본 논문 요약은 ['Int J Adv Manuf Technol']에 발표된 ['고압 다이캐스팅을 이용한 알루미늄 자동차 클러치 하우징 제조를 위한 금형 구조 설계 및 주조 시뮬레이션'] 논문을 기반으로 작성되었습니다.
1. 개요:
- 제목: 고압 다이캐스팅을 이용한 알루미늄 자동차 클러치 하우징 제조를 위한 금형 구조 설계 및 주조 시뮬레이션 (Mold structure design and casting simulation of the high-pressure die casting for aluminum automotive clutch housing manufacturing)
- 저자: 정성일, 진철규, 서형윤, 김종덕, 강충길 (Seong Il Jeong, Chul Kyu Jin, Hyung Yoon Seo, Jong Deok Kim, Chung Gil Kang)
- 출판 연도: 2015년
- 출판 저널/학회: 국제 첨단 제조 기술 저널 (Int J Adv Manuf Technol)
- 키워드: 고압 다이캐스팅, 금형 구조, 주조 시뮬레이션, 주조 결함, 알루미늄 합금 (High-pressure die casting, Mold structure, Casting simulation, Casting defects, Aluminum alloy)
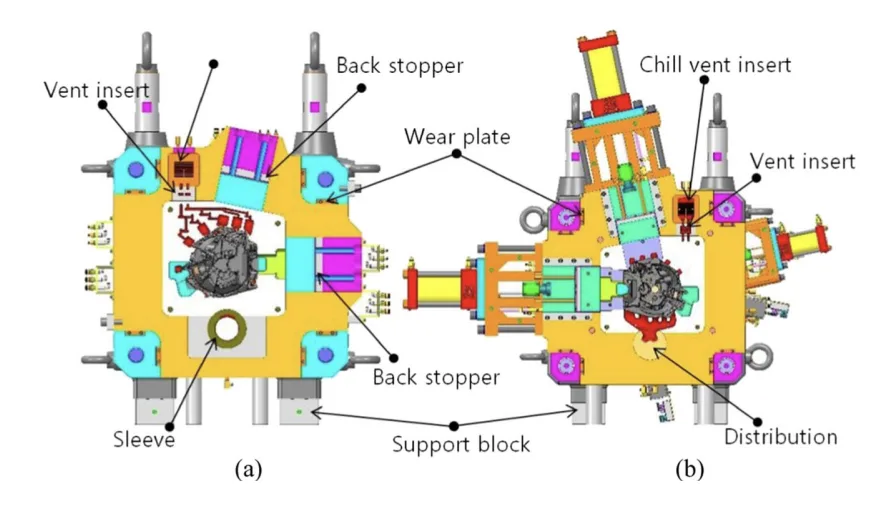
2. 연구 배경:
연구 주제 배경:
1915년 Doehle이 알루미늄 합금을 사용한 다이캐스팅 제품을 제조하기 시작한 이후, 특히 자동차 산업의 발전과 함께 다이캐스팅 제품에 대한 수요가 꾸준히 증가해 왔습니다 [1]. 알루미늄 자동차 부품 주조 방법 중에서는 고압 다이캐스팅(HPDC), 중력 다이캐스팅, 저압 다이캐스팅이 가장 일반적으로 사용됩니다. 저압 및 중력 다이캐스팅은 실린더 헤드와 같이 내부 구조가 복잡한 자동차 부품에 적용 가능하지만, HPDC는 기존에 저압 또는 중력 주조 방식으로 생산되던 경량 자동차 부품의 대량 생산에 점차적으로 적용되고 있습니다 [2-7]. HPDC는 수십 초에서 100~180초의 짧은 시간 안에 복잡하고 정밀한 형상을 대량 생산할 수 있다는 장점이 있습니다.
