이 기술 요약 자료는 M.C. Carter, S. Palit, M. Littler가 NADCA(2010)에 발표한 학술 논문 "Characterizing Flow Losses Occurring in Air Vents and Ejector Pins in High Pressure Die Castings"를 기반으로 작성되었습니다. 다이캐스팅 전문가를 위해 CASTMAN의 전문가들이 Gemini, ChatGPT, Grok과 같은 LLM AI의 도움을 받아 분석하고 요약했습니다.
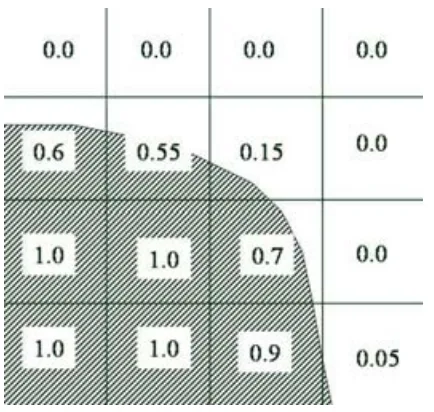
키워드
- 주요 키워드: HPDC 벤팅 시뮬레이션
- 보조 키워드: 유동 손실 계수, FLOW-3D 시뮬레이션, 가스 기공 감소, 이젝터 핀 벤팅, 다이캐스팅 결함, 단열 기포 모델, 전산 유체 역학 (CFD)
핵심 요약
- 과제: 고압 다이캐스팅(HPDC)에서 벤트, 이젝터 핀 및 기타 누출 경로를 통한 유동 손실은 단순 계산으로 정량화하기 어려워, 잔류 가스로 인한 기공을 정확하게 예측하고 제어하는 것은 매우 중요한 과제입니다.
- 연구 방법: 연구팀은 상용 금형을 이용한 물리적인 "공타(dry run)" 사출 실험과 전산 유체 역학(CFD) 소프트웨어인 FLOW-3D®를 사용한 시뮬레이션을 결합했습니다. 실제 금형 캐비티 내 압력 변화를 측정하고, 이 데이터를 사용하여 시뮬레이션의 유동 손실 계수를 보정했습니다.
- 핵심 성과: 본 연구는 FLOW-3D®의 단열 기포 모델(adiabatic bubble model)과 밸브 모델 같은 CFD 모델을 보정하여 벤트, 이젝터 핀, 금형의 잔류 누출로 인한 누적 유동 손실을 정확하게 재현할 수 있음을 성공적으로 입증했습니다.
- 결론: 이 연구는 엔지니어가 생산 전에 벤팅 전략을 시뮬레이션하고, 분석 및 최적화할 수 있는 강력하고 검증된 방법을 제공합니다. 이를 통해 가스 기공을 획기적으로 줄이고 더 높은 품질의 부품을 생산할 수 있습니다.
과제: 이 연구가 HPDC 전문가에게 중요한 이유
수십 년 동안 엔지니어들은 고압 다이캐스팅 부품의 표면 결함과 내부 기공 문제로 고심해 왔습니다. 항복 강도, 연성과 같은 기계적 특성을 저하시키는 이러한 결함은 주로 잔류 공기와 윤활유 분해 시 발생하는 가스 때문에 발생합니다. 진공 시스템이 하나의 해결책이 될 수 있지만, 비용이 많이 들고 공정을 복잡하게 만듭니다.
논문의 서론에서 언급했듯이, 벤팅은 잔류 공기를 제거하는 "가장 쉽고 저렴한 방법"으로 남아있습니다. 하지만 효과적인 벤팅 시스템을 설계하는 것은 결코 간단하지 않습니다. 총 배출량은 전용 벤트, 샷 슬리브, 이젝터 핀, 파팅 라인을 통한 유동의 복합적인 합계이기 때문입니다. 이러한 유동 손실을 신뢰성 있게 특성화하는 방법이 없다면, 엔지니어들은 종종 경험과 시행착오에 의존하게 되어 값비싼 금형 수정과 불안정한 부품 품질로 이어집니다. 본 연구는 이러한 중요한 유동 손실을 모델링하기 위한 실용적이고 정확한 방법을 모색함으로써 이 근본적인 문제를 정면으로 다루고 있습니다.
