77,000회 이상의 사이클: 일체형 온도조절 기술이 샷슬리브의 수명을 극적으로 연장하는 방법
이 기술 브리핑은 F. Miglierina와 B. Vianello가 작성하여 6th International Tooling Conference에서 발표한 학술 논문 "SHOT SLEEVE WITH INTEGRAL THERMAL REGULATION"을 기반으로 합니다. HPDC 전문가를 위해 CASTMAN의 전문가들이 요약 및 분석하였습니다.
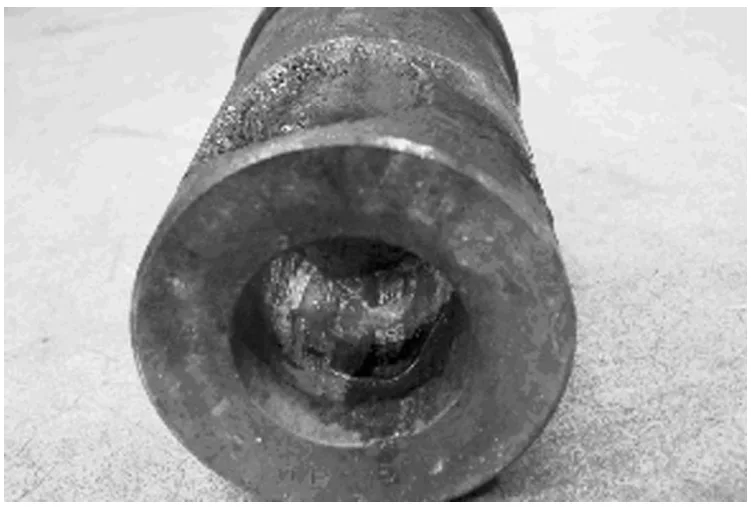
Keywords
- Primary Keyword: 샷슬리브 열관리
- Secondary Keywords: 다이캐스팅, 고압 다이캐스팅, 열 피로, Nipre® Duplex 처리, 일체형 온도조절, 주조 품질, 금형 수명
Executive Summary
- 과제: 기존의 샷슬리브는 극심한 열 충격과 불균일한 온도 분포로 인해 열 피로, 변형, 균열이 발생하여 조기에 파손됩니다. 이는 잦은 교체 비용과 생산성 저하의 주요 원인입니다.
- 방법: 이 연구에서는 전체 길이에 걸쳐 오일 온도조절 회로가 내장된 '일체형 온도조절 샷슬리브'를 설계 및 제작했습니다. 특수강(UNI 30CrMoV1227KU)을 사용하고, 염욕 열처리 및 Nipre® Duplex 표면 처리를 적용하여 내구성을 극대화했습니다.
- 핵심 성과: 2,000톤 다이캐스팅 머신에서 21kg의 알루미늄을 주조하는 실제 생산 환경에서 테스트한 결과, 온도조절 샷슬리브는 77,530회의 사출 사이클을 달성했습니다. 이는 일반 샷슬리브가 약 5,000회 만에 수명이 다하는 것과 비교해 비약적인 발전입니다.
- 결론: 샷슬리브의 온도를 균일하고 안정적으로 제어하는 것이 슬리브의 수명을 연장하고, 주조 품질을 일관되게 유지하며, 운영 비용을 절감하는 가장 효과적인 방법임이 입증되었습니다.
The Challenge: Why This Research Matters for HPDC Professionals
고압 다이캐스팅(HPDC) 공정에서 샷슬리브는 용융 금속이 주입되는 첫 관문으로, 가장 가혹한 환경에 노출되는 부품 중 하나입니다. 용융 알루미늄이 주입될 때마다 샷슬리브 내벽은 극심한 열 충격(thermal shock)을 받게 됩니다. 이러한 급격하고 반복적인 온도 변화는 다음과 같은 고질적인 문제들을 야기합니다(Ref. [1], [2]).
- 열 피로 및 균열: 표면에 미세 균열이 발생하고, 이 균열이 점차 내부로 전파되어 결국 파손으로 이어집니다.
- 기계적 마모 및 침식: 플런저와의 마찰, 용탕 내 실리카 입자에 의한 마모, 그리고 용융 알루미늄 자체에 의한 침식으로 슬리브 내경이 손상됩니다.
