본 소개 내용은 [특수 주조 및 비철 합금/Special Casting & Nonferrous Alloys]에서 발행한 ["Influence of Casting Distance on Microstructure of Simultaneously Mixed Controlled Diffusion Solidified Al-Si Alloys"] 의 연구 내용입니다.
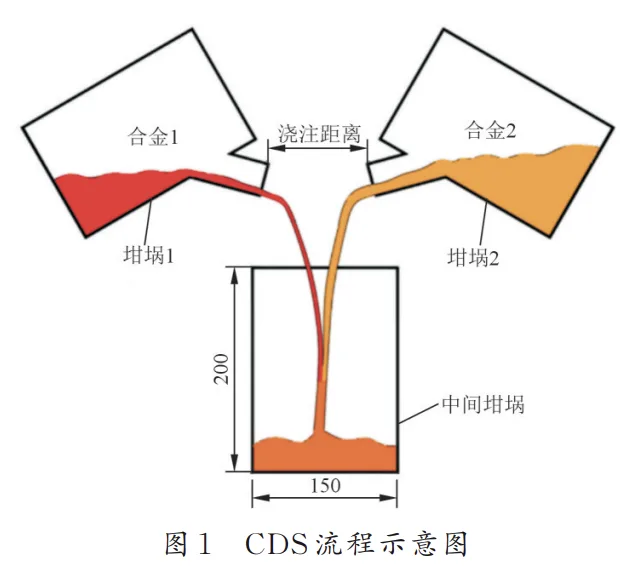
1. 개요:
- 제목: Influence of Casting Distance on Microstructure of Simultaneously Mixed Controlled Diffusion Solidified Al-Si Alloys / 주입 거리가 동시 혼합 제어 확산 응고 Al-Si 합금 조직에 미치는 영향
- 저자: LI Shaosi, CHEN Tijun / 리샤오시, 천티쥔
- 출판 연도: 2025년 2월
- 출판 저널/학회: Special Casting & Nonferrous Alloys / 특수 주조 및 비철 합금
- 키워드: Controlled Diffusion Solidification (CDS), Al-Si Alloy, Casting Distance, Nucleation Rate, Primary α-Al / 제어 확산 응고(CDS); Al-Si 합금; 주입 거리; 핵 생성률; 초정 α-Al
2. 초록 / 서론
목표 합금 Al-8Si는 모합금 1인 순수 Al과 모합금 2인 Al-12Si를 특정 질량비와 온도에서 사용하여 제어 확산 응고(CDS) 방식으로 얻었으며, 수치 모의 실험과 실험적 검증의 조합을 통해 혼합 용융물의 유동장, 온도장, 용질장 및 핵 생성률, 그리고 실험적으로 얻은 주조물의 초정 α-Al 상의 크기와 형상을 분석했습니다. 결과는 주입 거리가 두 모합금의 혼합 효과에 영향을 미치며, 주입 거리가 너무 작거나 너무 클 때 혼합 용융물의 용질장과 온도장이 불균일하고 핵 생성률이 낮으며, 실험적으로 얻은 주조물의 초정 α-Al 결정립이 조대하고 불규칙함을 보여줍니다. 주입 거리가 80mm일 때 혼합 효과가 가장 좋으며, 온도장과 용질장이 가장 균일하고 핵 생성률이 가장 높으며, 초정 α-Al 상의 평균 결정립 크기와 형상 계수는 각각 57.6 µm과 1.55입니다.
