림 2 가스 취입 공정
- 그림 3 "A" 등급은 최고, "D" 등급은 최악 품질
- 그림 4 결과에 대한 주 효과 그림
- 그림 5 확인 실험을 위해 5번째, 10번째 및 15번째 시편에서 채취한 부품에 대한 방사선 투과 검사 결과
- 그림 6 15번째 시편에서 채취한 광학 현미경 이미지
- 그림 7 Taguchi 확인 실험 시편의 미세 구조
- 그림 8 Taguchi 신뢰성 테스트 시편의 SEM 분석 BSE 이미지; a 전체 보기, b 중국 문자 모양 금속간 화합물, c 바늘 모양 금속간 화합물, d 다른 유형의 금속간 화합물로 구성된 영역

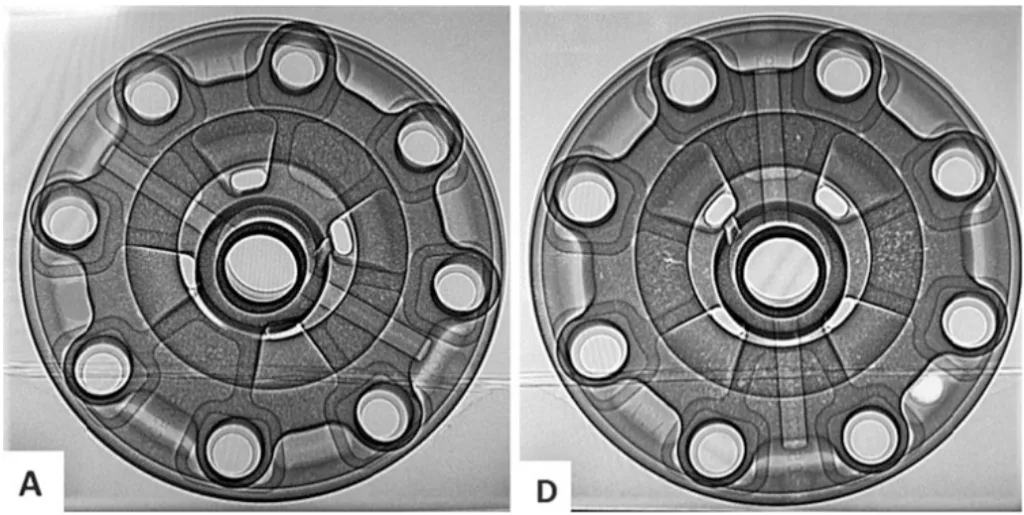
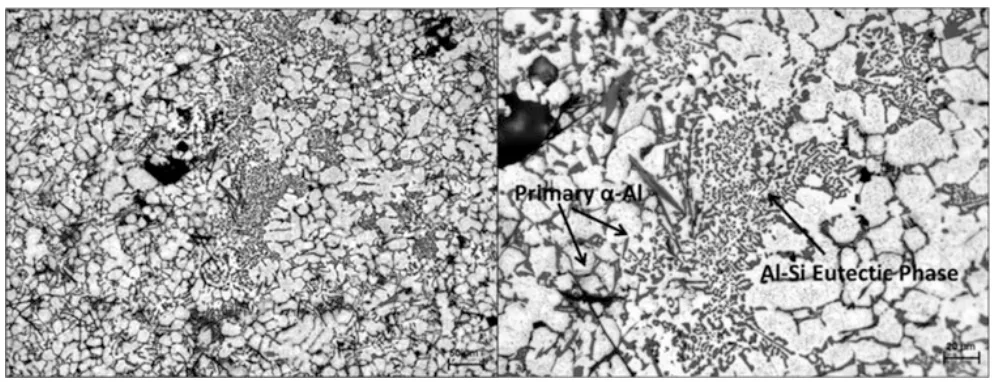
6. 결론 및 논의:
- 주요 결과 요약:
- Taguchi L9 직교 배열 방법은 알루미늄 자동차 부품 생산을 위한 GISS-HPDC 공정을 최적화하는 데 성공적으로 적용되었습니다.
- 최적 공정 매개변수 (A3B3C2D1: 용융 온도 690 ± 5 °C, 가스 취입 시간 10 s, 2차 속도 4.5 m/s, 게이트 두께 1.8 mm)는 기공을 최소화하고 "A" 등급 품질을 달성하기 위해 식별되었습니다.
- 게이트 두께가 기공에 가장 영향력 있는 매개변수로 밝혀졌습니다.
