이 기술 브리프는 Piyush Shukla가 International Journal for Multidisciplinary Research (IJFMR)에 발표한 학술 논문 "Process Selection on the Basis of Time Cost and Quality for Development Components of Aluminium Bracket" (2024)을 기반으로 합니다. 이 내용은 고압 다이캐스팅(HPDC) 전문가를 위해 CASTMAN의 전문가들이 요약하고 분석했습니다.
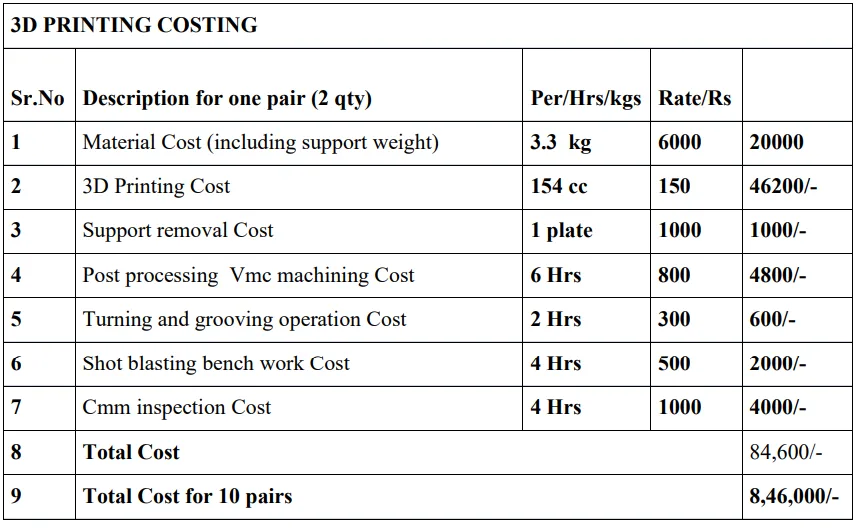
키워드
- 주요 키워드: 알루미늄 부품 프로토타입 공정 선택
- 보조 키워드: 프로토 다이캐스팅(Proto Die Casting), 3D 프린팅, VMC 머시닝, 개발 비용 절감, 알루미늄 브라켓, 품질 비교, 개발 시간 단축
핵심 요약
- 과제: 양산 금형 제작 전, 조립성 검증 및 시운전을 위한 소량(10~20개)의 알루미늄 프로토타입 부품을 제작할 때 시간, 비용, 품질을 모두 만족시키는 최적의 공정을 선택하는 것은 엔지니어들의 오랜 고민입니다.
- 연구 방법: 본 연구에서는 자동차용 알루미늄 브라켓을 대상으로 ① 3D 프린팅(DMLS), ② VMC 머시닝, ③ 소프트 툴을 이용한 프로토 다이캐스팅(Proto DCD)의 세 가지 공정을 적용하여 부품을 제작하고, 각각의 시간, 비용, 품질(치수 정밀도, 재료 특성)을 정량적으로 비교 분석했습니다.
- 핵심 발견: 단 한두 개의 시제품 제작에는 3D 프린팅이 유용하지만, 조립 라인 테스트에 필요한 10개 이상의 수량에서는 프로토 다이캐스팅이 3D 프린팅 대비 55% 이상 비용을 절감하면서도 양산품에 가장 가까운 재료 특성을 확보할 수 있는 가장 효율적인 공정임이 입증되었습니다.
- 결론: 시운전 및 검증 수량의 프로토타입 제작 시, 초기 비용과 시간, 최종 품질을 종합적으로 고려할 때 프로토 다이캐스팅은 3D 프린팅과 VMC 머시닝을 능가하는 강력한 대안이 될 수 있습니다.
과제: 왜 이 연구가 HPDC 전문가에게 중요한가?
신제품 개발 과정에서 양산을 위한 고가의 본 금형을 제작하기 전에 부품의 설계 타당성과 조립성을 검증하는 것은 필수적입니다. 특히 자동차 산업과 같이 높은 신뢰성이 요구되는 분야에서 알루미늄 브라켓과 같은 부품의 프로토타입은 최종 제품의 성패를 좌우할 수 있습니다.