기존 연구 현황:
과거 다이캐스팅 금형 설계는 금형 설계자와 현장 기술자의 시행착오 방식에 의존하는 경향이 있었습니다. 그러나 고압 다이캐스팅 금형 설계 프로세스는 컴퓨터 지원 엔지니어링(CAE)을 채택하여 초기 개발 단계에서 충전 및 응고 공정 시뮬레이션을 포함합니다. 이러한 CAE 기반 접근 방식은 품질 예측 및 평가를 가능하게 하여 최적화된 금형 설계를 확립합니다 [5, 8-10]. 오늘날 많은 설계자들이 CAE와 실무 경험을 결합한 금형 설계 방법을 채택하여 불량률을 줄이고 비용을 절감하며 개발 기간을 단축합니다. 또한 금형 고착 및 변형 예측이 가능하므로 금형의 구조 설계에도 큰 도움이 됩니다.
연구의 필요성:
본 연구는 특히 클러치 하우징과 같은 복잡한 자동차 부품의 HPDC에서 견고한 금형 설계의 필요성을 강조합니다. 본 연구는 충전 및 응고 단계에서 발생할 수 있는 잠재적인 주조 결함을 예측하고 완화하기 위해 주조 시뮬레이션 적용을 강조합니다. 또한 최소한의 주조 결함으로 최적화된 품질의 제품을 생산하기 위한 게이팅 시스템 설계 및 제품 형상 최적화를 목표로 하며, 금형 설계 단계부터 잠재적인 금형 손상을 예측하고 실험 횟수를 최소화하여 생산 비용과 시간을 절감하기 위해 금형 베이스의 구조 시뮬레이션을 수행합니다.
3. 연구 목적 및 연구 질문:
연구 목적:
본 연구의 목적은 고압 다이캐스팅 공정에서 알루미늄 자동차 클러치 하우징 부품을 제조하기 위한 금형 설계를 개발하는 것입니다. 이는 효율적이고 결함 없는 생산을 보장하기 위해 주조 시뮬레이션과 금형 구조 시뮬레이션을 통해 달성됩니다.
핵심 연구 질문:
- 용융 금속이 금형으로 흘러 들어가 제품 섹션을 고르게 채우도록 5개의 게이트를 갖는 게이팅 시스템을 설계하는 방법은 무엇인가?
- 충전 과정 및 응고 과정에서 발생할 수 있는 주조 결함의 가능성을 예측하거나 방지하기 위해 주조 시뮬레이션 프로그램인 MAGMAsoft를 사용하는 방법은 무엇인가?
- 클러치 하우징 제품 제조에 적합한 주조 장치를 선정하는 방법은 무엇인가?
- 금형 설계 단계에서부터 취약한 금형 부분에 대한 잠재적 손상을 예측하기 위해 ANSYS Workbench를 사용하여 금형 베이스의 구조 시뮬레이션을 수행하는 방법은 무엇인가?
연구 가설:
명시적으로 가설로 제시되지는 않았지만, 본 연구는 다음과 같은 전제하에 진행됩니다.
- 주조 및 구조 해석을 모두 통합한 시뮬레이션 기반 금형 설계는 주조 결함이 최소화된 알루미늄 자동차 클러치 하우징을 생산할 수 있는 견고한 금형을 만들 것이다.
- 시뮬레이션 결과를 바탕으로 최적화된 게이팅 시스템 설계 및 금형 구조는 제품 품질을 향상시키고 제조 비용과 시간을 절감할 것이다.
4. 연구 방법론
연구 설계:
본 연구는 주조 및 구조 시뮬레이션을 통합한 시뮬레이션 기반 설계 방법론을 채택하고 실제 숏 테스트를 통한 실험적 검증을 수행합니다.
자료 수집 방법:
- 주조 시뮬레이션: MAGMAsoft를 활용하여 충전 및 응고 과정을 시뮬레이션하고 잠재적인 주조 결함을 예측했습니다.
- 구조 시뮬레이션: ANSYS Workbench를 사용하여 금형 베이스의 구조 해석을 수행하고 잠재적인 손상을 예측했습니다.
