본 논문 요약은 Materials (MDPI)에 발표된 논문 "Development of Low-Pressure Die-Cast Al-Zn-Mg-Cu Alloy Propellers Part II: Simulations for Process Optimization"을 기반으로 작성되었습니다.
1. 개요:
제목: 저압 다이캐스팅 Al-Zn-Mg-Cu 합금 프로펠러 개발 Part II: 공정 최적화를 위한 시뮬레이션 (Development of Low-Pressure Die-Cast Al-Zn-Mg-Cu Alloy Propellers Part II: Simulations for Process Optimization)
저자: 김민석, 원순호 (Min-Seok Kim, Soonho Won)
발행년도: 2024년
발행 학술지: Materials (MDPI)
키워드: Al-Zn-Mg-Cu 합금; 저압 다이캐스팅; 시뮬레이션; 프로펠러; 열간 찢김 (Al-Zn-Mg-Cu alloy; low-pressure die-casting; simulation; propeller; hot tearing)
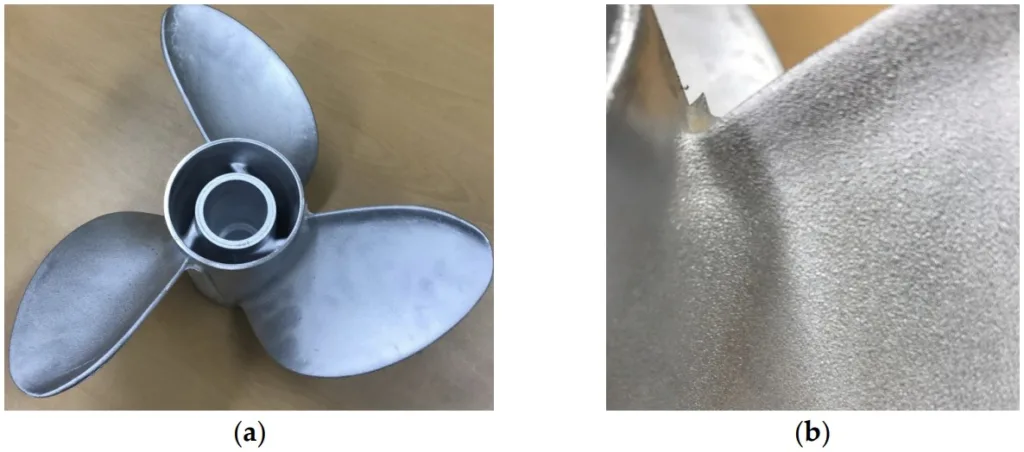
2. 연구 배경:
고성능 레저 보트 프로펠러에 대한 수요가 꾸준히 증가하고 있습니다. 스테인리스강 프로펠러는 우수한 물성을 제공하지만 높은 제조 비용과 가공 난이도로 인해 어려움이 있습니다. 주조 알루미늄 합금은 제조가 더 쉽지만 재료 특성으로 인해 저출력 응용 분야로 제한됩니다. 고강도 알루미늄 합금은 기계적 물성과 비용 효율성 사이의 균형을 맞춰 유망한 대안을 제시합니다.
본 연구의 Part I에서는 프로펠러 생산에 적합한 Al-6Zn-2Mg-1.5Cu 합금을 개발하고 저압 다이캐스팅(LPDC)에서 허브-블레이드 접합부의 열간 찢김을 중요한 문제점으로 확인했습니다. 기존의 중력 주조 방식으로는 고강도 알루미늄 합금의 주조 결함을 제어하기 어려워 고품질 부품 생산에 어려움이 있습니다. 따라서 LPDC 공정을 최적화하여 열간 찢김을 극복하고 이러한 프로펠러의 안정적인 대량 생산을 보장하는 것이 중요합니다. 대량 생산 라인에서 시행착오를 통한 변수 조정은 한계가 있으므로 효율적인 공정 최적화를 위해서는 시뮬레이션 기술이 필수적입니다.
3. 연구 목적 및 연구 질문:
연구 목적:
본 연구는 고강도 Al-Zn-Mg-Cu 합금 프로펠러 제조를 위한 LPDC 공정을 최적화하기 위해 ProCAST 소프트웨어를 사용하여 연성 열유체 응력 해석 모델을 개발하는 것을 목표로 합니다. 주요 목표는 허브와 블레이드 접합부에서 관찰되는 열간 찢김 결함을 최소화하는 것입니다.
