본 소개 자료는 "[IEICE Electronics Express]"에 게재된 "[Thermal management technology of high-power light-emitting diodes for automotive headlights]" 논문을 기반으로 작성되었습니다.
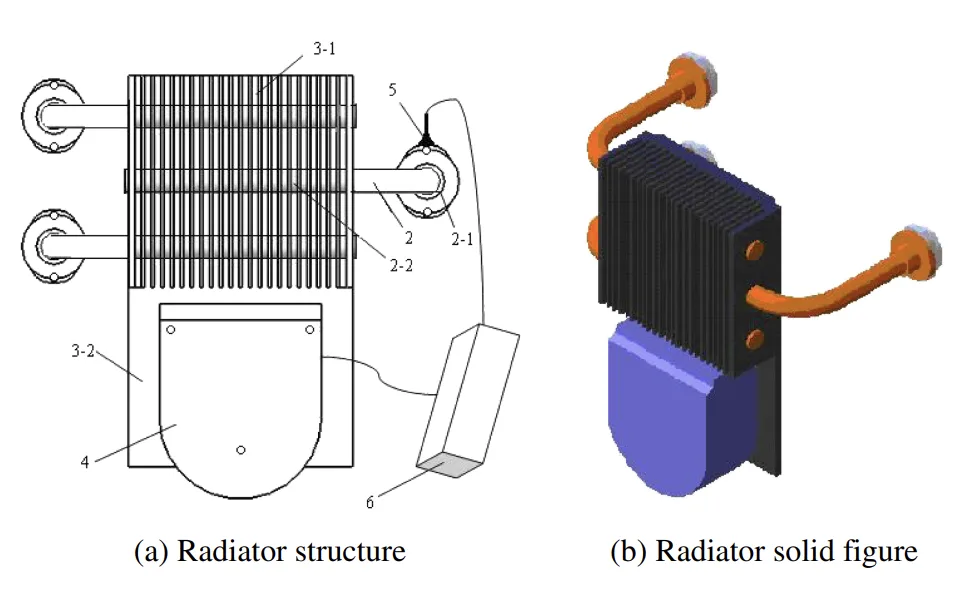
1. 개요:
- 논문 제목(Title): Thermal management technology of high-power light-emitting diodes for automotive headlights
- 저자(Author): Hui-Ming Qu, Xiao-Hui Yang, Qi Zheng, Xin-Tao Wang, and Qian Chen
- 발행 연도(Year of publication): 2014
- 학술지/학회(Journal/academic society of publication): IEICE Electronics Express
- 키워드(Keywords): LED automotive headlight, thermal management, cooling structure, thermal simulation, temperature feedback
2. 초록 (Abstract):
고출력 LED(발광 다이오드)의 방열 문제는 자동차 헤드라이트에서의 응용을 제한합니다. LED 헤드라이트 냉각을 위한 열 수요는 열전달 이론을 기반으로 분석됩니다. 본 연구는 온도 피드백 제어와 히트 파이프 및 히트 싱크를 결합한 능동적 방열 기술을 제안합니다. 해당 하드웨어 및 소프트웨어 제어 프로세스가 설계되었습니다. 온도 피드백 제어는 MCU(마이크로 컨트롤 유닛)를 통해 구현되며, 이는 합성 제트 장치의 작동 과정을 판단하고 제어합니다. 히트 파이프 라디에이터의 3D 모델은 CATIA를 사용하여 구성됩니다. 이 모델은 유체 열역학 시뮬레이션 소프트웨어인 FLOEFD로 최적화됩니다. 마지막으로, 샘플 램프를 제작하여 적외선 온도계로 테스트합니다. 각 LED 광원 및 라디에이터 핀의 온도 분포를 정량적으로 측정하고 분석합니다. 이러한 결과는 열 관리 시스템 설계와 제안된 기술이 실제로 50°C의 주변 온도에서 고출력 LED 자동차 헤드라이트의 방열 문제를 해결함을 확인시켜 줍니다.