摘要 以纯A1为母合金1, Al-12Si为母合金2, 在一定的质量比和温度下, 采用受控扩散凝固(CDS)的方法得到目标合金Al-8Si。采用数值模拟和试验验证相结合的方法对混合熔体的流场、温度场、溶质场和形核率以及试验所得铸件的初生α-Al相尺寸、形状进行分析。结果表明, 浇注距离对两种母合金混合效果产生影响, 在浇注距离过小或过大时, 混合熔体的溶质场和温度场都不均匀, 形核率较低, 试验所得铸件的初生α-Al晶粒粗大且不规则。浇注距离为80 mm时, 混合效果最好, 温度场、溶质场最均匀且形核率最高, 初生α-Al相的晶粒尺寸和形状因子分别为57.6 µm和1.55。
3. 연구 배경:
연구 주제의 배경:
알루미늄 합금은 높은 비강도, 저렴한 비용, 풍부한 자원, 우수한 열전도율, 내식성 및 용이한 가공성으로 인해 널리 사용됩니다. 전통적인 주조에서 알루미늄 합금의 넓은 결정 온도 범위는 조대한 수지상 조직을 유발합니다. 수지상 응고는 거시적 편석, 기공 및 미세 균열을 일으켜 기계적 성질에 심각한 영향을 미칠 수 있습니다. 제어 확산 응고(CDS)는 비수지상(구상) 조직을 달성하여 우수한 주조 특성을 얻는 효과적인 방법입니다.
알루미늄 합금은 높은 강도 대 중량비로 경금속으로 분류되며, 저렴한 비용, 풍부한 자원, 우수한 열전도율, 내식성, 용이한 가공 등의 특징을 가지고 있어 응용 전망이 넓습니다. 전통적인 주조에서 알루미늄 합금의 응고 과정은 결정 온도 구간이 넓어 미세 조직이 조대한 수지상 결정으로 나타납니다. 연구 결과에 따르면 주조품에서 수지상 조직 응고 방식은 다량의 수축공, 수축 공동 외에도 성분 불균일, 내부 다량의 기공 및 미세 균열을 형성하여 주조품의 역학적 성능에 심각한 영향을 미칩니다.
기존 연구 현황:
비수지상 조직을 얻기 위한 기존 방법에는 주조 중 결정립 미세화제 첨가, 전자기 진동 및 기계적 교반 등이 있습니다. 그러나 이러한 방법은 불순물 도입, 높은 비용, 복잡한 공정과 같은 제한 사항이 있습니다. 전통적인 CDS 기술은 장점을 제공하지만 여전히 비정상적인 결정립과 불균일한 결정립 크기를 생성할 수 있습니다.
연구자들은 주입 과정에서 결정립 미세화제, 전자기 진동, 기계적 교반 등의 방법을 사용하여 비수지상 슬러리를 얻었으며, 그중 결정립 미세화제 첨가는 불순물을 유입할 수 있고 결정립 미세화제 비용이 높으며, 전자기 진동과 기계적 교반은 모두 외부 장비가 필요하고 비용이 높고 공정이 복잡하여 산업 응용에 일정한 제한이 있습니다. 전통적인 제어 확산 응고 기술은 많은 제한 사항이 있으며, 요구 사항을 완전히 충족하는 합금이라도 여전히 비정상적인 결정립, 불균일한 결정립 크기를 생성합니다.
연구의 필요성:
CDS 공정에서 주입 거리의 영향에 대한 연구는 제한적입니다. CDS 매개변수를 최적화하고 Al-Si 합금의 기계적 성질과 성형성을 개선하기 위해 본 연구에서는 제어 확산 혼합 효과에 대한 주입 거리의 영향을 조사하고 결정립 핵 생성, 성장, 형태 및 형성 메커니즘에 초점을 맞춥니다. 이는 비철 합금에서 제어 확산 응고 기술의 응용에 대한 참고 자료를 제공하는 것을 목표로 합니다.
현재 국내에서 CDS 주입 거리에 대한 연구 보고는 거의 없습니다. 동시 혼합 CDS 공정 매개변수를 더욱 개선하고 Al-Si 합금의 역학적 성능과 성형성을 향상시키기 위해 본 연구에서는 모합금의 주입 거리가 제어 확산 혼합 효과에 미치는 영향을 분석하고 결정립의 핵 생성, 성장 방식 및 형태 등 형성 메커니즘을 연구하여 제어 확산 응고 기술의 유색 합금 응용에 참고 자료를 제공하고자 합니다.
4. 연구 목적 및 연구 질문:
연구 목적:
본 연구의 목적은 Al-Si 합금에 대한 동시 혼합 CDS의 혼합 효과에 대한 주입 거리의 영향을 조사하는 것입니다. 여기에는 응고 중 온도장, 용질장, 유동장 및 핵 생성률을 분석하고 이를 초정 α-Al의 미세 조직, 결정립 크기 및 형상과 연관시키는 것이 포함됩니다.