연구 방법: 연구 방법론 분석
이 문제를 해결하기 위해 연구원들은 물리적 실험과 첨단 시뮬레이션을 결합한 독창적인 방법론을 고안했습니다. 그들은 Littler DieCast에서 모터 엔드 헤드용 상용 금형을 사용하여 용탕 없이 사출하는 "공타(dry run)" 실험을 수행했습니다.
실험의 핵심은 다음과 같습니다:
- 변수 분리: 모든 벤트 개방, 진공 밸브 폐쇄, 파팅 라인 밀폐, 이젝터 핀 밀폐, 모든 벤트 폐쇄 등 다양한 조건에서 금형을 작동시켰습니다.
- 데이터 수집: 금형 캐비티 내부에 압력 변환기를 설치하여 각 조건에 대한 시간 경과에 따른 압력 증가를 정밀하게 측정했습니다(Figure 3).
- CFD 시뮬레이션: 상용 CFD 소프트웨어인 FLOW-3D®를 사용하여 이러한 "공타" 시나리오를 재현했습니다. 핵심은 소프트웨어의 단열 기포 모델(adiabatic bubble model)을 사용하여 캐비티 내 공기를 표현하고, 밸브 모델(valve model)을 사용하여 다양한 오리피스를 통한 유동 손실을 나타내는 것이었습니다.
- 보정(Calibration): 최종 목표는 시뮬레이션의 압력 곡선이 실제 실험 데이터와 완벽하게 일치할 때까지 시뮬레이션의 "누적 손실 계수"를 조정하는 것이었습니다. 이 과정은 시뮬레이션을 효과적으로 보정하여 실제 금형의 벤팅 성능을 신뢰할 수 있는 디지털 트윈으로 만듭니다.
핵심 성과: 주요 연구 결과 및 데이터
이 연구는 HPDC의 벤팅에 대해 우리가 어떻게 생각해야 하는지에 직접적인 영향을 미치는 몇 가지 중요한 통찰력을 제시했습니다.
- 성과 1: 벤팅 경로의 정량화: Figure 3의 실험적 압력 곡선은 각 벤팅 경로의 상대적 중요성을 명확하게 보여주었습니다. 진공 밸브가 닫혔을 때 가장 큰 압력 상승이 발생하여, 진공 밸브가 주된 벤팅 경로임을 확인했습니다. 밀폐되지 않은 이젝터 핀으로 인한 더 작지만 여전히 중요한 압력 강하(2 Psi 미만)도 정량화되었습니다. 반대로, 파팅 라인은 잘 밀폐되어 압력에 미미한 영향을 미쳤습니다.
- 성과 2: 잔류 누출의 결정적 역할: "모두 폐쇄(All Closed)" 실험과 순수 이론적 시뮬레이션을 비교하면서 중대한 사실이 밝혀졌습니다. 시뮬레이션은 최종 압력을 169 psi로 예측했지만(Figure 5), 실제 실험에서는 약 25 psi에 불과했습니다(Figure 3). 이 엄청난 144 psi의 차이는 샷 슬리브를 통한 누출과 같이 종종 간과되지만 공기 배출에 중요한 역할을 하는 "잔류 누출"이 상당하다는 것을 보여줍니다.
- 성과 3: 시뮬레이션 정확도 검증: 본 연구는 보정된 FLOW-3D® 모델이 실험 결과를 정확하게 재현할 수 있음을 성공적으로 입증했습니다. Figure 6에서 보듯이, "진공 밸브 폐쇄(Vacuum Closed)"와 "모두 개방(All Open)" 사례에 대한 계산된 압력 곡선은 측정된 실험 데이터와 뛰어난 일치성을 보여, 이 방법이 신뢰할 수 있는 엔지니어링 도구임을 검증했습니다.
