1. 개요:
- 제목: Al-Si 다이캐스트 엔진 블록의 미세 구조와 기계적 특성 간의 상관관계 (Correlation between microstructure and mechanical properties of Al-Si diecast engine blocks)
- 저자: 파비오 그로셀레, 줄리오 티멜리, 프랑코 보놀로, 로베르토 몰리나 (Fabio Grosselle, Giulio Timelli, Franco Bonollo, Roberto Molina)
- 발행 연도: 2009년
- 발행 학술지/학회: 금속학 및 기술 (Metallurgical Science and Technology)
- 키워드:
- 알루미늄 합금 (Aluminium alloys)
- EN-AC 46000
- 고압 다이캐스팅 (High-pressure die-casting)
- SDAS (2차 덴드라이트 암 간격)
- 공정 Si (Eutectic Si)
- 미세 구조 (Microstructure)
- 엔진 블록 (Engine block)
2. 연구 배경:
- 연구 주제의 사회적/학문적 맥락:
- 승용차에서 실린더 블록은 가장 무거운 부품이며, 연비와 차량 주행 성능에 중요한 역할을 합니다.
- 알루미늄 합금 주조는 경량화 및 배기가스 감소 잠재력으로 인해 현대 승용차 제작에 점점 더 많이 사용되고 있습니다.
- 주철 대신 알루미늄 합금을 실린더 블록에 적용하면 가솔린 엔진의 경우 최대 45%까지 무게를 줄일 수 있습니다.
- 알루미늄 합금은 열전도율이 높아 국부적인 온도 제어를 개선하여 실린더 크기당 더 많은 출력을 낼 수 있습니다.
- 고압 다이캐스팅(HPDC)은 복잡한 형상과 얇은 벽 두께를 가진 부품을 높은 생산 속도로 생산하여 비용을 절감할 수 있기 때문에 대량 생산 엔진 블록에 널리 사용됩니다.
- 아공정 2차 Al-Si 합금은 우수한 주조성, 우수한 기계적 특성 및 저비용으로 인해 HPDC 공정에 일반적으로 사용됩니다.
- 기존 연구의 한계점:
- HPDC 부품은 복잡한 주조 형상과 공정 변수의 가변성으로 인해 수축 공동, 냉간 접합, 산화 피막, 드로스 및 갇힌 공기 방울과 같은 결함이 발생할 수 있습니다.
- 1차 α-Al 및 공정 Si 입자의 분포, 형태 및 크기를 포함한 Al-Si 주물의 미세 구조는 냉각 조건 및 응고 이력에 따라 달라집니다.
- 다이 벽에서 주물 중심선으로 이동함에 따라 미세 구조가 조대화되고, 충전 역학과 긴 응고 시간의 결과로 결함이 쉽게 형성될 수 있습니다.
- Cu, Mg 및 미량 원소의 존재는 강화 석출물 및 철이 풍부한 금속간 화합물을 포함한 다른 상의 형성을 유도할 수 있습니다.
- 연구의 필요성:
- Al-Si 다이캐스트 엔진 블록의 성능과 신뢰성을 최적화하려면 미세 구조와 기계적 특성 간의 상관관계를 이해하는 것이 중요합니다.
- 공정 변수, 미세 구조 특징 및 결함은 모두 알루미늄 합금의 최종 기계적 특성에 기여합니다.
- 결함이 없는 부품에서 파괴는 취성 금속간 화합물 또는 공정 Si 입자의 벽개에 의해 시작되며, SDAS 값에 따라 결정립계 또는 셀 경계를 따라 전파됩니다.
- 결함은 파괴 시작 및 전파에 영향을 미쳐 기계적 특성을 저하시킬 수 있습니다.
- HPDC 엔진 블록에서 SDAS, 공정 Si 입자 크기 및 형태와 같은 미세 구조 특징과 기계적 특성 간의 관계를 분석할 필요가 있습니다.
3. 연구 목적 및 연구 질문:
- 연구 목적:
- HPDC 엔진 블록의 미세 구조와 기계적 특성 간의 상관관계를 분석합니다.
- 특히, 기계적 특성과 2차 덴드라이트 암 간격(SDAS), 크기 및 공정 Si 입자의 형태와 같은 미세 구조 특징을 연관시킵니다.