본 연구에서는 모합금의 주입 거리가 제어 확산 혼합 효과에 미치는 영향을 분석하고 결정립의 핵 생성, 성장 방식 및 형태 등 형성 메커니즘을 연구합니다.
핵심 연구 질문:
핵심 연구 질문은 다음과 같습니다.
- 주입 거리는 동시 혼합 CDS에서 혼합 용융물의 온도장, 용질장 및 유동장에 어떤 영향을 미치는가?
- 주입 거리는 CDS에서 핵 생성률 및 응고 과정에 어떤 영향을 미치는가?
- CDS Al-Si 합금에서 균일한 미세 조직과 미세한 결정립 크기를 달성하기 위한 최적의 주입 거리는 무엇인가?
- 주입 거리는 CDS Al-Si 합금에서 초정 α-Al상의 결정립 크기와 형상에 어떤 영향을 미치는가?
본 연구에서는 모합금의 주입 거리가 제어 확산 혼합 효과에 미치는 영향을 분석하고 결정립의 핵 생성, 성장 방식 및 형태 등 형성 메커니즘을 연구하여 제어 확산 응고 기술의 유색 합금 응용에 참고 자료를 제공하고자 합니다.
5. 연구 방법론
연구 설계:
본 연구에서는 수치 모의 실험과 실험적 검증을 병행하여 사용했습니다. Fluent 소프트웨어를 사용하여 순수 Al(합금 1)과 Al-12Si(합금 2)의 CDS 공정을 모의 실험하여 Al-8Si 합금을 얻었습니다. 모의 실험에서는 온도장, 용질장 및 유동장을 분석하기 위해 주입 거리(60mm, 80mm, 100mm)를 다양하게 변경했습니다. 실험은 모의 실험 결과를 검증하고 미세 조직을 분석하기 위해 60, 70, 80, 90 및 100mm의 주입 거리로 수행되었습니다.
Fluent 소프트웨어를 사용하여 순수 Al(합금 1)과 Al-12Si(합금 2)를 혼합하여 목표 합금 Al-8Si를 얻는 과정을 모의 실험했습니다. CDS 공정 개략도는 그림 1과 같습니다. 모의 실험 과정에는 연속 방정식(질량 보존 방정식), Navier-Stokes 방정식(운동량 보존 방정식), 에너지 보존 방정식 및 기타 관련 방정식과 이전 연구와 동일한 열물성 매개변수가 포함되었습니다. 실험 주입 거리는 5개 그룹으로 나누어 각각 60, 70, 80, 90, 100mm로 설정하고 순차적으로 검증했으며, 실험에서 도가니의 크기 매개변수와 CDS 공정 매개변수는 모의 실험의 매개변수와 완전히 일치했습니다.
자료 수집 방법:
수치 모의 실험 데이터에는 온도장, 용질장, 유동장 및 핵 생성률이 포함되었습니다. 실험 데이터에는 광학 현미경(OM)으로 얻은 미세 조직 이미지와 Image-Pro-Plus 6.0 소프트웨어를 사용하여 측정한 결정립 크기 및 형상 계수가 포함되었습니다.
Fluent 수치 모의 실험을 통해 중간 도가니 내 혼합 용융물의 유동장, 온도장, 용질장 분포 및 후속 응고 시 핵 생성률을 관찰하고, 실험적 검증과 결합하여 최적의 혼합 매개변수를 얻었습니다. Axio Scope Al 광학 현미경(OM)을 사용하여 주조품 단면 중심 부근의 미세 조직을 관찰했습니다. Image-Pro-Plus 6.0 소프트웨어를 사용하여 초정 α-Al의 평균 결정립 크기와 형상 계수를 계산했습니다.
분석 방법:
모의 실험 결과를 분석하여 용융물 혼합 특성 및 핵 생성률에 대한 주입 거리의 영향을 확인했습니다. 실험적 미세 조직을 분석하여 결정립 형태 및 크기를 평가했습니다. 결정립 크기(D) 및 형상 계수(F)는 방정식 D=2√(A₁/π), F = P² / (4πA₁)를 사용하여 계산했습니다.