- 성과 4: 특정 손실 계수 결정: 보정 과정을 통해 연구원들은 정밀한 누적 손실 계수를 계산했습니다. 이젝터 핀과 잔류 누출을 통한 벤팅("진공 밸브 폐쇄") 시나리오의 계수는 3.73e-6 m²/√(kg/m³)였습니다. 모든 벤팅 경로가 결합된("모두 개방") 시나리오의 계수는 6.4e-6 m²/√(kg/m³)였습니다. 이 값들은 향후 시뮬레이션 작업에 강력한 데이터 포인트를 제공합니다.
HPDC 제품에 대한 실질적인 시사점
- 공정 엔지니어: 이 논문의 방법론은 추측을 넘어설 수 있는 길을 제시합니다. "결과 및 토론(RESULTS AND DISCUSSION)" 섹션에 자세히 설명된 바와 같이 각 금형 요소의 벤팅 기여도를 정량화함으로써, 과도한 시행착오 없이 완전한 공기 배출을 보장하기 위해 샷 프로파일과 증압을 보다 정밀하게 최적화할 수 있습니다.
- 품질 관리: 이론적인 "모두 폐쇄" 압력(Figure 3 대 Figure 5)과 실제 압력 사이의 상당한 격차는 잔류 누출이 중요하고 측정 가능한 요인임을 강조합니다. 이는 간단한 공타 압력 테스트가 금형 마모나 밀봉 상태를 평가하는 강력한 QC 검사로 구현될 수 있음을 시사하며, 용탕을 주입하기 전에 잠재적인 기공 문제를 예측할 수 있게 합니다.
- 금형 설계: 이 연구는 FLOW-3D®와 같은 도구를 사용하면 설계자가 강재를 가공하기 전에 벤팅 및 오버플로우 설계의 효과를 디지털 방식으로 테스트하고 확인할 수 있음을 입증합니다. 연구에서 보여준 것처럼 보정된 손실 계수를 할당함으로써, 제안된 설계가 적절한 벤팅을 제공하는지 시뮬레이션하여 값비싼 금형 재작업을 방지하고 신규 금형에 대한 학습 곡선을 크게 단축할 수 있습니다.
논문 상세 정보
Characterizing Flow Losses Occurring in Air Vents and Ejector Pins in High Pressure Die Castings
1. 개요:
- Title: Characterizing Flow Losses Occurring in Air Vents and Ejector Pins in High Pressure Die Castings
- Author: M.C. Carter, S. Palit, M. Littler
- Year of publication: 2010
- Journal/academic society of publication: NADCA (North American Die Casting Association)
- Keywords: HPDC, venting, flow loss, porosity, computational fluid dynamics, FLOW-3D, ejector pins, adiabatic bubble model
2. 초록 (Abstract):
It will be demonstrated how the commercial computational fluid dynamics (CFD) software, FLOW-3D®, can be used to model the flow losses occurring in ejector pins and air vents in high pressure die castings. The results from an ejection experiment done without melt at a commercial tool shop will be discussed. These results will then be used to compute flow loss coefficients for the air vents, ejector pins and residual leaks with the help of the adiabatic bubble model in FLOW-3D®. We will explore an effective tool for calibrating the losses that occur during a pressurized fill in high pressure die castings.
3. 서론 (Introduction):
Surface defects reduce thermal and mechanical properties such as yield strength, ductility and modulus of elasticity of parts produced in high pressure die casting. The surface defects occur due to air entrapment and/or solidification shrinkage. Entrapped gases during fill and the gases evolved during decomposition of lubricants, cause porosity. Vacuum die casting can eliminate these gases. Vacuum valves are expensive and there is a possibility of destroying the valve and/or pump if the valve is not closed before the metal leaves the shot sleeve. Moreover, an additional runner system needs to be adequately designed so that effective cooling and solidification occurs preventing the metal from entering the vacuum valve. If no vacuum is used then adequate venting along with proper gating and runner design can eliminate gas porosity. Venting helps eliminate entrapped air by allowing the gas to have an outlet during the fill. Venting is the easiest and least expensive method to use. The amount of venting through the sleeve, ejector pins, parting line, and vacuum valves are considered while designing vents.
