본 논문 요약은 ['의료 기기 제조의 일반적인 경로']라는 제목의 논문을 ['Metallic Biomaterials Processing and Medical Device Manufacturing']에 발표된 내용을 기반으로 작성되었습니다.
1. 개요:
- 제목: 의료 기기 제조의 일반적인 경로 (General manufacturing route for medical devices)
- 저자: Yu Sun, Sen Yu, Gui Wang
- 출판 연도: 2021년
- 출판 저널/학회: Metallic Biomaterials Processing and Medical Device Manufacturing, Elsevier Ltd.
- 키워드: 제조 공정, 의료 기기, 금속 산업, 주조, 성형, 열처리, 접합, 티타늄 합금 (Manufacturing process, medical devices, metal industry, casting, forming, heat treatment, joining, titanium alloys)
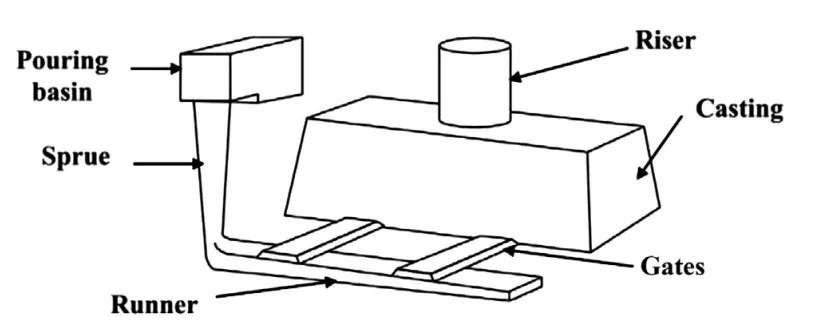
2. 연구 배경:
연구 주제 배경:
제조는 노동력, 기계, 도구, 가공 또는 제형을 사용하여 사용 또는 판매를 위한 제품을 생산하는 것으로, 2차 산업의 본질입니다. 이 용어는 광범위한 인간 활동을 지칭할 수 있지만, 일반적으로 1차 산업의 원자재가 대규모로 완제품으로 변형되는 엔지니어링 설계에 가장 많이 적용됩니다. 의료 기기 산업은 인간에게 영향을 미치는 질병과 상태를 진단, 모니터링 및 치료하는 광범위한 의료 제품을 설계하고 제조합니다. 이러한 제품은 수술 도구, 인공 관절, 엉덩이 임플란트, 복잡한 수술을 수행하는 소형 로봇, 인공 심장에서부터 자기 공명 영상 시스템과 같은 복잡한 수백만 달러 규모의 시스템에 이르기까지 다양합니다. 의료 기기 산업은 광범위한 생체 재료로부터 금속 부품 또는 제품을 제조하기 위해 금속 산업의 많은 제조 공정을 적용합니다. 제조 공정은 제품 설계 및 제품이 만들어지는 재료 사양으로 시작됩니다. 이러한 재료는 필요한 부품이 되기 위해 제조 공정을 통해 수정됩니다. 현대 제조에는 제품 구성 요소의 생산 및 통합에 필요한 모든 중간 공정이 포함됩니다.
기존 연구 현황:
금속 산업에서 대부분의 재료는 (1) 용융 금속을 냉각시켜 고체를 형성하고, (2) 고체 금속을 기계적으로 성형하여 특정 제품을 형성하는 경로를 통해 가공됩니다. 이러한 단계가 수행되는 방식은 매우 중요합니다. 왜냐하면 열과 소성 변형이 금속의 기계적 특성에 강력한 영향을 미칠 수 있기 때문입니다. 이 장에서는 의료 기기용 원자재에서 1차 형상까지의 주요 제조 공정을 다룹니다. 여기에는 주조, 성형, 열처리 및 접합이 포함됩니다. 다른 모든 제조 공정과 마찬가지로, 우수한 품질과 경제적인 부품 생산, 그리고 몰드 설계 및 주조 실습을 위한 적절한 기술 확립을 위해서는 기초 과학에 대한 이해가 필수적입니다. 티타늄 합금의 상세한 1차 제조 공정의 예도 설명되어 있습니다.
