1. 개요:
- 제목: Effects of die-casting defects on the blister formation in high-pressure die-casting aluminum structural components
- 저자:
- Bartłomiej Dybowski
- Andrzej Kiełbus
- Łukasz Poloczek
- 발행 연도: 2023
- 발행 학술지/학회: Engineering Failure Analysis
- Keywords:
- Blistering
- High pressure die casting
- Aluminum Alloys
- Heat treatment
- Microscopic characterization
2. 연구 배경:
- 연구 주제의 사회적/학문적 맥락:
- High-pressure die casting (HPDC)은 박막 비철금속 부품의 대량 생산에 널리 사용되며, 특히 자동차 구조 부품(쇼크 타워, A, B, C 필러 등)에 필수적이며 높은 기계적 물성(UTS > 180 MPa, YS > 130 MPa, A5 > 10%)을 요구합니다.
- 열처리는 HPDC 알루미늄 구조 부품에서 요구되는 연성을 확보하기 위해 종종 필요합니다.
- 그러나 열처리는 표면에 블리스터링을 유발할 수 있으며, 이는 최종 제품에서 허용되지 않고 부품 폐기로 이어져 생산 효율성을 감소시킵니다 [15].
- 기존 연구의 한계점:
- 새로운 Al-Si-Cu-Mn-Fe HPDC 합금에 대한 이전 연구에서는 강도 특성은 요구 사항을 충족하지만, 가소성은 구조 요소에 충분하지 않다는 것을 보여주었습니다.
- 최적의 합금 화학 조성과 초기 표면 블리스터가 없더라도 열처리가 향상된 강도 특성을 보장하지 않을 수 있습니다 [7].
- 기존 연구는 특정 다이캐스팅 결함과 블리스터 형성 간의 연관성을 더 자세히 조사하여 이 문제를 효과적으로 완화해야 합니다.
- 연구의 필요성:
- HPDC 알루미늄 부품의 열처리 중 블리스터링은 자동차 산업에서 심각한 문제이며, 생산 손실과 품질 문제를 야기합니다 [15].
- 특정 주조 결함이 블리스터 형성에 미치는 영향을 이해하는 것은 블리스터링을 최소화하거나 제거하고 구조 부품용 HPDC 공정의 신뢰성과 효율성을 개선하기 위한 전략 개발에 매우 중요합니다.
- 본 연구는 블리스터링을 시작하는 주조 결함의 유형을 식별하고 이러한 결함을 줄이기 위한 공정 최적화에 대한 통찰력을 제공하는 데 필요합니다.
3. 연구 목적 및 연구 질문:
- 연구 목적:
- AlSi10MnMg 합금 구조 부품에서 다이캐스팅 결함이 열처리 중 블리스터 형성 가능성에 미치는 영향을 제시합니다.
- HPDC 알루미늄 구조 부품에서 블리스터링의 시작점으로 작용하는 주조 결함의 유형을 식별합니다.
- 핵심 연구 질문:
- AlSi10MnMg 합금 구조 부품에서 다양한 유형의 다이캐스팅 결함은 열처리 중 블리스터 형성에 어떤 영향을 미칩니까?
- HPDC 부품의 핫 영역과 콜드 영역에서 블리스터 형성을 시작하는 주조 결함의 특징은 무엇입니까?
- 연구 가설:
- 열처리된 HPDC AlSi10MnMg 합금 구조 부품의 블리스터 형성은 미세 구조 불연속성을 생성하는 주조 결함에서 시작됩니다.
- 콜드 플레이크, 기공, 콜드 드롭, 콜드 샷, 산화막과 같은 다양한 유형의 주조 결함은 위치와 특성에 따라 블리스터 형성에 다양한 영향을 미칩니다.
4. 연구 방법론
- 연구 설계:
- 상용 9.5kg 쇼크 타워 AlSi10MnMg HPDC 합금 주조 사례 연구.
- 주조의 핫 영역(게이팅 시스템 근처)과 콜드 영역(게이팅 시스템에서 멀리 떨어진 영역)의 샘플 비교.