4. 연구 요약:
연구 주제 배경:
고압 다이캐스팅 중 공기 혼입은 기공을 유발하여 최종 제품의 기계적 특성을 저하시킵니다. 벤팅은 이 공기를 제거하는 가장 일반적이고 비용 효율적인 방법이지만, 금형 내 다양한 오리피스를 통한 유동 손실에 대한 명확한 이해 없이는 효과적인 벤팅 시스템을 설계하기 어렵습니다.
이전 연구 현황:
유동 손실을 모델링하려는 이전 시도들은 Darcy-friction factor나 Moody's diagram과 같은 방법을 사용했는데, 이는 복잡하고 다이캐스팅 환경의 동역학을 완전히 포착하지 못할 수 있습니다.
연구 목적:
본 연구는 상용 CFD 소프트웨어(FLOW-3D®)를 사용하여 HPDC 금형의 에어 벤트, 이젝터 핀 및 잔류 누출로 인한 누적 유동 손실을 모델링하고 보정하는 실용적이고 효과적인 방법을 입증하는 것을 목표로 했습니다.
핵심 연구 내용:
연구의 핵심은 다양한 벤팅 조건 하에서 상용 금형으로 물리적인 "공타(dry run)" 사출 실험을 수행하는 것이었습니다. 캐비티 내부의 압력을 측정하고 이를 CFD 시뮬레이션 보정을 위한 벤치마크로 사용했습니다. 시뮬레이션된 압력 곡선을 실험 데이터와 일치시킴으로써 연구진은 전체 벤팅 시스템에 대한 정확한 누적 손실 계수를 결정할 수 있었습니다.
5. 연구 방법론
연구 설계:
본 연구는 CFD 시뮬레이션 결과를 물리적 실험 데이터와 비교하는 비교 연구 설계를 채택했습니다. 모터 엔드 헤드 금형을 사용하여 용탕 없이 사출 실험을 수행했습니다. 실험 구성에는 모든 벤트 개방, 진공 밸브 폐쇄, 파팅 라인 폐쇄, 이젝터 핀 및 파팅 라인 폐쇄, 모든 벤트 폐쇄가 포함되었습니다.
데이터 수집 및 분석 방법:
금형에 압력 변환기를 설치하여 각 실험 실행에 대한 시간 함수로서의 압력을 기록했습니다. 이 압력 곡선들을 FLOW-3D®의 시뮬레이션 출력과 비교했습니다. 소프트웨어의 밸브 모델은 계산 결과가 실험 데이터와 좋은 일치를 보일 때까지 누적 손실 계수를 조정하여 보정되었습니다.
연구 주제 및 범위:
본 연구는 고압 다이캐스팅 금형에서의 공기 유동 손실을 특성화하는 데 중점을 두었습니다. 범위에는 진공 밸브, 26개의 이젝터 핀, 파팅 라인 및 기타 잔류 누출을 통한 손실이 포함되었습니다. 연구는 FLOW-3D®의 단열 기포 모델과 밸브 모델을 사용하여 시뮬레이션을 수행했습니다.
6. 주요 결과:
주요 결과:
- 실험 데이터는 진공 밸브가 주된 벤팅 경로이며, 이젝터 핀이 그 뒤를 잇는다는 것을 보여주었습니다. 파팅 라인 누출은 미미했습니다.
- 이론적인 "모두 폐쇄" 압력(169 psi)과 측정된 실험 압력(~25 psi) 사이의 큰 불일치로 입증된 상당한 잔류 누출이 확인되었습니다.
- 단열 기포 모델을 사용한 FLOW-3D® 시뮬레이션은 일단 보정되자 실험적인 압력 곡선과 뛰어난 일치를 보였습니다.
- 특정 누적 손실 계수가 계산되었습니다: "진공 밸브 폐쇄"의 경우 3.73e-6 m²/√(kg/m³), "모두 개방"의 경우 6.4e-6 m²/√(kg/m³).