기존에는 VMC 가공이나 최근 각광받는 3D 프린팅이 프로토타입 제작에 주로 사용되었습니다. 하지만 VMC 가공은 재료 손실이 크고 복잡한 형상 구현에 한계가 있으며, 3D 프린팅은 소량 제작에는 빠르지만 수량이 늘어날수록 비용이 기하급수적으로 증가하고 양산품과 동일한 재료 물성을 구현하기 어렵다는 단점이 있습니다. 본 연구는 바로 이 지점에서 "조립 검증을 위한 10개 이상의 프로토타입을 가장 효율적으로 제작하는 방법은 무엇인가?"라는 업계의 실질적인 질문에 대한 해답을 제시합니다.
접근 방식: 연구 방법론 분석
연구진은 이 문제를 해결하기 위해 실제 자동차용 알루미늄 브라켓을 대상으로 세 가지 다른 제조 공정을 통해 프로토타입을 제작하고 그 결과를 비교하는 실증적 접근법을 채택했습니다.
- 3D 프린팅: 직접 금속 레이저 소결(DMLS) 방식을 사용하여 AlSi10Mg 분말로 부품을 적층 제조했습니다.
- VMC 머시닝: Al6061 솔리드 블록을 5축 VMC(Vertical Machining Center)를 이용해 절삭 가공하여 부품을 제작했습니다.
- 프로토 다이캐스팅 (Proto DCD): 열처리 및 표면 코팅을 생략한 연질(soft condition)의 코어와 캐비티를 사용한 '소프트 툴' 금형을 제작하여 다이캐스팅으로 부품을 생산했습니다. 이는 양산 금형의 구조를 유지하면서 제작 시간과 비용을 크게 단축시키는 방법입니다.
각 공정으로 제작된 시제품에 대해 CMM(3차원 측정기)을 이용한 치수 정밀도 측정, 재료 성분 분석, 경도 및 인장 강도 테스트를 수행하여 시간, 비용, 품질이라는 세 가지 핵심 지표를 종합적으로 평가했습니다.
핵심 발견: 주요 결과 및 데이터
이 연구는 각 공정의 장단점을 명확히 보여주는 구체적인 데이터를 제시합니다. 특히 10쌍(20개)의 브라켓을 제작하는 시나리오에서 그 차이가 두드러졌습니다.
비용 비교 (10쌍 기준): 프로토 다이캐스팅이 375,900 INR로 가장 경제적이었습니다. VMC 머시닝은 398,300 INR로 근소하게 높았으나, 3D 프린팅은 850,000 INR로 프로토 다이캐스팅 대비 2배 이상 높은 비용이 발생했습니다. 이는 시운전 물량 제작 시 3D 프린팅의 경제성이 급격히 떨어진다는 것을 의미합니다. (Source: Table 2.2)
시간 비교 (10쌍 기준): 3D 프린팅이 15일로 가장 빨랐으며, 프로토 다이캐스팅과 VMC 머시닝은 각각 17일이 소요되어 큰 차이를 보이지 않았습니다. 이는 프로토 다이캐스팅이 소프트 툴을 사용함으로써 금형 제작 기간을 획기적으로 단축했기 때문입니다. (Source: Table 2.2)품질 비교:
- 치수 정밀도: 세 공정 모두 도면 공차를 만족하는 우수한 치수 정밀도를 보여주었습니다. (Source: Table 2.0)
- 재료 특성: 여기서 가장 큰 차이가 발생했습니다. VMC 머시닝으로 제작된 부품(Al6061)은 경도(81 HB)가 낮았고, 3D 프린팅 부품(AlSi10Mg)은 경도(121 HB)가 너무 높았습니다. 반면, 프로토 다이캐스팅 부품은 목표 범위인 95-100 HB에 완벽하게 부합하는 97 HB의 경도를 기록하며 양산품에 가장 근접한 기계적 특성을 보였습니다. (Source: Table 2.2)
HPDC 제품을 위한 실질적인 시사점
이 연구 결과는 실제 다이캐스팅 생산 현장의 엔지니어, 품질 관리자, 설계자에게 다음과 같은 중요한 시사점을 제공합니다.
공정 엔지니어: 10개 이상의 프로토타입이 필요하다면, 3D 프린팅 대신 프로토 다이캐스팅을 고려하는 것이 비용 효율성을 극대화하는 전략이 될 수 있습니다. 특히 "Proto Tool Costing Summary and Time Schedule" (p.14-15) 섹션의 데이터는 이러한 의사결정에 직접적인 근거를 제공합니다.
