본 소개 자료는 "[INTERNATIONAL JOURNAL OF INNOVATIONS IN ENGINEERING RESEARCH AND TECHNOLOGY [IJIERT] (NOVATEUR PUBLICATIONS)]"에서 발행한 "[DEVELOPMENT AND APPLICATION OF CASTING DISTORTION & COMPENSATION TECHNOLOGY BASED ON AUTOMATIC ITERATION METHOD]" 논문을 기반으로 합니다.
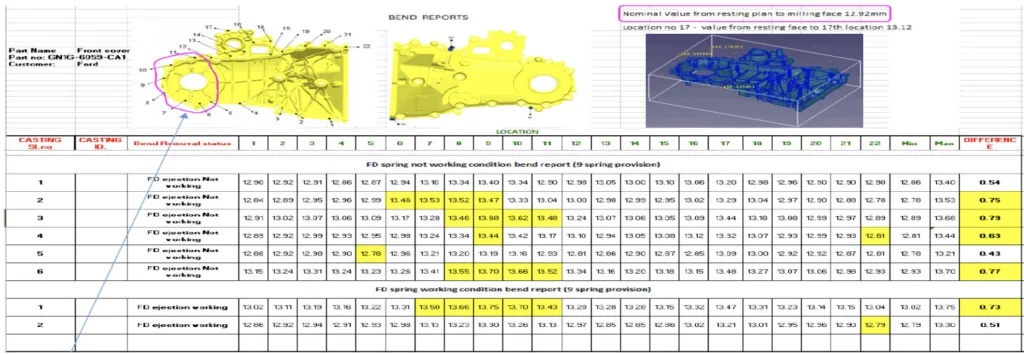
1. 개요:
- 제목: DEVELOPMENT AND APPLICATION OF CASTING DISTORTION & COMPENSATION TECHNOLOGY BASED ON AUTOMATIC ITERATION METHOD (자동 반복법 기반 주조 변형 및 보정 기술 개발 및 적용)
- 저자: DR. XIAOJUN YANG, MS. RAJESHWARI SANJAY RAWAL
- 발행 연도: 2020
- 발행 학술지/학회: INTERNATIONAL JOURNAL OF INNOVATIONS IN ENGINEERING RESEARCH AND TECHNOLOGY [IJIERT] (NOVATEUR PUBLICATIONS)
- 키워드: Die-casting, casting warp, distortion, compensation, automatic iteration, Cast-Designer, DCS (Distortion Compensation Solver), thermal stress, mechanical stress, finite element method.
2. 초록:
주조 휨 또는 변형은 다이캐스팅 생산에서 자주 발생하는 주요 결함 중 하나이며 해결하기 매우 어렵습니다. 전통적인 방법들은 낮은 효율성, 과도한 작업량, 열악한 작업 환경 등의 문제를 가지고 있습니다. 본 논문은 Cast-Designer의 새로 개발된 변형 보정 솔버인 DCS (Distortion Compensation Solver)를 소개합니다. 이 솔버는 사전에 주조 변형 및 휨을 예측하고, 자동 반복 최적화 기술을 통해 공차 요구사항을 만족하는 주조 제품을 찾을 수 있습니다. 이러한 도구와 기술을 통해 주조 변형을 효과적으로 줄이고 가공 요구사항을 직접적으로 만족시킬 수 있습니다.
3. 서론:
첨단 제조 기술로서 다이캐스팅은 높은 치수 정밀도, 우수한 기계적 특성, 높은 생산 효율성 등의 장점을 가지며, 자동차용 알루미늄 및 알루미늄-마그네슘 합금 부품 생산에서 강력한 기술적, 경제적 이점을 제공합니다. 그러나 여러 이유로 많은 다이캐스팅 알루미늄 부품들이 초기 설계 단계에서 제조 요인을 거의 고려하지 않습니다. 복잡한 구조, 큰 벽 두께 차이, 높은 정밀도 요구는 다이캐스팅 개발 및 생산에 큰 어려움을 야기합니다. 그중에서도 변형 및 휨 결함은 복잡한 주조품에서 흔하고 제어하기 어려운 문제 중 하나입니다. 주조 변형 결함은 부적절한 주조품 설계, 불균형한 이젝팅, 금형 온도 불균형 등 여러 원인에 의해 발생합니다. 변형 결함이 주조품 품질에 미치는 영향은 주로 다음과 같습니다: 1) 주조품의 치수 정밀도에 영향을 미침; 2) 후속 가공에 영향을 미침; 3) 주조 후 가공 깊이가 너무 깊은 부품의 경우, 주조품 표면의 치밀층 제거로 인해 내부의 기공 결함(기공 및 수축 등)이 노출되어 주조품의 외관 및 밀봉 성능(밀봉 요구사항이 있는 부품의 경우)에 영향을 미침.