- 핵심 연구 질문:
- HPDC Al-Si 합금 엔진 블록의 미세 구조 특징(SDAS, 공정 Si 입자 크기 및 형태)은 기계적 특성(UTS 및 파단 연신율)과 어떻게 상관관계가 있습니까?
- 응고 속도 및 냉각 조건은 엔진 블록의 미세 구조 및 기계적 특성에 어떤 영향을 미칩니까?
- 이러한 다이캐스트 부품에서 미세 구조 변수와 기계적 특성 간에 정량적 관계를 설정할 수 있습니까?
- 연구 가설:
- 기계적 특성, 특히 UTS 및 파단 연신율은 Al-Si 다이캐스트 엔진 블록의 미세 구조에 의해 크게 영향을 받습니다.
- 낮은 SDAS 값과 작고 조밀한 공정 Si 입자를 특징으로 하는 미세 구조가 더 우수한 기계적 특성을 나타낼 것입니다.
- UTS와 SDAS, 등가 직경 및 Si 입자의 종횡비의 곱 사이에 선형 상관관계가 존재하며, 파단 연신율은 미세 구조 변화에 대해 지수 함수적 경향을 나타냅니다.
4. 연구 방법론
- 연구 설계:
- 2차 AlSi9Cu3 주조 합금(EN AC-46000-UNI EN 1706 합금)으로 제작된 HPDC 4기통 직렬 엔진 블록에 대한 철저한 분석.
- 엔진 블록 주조 내의 여러 위치에서 기계적 특성과 미세 구조 특징 간의 상관관계 연구.
- 데이터 수집 방법:
- 화학 조성 분석: 별도로 주조된 시편에서 측정 (표 1). 측정 방법은 명시되지 않음.
- 열 분석: 액상선 온도 (Tliq = 585°C)는 열 분석을 통해 결정되었습니다.
- 방사선 투과 검사: 주조 전체에 걸쳐 거시적 결함의 존재를 감지하기 위해 수행되었습니다.
- 기계적 시험:
- ASTM-B577에 따라 절단된 엔진 블록의 여러 위치에서 가공된 직사각형 단면을 가진 평판 인장 시험편을 사용한 인장 시험.
- 항복 강도(YS), 극한 인장 강도(UTS) 및 파단 연신율(Sf)은 크로스헤드 속도 2mm/min(변형률 속도 ~10⁻³ s⁻¹)의 컴퓨터 제어 인장 시험기 MTS 810을 사용하여 측정했습니다.
- ASTM E-384에 따라 0.2 kgf의 하중과 30초의 유지 시간을 사용하여 연마된 시편에서 비커스 미세 경도 측정.
- 미세 구조 분석:
- 광학 현미경 및 에너지 분산 분광기(EDS)가 장착된 주사 전자 현미경(SEM).
- 이미지 분석기를 사용한 정량적 이미지 분석:
- 선형 절편법을 사용한 2차 덴드라이트 암 간격(SDAS) 측정.
- 공정 실리콘 입자 크기(등가 원 직경, d) 및 종횡비(α) 측정.
- 분석 방법:
- 주조 결함의 영향을 최소화하기 위해 최상의 값을 평균화하여 실험 데이터의 통계 분석.
- 미세 구조 변수(SDAS, 공정 Si 입자 크기 및 종횡비)와 기계적 특성(UTS, Sf, 미세 경도) 간의 관계를 결정하기 위한 상관관계 분석.
- 상관관계 유형(선형, 지수)을 설정하고 적합도 품질을 평가하기 위해 결정 계수(R²)를 계산하기 위한 회귀 분석.
- 연구 대상 및 범위:
- 다이나믹 샷 컨트롤 및 진공 시스템을 갖춘 냉간 챔버 다이캐스팅 기계를 사용하여 생산된 HPDC 4기통 직렬 엔진 블록.
- 재료: 2차 AlSi9Cu3 합금 (EN AC-46000-UNI EN 1706 합금).
- 응고 조건의 변화를 고려하여 엔진 블록 주조의 여러 영역 내에서 미세 구조와 기계적 특성을 연관시키는 데 중점을 둡니다.