- 주조 상태 및 T7 열처리(용체화 열처리 및 과시효) 후 샘플 분석.
- 데이터 수집 방법:
- 미세 구조 관찰:
- 구조 연구를 위한 광학 현미경(LM) 및 주사 전자 현미경(SEM) 사용.
- 미세 구조 성분 미세 분석을 위한 에너지 분산형 X선 분광법(EDS) 사용.
- 비에칭 미세 단면에서 일반적인 절차를 사용하여 준비된 금속 조직 시편.
- 블리스터를 반으로 절단하여 검사하는 데 EDM(방전 가공) 사용.
- 주조 공정 시뮬레이션:
- MAGMAsoft 상용 소프트웨어를 사용하여 다이 내 액체 합금 주입 시뮬레이션 및 흐름 분석.
- 금형 충전 중 용융 속도 및 온도 시뮬레이션.
- 주조 표면 관찰:
- 열처리 후 주조 표면의 육안 검사를 통해 블리스터 위치 및 특성 식별.
- 미세 구조 관찰:
- 분석 방법:
- 블리스터 형성과 관련된 주조 결함 및 특성을 식별하기 위한 미세 구조의 질적 분석.
- 주조의 핫 영역과 콜드 영역에서 결함 유형과 블리스터 형성 비교.
- 주조 결함과 블리스터 위치 및 크기의 상관 관계 분석.
- 주조 중 용융 흐름 및 온도 분포를 이해하기 위한 시뮬레이션 결과 분석.
- 연구 대상 및 범위:
- 재료: 상용 AlSi10MnMg HPDC 합금.
- 부품: ITALPRESSE 2700 기계에서 생산된 9.5kg 쇼크 타워 주조.
- 초점: 다이캐스팅 결함(콜드 플레이크, 기공, 콜드 드롭, 콜드 샷, 산화막) 및 T7 열처리 중 블리스터 형성에 미치는 영향.
- 조사 영역: 주조의 핫 영역(게이팅 시스템 근처) 및 콜드 영역(게이팅 시스템에서 멀리 떨어진 영역).
5. 주요 연구 결과:
- 핵심 연구 결과:
- 블리스터링 과정은 미세 구조 불연속성을 생성하는 주조 결함에서 시작됩니다.
- 불연속성에 기체가 존재하면 용체화 처리 중에 팽창하여 표면 블리스터를 형성합니다.
- 다양한 주조 결함이 다양한 심각도와 위치 의존성으로 블리스터 형성에 기여합니다.
- 가장 큰 블리스터는 콜드 플레이크에서 형성되며, 주로 게이팅 시스템 근처의 주조 영역(핫 영역)에서 발생합니다.
- 더 작은 블리스터는 기공(가스 및 수축 기공)에서 형성되며 핫 영역과 콜드 영역 모두에서 발견됩니다.
- 콜드 드롭, 콜드 샷 및 얇은 산화막은 주로 게이팅 시스템에서 멀리 떨어진 영역(콜드 영역)에서 블리스터링 부위로 작용합니다.
- 통계적/정성적 분석 결과:
- 블리스터 위치: 대부분의 블리스터링은 핫 영역인 게이팅 시스템 근처에서 발생합니다 [Fig. 3]. 반대로 콜드 영역에서는 블리스터가 거의 발생하지 않습니다 [Fig. 4a].
- 블리스터 크기: 핫 영역에 있는 블리스터는 콜드 영역에 있는 블리스터보다 분리되어 있고 더 큽니다 [Fig. 4b]. 핫 영역의 큰 블리스터는 크기가 5mm를 초과할 수 있지만 콜드 영역의 작은 블리스터는 2mm 미만입니다.
- 결함 유형 및 위치:
- 핫 영역: 주변 합금과는 다른 미세 구조를 가진 큰 입자(콜드 플레이크)가 특징입니다 [Fig. 8c, Fig. 9]. 또한 소수의 단일 기공 [Fig. 8a], Si 공정상의 단일 큰 분리, 금속간 화합물 및 두꺼운 α-Al 덴드라이트가 존재합니다 [Fig. 8b].
