본 소개서는 "[International Journal of Engineering Research & Technology (IJERT)]"에서 발행한 "[Optimization of Runner Design in Pressure Die Casting]" 논문을 기반으로 작성되었습니다.
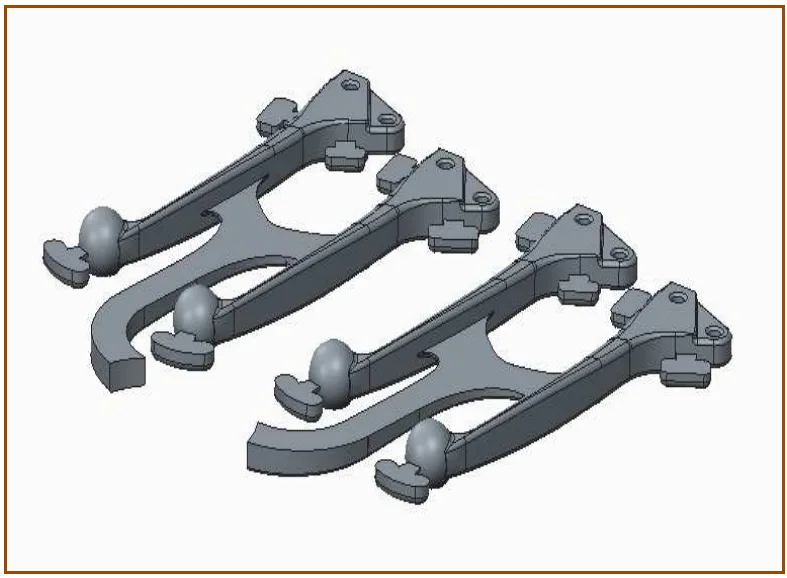
1. 개요:
- 제목: 압력 다이캐스팅에서 탕도 설계의 최적화 (Optimization of Runner Design in Pressure Die Casting)
- 저자: Nair Akhil K. Raveendran, Prof. Amol N. Patil
- 발행 연도: 2017년
- 발행 학술지/학회: International Journal of Engineering Research & Technology (IJERT)
- 키워드: 탕도(Runner), 게이트(Gate), 고압 다이캐스팅(High pressure die casting), 충전 시간(Fill time)
2. 초록:
고압 다이캐스팅을 통해 고품질 부품을 생산하기 위해 컴퓨터 지원 시뮬레이션이 금형 설계 최적화에 사용되어 왔습니다. 유한 차분법, 유한 체적법, 유한 요소법 등이 충전 과정 시뮬레이션에 사용되어 일반적인 문제에 대해 상당한 진전을 이루었습니다. 그러나 특정 문제를 해결하기 위한 금형 설계 최적화에 대한 추가 연구가 여전히 요구됩니다. 다이캐스팅에서는 금형이 동일하거나 다른 부품을 생산하는 여러 캐비티를 갖는 경우가 많습니다. 다중 캐비티는 주 탕도에 연결되는 분기 탕도의 적용을 필요로 합니다. 여러 캐비티가 동시에 충전을 시작하고 동일한 충전 시간을 갖도록 보장하는 것이 중요하기 때문에 탕도 시스템 설계는 항상 다이캐스팅의 주요 주제였습니다. 설계의 핵심 요소는 캐비티의 부피에 따라 각 분기 탕도의 단면적을 조정하는 것이지만, 이것만으로는 캐비티를 동시에 충전하기에 충분하지 않을 수 있습니다. 분기 탕도와 주 탕도 사이의 각도는 충전 압력, 충전 시간 및 잔류 응력에 영향을 미치는 것으로 관찰되었으나, 이러한 관찰은 실제 주조품보다는 매우 간단한 실험실 수준의 금형 설계에 국한되었습니다.
3. 서론:
다이캐스팅은 다이캐스팅 기계의 사출 시스템에서 발생하는 유압 에너지를 용탕에 적용하여 금형 캐비티를 빠르게 채우기 위한 운동 에너지를 전달하는 공정입니다. 본 논문은 콜드 챔버 고압 다이캐스팅의 탕도 문제를 다루며, 부정확하게 설계된 공급 시스템으로 인해 제품에 제트 마크(jet marks)가 발생하는 문제를 해결하고자 합니다. 용탕의 제팅(jetting)은 탕도 벽의 침식으로 이어지며, 장기간의 생산 과정에서 이 마모는 국부적인 함몰을 형성하여 유동 방향을 더욱 변화시킵니다. 이 문제를 해결하기 위해서는 탕도 벽의 마모를 최소화하기 위해 제팅이 거의 또는 전혀 없는 용탕 흐름을 생성하도록 탕도를 설계하는 솔루션이 필요합니다. 본 논문은 다이캐스팅 설계 공정의 중요한 도구인 P-Q² 다이어그램을 활용하여 공정 변수의 작동 범위를 결정합니다.