품질 관리: 최종 양산품과의 물성 일치성이 중요하다면 프로토 다이캐스팅이 가장 신뢰할 수 있는 선택입니다. Table 2.1과 Table 2.2에서 볼 수 있듯이, 프로토 다이캐스팅은 경도와 기계적 강도 측면에서 양산품의 특성을 가장 잘 예측하게 해줍니다. 이는 조립 및 성능 테스트 결과의 신뢰도를 높여줍니다.
금형 설계: 프로토 다이캐스팅은 양산 금형의 구조(예: 게이트, 러너, 냉각 채널)를 거의 그대로 적용하여 제작되므로, 프로토타입 단계에서 금형의 유동 및 응고 특성을 미리 검증해볼 수 있는 기회를 제공합니다. 이는 양산 금형 제작 시 발생할 수 있는 잠재적 문제를 사전에 파악하고 수정하여 최종 금형의 완성도를 높이는 데 기여할 수 있습니다.
논문 상세 정보
Process Selection on the Basis of Time Cost and Quality for Development Components of Aluminium Bracket
1. 개요:
- 제목: Process Selection on the Basis of Time Cost and Quality for Development Components of Aluminium Bracket
- 저자: Piyush Shukla
- 발행 연도: 2024
- 학술지/학회: International Journal for Multidisciplinary Research (IJFMR)
- 키워드: Process Selection, Time, Cost, Quality, Aluminium Bracket, Proto DCD, 3D printing, VMC machining
2. 초록:
다양한 신규 공정의 개발로 인해 다이캐스팅 금형을 이용한 양산 전 알루미늄 부품 설계 시 툴링 개발이 감소했습니다. 프로토 품질의 알루미늄을 제조하기 위한 공정 선택은 중요하지 않습니다. 본 연구는 한두 개의 프로토타이핑 수량으로는 충분하기 때문에, 소프트 컨디션의 다이캐스팅 다이 또한 알루미늄 부품의 시운전 수량을 위한 권장 공정임을 입증하려는 시도입니다. 프로토 DCD 공정은 시간, 비용, 품질 매개변수와도 비교되며, 이 기준에 따라 최대 1,000개 수량 요구사항에 대해서만 공정을 선택할 수 있습니다.
3. 서론:
신제품 개발 시, 조립 부품의 타당성 검토나 제품 조립의 시험적 시운전을 위한 제조 공정 선택은 일부 기계 엔지니어에게 중요한 역할을 합니다. 공정 선택은 설계 과정에서 그들이 마지막으로 생각하는 것입니다. 최선의 접근 방식은 전체 설계 과정 동안 제조 관련 문제를 염두에 두는 것입니다. 이는 더 쉽고 비용 효율적으로 생산할 수 있는 설계로 이어질 것입니다. 주조 및 기계 가공과 같은 가장 일반적인 제조 공정은 이미 익숙할 것입니다. 주어진 제품에 대해 선택해야 할 여러 제조 공정이 있을 것이며, 선택하는 공정은 공정 선택 동인이라고 불리는 많은 요인에 따라 달라집니다.
4. 연구 요약:
연구 주제의 배경:
신제품 개발, 특히 자동차 부품과 같은 복잡한 조립품의 경우, 양산에 들어가기 전 프로토타입을 통해 설계의 타당성을 검증하는 단계가 필수적입니다. 이 단계에서 어떤 제조 공정을 선택하느냐에 따라 개발 시간, 비용, 그리고 최종 제품의 품질이 크게 달라질 수 있습니다.
기존 연구 현황:
과거에는 주로 VMC 머시닝을 통해 프로토타입을 제작했으나, 최근에는 3D 프린팅 기술이 빠른 제작 시간 덕분에 주목받고 있습니다. 하지만 각 공정의 장단점은 명확하며, 특히 소량(예: 10~1,000개)의 시운전용 부품 제작에 대한 시간, 비용, 품질을 종합적으로 비교 분석한 연구는 드물었습니다. 특히 소프트 툴을 이용한 프로토 다이캐스팅(Proto DCD)을 다른 공정들과 직접 비교한 연구는 거의 없었습니다.
연구 목적:
본 연구의 목적은 ① 시간, ② 비용, ③ 품질이라는 세 가지 핵심 매개변수를 기준으로, 1개 이상의 프로토타입 수량에 대해 어떤 제조 공정이 가장 적합한지 비교하는 것입니다. 특히, 경화된 금형 대신 소프트 코어/캐비티를 사용하는 프로토 다이캐스팅의 효율성을 입증하고, 최소 20개의 시운전용 부품이 필요한 경우에 대한 최적의 공정을 찾는 것을 목표로 합니다.