- 콜드 영역: 가스 및 수축 기공이 핫 영역에 비해 더 높습니다 [Fig. 10a]. 긴 불연속성과 얇은 층이 주조 벽 가장자리 근처에 존재합니다. 미세하고 원형이며 길쭉한 입자(콜드 드롭) [Fig. 11a, b]. 산화막도 발견됩니다 [Fig. 11c, d].
- 블리스터 아래의 미세 구조: 블리스터 중심 아래의 AlSi10MnMg 합금 미세 구조는 주변 합금과 다르며 [Fig. 16a], 이는 블리스터링이 넓고 평평한 합금 미세 구조 불연속성에서 시작됨을 나타냅니다.
- 데이터 해석:
- 콜드 플레이크: 평평한 모양, 큰 크기 및 매트릭스와의 불연속성으로 인해 가스를 가두어 핫 영역에서 큰 블리스터 형성에 주요 부위로 작용합니다.
- 기공: 핫 영역과 콜드 영역 모두에서 더 작은 블리스터 형성에 기여합니다. 구형 기공은 블리스터를 형성하는 데 더 높은 압력이 필요하지만 [10], 상호 연결된 길쭉한 미세 수축 기공은 블리스터 위험을 증가시킵니다.
- 콜드 드롭, 콜드 샷, 산화막: 낮은 합금 온도와 반고체 흐름으로 인해 종종 기공 및 라미네이션과 관련된 콜드 영역에서 더 작은 블리스터를 시작합니다.
- 블리스터 모양: 핫 영역의 블리스터는 종종 반원형이며 주조 벽과 평행한 평평한 바닥 가장자리를 가지고 있습니다 [Fig. 13]. 이는 콜드 플레이크와 같은 평평한 불연속성에서 형성이 시작됨을 나타냅니다.
- Figure Name List:
- Fig. 1. 쇼크 타워 주조 개략도.
- Fig. 2. 다양한 금형 충전 단계(a, b)에서 액체 합금 온도.
- Fig. 3. 쇼크 타워 주조 표면의 블리스터 분포.
- Fig. 4. (a) 콜드 영역(Fig. 3의 영역 2E) 및 (b) 핫 영역(Fig. 3의 영역 10G)에서 열처리된 주조 표면의 블리스터.
- Fig. 5. 주조된 AlSi10MnMg 합금 미세 구조, LM: (a) 콜드 영역, (b) 핫 영역.
- Fig. 6. 주조된 AlSi10MnMg 합금의 금속간 화합물, SEM: (a) 판상형 및 (b) 다각형.
- Fig. 7. 열처리된 AlSi10MnMg 합금 미세 구조, SEM: (a) 구형화된 Si 및 (b) 금속간 화합물.
- Fig. 8. 쇼크 타워 주조 핫 영역의 주조 결함, LM: (a) 기공, (b) 외부 응고 결정(ESC), (c) 콜드 플레이크 및 (d) 플레이크 가장자리의 불연속성.
- Fig. 9. AlSi10MnMg 합금 미세 구조의 콜드 플레이크, LM.
- Fig. 10. 쇼크 타워 주조 콜드 영역의 주조 결함, SEM: (a) 기공, (b) 콜드 셧 및 라미네이션 (b-d).
- Fig. 11. 주조된 쇼크 타워 주조 콜드 영역의 주조 결함, SEM: 콜드 드롭 (a, b), 얇은 산화막 (c, d).
- Fig. 12. Fig. 11c에 표시된 얇은 막에서 얻은 EDS 차트.
- Fig. 13. 주조 벽 가장자리에 평행한 불연속성에서 형성된 블리스터, LM.
- Fig. 14. 주조 벽 가장자리에 각도를 두고 놓인 불연속성에서 형성된 블리스터, LM.
- Fig. 15. 블리스터에서 관찰된 표면 특성, SEM: (a) 중앙의 평평한 표면, (b) 가장자리의 거친 표면.
- Fig. 16. 다양한 합금 미세 구조, LM: (a) Fig. 13에 표시된 블리스터 중앙, (b) Fig. 14에 표시된 블리스터 아래의 2차 균열.