Fluent 수치 모의 실험을 통해 중간 도가니 내 혼합 용융물의 유동장, 온도장, 용질장 분포 및 후속 응고 시 핵 생성률을 관찰했습니다. Image-Pro-Plus 6.0 소프트웨어를 사용하여 초정 α-Al의 평균 결정립 크기와 형상 계수를 계산했으며, 판정 기준은 다음과 같습니다. D=2√A₁/π, F = P² / (4πA₁), 여기서 D는 결정립 평균 직경, A는 결정립 단면적, P는 결정립 경계 둘레, F는 결정립 형상 계수입니다.
연구 대상 및 범위:
본 연구는 Al-Si 합금, 특히 순수 Al과 Al-12Si의 CDS로 생산된 Al-8Si 합금을 대상으로 했습니다. 주입 거리는 주요 변수였으며, 60mm, 70mm, 80mm, 90mm 및 100mm의 거리를 조사했습니다.
순수 Al(합금 1)과 Al-12Si(합금 2)를 혼합하여 목표 합금 Al-8Si를 얻는 과정을 모의 실험했습니다. 실험 주입 거리는 5개 그룹으로 나누어 각각 60, 70, 80, 90, 100mm로 설정하고 순차적으로 검증했습니다.
6. 주요 연구 결과:
핵심 연구 결과:
- 80mm 주입 거리가 최적의 혼합 제공: 모의 실험 결과 80mm 주입 거리가 가장 균일한 온도장과 용질장, 가장 높은 핵 생성률을 나타냈습니다.
- 80mm에서 미세 조직 미세화: 실험적으로 80mm 주입 거리에서 미세 조직은 가장 미세하고 등축정인 초정 α-Al 결정립을 나타냈습니다.
- 결정립 크기 및 형상 계수: 80mm 주입 거리에서 평균 결정립 크기는 57.6 µm이고 형상 계수는 1.55로, 다른 거리에 비해 미세하고 더 구형인 결정립을 나타냅니다.
- 주입 거리가 장에 미치는 영향: 주입 거리가 너무 짧거나 너무 길면 불균일한 온도장과 용질장, 낮은 핵 생성률, 조대하고 불규칙한 결정립이 나타났습니다.
결과에 따르면 주입 거리는 두 모합금의 혼합 효과에 영향을 미치며, 주입 거리가 너무 작거나 너무 클 때 혼합 용융물의 용질장과 온도장이 불균일하고 핵 생성률이 낮으며, 실험적으로 얻은 주조물의 초정 α-Al 결정립이 조대하고 불규칙합니다. 주입 거리가 80mm일 때 혼합 효과가 가장 좋으며, 온도장과 용질장이 가장 균일하고 핵 생성률이 가장 높으며, 초정 α-Al상의 결정립 크기와 형상 계수는 각각 57.6 µm과 1.55입니다. 주입 거리가 80mm일 때 핵 생성 영역이 가장 넓으며, 여기서 짙은 색 영역은 핵 생성 영역이고 회색 영역은 액상 영역입니다(그림 5b). 주입 거리가 80mm일 때 결정립 크기가 가장 작고 균일하며, 평균 결정립 크기는 57.6 µm이고 1.55입니다.
제시된 데이터 분석:
- 온도장 및 용질장 (그림 2 & 3): 80mm에서 온도장과 용질장이 가장 균일합니다. 60mm 및 100mm에서는 불균일성이 관찰되어 혼합이 불량함을 나타냅니다.
- 유동장 (그림 4): 80mm에서 용융물 흐름이 고르게 분포되어 혼합을 촉진합니다. 60mm 및 100mm에서는 흐름이 편향되어 편석을 유발합니다.
- 핵 생성률 (그림 5): 핵 생성 영역은 80mm에서 최대화되어 균일한 장 및 흐름과 상관 관계를 갖습니다.
