본 논문 요약은 ['Rheinisch-Westfälischen Technischen Hochschule Aachen']에서 발행한 ['An Automatic CAE Tool for autonomous feasibility assessment of aluminum gravity die castings – development and calibration'] 논문을 기반으로 작성되었습니다.
1. 개요:
- 제목: An Automatic CAE Tool for autonomous feasibility assessment of aluminum gravity die castings – development and calibration (알루미늄 중력 다이캐스팅의 자율적 타당성 평가를 위한 자동 CAE 도구 – 개발 및 보정)
- 저자: Marcus Schopen, M.Sc.
- 발행 연도: 2022년
- 발행 학술지/학회: Rheinisch-Westfälischen Technischen Hochschule Aachen (아헨 공과대학교)
- 키워드: 자동 CAE 도구, 타당성 평가, 알루미늄 중력 다이캐스팅, 개발, 보정, 주조 시뮬레이션, 응고, 기공, SDAS, 효율성 향상 방법

length-dependent cooling rate 𝑇̇𝐹𝐿, engineering specification (eng. spec.), industrial prototypes (ind.
prot.)
2. 초록 또는 서론
본 논문은 차세대 개발 프로세스에서 다분야 설계 최적화(MDO)를 가능하게 하고 설계 엔지니어가 초기 설계 개념 단계에서 주조 부품 형상 변형의 타당성과 품질을 정량적이고 효율적으로 평가할 수 있도록 완전 자동화된 CAE 도구에 대한 증가하는 요구를 다룹니다. 주요 연구 질문은 다음과 같습니다.
I) "최적의 초기 조건에서 빠르고 효율적인 방식으로 시뮬레이션을 설정, 실행 및 평가하고 정량적 타당성 평가를 위해 주조 전문가의 수동적인 사용자 개입이 필요 없는 완전 자동 CAE 도구를 개발하는 것이 가능할까요?"
II) "개발된 자동 CAE 도구와 효율성 향상 방법을 보정하고 검증하는 데 필요한 시험 데이터 품질 수준은 어느 정도여야 할까요? - 전체 CAE 방법이 새로운 과제를 가진 유사 부품으로 이전될 수 있을 만큼 정확하고 신뢰할 수 있어야 합니다."
본 연구는 주요 타당성 효과이기 때문에 "충전 성공, 미세 구조 및 수축 기공에 대한 품질 척도로서 2차 덴드라이트 암 간격(SDAS) 및 수축 기공"이라는 조사된 메트릭에 중점을 둡니다. 개발된 CAE 도구는 "주조 결함 감소 측면에서 최상의 초기 주조 공정 조건(상한)"을 가정하고 "토폴로지 최적화와 제품 설계 사이의 초기 설계 단계"에 적용하도록 설계되었습니다. 솔루션은 "최고 사례 규칙(상한)"을 기반으로 하며 "최종 공정 설계, 예를 들어 스피더 및 주입구의 수/위치에 대한 권장 사항"을 제공하는 것을 목표로 합니다. 도구의 보정 및 검증은 "최상의 초기 조건 및 효율성 향상 방법에 관한 적용된 규칙"과 함께 중요하며, "민감도 및 사례 독립성"을 연구해야 합니다.
3. 연구 배경:
연구 주제 배경:
주조 부품의 사용 중 성능은 "부품 설계뿐만 아니라 금형, 게이팅 및 피더(크기, 위치)의 주조 부품 방향, 충전 속도, 주입 및 금형 온도와 같은 공정 매개변수와 같은 제조 효과"에 따라 달라집니다. "주조 공정 제한 및 요구 사항은 속성 요구 사항(강도, 내구성, 소음 진동 가혹도 NVH, 충돌)만큼 설계 최적화에서 중요합니다." 기존 CAE 접근 방식은 "주조 전문가 기술 및 전문가 안내 분석 루프"에 의존하여 설계 반복 횟수를 제한하고 CAE 적용을 후기 제품 개발 단계로 제한합니다.
기존 연구 현황:
주조 평가를 위한 기존 CAE 접근 방식은 종종 전문가의 개입이 필요한 "수동, 컴퓨터 지원 엔지니어링(CAE) 접근 방식"입니다. 문헌 검토에서는 "충전 성공, 미세 구조(SDAS) 및 수축 기공"의 중요성을 핵심 품질 지표로 강조합니다. 이전 연구에서는 섀시 부품용 합금, 영구 금형 주조, 품질 지표, 주조 결함 및 주조 최적화 전략을 탐구했습니다. 그러나 초기 설계 단계 타당성 평가를 위한 완전 자동 CAE 도구가 필요합니다.
연구의 필요성:
"차세대 개발 프로세스에서는 다분야 설계 최적화(MDO) 도구뿐만 아니라 설계 엔지니어가 초기 설계 개념 단계에서 주조 부품 형상 변형의 타당성과 품질을 정량적이고 효율적으로 평가할 수 있도록 완전 자동화된 CAE 도구 및 전문가 시스템이 필요합니다." 초기 설계 단계에서 주조 타당성을 효율적이고 자율적으로 평가하고 수동 전문가 개입에 대한 의존도를 줄이며 더 빠른 설계 반복을 가능하게 하는 "자동 CAE 도구"에 대한 명확한 필요성이 있습니다.