- Fig. 17. 확장되지 않은 불연속성, LM: (a) 블리스터 가장자리, (b) 주조 가장자리에서 멀리 떨어진 콜드 플레이크.
- Fig. 18. 콜드 드롭, SEM: (a) 블리스터 가장자리, (b) 합금 기공에 의해 형성된 블리스터.
- Fig. 19. 쇼크 타워 콜드 영역의 큰 블리스터, LM.
- Fig. 20. AlSi10MnMg 합금 기공에서 형성된 블리스터, SEM: a) 분리된 가스 기공, b) 연결된 가스 기공, c) 수축 기공.
- Fig. 21. 쇼크 타워 주조의 콜드 영역, SEM: (a) 반구형 블리스터, (b) 확장된 얇은 불연속성.
- Fig. 22. 확장된 불연속성, SEM: (a) 평평한 콜드 드롭에서 형성, (b) 구형 콜드 드롭에서 형성.
- Fig. 23. 쇼크 타워 콜드 영역의 바늘 모양 콜드 드롭, SEM: (a) 주조 상태, (b) 열처리 상태.
- Fig. 24. 얇은 산화막에 의해 형성된 블리스터, SEM.
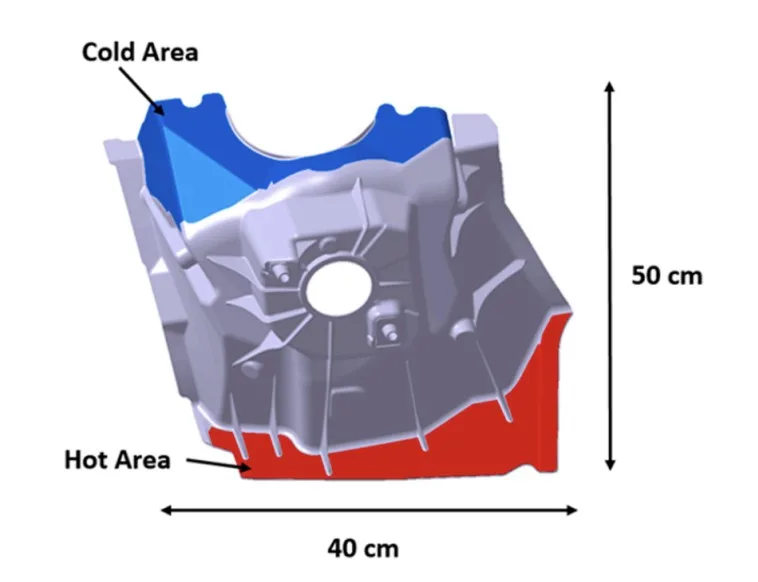