- 미세 조직 (그림 6): 결정립 크기는 80mm에서 최소화되고 형상 계수는 1에 가장 가까워(더 구형) 최적의 미세 조직을 확인합니다. 80mm에서의 결정립 크기 및 형상 계수는 60mm 및 100mm보다 훨씬 우수합니다.
그림 2는 다른 주입 거리에서 혼합 용융물 반 높이 단면의 온도장, 그림 3은 다른 주입 거리에서 혼합 용융물 반 높이 단면의 용질장, 그림 4는 다른 주입 거리에서 혼합 용융물 반 높이 단면의 유동장, 그림 5는 다른 주입 거리에 해당하는 응고 영역, 그림 6은 다른 주입 거리에서 CDS 초정 α-Al의 미세 형태 및 해당 결정립 크기 및 형상 계수입니다. 주입 거리가 80mm일 때 온도장, 용질장이 가장 균일하고 핵 생성률이 가장 높으며, 초정 α-Al상의 결정립 크기가 가장 작고 균일합니다.
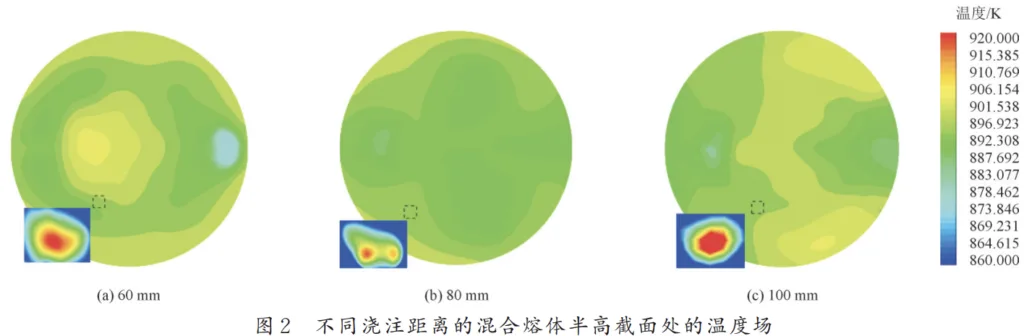
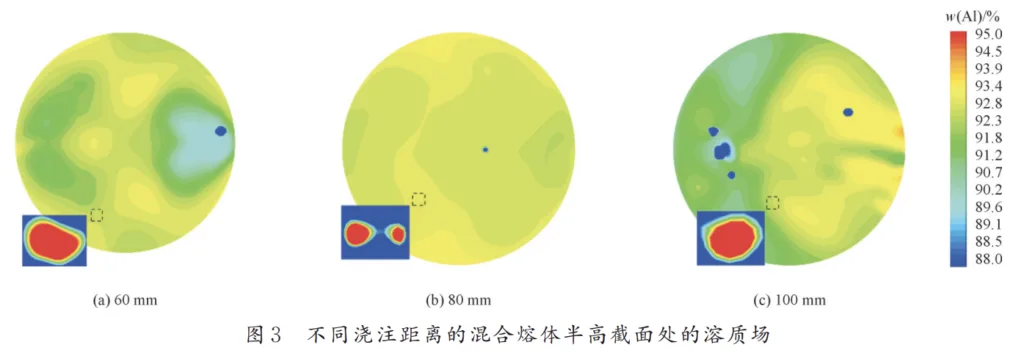
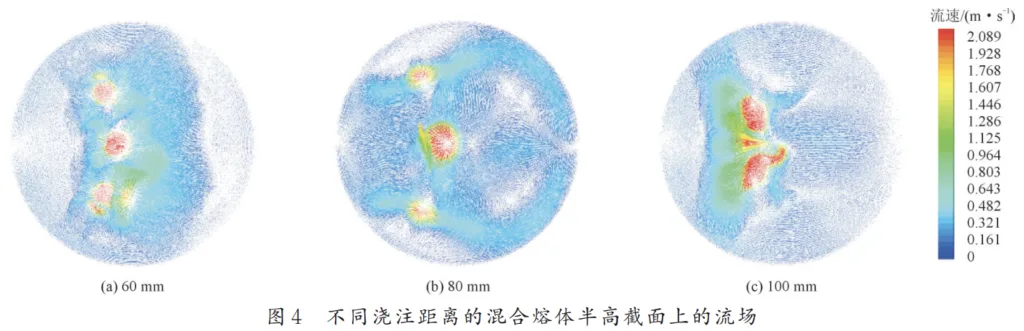
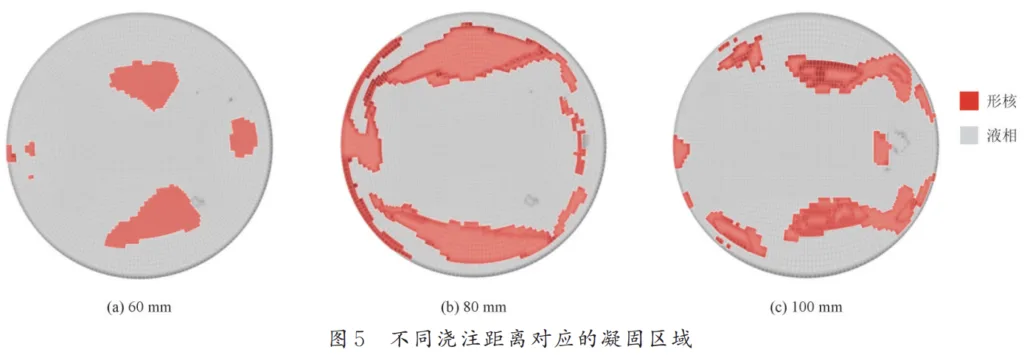
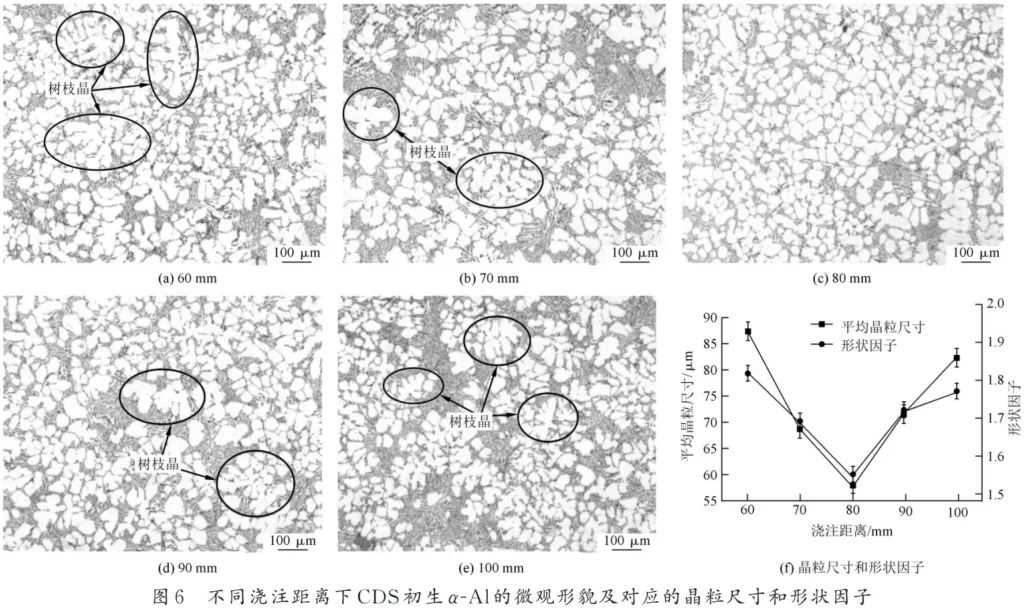
그림 이름 목록:
- Fig.1 Schematic diagram of CDS process / 그림 1 CDS 공정 개략도
- Fig.2 Temperature fields in the cross section at half height of mixtures with different casting distances / 그림 2 다른 주입 거리에서 혼합 용융물 반 높이 단면의 온도장