- 변형 (Ovalization & Bending): 샷슬리브의 상부와 하부 간의 극심한 온도 차이로 인해 슬리브가 타원형으로 변형되거나 활처럼 휘는 현상이 발생합니다. 이는 플런저의 비정상적인 마모와 소착(seizure)을 유발하여 주조 품질을 저하시킵니다.
이러한 문제들은 샷슬리브의 수명을 단축시켜 잦은 교체를 필요하게 만들고, 이는 곧 생산 중단 시간 증가와 운영 비용 상승으로 직결됩니다. 따라서 샷슬리브의 수명을 연장하고 성능을 안정적으로 유지하는 것은 모든 다이캐스팅 현장의 중요한 과제입니다.
The Approach: Unpacking the Methodology
이 연구는 샷슬리브의 수명을 극대화하기 위해 재료, 열처리, 표면 처리, 그리고 엔지니어링 설계라는 네 가지 핵심 요소에 대한 통합적인 접근법을 제시했습니다.
- 강재 선택 (Steel Choice): 내열성, 인성, 내마모성이 뛰어난 고온 공구강 UNI 30CrMoV1227KU (AISI H10 계열)를 선택했습니다. 이 강재는 고온에서의 기계적 특성 저하가 적고 열 충격에 대한 저항성이 우수합니다(Ref. [8]).
- 열처리 (Hardening and Tempering): 일반적인 가스 담금질 대신 염욕(salt bath) 열처리를 적용했습니다. 염욕 열처리는 균일하고 빠른 냉각 속도를 보장하여 변형을 최소화하면서도, 베이나이트(bainite)와 마텐자이트(martensite)가 혼합된 강인한 미세조직을 얻을 수 있게 합니다(Ref. [9], [10]).
- 표면 처리 (Superficial Treatment): 이온 질화(ionic nitriding)와 자철광(magnetite) 코팅을 결합한 Nipre® Duplex 특허 공법을 적용했습니다. 이 처리는 표면에 약 1050Hv의 높은 경도와 내마모성, 내소착성을 부여하고, 용융 알루미늄과의 화학 반응을 억제하는 강력한 보호층을 형성합니다(page 11, 13).
- 엔지니어링 설계 (Engineering Modification): 가장 핵심적인 혁신으로, 샷슬리브 전체 길이와 원주에 걸쳐 오일 순환 채널을 가공한 일체형 온도조절 회로(integral thermal regulation circuit)를 적용했습니다. 이 설계는 슬리브 전체의 온도를 균일하게 유지하여 열 변형을 근본적으로 제거하는 것을 목표로 합니다(page 15).
The Breakthrough: Key Findings & Data
이론적 분석과 최적의 기술을 결합하여 제작된 일체형 온도조절 샷슬리브는 실제 생산 라인에서 놀라운 성능을 입증했습니다.
- 균일한 온도 분포 달성: Figure 22는 온도조절 슬리브와 일반 슬리브의 작동 중 온도 프로파일을 비교합니다. 온도조절 슬리브는 상부와 하부의 온도 차이가 현저히 적고 전체적으로 더 낮은 온도를 유지하는 반면, 일반 슬리브는 하부에 열이 집중되어 심각한 온도 불균형을 보입니다.
- 열 변형의 근본적 제거: 균일한 온도 관리 덕분에 슬리브의 휨(bending)과 타원화(ovalization) 현상이 사실상 제거되었습니다. 이로 인해 플런저가 원통형의 홀 내부에서 안정적으로 작동하여 수명이 연장되고 일관된 사출이 가능해졌습니다(page 17).
- 혁신적인 수명 연장: Figure 23은 마모 현상의 진행 과정을 보여줍니다. 일반 슬리브가 1,500회 사출 후 침식 현상이 나타나고 5,000회 만에 사용 불능 상태가 된 반면, 온도조절 슬리브는 9,500회에서 경미한 피팅이 처음 관찰되었고, 최종적으로 77,530회 사출 후에도 심각한 마모 없이 사용되었습니다. (교체 사유는 마모가 아닌 칼라의 날카로운 모서리로 인한 균열이었음) (page 23).
Practical Implications for Your HPDC Operations
이 연구 결과는 실제 다이캐스팅 공정에 다음과 같은 중요한 시사점을 제공합니다.
