마찰교반용접(FSW)을 통한 구리-스테인리스강 이종 접합부의 국소 물성 평가: 고체 상태 용접의 잠재력과 그 한계 분석
이 기술 브리핑은 S. Ramachandran 외 저자가 발표한 학술 논문 "A combined full-field imaging and metallography approach to assess the local properties of friction stir welded (FSW) copper-stainless steel joints"를 기반으로 합니다. 이 내용은 고압 다이캐스팅(HPDC) 및 금속 접합 전문가를 위해 CASTMAN의 전문가 팀이 요약하고 분석했습니다.
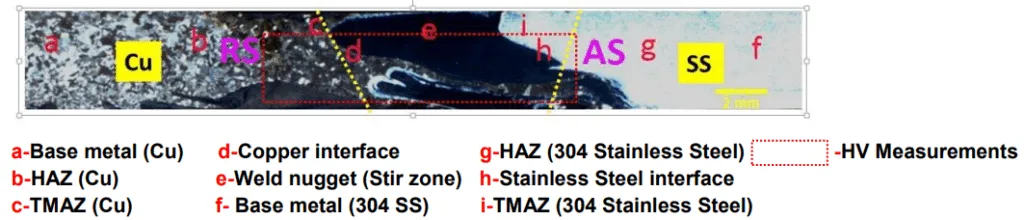
키워드
- Primary Keyword: 마찰교반용접(FSW)
- Secondary Keywords: 구리-스테인리스강 접합, 이종 금속 용접, 미세조직 분석, 미세경도, DIC(디지털 이미지 상관법), TSA(열탄성 응력 분석)
Executive Summary
- 도전 과제: 구리(Cu)와 스테인리스강(SS)은 녹는점, 열전도율 등 물리적 특성 차이가 커 기존의 융합 용접 방식으로는 결함 없는 고품질 접합이 매우 어렵습니다.
- 연구 방법: 고체 상태 용접 기술인 마찰교반용접(FSW)을 사용하여 2mm 두께의 구리와 304 스테인리스강 판재를 접합했습니다. 이후 EBSD, SEM, 광학 현미경, 미세경도 매핑, DIC, TSA 등 다양한 분석 기법을 동원해 용접부의 국소적 특성을 종합적으로 평가했습니다.
- 핵심 발견: FSW는 모재를 녹이지 않고 성공적으로 두 이종 금속을 접합했으며, 용접 너겟(weld nugget) 내부에 구리와 스테인리스강이 혼합된 복잡한 미세조직을 형성했습니다. 이로 인해 용접부 전반에 걸쳐 경도 분포가 매우 불균일하게 나타났습니다.
- 결론: 마찰교반용접은 기존 융합 용접의 한계를 극복하고 구리와 스테인리스강 같은 이종 재료를 접합할 수 있는 효과적인 대안이 될 수 있음을 입증했습니다.
도전 과제: 왜 이 연구가 금속 가공 전문가에게 중요한가?
엔지니어링 현장에서 서로 다른 특성을 가진 재료를 접합해야 하는 경우는 매우 흔합니다. 특히 높은 열전도성이 필요한 구리와 우수한 강도 및 내식성을 지닌 스테인리스강의 접합은 많은 산업 분야에서 요구되는 기술입니다. 하지만 두 재료는 물리적 특성에서 극명한 차이를 보입니다. 구리의 녹는점은 약 1085°C인 반면, 스테인리스강은 1400°C 이상입니다. 또한 구리의 열전도율은 스테인리스강보다 10배 이상 높아, 융합 용접 시 한쪽 재료만 먼저 녹거나 열이 급격히 분산되어 용접 자체가 어려워지는 문제가 발생합니다.
이러한 문제들은 금속간 화합물 형성, 기공, 고온 균열과 같은 심각한 결함으로 이어져 접합부의 기계적 특성을 저하시키고 최종 제품의 조기 파손을 유발합니다(Ref. [1]). 따라서 이러한 이종 금속을 안정적으로 접합하기 위한 새로운 공정 기술의 필요성이 꾸준히 제기되어 왔습니다.
연구 접근법: 방법론 분석
이 연구는 기존 융합 용접의 한계를 극복하기 위해 '고체 상태' 용접 방식인 마찰교반용접(FSW)을 채택했습니다. FSW는 재료를 녹이는 대신, 회전하는 툴(tool)의 마찰열과 강력한 기계적 교반 작용을 이용해 재료를 연화시키고 소성 변형을 통해 접합하는 기술입니다(Ref. [2]).