5. 주요 연구 결과:
- 핵심 연구 결과:
- HPDC 엔진 블록의 기계적 특성은 미세 구조에 의해 크게 영향을 받습니다.
- 더 높은 응고 속도(예: 주조 벽 근처 및 얇은 단면)로 얻은 더 미세한 미세 구조는 더 높은 UTS 및 파단 연신율을 나타냅니다.
- 더 느린 응고(예: 두꺼운 단면 및 벌크헤드 지지대)로 인한 더 조대한 미세 구조는 더 낮은 기계적 특성과 결함의 증가된 존재를 보여줍니다.
- UTS 및 파단 연신율은 SDAS 및 공정 Si 입자 크기가 증가함에 따라 감소합니다.
- UTS와 SDAS, 등가 직경 및 공정 Si 입자의 종횡비의 곱 사이에 선형 상관관계가 발견되었습니다.
- 파단 연신율은 SDAS 및 공정 Si 입자 크기가 증가함에 따라 지수 함수적으로 감소하여 UTS보다 미세 구조 변화에 더 높은 민감도를 나타냅니다.
- 통계적/정성적 분석 결과:
- 방사선 투과 검사 결과 진공 시스템으로 인해 중요한 결함이 최소화된 우수한 주조 건전성을 보였습니다. 작은 거시적 기공은 원형 단면, 벌크헤드 지지대 및 라이너 아래, 특히 진공 라인 근처에서 관찰되었습니다.
- 미세 구조는 주조 전체에 걸쳐 다양했습니다.
- 벽 근처: 더 미세하고 기공이 없는 미세 구조.
- 중심 방향: 더 조대한 미세 구조, 더 큰 α-Al 상, 더 조대한 공정 Si 입자 및 더 많은 결함.
- α-Al 상 형태: 벽 근처에서는 등축 구상, 중심 방향에서는 덴드라이트.
- 공정 Si 형태: 벽 근처에서는 섬유상 및 미세, 두꺼운 단면에서는 조대한 판상.
- 미세 경도는 주조 단면의 가장자리에서 중심 방향으로 감소했습니다.
- YS 값은 여러 영역에서 유의미한 변화를 보이지 않았습니다.
- UTS 및 파단 연신율 값은 주철 라이너 사이의 영역(UTS: 274±10MPa, 연신율: 2.5±0.4%)이 라이너 및 벌크헤드 지지대 아래 영역(UTS: 236 MPa, 연신율: 1.4%)보다 높았습니다.
- UTS와 SDAS 간의 상관관계 및 파단 연신율과 SDAS 간의 상관관계에 대한 결정 계수(R²)는 0.52였습니다.
- UTS와 공정 Si 입자 크기 간의 상관관계 및 파단 연신율과 공정 Si 입자 크기 간의 상관관계에 대한 R²는 각각 0.83 및 0.89였습니다.
- UTS와 결합된 매개변수(SDAS x 등가 직경 x 종횡비) 간의 상관관계에 대한 R²는 0.50이었고, 파단 연신율의 경우 0.55였습니다.
- 데이터 해석:
- 응고 속도 및 냉각 조건은 미세 구조와 결과적으로 기계적 특성에 영향을 미치는 주요 요인입니다.
- 빠른 응고를 통해 얻은 더 미세한 미세 구조는 기계적 강도와 연성을 향상시킵니다.
- 공정 Si 입자 크기 및 형태는 UTS보다 파단 연신율에 더 큰 영향을 미칩니다.
- SDAS와 공정 Si 입자 특성의 결합된 효과는 기계적 특성에 대한 영향을 포괄적으로 이해하는 데 도움이 됩니다.
- Figure Name List:
- Fig. 1: 6개의 인게이트와 진공 채널이 있는 엔진 블록 그림.
- Fig. 2: 인장 시편이 가공된 위치.
- Fig. 3: 기공률의 존재를 보여주는 벌크헤드 지지대의 방사선 투과 이미지.
- Fig. 4: 두꺼운 단면에 해당하는 미세 구조.
- Fig. 5: (a) 섬유상 및 (b) 층상 모양의 공정 실리콘 입자 (각각 높은 냉각 속도 및 낮은 냉각 속도 영역).
- Fig. 6: SDAS의 함수로서의 공정 Si 입자의 평균 직경 및 종횡비.
