본 소개 논문은 IOP Publishing에서 발행한 "High strength aluminum alloys in car manufacturing" 논문의 연구 내용입니다.
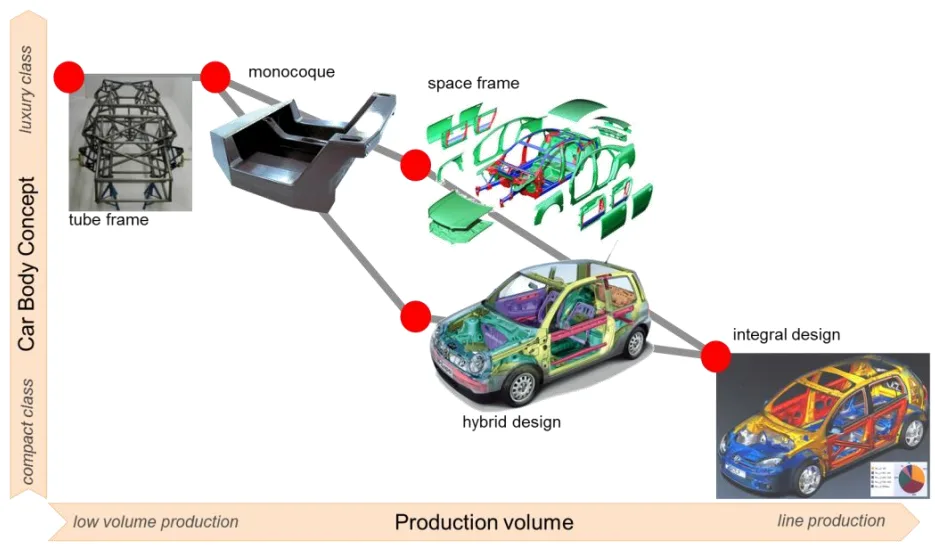
1. 개요:
- 제목: High strength aluminum alloys in car manufacturing (자동차 제조 분야의 고강도 알루미늄 합금)
- 저자: M Tisza and Zs Lukács
- 출판 연도: 2018
- 게시된 저널/학회: IOP Conference Series: Materials Science and Engineering, 418 (2018) 012033
- 키워드: aluminum alloys, lightweight design, car body construction, hot forming, formability, HFQ (알루미늄 합금, 경량 설계, 차체 구조, 열간 성형, 성형성, HFQ)
2. 초록
최근 수십 년 동안 자동차 제조 분야에서는 고객 측면과 법적 요구 사항 양쪽 모두에서 많은 요구 사항이 제기되고 있습니다. 이러한 요구 사항에는 유해 배출 감소를 통한 환경 보호 강화, 안전성 및 편안함 증대, 경제적인 차량 생산 등이 포함됩니다. 이러한 상충되는 요구 사항을 충족하기 위해 경량 설계 원칙을 적용하는 것이 가장 널리 사용되는 해결책 중 하나입니다. 판재 성형으로 생산되는 차체 부품에 특히 유효한 저비용 제조를 통해 경량 자동차 구조물을 생산하는 두 가지 주요 트렌드가 있습니다. 경량 합금 재료, 특히 다양한 알루미늄 합금의 적용은 경량 차체 구조의 요구 사항을 충족하는 다른 가능한 해결책으로 간주됩니다. 알루미늄은 강철 재료보다 무게 감소 잠재력이 더 크지만, 알루미늄은 강철보다 성형성이 낮습니다. 알루미늄과 같은 가벼운 재료로 강철을 대체하는 것은 비용이 많이 들고 간단하지 않을 수 있습니다. 이는 최근 알루미늄 합금의 열간 성형이 연구 활동의 최전선에 오게 된 주요 이유 중 하나입니다. 이 논문에서는 "경량 차량의 대량 생산을 위한 저비용 재료 가공 기술"이라는 제목의 공동 유럽 프로젝트에서 얻은 몇 가지 최근 결과를 소개합니다.
3. 연구 배경:
연구 주제의 배경:
자동차 제조의 주요 발전 추세는 고객 요구(낮은 소비, 안전성, 기능성 및 편안함 향상)와 엄격한 법적 요구 사항(유해 배출 감소, 충돌 안전성 향상)에 의해 주도됩니다 [1]. 경량화는 이러한 상충되는 요구 사항을 충족하기 위한 핵심 전략입니다.