4. 연구 목적 및 연구 질문:
연구 목적:
주요 연구 목적은 "알루미늄 중력 다이캐스팅의 자율적 타당성 평가"를 위한 "자동 CAE 도구"를 개발하고 검증하는 것입니다. 이 도구는 "최적화 루프에 통합하거나 주조 전문가 안내 수동 CAE 접근 방식을 위한 독립 실행형 도구로 사용할 수 있는 개방형 인터페이스를 갖춘 자동 CAE 도구를 대체"하는 것을 목표로 합니다.
주요 연구:
주요 연구는 다음 사항에 중점을 둡니다.
- "최상의 초기 조건에서 빠르고 효율적인 방식으로 시뮬레이션을 설정, 실행 및 평가하고 수동적인 사용자 개입이 필요 없는" "자동 CAE 도구" 개발.
- 도구와 "효율성 향상 방법"을 보정 및 검증하여 정확성, 신뢰성 및 새로운 과제를 가진 유사 부품으로의 이전 가능성을 보장합니다.
- "충전 성공, 미세 구조에 대한 품질 척도로서 2차 덴드라이트 암 간격(SDAS) 및 수축 기공" 조사 및 핵심 메트릭으로서의 수축 기공.
연구 가설:
본 논문에서는 전통적인 형식으로 연구 가설을 명시적으로 언급하지 않습니다. 그러나 암묵적 가설은 연구 질문 및 목표에서 추론할 수 있습니다.
- 완전 자동 CAE 도구를 알루미늄 중력 다이캐스팅의 자율적 타당성 평가를 위해 개발할 수 있다는 가설이 있습니다.
- 효율성 향상 방법은 방향성 타당성 평가의 정확성을 손상시키지 않으면서 계산 시간을 크게 줄이기 위해 CAE 도구에 구현될 수 있다는 가설이 있습니다.
- 실험 데이터를 사용하여 자동 CAE 도구 및 효율성 향상 방법을 보정하고 검증할 수 있다는 가설이 있습니다.
5. 연구 방법론
연구 설계:
본 연구는 개발 및 검증 접근 방식을 채택합니다. 여기에는 "자동 CAE 도구" 개발, 유동성 나선형 테스트의 실험 데이터를 사용하여 보정, Multi-Tool 실험으로 검증, 산업 프로토타입에 대한 타당성 및 민감도 평가가 포함됩니다.
자료 수집 방법:
다음과 같은 주조 실험에서 실험 데이터를 수집했습니다.
- 냉각 및 충전 정도를 조사하기 위한 유동성 나선형 금형.
- 냉각, 충전 거동 및 기공률을 평가하기 위한 Multi-Tool 데모 장치.
- 주조 중 온도 곡선을 측정하기 위한 열전대(TC).
- 기공률 분석을 위한 X선 및 CT 스캔.
- 미세 구조 및 기공 유형을 특성화하기 위한 금속 조직학 및 SEM.
- 기공률 정량화를 위한 아르키메데스 밀도 측정 및 블리스터 테스트.
분석 방법:
본 연구에서는 다음 방법들을 조합하여 사용합니다.
- 최고 사례 및 설계 규칙을 설정하기 위한 문헌 검토.
- 도구 개발 및 검증을 위한 Inspire Cast®를 사용한 CAE 시뮬레이션.
- 충전 성공 평가를 위한 분석적 방법.
- CAE 도구를 보정 및 검증하고 실험 데이터를 분석하기 위한 통계 분석(상관 행렬, 회귀 분석).
- 검증 및 타당성 평가를 위한 실험 및 시뮬레이션 결과의 정량적 및 정성적 비교.
연구 대상 및 범위:
본 연구는 다음 사항에 중점을 둡니다.
- 알루미늄 중력 다이캐스팅, 특히 A356 합금 사용.
- 두 가지 데모 장치 형상: 유동성 나선형 및 Multi-Tool.
- 적용 및 민감도 연구를 위한 산업 프로토타입 섀시 부품(FLCA 및 RLCA).
- 주요 품질 지표: 충전 성공, SDAS 및 수축 기공.
- 공정 매개변수: 주입 온도, 금형 온도 및 냉각 조건.
6. 주요 연구 결과:
주요 연구 결과:
- 알루미늄 중력 다이캐스팅의 자율적 타당성 평가를 위한 완전 "자동 CAE 도구" 개발.
- 충전 시뮬레이션을 순수 응고 및 분석적 충전 성공 평가로 대체하고 3D 구성 요소 대신 1D 구성 요소를 구현하는 "효율성 향상 방법" 구현.
- 유동성 나선형 실험을 사용하여 CAE 도구 보정 및 Multi-Tool 실험을 사용하여 검증.
- 실험을 통한 분석적 충전 기준 및 1D 피더 구성 요소 검증.
