이 소개 자료는 "[The 75th World Foundry Congress]"에서 발표된 "[Influence of Super Large Single Piece Die Casting Production to Automotive Industry]" 논문을 기반으로 합니다.
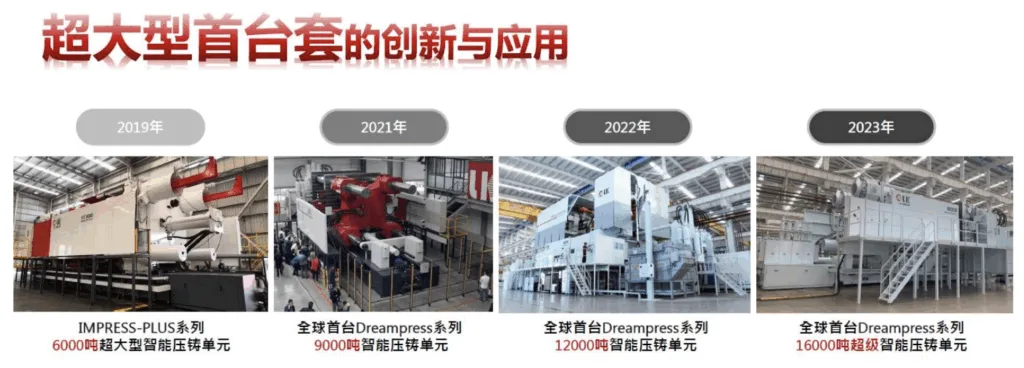
1. 개요:
- 제목: Influence of Super Large Single Piece Die Casting Production to Automotive Industry (초대형 단일 부품 다이캐스팅 생산이 자동차 산업에 미치는 영향)
- 저자: Liu Siong Song*, Chan Kwok Keung, Qiu Ge (L.K.Machinery International Limited, 홍콩/중국)
- 발행 연도: 2024
- 발행 학술지/학회: The 75th World Foundry Congress (Part 10: Die-Casting Technology)
- 키워드: Super Large Single Piece die-casting (초대형 단일 부품 다이캐스팅), new energy vehicles new production (신에너지 자동차 신규 생산), underbody casting (언더바디 캐스팅)
2. 초록:
미국의 한 신에너지 자동차 회사의 혁신 아이디어와 여러 당사자들의 훌륭한 작업 및 협력을 통해 새로운 유형의 초대형 단일 부품 다이캐스팅 생산 방식이 확립되었습니다. 이는 생산 비용을 절감했을 뿐만 아니라 생산 속도를 가속화하고 차체 무게를 더욱 줄였습니다. 신에너지 자동차의 지속적인 폭발적 성장과 에너지 절약 및 배출 감소 요구로 인해 신에너지 자동차의 경량화는 피할 수 없는 추세가 되었으며, 이는 초대형 단일 부품 다이캐스팅 개발을 더욱 촉진했습니다.
자동차 프론트 언더바디, 리어 언더바디, 배터리 트레이와 같은 대형 알루미늄 합금 다이캐스팅 부품은 기존에는 최대 70개 이상의 작은 부품으로 구성되었습니다. 이 새로운 기술을 사용하면 한 번의 주조로 생산할 수 있습니다. 이는 단순히 모든 장비를 확대하는 것만으로는 불가능하며, 많은 어려움과 과제가 수반됩니다. 이 글은 다이캐스팅 유닛의 관점에서 시작하여 각 단계의 설계 및 공정 최적화를 통해, 그리고 현장 검증을 통해 다이캐스팅 제품의 성능과 생산 효율성을 개선하는 방법을 다룹니다.
다이캐스팅 유닛의 생산 공정에는 금속 용탕 주입(metal ladling), 사출(injection), 금형 냉각(die cooling), 부품 제거(parts removal), 이형제 분무(spraying), 부품 냉각(parts cooling), 트리밍(trimming), 마킹(marking), 그리고 배출(output)이 포함됩니다.