연구의 필요성:
본 장에서는 의료 기기, 특히 금속 가공에 대한 일반적인 제조 경로를 명확히 하는 것을 목표로 합니다. 의료 기기 생산과 관련된 주조, 성형, 열처리 및 접합을 포함한 주요 제조 공정에 대한 핸드북 수준의 이해를 제공하는 것을 목표로 합니다.
3. 연구 목적 및 연구 질문:
연구 목적:
본 장의 목적은 의료 기기, 특히 금속 가공에 대한 일반적인 제조 경로를 설명하는 것입니다. 주조, 성형, 열처리 및 접합을 포함하여 의료 기기 생산과 관련된 주요 제조 공정에 대한 핸드북 수준의 이해를 제공하는 것을 목표로 합니다.
주요 연구 내용:
본 장에서 다루는 주요 연구 분야는 다음과 같습니다.
- 금속 주조 기초 및 공정 (금속 흐름, 응고 및 결함 형성 포함).
- 금속 성형 공정 (압연, 단조, 압출 및 인발 포함) 및 온도 효과.
- 열처리 방법 및 미세 구조와 특성에 미치는 영향.
- 의료 기기 제조에서 재료 접합을 위한 용접 기술.
- 티타늄 합금 튜브 및 와이어의 특정 제조 공정.
연구 가설:
본 장은 핸드북 챕터로서 명시적인 연구 가설을 제시하지 않습니다. 그러나 근본적인 전제는 이러한 제조 공정에 대한 철저한 이해가 금속 생체 재료로 만든 고품질 의료 기기를 생산하는 데 필수적이라는 것입니다.
4. 연구 방법론
연구 설계:
본 장에서는 의료 기기를 금속 재료로 제조하는 데 관련된 기본 원리 및 공정을 설명하는 기술적 및 설명적 접근 방식을 사용합니다. 금속 주조 및 성형에 초점을 맞춰 다양한 제조 기술에 대한 구조화된 개요를 제공합니다.
자료 수집 방법:
본 장에서는 재료 과학 및 제조 공학 분야의 기존 지식과 원리를 종합합니다. 제조 경로를 설명하고 설명하기 위해 해당 분야의 확립된 이론과 관행을 활용합니다.
분석 방법:
본 장에서는 복잡한 제조 공정을 기본 단계와 원리로 분류하는 기술적 분석 방법을 사용합니다. 주조 시 응고 (그림 3.2), 주조 중 수축 (그림 3.5), 열간 압연 중 미세 구조 진화 (그림 3.11)와 같은 핵심 개념과 메커니즘을 설명하기 위해 그림과 예시를 활용합니다.
연구 대상 및 범위:
본 장의 범위는 의료 기기의 일반적인 제조 경로에 초점을 맞추고 있으며, 특히 금속 주조, 금속 성형, 열처리 및 용접을 다룹니다. 주요 대상은 금속 생체 재료와 이를 의료 부품으로 성형하는 데 사용되는 제조 공정입니다. 본 장에는 티타늄 합금에 대한 특정 초점도 포함되어 있습니다.
5. 주요 연구 결과:
주요 연구 결과:
- 금속 주조: 금속 주조를 제조 공정으로 상세히 설명하고, 유체 흐름 (유동성, 주입 온도, 게이팅 시스템), 응고 (핵 생성, 결정 성장, 결정립 구조), 열 전달 및 주조 결함 형성 (수축, 편석)과 같은 기초 사항을 다룹니다. 인베스트먼트 주조 및 잉곳 주조와 같은 다양한 주조 공정이 설명되어 있습니다 (그림 3.7, 그림 3.8, 그림 3.9).