- 산업 프로토타입(FLCA 및 RLCA)에 대한 도구의 민감도 및 타당성 시연.
- 기본 HTC 데이터 세트 사용의 한계와 다양한 주조 부품 설계를 위한 HTC 구성 요소 클래스의 필요성 확인.
제시된 데이터 분석:
본 논문에서는 다음과 같은 광범위한 데이터 분석을 제시합니다.
- 보정 후 우수한 일치를 보여주는 실험과 시뮬레이션 간의 온도 곡선 비교.
- 거의 완벽한 일치를 보여주는 기하학적 유동 길이와 나선형 길이 비교.
- =0.3에서 우수한 일치를 보여주는 실험과 시뮬레이션 간의 충전 정도 비교.
- 불균일한 HTC 및 Inspire Cast®의 기공률 시뮬레이션의 한계로 인해 기공 위치의 차이를 보여주는 CT 스캔과의 기공률 추정 비교.
- FLCA 설계 변형에 대한 민감도 연구, 충전 성공, SDAS 및 기공률에서 관련 차이점을 식별하는 도구의 능력 입증.
그림 목록:
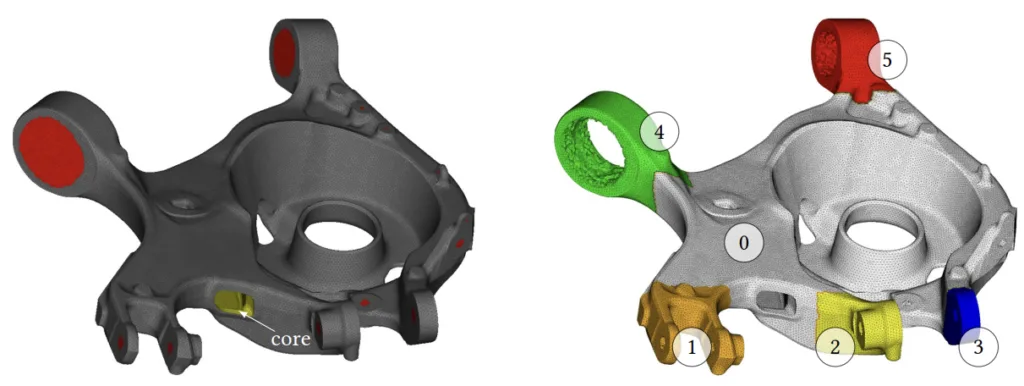
(b) mesh, critical area IDs CAID 0–5, only fullymachined (=evaluation) nodes visible
Fig. 0.2: Exemplary feature detection and critical areas of a rear lower control arm (RLCA)
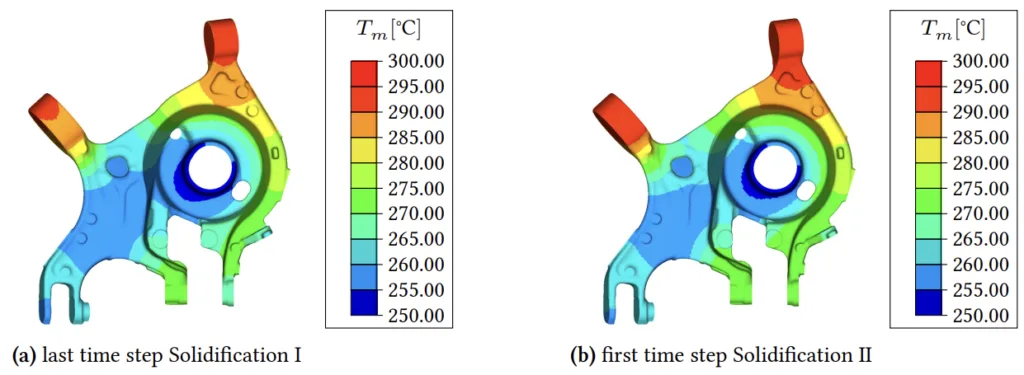
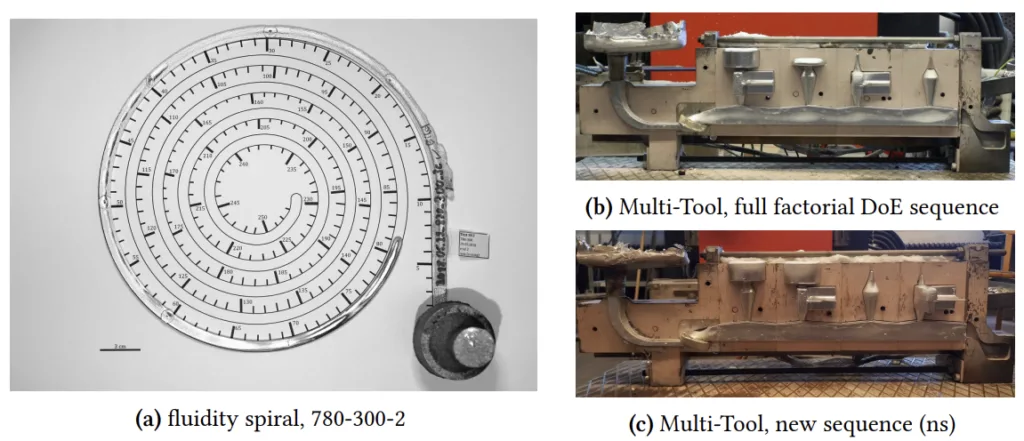
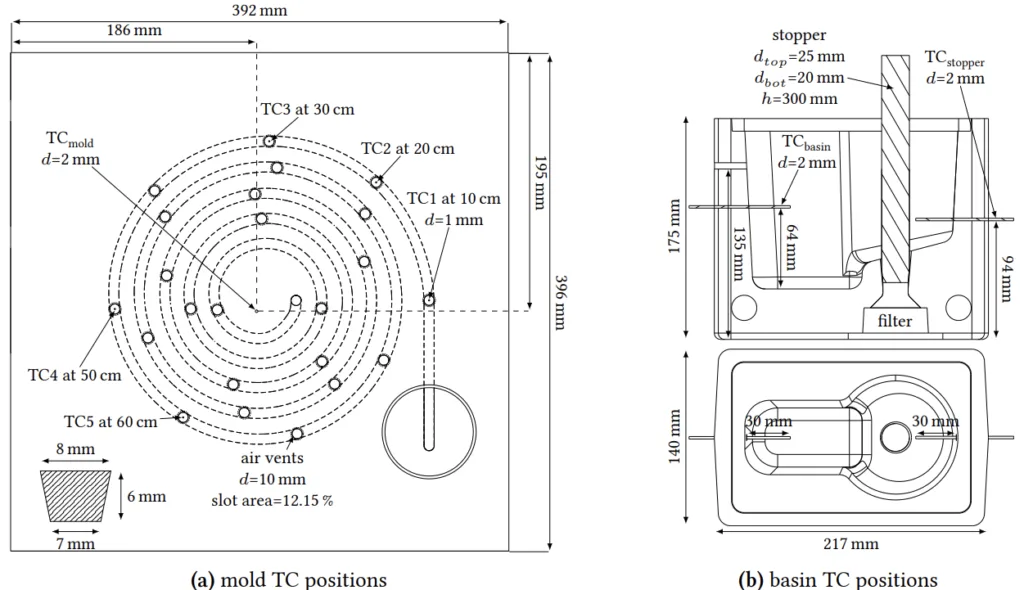
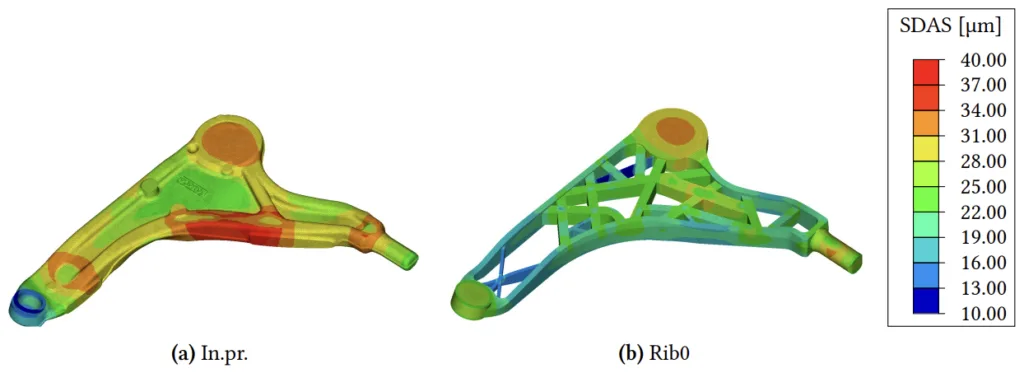
- Fig. 0.1: 자동 CAE 도구 개요
- Fig. 0.2: 후방 로어 컨트롤 암(RLCA)의 예시적인 특징 감지 및 중요 영역
- Fig. 0.3: Solidification II에 대한 피더 및 주입구 배치에서 Solidification I 결과의 예시적인 수축 기공 ℎ 평가