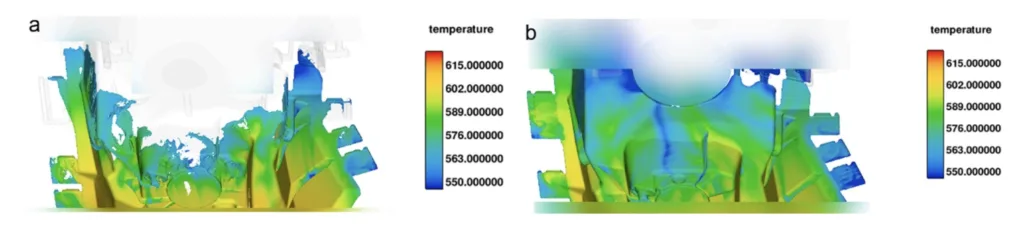
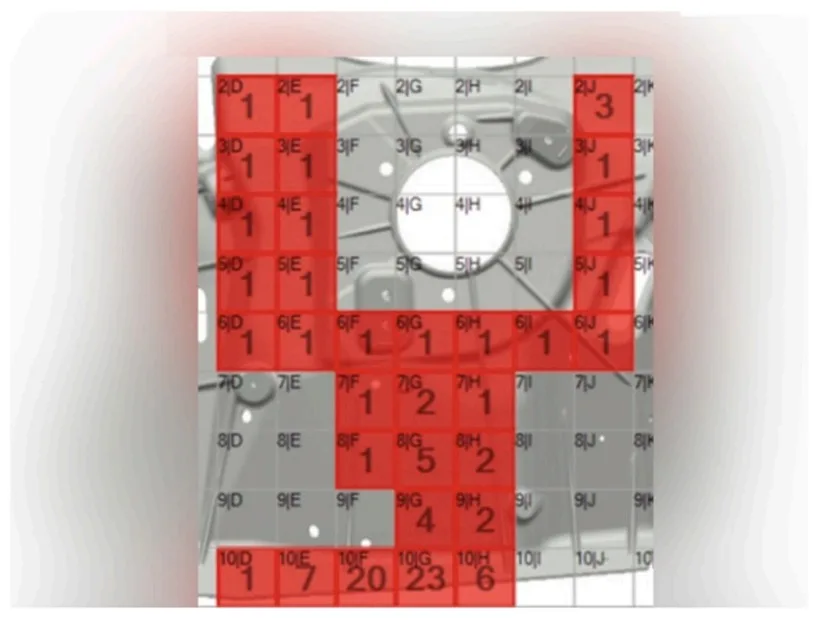
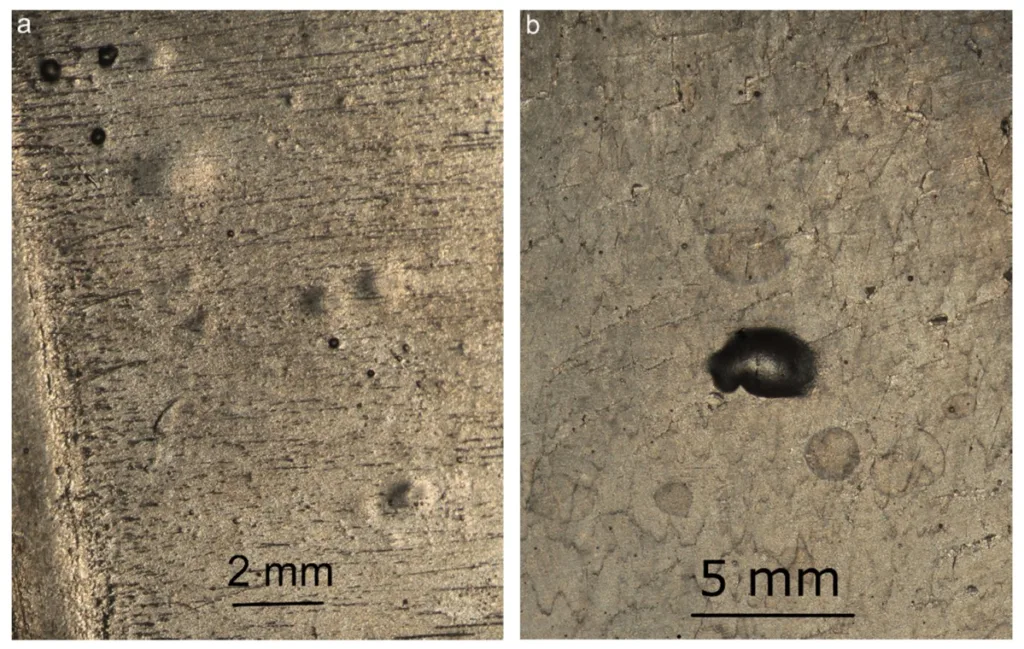
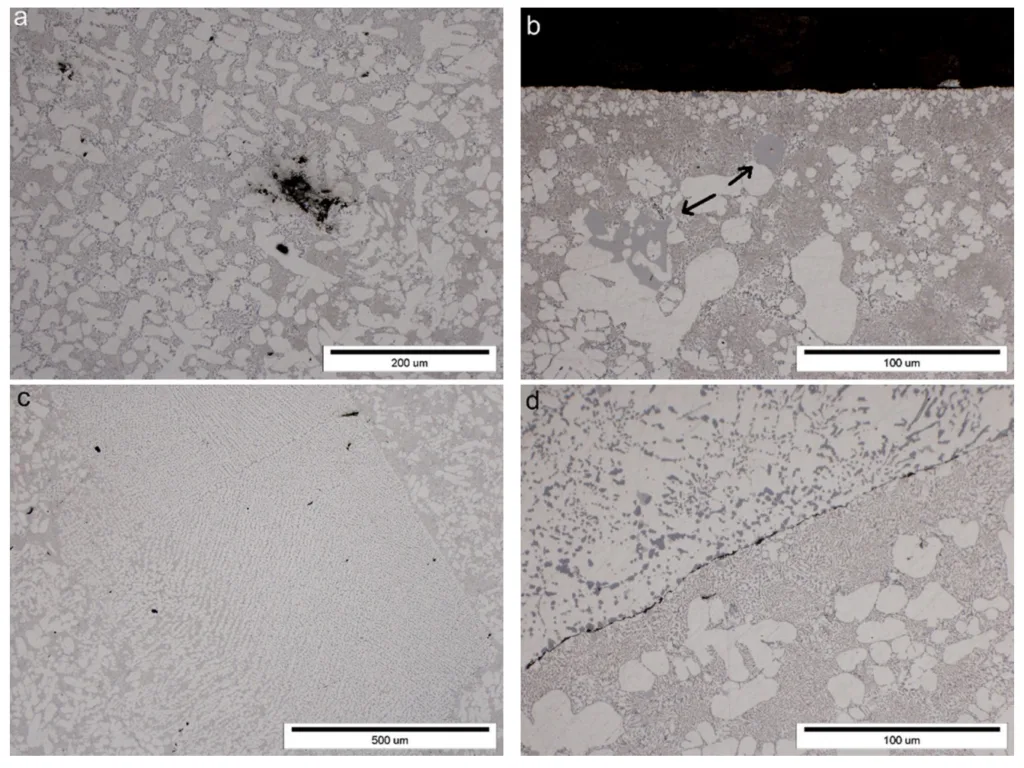
6. 결론 및 논의:
- 주요 결과 요약:
- HPDC AlSi10MnMg 합금의 블리스터 형성은 미세 구조 불연속성을 생성하는 주조 결함에 의해 시작됩니다.
- 콜드 플레이크는 가장 해로운 결함으로, 핫 영역에서 큰 블리스터를 유발하고 합금 연성을 감소시킵니다.
- 기공, 콜드 드롭, 콜드 샷 및 산화막도 블리스터링에 기여하며, 특히 콜드 영역에서 더 작은 블리스터를 유발합니다.
- 블리스터링은 큰 콜드 플레이크의 유병률로 인해 게이팅 시스템 근처의 핫 영역에서 더 두드러집니다.
- 연구의 학술적 의의:
- 본 연구는 HPDC 알루미늄 구조 부품에서 특정 다이캐스팅 결함과 블리스터 형성 간의 관계에 대한 자세한 분석을 제공합니다.