4. 연구 요약:
연구 주제 배경:
주조 변형(휨)은 다이캐스팅 생산에서 중요하고 해결하기 어려운 결함입니다. 이는 부적절한 주조품 설계, 이젝팅 시 불균형한 힘, 불균일한 금형 온도 등 다양한 원인에서 비롯됩니다. 이 결함은 주조품의 치수 정밀도를 저해하고 필요한 후속 가공 작업을 복잡하게 만듭니다. 주조 후 상당한 재료 제거가 필요한 부품의 경우, 변형으로 인해 기공 및 수축과 같은 내부 결함이 노출될 수 있습니다.
기존 연구 현황:
주조 변형 관리를 위한 전통적인 방법들은 다음과 같습니다:
- 방법 1: 공정 변수 조정: 금형 설계, 스프레이 냉각, 다이캐스팅 공정 변수 조정을 통해 변형을 제어합니다. 이 방법은 항상 요구되는 공차를 달성하지 못할 수 있으며 공정 안정성 문제가 있습니다.
- 방법 2: 주조 여유 증가: 가공을 위해 추가 재료를 더합니다. 이는 벽 두께를 증가시켜 내부 결함(기공, 수축)을 악화시키고 가공 중 노출 위험을 높일 수 있습니다. 이상적인 해결책으로 간주되지 않습니다.
- 방법 3: 인공 교정 방법: 냉각 후 도구를 사용하여 수동으로 치수를 교정합니다. 이는 비효율적이고, 노동 집약적이며, 소음이 많고, 결과가 좋지 않으며, 균열 위험이 있고, 실제 생산에서 스프링백이 발생할 수 있습니다.
- 방법 4: 고온 교정(Hot Orthotics): 아직 뜨거울 때(약 200°C) 교정 금형에서 주조품을 압착하여 변형을 줄입니다. 이는 복잡한 공정과 상당한 냉각을 필요로 합니다.
이러한 전통적인 접근 방식은 종종 낮은 효율성, 과도한 작업량, 열악한 작업 환경을 수반합니다.
연구 목적:
본 논문은 Cast-Designer의 새로 개발된 Distortion Compensation Solver (DCS)를 소개합니다. 이 연구는 사전에 주조 변형 및 휨을 예측하고 자동 반복 최적화를 활용하여 공차 요구사항을 만족하는 주조 제품을 찾는 기술을 시연하는 것을 목표로 합니다. 목표는 주조 변형을 효과적으로 줄이고 전통적인 방법의 한계를 극복하여 가공 요구사항을 직접적으로 만족시키는 것입니다.
핵심 연구:
연구의 핵심은 Cast-Designer 소프트웨어 제품군 내에서 개발된 Distortion Compensation Solver (DCS) 기술에 초점을 맞춥니다. 이 기술은 자동 반복법을 사용합니다. 이는 유한 요소 해석을 사용하여 열 및 기계적 응력과 그로 인한 변형을 계산하는 주조 공정의 정확한 시뮬레이션으로 시작합니다. 예측된 변형을 기반으로 DCS는 예측된 변형의 반대 방향으로 보정을 적용하여 금형 캐비티 형상을 반복적으로 수정합니다. 이 과정은 응고 및 냉각 후 최종 주조품이 지정된 치수 공차 내에 있도록 하는 것을 목표로 합니다.
5. 연구 방법론
연구 설계:
연구 방법론은 Cast-Designer 소프트웨어를 사용하여 특정 자동차 부품의 다이캐스팅 공정을 시뮬레이션하는 것을 포함했습니다. 시뮬레이션은 열 및 기계적 응력과 그로 인한 변형을 정확하게 예측하는 데 중점을 두었습니다. 이러한 시뮬레이션 결과는 실제 주조 부품에서 측정한 평탄도 측정값과 비교하여 검증되었습니다. 이후, 예측된 변형을 기반으로 부품 형상을 수정하기 위해 자동 반복 접근 방식을 사용하는 Distortion Compensation Solver (DCS)가 적용되었으며, 최종 주조 부품의 변형을 최소화하는 것을 목표로 했습니다.
데이터 수집 및 분석 방법:
- 데이터 수집:
- 시뮬레이션 데이터는 Cast-Designer의 응력 모듈을 사용하여 생성되었으며, 열, 유동 및 응력 현상의 완전 연성 해석(full-coupling analysis)을 수행했습니다. 시뮬레이션은 금형 구속 조건, 금형 개방, 재료 특성(탄소성 모델), 공정 변수(예: 금형 개방 시간, 이젝션 온도, 냉각)를 고려했습니다.
- 물리적 데이터는 한 배치에서 무작위로 선택된 6개의 주조 부품의 평탄도를 정의된 22개의 측정 지점을 사용하여 측정하여 수집했습니다.