- Fig. 7: 다이캐스트 AlSi9Cu3 엔진 블록의 미세 구조.
- Fig. 8: 시편의 단면을 따라 측정한 비커스 미세 경도.
- Fig. 9: (a) 산화물 개재물 및 피막, (b) 기공률 및 (c) 다이캐스팅에서 관찰된 냉간 접합.
- Fig. 10: 낮은 응고 속도 영역에서 공정 실리콘의 편석 밴드.
- Fig. 11: SDAS의 함수로서의 UTS 및 파단 연신율.
- Fig. 12: 공정 Si 입자의 등가 직경의 함수로서의 UTS 및 파단 연신율.
- Fig. 13: 결합된 매개변수 SDAS x 등가 직경 x 공정 Si 입자의 종횡비의 함수로서의 UTS 및 파단 연신율 값.
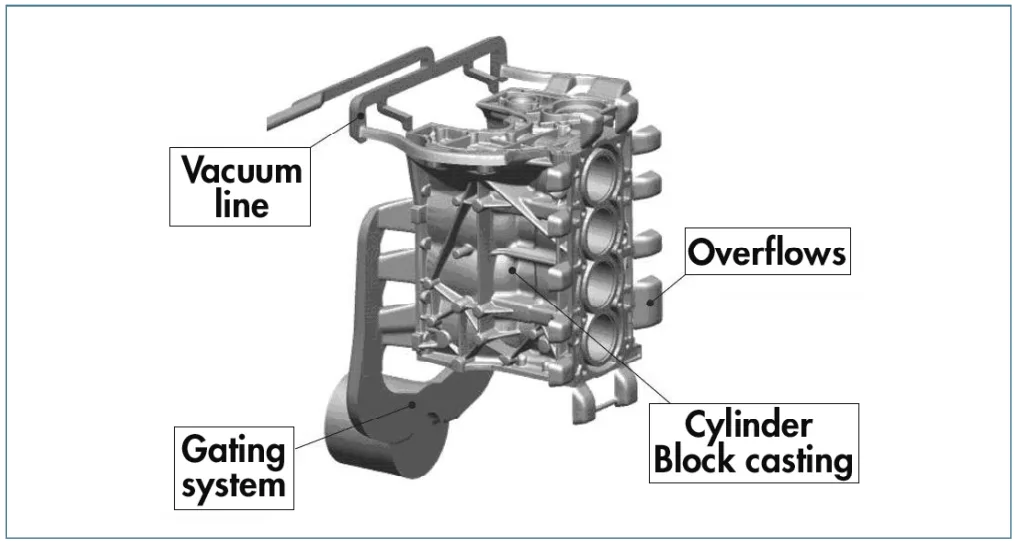
6. 결론 및 논의:
- 주요 결과 요약:
- HPDC 4기통 직렬 엔진 블록의 미세 구조와 기계적 특성은 밀접하게 관련되어 있습니다.
- 더 높은 응고 속도는 더 미세한 미세 구조와 향상된 기계적 특성(UTS 및 파단 연신율)으로 이어집니다.
- 응고 시간이 증가하면 SDAS가 더 크고, 공정 Si 입자가 더 조대하며, 블록형 α-Al(Mn, Fe, Cr)Si 상의 비율이 더 높은 더 조대한 미세 구조가 되어 기계적 특성이 저하됩니다.
- 기계적 특성은 미세 구조에 의해 영향을 받으며, 최상의 UTS 및 연신율 값은 낮은 SDAS와 작고 조밀한 공정 Si 입자에 대해 얻어집니다.
- 더 조대한 미세 구조와 더 높은 결함량은 합금 강도를 감소시키고 파괴 핵 생성을 촉진합니다.
- UTS와 SDAS, 공정 Si 입자 크기 및 종횡비의 결합된 매개변수 사이에 선형 상관관계가 존재하며, 파단 연신율은 이러한 미세 구조 변화에 지수 함수적 민감도를 나타냅니다.
- 연구의 학술적 의의:
- 이 연구는 HPDC Al-Si 합금 엔진 블록에서 주요 미세 구조 특징(SDAS, 공정 Si 입자 특성)과 기계적 특성(UTS, 파단 연신율) 간의 정량적 데이터와 상관관계를 제공합니다.
