이 소개 논문은 "DAAAM International Scientific Book 2015"에 발표된 "A Critical Review of Friction Stir Welding Process" 논문을 바탕으로 합니다.
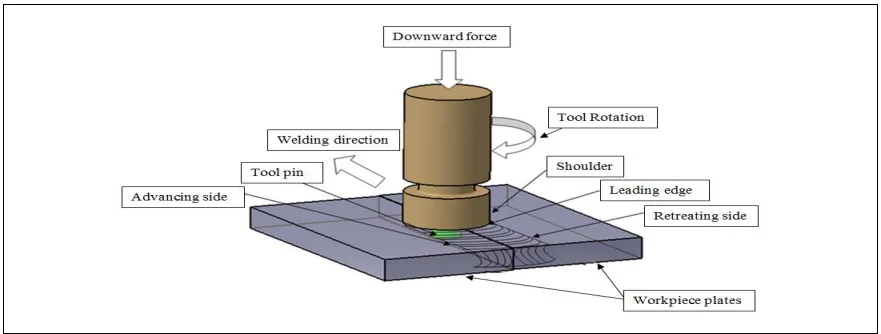
1. 개요:
- 제목: A Critical Review of Friction Stir Welding Process
- 저자: Verma, S. M. & Misra, J.P.
- 발표년도: 2015
- 발표 학술지/학회: DAAAM International Scientific Book 2015
- 키워드: Solid-state welding, friction stir welding, preheating, quenching, nano-particle inclusion
2. 초록:
마찰교반용접(FSW)은 항공우주, 해양, 우주선, 자동차 등 제조업에서 서로 다른 금속합금과 비금속을 접합하는 데 급속히 증가하고 있는 영구적인 고체상태 접합공정입니다. 현재 상황에서 금속합금의 용접은 융접공정 대비 고유한 특징들, 즉 기공결함 감소, 열영향부(HAZ) 감소, 보호가스 불필요, 환경친화적, 변형 감소 등으로 인해 FSW로 대체되고 있습니다. 이 장에서는 마찰교반용접의 핵심 측면들인 공정원리, 야금학적 및 기계적 특성, 예열 및 나노입자 첨가의 효과에 대한 비판적 평가가 논의되었습니다. FSW와 관련된 어려움과 기타 문제들도 이 분야에서 광범위한 연구를 수행할 수 있도록 전 세계 연구 커뮤니티에 가이드라인을 제공하기 위해 다루어졌습니다.
3. 서론:
용접 산업은 19세기 이후 크게 발전했으며, 초기에는 융접 기술이 주를 이루었습니다. 그러나 융접은 넓은 열영향부, 응고결함, 기계적 특성 저하 등의 문제를 제시합니다. 특히 알루미늄 및 마그네슘과 같은 반응성 원소에 대해서는 전통적인 융접 방법의 한계로 인해 고체상태 용접 기술, 특히 마찰교반용접(FSW)의 개발이 필요했습니다. FSW는 1991년 The Welding Institute(TWI)의 Wayne Thomas와 동료들에 의해 발명되었으며, 모재를 용융시키지 않고도 90% 결함 없는 접합부를 생성합니다. 이 기술은 우주선 제조에서 접합강도를 30%~50% 증가시키고 제조시간을 23일에서 6일로 단축시키는 것으로 입증되어 FSW를 녹색기술로 확립했습니다.
4. 연구 요약:
연구 주제의 배경:
전통적인 융접 기술은 넓은 열영향부, 응고결함, 변형, 기계적 특성 감소 등의 한계를 겪고 있습니다. 이러한 문제들은 높은 강도 대 중량비로 인해 항공우주, 해양, 자동차 산업에서 점점 더 많이 사용되는 알루미늄 및 마그네슘 합금과 같은 반응성 원소를 용접할 때 특히 두드러집니다.
기존 연구 현황:
논문은 다양한 재료에 걸친 FSW에 대한 광범위한 연구를 검토하며, 연구의 76%가 알루미늄 합금에 집중되어 있고, 15%가 강철, 6%가 마그네슘, 3%가 구리에 대한 것입니다. 연구는 공구 형상 효과, 공정변수 최적화, 미세구조 분석, 다양한 합금 시스템에서의 기계적 특성 평가 등 다양한 측면을 다루었습니다.
연구 목적:
이 연구는 마찰교반용접 공정에 대한 포괄적이고 비판적인 검토를 제공하고, 공정원리, 야금학적 및 기계적 측면, 예열 및 나노입자 첨가의 효과를 다루며, 이 분야의 미래 연구를 안내하기 위해 현재 연구의 공백을 식별하는 것을 목표로 합니다.