연구팀은 2mm 두께의 구리(Cu)와 304 스테인리스강(SS) 시트를 FSW 공법으로 접합했습니다. 이후 접합부의 특성을 정밀하게 분석하기 위해 다음과 같은 최신 분석 기법들을 총동원했습니다.
- 금속 조직 분석: EBSD(후방산란전자회절), SEM(주사전자현미경), 광학 현미경을 사용하여 용접부의 미세조직 변화를 관찰했습니다.
- 기계적 특성 평가: 미세경도 매핑을 통해 용접 영역 전반의 경도 분포를 2D 등고선 맵으로 시각화했습니다.
- 변형 및 응력 분석: DIC(디지털 이미지 상관법)와 TSA(열탄성 응력 분석)를 활용하여 인장 하중 시 용접부의 변형 및 응력 재분배를 평가할 준비를 마쳤습니다.
핵심 발견: 주요 결과 및 데이터
- 결과 1: 뚜렷하게 구분되는 용접 영역 형성
Fig. 1에서 볼 수 있듯이, FSW 접합부는 모재(BM), 열영향부(HAZ), 열-기계적 영향부(TMAZ), 그리고 용접 너겟(교반 영역)으로 명확하게 구분되는 미세조직 영역을 형성했습니다. 이는 FSW 공정 중 각 위치가 겪는 열과 기계적 변형의 정도가 다르기 때문입니다. - 결과 2: 용접 너겟 내부의 불균일한 경도 분포
Fig. 2의 2D 미세경도 등고선 맵은 이 연구의 가장 흥미로운 결과 중 하나입니다. 용접 너겟(SZ, Stir Zone) 내부에서 경도 값이 급격하게 변동하는 것을 확인할 수 있습니다. 이는 FSW 툴의 교반 작용으로 인해 경도가 낮은 구리(HV 85-95)와 경도가 높은 스테인리스강(HV 250-280)이 물리적으로 혼합되었기 때문입니다. - 결과 3: 영역별 미세조직의 현저한 차이
Fig. 3의 광학 현미경 사진은 각 영역의 미세조직 차이를 명확히 보여줍니다. 용접 너겟(Fig. 3(c))에서는 미세한 재결정립이 관찰되었고, 구리 측 열영향부(HAZ, Fig. 3(d))와 스테인리스강 측 열영향부(HAZ, Fig. 3(e))는 각각의 모재(Fig. 3(a), (b))와 비교하여 결정립 크기에 상당한 변화를 보였습니다. 이러한 미세조직의 이질성은 FSW 접합부의 복합적인 기계적 거동을 유발하는 주요 원인입니다(Ref. [3]).
귀사의 운영을 위한 실질적 시사점
이 연구 결과는 단순한 학술적 발견을 넘어, 실제 산업 현장에서 다음과 같은 중요한 시사점을 제공합니다.
- 공정 엔지니어: 구리-스테인리스강과 같이 열적으로 매우 다른 재료를 접합해야 할 때, FSW는 고온 균열이나 기공과 같은 융합 용접의 고질적인 문제를 피할 수 있는 강력한 대안이 될 수 있습니다. 이는 제품의 신뢰성을 높이는 데 직접적으로 기여할 수 있습니다.
- 품질 관리: Fig. 2의 미세경도 매핑과 Fig. 3의 미세조직 분석은 FSW 접합부의 품질을 정량적으로 평가하고 관리하는 효과적인 지표를 제공합니다. 용접 너겟의 혼합 정도와 각 영역의 조직적 건전성을 확인함으로써 최종 제품의 성능을 예측하고 보증할 수 있습니다.
- 설계 엔지니어: FSW를 통해 구리의 높은 열/전기 전도성과 스테인리스강의 우수한 기계적 강도 및 내식성을 하나의 부품에서 동시에 구현할 수 있게 됩니다. 이는 전기차 배터리 케이스, 방열판, 전자 부품 등 혁신적인 제품 설계의 가능성을 열어줍니다.