- GISS 기술은 비수지상, 구상 미세 구조를 가져왔습니다.
- 금속간 화합물상 (α-Al, Al-Cu-Ni, Al₃FeSi, Al₁₅Si₂(FeMn)₃, Al₂Cu, Al₅(FeMn)Si₁.₅)이 식별되었습니다.
- 확인 실험은 최적화 결과를 검증했습니다.
- 연구의 학문적 의의:
- 본 연구는 GISS-HPDC와 같은 새로운 제조 공정을 최적화하기 위한 Taguchi 방법의 효과적인 적용을 보여줍니다.
- 부분 응고 알루미늄 합금 다이캐스팅에서 기공 및 미세 구조에 대한 주요 공정 매개변수의 영향에 대한 귀중한 통찰력을 제공합니다.
- 본 연구는 GISS 기술과 HPDC 부품 품질 향상 가능성에 대한 이해에 기여합니다.
- 실용적 의미:
- 최적화된 GISS-HPDC 공정은 산업 현장에서 직접 구현하여 기공이 감소하고 성능이 향상된 고품질 알루미늄 자동차 부품을 생산할 수 있습니다.
- 식별된 최적 매개변수 설정은 EN AC 48000 합금 및 유사한 부품 형상을 사용하여 GISS-HPDC를 사용하는 제조업체에 귀중한 지침을 제공합니다.
- 본 연구는 GISS-HPDC에서 기공을 제어하는 데 있어 게이트 두께의 중요성을 강조하여 다이 설계에 대한 실질적인 지침을 제공합니다.
- 연구의 한계:
- 최적화는 특정 알루미늄 합금 (EN AC 48000) 및 특정 자동차 부품 형상에 대해 수행되었습니다. 최적 매개변수는 다른 합금 또는 부품 설계에 대해 재평가해야 할 수 있습니다.
- 본 연구는 기공을 주요 품질 특성으로 중점을 두었습니다. 기계적 특성 및 표면 조도와 같은 부품 품질의 다른 측면은 추가로 조사할 수 있습니다.
- 조사된 매개변수 및 수준의 범위는 표 3에 정의된 범위로 제한되었습니다. 더 넓은 범위 또는 더 미세한 수준을 탐색하면 추가 최적화 가능성이 밝혀질 수 있습니다.
7. 향후 후속 연구:
- 후속 연구 방향:
- 최적화된 GISS-HPDC 매개변수가 생산된 부품의 기계적 특성 (인장 강도, 항복 강도, 연신율, 경도, 피로 저항)에 미치는 영향을 조사합니다.
- 최적화된 GISS-HPDC 공정을 다른 알루미늄 합금 및 다른 부품 형상에 적용 가능성을 탐색합니다.
- 금형 온도, 사출 압력 프로파일 및 냉각 속도와 같은 추가 요소를 고려하여 GISS 공정 매개변수를 추가로 최적화합니다.
- GISS 공정 및 부품 품질에 대한 다양한 불활성 가스 (예: 아르곤, 질소) 및 가스 주입 방법의 영향을 조사합니다.
- GISS-HPDC에서 금속간 화합물상의 형성 메커니즘과 기계적 특성에 미치는 영향에 대한 상세한 분석을 수행합니다.
- 고급 시뮬레이션 도구를 사용하여 GISS-HPDC 공정을 더욱 최적화하고 부품 품질을 예측하는 방법을 탐색합니다.
- 추가 탐구가 필요한 영역:
- 실제 자동차 응용 분야에서 최적화된 GISS-HPDC로 생산된 부품의 장기 성능 및 신뢰성.
- 대량 생산을 위한 GISS-HPDC 공정의 비용 효율성 및 확장성.
- 기존 HPDC와 비교한 GISS-HPDC 공정의 환경 영향 평가.
8. 참고 문헌:
- http://www.aluminum.org/product-markets (August, 2017)
- Bonollo F, Gramegna N, Timelli G (2015) High-pressure die-casting: Contradictions and challenges. JOM, 67(5), 901–908.
- Atkinson H (2010) Semisolid processing of metallic materials. Materials Science and Technology, 26(12): 1401-1413.
- Czerwinski F (2006) The basics of modern semi-solid metal processing. JOM, 58(6): 17.
- Nafisi S, Gomashchi R (2016) Semi-solid processing of aluminum alloys, Springer, Switzerland, 9.
- Rice CS, Mendez PF (2001) Slurry-Based Semi-Solid DIE CASTING. Advanced materials & processes, 159(10): 49-52.