이전 연구 현황:
전통적으로 강철은 BIW(Body in White) 제조에서 지배적인 재료였습니다. 그러나 고강도 강철(예: DP-steels, TRIP steels, XHSS 및 UHSS)의 다양한 세대를 포함하는 발전이 이루어졌습니다 [그림 2]. 특히 알루미늄과 같은 경량 합금 재료의 적용은 효과적인 해결책으로 간주됩니다.
연구의 필요성:
알루미늄은 실온에서 강철보다 성형성이 낮아 직접적인 대체가 어렵고 비용이 많이 듭니다. 이로 인해 알루미늄 합금의 열간 성형에 대한 연구가 활발히 진행되고 있습니다.
4. 연구 목적 및 연구 질문:
연구 목적:
재료 및 공정 개발을 포함한 요구 사항을 충족하기 위한 주요 가능성을 검토하고, 미래 자동차 제조 솔루션의 가능성과 개발 동향을 비교합니다. 공동 유럽 프로젝트(경량 차량의 대량 생산을 위한 저비용 재료 가공 기술)에서 얻은 최근 결과를 소개합니다.
핵심 연구:
차체 제조에서 알루미늄 합금을 사용할 때 발생하는 문제, 특히 실온에서 강철에 비해 알루미늄의 낮은 성형성을 해결하는 데 중점을 둡니다.
5. 연구 방법
- 문헌 검토: 기존 차체 개념(일체형 설계, 스페이스 프레임, 하이브리드 설계, 튜브 프레임, 모노코크)과 생산량 및 경제성과의 관계 검토 [그림 1] [3]. 고강도 강철 및 알루미늄 합금을 포함한 재료 개발 및 중량 감소 잠재력 검토 [그림 2] [4]. 알루미늄의 역사적 개요 및 다중 재료 접근 방식에 대한 검토.
- 재료 및 성형성 시험: 여러 재료 및 성형성 시험. 수정된 나카지마 시험(광학 변형 측정 시스템을 갖춘 컴퓨터 제어 범용 판재 성형성 시험기)을 사용하여 성형성 조사를 수행했습니다. 다양한 온도에서 AA7075 알루미늄 합금의 유동 곡선 및 성형 한계 곡선 결정 [그림 6].
- 실험 데이터 분석: 특히 AA7075 알루미늄 합금에 대해 다양한 고온 및 변형률에서 성형성 매개변수 분석.
6. 주요 연구 결과:
주요 연구 결과 및 제시된 데이터 분석:
- 알루미늄 합금은 기준 HSLA 강철에 비해 상당한 중량 감소 잠재력(25-40%)을 제공합니다 [그림 2].
- 열간 성형은 낮은 실온 성형성을 가진 고강도 알루미늄 합금을 위한 핵심 기술입니다.
- HFQTM 공정 [그림 5] [19]은 붕소 합금강의 열간 성형과 유사점 및 차이점을 가지며 강조됩니다.
- AA7075 알루미늄 합금의 성형성은 온도가 증가함에 따라 증가하며 최적의 열간 성형 온도는 약 400°C입니다. [그림 6]
- AA7075는 T=450°C에서 유동 곡선을 가지며 [그림 6.a], 이 온도 이상에서는 열간 단축 시험에서 파단 변형률이 감소했습니다 [그림 6.b].