- 응고 조건과 미세 구조가 다이캐스트 알루미늄 부품의 성능에 미치는 영향에 대한 이해를 높입니다.
- 이 연구는 HPDC 부품에서 기계적 특성을 최적화하기 위해 응고 속도와 미세 구조를 제어하는 것의 중요성을 강조합니다.
- 실무적 시사점:
- 이 연구 결과는 엔진 블록 및 유사 부품에서 원하는 미세 구조 및 기계적 특성을 달성하기 위해 HPDC 공정 변수(예: 다이 온도, 사출 속도, 냉각 전략)의 최적화를 안내할 수 있습니다.
- 공정 제어를 통해 SDAS 및 공정 Si 입자 특성을 제어하면 Al-Si 다이캐스트 엔진 블록의 신뢰성과 성능을 향상시킬 수 있습니다.
- 확립된 상관관계는 미세 구조 분석을 기반으로 기계적 특성의 품질 관리 및 예측에 사용할 수 있습니다.
- 연구의 한계점:
- 이 연구는 특정 HPDC 엔진 블록 설계 및 합금 조성에 초점을 맞추었습니다.
- 상관관계 분석은 유의미하지만 HPDC 부품의 고유한 결함과 개별 미세 구조 효과를 분리하는 복잡성으로 인해 데이터에 약간의 산포가 나타납니다.
- 이 연구는 주로 SDAS와 공정 Si 입자를 고려했지만 다른 미세 구조 특징과 결함도 기계적 특성 변화에 기여할 수 있습니다.
7. 향후 후속 연구:
- 후속 연구 방향:
- 기공률, 금속간 화합물 및 결정립 크기와 같은 다른 미세 구조 특징이 기계적 특성에 미치는 영향에 대한 추가 조사.
- 특정 HPDC 공정 변수가 미세 구조 진화 및 기계적 특성 변화에 미치는 영향에 대한 상세 분석.
- HPDC Al-Si 합금에 대한 공정 변수, 미세 구조 및 기계적 성능을 연결하는 예측 모델 개발.
- 다이캐스트 부품의 품질 평가를 위한 고급 미세 구조 특성 분석 기술 및 비파괴 검사 방법 탐색.
- HPDC 엔진 블록에서 미세 구조와 관련된 피로 및 파괴 거동 연구.
- 추가 탐구가 필요한 영역:
- 다양한 합금 원소의 역할과 HPDC Al-Si 합금의 미세 구조 및 기계적 특성에 미치는 영향.
- 다이캐스트 엔진 블록의 성능을 더욱 향상시키기 위한 합금 조성 및 열처리 전략 최적화.
- 이러한 연구 결과를 다른 복잡한 HPDC 부품 및 산업에 적용.
8. 참고문헌:
[1] Colás, R., A. Rodríguez, J. Talamantes, and S. Valtierra. Solidification analysis of aluminium engine block. Int. J. Cast Metals Res., 17 (2004), 332-338.
[2] Verran, G.O., R.P.K. Mendes and M.A. Rossi. Influence of injection parameters on defects formation in die casting Al12Si1,3Cu alloy: experimental results and numeric simulation. J. Mater. Process Technol., 179 (2006), 190-195.
[3] Avalle, M., G. Bellingardi, M.P. Cavatorta and R. Doglione. Casting defects and fatigue strength of a die cast aluminium alloy: a comparison between standard specimens and production components. Int. J. Fatigue 24 (2002), 1-9.
[4] Timelli, G. and F. Bonollo. Quality mapping of aluminium alloy diecastings. Metal. Sci. Tech., 26 (2008), 2-8.
[5] Shabestari, S.G. and F. Shari. Influence of modification, solidification conditions and heat treatment on the microstructure and mechanical properties of A356 aluminum alloy. J. Mater. Sci., 39 (2004), 2023-2032.
[6] Viswanathan, S., A.J. Duncan, S.A. Sabau, Q. Han, W.D. Porter and B.W. Riemer. Modeling of Solidification and Porosity in Aluminum Alloy Castings. AFS Transactions, 98-103 (1998), 411-417.