핵심 연구:
연구의 핵심은 자동차용 알루미늄 브라켓을 대상으로 다음 세 가지 공정을 실제로 수행하고 그 결과를 비교 분석하는 것입니다.
1. 3D 프린팅 (DMLS): 금속 분말을 이용한 적층 가공
2. VMC 머시닝: 솔리드 블록을 이용한 절삭 가공
3. 프로토 다이캐스팅 (Proto DCD): 소프트 툴을 이용한 다이캐스팅
각 공정별로 부품 10쌍(20개)을 제작하는 데 소요되는 총 시간과 비용을 상세히 산출하고, 제작된 부품의 치수 정밀도(CMM 측정)와 재료 특성(성분, 경도, 강도 등)을 비교하여 어떤 공정이 가장 균형 잡힌 결과를 제공하는지 실증적으로 분석했습니다.
5. 연구 방법론
연구 설계:
본 연구는 실제 자동차용 알루미늄 브라켓(재질: AlSi10Mg)을 대상으로 세 가지 다른 제조 공정(3D 프린팅, VMC 머시닝, 프로토 다이캐스팅)을 적용하여 프로토타입을 제작하고, 그 결과를 비교하는 실험적 연구 설계를 따랐습니다. 비교 기준은 시간, 비용, 품질로 설정되었습니다.
데이터 수집 및 분석 방법:
- 시간: 각 공정 단계별(예: 설계, 준비, 가공, 후처리, 검사) 소요 시간을 측정하여 10쌍의 부품을 제작하는 데 걸리는 총 시간을 계산했습니다. (Source: Table 1.2, 1.5, 1.9)
- 비용: 재료비, 장비 사용료, 인건비, 툴링 비용 등을 포함한 총 제작 비용을 각 공정별로 상세히 산출했습니다. (Source: Table on p.5, 7, 15)
- 품질:
- 치수 품질: CMM(3차원 측정기)을 사용하여 제작된 부품의 주요 치수 및 기하 공차를 측정하고 도면 값과 비교했습니다. (Source: Table 2.0)
- 재료 품질: 각 공정으로 제작된 샘플의 화학 성분, 브리넬 경도(HB), 인장 강도, 연신율 등을 측정하여 비교 분석했습니다. (Source: Table 2.1)
연구 주제 및 범위:
이 연구는 양산 전 개발 단계에서 필요한 시운전용 알루미늄 부품(최대 1,000개) 제작을 위한 최적의 공정 선택에 초점을 맞춥니다. 특히, 1~2개가 아닌 10개 이상의 프로토타입이 필요한 상황에서 3D 프린팅, VMC 머시닝, 그리고 프로토 다이캐스팅(Proto DCD)의 효율성을 비교하는 데 그 범위가 한정됩니다.
6. 주요 결과:
주요 결과:
연구 결과, 10쌍(20개)의 알루미늄 브라켓 프로토타입을 제작할 때, 프로토 다이캐스팅(Proto DCD)이 비용과 품질 측면에서 가장 우수한 공정으로 나타났습니다.
- 비용: 프로토 다이캐스팅(375,900 INR)이 3D 프린팅(850,000 INR)보다 약 55.8% 저렴했으며, VMC 머시닝(398,300 INR)보다도 경제적이었습니다.
- 시간: 3D 프린팅(15일)이 가장 빨랐으나, 프로토 다이캐스팅(17일)과 VMC 머시닝(17일)도 경쟁력 있는 제작 기간을 보였습니다.
- 품질: 모든 공정이 치수 공차를 만족했지만, 재료의 기계적 특성(특히 경도)에서 프로토 다이캐스팅(97 HB)이 양산품의 목표 범위(95-100 HB)에 가장 근접한 결과를 보여주어 테스트 신뢰도가 가장 높았습니다. VMC 머시닝(81 HB)은 너무 무르고, 3D 프린팅(121 HB)은 너무 단단했습니다.