주요 연구 질문:
본 연구는 LPDC 공정 변수, 특히 다음 사항의 조정이 Al-Zn-Mg-Cu 합금 프로펠러의 열간 찢김 발생에 미치는 영향에 초점을 맞춥니다.
- 용탕 공급 온도 (Melt supply temperature)
- 초기 금형 온도 (Initial mold temperature)
- 허브와 블레이드 사이의 곡률 반경 (Curvature radius between the hub and blades)
연구 가설:
본 연구는 이러한 주조 변수와 기하학적 설계(곡률 반경)를 전략적으로 조정함으로써 열간 찢김을 최소화하고 LPDC Al-Zn-Mg-Cu 합금 프로펠러의 전반적인 품질과 구조적 무결성을 향상시킬 수 있다고 가정합니다.
4. 연구 방법론
연구 설계:
본 연구는 상용 ProCAST 소프트웨어를 사용한 시뮬레이션 기반 공정 최적화 접근 방식을 채택합니다. 시뮬레이션 결과는 추가 시뮬레이션과 대량 생산 환경에서의 실제 적용을 통해 검증됩니다. 비파괴 검사를 사용하여 시뮬레이션 결과를 확인합니다.
자료 수집 방법:
- 시뮬레이션 데이터: ProCAST 소프트웨어를 사용하여 연성 열유체 응력 해석을 수행하고 다양한 공정 조건에서 유효 소성 변형률(Effective Plastic Strain, EPS) 분포에 대한 데이터를 생성합니다.
- 실험적 검증: 최적화된 LPDC 변수를 사용하여 프로토타입 프로펠러를 제조합니다.
- 결함 분석: 최적화된 프로펠러와 상용 프로펠러 모두에서 내부 결함을 분석하기 위해 비파괴 X선 컴퓨터 단층 촬영(Computed Tomography, CT)을 사용합니다. 열간 찢김의 표면 미세 구조는 주사 전자 현미경(Scanning Electron Microscopy, SEM)을 사용하여 검사합니다.
분석 방법:
- 유한 요소법 (Finite Element Method, FEM): ProCAST 소프트웨어는 열유체 응력 해석에 FEM을 사용합니다.
- 유효 소성 변형률 (Effective Plastic Strain, EPS) 모델: ProCAST 내의 EPS 모델은 열간 찢김 민감성을 예측하는 데 사용됩니다. EPS는 응고 중 각 부분에서 누적된 총 소성 변형률로 정의됩니다. 응력 분석은 수지상 응집점(dendrite coherency point)을 고려하여 0.5 이상의 고상 분율부터 시작하여 수행됩니다.
연구 대상 및 범위:
본 연구는 Al-6Zn-2Mg-1.5Cu 합금을 사용하여 프로펠러를 제조하는 LPDC 공정에 초점을 맞춥니다. 범위는 다음을 포함합니다.
- ProCAST를 사용한 LPDC 공정 시뮬레이션.
- 용탕 공급 온도 (680~820 °C), 초기 금형 온도 (200~500 °C) 및 곡률 반경 (4.0 mm 및 4.6 mm)이 열간 찢김에 미치는 영향 조사.
- 실제 제조 및 결함 분석을 통한 시뮬레이션 결과 검증.
5. 주요 연구 결과:
주요 연구 결과:
- EPS 예측 정확도: EPS 모델을 사용한 시뮬레이션은 실제 프로펠러 주조에서 관찰된 열간 찢김 위치를 정확하게 예측하여 모델의 효과를 검증했습니다.
- 곡률 반경 최적화: 허브-블레이드 접합부의 곡률 반경을 4.6 mm에서 4.0 mm로 줄임으로써 최대 EPS 값이 "0.085에서 0.058"로 크게 감소하여 (그림 4) 열간 찢김 민감성이 감소했음을 나타냅니다. 이는 접합부에서 더 부드러운 전환 구조가 변형 집중을 분산시키는 것을 시사합니다.
- 초기 금형 온도 효과: 초기 금형 온도를 200 °C에서 500 °C로 높임으로써 최대 EPS 값이 "0.065에서 0.051"로 감소하여 (그림 6) 더 높은 금형 온도가 열간 찢김 억제에 도움이 됨을 입증했습니다.