- Fig.3 Concentration fields in the cross section at half height of mixtures with different casting distances / 그림 3 다른 주입 거리에서 혼합 용융물 반 높이 단면의 용질장
- Fig.4 Flow fields in the cross section at half height of mixtures with different casting distances / 그림 4 다른 주입 거리에서 혼합 용융물 반 높이 단면의 유동장
- Fig.5 Solidified regions corresponding to different casting distances / 그림 5 다른 주입 거리에 해당하는 응고 영역
- Fig.6 Micromorphologies of CDS primary α-Al with different casting distances as well as the corresponding grain size and shape factor / 그림 6 다른 주입 거리에서 CDS 초정 α-Al의 미세 형태 및 해당 결정립 크기 및 형상 계수
7. 결론:
주요 연구 결과 요약:
본 연구에서는 주입 거리가 동시 혼합 CDS Al-Si 합금의 미세 조직에 상당한 영향을 미친다는 것을 입증했습니다. 80mm의 주입 거리가 최적인 것으로 확인되었으며, 균일한 온도장과 용질장, 높은 핵 생성률, 미세하고 구형인 초정 α-Al 결정립을 생성했습니다. 이 거리에서 벗어나 짧거나 긴 거리는 불균일한 장, 낮은 핵 생성률, 조대하고 불규칙한 결정립을 유발했습니다.