그림 이름 목록 (Figure Name List):
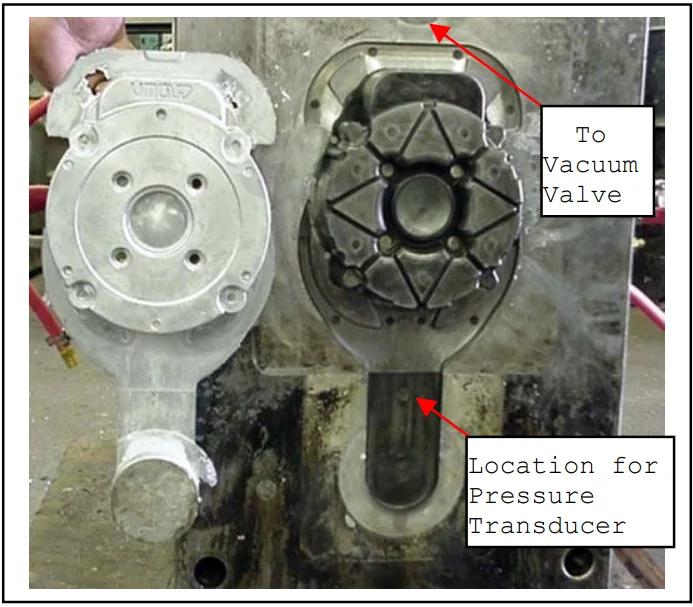
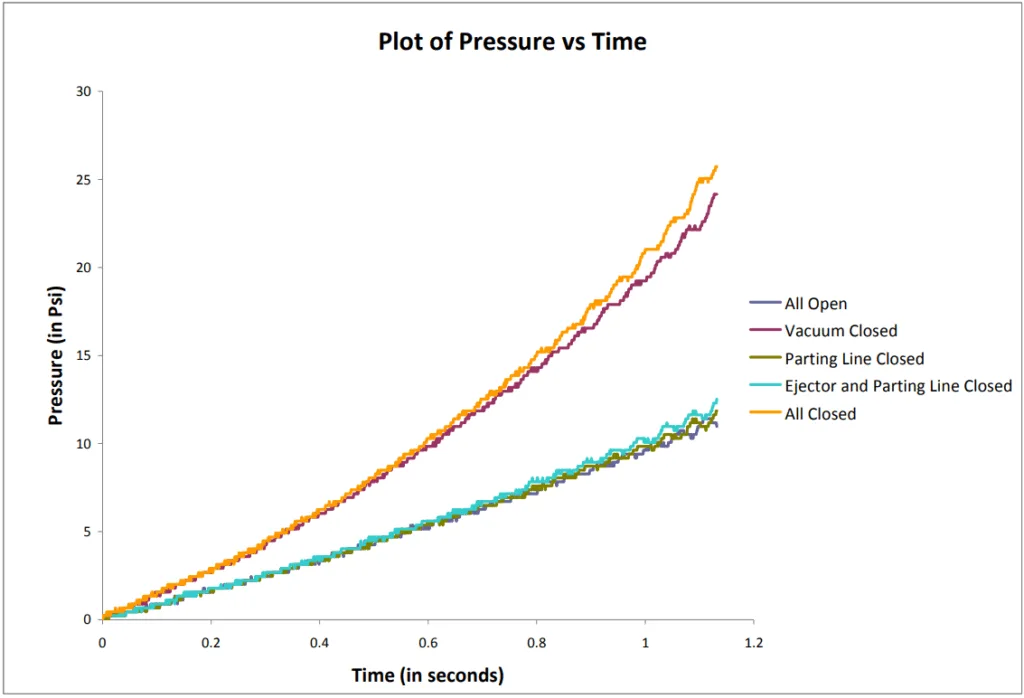
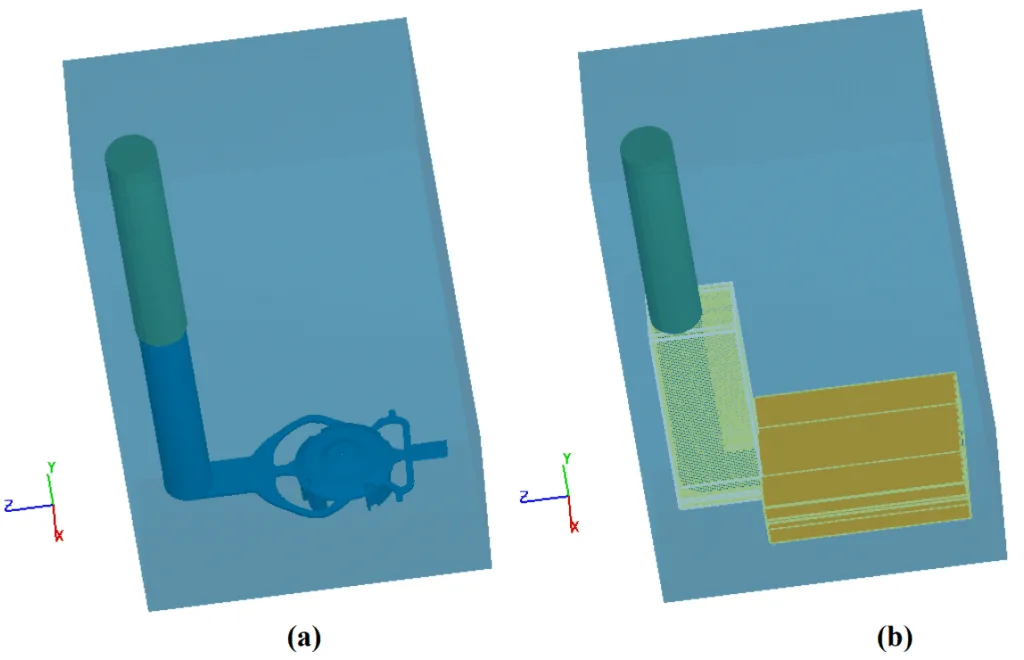