그림 이름 목록:
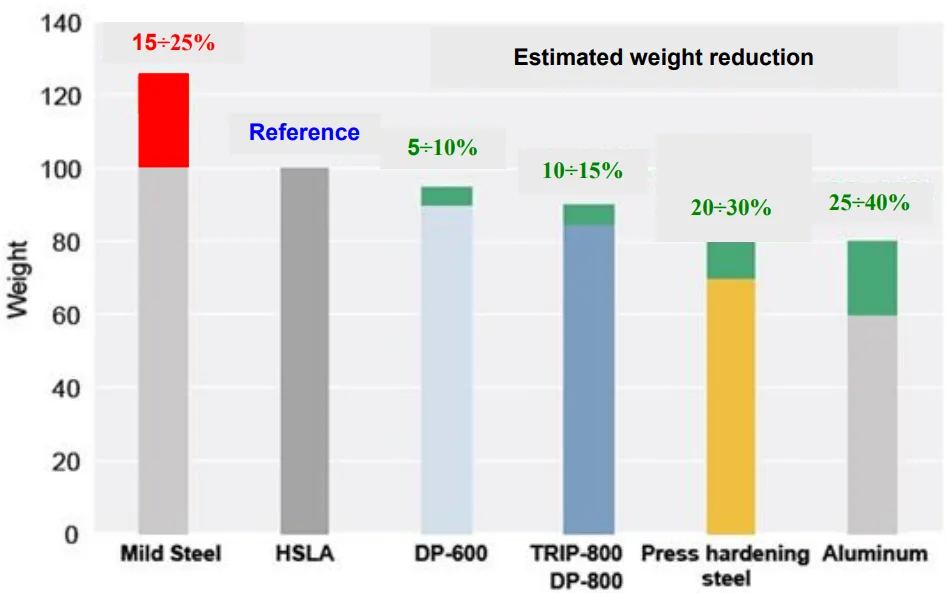

![Figure 4. Affordability of weight reduction using various multi-material concepts [15].](https://castman.co.kr/wp-content/uploads/image-1529-1024x539.webp)
![Figure 5. Basic principle of Hot Forming and QuenchingTM of aluminum alloys [19].](https://castman.co.kr/wp-content/uploads/image-1530-1024x344.webp)
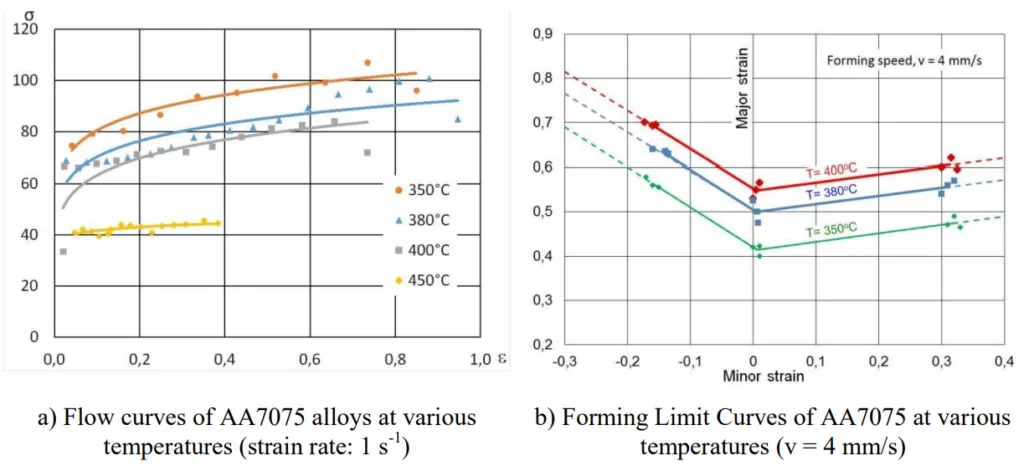
- 그림 1. 생산량의 함수로서의 차체 개념.
- 그림 2. 차체 제조에서 다양한 고강도 재료의 중량 감소 잠재력.
- 그림 3. 차체 제조의 다중 재료 개념.
- 그림 4. 다양한 다중 재료 개념을 사용한 중량 감소의 경제성 [15].
- 그림 5. 알루미늄 합금의 열간 성형 및 담금질™의 기본 원리 [19].
- 그림 6. 다양한 온도에서 AA7075 합금의 유동 곡선 및 성형 한계 곡선.
7. 결론:
주요 연구 결과 요약:
- 고강도 강철 및 알루미늄 합금의 사용을 포함한 경량 구조 원리는 현대 자동차 요구 사항을 충족하는 데 중요합니다.
- HFQ와 같은 열간 성형 공정은 고강도 알루미늄 합금을 효과적으로 활용하는 데 필수적입니다.
- 알루미늄 합금의 재료 특성 및 성형 한계는 열간 성형 중 온도 및 변형률에 크게 의존합니다.
- 고강도 알루미늄 합금의 적용이 크게 증가하고 있습니다.