- Fig. 0.4: 금형 온도 필드 비교
- Fig. 0.5: Solidification II의 최종 평가
- Fig. 0.6: Assessment II의 예시적인 출력 텍스트 파일
- Fig. 0.7: 주입된 형상, 유동성 나선형 및 새로 개발된 Multi-Tool(두 가지 다른 시퀀스 포함)
- Fig. 0.8: 유동성 나선형 금형 치수 및 계측
- Fig. 0.9: 십자형 및 스핀들 치수 개요
- Fig. 0.10: 계측 기능이 있는 Multi-Tool 설계
- Fig. 0.11: Multi-Tool에 대한 샘플 및 열전대 TC 라벨링 정의
- Fig. 0.12: 온도 보정, 실험 및 계산된 온도
- Fig. 0.13: 계산된 기하학적 유동 길이 ∗ 및 나선형 길이 비교
- Fig. 0.14: 실험과 시뮬레이션의 나선형 길이 비교
- Fig. 0.15: 실험과 시뮬레이션 간의 Cf 및 Cp의 충전 정도 비교
- Fig. 0.16: 다양한 온도 설정에 대한 스핀들 및 공기 파이프 CT 스캔 결과
- Fig. 0.17: 전체 팩토리얼 DoE의 Sp 및 Cp에 대해 계산된 기공률 값
- Fig. 0.18: 다양한 FLCA 설계 변형, 벽 두께
- Fig. 0.19: 최대 기하학적 유동 길이 ∗ , SDAS 및 임계 기공 수에 대한 FLCA 설계 및 다중/단일 주입구 영향
- Fig. 0.20: 충전 성공에 대한 FLCA 설계, 다중/단일 주입구, 분석적 충전 시간 유형
∗ −
및 임계 고체 분율 값 0.3–0.7 영향 - Fig. 0.21: 충전 성공, 임계 비율 CRfill에 대한 RLCA 온도, 분석적 충전 시간 유형
∗ −
및 임계 고체 분율 값 0.3–0.7 영향 - Fig. 1.1: 주조 CAE 접근 방식
- Fig. 1.2: 논문 작업 패키지는 개발 및 보정 및 타당성 단계로 나뉩니다.