- 금속 성형: 압연 (평판 압연, 형상 압연, 링 압연, 나사 압연), 단조 (밀폐형, 개방형), 압출 (정압출, 역압출, 측면 압출) 및 인발을 포함한 금속 성형 공정에 대한 포괄적인 개요. 온도 (냉간, 온간, 열간 가공)가 금속 성형에 미치는 영향에 대해 논의합니다 (그림 3.10, 그림 3.11, 그림 3.12, 그림 3.13, 그림 3.14, 그림 3.15, 그림 3.16, 그림 3.17, 그림 3.18, 그림 3.19, 그림 3.20, 그림 3.21).
- 열처리: 열처리 공정 (노멀라이징, 풀림, 담금질, 템퍼링)과 금속 재료의 미세 구조 및 특성에 미치는 영향 (그림 3.22, 그림 3.23)에 대한 설명.
- 용접: 용접을 접합 공정으로 설명하고, 융착 용접, 용접 영역 (모재, 용착 금속, HAZ) 및 용접 품질에 영향을 미치는 요인 (그림 3.24, 그림 3.25)을 포함합니다. 티타늄 튜브 용접에 대한 특정 고려 사항이 제공됩니다.
- 티타늄 합금 가공: 티타늄 합금 튜브 및 와이어의 특정 제조 경로에 대해 논의하고, 튜브의 압출 (천공 압출, 백 스퀴즈) 및 압연, 와이어의 인발을 포함합니다 (그림 3.26, 그림 3.27, 그림 3.28, 그림 3.29).
데이터 해석:
- 주조의 유동성: 유동성은 점도, 표면 장력 및 응고 패턴에 의해 결정됩니다. 더 높은 과열도 및 몰드 표면 특성은 금속 흐름 능력에 영향을 미칩니다.
- 응고 및 결정립 구조: 응고는 핵 생성 및 결정 성장을 통해 발생하며, 주조 특성에 영향을 미치는 결정립 구조를 유도합니다. 냉각 속도는 수지상 결정 구조에 영향을 미칩니다 (그림 3.4).
- 수축 및 기공: 응고 중 수축은 기공을 유발할 수 있으며, 이는 주조 설계 및 방향성 응고를 통해 완화할 수 있습니다. 표 3.1은 금속의 응고 수축을 보여줍니다.
- 성형 시 온도: 온도는 금속 성형에 큰 영향을 미칩니다. 냉간 가공은 강도를 증가시키지만 연성을 감소시키는 반면, 열간 가공은 동적 재결정으로 인해 더 큰 형상 변화를 허용합니다 (그림 3.11).
- 열처리 효과: 풀림, 노멀라이징, 담금질 및 템퍼링과 같은 열처리 공정은 경도 및 강도와 같은 미세 구조 및 기계적 특성을 수정하는 데 사용됩니다 (그림 3.23).
- 용접 영역: 융착 용접은 다양한 미세 구조와 특성을 가진 뚜렷한 영역 (모재, 용착 금속, HAZ)을 생성합니다. 용접 매개 변수 및 재료 특성은 HAZ 특성에 영향을 미칩니다 (그림 3.24).
그림 목록:
- 그림 3.1 일반적인 라이저 게이트 주조의 개략도.
- 그림 3.2 (A) 응고 금속의 응고 및 온도 분포 그림 및 (B) 잘 발달된 수지상 결정 구조 주조.
- 그림 3.3 주조된 금속 결정립 구조 (A) 몰드 벽에서 기둥 모양 결정립과 중앙에서 등축 결정립의 일반적인 조합을 보여주는 순수 아연, (B) 마그네슘의 주조 결정립은 주조 공정 중에 접종제 (C)를 첨가하여 미세화할 수 있습니다.
- 그림 3.4 (A) 주조 응고 중 온도 분포 및 (B) 느린 냉각 속도로 인해 수지상 결정 팔 사이의 간격이 넓은 조대한 수지상 결정 구조.
- 그림 3.5 주조 중 3단계 수축 그림.
- 그림 3.6 (A) 미세 편석, (B) 강철 잉곳의 일반적인 거시적 편석 패턴의 개략도.
- 그림 3.7 주조 공정 분류.
- 그림 3.8 인베스트먼트 주조 공정.