논문 상세 정보
A combined full-field imaging and metallography approach to assess the local properties of friction stir welded (FSW) copper-stainless steel joints
1. 개요:
- 제목: A combined full-field imaging and metallography approach to assess the local properties of friction stir welded (FSW) copper-stainless steel joints
- 저자: S. Ramachandran, J.M. Dulieu-Barton, P.A.S. Reed, A.K.Lakshminarayanan
- 발행 연도: (명시되지 않음)
- 학술지/학회: (명시되지 않음)
- 키워드: FSW, Cu, SS, DIC, TSA, Metallography, Microhardness, local properties
2. 초록:
마찰교반용접(FSW) 공정을 사용하여 2mm 두께의 구리(Cu)와 304 스테인리스강(SS) 시트를 접합했습니다. 용접부의 국소적 재료 형태를 규명하기 위해 EBSD, SEM, 광학 현미경 등 다양한 금속 조직 분석 기법이 사용되었습니다. 이러한 기법들을 통해 용접부의 다양한 미세조직 특징(열영향부(HAZ), 열-기계적 영향부(TMAZ), 용접 너겟)이 확인되었습니다. Cu-SS 접합부의 미세경도 변화를 매핑하여 다양한 영역에 걸친 경도 분포를 분석했습니다. 디지털 이미지 상관법(DIC)과 열탄성 응력 분석(TSA)은 용접부의 기계적 특성과 응력 재분배를 평가하는 데 사용되었습니다.
3. 서론 요약:
이종 재료를 용접할 때, 특히 녹는점과 같은 물리적 특성의 큰 차이는 문제를 일으킬 수 있습니다. 융합 용접 공정 중 한 재료가 다른 재료보다 훨씬 먼저 녹는점이 도달하는 경우가 그 예입니다. 그 결과 금속간 화합물, 기공, 고온 균열, 응고 균열과 같은 결함이 형성됩니다[1]. 따라서 이종 재료 용접 조인트는 기계적 특성이 저하되고 사용 중 조기 파손을 겪는 경우가 많습니다. 구리와 스테인리스강과 같은 이종 재료의 특성을 맞춤화하기 위해서는 적절한 용접 공정이 정의되어야 하지만, 녹는점(Cu-1085°C, SS-1400-1500°C), 열전도율(Cu-401 W/m-K, SS-17-19 W/m-K), 결정 구조(Cu-FCC, SS-BCC 또는 FCC) 등 특성의 큰 차이로 인해 용접 작업이 어렵습니다. FSW는 모재의 용융을 포함하지 않는 "고체 상태" 용접 공정으로, 융합 용접 공정의 많은 단점을 제거합니다[2].
4. 연구 요약:
연구 주제의 배경:
구리와 스테인리스강은 녹는점, 열전도율, 결정 구조 등 물리적 특성이 매우 달라 기존의 융합 용접 방식으로는 고품질의 접합이 어렵습니다. 이러한 문제를 해결하기 위해 고체 상태에서 접합이 이루어지는 마찰교반용접(FSW) 기술의 적용 가능성을 탐구할 필요가 있습니다.
이전 연구 현황:
기존의 융합 용접 방식은 이종 금속 접합 시 금속간 화합물, 기공, 균열 등 다양한 결함을 유발하는 것으로 알려져 있습니다[1]. FSW는 이러한 결함을 피할 수 있는 잠재력을 가진 기술로 연구되고 있습니다[2].
연구 목적:
본 연구의 목적은 FSW를 사용하여 구리와 304 스테인리스강을 접합하고, 결합된 전체 필드 이미징 및 금속 조직학적 접근법을 통해 접합부의 국소적 특성(미세조직, 경도, 기계적 거동)을 종합적으로 평가하는 것입니다.
핵심 연구:
2mm 두께의 구리와 304 스테인리스강을 FSW로 접합한 후, 접합부 단면을 따라 다양한 분석을 수행했습니다. 광학 현미경, SEM, EBSD를 통해 미세조직을 관찰하고, 미세경도 시험을 통해 경도 분포를 2D 맵으로 작성했습니다. 이를 통해 FSW로 생성된 이종 접합부의 복잡하고 이질적인 특성을 규명하고자 했습니다.
5. 연구 방법론
연구 설계:
2mm 두께의 구리(Cu)와 304 스테인리스강(SS) 판재를 맞대기(butt joint) 형태로 배치하고 마찰교반용접을 수행했습니다. 용접된 시편의 단면을 채취하여 분석을 위한 시료를 준비했습니다.
데이터 수집 및 분석 방법:
- 금속 조직 분석: EBSD, SEM, 광학 현미경을 사용하여 용접부의 각 영역(모재, HAZ, TMAZ, 너겟)에서 미세조직을 관찰했습니다.