3. 서론:
자동차 산업은 기술 발전이 차량 설계, 제조 효율성 및 전반적인 성능 향상을 주도하면서 끊임없이 진화하고 있습니다. 이러한 획기적인 혁신 중 하나는 초대형 단일 부품 다이캐스팅 생산의 도입입니다. 이 기술은 비용, 무게, 강도 및 생산 속도 측면에서 수많은 이점을 제공하며 차량 제조 방식을 혁신할 잠재력을 가지고 있습니다.
전통적인 방식에서는 차량의 언더바디를 70~100개의 작은 부품을 결합하여 전체 언더바디를 형성했습니다[1]. 이 방식은 수백 대의 로봇과 조립 라인을 구축하기 위한 넓은 공간을 필요로 했으며, 소요 시간은 시간 단위였습니다.
초대형 다이캐스팅 기계를 사용하면 프론트 언더바디 또는 리어 언더바디를 약 100초가 걸리는 단일 부품으로 생산할 수 있습니다. 필요한 공간은 훨씬 적어서 다이캐스팅 셀당 약 800~1000 평방미터(농구 코트 2개 크기 정도)면 충분합니다.
다이캐스팅은 용융된 금속을 고압으로 금형 캐비티에 주입하는 제조 공정입니다. 전통적으로 이 공정은 더 작은 부품을 만드는 데 사용되었고, 이 부품들은 더 큰 구조물로 조립되었습니다. 그러나 최근의 발전으로 훨씬 더 큰 부품을 단일 부품으로 생산할 수 있게 되었으며, 이 공정을 초대형 단일 부품 다이캐스팅이라고 합니다. 이는 기가 캐스팅(Giga casting)이라고도 불립니다.
2019년에는 6000톤 다이캐스팅 기계가 있었고, 2020년에는 9000톤 다이캐스팅 기계가 발표되었습니다. 2021년에는 12000톤 다이캐스팅 기계가 선보였고, 2023년에는 16000톤 다이캐스팅 기계가 전시되었습니다.
다이캐스팅 기계의 형체력(clamping force)이 점점 커짐에 따라 단일 부품 캐스팅의 크기도 더 커질 수 있음을 나타냅니다.
4. 연구 요약:
연구 주제 배경:
자동차 산업은 설계, 효율성, 성능 면에서 지속적인 개선을 요구합니다. 전통적인 언더바디 제조는 70-100개의 작은 부품을 조립하는 복잡하고 시간과 공간이 많이 소요되는 공정이었습니다. 신에너지 자동차(NEV)의 부상과 경량화 추진은 보다 효율적인 생산 방식의 필요성을 야기했습니다. 미국 NEV 회사의 혁신 아이디어가 초대형 단일 부품(SLSP) 다이캐스팅 개발을 촉발했습니다.
기존 연구 현황:
이전에는 차량 언더바디가 수백 대의 로봇을 사용하여 여러 시간 동안 많은 작은 부품을 결합하여 만들어졌습니다[1]. 다이캐스팅은 일반적으로 더 작은 부품에 사용되었습니다. 최근의 발전으로 점점 더 큰 다이캐스팅 기계가 등장했습니다: 6000톤(2019), 9000톤(2020 발표), 12000톤(2021 전시), 16000톤(2023 전시). 이를 통해 훨씬 더 큰 단일 부품 주조가 가능해졌습니다.
연구 목적:
이 논문은 다이캐스팅 유닛의 관점에서 SLSP 다이캐스팅을 검토합니다. 각 단계의 설계 및 공정 최적화와 현장 검증을 통해 다이캐스팅 제품의 성능과 생산 효율성을 개선하는 것을 목표로 합니다. 또한 이 기술의 장점과 자동차 산업에 미치는 영향을 논의합니다.