동시 혼합 제어 확산 응고 모의 실험 결과에 따르면 주입 거리가 80mm일 때 온도장과 용질장이 가장 균일하고, 이때 미세 용융 풀의 수가 가장 많고 크기가 가장 작아 이때 혼합 효과가 가장 좋다는 것을 알 수 있습니다. 핵 생성률에서 볼 수 있듯이 주입 거리가 80mm일 때 핵 생성 영역이 가장 큽니다. 다양한 매개변수에서 주조품의 미세 조직 형태를 관찰한 결과, 주입 거리가 80mm일 때 결정립 크기가 가장 작고 균일합니다.
연구의 학문적 의의:
본 연구는 Al-Si 합금에 대한 CDS 매개변수, 특히 주입 거리의 최적화에 대한 귀중한 통찰력을 제공합니다. 동시 혼합 CDS에서 주입 거리, 용융물 혼합, 응고 거동 및 미세 조직 진화 간의 관계를 명확히 합니다. 본 연구 결과는 CDS 공정 및 고성능 알루미늄 합금 주조품 생산 가능성에 대한 더 깊은 이해에 기여합니다.
본 연구에서는 최적의 주입 거리에서 초정 α-Al이 더욱 미세하고 구형화되어 이상적인 반고상 비수지상 슬러리와 주괴를 얻어 주조품 성능 향상이라는 목표를 달성했습니다. 본 연구에서 제안한 동시 혼합 CDS는 기존 CDS의 단점을 극복할 수 있음을 알 수 있습니다.
실용적 의미:
본 연구 결과는 Al-Si 합금에서 원하는 미세 조직과 특성을 얻기 위해 동시 혼합 CDS에서 주입 거리 제어가 중요하다는 것을 시사합니다. 80mm의 주입 거리는 이 CDS 방법을 사용하여 미세 조직이 미세화된 Al-8Si 합금을 생산하는 데 참고 자료로 사용할 수 있습니다. 이는 Al-Si 합금 주조품의 기계적 성질과 성형성을 향상시켜 이러한 재료를 활용하는 산업에 도움이 될 수 있습니다.
주입 거리가 80mm일 때 혼합 효과가 가장 좋으며, 온도장, 용질장이 가장 균일하고 핵 생성률이 가장 높으며, 초정 α-Al상의 결정립 크기와 형상 계수는 각각 57.6 µm과 1.55입니다. 이는 본 연구에서 제안한 동시 혼합 CDS가 우수한 혼합 효과로 인해 기존 CDS의 단점을 피할 수 있음을 의미합니다.
연구의 한계 및 향후 연구 분야:
본 연구는 특정 Al-Si 합금 조성(Al-8Si)과 제한된 범위의 주입 거리에 초점을 맞추었습니다. 향후 연구에서는 다른 Al-Si 합금 조성과 주입 온도 및 혼합 속도를 포함한 더 넓은 범위의 주조 매개변수에 대한 주입 거리의 영향을 탐구할 수 있습니다. 다양한 주입 거리에서 응고 메커니즘과 미세 조직 진화에 대한 추가 조사도 유익할 것입니다.