- 실험적 검증: 실제 숏 테스트를 수행하여 5개의 클러치 하우징 제품을 제조했습니다. 주조 후 분석에는 표면 결함에 대한 육안 검사, 수축 기공 평가, 비커스 경도 측정이 포함되었습니다.
- 온도 측정: 예열 및 주조 중 금형 온도를 비접촉식 열화상 카메라를 사용하여 측정했습니다.
분석 방법:
- 시뮬레이션 분석: MAGMAsoft 시뮬레이션 결과를 분석하여 게이팅 시스템을 최적화하고 수축 기공과 같은 주조 결함을 예측했습니다. ANSYS Workbench 결과를 분석하여 금형 베이스 구조를 최적화하고 구조적 무결성을 확보했습니다.
- 실험 데이터 분석: MAGMAsoft에서 예측된 수축 기공 위치와 숏 테스트 샘플에서 관찰된 실제 기공을 비교했습니다. 주조 부품의 표면 품질을 평가했습니다. 클러치 하우징의 여러 위치에서 비커스 경도를 측정하고 분석했습니다. 시뮬레이션된 금형 온도 분포와 열화상 측정 결과를 비교했습니다.
연구 대상 및 범위:
본 연구는 고압 다이캐스팅을 통해 생산되는 알루미늄 자동차 클러치 하우징의 금형 설계 및 제조 공정에 초점을 맞춥니다. 범위는 다음을 포함합니다.
- 알루미늄 자동차 클러치 하우징의 HPDC용 금형 설계.
- 충전 및 응고를 포함한 주조 공정 시뮬레이션.
- 금형 베이스의 구조 시뮬레이션.
- 숏 테스트 및 클러치 하우징 제품의 주조 후 분석을 통한 실험적 검증.
- 재료: 클러치 하우징용 ALDC12 알루미늄 합금 및 금형 베이스용 GCD500 연성 철.
5. 주요 연구 결과:
핵심 연구 결과:
- 게이팅 시스템 설계: 5개의 게이트 게이팅 시스템이 용융 금속의 고른 흐름과 클러치 하우징 금형 캐비티의 완전한 충전을 용이하게 하도록 성공적으로 설계되었습니다 (Fig. 1).
- 주조 시뮬레이션 및 결함 예측: MAGMAsoft 시뮬레이션은 주조 내 수축 기공의 가능성을 효과적으로 예측했습니다. 예측된 수축 기공 위치는 제조된 부품에서 관찰된 실제 발생 위치와 밀접한 상관관계를 보였습니다.
- 금형 구조 시뮬레이션 및 최적화: ANSYS Workbench를 사용한 구조 시뮬레이션은 금형 베이스 두께를 최적화하는 데 매우 중요했습니다. 23cm 금형 베이스 두께가 추가적인 지지대 없이도 충분하고 안전한 것으로 확인되었습니다 (Fig. 7d).
- 숏 테스트 검증: 실제 숏 테스트를 통해 5개의 알루미늄 클러치 하우징 부품을 성공적으로 생산했습니다. 모든 부품은 완전히 충전되었고 표면 결함이 나타나지 않았습니다. 제조된 클러치 하우징의 경도는 위치에 관계없이 약 84 HV로 일관되게 측정되었습니다.
- 온도 분포 분석: 열화상 카메라를 사용한 온도 측정 결과는 주조 시뮬레이션에서 예측한 온도 분포와 합리적인 일치를 보였습니다 (Fig. 15).
데이터 해석:
결과는 시뮬레이션 예측과 실험 결과 사이에 강력한 상관관계가 있음을 보여줍니다. 주조 시뮬레이션은 잠재적인 수축 기공 영역을 정확하게 식별했으며, 구조 시뮬레이션은 금형 베이스 두께 최적화를 효과적으로 안내했습니다. 결함 없는 클러치 하우징을 생산한 성공적인 숏 테스트는 본 연구에서 사용된 시뮬레이션 기반 금형 설계 접근 방식의 효과를 입증합니다. 부품 전체에서 일관된 경도 값은 공정 안정성과 제품 균일성을 나타냅니다.