- Fig. 2.1: 예시적인 알루미늄 섀시 부품
- Fig. 2.2: 섀시 부품의 합금
- Fig. 2.3: Al-Si 상 다이어그램
- Fig. 2.4: 영구 금형 설정의 개략도
- Fig. 2.5: 유동성 결정을 위한 표준 금형
- Fig. 2.6: 다양한 유동성 나선형 길이 비교
- Fig. 2.7: 코팅 또는 금형 거칠기 효과의 개략적 시각화
- Fig. 2.8: 코팅된 금형과 용융물 사이의 계면의 개략도
- Fig. 2.9: 열 전달 계수(HTC)에 대한 문헌 값
- Fig. 2.10: 덴드라이트 형성의 개략도
- Fig. 2.11: 문헌에서 가져온 A356 SDAS 대 액상선 시간 곡선
- Fig. 2.12: 평균 SDAS ̄ (SDAS)에 대한 벽 두께 의 영향
- Fig. 2.13: 주조 표면에서 다른 거리에서의 SDAS 값
- Fig. 2.14: A356의 SDAS에 대한 금형( ) 및 주입 온도( ), 벽 두께 및 위치 영향
- Fig. 2.15: 1 atm에서 순수 알루미늄의 수소 용해도
- Fig. 2.16: A356에 대한 수축(왼쪽) 및 가스 기공(오른쪽)의 특징적인 기공 형태
- Fig. 2.17: 다양한 와 관련된 매크로 그래프의 기공률 결과
- Fig. 2.18: 다공성에 대한 벽 두께 의 영향, ZL114A 합금 판재 주조의 CT 결함 부피 def
- Fig. 2.19: 주조 시 기하학적 제조 제약
- Fig. 2.20: 주조 시뮬레이션 및 최적화 단계
- Fig. 2.21: 박스형 주조의 게이팅 시스템 변형
- Fig. 2.22: 높이 감소로 점진적으로 개선된 주조 시스템으로 인한 개선된 하단 게이팅 시스템
- Fig. 2.23: 외부(파이프, 싱크 마크) 및 내부(매크로, 마이크로) 기공률 유형의 개략도
- Fig. 2.24: 다양한 초기 속도에서 금형에 들어가는 용융물의 개략도
- Fig. 2.25: 컨트롤 암의 피더 최적화로 더 나은 수율 달성
- Fig. 2.26: 총 산화물 입자량 total
oxid 및 주조 부품 산화물 입자 cast
oxid - Fig. 2.27: 개발 시간과 관련된 [120]에서 사용된 단순화 단계
- Fig. 2.28: 가장 단순화된 버전과 완전한 버전의 결함 가능성 척도로서 Hot Spots FSTime 비교
- Fig. 2.29: 표준 및 개선된 최적화의 응고 시뮬레이션 비교
- Fig. 2.30: 통합 주조 시뮬레이션
- Fig. 2.31: ICME(Integrated Computational Materials Engineering)의 일반적인 흐름도
7. 결론:
주요 결과 요약:
본 연구에서는 알루미늄 중력 다이캐스팅의 자율적 타당성 평가를 위한 "자동 CAE 도구"를 성공적으로 개발하고 보정했습니다. 이 도구는 충전 시뮬레이션을 순수 응고 분석 및 분석적 충전 성공 평가로 대체하고 3D 구성 요소 대신 1D 구성 요소를 활용하는 것과 같은 효율성 향상 방법을 효과적으로 통합합니다. 실험적 검증을 통해 도구의 방향성 정확성을 확인하고 HTC 모델링 및 가스 기공률 예측과 관련하여 추가 개선이 필요한 영역을 식별했습니다. 이 도구는 설계 변형 및 공정 매개변수에 대한 민감도를 입증하여 초기 설계 단계 최적화를 위한 귀중한 통찰력을 제공합니다.