- 공정 엔지니어: 샷슬리브의 온도조절 시스템을 도입함으로써 금형 교체 주기를 획기적으로 늘리고 설비 가동 시간을 극대화할 수 있습니다. 이는 특히 대형 주물이나 대량 생산 라인에서 상당한 비용 절감 효과로 이어질 수 있습니다.
- 품질 관리: Figure 22에서 보듯이, 안정적인 슬리브 온도는 일관된 사출 조건을 보장합니다. 이는 용탕의 예비 응고(pre-solidification)를 방지하고, 최종 주조품의 기공 감소 및 기계적 특성 향상에 직접적으로 기여합니다.
- 금형 설계: 이 연구는 특히 대형 샷슬리브(본 연구에서는 직경 140mm, 길이 980mm)의 경우, 외부 재킷이나 부분 냉각과 같은 전통적인 방식(page 14)으로는 한계가 있으며, 슬리브 자체에 내장된 일체형 온도조절 회로가 필수적임을 증명합니다. 이는 향후 대형 부품 금형 설계의 표준이 될 수 있습니다.
Paper Details
SHOT SLEEVE WITH INTEGRAL THERMAL REGULATION
1. Overview:
- Title: SHOT SLEEVE WITH INTEGRAL THERMAL REGULATION
- Author: F. Miglierina, B. Vianello
- Year of publication: The paper is from the 6th International Tooling Conference. The exact year is not specified, but references go up to 2000, suggesting publication around or after 2000.
- Journal/academic society of publication: 6TH INTERNATIONAL TOOLING CONFERENCE
- Keywords: Die-casting technique, injection group, shot sleeve, aluminum;
2. Abstract:
The modern die-casting technique is mainly focused on processing more complex and bigger pieces maintaining a high quality level and very low costs. This aim can be achieved by producing, with the use of faster and faster die forming cycles, aluminum alloy die-cast pieces weighing more than 20 kilos and by improving the life of the press mechanical parts, such as the shot sleeves. The company Zanussi Metallurgica decided to equip a horizontal die-casting machine featured by a 2000-ton cold room and a 21-kilo aluminum dying capacity with a shot sleeve (length: 980 mm, hole diameter: 140 mm) supplied with an Omnia Press integral thermal regulation circuit made of warm processed steel, hardened in a salt bath and with a surface covered with Nipre® Duplex. Thanks to the user care and to the special design, the shot sleeve could reach 80,000 injections at the end of the working cycle. The aim of this report is to introduce those technical solutions which brought to this successful conditions and to suggest shot sleeves with a long life granting a constant casting quality.
3. Introduction:
현대 다이캐스팅 기술은 높은 품질 수준과 낮은 비용을 유지하면서 더 복잡하고 큰 부품을 가공하는 데 중점을 둔다. 이는 더 빠른 다이 포밍 사이클을 사용하여 20kg 이상의 알루미늄 합금 다이캐스트 부품을 생산하고, 샷슬리브와 같은 프레스 기계 부품의 수명을 개선함으로써 달성될 수 있다. 본 연구는 이러한 기술적 솔루션을 소개하여 긴 수명과 일정한 주조 품질을 보장하는 샷슬리브를 제안하는 것을 목표로 한다.
4. Summary of the study:
Background of the research topic:
샷슬리브는 사출 단계에서 열 충격과 기계적 마모에 지속적으로 노출된다. 용융 금속이 주입될 때마다 발생하는 급격한 온도 변화는 강재의 저항력을 약화시키고 표면에 균열을 생성한다. 또한 플런저의 마찰, 합금 내 실리카 입자, 알루미늄 자체에 의한 마모가 발생한다. 이러한 복합적인 요인으로 인해 샷슬리브는 용탕 주입구에 구멍이 생기거나, 열 피로 균열, "비스킷" 영역의 변형 등이 발생하여 조기에 수명을 다하게 된다. 특히 상하부의 온도 차이로 인한 휨(bending)과 타원화(ovalization)는 심각한 문제이다.
Status of previous research:
기존에는 샷슬리브의 온도 제어를 위해 외부 재킷이나 구리 플레이트를 사용하거나, 용탕 주입구 영역에만 국부적인 냉각 회로를 만드는 방법들이 사용되었다. 그러나 이러한 방법들은 슬리브 전체의 온도 불균형을 해소하지 못해 열 변형 문제를 근본적으로 해결하는 데 한계가 있었다.