핵심 연구:
논문은 알루미늄 합금, 강철, 구리, 마그네슘, 이종금속을 포함한 다양한 재료 범주에 걸친 FSW 연구를 체계적으로 검토하고, 공정변수, 공구 형상 효과, 미세구조 변화, 기계적 특성을 분석합니다.
5. 연구 방법론
연구 설계:
이 연구는 포괄적인 문헌 검토 방법론을 사용하여, 1991년 FSW 발명부터 2015년까지 발표된 FSW 연구를 체계적으로 분석합니다.
데이터 수집 및 분석 방법:
저자들은 다양한 학술지와 학회에서 연구논문을 수집하고 분석하여, 재료 유형, 공정변수, 연구 초점 영역별로 분류했습니다. "Fig. 5.Comparative study of published research work on FSW"에 나타난 바와 같이 비교 분석이 수행되었습니다.
연구 주제 및 범위:
검토는 알루미늄 합금(2xxx, 5xxx, 6xxx, 7xxx, 8xxx 시리즈), 강철, 구리, 마그네슘, 티타늄, 플라스틱, 이종금속 조합을 포함한 다양한 재료에서의 FSW 적용과 나노입자 첨가 및 예열 효과와 같은 고급 주제를 다룹니다.
6. 주요 결과:
주요 결과:
검토 결과 FSW는 융접 대비 우수한 기계적 특성을 생산하며, 접합부가 향상된 인장강도, 연성, 피로, 파괴인성을 나타내는 것으로 확인되었습니다. 공구 회전속도, 이송속도, 스핀들 기울기 각도를 포함한 공정변수가 접합품질에 크게 영향을 미칩니다. 공구 형상, 특히 핀과 숄더 설계는 재료 흐름과 열 생성에 중요한 역할을 합니다. 논문은 또한 예열과 나노입자 첨가가 접합 특성을 더욱 향상시킬 수 있는 잠재력을 강조합니다.
그림 목록:
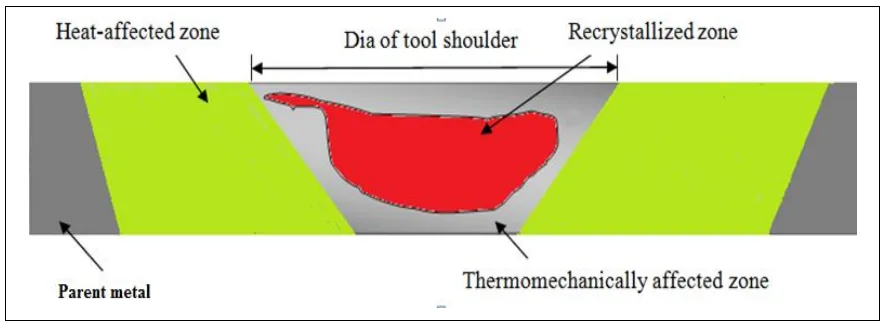
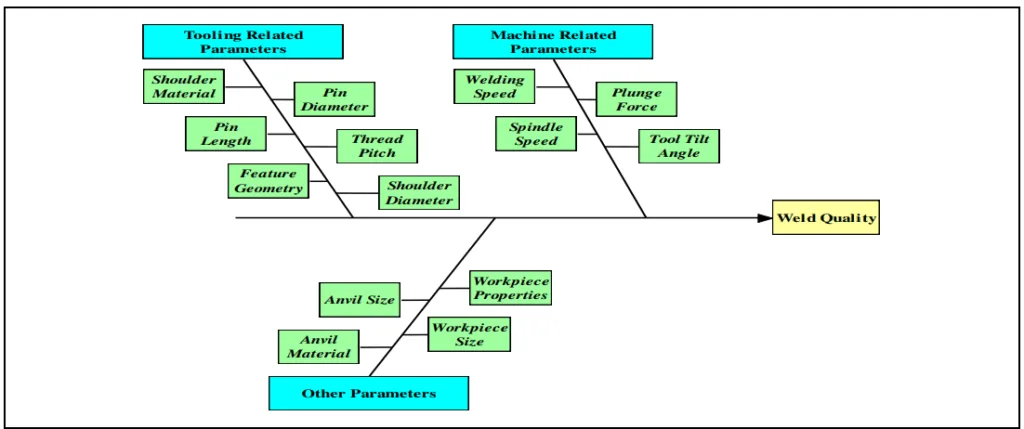