- 그림 3.9 잉곳 주조 공정 및 일반적인 결정립 구조 개발의 개략도.
- 그림 3.10 저탄소강의 응력-변형률 곡선에 대한 개략도.
- 그림 3.11 열간 압연 공정 중 미세 구조 진화의 개략도.
- 그림 3.12 기계 가공 볼트와 압연 볼트 간의 결정립 구조 비교.
- 그림 3.13 압연 공정의 개략도.
- 그림 3.14 플래시가 있는 밀폐형 단조. (A) 플래시 용어에 대한 개략도. (B) 커넥팅 로드의 밀폐형 단조의 단조 순서.
- 그림 3.15 개방형 단조.
- 그림 3.16 금속 압출의 기본 원리.
- 그림 3.17 정압출 및 역압출에 대한 힘과 변위 간의 관계.
- 그림 3.18 인발 공정.
- 그림 3.19 직선 칼날 전단 메커니즘을 보여주는 개략도.
- 그림 3.20 V-다이에서의 굽힘.
- 그림 3.21 평판 블랭크에서 컵을 인발할 때 금속 흐름의 진행.
- 그림 3.22 철-탄소 상평형 그림의 1 국부 확대.
- 그림 3.23 주요 풀림 공정의 개략도: (A) 변형된 상태, (B) 회복된 상태, (C) 부분적으로 재결정화된 상태, (D) 완전히 재결정화된 상태, (E) 결정립 성장 및 (F) 비정상적인 결정립 성장.
- 그림 3.24 아크 용접에서 일반적인 융착 용접 영역의 특징.
- 그림 3.25 (A) 깊은 용접과 (B) 얕은 용접의 결정립 구조; 응고된 용접 금속의 결정립은 모재와의 계면에 수직입니다. (C) 레이저 빔으로 생성된 냉간 압연 니켈 스트립의 용접 비드. (D) 용접 비드 전체의 미세 경도 (HV) 프로파일.
- 그림 3.26 솔리드 잉곳 천공 및 압출 공정의 개략도.