연구의 학문적 의의:
본 연구는 초기 설계 단계에서 효율적인 타당성 평가의 필요성을 해결하는 새로운 자동 CAE 도구를 제공함으로써 다이캐스팅 분야에 기여합니다. 보정 접근 방식 및 효율성 향상 방법 조사를 포함한 도구 개발 및 검증 방법론은 주조 시뮬레이션 및 MDO 연구자에게 귀중한 통찰력을 제공합니다. 또한 본 연구에서는 시뮬레이션 보정을 위한 정확한 데이터 세트를 얻기 위한 측정 기술의 한계를 강조하고 HTC 모델링 및 가스 기공률 시뮬레이션에서 향후 연구 방향을 제시합니다.
실용적 의미:
자동 CAE 도구는 다이캐스팅 산업에 상당한 실용적 의미를 갖습니다. 다음과 같은 이점을 제공합니다.
- 더 빠르고 효율적인 타당성 평가를 가능하게 하여 수동 전문가 개입에 대한 의존도 감소.
- 주조 타당성 및 품질에 대한 설계 변형 및 최적화의 신속한 탐색을 용이하게 하는 MDO 워크플로에 통합.
- 방향성이 있지만 타당한 결과는 초기 설계 단계 의사 결정을 위해 설계 엔지니어에게 실현 가능하고 고품질 주조 부품 설계를 안내합니다.
- HTC 모델링 및 가스 기공률 시뮬레이션과 같이 추가 연구가 필요한 영역을 강조하여 보다 예측적인 CAE 도구 개발을 위한 기반.
연구의 한계 및 향후 연구 분야:
본 연구에서는 다음과 같은 한계를 인정합니다.
- 불완전한 메트릭 범위(예: 비용 측면, 공급업체 시설별 특성)로 인해 CAE 평가는 완전히 예측 가능한 것이 아니라 방향성으로 간주되어야 합니다.
- HTC 문제 및 Inspire Cast®에서 가스 기공률 시뮬레이션이 부족하여 발생하는 정확도 제한.
- CAE 모델링에 내재된 단순화로 인해 실험 데이터에 대한 보정 및 검증이 필요합니다.
- 시뮬레이션 보정을 위한 보다 정확한 데이터 세트를 얻기 위한 측정 기술의 추가 개선 필요.
향후 연구 분야는 다음과 같습니다.
- 특히 갭 의존적 HTC 및 가스 기공률에 대한 주조 공정 시뮬레이션의 미해결 문제에 대한 물리 기반의 효율적인 방법 개발.
- 시뮬레이션 정확도 향상을 위해 다양한 주조 부품 설계를 위한 HTC 구성 요소 클래스 결정.
- 공정 매개변수 및 설계 변형이 기공 형성에 미치는 영향에 대한 추가 조사.
- 국부적 갭 크기의 함수로서 정확한 HTC를 제공하기 위한 열역학적 시뮬레이션과 주조 시뮬레이션 결합 탐색.
- 도구의 모든 효율성 향상 방법(1D 구성 요소, 순수 응고)이 "꺼져도" 이 한계에 여전히 부딪힐 것이라는 점을 지적해야 합니다.
- 더 복잡한 흐름 현상 및 용융 거동을 처리하기 위한 CAE 도구 개발.
8. 참고 문헌:
- [1] Ahmadein, M.; Pustal, B.; Wolff, N.; BÜhRig-PolaczeK, A.: “Determination and verification of the gap dependent heat transfer coefficient during permanent mold casting of A356 aluminum alloy.” In: Materialwissenschaft und Werkstofftechnik 48.12 (2017), pp. 1249–1256.
- [2] AichbeRgeR, W.; RieneR, H.; DannbaueR, H.: “Regarding Influences of Production Processes on Material Parameters in Fatigue Life Prediction.” In: SAE Technical Paper. SAE International, 2007.
- [3] AKhtaR, S.; ARnbeRg, L.; Di Sabatino, M.; DispinaR, D.; SyveRtsen, M.: “A comparative study of porosity and pore morphology in a directionally solidified A356 alloy.” In: International Journal of Metalcasting 3.1 (2009), pp. 39–52.
- [4] AllaiRe, G.; Jouve, F.; Michailidis, G.: “Molding direction constraints in structural optimization via a level-set method.” In: Variational Analysis and Aerospace Engineering. Springer, 2015, pp. 1–39.
- [5] Allison, J.: “Integrated Computational Materials Engineering: A Perspective on Progress and Future Steps.” English. In: JOM 63.4 (2011), pp. 15–18.
- [6] Allison, J.; Li, M.; WolveRton, C.; Su, X.: “Virtual aluminum castings: An industrial application of ICME.” In: JOM 58.11 (2006), pp. 28–35.
- [7] AltaiR EngineeRing, Inc: Altair HyperMesh™ – High-Fidelity Finite Element Modeling. 2019.
- [8] AltaiR EngineeRing, Inc: Altair HyperView™ – CAE Results Visualization and Reporting. 2019.