Figure Name List:
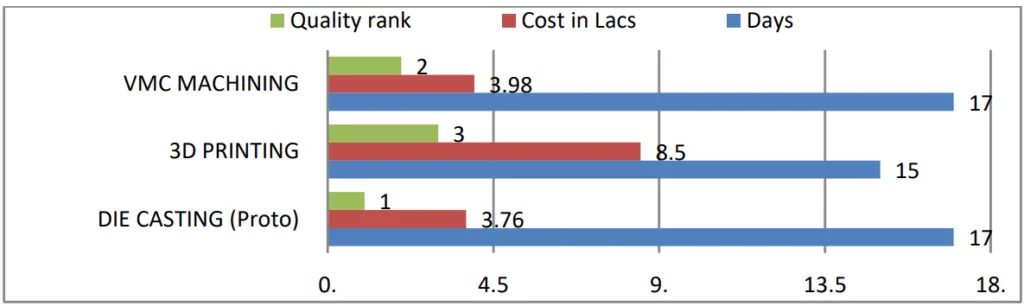
- Figure 2.2 Die casting machine
- Graph 1.3 Result chart.
7. 결론:
실험 결과, 3D 프린팅은 한두 개의 프로토타입을 제작하여 신속하게 형상을 확인하는 데는 적합했지만, 주조 VMC 및 프로토 다이캐스팅과 비교할 때 비용이 매우 높았습니다. VMC 머시닝 공정은 요구되는 재료 조성과 일치하지 않았습니다. 10개 샘플에 대한 프로토 다이캐스팅(소프트 다이) 툴 비용은 세 공정 중 가장 저렴했습니다. 최종적으로 양산 공정 또한 다이캐스팅이므로, 본 실험 연구를 통해 더 많은 비용과 시간을 절약할 수 있음이 보고되었습니다.
8. 참고 문헌:
- International Conference on Mechanical Engineering Research 2011 (ICMER2011) IOP Publishing IOP Conf. Series: Optimization of Process Parameters of CNC
- Characteristic Behaviour of Aluminium Metal Matrix Composites:A Review 2018 Prasanna Nagasai Bellamkondal, Srikanth Sudabathula2Mr. NISHANTH PATEL GM1, Dr. K G SATISH2b © 2020, IRJET | Impact Factor value: 7.34 | ISO 9001:2008 Certified Journal
- https://www.researchgate.net/publication/307446249ThermalFatigueofDie-CastingDiesAn_Overview
- https://www.researchgate.net/publication/257707301 Mechanical Properties of AlSi10Mg Produced by Selective Laser Melting Article in Physics Procedia · December 2012
- Experimental investigation into characterization and machining of Al + SiCp nano-composites using coated carbide tool https://ui.adsabs.harvard.edu/abs/2020MeInd..21 307S /abstract
- Pradyut Kumar Swain1,*, Kasinath Das Mohapatral, Ratnakar Das2, Ashok Kumar Sahoo3, and Amlana Panda3 February 2020
- https://ui.adsabs.harvard.edu/abs/2020MeInd..21..307S
- https://www.researchgate.net/publication/266863408 Quality Improvement Model At The Manufacturing Process Preparation Level Article in International Journal for Quality Research December 2009
- https://www.researchgate.net/publication/342349012 Application of die casting: Article January 2018
- Manufacturing Engineering and materials processing A Series of Reference Books and Textbooks Copyright © 2002 by Marcel Dekker, Inc.
- Mass Production Definition – Investopedia https://www.investopedia.com
- https://www.villageplastics.com/3d-printing processes,additive manufacturing(AM).
- 3D Printing - Keene Village Plastics
- https://www.bartleby.com/questions-and-answers/milling-is-the-process-of-machining-using-rotary-cutters-to-remove-material-by-advancing-a-cutter-in/9570b70c-47df-4e5f-a80d-0e51fa920073
- https://www.custompartnet.com/wu/die-casting
- Experimental investigation into characterization and machining of Al + SiCp nano-composites using coated carbide tool
- A Study on Wear and Microstructure Properties of AA7075 Reinforced with SiC MMC by Powder Metallurgy Technique © 2020, IRJET | Impact Factor value: 7.34
- Comparative study of Al6061 and AlSi10Mg produced by Selective Laser Melting Process
... (and so on for references 19-32)
전문가 Q&A: 가장 궁금한 질문에 대한 답변
Q1: 이 연구에서 품질, 비용, 시간을 종합했을 때 시운전용 부품 제작에 가장 중요한 단일 요소는 무엇이었습니까?
A1: 연구는 "제작 수량"이 가장 중요한 결정 요소임을 시사합니다. 한두 개의 부품에는 3D 프린팅이 유리할 수 있지만, 논문에서 집중적으로 분석한 10쌍(20개)의 시운전 수량에서는 프로토 다이캐스팅(Proto DCD)이 비용과 품질 면에서 가장 균형 잡힌 최적의 선택이었습니다. 이는 Table 2.2 Result values에 명확히 요약되어 있습니다.