3. 서론 (Introduction):
발광 다이오드(LED)는 작은 크기, 긴 수명, 낮은 에너지 소비, 진동 저항성, 빠른 시동 시간 및 환경 친화성으로 인해 자동차 조명에 점점 더 많이 사용되고 있습니다. 고출력, 고휘도 백색 LED는 자동차 헤드라이트의 유력한 후보가 되어 "4세대" 조명으로 자리매김하고 있습니다. 그러나 LED의 낮은 전기-광학 변환 효율은 입력 전력의 상당 부분이 열로 변환되어 접합 온도를 상승시킵니다. 높은 접합 온도는 낮은 양자 효율, 파장 이동, 짧은 수명 및 치명적인 고장과 같은 신뢰성 문제를 야기할 수 있습니다. 따라서 적절한 열 관리는 고효율 조명 시스템, 특히 엔진룸 근처의 까다로운 환경에서 작동하며 높은 밀봉성, 내충격성, 고온에서의 안정성 및 제한된 공간 내에서의 작동을 요구하는 자동차 헤드라이트에 LED를 채택하는 데 매우 중요합니다. 효과적인 열 설계는 LED 헤드라이트의 정상적인 작동을 보장하고 성능을 향상시키는 데 필수적입니다.
4. 연구 요약 (Summary of the study):
연구 주제의 배경 (Background of the research topic):
자동차 헤드라이트용으로 유망한 고출력 LED는 상당한 열을 발생시킵니다. 이 열이 효과적으로 관리되지 않으면 LED 접합 온도가 상승하여 성능 저하 및 수명 단축을 초래합니다. 자동차 헤드라이트는 높은 주변 온도와 제한된 공간을 포함한 열악한 조건에서 작동하므로 열 관리가 특히 어렵습니다.
선행 연구 현황 (Status of previous research):
LED 열 관리를 위한 다양한 방법이 연구되어 왔으며, 여기에는 핀-히트 싱크 [17] 및 히트 파이프 [18]와 같은 수동적 솔루션과 능동 냉각 시스템 [15, 16]이 포함됩니다. 기타 고급 방법으로는 마이크로 채널 히트 싱크 [12, 13], 마이크로 제트 어레이 냉각 [21, 22], 전기 유체 역학적 접근법 [23], 열전 냉각 [24], MEMS 기술을 이용한 상변화 방법 [25] 및 압전 팬 [26]이 있습니다. 그러나 이러한 전략들은 복잡한 설계, 신뢰성 문제, 높은 비용 또는 불충분한 냉각 능력을 수반할 수 있어, 특히 자동차 LED 헤드라이트의 까다로운 요구 사항에 대한 상용화를 저해합니다.
연구 목적 (Purpose of the study):
본 연구는 고출력 LED 자동차 헤드라이트의 냉각 요구 사항을 충족시키기 위해 온도 피드백 제어 방열과 결합된 효과적인 냉각 구조를 설계하는 것을 목표로 합니다. 목표는 고출력 LED 헤드라이트의 적용 및 보급을 제한하는 방열 문제를 해결하는 것입니다.
핵심 연구 내용 (Core study):
본 연구는 히트 파이프와 히트 싱크를 온도 피드백 제어와 결합한 능동적 방열 기술을 제안합니다. 이 시스템에는 다음이 포함됩니다:
- 3개의 통합 백색 LED 패키지와 해당 3개의 히트 파이프를 사용하는 LED 헤드라이트의 열전달 이론에 기반한 열 설계.
- 합성 제트가 히트 파이프 응축기 섹션 및 알루미늄 파이프 싱크와 함께 설치된 온도 피드백 능동 냉각 장치.
- 온도 센서를 통해 온도를 모니터링하고 합성 제트 장치를 제어하는 MCU(마이크로 컨트롤 유닛).
- CATIA를 사용한 히트 파이프 라디에이터 구조의 3D 모델링.
- 유체 열역학 시뮬레이션 소프트웨어 FLOEFD를 사용한 모델 최적화.
- 설계된 열 관리 시스템을 갖춘 샘플 램프의 적외선 온도계를 사용한 실험적 검증.