그림 목록:
- Fig. 1 클러치 하우징의 게이팅 시스템 설계 (Gating system design of clutch housing)
- Fig. 2 3D 금형 모델링: a 고정 금형 및 b 이동 금형 (3D mold modeling: a fixed mold and b movable mold)
- Fig. 3 금형 냉각 라인 (Cooling line of mold)
- Fig. 4 이동 금형 각 사분면의 체결력 (Locking force in each quadrant of movable mold)
- Fig. 5 구조 해석을 위한 이동 금형 베이스의 형상 조건 (Shape condition of movable mold base for structural analysis)
- Fig. 6 조립된 고압 다이캐스팅 기계 금형: a 고정 금형 및 b 이동 금형 (Molds assembled high-pressure die casting machine: a fixed mold and b movable mold)
- Fig. 7 이동 금형 베이스의 구조 해석 결과: a h=20 cm, b h=22 cm, c h=24 cm, 및 d h=23 cm (Results of structural analysis for movable mold base: a h=20 cm, b h=22 cm, c h=24 cm, and d h=23 cm)
- Fig. 8 금형 캐비티 내 충전 거동 (Filling behavior in mold cavity)
- Fig. 9 금형 캐비티 내 공기압 및 공기 포획 (Air pressure and air entrapment in mold cavity)
- Fig. 10 금형 캐비티 내 속도 분포 (Velocity distribution in mold cavity)
- Fig. 11 충전 완료 후 금형 캐비티 내 응고 거동 (Solidification behavior in mold cavity after filling finish)
- Fig. 12 응고 완료 후 수축 기공 (Shrinkage porosity after solidification finish)
- Fig. 13 응고 완료 후 금형 납땜: a 고정 금형 및 b 이동 금형 (Mold soldering after solidification finish: a fixed mold and b movable mold)
- Fig. 14 예열 후 금형 온도 분포 (열화상 카메라 측정): a 고정 금형 및 b 이동 금형 (Temperature distribution of molds after pre-heating measured by thermo-graphic camera: a fixed mold and b movable mold)