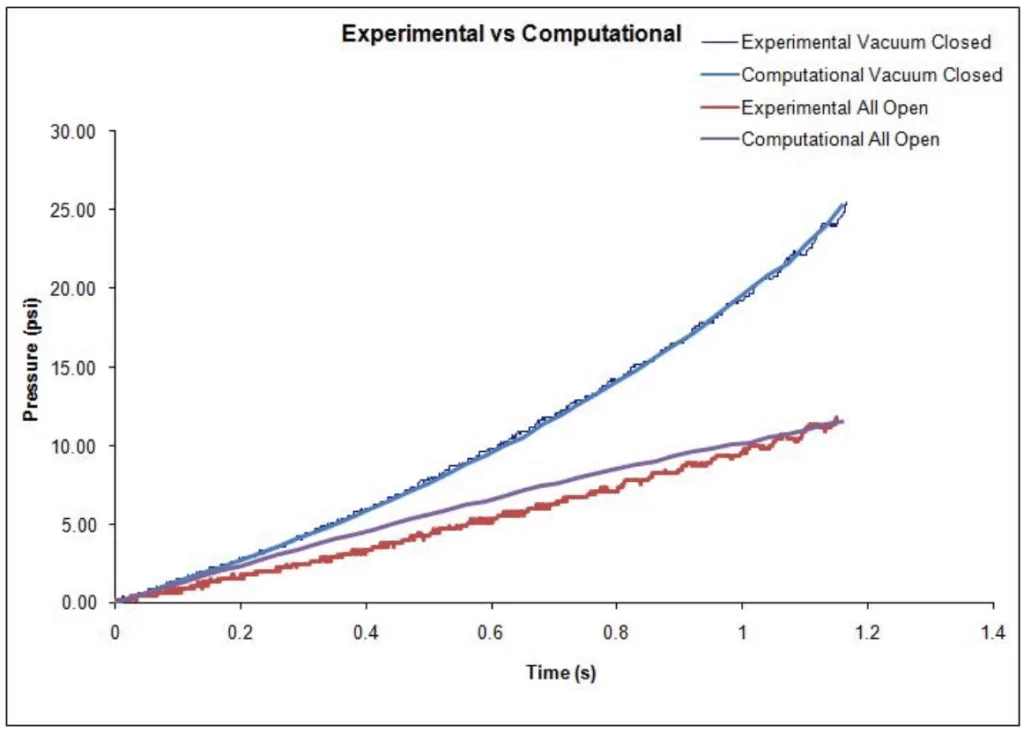
- Figure 1: Typical values of the VOF function near a moving metal front.