5. 연구 방법론 (Research Methodology)
연구 설계 (Research Design):
본 연구는 여러 단계로 진행되었습니다:
- LED 헤드라이트의 열전달 이론적 분석 및 냉각 시스템의 열 저항 모델 개발.
- 수동적 요소(히트 파이프, 히트 싱크 핀)와 능동적 요소(합성 제트 장치)를 통합한 냉각 시스템 설계.
- 온도 센서(DS18B20)와 MCU를 사용하여 합성 제트의 작동을 관리하는 온도 피드백 제어 시스템 통합.
- CATIA를 사용한 LED 헤드라이트 라디에이터의 3D 모델 구성.
- 특정 작동 조건에서 성능을 예측하기 위해 FLOEFD 소프트웨어를 사용한 설계된 라디에이터의 열 및 유체 역학 시뮬레이션.
- 설계를 기반으로 한 샘플 LED 헤드라이트 제작.
- 시뮬레이션 결과를 검증하고 열 관리 시스템의 효과를 평가하기 위한 샘플 램프의 실험적 테스트.
데이터 수집 및 분석 방법 (Data Collection and Analysis Methods):
- 시뮬레이션 (Simulation): FLOEFD 소프트웨어를 사용하여 라디에이터의 온도 분포와 공기 흐름 패턴을 시뮬레이션했습니다. 주요 결과에는 온도 등고선 및 다양한 지점에서의 최고 온도가 포함되었습니다.
- 실험 테스트 (Experimental Testing): 적외선 온도계를 사용하여 제어된 주변 온도의 밀폐된 공간에서 샘플 램프의 LED 광원 및 라디에이터 핀의 온도 분포를 측정했습니다. 실시간 온도 데이터를 기록하고 분석했으며, 특히 합성 제트 작동의 효과를 분석했습니다.
연구 주제 및 범위 (Research Topics and Scope):
본 연구는 특히 자동차 헤드라이트 응용 분야를 위한 고출력 LED의 열 관리에 중점을 두었습니다. 범위는 다음과 같습니다:
- 히트 파이프, 히트 싱크 및 MCU 제어 합성 제트를 결합한 하이브리드 냉각 시스템의 설계 및 분석.
- 자동차 사용과 관련된 조건(시뮬레이션의 경우 주변 온도 50°C, 주행 속도 45km/h)에서의 라디에이터 구조 모델링 및 시뮬레이션.
- 주변 온도 50°C의 정지 상태에서 냉각 성능, 특히 온도 피드백 제어 및 합성 제트의 효과에 대한 실험적 검증.
6. 주요 결과 (Key Results):
주요 결과 (Key Results):
- 냉각 시스템에 대한 열 저항 모델이 수립되었습니다 (Fig. 1, Equations 1-10).
- 히트 파이프, 히트 싱크 핀, 합성 제트 장치, 온도 센서 및 MCU 제어 장치를 통합한 LED 헤드라이트 라디에이터의 3D 모델이 CATIA를 사용하여 설계되었습니다 (Fig. 2).
- 주변 온도 50°C 및 주행 속도 45km/h에 대한 FLOEFD 시뮬레이션 결과 (Fig. 3)는 다음과 같습니다:
- 최대 라디에이터 온도 92.9°C.
- LED 접합 온도 124.6°C (브래킷과 PN 접합 사이의 고정 온도 차이 31.7°C로 계산), 설계 요구 사항인 <125°C 충족.
- 주변 온도 50°C(정지 상태)에서 샘플 램프에 대한 실험 테스트 (Fig. 4) 결과:
- 합성 제트 작동 10분 후 광원 온도가 안정화되었습니다 (Fig. 5).
- 합성 제트가 활성화되면 샘플 램프 온도가 18°C 낮아졌습니다 (Fig. 6).
- 온도 피드백 제어 시스템은 LED 온도를 효과적으로 관리하여 설계 요구 사항을 초과하지 않도록 했습니다.
- 제안된 열 관리 시스템 및 기술은 고출력 LED 자동차 헤드라이트의 방열 문제를 성공적으로 해결합니다.