- 용탕 공급 온도 효과: 용탕 공급 온도 (680 °C ~ 820 °C)를 변경하는 것은 테스트 범위 내에서 열간 찢김에 미치는 영향이 미미했습니다. "최대값 0.059와 최소값 0.052의 차이를 고려할 때, 유의미한 효과는 관찰되지 않았습니다." (그림 5).
- 불균일 금형 온도: 금형 예열 및 사이클 분석을 반영하여 불균일 금형 온도 분포를 고려한 시뮬레이션은 균일 금형 온도 조건에 비해 더 높은 냉각 속도와 증가된 EPS 값을 초래할 수 있음을 보여주었습니다 (그림 7). "그림 7의 결과에 대해 열간 찢김 영역 근처의 평균 냉각 속도를 계산했을 때, 균일 온도 조건과 불균일 온도 조건은 각각 약 1.9 °C/s 및 4.4 °C/s의 냉각 속도를 나타냈습니다."
통계적/정성적 분석 결과:
- EPS 값: 다양한 곡률 반경 및 초기 금형 온도에 대한 시뮬레이션에서 정량적 EPS 값을 얻어 최적화된 변수에 따른 열간 찢김 가능성 감소를 입증했습니다.
- 냉각 속도: 냉각 속도 분석 결과 초기 금형 온도가 냉각 속도에 상당한 영향을 미치고, 이는 다시 열간 찢김 민감성에 영향을 미치는 것으로 나타났습니다.
- 육안 검사 및 SEM: 육안 검사 및 SEM 분석 (그림 3)을 통해 초기 프로토타입의 허브-블레이드 접합부에서 열간 찢김이 발생했음을 확인하고 파단면을 특성화했습니다.
- X선 CT 분석: X선 CT 분석 (그림 9) 결과 최적화된 프로펠러에서 내부 결함(수축 공동 및 기공)이 상용 Al-7Si-0.3Mg 프로펠러에 비해 크게 감소한 것으로 나타났습니다.
데이터 해석:
실험적 관찰 및 비파괴 검사로 검증된 시뮬레이션 결과는 LPDC 공정에서 곡률 반경을 최적화하고 초기 금형 온도를 높이는 것이 Al-Zn-Mg-Cu 합금 프로펠러의 열간 찢김을 효과적으로 감소시킨다는 것을 보여줍니다. 균일한 금형 온도 유지는 열간 찢김을 최소화하는 데에도 중요합니다.
그림 목록:
- 그림 1. 프로펠러 LPDC 공정의 시뮬레이션 모델
- 그림 2. 프로펠러 허브와 블레이드 사이의 곡률 반경 조건
- 그림 3. Al-6Zn-2Mg-1.5Cu 프로펠러의 열간 찢김
- 그림 4. 프로펠러 블레이드와 허브 사이의 곡률 반경에 따른 EPS 예측 시뮬레이션 결과
- 그림 5. 최대 EPS 영역에서 용탕 공급 온도가 EPS 및 냉각 속도에 미치는 영향에 대한 시뮬레이션 결과
- 그림 6. 최대 EPS 영역에서 초기 금형 온도가 EPS 및 냉각 속도에 미치는 영향에 대한 시뮬레이션 결과
- 그림 7. 초기 금형 온도 조건 및 결과 EPS 예측
- 그림 8. 개발된 Al-6Zn-2Mg-1.5Cu 합금 프로펠러
- 그림 9. CT 분석을 통한 알루미늄 합금 프로펠러의 내부 결함 조사
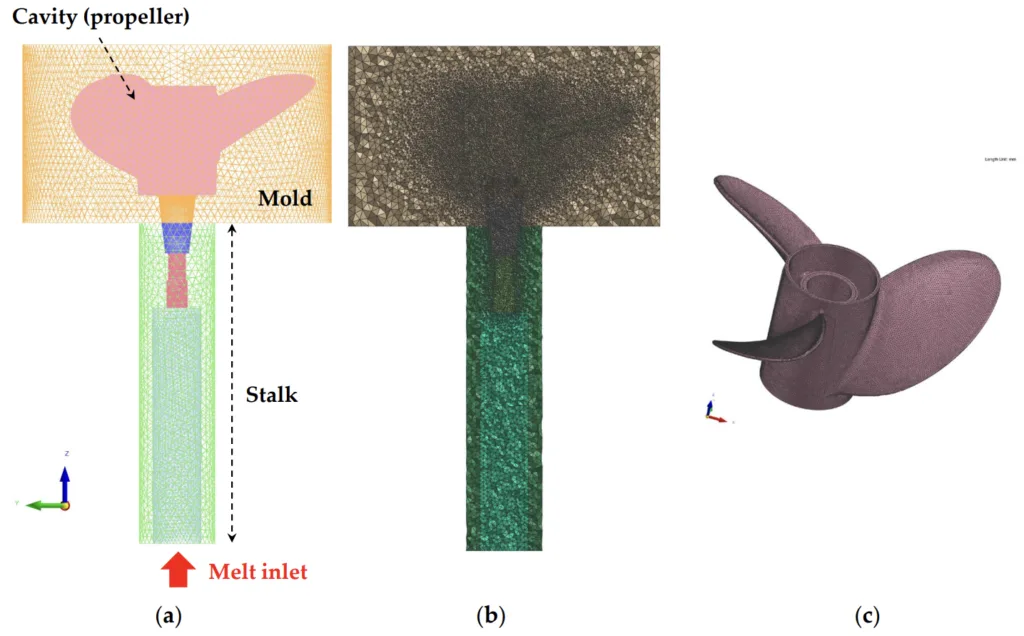
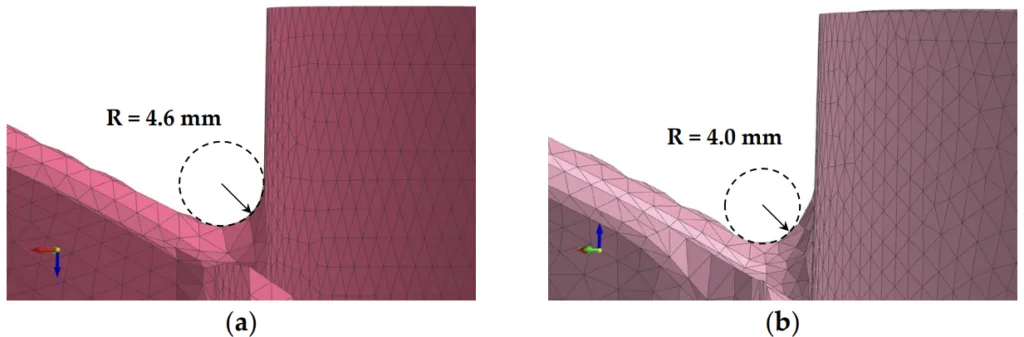
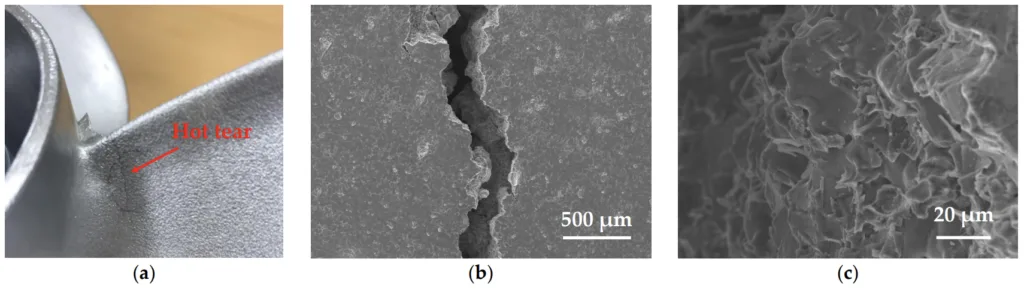
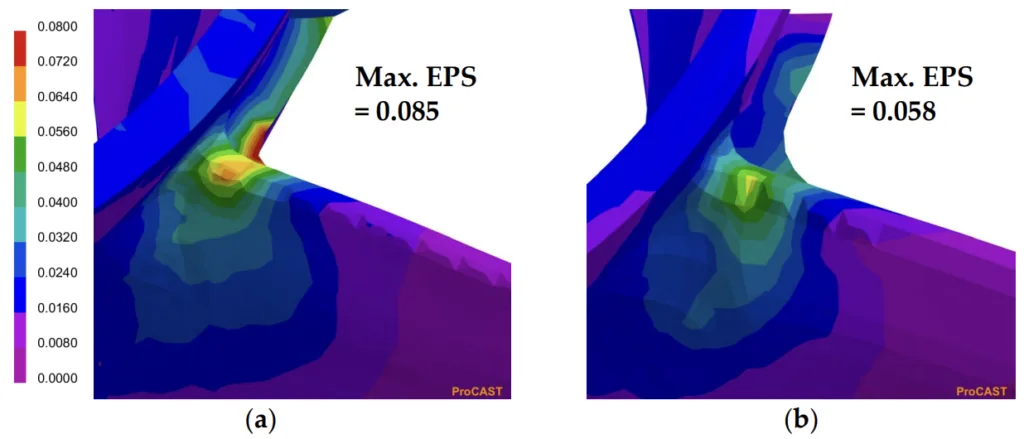
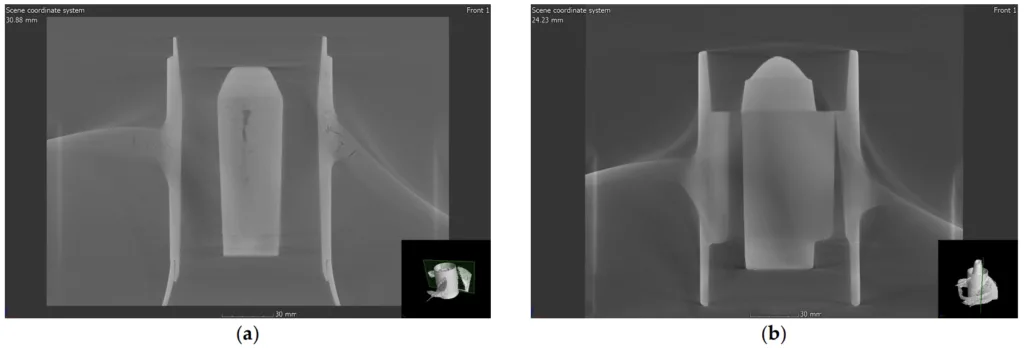
6. 결론 및 논의:
주요 결과 요약:
본 연구는 ProCAST 소프트웨어를 사용한 시뮬레이션 기반 공정 최적화를 통해 Al-Zn-Mg-Cu 합금 프로펠러용 LPDC 공정을 성공적으로 최적화했습니다. 주요 결과는 다음과 같습니다. 최적화된 곡률 반경과 증가된 초기 금형 온도는 열간 찢김을 효과적으로 감소시킵니다. 용탕 공급 온도는 테스트 범위 내에서 영향이 미미합니다. 균일한 금형 온도 유지가 유익합니다. 이러한 최적화된 조건을 실제 적용한 결과 열간 찢김 및 내부 결함이 최소화된 고품질 프로펠러가 생산되었으며, 이는 X선 CT 분석으로 검증되었습니다.
연구의 학문적 의의:
본 연구는 다이캐스팅 공정, 특히 고강도 알루미늄 합금의 열간 찢김 완화를 위한 시뮬레이션 기술의 효과와 실용성을 입증합니다. 또한 자원이 제한된 중소기업조차도 시뮬레이션 도구를 활용하여 효율적인 제품 개발 및 공정 개선을 달성할 수 있음을 강조합니다.
실용적 의미:
본 연구에서 확인된 최적화된 LPDC 공정 변수는 열간 찢김 및 내부 결함이 크게 감소된 고품질 Al-Zn-Mg-Cu 합금 프로펠러를 대량 생산하기 위한 실용적인 지침을 제공합니다. 연구 결과는 결함 없는 LPDC 부품을 달성하는 데 있어 곡률 반경 설계, 초기 금형 온도 제어 및 균일한 금형 온도 관리의 중요성을 강조합니다.
연구의 한계:
본 연구는 특정 주조 조건을 제어하여 열간 찢김의 경향을 이해하는 데 주로 초점을 맞추었습니다. 시뮬레이션과 실험적 검증이 일치하지만, 대량 생산 조건에서 다른 잠재적 결함과 여러 변수의 상호 작용을 탐구하고 최적화하기 위해서는 추가 연구가 필요할 수 있습니다.