- [9] AltaiR EngineeRing, Inc: Altair SimLab™ – Multiphysics Workflows with CAD Associativity. 2020. uRl: https://www.altair.com/simlab/ (visited on 12/08/2020).
- [10] AltaiR EngineeRing, Inc: Show Simulation Results. 2019. uRl: https://solid%5Cthink%5C-ing.com/helpst/2019.2/cast/en_us/topics/cast/analysis/view_simulation_results_t.htm#view_simulation_results_t (visited on 11/26/2019).
- [11] AmeRican FoundRy Society: Aluminum Permanent Mold Handbook. Des Plaines, Illinois, 2001.
- [12] Anastasiou, K. S.: “Optimization of the aluminium die casting process based on the Taguchi method.” In: Proceedings of the Institution of Mechanical Engineers, Part B: Journal of Engineering Manufacture 216.7 (2002), pp. 969–977.
- [13] “356.0 and A356.0: Al-Si-Mg High-Strength Casting Alloys.” In: Properties and Selection of Aluminum Alloys. Ed. by AndeRson, K.; WeRitz, J.; Kaufman, J. G. ASM International, 2019.
- [14] ASM: “Al (Aluminum) Binary Alloy Phase – Diagrams, Alloy Phase Diagrams.” In:ASM Handbook. Vol. 3. ASM International, 2016, pp. 113–139.
- [15] ASTM InteRnational: E155-15. Reference Radiographs for Inspection of Aluminum and Magnesium Castings. Standard. 2015.
- [16] ASTM InteRnational: E2422-17. Digital Reference Images for Inspection of Aluminum Castings. Standard. 2017.
- [17] Baez, J. C.; Gonzalez, C.; Chavez, M. R.; CastRo, M.; JuaRez, J.: “Fourier thermal analysis of the solidification kinetics in A356/SiCp cast composites.” In: Journal of Materials Processing Technology 153-154 (2004). Proceedings of the International Conference in Advances in Materials and Processing Technologies, pp. 531–536.
- [18] BÄhR, R.; Rehse, C.; StRoppe, H.: “Auswirkung von Porosität auf Festigkeit und Lebensdauer von Gussteilen - theoretische Modellierung.” de. In: Deutscher Gießereitag 2014. 2014.
- [19] Bazhenov, V. E.; PetRova, A. V.; Koltygin, A. V.: “Simulation of Fluidity and Misrun Prediction for the Casting of 356.0 Aluminum Alloy into Sand Molds.” In: International Journal of Metalcasting 12.3 (2018), pp. 514–522.
- [20] BDG: P202. Volumendefizite von Gussstücken aus Aluminium-, Magnesium- und Zinkgusslegierungen. 2010.
- [21] BDG: P203. Porositätsanalyse und -beurteilung mittels industrieller Röntgen-Computertomographie (CT). 2019.
- [22] Beganovic, T.: “Evolution im Aluminium-Guss von Fahrwerk-Komponenten.” PhD thesis. Fakultät für Werkstoffwissenschaft und Werkstofftechnologie der Technischen Universität Bergakademie Freiberg, 2016.
- [23] BETA Simulation Solutions: ANSA – The advanced CAE pre-processing software for complete model build up. 2018.
- [24] BETA Simulation Solutions: META – The high performance multi-disciplinary CAE post-processor. 2018.
- [25] Biancolini, M. E.: “Mesh Morphing and Smoothing by Means of Radial Basis Functions (RBF).” In: Handbook of Research on Computational Science and Engineering. IGI Global, 2012, pp. 347–380.
- [26] Bonollo, F.; Timelli, G.; GRamegna, N.; B.Molinas: “Permanent Mold Casting of Aluminum Alloys: Correlation among Processing, Microstructure and Simulation.” In: Proceeding of 3ʳd International Conference High Tech Die Casting. 2006.
- [27] BousKa, O.: “The effect of different casting parameters on the relationship between flowability, mould filling capacity and cooling conditions of Al-Si alloys.” In: Metalurgija-Journal of Metallurgy 14 (2008), pp. 18–30.
- [28] BRabazon, D.; BRowne, D. J.; CaRR, A. J.: “Experimental investigation of the transient and steady state rheological behaviour of Al–Si alloys in the mushy state.” In: Materials Science and Engineering: A 356.1 (2003), pp. 69–80.
- [29] BRamann, H.; PavlaK, L.: “Innovatives Produktdesign und robuste Prozessauslegung durch virtuelles Experimentieren mit der Gießprozess-Simulation.” In:GIESSEREI 102.3 (2015), pp. 28–39.
- [30] BRamann, H.; LeinewebeR, L.; StuRm, J. C.: “Innovatives Produktdesign und robuste Prozessauslegung im Druckgießprozess mit Autonomous Engineering.” In: GIESSEREI 105.1 (2018), pp. 34–45.
- [31] BRandenbeRgeR, U.: Giess- und Anschnitttechnik nach Friedrich Nielsen. Ed. by BRandenbeRgeR, U. online. 2009.