- 그림 3.27 파이프 역압출의 개략도.
- 그림 3.28 스큐 압연 천공기의 작동 원리 개략도.
- 그림 3.29 고압 열간 가스 성형의 원리.
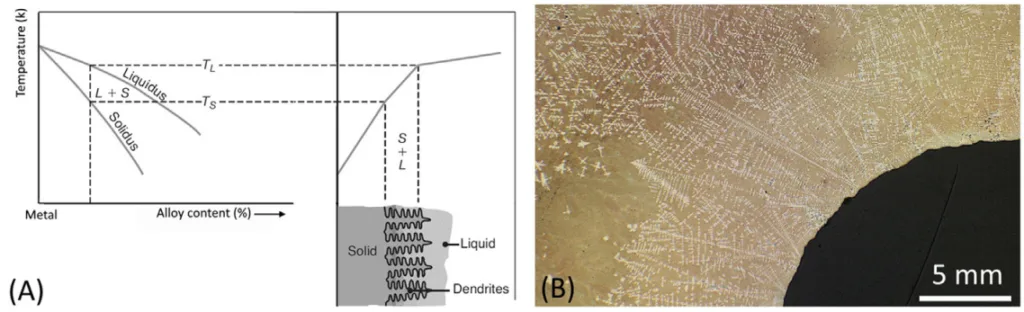
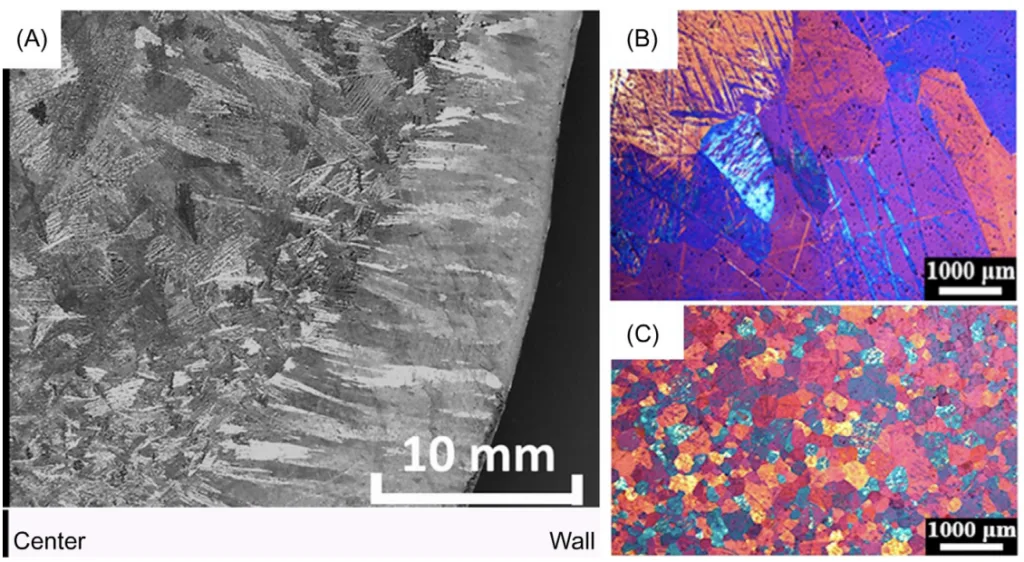
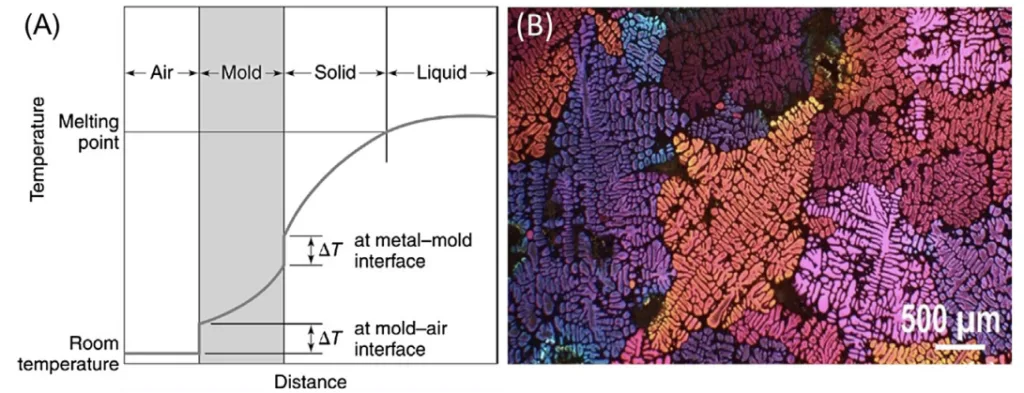

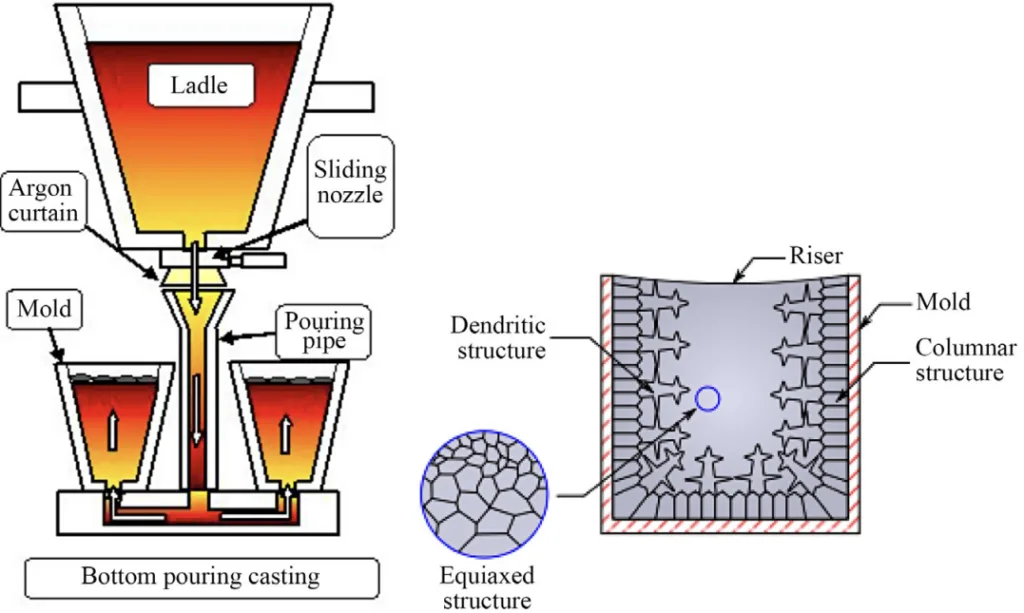
6. 결론:
주요 결과 요약:
본 장에서는 의료 기기의 일반적인 제조 경로에 대한 포괄적인 개요를 제공하며, 금속 주조, 성형, 열처리 및 용접에 중점을 둡니다. 각 제조 기술에 대한 기본 원리, 공정 및 영향 요인을 자세히 설명합니다. 티타늄 합금 가공과 같은 특정 예는 의료 기기 제조에서 이러한 방법의 실제 적용을 보여줍니다. 본 장에서는 원하는 제품 품질과 성능을 달성하기 위해 재료 거동 및 공정 매개 변수를 이해하는 것의 중요성을 강조합니다.
연구의 학문적 의의:
본 장은 의료 기기 제조 및 재료 과학 분야의 전문가 및 연구원에게 귀중한 자료 역할을 합니다. 다양한 제조 공정에 대한 필수 지식을 통합하여 이 분야의 이해와 추가 연구를 위한 구조화된 프레임워크를 제공합니다. 각 공정의 기본 과학적 원리를 강조하여 제조 야금에 대한 더 깊은 이해를 촉진합니다.
실제적 의미:
의료 기기 산업의 실무자에게 본 장은 금속 부품에 대한 제조 공정을 선택하고 최적화하는 데 대한 실질적인 지침을 제공합니다. 공정 매개 변수, 결함 제어 및 재료 선택에 대한 통찰력을 제공하여 고품질의 신뢰할 수 있는 의료 기기 생산을 지원합니다. 주조, 성형, 열처리 및 용접 기술에 대한 자세한 설명은 공정 설계 및 개선을 위한 기반을 제공합니다.