- 콜드 플레이크를 큰 블리스터의 주요 원인으로 식별하고 기공, 콜드 드롭 및 산화막과 같은 다른 결함이 블리스터 시작에 미치는 역할을 강조합니다.
- 연구 결과는 HPDC 합금의 블리스터링 메커니즘과 이 현상에서 주조 결함의 중요한 역할에 대한 더 나은 이해에 기여합니다.
- 실무적 시사점:
- 콜드 플레이크 형성을 최소화하는 것은 HPDC AlSi10MnMg 합금 구조 부품, 특히 핫 영역에서 블리스터링을 줄이는 데 매우 중요합니다.
- 공정 최적화 전략은 다음 사항에 초점을 맞춰야 합니다.
- 콜드 플레이크 형성을 줄이기 위해 높은 샷 슬리브 온도를 유지하고 합금 체류 시간을 최소화합니다.
- 큰 플레이크를 분해하기 위해 게이팅 시스템에 장애물을 구현합니다 [17].
- 콜드 플레이크를 줄이기 위해 정기적인 용광로 유지 보수 및 도징 탭 청소를 실시합니다.
- 가스 혼입 및 기공을 최소화하기 위해 윤활 시스템, 진공 시스템 및 샷 프로파일 설정을 최적화합니다 [19].