- 분석 방법:
- 시뮬레이션된 변형(평탄도) 결과는 물리적 테스트 피스(특히 샘플 No. 2, 3, 4)의 실제 평탄도 측정값과 비교하여 시뮬레이션 정확도를 검증했습니다.
- DCS는 자동 반복 보정 방법을 사용했습니다. 한 반복에서 계산된 변형을 기반으로 다음 반복을 위해 메쉬 노드 좌표를 조정하기 위해 보정 계수가 적용되었습니다. 이 과정은 최종 주조품의 예측된 변형이 사용자가 정의한 공차 요구사항을 만족할 때까지 반복되었습니다.
연구 주제 및 범위:
- 연구 주제: 이 연구는 고압 다이캐스팅에서 주조 변형 및 휨 예측과 이러한 결함을 최소화하기 위한 자동 반복 보정 방법(DCS)의 적용을 조사했습니다. 주요 주제에는 정확한 응력/변형률 시뮬레이션(열 및 기계적), 시뮬레이션 검증, 보정을 위한 형상 수정이 포함되었습니다.
- 범위: 연구는 Ford용 "Front cover"(부품 번호: GN1G-6059-CA1)로 식별된 특정 복합 자동차 주조 부품에 적용되었습니다. 부품 치수는 438 X 350 X 145mm이고 평균 벽 두께는 3.3mm였습니다. 연구는 주조 및 냉각 후 특정 표면에서 0.5mm의 평탄도 요구사항을 달성하는 데 중점을 두었습니다.
6. 주요 결과:
주요 결과:
- Cast-Designer를 사용하여 열 전달, 응고, 금형 구속 조건, 금형 개방과 같은 요인을 고려하여 다이캐스팅 공정 중 응력(열 및 기계적) 및 변형의 정확한 시뮬레이션이 달성되었습니다.
- 부품 평탄도에 대한 시뮬레이션 결과는 물리적 테스트 피스(No. 2, 3, 4)에서 얻은 실제 평탄도 측정값과 매우 잘 일치하여 시뮬레이션 모델을 검증했습니다 (Figure 3).
- Distortion Compensation Solver (DCS)는 자동 반복 보정 방법을 성공적으로 적용했습니다. 초기 시뮬레이션된 변형은 0.5mm 평탄도 공차를 초과했습니다(0.8mm 이상 도달).
- DCS를 사용한 4번의 자동 반복 계산 후, 실온으로 냉각된 후 주조품의 최종 예측 평탄도는 0.05mm에서 0.15mm 사이로 유지되었습니다.
- 이 결과는 보정된 금형 형상을 사용하여 주조된 제품이 지정된 공차 내에서 직접 공급 가공 생산 요구사항을 100% 만족할 것임을 나타냅니다.
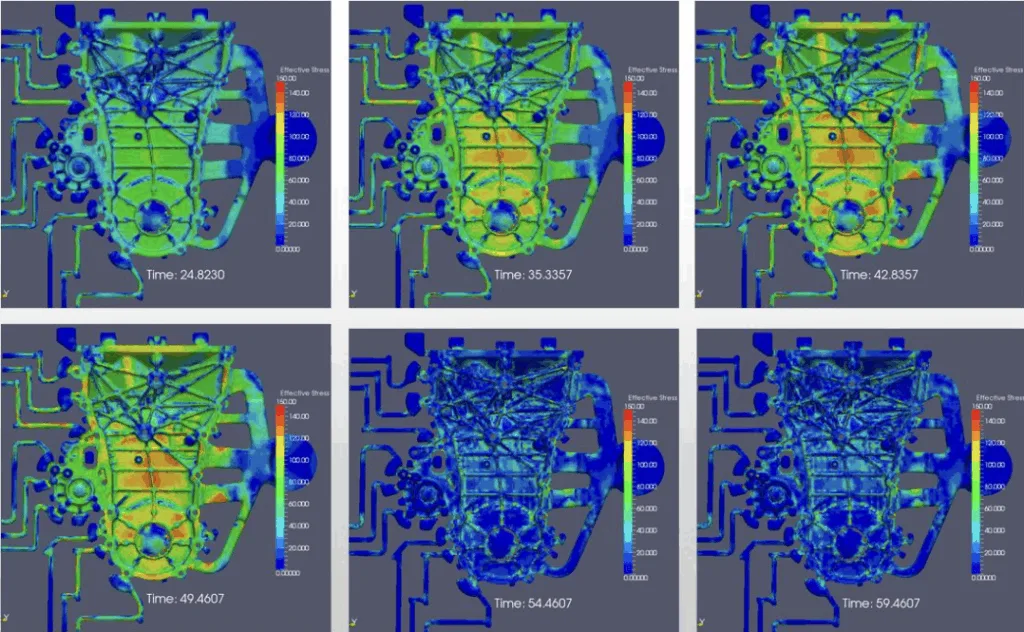
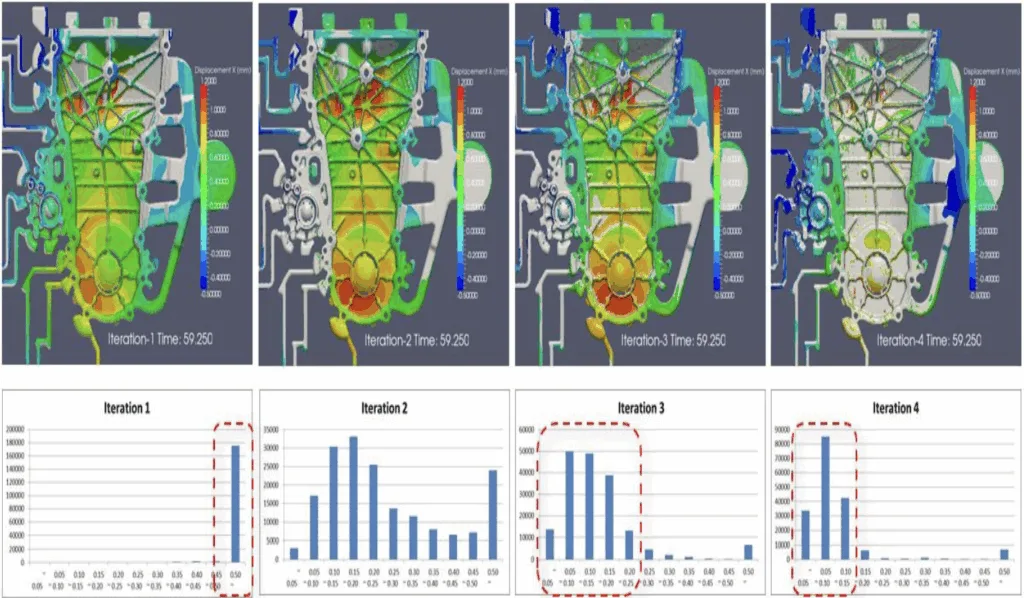
그림 이름 목록:
- Figure 1 Casting part and dimension after casting, the yellow cells are out of tolerance
- Figure 2 Effective stress contours vs. Time
- Figure 3 Part flatness analysis (simulation results vs. the actual measurement results)
- Figure 4 The first line: left: before casting right: after casting The second line with compensation: left: before casting right: after casting