연구의 한계
본 장은 핸드북 챕터로서 광범위한 개요를 제공하며, 매우 구체적이거나 최첨단 연구 주제를 깊이 있게 다루지는 않습니다. 각 공정에 대한 적용 범위는 단일 챕터의 범위에 의해 제한됩니다. 각 제조 방법에 대한 철저한 연구보다는 소개 및 참조 지점 역할을 합니다.
7. 향후 후속 연구:
- 후속 연구 방향
향후 연구에서는 주조 또는 성형과 통합된 적층 제조, 특정 생체 재료에 대한 새로운 열처리 전략, 의료 기기의 이종 금속 접합을 위한 고급 용접 기술과 같이 논의된 각 제조 공정 내에서 고급 변형 및 최적화를 탐구할 수 있습니다. - 추가 탐구가 필요한 영역
추가 탐구가 필요한 영역에는 의료 기기 제조에 Industry 4.0 기술 적용, 이러한 경로를 사용하여 가공된 재료의 생체 적합성 및 장기 성능에 대한 심층 연구, 의료 기기 산업을 위한 지속 가능하고 비용 효율적인 제조 솔루션 개발이 포함됩니다.
8. 참고 문헌:
- J. Campbell, Casting, second ed., Elsevier, Butterworth-Heinemann, 2003.
- B. Cantor, K. O'Reilly, Solidification and Casting, CRC Press, 2002.
- K. Serope, S.R. Schmid, Manufacturing Engineering and Technology, seventh ed., P&C ECS, 2013.