연구 대상은 Al-Si 합금입니다. 향후 연구에서는 주입 거리가 다른 알루미늄-실리콘 합금 조성과 더 넓은 범위의 주입 변수에 미치는 영향, 즉 주입 온도와 혼합 속도를 탐구할 수 있습니다. 다양한 주입 거리에서 응고 메커니즘과 미세 조직 진화에 대한 추가 연구도 유익할 것입니다.
8. 참고 문헌:
- [1] 徐通,张宇飞,李咏凯. 高性能亚共晶铝硅合金的研究[J]. 材料研究与应用, 2017, 11(4): 236-239.
- [2] WU Y. Application of aluminum alloy in aircraft [J]. Journal of Physics, 2022, 2228(1): 12-24.
- [3] XU YJ, ZHAO DD, LI YJ. A thermodynamic study on the effect of solute on the nucleation driving force, solid-liquid interfacial energy, and grain refinement of Al alloys [J]. Metallurgical and Materials Transactions, 2018, A49: 1770-1781.
- [4] LIU B, KANG J, YANG X, et al. Effects of hollow sand mold on the microstructure and mechanical properties of a low pressure aluminum alloy casting [J]. Journal of Materials Research and Technology, 2024, 28: 4488-4497.
- [5] 丁俭,靳子惠,杜喜望,等. 添加A1-5Ti-B和A1-2Zr-Er对铸态铝锌镁合金力学性能的影响[J]. 材料科学与工艺, 2017, 25(2): 39-44.
- [6] 李安庆,张立华,蒋日鹏,等. 冷却速度及超声振动协同作用对7085铝合金凝固组织及力学性能的影响[J]. 材料工程, 2021, 49 (8): 63-71.
- [7] 余柯培,沈利,麻永林,等. 电磁能对ZL102铝合金凝固组织的影响[J]. 内蒙古科技大学学报, 2019, 38(1): 18-21.
- [8] 彭洪美,李晓谦,蒋日鹏. 熔体超声处理对7050铝合金铸锭微观偏析的影响[J]. 北京理工大学学报, 2016, 36(11): 1105-1110.
- [9] 李夏,李元东,马颖,等. 混合方式对受控扩散凝固过共晶 Al-Si 合金初生硅相的影响[J]. 中国有色金属学报, 2011, 21(12): 3033-3041.
- [10] LI YD, HU SH, LI X. Study on hypereutectic Al-Si alloy fabricated by liquid-liquid mixing [J]. Advanced Materials Research, 2013, 815:13-18.
- [11] POURGHARIBSHAHI M, DIVANDARJ M, LARIJANI H S, et al. Controlled diffusion solidification processing: A review [J]. Journal of Materials Processing Technology, 2017, 250 (1): 203-219.
- [12] CHEN TJ, YANG XK, XUE H, et al. Mixing process and nucleation of an Al-Si alloy during controlled diffusion solidification with modified and effect of melt mass [J]. Journal of Materials Science, 2022, 57: 3018-3040.
- [13] XUE H, CHEN TJ. Effect of mixing temperature on microstructure of an Al-Si alloy prepared by controlled diffusion solidification [J]. China Foundry, 2023, 20(3): 241-252.
- [14] LIU YH, CHEN TJ. Effect of standing time after mixing on the mixture microstructure of an Al-Si alloy during controlled diffusion solidification with modified [J]. Metals, 2023, 13(4): 733-740.
- [15] KHALAF A A. Studying of non-dendritic microstructure forming in controlled diffusion solidification [J]. International Journal of Metal Casting, 2022, 16(1): 223-233.
9. 저작권:
- 본 자료는 "[LI Shaosi, CHEN Tijun]"의 논문: "[Influence of Casting Distance on Microstructure of Simultaneously Mixed Controlled Diffusion Solidified Al-Si Alloys]"을 기반으로 합니다.
- 논문 출처: DOI: 10.15980/j.tzzz.T20240050
본 자료는 위 논문을 소개하기 위해 제작되었으며, 상업적 목적으로 무단 사용하는 것을 금지합니다.
Copyright © 2025 CASTMAN. All rights reserved.