그림 이름 목록 (Figure Name List):
- Fig. 1. Thermal resistance network diagram of the cooling system
- Fig. 2. LED headlight radiator structure
- Fig. 3. FLOEFD simulation results of the radiator
- Fig. 4. Image of the sample lamp test
- Fig. 5. The highest temperature of test positions versus the run time of synthetic jet
- Fig. 6. Heat dissipation effect with the synthetic jet
7. 결론 (Conclusion):
본 연구는 다양한 조건에서 LED 헤드라이트의 냉각 요구 사항을 분석합니다. 주행 중 역방향 흐름에 의존하는 수동적 히트 파이프 냉각 기술과 온도 피드백 제어의 능동 냉각 기술이 제안됩니다. 라디에이터 구조와 샘플 램프는 CATIA로 설계되었습니다. FLOEFD 시뮬레이션 및 실험 결과는 주변 온도가 50°C이고 정지 상태일 때 LED의 접합 온도가 적절한 범위 내에 있음을 보여줍니다. 최고 온도는 요구되는 범위 내에서 제어될 수 있습니다. 제안된 기술은 현재 고출력 LED 헤드라이트의 적용 및 보급을 제한하는 방열 문제를 해결하기 위한 접근 방식을 제공합니다.
8. 참고문헌 (References):
- [1] C.-C. Hsieh, Y.-H. Li and C.-C. Hung: Appl. Opt. 52 (2013) 5221. DOI:10.1364/AO.52.005221
- [2] M. Arik, C. Becker, S. Weaver and J. Petroski: Proc. SPIE 5187 (2004) 64. DOI:10.1117/12.512731
- [3] R. V. Steele: Laser Focus World 41 (2005) 91.
- [4] A. Cvetkovic, O. Dross, J. Chaves, P. Benitez, J. C. Miñano and R. Mohedano: Opt. Express 14 (2006) 13014. DOI:10.1364/OE.14.013014
- [5] J.-J. Chen, K.-L. Huang and P.-C. Lin: Opt. Eng. 49 (2010) 073002. DOI:10.1117/1.3461984
- [6] W. Pohlmann, T. Vieregge and M. Rode: Proc. SPIE 6797 (2007) 67970D. DOI:10.1117/12.760978
- [7] M. Ha and S. Graham: Microelectron. Reliab. 52 (2012) 836. DOI:10.1016/j.microrel.2012.02.005
- [8] M. Arik, A. Setlur, S. Weaver, D. Haitko and J. Petroski: J. Electron. Packag. 129 (2007) 328. DOI:10.1115/1.2753958
- [9] N. Narendran and Y. Gu: IEEE/OSA J. Disp. Technol. 1 (2005) 167. DOI:10.1109/JDT.2005.852510
- [10] Q. Chen, X. Luo, S. Zhou and S. Liu: Rev. Sci. Instrum. 82 (2011) 084904. DOI:10.1063/1.3624699
- [11] A. Jayawardena, Y.-w. Liu and N. Narendran: Solid-State Electron. 86 (2013) 11. DOI:10.1016/j.sse.2013.04.001
- [12] D. B. Tuckerman and R. F. W. Pease: IEEE Electron Device Lett. 2 (1981) 126. DOI:10.1109/EDL.1981.25367
- [13] T. Kishimoto and S. Sasaki: Electron. Lett. 23 (1987) 456. DOI:10.1049/el:19870328
- [14] A. S. Panahi: Proc. SPIE 8368 (2012) 83680T. DOI:10.1117/12.977566
- [15] A. Christensen and S. Graham: Appl. Therm. Eng. 29 (2009) 364. DOI:10.1016/j.applthermaleng.2008.03.019
- [16] O. Kückmann: Proc. SPIE 6134 (2006) 613404. DOI:10.1117/12.646321
- [17] X. B. Luo, W. Xiong, T. Cheng and S. Liu: IET Optoelectron. 3 (2009) 225. DOI:10.1049/iet-opt.2008.0068
- [18] L. Kim, J. H. Choi, S. H. Jang and M. W. Shin: Thermochim. Acta 455 (2007) 21. DOI:10.1016/j.tca.2006.11.031