- K.R. Ravi, R.M. Pillai, K.R. Amaranathan, B.C. Pai, M. Chakraborty, Fluidity of aluminum alloys and composites: a review, J. Alloy. Compd. 456 (2008) 201–210.
- P.R. Beeley, R.F. Smart, Investment Casting, Maney Publishing for IOM3, the Institute of Materials, Minerals and Mining, 1995.
- J. Campbell, Complete Casting Handbook Metal Casting Processes, Metallurgy, Techniques and Design, second ed., Elsevier, 2015.
- F. Herlach, Solidification and Crystallization, John Wiley & Sons, 2004.
- C. Beckermann, Macrosegregation, ASM Handbook, Volume 15: Casting, ASM Handbook Committee, 2008, pp. 348-352. https://doi.org/10.1361/asmhba0005216.
- R. Mehrabian, M. Keane, M.C. Flemings, Interdendritic fluid flow and macrosegregation; influence of gravity, Metall. Trans. 1 (1979) 1209–1220.
- H. Fredriksson, U. Åkerlind, Materials Processing During Casting, John Wiley & Sons Ltd, 2012.
- T. Altan, G. Ngaile, G. Shen, Cold and Hot Forging: Fundamentals and Applications, ASM International, 2004.
- T.A. Perkins, T.J. Kronenberger, J.T. Roth, Metallic forging using electrical flow as an alternative to warm/hot working, J. Manuf. Sci. Eng 129 (2007) 84–94.
- M. Spittel, T. Spittel, Metal Forming Data of Ferrous Alloys - Deformation Behaviour, Springer, Berlin Heidelberg, 2009.
- J.L. Duncan, Geometric and Mechanics Models of Sheet Forming Processes, Elsevier Inc, 2002.
- K. Styles, A. Bichard, Working Drawings Handbook, Taylor and Francis, 2012.
- C.N.A. Kumar, R. Deivanathan, Effect of aluminium alloy and mild steel on the productivity in sheet metal forming processes, Appl. Mech. Mater 234 (2012) 64–68.
- S.C. Babu, V.S.S. Kumar. 2012. Experimental studies on incremental forming of stainless steel AISI 304 sheets. Proc. IMechE Part B J. Eng. Manufacture 226 (7) 1224-1229.
- W.H. Sillekens, G. Kurz, R.J. Werkhoven, Magnesium forging technology: state-of-the-art and development perspectives, in: L. Katgerman, F. Soetens (Eds.), 11th International Aluminium Conference - INALCO 2010 New Frontiers in Light Metals, IOS Press © 2010 The authors and IOS Press, 2010.
- Z. Feng, L. Chai, Z. Chen, T. Jin, G. Shi, Y. Jin, et al., Forging technology and microstructure and mechanical properties of a novel high temperature titanium alloy resistant to 650°C, in: Y. Han (Ed.), High Performance Structural Materials. CMC 2017, Springer, 2018.
- T.P. Wang, K.M. Qi, Metal Plastic Processing-Rolling Theory and Process, Metallurgical Industry Press, 2001.
- M.P. Dixit, U.S. Dixit, Modeling of Metal Forming and Machining Processes, Springer, London, 2008.
- B.R. Song, Rolling Technology, Metallurgical Industry Press, 2014.
- H. Tschaetsch, Extrusion, Metal Forming Practise, Springer, Berlin, Heidelberg, 2006.
- L. Katgerman, F. Soetens, A.R. Eivani, A.J. den Bakker, J. Zhou, J. Duszczyk, An Investigation of Dynamic Recrystallization During Hot Extrusion of Al-4.5Zn-1Mg Alloy, IOS Press, 2010.
- Dorel Banabic, Advanced Methods in Material Forming, Springer,, Berlin, Heidelberg, 2007.
- George E. Totten, Steel Heat Treatment, Taylor and Francis, 2006.
- M.I. Khan, Welding Science and Technology, New Age International, 2007.
- B.K. Choudhary, J. Christopher, D.P. Rao Palaparti, E. Isaac Samuel, M.D. Mathew, Influence of temperature and post weld heat treatment on tensile stress-strain and work hardening behaviour of modified 9Cr-1Mo steel, Mater. Des 52 (2013) 58-66.