Purpose of the study:
본 연구의 목적은 재료 선택, 열처리, 표면 처리, 그리고 엔지니어링 설계를 포함한 최신 기술들을 결합하여, 긴 수명과 일관된 주조 품질을 보장하는 '일체형 온도조절 샷슬리브'의 기술적 솔루션을 소개하고 그 효과를 입증하는 것이다.
Core study:
본 연구는 Zanussi Metallurgica사의 2,000톤 수평 다이캐스팅 머신에 장착된 샷슬리브(내경 140mm, 길이 980mm)를 대상으로 한 사례 연구를 중심으로 진행되었다. 이 샷슬리브는 Omnia Press에서 제작한 일체형 온도조절 회로를 특징으로 하며, 특수강(UNI 30CrMoV1227KU)으로 제작되어 염욕 열처리와 Nipre® Duplex 표면 처리를 거쳤다. 연구팀은 예열 단계와 실제 생산 단계에서 슬리브의 온도 분포를 측정하고, 장기간에 걸친 마모 현상의 진화 과정을 추적하여 그 성능을 평가했다.
5. Research Methodology
Research Design:
연구는 이론적 분석과 실제 사례 연구를 결합하여 진행되었다. 먼저, 표준 샷슬리브에서 발생하는 열 변형(휨, 타원화)을 이론적으로 계산하여 문제의 심각성을 정량화했다. 그 후, 이 문제를 해결하기 위해 (1) 강재 선택, (2) 열처리 방법, (3) 표면 처리, (4) 엔지니어링 설계(일체형 온도조절 회로)라는 네 가지 기술적 솔루션을 적용한 샷슬리브를 설계 및 제작했다. 마지막으로, 제작된 샷슬리브를 실제 생산 라인에 적용하여 장기간의 성능을 평가했다.
Data Collection and Analysis Methods:
- 온도 측정: 예열 및 생산 단계에서 샷슬리브 표면의 온도를 레이저 조준 기능이 있는 적외선 온도계와 K-타입 열전대가 장착된 접촉식 전자 온도계를 사용하여 측정했다.
- 마모 분석: 일정 사출 횟수(9,500회, 21,000회 등)마다 샷슬리브의 내면을 육안 및 사진으로 검사하여 피팅, 균열 등 마모 현상의 발생과 진화 과정을 기록했다.
- 미세조직 분석: 77,530회 사출 후, 용탕 주입구 영역에서 샘플을 채취하여 미세조직을 분석하고 질화층의 상태와 균열 등을 관찰했다.
Research Topics and Scope:
본 연구는 21kg의 대형 알루미늄(EN AC-46000 합금) 부품을 생산하는 2,000톤 콜드 챔버 다이캐스팅 공정에 사용되는 대구경(140mm) 샷슬리브에 초점을 맞췄다. 연구의 핵심은 일체형 온도조절 회로가 샷슬리브의 온도 분포, 열 변형, 그리고 최종 수명에 미치는 영향을 평가하는 것이다.
6. Key Results:
Key Results:
- 온도 균일성: 일체형 온도조절 시스템은 예열 및 생산 단계 모두에서 샷슬리브 전체에 걸쳐 매우 균일한 온도 분포를 유지했다. 생산 중 슬리브 상부와 하부의 평균 온도 차이는 일반 슬리브에 비해 현저히 낮았다 (Figure 22).
- 수명: 온도조절 샷슬리브는 77,530회의 사출 사이클을 달성했다. 이는 열조절 기능이 없는 슬리브가 1,500회 만에 마모가 시작되어 5,000회 만에 교체되는 것과 비교할 때 15배 이상의 수명 향상을 의미한다 (page 23).
- 마모 형태: 마모의 진행이 매우 점진적이었다. 9,500회에서 경미한 피팅이 시작되었고, 21,000회에서 열 피로 균열이 관찰되었으나, 심각한 손상으로 빠르게 발전하지 않았다 (Figure 23). 최종적으로 77,530회 사용 후 미세조직 분석 결과, 질화층은 0.4mm 두께로 존재했으나 자철광 층은 발견되지 않았다 (Figure 24).
