연구의 핵심 목적: 고성능 열 방출이 요구되는 전자 시스템의 열 관리 문제 해결을 위해 고밀도 다이캐스팅(HDDC) 공정을 개발하고, 기존 다이캐스팅 및 압출 공정의 한계를 극복하여 열 싱크 제조의 새로운 가능성을 제시하는 것.
주요 방법론: 고열전도성 알루미늄 합금을 사용한 HDDC 공정을 개발하고, 다양한 형상의 핀 구조를 갖는 열 싱크 제작. 유한요소해석 및 실험을 통해 HDDC 공정의 성능 평가.
핵심 결과: HDDC 공정은 기존 다이캐스팅 대비 열 전달 효율을 크게 향상시키고, 3차원 형상 설계의 유연성을 제공. 다양한 금속 재료의 결합을 통해 열 전도율을 향상시키고, 기공이 없는 고강도 제품 생산 가능.
연구진 정보
- 소속 기관: Aavid Thermalloy S.r.l.
- 저자명: Andrea Sce, Lorenzo Caporale
- 주요 연구 분야: 열 관리, 다이캐스팅 공정
연구 배경 및 목적
- 해당 연구가 필요한 산업적 배경: 전자 시스템의 고성능화 및 소형화 추세로 인해 열 관리의 중요성 증대. 대량 생산에 적합한 효율적인 열 싱크 제조 기술의 필요성.
- 구체적인 기술적 문제점 과제: 기존 압출 공정은 2차원 설계에 국한되고, 6xxx 계열 알루미늄 합금만 사용 가능하며 핀 밀도와 형상에 제약이 있음. 기존 다이캐스팅 공정은 열전도율이 낮은 알루미늄 합금 사용으로 열 방출 성능 저하 및 기공 발생 문제 존재. 다양한 금속 재료의 결합이 어려움.
- 연구 목표: 기존 공정의 한계를 극복하는 새로운 고밀도 다이캐스팅(HDDC) 공정 개발. 고열전도성 알루미늄 합금을 활용하여 열 방출 성능 향상. 3차원 형상 설계의 자유도 확보. 다양한 금속 재료의 결합을 통한 열 관리 성능 향상.
논문의 주요 목표와 연구내용
- 논문의 주요 목표와 연구내용: 고밀도 다이캐스팅(HDDC) 공정을 이용한 고성능 열 싱크 제작 기술 개발. 기존 압출 및 다이캐스팅 공정과의 성능 비교 분석.
- 문제점: 기존 압출 및 다이캐스팅 공정의 열 전달 성능 저하, 설계 자유도 부족, 다양한 소재 사용의 어려움 등의 문제점 해결.
- 문제 해결을 위한 단계적 접근:
- 고열전도성 알루미늄 합금(Al 6063 또는 Al 11070)을 사용한 HDDC 공정 개발.
- 고압 주입을 통해 기공 없는 고강도 열 싱크 제작.
- 3차원 형상 설계를 통해 다양한 핀 구조(평평한 핀, 경사진 핀, 타원형 핀, 원형 핀, 방사형 플레이트) 구현.
- 유한요소해석(CFD) 및 실험을 통해 HDDC 공정의 열 전달 성능을 기존 다이캐스팅 공정과 비교 평가.
- 다양한 금속 재료(알루미늄, 구리)의 결합을 통한 열 전달 성능 향상 및 새로운 제품 개발.
- 내구성 향상을 위한 표면 처리 공정 적용.
- 주요 Figure:
- Figure 1. Extrusion limits: 압출 공정의 형상 및 소재 제약을 보여주는 그림.
- Figure 2. Die-casting limits: 다이캐스팅 공정의 형상, 소재, 기공 등의 제약을 보여주는 그림.
- Figure 3. Steps in the HDDC process: HDDC 공정의 단계별 과정을 보여주는 그림.
- Figure 4. CFD comparison between traditional DC (left) and HDDC (right); HDDC allow more fins: CFD 시뮬레이션 결과를 통해 HDDC 공정의 열 저항 감소 효과를 보여주는 그림. HDDC는 기존 다이캐스팅보다 더 많은 핀을 허용하여 열 저항(Rth)을 0.281 °C/W에서 0.169 °C/W로 감소.