- K.E. Thelning, Steel and Its Heat Treatment, Butterworth-Heinemann, 2013.
- R.M. Mahamood, E.T. Akinlabi, Non-contact welding technologies: fusion welding, Advanced Noncontact Cutting and Joining Technologies. Mechanical Engineering Series, Springer, Cham, 2018.
- R. Timings, Fabrication and Welding Engineering, Taylor and Francis, 2008.
- P.T. Houldcroft, R. John, Welding and Cutting: A Guide to Fusion Welding and Associated Cutting Processes, Elsevier, Woodhead Publishing, 2001.
- R.W. Messler, Welding as a Joining Process, Elsevier Inc, 2004.
- G.F. Deyev, Surface Phenomena in Fusion Welding Processes, Taylor and Francis, 2010.
- V.Y. Osadchy, A.S. Vavilin, V.G. Zimovec, A.P. Kolikov, The technology and equipment of the pipe production, internet engineering, Moscow, 2002 (in Russian).
- S.B. Bodlani, S.C.K. Yuen, G.N. Nurick, The energy absorption characteristics of square mild steel tubes with multiple induced circular hole discontinuities-part 1: experiments, J. Appl. Mech 76 (2009) 041012.
- S.D. Hu, B. Ye, L.X. Li, Materials properties of thick-wall cold-rolled welded tube with a rectangular or square hollow section, Constr. Build Mater 25 (2011) 2683-2689.
- R.S. Saluja, V. Singh. 2019. Subjective factors consideration in the selection of welding technique for welded tube manufacturing. In: R. Narayanan, S. Joshi, U. Dixit (Eds.). Advances in Computational Methods in Manufacturing. Lecture Notes on Multidisciplinary Industrial Engineering, Springer, Singapore.
- A. Kumar, M. Sapp, J. Vincelli, M.C. Gupta, A study on laser cleaning and pulsed gas tungsten arc welding of Ti-3Al-2.5V alloy tubes, J. Mater. Process Tech. 210 (2009) 64-71.
- A. Kumar, Mool C. Gupta, Surface preparation of Ti-3Al-2.5V alloy tubes for welding using a fiber laser, Opt. Lasers Eng 47 (2009) 1259–1265.
- B. Ren, G. Tao, P. Wen, C. Du, Study on weldability window and interface morphology of steel tube and tungsten alloy rod welded by explosive welding, Int. J. Refractory Met. Hard Mater 84 (2019) 105005.
- H. Pan, Z. Wang, Y. Hui, C. Yang, X. Deng, C. Bao, Product Design and Production Practice of 700MPa High Strength Hot Rolled Strip for Auto Axle Tube, Springer International Publishing, 2016.
- S. Yuan, Development and trends in internal high pressure forming, Metal Form. Technol. 21 (4) (2003) 32-34.
- R. Neugebauer, A. Sterzing, F. Schieck. Opportunities for progressive applications by means of integrating and combining various technologies with hydroforming, Tube Hydroforming Technology-Proceedings Tubehydro, Harbin, 2007, pp. 65-69.
- X. Long, L. Shuyu, A new type of rod and tubular high-power ultrasonic-focused radiator, J Nanjing Univ. (Nat. Sci.) 05 (2012) 544-552.
- H. Hosseinabadi, S.S.A. Goodarzi, A coupled stream function-finite element analysis for wire drawing processes, Int. J. Adv. Manuf. Technol 57 (2011) 917–926.
9. 저작권:
- 본 자료는 "Yu Sun, Sen Yu, Gui Wang"의 논문: "의료 기기 제조의 일반적인 경로"를 기반으로 합니다.
- 논문 출처: https://doi.org/10.1016/B978-0-08-102965-7.00003-5
본 자료는 위 논문을 기반으로 요약되었으며, 상업적 목적으로 무단 사용하는 것을 금지합니다.
Copyright © 2025 CASTMAN. All rights reserved.