Q2: 이 연구에서 제시된 프로토 다이캐스팅은 기존의 프로토타입 제작 방식과 어떻게 다른가요?
A2: 논문의 Introduction
과 Proto Tooling Die Casting Process
섹션에 따르면, 기존 방식인 VMC 머시닝이나 3D 프린팅과 달리 프로토 다이캐스팅은 양산 공정과 거의 동일한 방식으로 부품을 제작합니다. 차이점은 열처리 및 코팅을 생략한 '소프트 툴'을 사용하여 금형 제작 비용과 시간을 획기적으로 줄인다는 점입니다. 이로 인해 양산품과 가장 유사한 품질을 저렴한 비용으로 얻을 수 있습니다.
Q3: 이 연구 결과는 모든 알루미늄 합금에 적용될 수 있나요, 아니면 특정 합금에만 해당되나요?
A3: 본 연구는 Component Spacification
섹션에 명시된 바와 같이 주로 AlSi10Mg 합금을 사용하여 진행되었습니다. VMC 머시닝에는 Al6061이 사용되었습니다. 따라서 결과는 이들 합금에 가장 직접적으로 적용됩니다. 다른 합금에 대한 적용 가능성은 추가적인 연구가 필요할 수 있습니다.
Q4: 연구진은 품질을 평가하기 위해 구체적으로 어떤 측정 기술을 사용했습니까?
A4: 연구진은 Geometrical Dimention Comparision
섹션에서 설명하듯이, CMM(3차원 측정기)을 사용하여 부품의 치수 및 기하 공차를 정밀하게 측정했습니다. 또한, Material Comparision
섹션에서는 재료의 화학 성분 분석, 브리넬 경도 시험기, 인장 강도 시험기 등을 사용하여 기계적 물성을 평가했습니다.
Q5: 논문에 따르면, 이 연구의 한계점이나 향후 연구 분야는 무엇인가요?
A5: 논문의 Future Scope
섹션에서는 프로토 다이(Proto Die)를 추가 수정하여 더 많은 수량(예: 5,000개) 생산 후 하드 인서트로 교체하면 10만 쇼트 이상의 정규 다이캐스팅 금형으로도 활용할 수 있는 가능성을 제시합니다. 이는 프로토 툴의 활용 범위를 확장하는 향후 연구 방향을 시사합니다.
Q6: 이 논문이 다이캐스팅 시설에 주는 직접적이고 실용적인 교훈은 무엇입니까?
A6: 핵심 교훈은 조립성 검증 등을 위해 10개 이상의 프로토타입이 필요할 경우, 무조건 3D 프린팅을 선택하기보다 프로토 다이캐스팅(Proto DCD)을 적극적으로 검토해야 한다는 것입니다. 이를 통해 최종 제품과 유사한 품질을 확보하면서도 개발 비용과 시간을 크게 절감할 수 있다는 점이 논문 "Process Selection on the Basis of Time Cost and Quality for Development Components of Aluminium Bracket"의 전반적인 결과가 강력하게 뒷받침하는 결론입니다.
결론 및 다음 단계
본 연구는 HPDC 공정에서 프로토타입 제작 단계의 효율성을 높이는 귀중한 로드맵을 제공합니다. 연구 결과는 품질을 개선하고, 결함을 줄이며, 생산을 최적화하기 위한 명확하고 데이터에 기반한 경로를 제시합니다.
CASTMAN은 최신 산업 연구를 적용하여 고객의 가장 까다로운 다이캐스팅 문제를 해결하는 데 전념하고 있습니다. 이 백서에서 논의된 문제가 귀사의 운영 목표와 관련이 있다면, 저희 엔지니어링 팀에 연락하여 이러한 고급 원칙을 귀사의 부품에 어떻게 구현할 수 있는지 논의해 보십시오.
저작권
- 이 자료는 "Piyush Shukla"의 논문 "Process Selection on the Basis of Time Cost and Quality for Development Components of Aluminium Bracket"을 기반으로 작성되었습니다.
- 논문 출처: International Journal for Multidisciplinary Research (IJFMR), Volume 6, Issue 4, July-August 2024
이 자료는 정보 제공 목적으로만 사용됩니다. 무단 상업적 사용을 금지합니다.
Copyright © 2025 CASTMAN. All rights reserved.