- 콜드 영역에서 응고 속도를 줄이고 콜드 드롭 및 콜드 셧을 최소화하기 위해 금형 냉각을 제어합니다.
- 연구의 한계점:
- 본 연구는 쇼크 타워 주조의 단일 사례 연구를 기반으로 하며, 연구 결과는 이 부품 형상 및 생산 공정에 특이적일 수 있습니다.
- 연구는 주로 질적 연구이며, 블리스터 형성 및 결함 빈도에 대한 양적 통계 분석보다는 미세 현미경 관찰 및 결함 특성 분석에 중점을 둡니다.
- 다양한 HPDC 부품 및 합금에서 결함 크기, 유형 및 블리스터 심각도 간의 관계를 정량화하기 위한 추가 연구가 필요합니다.
7. 향후 후속 연구:
- 후속 연구 방향:
- 다양한 유형 및 크기의 주조 결함과 블리스터 형성 확률 및 크기 간의 상관 관계에 대한 정량적 분석.
- 다양한 주조 결함 유형과 관련된 블리스터 형성에 대한 다양한 열처리 매개변수(온도, 시간)의 영향 조사.
- HPDC에서 콜드 플레이크 및 기타 블리스터 유발 결함의 형성을 구체적으로 목표로 하고 줄이기 위한 공정 최적화 전략 개발 및 검증.
- 다양한 합금 조성과 주조 결함과 관련된 블리스터 형성 민감도 연구.
- 추가 탐구가 필요한 영역:
- 열처리 중 다양한 유형의 주조 결함 내에서 가스 혼입 및 팽창의 정확한 메커니즘.
- 콜드 플레이크 및 기타 결함의 형성 및 분포에 대한 금형 설계 및 게이팅 시스템의 영향.
- HPDC 생산에서 블리스터 형성을 줄이기 위한 실시간 결함 감지 및 공정 제어 방법의 효과.
8. 참고문헌:
- [1] F. Bonollo, N. Gramegna, G. Timelli, High-pressure die-casting: contradictions and challenges, JOM 67 (2015) 901-908, https://doi.org/10.1007/s11837-015-1333-8.
- [2] S. Ji, Y. Wang, D. Watson, Z. Fan, Microstructural evolution and solidification behavior of Al-Mg-Si alloy in high-pressure die casting, Metall. Mater. Trans. A 44 (2013) 3185-3197, https://doi.org/10.1007/s11661-013-1663-5.
- [3] M. Jolly, L. Katgerman, Modelling of defects in aluminium cast products, Prog Mater Sci. 123 (2022), 100824, https://doi.org/10.1016/j.pmatsci.2021.100824.
- [4] A. Zhang, Z. Guo, Q. Wang, S. Xiong, Multiphase-field modelling of hydrogen pore evolution during alloy solidification, IOP Conf Ser Mater Sci Eng. 861 (2020), 012021, https://doi.org/10.1088/1757-899X/861/1/012021.
- [5] P. Zhang, Z. Li, B. Liu, W. Ding, Effect of chemical compositions on tensile behaviors of high pressure die-casting alloys Al-10Si-yCu-xMn-zFe, Mater. Sci. Eng. A 661 (2016) 198-210, https://doi.org/10.1016/j.msea.2016.03.032.
- [6] P. Zhang, Z. Li, B. Liu, W. Ding, Tensile properties and deformation behaviors of a new aluminum alloy for high pressure die casting, J Mater Sci Technol. 33 (2017) 367-378, https://doi.org/10.1016/j.jmst.2016.02.013.
- [7] S. Seifeddine, D. Poletaeva, M. Ghorbani, A. Jarfors, Heat treating of high pressure die cast components: challenges and possibilities, in: Light Metals 2014, Springer International Publishing, Cham, 2014, pp. 183-188, https://doi.org/10.1007/978-3-319-48144-9_32.
- [8] X.G. Hu, Q. Zhu, S.P. Midson, H.V. Atkinson, H.B. Dong, F. Zhang, Y.L. Kang, Blistering in semi-solid die casting of aluminium alloys and its avoidance, Acta Mater. 124 (2017) 446-455, https://doi.org/10.1016/j.actamat.2016.11.032.