- Wannasin J et al. (2008) Development of the Gas Induced Semi-Solid metal process for aluminum die casting applications. In Solid State Phenomena, 141: 97-102.
- Flemings MC, Yurko JA, Martinez RA (2004) Solidification processes and microstructures. Proceedings of the TMS Annual Meeting, 3-14.
- Wannasin J, Janudom S, Rattanochaikul T, Canyook R, Burapa R, Chucheep T, Thanabumrungkul S (2010) Research and development of gas induced semi-solid process for industrial applications. Transactions of Nonferrous Metals Society of China 20: 1010-1015.
- Curle UA (2010) Semi-solid near-net shape rheocasting of heat treatable wrought aluminum alloys. Transactions of Nonferrous Metals Society of China (20)9: 1719-1724.
- Mahathaninwong N, Plookphol T, Wannasin J, Wisutmethangoon S (2012) T6 heat treatment of rheocasting 7075 Al alloy. Materials Science and Engineering: A, 532: 91-99.
- Verran GO, Mendes RPK, Dalla Valentina LVO (2008) DOE applied to optimization of aluminum alloy die castings. Journal of materials processing technology, 200.1: 120-125.
- Syrcos GP (2003) Die casting process optimization using Taguchi methods. Journal of materials processing technology, 135.1: 68-74.
- Thanabumrungkul S, et al. (2010) Industrial development of gas induced semi-solid process. Transactions of Nonferrous Metals Society of China 20: 1016-1021.
- Jumpol W, Wannasin J, Janudom S, Canyook R, Plookphol T, Wisutmethangoon S (2015) Effects of Solid Fractions in a Slurry Die Casting Process on Defects of 7075 Aluminum Alloy. In Applied Mechanics and Materials, 752: 7–10.
- Wannasin J, Martinez RA, Flemings MC (2006) Grain refinement of an aluminum alloy by introducing gas bubbles during solidification. Scripta Materialia, 55.2: 115-118.
- Canyook R, et al. (2012) Characterization of the microstructure evolution of semi-solid metal slurry during the early stages. Acta Materialia, 60.8: 3501-3510.
- Shabestari SG, Honarmand M, Saghafian H. (2015) Microstructural evolution of A380 aluminum alloy produced by gas-induced semi-solid technique (GISS). Advances in Materials and Processing Technologies, 1(1-2), 155-163.
- Janudom S, Rattanochaikul T, Burapa R, et al. (2010) Feasibility of semi-solid die casting of ADC12 aluminum alloy. Transactions of Nonferrous Metals Society of China 20(9);1756–1762.
- Krendelsberger N, Weitzer F, Schuster JC. (2007) On the Reaction Scheme and Liquidus Surface in the Ternary System Al-Fe-Si. Metallic Materials Transactions, 38A: 1681-1691.
- Bosselet F et al. (2004) Affinement expérimental de l'isotherme Al-Fe-Si à 1000 K. Journal de Physique IV (Proceedings), 122: 41-46.
- Dinnis CM, Taylor JA, Dahle AK (2005) As-cast morphology of iron-intermetallics in Al-Si foundry alloys. Scripta Materialia, 53 (8): 955-958.
- Irizalp SG, Saklakoglu N, (2014) Effect of Fe-rich intermetallics on the microstructure and mechanical properties of thixoformed A380 aluminum alloy. Engineering Science and Technology, an International Journal, 17(2): 58-62.
- Mohamed AMA, Samuel AM, Samuel FH, Doty HW (2009) Influence of additives on the microstructure and tensile properties of near-eutectic Al-10.8% Si cast alloy. Materials & Design, 30 (10): 3943-3957.
9. 저작권:
- 본 자료는 예크타 베르크 수슬루 (Yekta Berk Suslu), 메흐메트 시락 아카르 (Mehmet Sirac Acar), 미트하트 세놀 (Mithat Senol), 무아메르 무틀루 (Muammer Mutlu), 오즈굴 켈레스 (Ozgul Keles)의 논문: Taguchi 방법을 이용한 새로운 부분 응고 고압 알루미늄 다이캐스팅 최적화 (Optimization in Novel Partial-Solid High Pressure Aluminum Die Casting by Taguchi Method)를 기반으로 합니다.
- 논문 출처: https://doi.org/10.1007/978-3-319-72284-9_40
본 자료는 상기 논문을 기반으로 요약되었으며, 상업적 목적으로 무단 사용하는 것을 금지합니다.
Copyright © 2025 CASTMAN. All rights reserved.