핵심 연구:
본 연구는 금속 용탕 주입, 사출, 금형 냉각, 부품 제거, 이형제 분무, 부품 냉각, 트리밍, 마킹, 배출을 포함하는 SLSP 다이캐스팅 생산 공정에 초점을 맞춥니다. 이 기술의 장점을 분석합니다: (1) 비용 효율성(부품, 조립, 노동, 금형 비용 감소), (2) 무게 감소(복잡한 형상, 최적화된 재료 분포), (3) 구조적 무결성 향상(접합부/약점 제거), (4) 생산 속도 증가(단일 사이클 대 긴 조립 시간), (5) 설계 유연성(복잡하고 혁신적인 구조). 또한 SLSP 다이캐스팅이 전기 자동차(EV), 전반적인 제조 효율성, 공급망 단순화 및 지속 가능성에 미치는 영향을 논의합니다.
5. 연구 방법론
연구 설계:
논문은 공식적인 연구 설계를 명시적으로 밝히지 않았습니다. 산업 발전과 기술 진보를 바탕으로 SLSP 다이캐스팅 기술과 자동차 산업에서의 응용에 대한 기술적이고 분석적인 개요를 제시합니다. 초록에서는 성능과 효율성을 개선하기 위해 "설계 및 공정 최적화"와 "현장 검증"이 사용되었다고 언급하여 경험적 요소가 있음을 시사하지만, 설계의 세부 사항은 제공되지 않았습니다.
데이터 수집 및 분석 방법:
구체적인 데이터 수집 및 분석 방법은 논문에 자세히 설명되어 있지 않습니다. 연구는 SLSP 기술을 설명하고, 공정 단계를 개괄하며, 장점을 분석하고, 산업 동향(예: 참고문헌 [2]로 인용되고 그림으로 설명된 EV 성장)과 기술 발전(예: 그림으로 표시된 기계 톤수 증가)을 기반으로 그 영향을 논의하는 데 의존합니다. "현장 검증"이 언급되었지만 이 검증 방법론은 상세히 설명되지 않았습니다.
연구 주제 및 범위:
연구 주제는 초대형 단일 부품 다이캐스팅 생산이 자동차 산업에 미치는 영향입니다. 범위는 기술 설명, 생산 공정(다이캐스팅 유닛 내), 장점(비용, 무게, 강도, 속도, 설계), 그리고 특히 신에너지 자동차, 제조 효율성, 공급망 및 지속 가능성과 관련된 영향을 포함합니다. 차량 언더바디와 같은 대형 부품에 초점을 맞춥니다.
6. 주요 결과:
주요 결과:
- SLSP 다이캐스팅은 이전에 70개 이상의 부품으로 만들어졌던 대형 자동차 부품(예: 프론트/리어 언더바디, 배터리 트레이)을 단 한 번의 주조(약 100초)로 생산할 수 있게 합니다.
- 이 기술은 전통적인 조립 방식에 비해 제조 비용, 노동력, 금형 비용 및 공장 공간을 크게 줄입니다.
- 최적화된 설계와 재료 분포를 통해 무게 감소를 촉진하며, 이는 NEV 효율성과 성능에 중요합니다.
- SLSP 캐스팅은 용접, 볼트 체결 또는 접착제로 인한 접합부를 제거하여 구조적 무결성을 향상시킵니다.
- 생산 속도가 극적으로 증가하여 시장 수요에 더 빠르게 대응할 수 있습니다.
- 이 기술은 복잡하고 혁신적인 차량 구조를 위한 더 큰 설계 유연성을 제공합니다.
- SLSP 다이캐스팅은 EV 생산, 전반적인 제조 효율성, 공급망 단순화(부품 수 감소), 지속 가능성(폐기물, 에너지, 배출 감소; 더 가벼운 차량)에 긍정적인 영향을 미칩니다.
- 이 기술은 EV뿐만 아니라 잠재적으로 전통적인 내연기관(IC) 차량에도 적용 가능하며, 이는 전체 차량 생산 비용을 낮출 수 있는 잠재력을 시사합니다.