4. 연구 요약:
연구 주제의 배경:
고압 다이캐스팅에서 고품질 부품 생산은 최적의 금형 설계에 크게 의존합니다. 다중 캐비티를 가진 금형의 경우, 모든 캐비티가 동시에 균일하게 충전되도록 하는 탕도 시스템이 매우 중요합니다. 부적절하게 설계된 탕도는 결함, 생산 비용 증가, 금형 마모를 유발할 수 있습니다.
기존 연구 현황:
컴퓨터 지원 시뮬레이션은 금형 설계를 최적화하기 위해 널리 사용되어 왔습니다. 이전 연구에서는 분기 탕도와 주 탕도 사이의 각도와 같은 요소가 충전 압력과 시간에 영향을 미친다는 것을 보여주었습니다. 그러나 이러한 관찰은 종종 간단한 실험실 수준의 설계에 국한되었습니다. 본 연구는 전산유체역학(CFD) 방법을 실제 산업용 다중 캐비티 부품에 적용함으로써 기존 지식을 확장합니다. 또한 게이팅 시스템에 대한 Herman의 방법론 및 공정 변수 최적화를 위한 P-Q² 다이어그램 사용과 같은 기존 설계 방법론을 참조합니다(참고문헌).
연구의 목적:
본 연구의 주된 목적은 고압 다이캐스팅 금형의 탕도 설계를 최적화하여 제트 마크와 같은 제품 결함을 제거하는 것입니다. 이 연구는 탕도 측벽의 제팅을 최소화하고, 침식을 방지하며, 금형 캐비티의 완전한 충전을 보장하고, 궁극적으로 주조 부품의 불량률을 줄이는 탕도를 설계하는 것을 목표로 했습니다.
핵심 연구:
연구의 핵심은 결함 부품을 생산하던 기존 클러치 레버용 금형을 분석하기 위해 전산유체역학(CFD) 시뮬레이션을 사용하는 것이었습니다. 분석 결과, 불균일한 충전으로 인해 응고 결함과 제트 마크가 발생하는 충전 패턴의 문제가 확인되었습니다. 이 분석을 바탕으로 탕도 설계를 팬(fan) 타입에서 탠젠셜(tangential) 타입으로 수정했습니다. 이후 이 새로운 설계를 시뮬레이션하고 분석하여 원활한 충전, 기공 감소, 결함 제거 효과를 검증했습니다.
5. 연구 방법론
연구 설계:
본 연구는 비교 분석 방법론을 따랐습니다. 네 개의 캐비티를 가진 클러치 레버용 기존 금형 설계의 결함을 파악하기 위해 먼저 분석을 수행했습니다. 그 후 수정된 탕도 설계를 개발하고 시뮬레이션했습니다. 수정된 설계의 성능을 기존 설계와 비교하여 주요 주조 매개변수를 평가하고 개선 사항을 검증했습니다.
데이터 수집 및 분석 방법:
본 연구는 주로 전산유체역학(CFD) 시뮬레이션을 사용하여 주조 공정을 분석했습니다. 충전 시간, 응고, 인게이트(ingate) 속도, 금형 침식, 공기 혼입, 콜드셧(cold shut)과 같은 매개변수가 고려되었습니다. 분석은 팬 타입 및 탠젠셜 타입을 포함한 여러 탕도 설계안의 결과를 분석 소프트웨어를 사용하여 비교함으로써 가장 적합한 설계를 결정했습니다.
연구 주제 및 범위:
본 연구는 클러치 레버를 생산하는 네 개의 캐비티를 가진 고압 다이캐스팅(HPDC) 금형의 탕도 시스템 최적화에 중점을 둡니다. 연구 범위는 캐비티의 원활한 충전을 달성하고, 제품 결함을 줄이며, 전반적인 주조 품질을 향상시키기 위한 탕도 궤적 및 방향 변화 분석을 포함합니다.
6. 주요 결과:
주요 결과:
CFD 분석 결과, 탕도를 팬 타입에서 탠젠셜 타입으로 변경함으로써 용탕 흐름이 금형과 제품에 미치는 부정적인 영향을 성공적으로 줄일 수 있었습니다. 이 변화는 주조품의 제트 마크를 현저히 감소시켰습니다. 결과적으로 용탕이 조기 응고 없이 금형을 완전히 채우면서 불량률이 감소했습니다. 분석은 또한 새로운 설계에서 이전 설계안에 비해 기공이 감소했음을 확인했습니다. 제트 마크가 제거됨에 따라 연마와 같은 후처리 공정의 필요성도 사라졌습니다.