- [9] H. Zhao, Y. Bai, X. Ouyang, P. Dong, Simulation of mold filling and prediction of gas entrapment on practical high pressure die castings, Trans. Nonferrous Met. Soc. Chin. 20 (2010) 2064-2070, https://doi.org/10.1016/S1003-6326(09)60418-0.
- [10] O. Ozhoga-Maslovskaja, E. Gariboldi, J.N. Lemke, Conditions for blister formation during thermal cycles of Al-Si-Cu-Fe alloys for high pressure die-casting, Mater Des. 92 (2016) 151-159, https://doi.org/10.1016/j.matdes.2015.12.003.
- [11] H. Toda, P.C. Qu, S. Ito, K. Shimizu, K. Uesugi, A. Takeuchi, Y. Suzuki, M. Kobayashi, Formation behaviour of blister in cast aluminium alloy, Int. J. Cast Met. Res. 27 (2014) 369-377, https://doi.org/10.1179/1743133614Y.0000000123.
- [12] H. Kang, H. Jang, S. Oh, P. Yoon, G. Lee, J. Park, E. Kim, Y. Choi, Effects of solution treatment temperature and time on the porosities and mechanical properties of vacuum die-casted and T6 heat-treated Al-Si-Mg alloy, Vacuum 193 (2021), 110536, https://doi.org/10.1016/j.vacuum.2021.110536.
- [13] H. Cao, Q. Sun, Q. Pu, L. Wang, M. Huang, Z. Luo, J. Che, Effect of vacuum degree and T6 treatment on the microstructure and mechanical properties of Al-Si-Cu alloy die castings, Vacuum 172 (2020), 109063, https://doi.org/10.1016/j.vacuum.2019.109063.
- [14] H.J. Kang, P.H. Yoon, G.H. Lee, J.Y. Park, B.J. Jung, J.Y. Lee, C.U. Lee, E.S. Kim, Y.S. Choi, Evaluation of the gas porosity and mechanical properties of vacuum assisted pore-free die-cast Al-Si-Cu alloy, Vacuum 184 (2021), 109917, https://doi.org/10.1016/j.vacuum.2020.109917.
- [15] R.N. Lumley, R.G. O'Donnell, D.R. Gunasegaram, M. Givord, Heat treatment of high-pressure die castings, Metall. Mater. Trans. A 38 (2007) 2564-2574, https://doi.org/10.1007/s11661-007-9285-4.
- [16] P.W. Cleary, J. Ha, M. Prakash, T. Nguyen, Short shots and industrial case studies: understanding fluid flow and solidification in high pressure die casting, Appl Math Model. 34 (2010) 2018-2033, https://doi.org/10.1016/j.apm.2009.10.015.
- [17] D.R. Gunasegaram, M. Givord, R.G. O'Donnell, B.R. Finnin, Improvements engineered in UTS and elongation of aluminum alloy high pressure die castings through the alteration of runner geometry and plunger velocity, Mater. Sci. Eng. A 559 (2013) 276-286, https://doi.org/10.1016/j.msea.2012.08.098.
- [18] W.G. Walkington, Die casting defects: causes and solutions, NADCA, 1997.
- [19] X.P. Niu, B.H. Hu, I. Pinwill, H. Li, Vacuum assisted high pressure die casting of aluminium alloys, J. Mater. Process Technol. 105 (2000) 119-127, https://doi.org/10.1016/S0924-0136(00)00545-8.
9. Copyright:
*본 자료는 Bartłomiej Dybowski, Andrzej Kiełbus, Łukasz Poloczek의 논문: Effects of die-casting defects on the blister formation in high-pressure die-casting aluminum structural components을 기반으로 작성되었습니다.
*논문 출처: https://doi.org/10.1016/j.engfailanal.2023.107223
본 자료는 위 논문을 바탕으로 요약 작성되었으며, 상업적 목적으로 무단 사용이 금지됩니다.
Copyright © 2025 CASTMAN. All rights reserved.