- Figure 5. Metallographic analysis of HDDC structure vs die-casting structure: HDDC 공정과 기존 다이캐스팅 공정의 미세구조 비교. HDDC 공정은 기공이 없음.
- Figure 6. Mechanical Properties for Al 6xxx-T4 Series: test results comparison between HDDC and extruded material: HDDC 공정으로 제작된 열 싱크의 기계적 특성(항복강도, 인장강도)을 기존 압출 제품과 비교한 그래프.
- Figure 7. Capabilities development path: HDDC 공정의 개발 단계를 보여주는 그림.
- Figure 8. Examples of HDDC products: HDDC 공정으로 제작 가능한 다양한 제품의 예시.
- Figure 9. Examples of HDDC products with Al and Cu (cut section – 60x17x40 mm): 알루미늄과 구리를 결합한 HDDC 제품의 단면 사진.
- Figure 10. Microscopic and ultrasonic scan on HDDC made with Al and Cu: 알루미늄과 구리를 결합한 HDDC 제품의 미세구조 및 초음파 검사 결과.
- Figure 11. A big part made by HDDC with Al and Cu: 알루미늄과 구리를 결합한 대형 HDDC 제품.
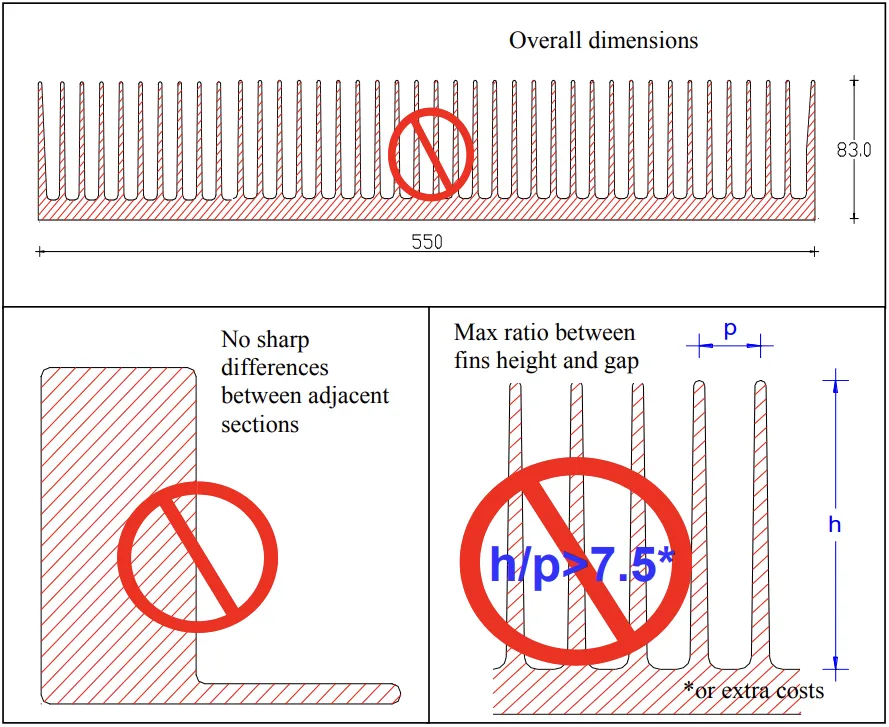
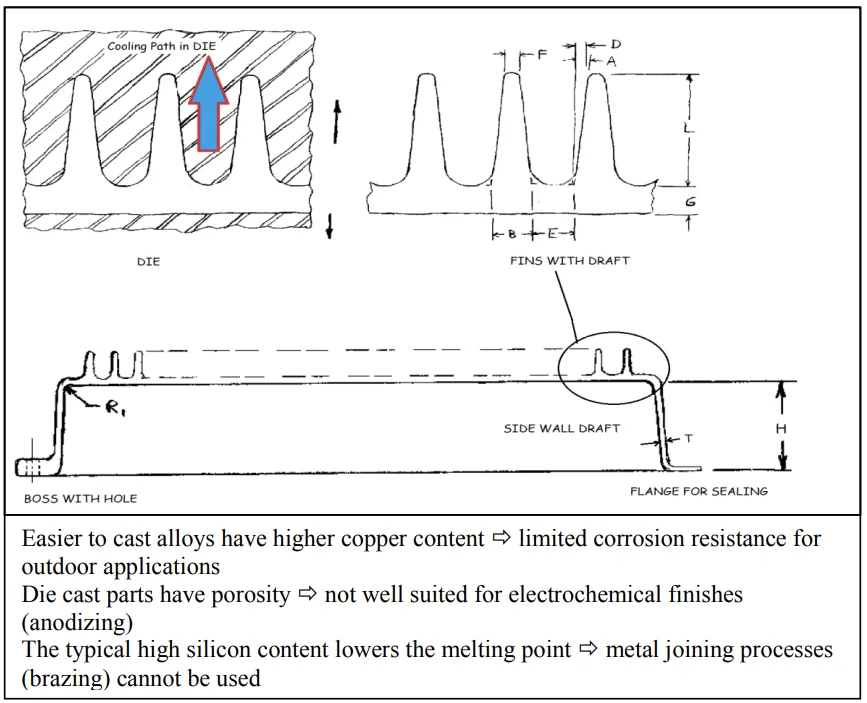
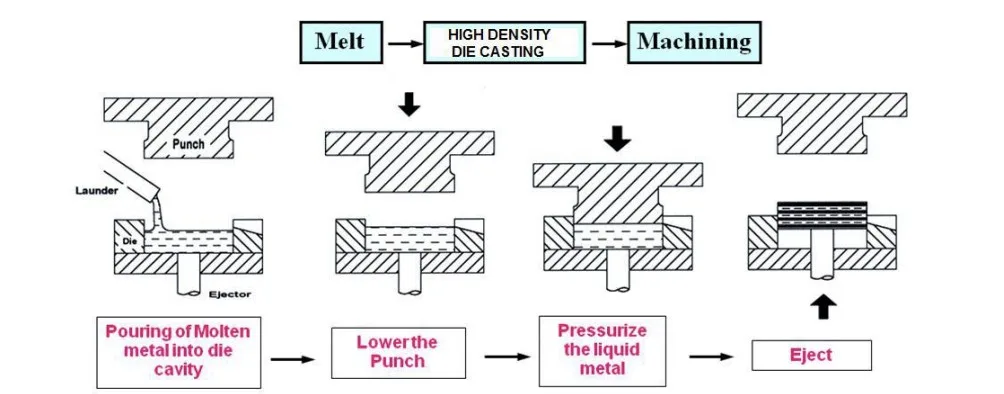
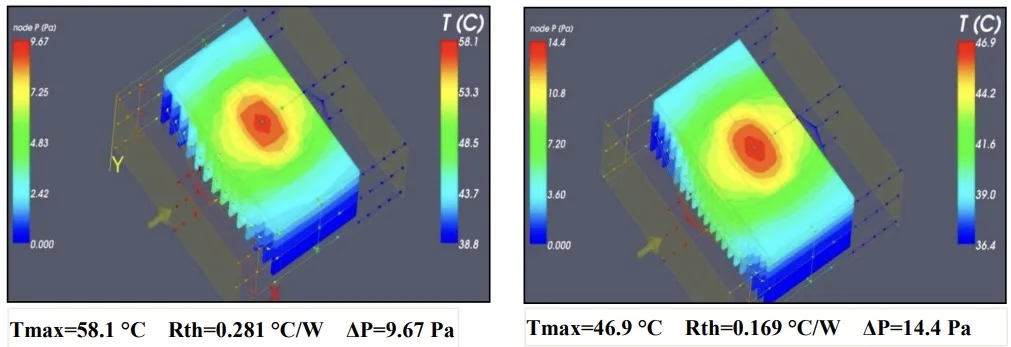
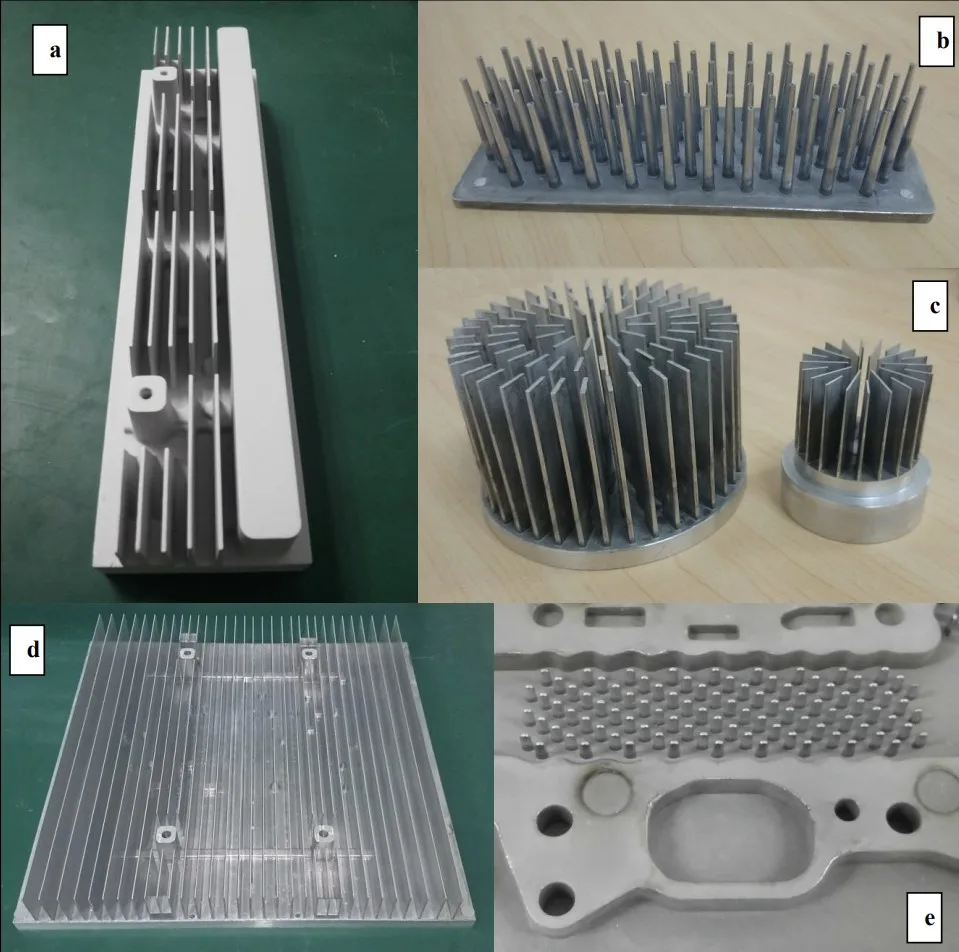
결과 및 성과:
- 정량적 결과: HDDC 공정은 기존 다이캐스팅 대비 열 저항을 약 40% 감소. HDDC 열 싱크의 인장 강도와 항복 강도는 기존 압출 제품과 유사하거나 우수함.
- 정성적 결과: HDDC 공정은 기공이 없는 고강도 열 싱크를 제작하고, 3차원 형상 설계의 자유도를 제공하며, 다양한 금속 재료의 결합을 가능하게 함.
- 기술적 성과: 고밀도 다이캐스팅(HDDC) 공정 개발을 통해 고성능 열 싱크 제조 기술 확보. 기존 공정의 한계 극복 및 열 관리 기술 향상에 기여.
저작권 및 참고 자료
본 자료는 Andrea Sce와 Lorenzo Caporale의 논문 "High Density Die Casting (HDDC): new frontiers in the manufacturing of heat sinks"를 기반으로 작성되었습니다.
논문 출처: doi:10.1088/1742-6596/525/1/012020
본 자료는 위 논문을 바탕으로 요약 작성되었으며, 상업적 목적으로 무단 사용이 금지됩니다.