그림 이름 목록:
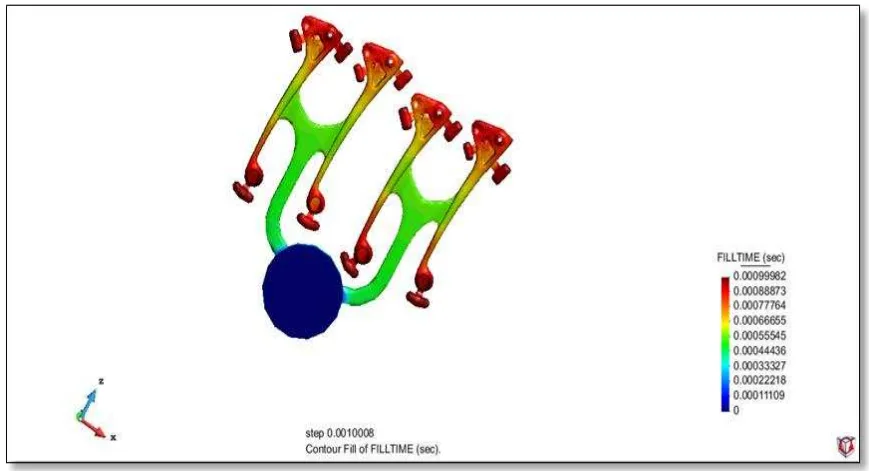
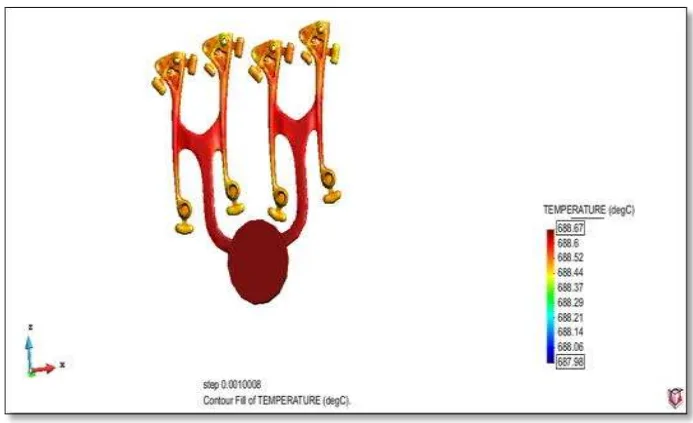
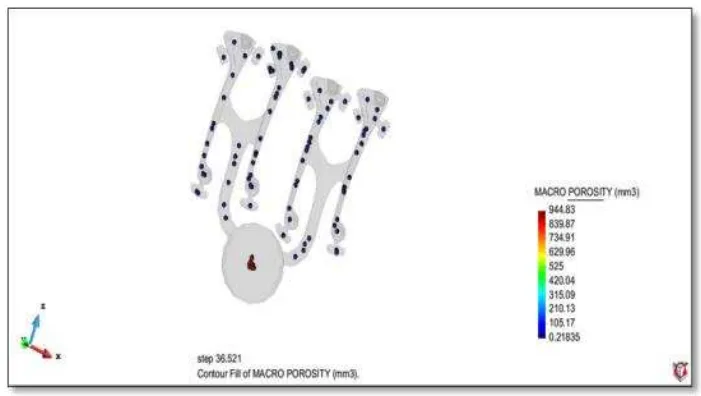
- Fig. 1. Runner System of the Modified Design
- Fig. 2. Filling Time of the Modified Design
- Fig. 3. Temperature of molten metal in Modified Design
- Fig. 4. Porosity in runner system of Modified Design
7. 결론:
CFD 분석을 통해 탕도를 팬 타입에서 탠젠셜 타입으로 변경함으로써 유동이 금형과 제품에 미치는 영향을 줄일 수 있음을 발견했습니다. 금형과 제품에 제트 마크가 발생할 가능성이 줄어들었습니다. 용탕이 이제 금형을 완전히 채우면서 불량률이 감소했습니다. 또한, 첫 번째 설계안과 비교하여 기공이 감소했습니다. 제트 마크가 줄어들면서 연마와 같은 제품 후처리가 필요하지 않게 되었습니다.