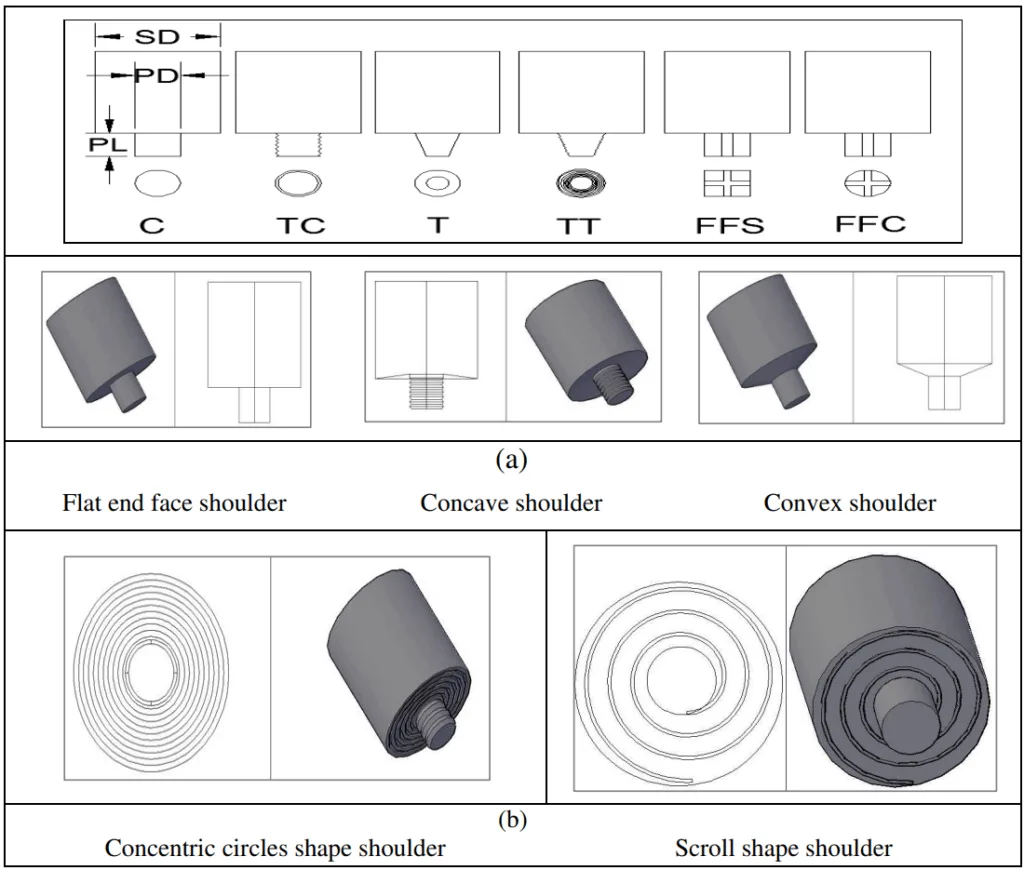
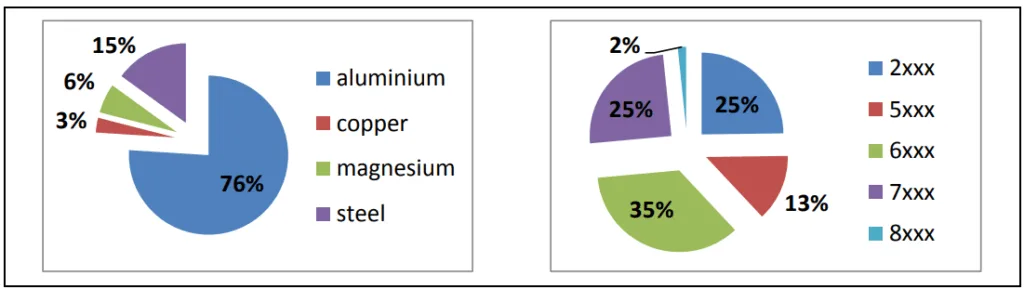
- Fig. 1. Principle of friction stir welding (Backer and Bolmsjo, 2014)
- Fig. 2. Microstructural regions of friction stir welding (Mahoney et al., 1998)
- Fig. 3. Cause and effect diagram for friction stir welding process
- Fig. 4. (a) FSW tool with different pin geometry (C: Cylindrical; TC: Threaded cylindrical; T: Tapered; TT: Threaded taper; FFS: Four flute square; FFC: Four flute cylindrical)(b) FSW tools with different shoulder geometry
- Fig. 5.Comparative study of published research work on FSW
7. 결론:
FSW는 낮은 변형, 아크 및 용가재 불필요, 감소된 HAZ, 스패터 및 기공결함으로부터의 자유로움 등 고유한 특성으로 인해 융접의 우수한 대안으로 나타납니다. 이 공정은 알루미늄, 마그네슘, 구리, 강철, 아연, 니켈 합금, 플라스틱을 포함한 동종 또는 이종 금속 접합에 적합합니다. 그러나 복합재료의 FSW, 공정변수 상호작용의 상세한 연구, 마찰학적 거동 분석, 공정 최적화를 위한 수학적 모델 개발 등 여러 영역에서 추가 연구가 필요합니다.