- 미세경도 측정: 비커스 경도 시험기를 사용하여 용접부 단면을 가로지르는 넓은 영역에 걸쳐 5행 x 84열, 총 420개의 압흔을 생성하여 미세경도 값을 측정하고 2D 등고선 맵을 작성했습니다.
- 기계적 거동 분석 (향후 계획): DIC와 TSA를 사용하여 인장 시험 중 용접부의 변형률 및 응력 분포를 측정할 계획입니다.
연구 주제 및 범위:
본 연구는 FSW로 제작된 구리-스테인리스강 이종 접합부의 국소적 특성 평가에 초점을 맞춥니다. 연구 범위는 미세조직 분석, 경도 분포 매핑, 그리고 향후 진행될 기계적 특성 평가를 포함합니다.
6. 주요 결과:
주요 결과:
FSW를 통해 구리와 스테인리스강의 성공적인 접합이 가능했습니다. 접합부는 뚜렷한 미세조직 영역(HAZ, TMAZ, 너겟)으로 구성되었습니다. 특히 용접 너겟은 구리와 스테인리스강이 혼합된 복합 구조를 보였으며, 이로 인해 경도 값이 크게 변동하는 불균일한 특성을 나타냈습니다. HAZ 영역에서는 모재와 비교하여 결정립 크기의 변화가 관찰되었습니다.
Figure 이름 목록:
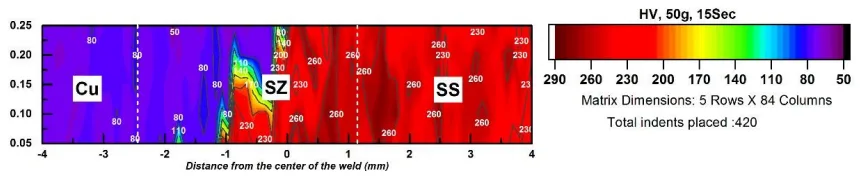
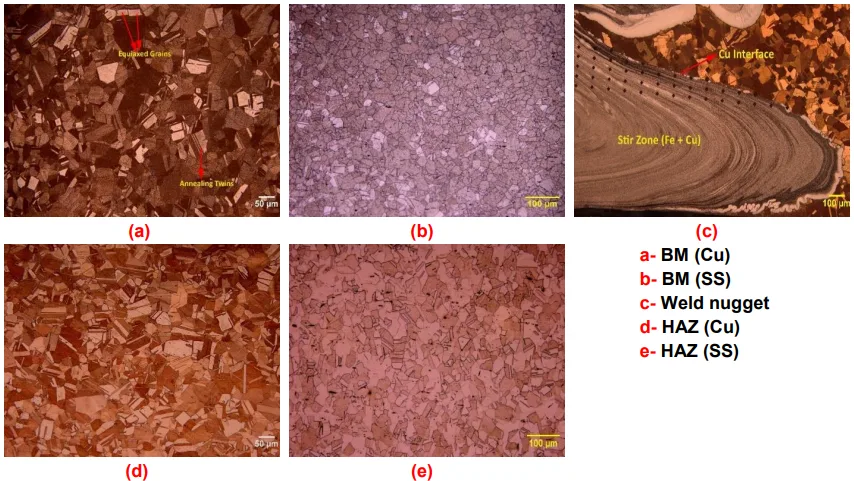
- Fig. 1 Macrostructure along a transverse section of the friction stir welded Cu-SS joint
- Fig. 2 Microhardness 2D-contour map of Cu-SS FSW joint over the region shown in Fig. 1
- Fig. 3 Microstructures at different zones of the friction stir welded Cu-SS Joint
7. 결론:
본 연구는 FSW 공정을 통해 구리와 스테인리스강 이종 금속을 성공적으로 접합하고, 그 결과 생성된 접합부의 복잡한 미세조직과 경도 분포를 규명했습니다. 용접 너겟은 구리와 스테인리스강의 혼합물로 구성되어 큰 경도 변동을 보였습니다. 이러한 결과는 FSW가 융합 용접의 한계를 극복할 수 있는 유망한 기술임을 보여주며, 접합부의 이질적인 특성이 기계적 성능에 미치는 영향을 이해하는 데 중요한 기초 자료를 제공합니다. 향후 DIC 및 TSA를 이용한 추가 연구를 통해 용접부의 응력 분포 및 기계적 거동을 심도 있게 평가할 예정입니다.