- Figure 2: The cast part (end head of motor) and the die.
- Figure 3: Experimental results of pressure (in Psi) plotted against time (in sec) for the dry runs.
- Figure 4: A snapshot of the geometry (a) without mesh and (b) with computational mesh.
- Figure 5: Pressure curves from the "All Closed" for 1-compressible and 2-adiabatic simulations.
- Figure 6: Comparison of experimental and computational results.
7. 결론 (Conclusion):
Many authors have tried to model the flow losses at vents using the Darcy-friction factor and Moody’s diagram and Fanno flows where compressibility effects are taken into account. We have shown that these losses can be modeled through the use of simple adiabatic bubble and valve models in FLOW-3D®. In future this model needs to be used in conjunction with an actual metal fill in order to study the porosity in the part due to improper venting. The valve model also needs to be used in a broader framework which looks at compressible flow losses occurring at vents under certain conditions as well as the effect of different geometries, and gas densities on the cumulative loss coefficient.
8. 참고 문헌 (References):
- [1] White, F.M., Fluid Mechanics, 4th ed., p 256, John Fellows Publishing Co., New York, NY (1940)
- [2] Flow of Fluids Through Valves, Fittings, and Pipe, Crane Technical Paper No. 410, Joliet, IL: Crane Co., 1988.
- [3] C.W. Hirt and B.D. Nichols, “Volume-of-Fluid (VOF) Method for the Dynamics of. Free Boundaries,” J. Comp. Phys., 39, 1981, pp. 201-225.
- [4] FLOW-3D® v 9.4 Manual
- [5] Mold Filling Simulation of High Pressure Die Casting for Predicting Gas Porosity, Modeling of Casting, Welding, and Advanced Solidification Processes X, TMS (The Mineral, Metals, & Materials Society), 2003, pp. 335
- [6] Modeling of Air Venting in Pressure Die Casting Process, Nouri-Borujerdi, A., Goldak, J.A., AD, Journal of Manufacturing and Science and Engineering, ASME, 2004
전문가 Q&A: 자주 묻는 질문에 대한 답변
Q1: HPDC에서 유동 손실을 정확하게 모델링하는 것이 왜 그렇게 중요한가요?
A1: 유동 손실을 정확하게 모델링하는 것은 통제되지 않은 공기 혼입이 가스 기공의 주된 원인이기 때문에 매우 중요합니다. 논문의 서론에서 언급했듯이, 기공은 항복 강도 및 연성과 같은 필수적인 기계적 특성을 저하시켜 부품 불량 및 스크랩 증가로 이어집니다.
Q2: 벤트를 올바르게 설계한 것 같은데도 여전히 가스 기공이 발생합니다. 원인이 무엇일까요?
A2: 이 연구는 샷 슬리브를 통한 누출과 같은 "잔류 누출"이 매우 중요하면서도 종종 간과되는 벤팅 요인일 수 있음을 강조합니다. 연구에 따르면 완전히 닫힌 금형에서 이론과 실제 사이에 140 psi 이상의 압력 차이가 발생했으며, 이는 이러한 누출이 상당하다는 것을 증명합니다. 귀하의 문제는 주된 벤트가 아니라 이러한 정량화되지 않은 누출 경로에 있을 수 있습니다 (Figure 3와 Figure 5 비교).
Q3: 이젝터 핀과 전용 벤트에서 각각 얼마나 많은 벤팅이 이루어지는지 정량화할 수 있나요?