7. 향후 후속 연구:
후속 연구 방향:
향후 연구 방향에는 입증된 시뮬레이션 기술과 머신 러닝 기술의 통합이 포함됩니다. 이러한 통합은 다이캐스팅 공정 최적화 연구 개발의 효율성과 효과를 더욱 향상시켜 보다 정교한 예측 모델과 자동화된 공정 제어 전략으로 이어질 수 있습니다.
추가 탐구가 필요한 영역:
추가 탐구는 다른 주조 결함 및 기계적 물성을 고려한 보다 포괄적인 다목적 최적화에 초점을 맞추고, 시뮬레이션 기반 최적화 접근 방식을 다른 복잡한 다이캐스팅 부품 및 합금 시스템으로 확장할 수 있습니다.
8. 참고 문헌:
- Kluczyk, M.; Grządziela, A.; Batur, T. Design and operational diagnostics of marine propellers made of polymer materials. Pol. Marit. Res. 2022, 29, 49–59.
- Cass, A.; Nielson, J.R. Smart energy systems approach to zero emissions long-range sailing vessels. Smart Energy 2022, 7, 100086.
- Oloruntobi, O.; Mokhtar, K.; Gohari, A.; Asif, S. Sustainable transition towards greener and cleaner seaborne shipping industry: Challenges and opportunities. Clean. Eng. Technol. 2023, 13, 100628.
- Baley, C.; Davies, P.; Troalen, W.; Chamley, A.; Dinham-Price, I.; Marchandise, A.; Keryvin, V. Sustainable polymer composite marine structure: Developments and challenges. Prog. Mater. Sci. 2024, 145, 101307.
- Dashtimanesh, A.; Ghaemi, M.H.; Wang, Y. Digitalization of high speed craft design and operation challenges and opportunities. Procedia Comput. Sci. 2022, 200, 566–576.
- Begovic, E.; Bertorello, C.; De Luca, F. KISS (Keep It Sustainable and Smart): A research and development program for a zero-emission small crafts. J. Mar. Sci. Eng. 2022, 10, 16.
- Choudhary, G.; Singh, G. Comparative analysis of corrosion behaviour of stainless steel grades 304 and 316L for different applications. I-Manag. J. Mater. Sci. 2020, 7, 8–22.
- Mendagaliev, R.; Klimova-Korsmik, O.; Promakhov, V.; Schulz, N.; Zhukov, A.; Klimenko, V.; Olisov, A. Heat treatment of corrosion resistant steel for water propellers fabricated by direct laser deposition. Materials 2020, 13, 2738.
- Konieczny, J.; Labisz, K. Materials used in the combat aviation construction. Transp. Probl. 2021, 16, 5–18.
- Kim, M.S.; Kim, J. Development of low-pressure die-cast Al—Zn—Mg—Cu alloy propellers—Part I: Hot tearing simulations for alloy optimization. Materials 2024, 17, 3133.
- Pulisheru, K.S.; Birru, A.K. Effect of pouring temperature on hot tearing susceptibility of Al-Cu cast alloy: Casting simulation. Mater. Today Proc. 2021, 47, 7086–7090.
- Rahangmetan, K.A.; Sariman, F.; Parenden, D. The effect of riser use in the quality of casting Al 7075 for ship propeller. Int. J. Mech. Eng. Technol. 2019, 10, 10–17.
- Dong, G.; Li, S.; Ma, S.; Zhang, D.; Bi, J.; Wang, J.; Starostenkov, M.D.; Xu, Z. Process optimization of A356 aluminum alloy wheel hub fabricated by low-pressure die casting with simulation and experimental coupling methods. J. Mater. Res. Tehnol. 2023, 24, 3118–3132.
- Khan, M.A.A.; Sheikh, A.K. A comparative study of simulation software for modelling metal casting processes. Int. J. Simul. Model. 2018, 17, 197–209.
- Wei, C.; Ou, J.; Mehr, F.F.; Maijer, D.; Cockcroft, S.; Wang, X.; A, L.; Chen, Z.; Zhu, Z. A thermal-stress modelling methodology in ABAQUS for fundamentally describing the die/casting interface bahaviour in a cyclic permanent die casting process. J. Mater. Res. Technol. 2021, 15, 5252–5264.
- Zhnag, B.; Maijer, D.M.; Cockcroft, S.L. Development of a 3-D thermal model of the low-pressure die-cast (LPDC) process of A356 aluminum alloy wheels. Mater. Sci. Eng. A 2007, 464, 295–305.