향후 확장 연구 가능 분야:
- 빠른 가열/냉각 및 다른 제조 공정(예: 페인트 베이킹)과의 통합을 통한 주기 시간 단축을 포함하여 열간 성형 공정의 추가 최적화.
- 자동차 응용 분야를 위한 다양한 알루미늄 합금의 지속적인 탐색 및 특성화.
- 다중 재료 경량 구조와 관련된 추가 연구.
8. 참고 문헌:
- [1] Tisza M (2015) Metal Forming in the automotive industry, Miskolc University Press, p. 294 ISBN 978-963-358-082-0
- [2] Czinege I (2017) Comparative analysis of steel and aluminum sheets, Proc. 16th Metal Forming Conf. Miskolc-Hungary
- [3] Liewald M and Schleich R (2007) Robust processes in sheet metal forming in car body manufacturing with regard to production volume, Proc. of IDDRG 2007, Győr, Hungary, 21-23. May 2007. pp. 11-20.
- [4] Tisza M (2013) Recent development trends in sheet metal forming, Int. J. Microstructure and Material Prop. 8. No. 1-2. pp. 125-139.
- [5] Tisza, M (2014) Advanced materials in sheet metal forming, Key Engineering Materials, 581 pp. 137-142. DOI:10.4028/www.scientific.net/KEM.581.137
- [6] Ghassemieh E (2011) Materials in Automotive Application – State of the Art and Prospects, in New Trends and Developments in Automotive Industry, InTech Open Publications, DOI: 10.5772/1821
- [7] Banik J et. al (2013) Warmumformung im Automobilbau, Süddeutsche Verlag, Munich, p. 84.
- [8] Lin Jianguo et. al (2011) A method of forming a component of complex shape from aluminum alloy sheet, GB 2473298 British Patent
- [9] Keeler S, Kimchi M and Mooney, P (2017) Advanced High Strength Steels – Application Guidelines 6.0, World Auto Steel April, pp. 314.
- [10] Tisza M (2015) Material and technological developments in sheet metal forming with special regards to the needs of the automotive industry, Archives of Materials Science and Engineering, 71 No.1. pp. 36-45.
- [11] Audi AG.: Historical background on use of aluminium at Audi, https://www.audiworld.com/news/02/aluminum/content1.shtml
- [12] European Aluminium Association (2012) Aluminium in cars-unlocking – The light weighting potential http://www.alueurope.eu/publications-automotive/
- [13] Kelkar A, Roth R and Clark J (2001) Automobile Bodies: Can Aluminum Be an Economical Alternative to Steel, Journal of Manufacturing 53 No. 8. pp. 28-32.
- [14] Lotus Engineering (2010) An assessment of mass reduction opportunities for 2017-2020 model year vehicle program, The International Council on Clean Transportation
- [15] Goede M et. al (2009) Super Light Car - lightweight construction thanks to a multi-material design and function integration, European Transp. Res. Rev No.1. pp. 5-10. DOI 10.1007/s12544-008-0001-2
- [16] Budai D and Tisza M (2017) Investigation of EN AW 5754 Aluminum Alloy's Formability at Elevated Temperatures Material Science Forum, 885, pp 98-103.
- [17] Budai D, Kovács P and Lukács Zs (2016) Formability investigations of Aluminum alloys at elevated temperatures, IDDRG 2016 Conference, Linz, 12-15. June 2016
- [18] Bach, R.: Aluminium in transport industry, https://www.aluminiumleader.com/application/transport/
- [19] LoCoMaTech (2016) Low Cost Materials Processing Technologies for Mass Production of Lightweight Vehicles EU H-2020 project 2016-2019, ID No: 723517.
- [20] Tisza M (2001) Physical Metallurgy for Engineers, ASM Publisher, 2001, Ohio-London, p.405.
9. 저작권:
- 이 자료는 "M Tisza and Zs Lukács"의 "High strength aluminum alloys in car manufacturing" 논문을 기반으로 합니다.
- 논문 출처: doi:10.1088/1757-899X/418/1/012033
본 자료는 위 논문을 소개하기 위해 작성되었으며, 상업적 목적으로 무단 사용하는 것을 금합니다. Copyright © 2025 CASTMAN. All rights reserved.