- Figure 5 The compensation result after four iterations
7. 결론:
컴퓨터 시뮬레이션과 자동 반복 보정 방법을 사용하면 주조 변형 및 왜곡 문제를 효과적으로 해결할 수 있습니다. 이 방법은 통신 제품, 방열판, 커버, 자동차 부품 등과 같은 복잡한 형상의 주조에 효과적입니다.
대량 주문이나 체인 커버, 오일 패널, 전기차 전기 커버 및 기타 주조품과 같이 평탄한 구조와 평탄도 요구사항이 큰 자동차 부품의 경우, 변형 보정 기술을 적용하면 효율성을 향상시키고 인건비를 절감할 수 있습니다.
8. 참고 문헌:
- [1] A.A. Luo, “Magnesium casting technology for structure applications," Journal of Magnesium and Alloys, vol. 1, pp. 2–22, 2013.
- [2] K.K.S. Thong, B.H. Hu, X.P. Nui and I. Pinwill, “Cavity pressure measurements and process monitoring for magnesium die casting of a thin-wall-hand-phone component to improve quality,” J. Mater. Process. Tech., vol. 127, pp. 238–241, 2002.
- [3] Piyanut Meethum, Chakrit Suvanjumrat,“Evaluate of Chill Vent Performance for High Pressure Die-Casting Production and Simulation of Motorcycle Fuel Caps”, MATEC Web of Conferences 95, 07025 (2017) DOI: 10.1051/matecconf/2017950 ,ICMME 2016
- [4] P. Meethum, C. Suvanjumrat, “Porosities Comparison between Production and Simulation in Motorcycle Fuel Caps of Aluminum High Pressure Die Casting", World Academy of Science, Engineering and Technology International Journal of Mechanical and Mechatronics Engineering Vol:9, No:3, 2015.
9. 저작권:
- 본 자료는 "DR. XIAOJUN YANG, MS. RAJESHWARI SANJAY RAWAL"의 논문입니다. "[DEVELOPMENT AND APPLICATION OF CASTING DISTORTION & COMPENSATION TECHNOLOGY BASED ON AUTOMATIC ITERATION METHOD]"를 기반으로 합니다.
- 논문 출처: [논문에 DOI URL이 제공되지 않음]
본 자료는 상기 논문을 바탕으로 요약되었으며, 상업적 목적의 무단 사용을 금지합니다.
Copyright © 2025 CASTMAN. All rights reserved.