- Ou, J.; Wei, C.; Cockcroft, S.; Maijer, D.; Zhu, L.; A, L.; Li, C.; Zhu, Z. Advanced process simulation of low pressure die cast A356 aluminum automotive wheels—Part II modeling methodology and validation. Metals 2020, 10, 1418.
- Sun, J.; Le, Q.; Fu, L.; Bai, J.; Tretter, J.; Herbold, K.; Huo, H. Gas entrainment behavior of aluminum alloy engine crankcases during the low-pressure-die-casting process. J. Mater. Process. Technol. 2019, 266, 274–282.
- Song, J.; Pan, F.; Jiang, B.; Atrens, A.; Zhang, M.; Lu, Y. A review on hot tearing of magnesium alloys. J. Magnes. Alloy 2016, 4, 151–172.
- Chen, Z.; Li, Y.; Zhao, F.; Li, S.; Zhang, J. Process in numerical simulation of casting process. Meas. Control 2022, 55, 257–264.
- Ren, Y.; Zhang, S.; Liu, T.; Bao, C.; Song, H. Prediction of hot tearing and grain structure in TiAl alloy casting. Int. J. Met. 2024, 18, 799–809.
- Dubey, S.; Swain, R. Numerical investigation on solidification in casting using ProCAST. IOP Conf. Ser. Mater. Sci. Eng. 2019, 561, 012049.
- Li, Y.; Zhang, Z.R.; Zhao, Z.Y.; Li, H.X.; Katgerman, L.; Zhang, J.S.; Zhuang, L.Z. Effect of main elements (Zn, Mg, and Cu) on hot tearing susceptibility during direct-chill casting of 7xxx aluminum alloys. Metall. Mater. Trans. A 2019, 50, 3603–3616.
- Kim, J.H.; Jo, J.S.; Sim, W.J.; Im, H.J. The influence of alloy composition on the hot tear susceptibility of the Al-Zn-Mg-Cu alloy system. Korean J. Met. Mater. 2012, 50, 669–675.
- Guo, J.; Samonds, M.T. Alloy thermal physical property prediction coupled computational thermodynamics with back diffusion consideration. J. Ph. Equilibr. Diffus. 2007, 28, 58–63.
- Wang, H.; Alexandrov, B.T.; Przybylowicz, E. Experimental and numerical modeling study of solidification cracking in alloy 52M filler metal in the cast pin tear test. Weld. World 2019, 63, 913–924.
- Dahle, A.K.; Arnberg, L. Development of strength in solidifying aluminium alloys. Acta Mater. 1997, 45, 547–559.
- Ha, Y.S.; Kwon, J.B.; Yang, W.J.; Seo, J.K. Application of industrial 3D X-ray CT (computed tomography) to improve reliability of additive manufacturing technology. In Proceedings of the 34th International Ocean and Polar Engineering Conference, Rhodes, Greece, 16-21 June 2024.
- Clyne, T.W.; Wolf, M.; Kurz, W. The effect of melt composition on solidification cracking of steel, with particular reference to continuous casting. Metall. Trans. B 1982, 13B, 259–266.
- Li, Y.; Li, H.; Katgerman, L.; Du, Q.; Zhang, J. Recent advances in hot tearing during casting of aluminium alloys. Prog. Mater. Sci. 2021, 117, 100741.
- Dutta, B.; Pompe, O.; Rettenmayr, M. Quantitative image analysis for evaluation of eutectic fractions in as cast microstructures. Mater. Sci. Technol. 2004, 20, 1011–1018.
- Zhang, L.Y.; Jiang, Y.H.; Ma, Z.; Shan, S.F.; Jia, Y.Z.; Fan, C.Z.; Wang, W.K. Effect of cooling rate on solidified microstructure and mechanical properties of aluminium-A356 alloy. J. Mater. Process. Technol. 2008, 207, 107–111.
9. 저작권:
본 자료는 김민석, 원순호의 논문 "Development of Low-Pressure Die-Cast Al-Zn-Mg-Cu Alloy Propellers Part II: Simulations for Process Optimization"을 기반으로 합니다.
논문 출처: https://doi.org/10.3390/ma17164027
본 자료는 상기 논문을 기반으로 요약되었으며, 상업적 목적으로 무단 사용하는 것을 금지합니다.
Copyright © 2025 CASTMAN. All rights reserved.