8. 참고 문헌:
- 1. http://nhml.com/weld-discrepancies/
- 2. Bhadeshia, H.K.D.H. & Debroy, T., 2009. Critical assessment: friction stir welding of steels. Science and Technology of Welding and Joining, 14(3), pp. 193-196.
- 3. Lockwood, W.D. & Reynolds, A.P., 2003. Simulation of the global response of a friction stir weld using local constitutive behaviour. Materials Science and Engineering A, 339(1-2), pp.35-42.
결론 및 다음 단계
이 연구는 이종 금속 접합이라는 까다로운 과제를 해결하는 데 있어 마찰교반용접(FSW) 기술의 가치와 잠재력을 명확하게 보여줍니다. 연구 결과는 품질을 개선하고 결함을 줄이며 생산을 최적화하기 위한 데이터 기반의 명확한 경로를 제공합니다.
CASTMAN은 고압 다이캐스팅 분야의 선두주자로서, 고객의 가장 어려운 제조 문제를 해결하기 위해 최신 산업 연구를 적용하는 데 전념하고 있습니다. 본 보고서에서 논의된 이종 재료 접합 문제가 귀사의 운영 목표와 관련이 있다면, 저희 엔지니어링 팀에 연락하여 귀사의 부품에 이러한 첨단 원리를 어떻게 적용할 수 있는지 논의해 보십시오.
전문가 Q&A: 자주 묻는 질문에 대한 답변
(참고: 모든 답변은 제공된 논문의 특정 내용을 근거로 합니다.)
Q1: 이 연구에서 구리와 스테인리스강 접합에 FSW를 사용한 가장 큰 이점은 무엇이었습니까?
A1: 가장 큰 이점은 FSW가 재료를 녹이지 않는 '고체 상태' 공정이라는 점입니다. 논문의 Introduction
섹션에 명시된 바와 같이, 이를 통해 융합 용접에서 흔히 발생하는 금속간 화합물, 기공, 균열과 같은 결함을 원천적으로 방지할 수 있습니다.
Q2: 용접 너겟(weld nugget)의 미세구조는 어떻게 구성되어 있습니까?
A2: Experimental work
섹션의 설명과 Fig. 2의 경도 맵에서 알 수 있듯이, 용접 너겟은 FSW 툴의 강력한 교반 작용으로 인해 구리(Cu)와 스테인리스강(SS)이 물리적으로 혼합된 복합 구조를 가집니다.
Q3: 이 연구에서 접합부의 특성을 평가하기 위해 어떤 분석 기법들이 사용되었습니까?
A3: Abstract
와 Experimental work
섹션에 따르면, 연구팀은 EBSD, SEM, 광학 현미경과 같은 금속 조직 분석 기법과 함께 미세경도 매핑, 그리고 향후 연구를 위한 DIC 및 TSA를 사용했습니다.
Q4: 이 연구의 향후 계획은 무엇입니까?
A4: 논문의 Future work
섹션에 명시된 바와 같이, 연구팀은 고해상도 DIC와 TSA를 사용하여 단축 인장 하중을 받는 시편의 기계적 특성과 응력 분포를 정량적으로 평가할 계획입니다.
Q5: 용접 너겟에서 경도 변동이 크게 나타나는 이유는 무엇입니까?
A5: Experimental work
섹션 마지막 부분에서 설명하듯이, 이는 경도가 매우 다른 두 재료, 즉 부드러운 구리(HV 85-95)와 단단한 스테인리스강(HV 250-280)이 혼합되어 있기 때문입니다.
Q6: 이 논문이 엔지니어에게 주는 가장 직접적이고 실용적인 교훈은 무엇입니까?
A6: 논문 "[Paper Title]"의 전반적인 결과가 강력하게 뒷받침하듯이, 핵심 교훈은 FSW가 물리적 특성이 극명하게 다른 재료들을 효과적으로 접합할 수 있는 매우 유용한 기술이라는 점입니다. 이는 많은 산업 분야에서 직면하는 설계 및 제조상의 난제를 해결할 새로운 가능성을 제시합니다.
저작권
- 이 자료는 S. Ramachandran 외 저자의 논문 "[Paper Title]"을 분석한 것입니다.
- 논문 출처: (명시되지 않음)
- 본 자료는 정보 제공 목적으로만 사용됩니다. 무단 상업적 사용을 금합니다.
- Copyright © 2025 CASTMAN. All rights reserved.