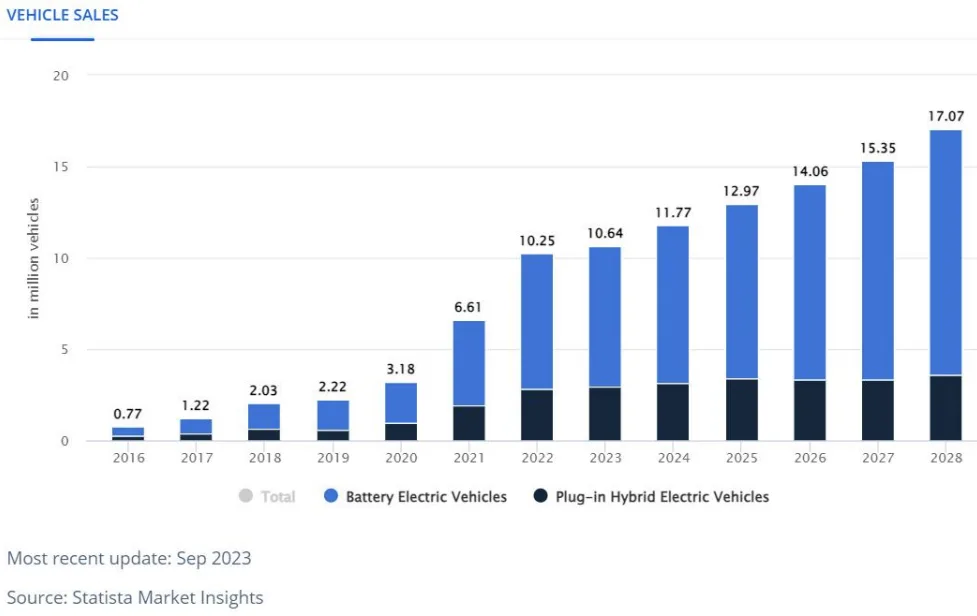
그림 이름 목록:
- Figure: "超大型首台套的创新与应用" 제목 아래의 라벨 없는 그림. L.K. Machinery가 개발한 대형 다이캐스팅 기계의 발전을 보여주며, 증가하는 톤수(6000t, 9000t, 12000t, 16000t)와 도입 연도(각각 2019, 2021, 2022, 2023 - 참고: 본문에서는 9000t가 2020년에 발표되었다고 하지만, 그림의 9000t 아래 라벨은 2021년으로 되어 있음)를 보여줌.
- Figure: "VEHICLE SALES"라는 제목의 그래프. 전체 차량, 배터리 전기 자동차, 플러그인 하이브리드 전기 자동차의 과거(2016년부터) 및 예측(2028년까지) 판매 데이터(백만 대 단위)를 보여줌. (출처: Statista Market Insights, 2023년 9월 업데이트).
7. 결론:
초대형 단일 부품 다이캐스팅은 자동차 제조 기술의 중요한 발전을 나타냅니다. 비용 절감, 효율성 향상, 차량 성능 개선 및 지속 가능성에 기여할 수 있는 잠재력은 자동차 제조업체에게 매우 매력적인 옵션입니다. 산업이 계속 발전함에 따라 이 기술의 채택은 차량 생산 및 설계의 미래를 형성하는 데 중추적인 역할을 할 가능성이 높습니다.
초대형 단일 부품 다이캐스팅은 EV뿐만 아니라 전통적인 IC 차량 생산에도 사용될 수 있으므로, 향후 자동차 산업의 생산 비용을 낮추고 결과적으로 차량 가격을 낮출 수 있을 것으로 믿어집니다.
8. 참고 문헌:
- [1] https://x.com/tesla/status/1513886756923445254?lang=th
- [2] https://www.statista.com/outlook/mmo/electric-vehicles/worldwide#unit-sales
9. 저작권:
- 이 자료는 "Liu Siong Song, Chan Kwok Keung, Qiu Ge"의 논문입니다. "[Influence of Super Large Single Piece Die Casting Production to Automotive Industry]"를 기반으로 합니다.
- 논문 출처: [논문에 DOI URL이 제공되지 않음]
이 자료는 위 논문을 바탕으로 요약되었으며, 상업적 목적의 무단 사용을 금지합니다.
Copyright © 2025 CASTMAN. All rights reserved.