[7] Rontó, V. and A. Roósz. The effect of the cooling rate or the local solidification time and composition on the secondary dendrite arm spacing during solidification Part II: Al-Mg-Si alloys. Int. J. Cast Metals Res., 13 (2001), 337-342.
[8] Grosselle, F., G. Timelli, F. Bonollo, A. Tiziani and E. Della Corte. Correlation between microstructure and mechanical properties of Al-Si cast alloys. Metall. Ital., 6 (2009), 25-32.
[9] Chen, Z.W. Skin solidification during high pressure die casting of Al-11 Si-2 Cu-1Fe alloy. Mater. Sci. Eng., A348 (2003), 145-153.
[10] Ye, H. An overview of the development of Al-Si alloy based material for engine applications. J. Mater. Eng. Perf., 12(3) (2003), 288-297.
[11] Samuel, F.H., A.M. Samuel and H.W. Doty. Factors controlling the type and morphology of Cu-containing phases in 319 Al alloy. AFS Trans., 104 (1996), 893-901.
[12] Νίυ, Χ.P, B.H. Hu and S.W. Hao. Effect of iron on the microstructure and mechanical properties of Al die-casting alloys. J. Mater. Sci. Letters, 17 (1998), 1727-1729
[13] Wang, Q.G. and C.H. Cáceres. Fracture mode in Al-Si-Mg casting alloys. Mater. Sci. Eng, A241 (1998), 72-82
[14] Wang, Q.G., C.H. Cáceres and J.R. Griffiths. Damage by eutectic particle cracking in aluminum casting alloys A356/357. Metall. Mater. Trans. A, 34 (2003), 2901-2912
[15] Cáceres, C.H. and J.R. Griffiths. Damage by the cracking of silicon particles in an Al-7Si-0.4Mg casting alloy. Acta Mater. 44 (1996), 25-33.
[16] Cáceres, C.H. and B.I. Selling. Casting defects and the tensile properties of an Al-Si-Mg alloy. Mater. Sci. Eng., A220 (1996), 109-116.
[17] Gokhale, A.M. and G.R. Patel. Origins of Variability in the fracture related mechanical properties of a tilt-pour-permanent-mold cast Al-alloy. Scripta Mater., 52 (2004), 237-241.
[18] Shankar, S. and D. Apelian. Die soldering: Mechanism of the interface reaction between molten aluminum alloy and tool steel. Mater. Trans., 33B (2002), 465-476.
[19] Jorstad, J.L. Understanding "Sludge". Die Casting Eng., November/December (1986), 30-36.
[20] Ghomashchi, M.R. Intermetallic compounds in an Al-Si Alloy used in high pressure diecasting. Z. Metallkunde, 78 (1987), 784-787.
[21] Seifeddine, S., T. Sjögren and I.L. Svensson. Variations in microstructure and mechanical properties of cast aluminium EN AC 43100 alloy. Proc. High Tech Die Casting, AIM, (2006), Vicenza.
[22] Zovi, A. and F. Casarotto. Silafont-36, the low iron ductile die casting alloy development and applications. Metall. Ital. 6 (2007), vol., 33-38.
[23] Asensio-Lozano, J. and B. Suárez-Peña. Microstructure-properties correlation of pressure die cast eutectic aluminum-silicon alloys for escalator steps (Part I). Mater. Characterization, 56 (2006), 169-177.
[24] Mondolfo, L.F. Manganese in Aluminum Alloys. The Manganese Center, (1978).
[25] Μο, Α., M. M'Handi and H.I. Laukly. Modelling defect bend formation in Al-Si die casting. Proc. High Tech Die Casting, AIM, (2006), Vicenza.
9. 저작권:
- 본 자료는 파비오 그로셀레, 줄리오 티멜리, 프랑코 보놀로, 로베르토 몰리나의 논문: Al-Si 다이캐스트 엔진 블록의 미세 구조와 기계적 특성 간의 상관관계을 기반으로 작성되었습니다.
- 논문 출처: https://www.metallurgical.org.rs/uploads/editor/files/Metals_and_Technology/Vol_27_2/Grosselle.pdf
본 자료는 위 논문을 바탕으로 요약 작성되었으며, 상업적 목적으로 무단 사용이 금지됩니다.
Copyright © 2025 CASTMAN. All rights reserved.