- 변형 제어: 슬리브의 휨과 타원화 현상이 사실상 제거되어, 플런저가 원통형의 홀에서 안정적으로 작동할 수 있었다 (page 17).
Figure Name List:
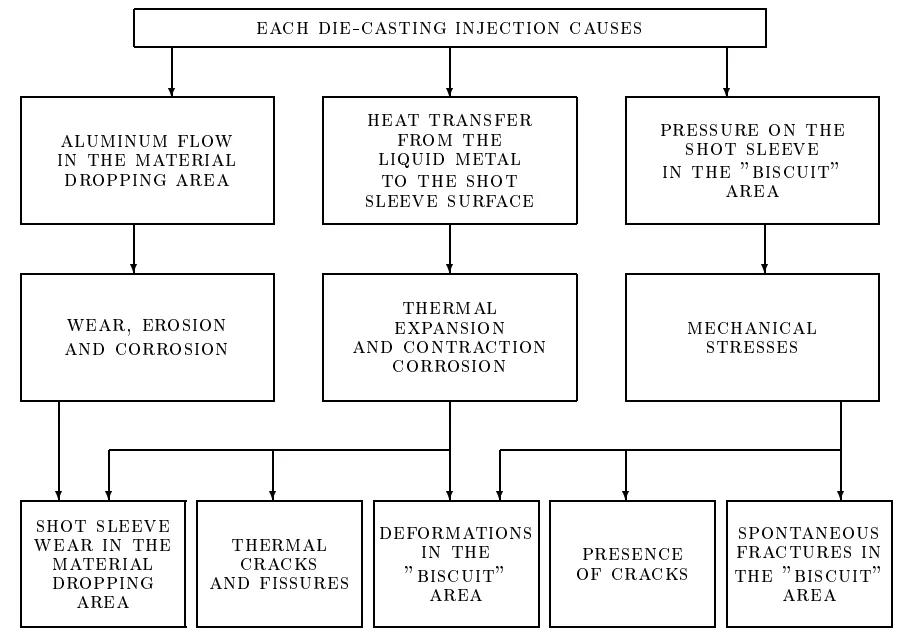
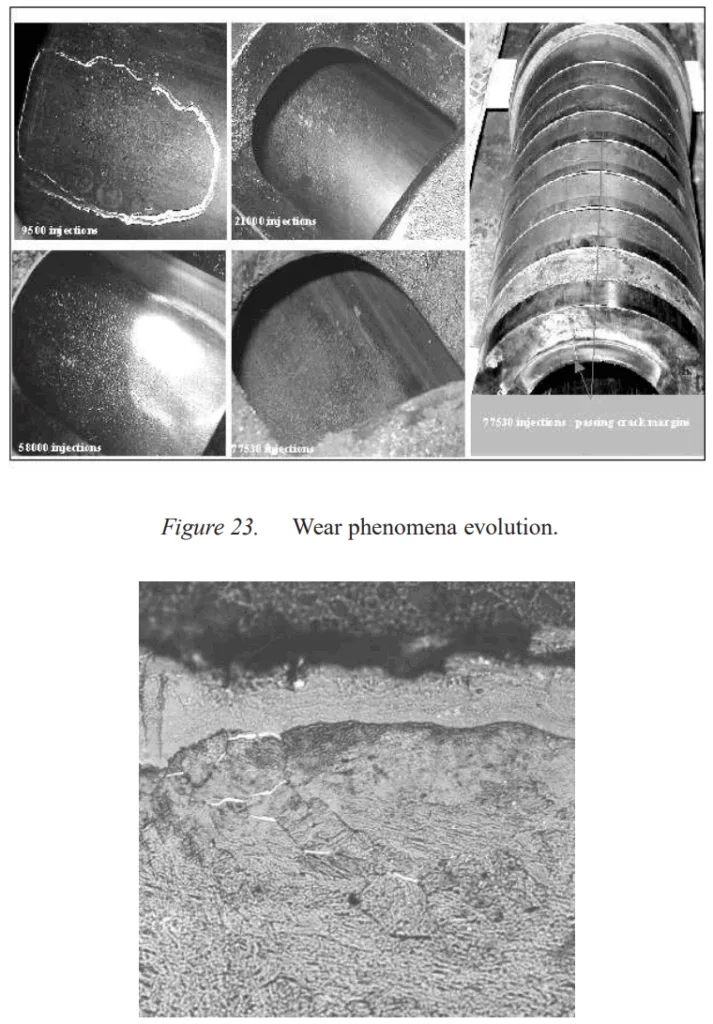
- Figure 1. Hole in the material dropping area.