A3: 네, 가능합니다. 이 논문의 방법론은 명확한 템플릿을 제공합니다. 한 번에 하나의 벤팅 시스템을 차단하는 순차적인 "공타"를 수행함으로써(예: 실행 1: 모두 개방; 실행 2: 전용 벤트 폐쇄), Figure 3에서 수행된 것처럼 압력 변환기를 사용하여 압력 곡선의 변화를 측정할 수 있습니다. 이를 통해 각 구성 요소의 벤팅 효과를 분리하고 정량화할 수 있습니다.
Q4: "단열 기포 모델(adiabatic bubble model)"은 무엇이며 왜 유용한가요?
A4: 단열 기포 모델은 FLOW-3D®의 기능으로, 압축성 가스의 복잡한 물리를 매우 효율적이고 정확한 계산으로 단순화합니다. Figure 5에서 보여주듯이, 그 결과는 더 복잡한 압축성 가스 시뮬레이션과 "뛰어난 일치"를 보였습니다. 이는 충전 시뮬레이션 중 금형 캐비티 내의 압력 상승을 정확하게 계산하는 강력하고 실용적인 도구입니다.
Q5: 신규 금형의 강재를 가공하기 전에 시뮬레이션을 통해 벤팅 설계를 어떻게 최적화할 수 있나요?
A5: 본 연구는 CFD 모델을 보정함으로써 전체 금형의 벤팅 시스템을 나타내는 단일 "누적 손실 계수"를 결정할 수 있음을 보여줍니다. 논문의 결론에서 논의된 바와 같이, 이를 통해 FLOW-3D®와 같은 도구를 사용하여 금형을 제작하기 전에 다양한 벤트 크기, 오버플로우 설계 및 위치를 디지털 방식으로 테스트하고 비교하여 적절한 공기 배출을 보장할 수 있으므로 상당한 시간과 비용을 절약할 수 있습니다.
Q6: 이 연구에서 참고할 만한 핵심적인 수치 결과는 무엇이었나요?
A6: 이 연구는 두 가지 주요 보정 값을 산출했습니다. 이젝터 핀과 잔류 누출만을 통한 벤팅("진공 밸브 폐쇄")의 누적 손실 계수는 3.73e-6 m²/√(kg/m³)였습니다. 전체 시스템이 함께 벤팅될 때("모두 개방")의 계수는 6.4e-6 m²/√(kg/m³)였습니다. 이 값들은 Figure 6에서 보여주듯이 시뮬레이션을 실제 데이터와 일치시켜 도출되었습니다.
결론 및 다음 단계
이 연구는 HPDC 벤트 설계에서 직관을 넘어설 수 있는 귀중한 로드맵을 제공합니다. 목표에 맞춘 물리적 실험과 보정된 CFD 시뮬레이션을 결합함으로써 금형 내 공기 유동 경로의 복잡한 네트워크를 정량화하고 최적화하는 것이 가능합니다. 연구 결과는 부품 품질을 개선하고, 기공 관련 결함을 줄이며, 첫날부터 생산을 최적화하기 위한 명확하고 데이터 기반의 길을 제시합니다.
저희 CASTMAN은 고객의 가장 어려운 다이캐스팅 문제를 해결하기 위해 최신 산업 연구를 적용하는 데 전념하고 있습니다. 이 논문에서 논의된 문제들이 귀사의 운영 목표와 관련이 있다면, 저희 엔지니어링 팀에 연락하여 이러한 고급 원칙을 귀사의 부품에 어떻게 구현할 수 있는지 논의해 보십시오.
저작권
- 이 자료는 "M.C. Carter, S. Palit, and M. Littler"의 논문을 기반으로 합니다. 논문 제목: "Characterizing Flow Losses Occurring in Air Vents and Ejector Pins in High Pressure Die Castings".
- 논문 출처: NADCA CastExpo'10 Conference Proceedings.
이 자료는 정보 제공 목적으로만 사용됩니다. 무단 상업적 사용을 금지합니다. Copyright © 2025 CASTMAN. All rights reserved.