8. 참고문헌:
- B. Vijaya Ramnath et al. (2014), Analysis and Optimization of Gating System for Commutator End Bracket, Procedia Materials Science 6 (2014) 1312–1328
- Marco Antonio Pego Guerr, Die Casting Design – A Parametric Approach, Thesis submitted to Ottawa-Carleton Institute for Mechanical and Aerospace Engineering (1997)
- P.R.Vispute, D.S.Chaudhari, Swapnil Kulkarni, Utilizing Flow Simulation In The Design Phase Of A Die Casting Die To Optimize Design Parameters While Validating Through Experimentation During Trials, International Journal of Scientific Research and Management Studies (IJSRMS) ISSN: 23493771 Volume 1 Issue 8, pg: 263-269
- Shaik Riyaz Ahmed, K.Devaki Devi and S.V.S. Himathejeswini, Design & Analysis of Heat Sink High-Pressure Die Casting Component, International Journal of Current Engineering and Technology, Vol.6, No.5 (Oct 2016)
- Tuula Höök, Tampere University of Technology, HPDC runner and gating system design, CAE Mould Design.
9. 저작권:
- 이 자료는 "Nair Akhil K. Raveendran, Prof. Amol N. Patil"의 논문입니다. "[Optimization of Runner Design in Pressure Die Casting]" 논문을 기반으로 합니다.
- 논문 출처: http://www.ijert.org
이 자료는 위 논문을 바탕으로 요약되었으며, 상업적 목적의 무단 사용을 금합니다.
Copyright © 2025 CASTMAN. All rights reserved.
논문 요약:
연구에 대한 주요 질문과 답변:
본 연구는 탕도 시스템을 최적화하여 고압 다이캐스팅에서 발생하는 제트 마크와 높은 불량률과 같은 결함을 해결하는 것을 목표로 했습니다. CFD 분석을 통해, 클러치 레버 부품의 탕도 설계를 팬 타입에서 탠젠셜 타입으로 변경하면 용탕 흐름이 개선됨을 입증했습니다. 새로운 설계는 완전하고 균일한 금형 충전을 보장함으로써 제트 마크를 성공적으로 제거하고, 기공을 줄이며, 부품 불량률을 감소시켰습니다.
Q1. 논문에서 논의된 기존 다이캐스팅 공정의 주요 문제는 무엇이었습니까?
A1. 주요 문제는 콜드 챔버 고압 다이캐스팅 금형의 부정확하게 설계된 공급 시스템으로, 이로 인해 제팅 현상, 탕도 벽의 침식, 불완전한 금형 충전, 최종 제품의 제트 마크가 발생하여 높은 불량률을 초래했습니다. (출처: "Optimization of Runner Design in Pressure Die Casting", 서론 및 설계 및 분석 섹션).
Q2. 이 문제를 해결하기 위해 어떤 구체적인 설계 변경이 이루어졌습니까?
A2. 용탕 흐름이 금형과 제품에 미치는 난류 효과를 줄이기 위해 탕도 설계를 팬(fan) 탕도에서 탠젠셜(tangential) 탕도로 변경했습니다. (출처: "Optimization of Runner Design in Pressure Die Casting", 결론).
Q3. 새로운 설계를 평가하기 위해 어떤 방법론이 사용되었습니까?
A3. 전산유체역학(CFD) 시뮬레이션을 사용하여 기존 및 수정된 탕도 설계의 성능을 비교 분석했으며, 충전 시간, 기공률, 온도 분포와 같은 매개변수에 중점을 두었습니다. (출처: "Optimization of Runner Design in Pressure Die Casting", 설계 및 분석 섹션).
Q4. 새로운 탕도 설계가 충전 시간에 영향을 미쳤습니까?
A4. 네, 수정된 탠젠셜 탕도의 충전 시간은 0.00099982초로, 이전 팬 게이트 탕도에 비해 약간 증가했지만 급격한 변화는 아니었으며 공정에 부정적인 영향을 미치지 않았습니다. (출처: "Optimization of Runner Design in Pressure Die Casting", 그림 2 및 관련 텍스트).
Q5. 수정된 설계는 결함 측면에서 제품 품질에 어떤 영향을 미쳤습니까?
A5. 수정된 설계는 기공률 감소, 제품의 가시적인 제트 마크 제거, 용탕의 완전하고 균일한 금형 충전을 보장하여 부품 불량률을 크게 감소시켰습니다. (출처: "Optimization of Runner Design in Pressure Die Casting", 결론 및 3페이지 텍스트).
Q6. 최적화된 설계로 만든 제품에 후처리가 필요했습니까?
A6. 아니요, 개선된 탕도 설계 덕분에 제트 마크가 제거되어 연마와 같은 후처리 공정이 더 이상 필요하지 않았습니다. (출처: "Optimization of Runner Design in Pressure Die Casting", 결론).