8. 참고문헌:
[논문은 Al-jarrah et al. (2014)부터 Zhou et al. (2015)까지 알파벳순으로 나열된 89개의 참고문헌을 포함하며, 다양한 국제 학술지와 학회의 FSW 관련 포괄적인 연구를 다룹니다]
9. 저작권:
- 이 자료는 "Verma, S. M. & Misra, J.P."의 논문입니다. "A Critical Review of Friction Stir Welding Process"를 바탕으로 합니다.
- 논문 출처: DOI: 10.2507/daaam.scibook.2015.22 이 자료는 위 논문을 바탕으로 요약된 것이며, 상업적 목적의 무단 사용을 금지합니다. Copyright © 2025 CASTMAN. All rights reserved.
논문 요약:
이 포괄적인 리뷰 논문은 전통적인 융접 방법의 한계를 해결하는 혁신적인 고체상태 접합기술인 마찰교반용접(FSW)을 검토합니다. 저자들은 1991년부터 2015년까지의 연구 발전을 체계적으로 분석하여 공정원리, 재료 적용, 기술적 진보를 다룹니다. 논문은 FSW가 결함 감소, 기계적 특성 향상, 환경적 이점 등 상당한 장점을 제공하면서도 향후 연구가 필요한 주요 연구 공백을 식별한다는 것을 보여줍니다.
연구에 관한 핵심 질문과 답변:
Q1. 마찰교반용접이 전통적인 융접공정에 비해 갖는 주요 장점은 무엇인가요?
A1. "A Critical Review of Friction Stir Welding Process"에 따르면, FSW는 기공결함 감소, 열영향부(HAZ) 감소, 보호가스 불필요, 환경친화적 특성, 융접공정 대비 변형 감소 등의 고유한 특성을 제공합니다.
Q2. FSW 적용에서 가장 광범위하게 연구된 재료는 무엇인가요?
A2. 논문의 "Fig. 5.Comparative study of published research work on FSW"를 기반으로, 산업적 응용과 융접 시 겪는 어려움으로 인해 연구 작업의 76%가 알루미늄에 집중되어 있으며, 이어서 강철 15%, 마그네슘 6%, 구리 3% 순입니다.
Q3. FSW 중에 형성되는 주요 미세구조 영역은 무엇인가요?
A3. "Fig. 2. Microstructural regions of friction stir welding (Mahoney et al., 1998)"에 나타난 바와 같이, FSW 접합부는 네 개의 뚜렷한 영역을 포함합니다: 모재(영향받지 않음), 열영향부(HAZ), 열기계적영향부(TMAZ), 그리고 너겟부 또는 교반부(완전 재결정화부).
Q4. 공구 형상이 FSW 공정 성능에 어떤 영향을 미치나요?
A4. "A Critical Review of Friction Stir Welding Process"의 연구방법론 섹션에 따르면, "Fig. 4"에 나타난 바와 같이 FSW 공구 형상, 특히 핀과 숄더 설계는 교반되는 재료의 양과 마찰열 생성을 조절하여 건전한 용접부를 얻는 결정적인 요소가 됩니다.
Q5. 예열이 FSW 접합품질 향상에 어떤 역할을 하나요?
A5. 논문의 3.6절에서 언급된 바와 같이, 예열은 재료를 연화시키고 교반부에서 재료 흐름을 증가시켜 용접력을 감소시키고 효율성을 향상시키며, FSW 접합부가 기존 FSW 대비 8% 강도 증가를 보이고 공구 마모를 줄여 공구 수명을 연장시킵니다.
Q6. 향후 FSW 연구를 위해 식별된 주요 연구 공백은 무엇인가요?
A6. "A Critical Review of Friction Stir Welding Process"의 결론 섹션에서는 주목이 필요한 여러 영역을 식별합니다: 합금, 플라스틱, 복합재료에 대한 제한적 연구; 공정변수 상호작용에 대한 불충분한 연구; 재료 흐름 메커니즘과 공구 설계에 대한 부적절한 이해; 그리고 공정 최적화를 위한 수학적 모델의 부족.