- [32] BRandenbeRgeR, U. et al.: Sand- und -Kokillenguss aus Aluminium. Bundesverband der Deutschen Gießerei-Industrie (BDG), 2010.
- [33] BRůna, M.; SlÁdeK, A.; KuchaRčiK, L.: “Formation of porosity in Al-Si alloys.” In: ́ Archives of Foundry Engineering 12.1 (2012), pp. 5–8.
- [34] BRůna, M.; BolibRuchovÁ, D.; PastiRčÁK, R.: “Numerical Simulation of Porosity for Al Based Alloys.” In: 177 (2017), pp. 488–495.
- [35] BRunhubeR, E.: Leichtmetall- und Schwermetall-Kokillenguss. Schiele & Schön, 1966.
- [36] BÜhRig-PolaczeK, A.; Michaeli, W.; SpuR, G.: Handbuch Urformen. Carl Hanser Verlag GmbH & Co. KG, 2013.
- [37] Cabannes, P. M.; FoRRest, R.; MuRatoRe, G.; RÖdteR, H.; GagnÉ, M.: Gusseisen mit Kugelgraphit - Das Wichtigste über Anschnitt und Speisertechnik. Rio Tinto iron & Titanium Inc., 2002.
- [38] CaliaRi, D.; Timelli, G.; Bonollo, F.; AmalbeRto, P.; GioRdano, P.: “Fluidity of aluminium foundry alloys: Development of a testing procedure.” In: Metallurgia Italiana 107.6 (2015), pp. 11–18.
- [39] Cambell, J.; HaRding, A.: “3201: Introduction to Casting Technology.” In: TALAT Lecture. Birmingham: EAA – European Aluminium Association, 1994.
- [40] Campbell, J.: “Invisible macrodefects in castings.” In: Le Journal de Physique IV 3.C7 (1993), pp. 861–872.
- [41] Campbell, J.: “Review of fluidity concepts in casting.” In: Cast Metals 7 (4 1995), pp. 227–237.
- [42] Campbell, J.: “Chapter 10 - The 10 Rules for Good Castings.” In: Complete Casting Handbook (Second Edition). Ed. by Campbell, J. Second Edition. Boston: Butterworth-Heinemann, 2015, pp. 535–638.
- [43] Campbell, J.: “Chapter 11 - Filling system design fundamentals.” In: Complete Casting Handbook. Ed. by Campbell, J. Oxford: Butterworth-Heinemann, 2011, pp. 741–756.
- [44] Campbell, J.: “Chapter 2 - Entrainment.” In: Complete Casting Handbook. Ed. by Campbell, J. Oxford: Butterworth-Heinemann, 2011, pp. 19–103.
- [45] Campbell, J.: “Chapter 3 - Flow.” In: Complete Casting Handbook. Ed. by Campbell, J. Oxford: Butterworth-Heinemann, 2011, pp. 105–153.
- [46] Campbell, J.: “Chapter 4 - Molds and cores.” In: Complete Casting Handbook. Ed. by Campbell, J. Oxford: Butterworth-Heinemann, 2011, pp. 155–186.
- [47] Campbell, J.: “Chapter 5 - Solidification structure.” In: Complete Casting Handbook. Ed. by Campbell, J. Oxford: Butterworth-Heinemann, 2011, pp. 187–253.
- [48] Campbell, J.: “Chapter 6 - Casting alloys.” In: Complete Casting Handbook. Oxford: Butterworth-Heinemann, 2011, pp. 255–390.
- [49] CaRl Zeiss MicRoscopy GmbH: AxioVision 4 Modul MosaiX. 2019. uRl: https : / / www.micro-shop.zeiss.com/de/de/system/axiovision+software/software+axiovision/module+biomed%252Fmat/000000-1235-913 (visited on 11/18/2019).
- [50] CaRlson, K. D.; BecKeRmann, C.: “Prediction of Shrinkage Pore Volume Fraction Using a Dimensionless Niyama Criterion.” In: Metallurgical and Materials Transactions A 40.1 (2009), pp. 163–175.
- [51] Chen, R.; Shi, Y.-F.; Xu, Q.-Y.; Liu, B.-C.: “Effect of cooling rate on solidification parameters and microstructure of Al-7Si-0.3Mg-0.15Fe alloy.” In: Transactions of Nonferrous Metals Society of China 24.6 (2014), pp. 1645–1652.
- [52] Chen, R. et al.: “Correlation of solidification microstructure refining scale, Mg composition and heat treatment conditions with mechanical properties in Al-7Si-Mg cast aluminum alloys.” In: Materials Science and Engineering: A 685 (2017), pp. 391–402.
9. 저작권:
- 본 자료는 "[Marcus Schopen]"의 논문: "[An Automatic CAE Tool for autonomous feasibility assessment of aluminum gravity die castings – development and calibration]"을 기반으로 합니다.
- 논문 출처: 10.18154/RWTH-2022-07470
본 자료는 상기 논문을 기반으로 요약되었으며, 상업적 목적으로 무단 사용하는 것을 금지합니다.
Copyright © 2025 CASTMAN. All rights reserved.