- Figure 2. Theoretical ovalization in a shot sleeve with a 110-mm diameter hole.
- Figure 3. Bending Effect theoretical calculation.
- Figure 4. Micrographies of annealed steel (×100; ×500).
- Figure 5. Time-temperature-transformation continuous diagram.
- Figure 6. Warm resistance curve.
- Figure 7. Tempering diagram.
- Figure 8. Creep.
- Figure 9. Plant for hardening in salt bath – T.T.N. s.p.a. Nerviano-MI.
- Figure 10. Micrographies of hardened and tempered steel (100X; 500X).
- Figure 11. Micrography with NIPRE Duplex.
- Figure 12. Drawings of heat earth plates in copper alloy.
- Figure 13. Drawing of the cooling system with water in the material dropping area.
- Figure 14. Drawing of the oil thermal regulated circuit in the material dropping area and in the "biscuit" area.
- Figure 15. Photo showing the section of the thermal regulated circuit.
- Figure 16. Photo showing the material dropping area with thermal regulation holes.
- Figure 17. Web cracks.
- Figure 18. Passing crack.
- Figure 19. Hole in the material fall area.
- Figure 20. Pre-heating temperature trend.
- Figure 21. Thermal profile at the end of pre-heating.
- Figure 22. Thermal profile of the thermoregulated and no thermoregulated shot sleeves.
- Figure 23. Wear phenomena evolution.
- Figure 24. Micrograph of material fall area zona after 77530 injections.
7. Conclusion:
일체형 온도조절 샷슬리브의 사용은 다음과 같은 결론을 가능하게 했다:
- 샷슬리브의 잦은 교체로 인한 비용을 극적으로 줄일 수 있다.
- 일관된 사출 조건 유지로 주조 품질을 향상시킬 수 있다.
- 사출 플런저의 잦은 마모로 인한 비용을 줄일 수 있다.
- 대형 일체형 온도조절 샷슬리브에 대한 흥미로운 연구와 표준화를 이루었다.
8. References:
- [1] ANDREONI, Casè, Pomesano " Il processo della pressofusione" Edimet, I Edizione 1993.
- [2] M. SUNDQVIST and S. HOGMARK "The mechanism of erosive wear of die casting dies for aluminium" New materials process experience for tooling, Mat. Search 1992.
- [3] R. BREITLER, A. RIVOLTA "I processi di rifusione degli acciai per stampi per pressocolata" Böhler, 2000
- [4] C. CIBALDI, "I criteri di scelta e di trattamento degli acciai da costruzione e da utensili", Edito dall'autore, Ila Edizione 1990.
- [5] B. VIANELLO, "Studio sull'andamento delle temperature superficiali nei contenitori integrali", Comunicazione Interna Zanussi Metallurgica, 1999.
- [6] P. ROBBINS "A plunger system for future" Die Casting Technology-NADCA 1993.
- [7] P. ROBBINS, Glenn Mackie" Controlling Thermal expansion of plunger tips and shot sleeves in cold chamber die casting" Die Casing Innavation NADCA 1995.
- [8] "Acciai da utensili "Thyssen acciai speciali s.p.a."1992.
- [9] "Acciai per utensili" Cogne Acciai Speciali.
- [10] "Il trattamento termico degli acciai per utensili" Uddeholm S.p.a.
- [11] Piana "Acciai da lavorazione a caldo" Aubert&Duval
- [12] M. PIROVANO "NIPRE" TTN S.p.a. Nerviano
- [13] Brevik, Gruber, Sobol, Park, Udvardy "Optimization of shot sleeves performace" NADCA publication #203, 1998.
- [14] ROBBINS, SINGH "Bigger casting, Bigger problem" Die casting technology for the new century NADCA publication.
Conclusion & Next Steps
이 연구는 HPDC 공정에서 샷슬리브의 수명과 성능을 향상시키는 데 있어 열관리가 얼마나 중요한지를 명확한 데이터로 증명했습니다. 연구 결과는 품질을 개선하고, 결함을 줄이며, 생산을 최적화하기 위한 데이터 기반의 명확한 길을 제시합니다.