- [19] Z. M. Wang, K. Bao, L. P. Xu, C. X. Luo, B. Zhang, H. Ji, Q. Ouyang and Y. Chen: Microelectron. Eng. 84 (2007) 1223. DOI:10.1016/j.mee.2007.01.188
- [20] Y. Lai, N. Cordero, F. Barthel, F. Tebbe, J. Kuhn, R. Apfelbeck and D. Würtenberger: Appl. Therm. Eng. 29 (2009) 1239. DOI:10.1016/j.applthermaleng.2008.06.023
- [21] X. B. Luo and S. Liu: IEEE Trans. Adv. Packag. 30 (2007) 475. DOI:10.1109/TADVP.2007.898522
- [22] S. Liu, J. H. Yang, Z. Y. Gan and X. B. Luo: Int. J. Therm. Sci. 47 (2008) 1086. DOI:10.1016/j.ijthermalsci.2007.09.005
- [23] S. W. Chau, C. H. Lin, C. H. Yeh and C. Yang: 33rd Annual Conference of the IEEE Industrial Electronics Society (2007) 2934. DOI:10.1109/IECON.2007.4460209
- [24] J. Li, B. Ma, R. Wang and L. Han: Microelectron. Reliab. 51 (2011) 2210. DOI:10.1016/j.microrel.2011.05.006
- [25] H. Ye, M. Mihailovic, C. K. Y. Wong, H. W. van Zeijl, A. W. J. Gielen, G. Q. Zhang and P. M. Sarro: Appl. Therm. Eng. 52 (2013) 353. DOI:10.1016/j.applthermaleng.2012.12.015
- [26] T. Acikalin, S. V. Garimella, J. Petroski and A. Raman: 9th Intersociety Conference on Thermal and Thermomechanical Phenomena in Electronic Systems (2004) 663. DOI:10.1109/ITHERM.2004.1319239
- [27] X.-Y. Lu, T.-C. Hua, M.-J. Liu and Y.-X. Cheng: Thermochim. Acta 493 (2009) 25. DOI:10.1016/j.tca.2009.03.016
- [28] X.-Y. Lu, T.-C. Hua and Y.-X. Cheng: Microelectron. J. 42 (2011) 1257. DOI:10.1016/j.mejo.2011.08.009
- [29] F. Chen, K. Wang, Z. Qin, D. Wu, X. Luo and S. Liu: Opt. Express 18 (2010) 20926. DOI:10.1364/OE.18.020926
- [30] S. Jang and M. W. Shin: IEEE Trans. Device Mater. Rel. 8 (2008) 561. DOI:10.1109/TDMR.2008.2002355
- [31] H.-Y. Ryu, K.-H. Ha, J.-H. Chae, O.-H. Nam and Y.-J. Park: Appl. Phys. Lett. 87 (2005) 093506. DOI:10.1063/1.2037201
- [32] Y.-J. Lee, C.-J. Lee and C.-H. Chen: Jpn. J. Appl. Phys. 50 (2011) 04DG18. DOI:10.1143/JJAP.50.04DG18
- [33] M. Le Berre, G. Pandraud, P. Morfouli and M. Lallemand: J. Micromech. Microeng. 16 (2006) 1047. DOI:10.1088/0960-1317/16/5/023
- [34] G. J. Michna, E. A. Browne, Y. Peles and M. K. Jensen: J. Heat Transfer 131 (2009) 111402. DOI:10.1115/1.3154750
9. 저작권 (Copyright):
- 본 자료는 "Hui-Ming Qu, Xiao-Hui Yang, Qi Zheng, Xin-Tao Wang, and Qian Chen"의 논문입니다. "[Thermal management technology of high-power light-emitting diodes for automotive headlights]"를 기반으로 합니다.
- 논문 출처 (Source of the paper): 10.1587/elex.11.20140965
본 자료는 위 논문을 바탕으로 요약되었으며, 상업적 목적의 무단 사용을 금합니다.
Copyright © 2025 CASTMAN. All rights reserved.