CASTMAN은 최신 산업 연구를 적용하여 고객의 가장 어려운 다이캐스팅 문제를 해결하는 데 전념하고 있습니다. 이 보고서에서 논의된 문제들이 귀사의 운영 목표와 관련이 있다면, CASTMAN의 엔지니어링 팀에 연락하여 이러한 고급 원칙을 귀사의 부품에 어떻게 구현할 수 있는지 논의해 보십시오.
Expert Q&A: Your Top Questions Answered
Q1: 이 연구에서 샷슬리브 수명 향상에 가장 중요한 요소는 무엇이었습니까?
A1: 연구의 결론에 따르면, 가장 중요한 요소는 슬리브 전체에 걸쳐 균일한 온도를 유지하는 '일체형 온도조절 회로'였습니다. 이는 Figure 22의 데이터로 뒷받침되며, 논문의 Conclusions
섹션에서 그 효과를 명확히 하고 있습니다.
Q2: 이 연구의 접근 방식은 기존의 문제 해결 방식과 어떻게 다릅니까?
A2: 논문의 ENGINEERING MODIFICATION
섹션(page 14)에 따르면, 외부 재킷이나 부분 냉각과 같은 기존 방식은 슬리브의 휨이나 타원화 같은 변형 문제를 해결하지 못했습니다. 반면, 이 연구에서 제시한 일체형 온도조절 방식(page 15)은 슬리브 전체의 온도를 제어하여 이러한 변형을 근본적으로 제거했습니다.
Q3: 이 연구 결과는 특정 합금에만 적용됩니까, 아니면 모든 종류의 합금에 적용 가능합니까?
A3: THERMOREGULATED SHOT SLEEVE, PRODUCT AND PRODUCTIVE PROCESS
섹션(page 19)에 명시된 바와 같이, 이 연구는 구체적으로 알루미늄 합금(EN AC-46000)을 사용하여 수행되었습니다. 다만, 논문은 마그네슘 다이캐스팅에도 적용 가능하다고 언급하고 있어(page 17), 다른 합금에 대한 적용 가능성도 시사합니다.
Q4: 연구원들은 이 결론에 도달하기 위해 어떤 특정 측정 기술을 사용했습니까?
A4: HEATING EQUIPMENT AND MEASUREMENT DEVICES
섹션(page 20)에 설명된 바와 같이, 연구원들은 레이저 조준 기능이 있는 적외선 온도계와 K-타입 열전대가 장착된 접촉식 전자 온도계를 사용하여 온도를 정밀하게 측정했습니다.
Q5: 논문에 따르면, 이 연구의 한계점이나 향후 연구 분야는 무엇입니까?
A5: 논문에서 명시적인 한계점을 언급하지는 않았습니다. 그러나 ACHIEVED RESULTS
섹션(page 23)에서 최종적인 사용 중단 원인이 마모가 아닌 '칼라의 날카로운 모서리로 인한 균열'이었다고 밝힌 점은 주목할 만합니다. 이는 열관리 외에도 기계적 설계의 세부 사항(모서리 처리 등)이 슬리브의 전체 수명에 중요하게 작용할 수 있음을 시사하며, 이 부분이 향후 연구 분야가 될 수 있습니다.
Q6: 이 논문이 다이캐스팅 현장에 주는 가장 직접적이고 실용적인 교훈은 무엇입니까?
A6: 논문 "[Paper Title]"에 근거한 핵심 교훈은, 특히 대형/대량 주조 공정에서 일체형 온도조절 시스템에 투자하는 것이 샷슬리브의 수명을 극대화하고, 주조 품질을 안정시키며, 장기적으로 총 운영 비용을 절감하는 가장 확실한 방법이라는 것입니다. 77,530회라는 압도적인 사이클 수명이 이를 강력하게 뒷받침합니다.
Copyright
- This material is an analysis of the paper "SHOT SLEEVE WITH INTEGRAL THERMAL REGULATION" by F. Miglierina and B. Vianello.
- Source of the paper: 6th International Tooling Conference proceedings.
- This material is for informational purposes only. Unauthorized commercial use is prohibited.
- Copyright © 2025 CASTMAN. All rights reserved.