- Fig. 15 시뮬레이션과 실제 숏 테스트 간의 금형 온도 비교: a 시뮬레이션 결과 및 b 실제 숏 테스트 (Comparison of mold temperature between simulation and real shot test: a simulation result and b real shot test)
- Fig. 16 제작된 클러치 하우징 주물: a 첫 번째 숏, b 두 번째 숏, c 세 번째 숏, d 네 번째 숏, 및 e 다섯 번째 숏 (Fabricated clutch housing castings: a first shot, b second shot, c third shot, d fourth shot, and e fifth shot)
- Fig. 17 시뮬레이션과 실제 숏 테스트 간의 기공 분포 비교 (Comparison of porosity distribution between simulation and real shot test)
- Fig. 18 다른 위치에서 클러치 하우징의 미세 구조: a 일반 두께 및 b 두꺼운 두께 (Microstructures of clutch housing in different positions: a normal thickness and b thick thickness)
- Fig. 19 다른 위치에서 비커스 경도 (Vickers hardness at different positions)
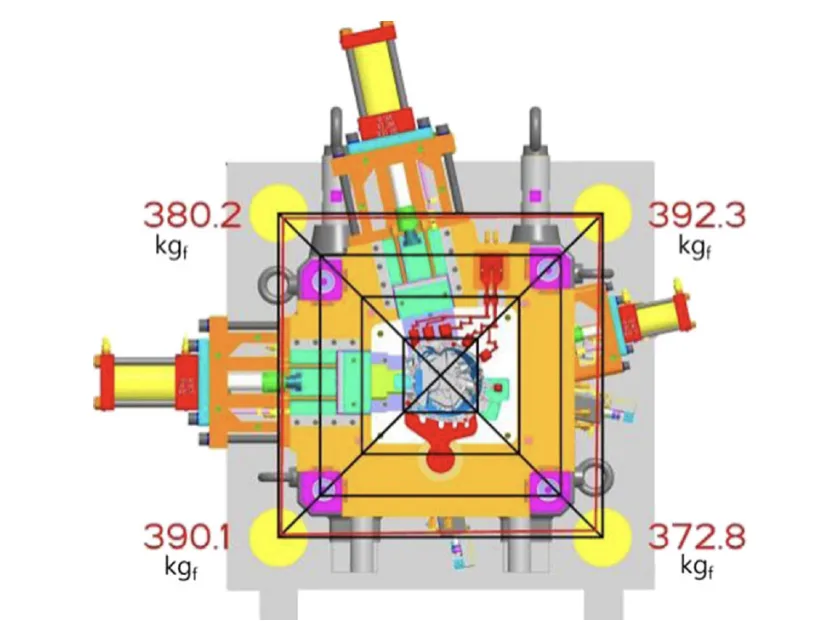
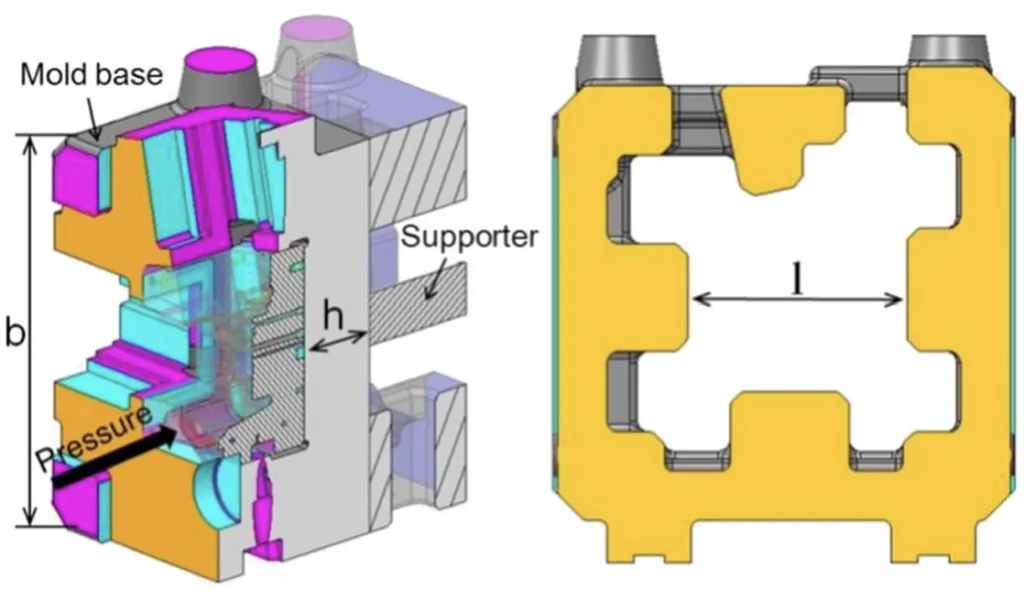
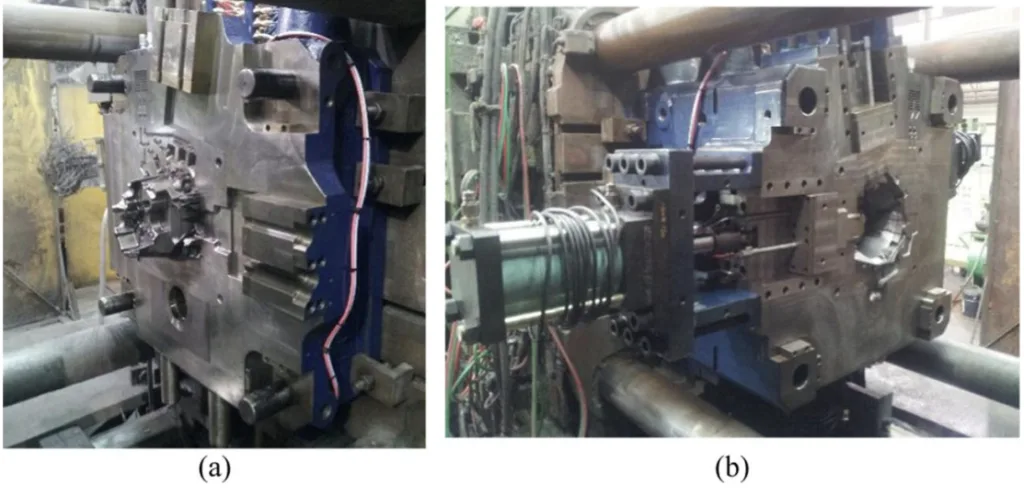
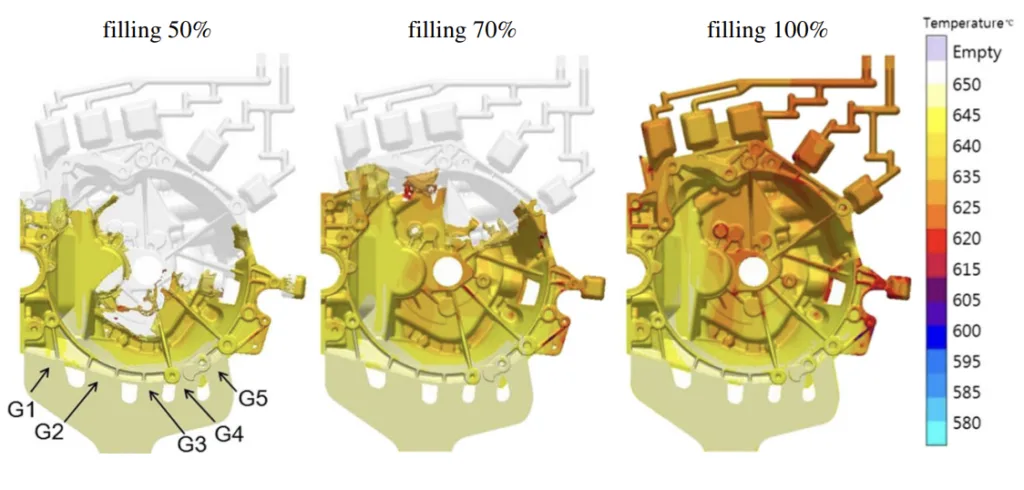
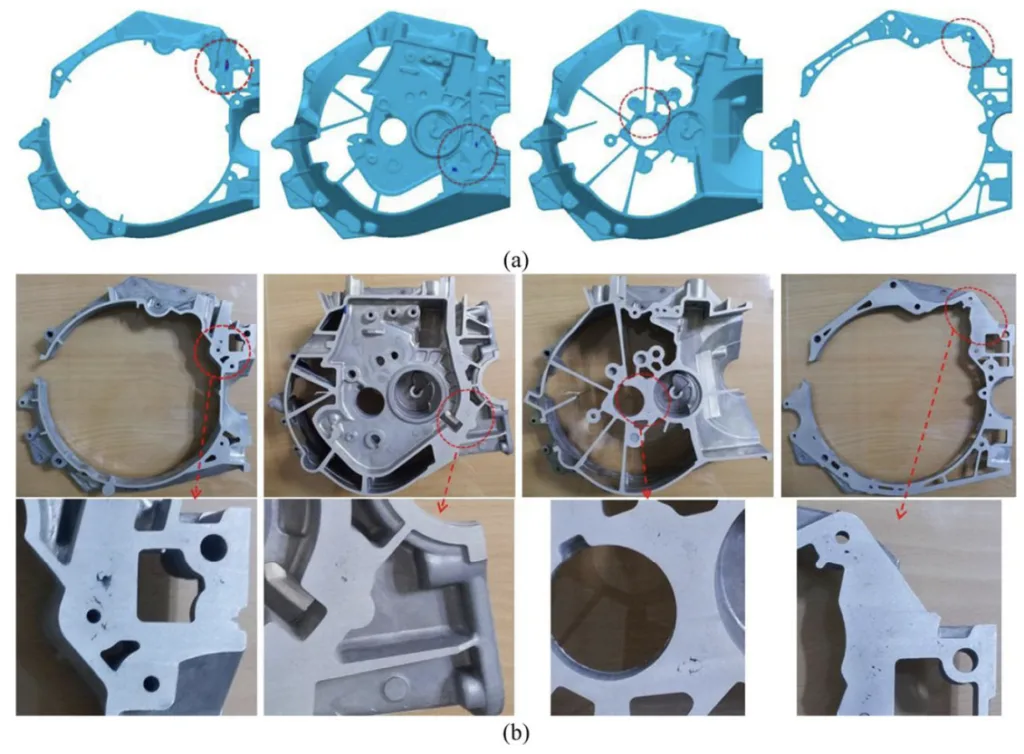
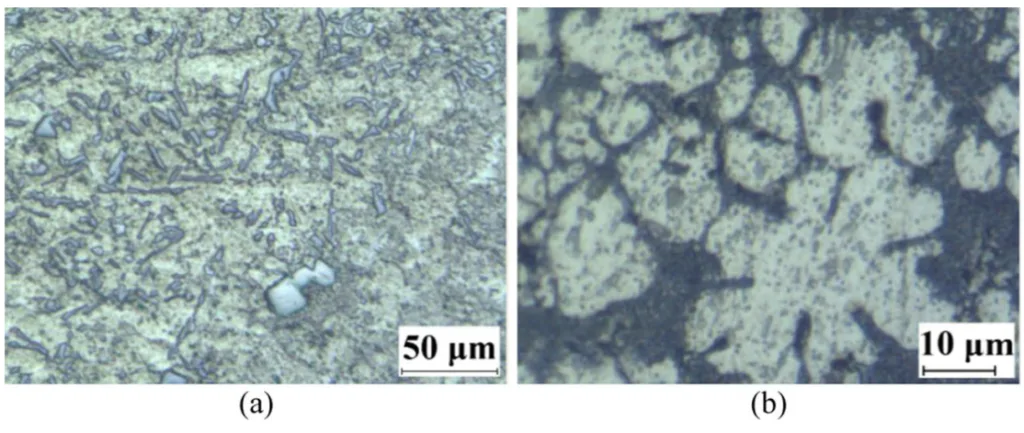
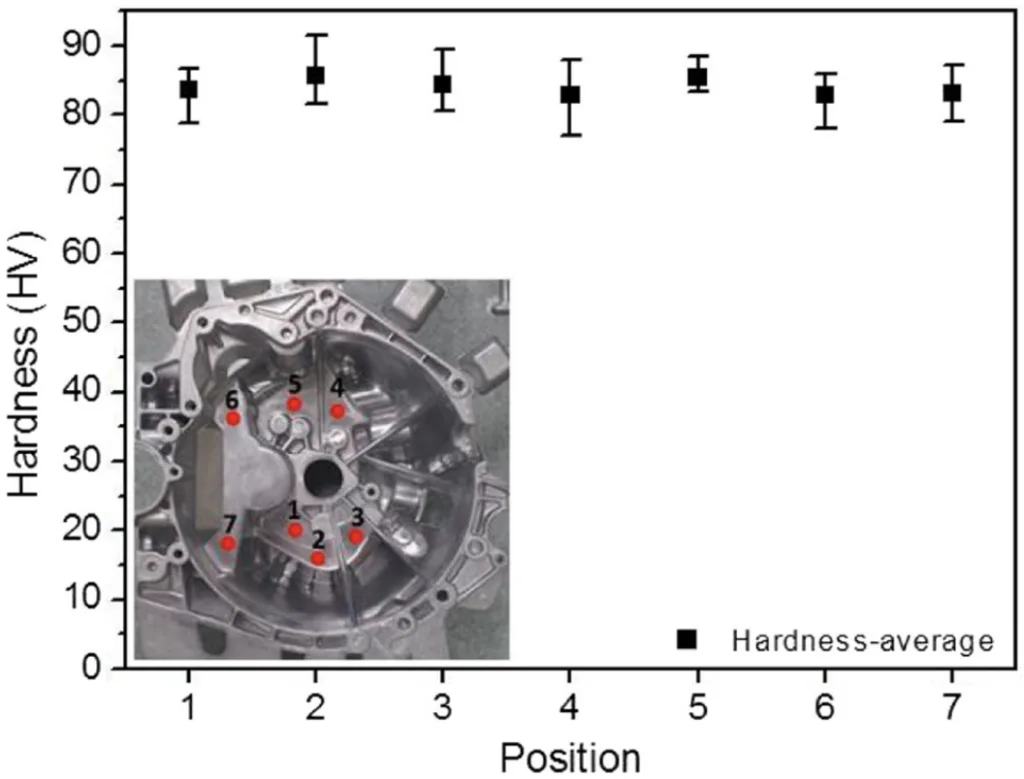
6. 결론:
주요 결과 요약:
본 연구는 알루미늄 자동차 클러치 하우징의 고압 다이캐스팅을 위한 금형 설계에 시뮬레이션 기반 접근 방식을 성공적으로 입증했습니다. MAGMAsoft와 ANSYS Workbench를 각각 사용하여 주조 및 구조 시뮬레이션을 통합함으로써 5-게이트 게이팅 시스템과 23cm 두께의 금형 베이스를 최적화했습니다. 숏 테스트를 통한 실험적 검증은 시뮬레이션 예측을 확인하여 일관된 경도를 가진 결함 없는 클러치 하우징 생산으로 이어졌습니다.
연구의 학문적 의의:
본 연구는 다이캐스팅 금형 설계에 CAE 도구를 사용하는 것의 학문적 중요성을 강조합니다. 복잡한 HPDC 부품용 금형 설계를 위한 상세하고 검증된 방법론을 제공합니다. 본 연구는 주조 결함 예측, HPDC 조건 하에서 금형 구조 거동, 제조 공정에서 시뮬레이션 기반 최적화의 효과에 대한 지식 체계에 기여합니다.
실용적 의미:
본 연구의 실용적 의미는 다이캐스팅 산업에 상당합니다. 제시된 방법론은 비용이 많이 들고 시간이 많이 소요되는 시행착오 접근 방식에 대한 의존도를 최소화하면서 복잡한 자동차 부품용 견고한 금형을 설계할 수 있는 경로를 제공합니다. 주조 및 구조 시뮬레이션을 활용함으로써 제조업체는 생산 비용을 절감하고 개발 주기를 단축하며 HPDC 부품의 품질과 신뢰성을 향상시킬 수 있습니다.
연구의 한계점
본 연구의 한계점은 단일 부품(클러치 하우징)과 재료(ALDC12)에 초점을 맞추었다는 것입니다. 방법론은 견고하지만, 크게 다른 부품 형상 또는 합금 시스템으로의 직접적인 일반화에는 추가적인 연구가 필요합니다. 또한 수축 기공 예측은 합리적으로 정확했지만, 시뮬레이션된 위치와 실제 위치 간의 불일치는 시뮬레이션 모델 개선 또는 향후 연구에서 추가적인 영향 요인 고려가 필요한 영역임을 시사합니다.
7. 향후 후속 연구:
- 후속 연구 방향
향후 연구는 특히 수축 기공의 정확한 위치와 범위와 관련하여 결함 예측의 정확도를 높이기 위해 시뮬레이션 모델을 개선하는 데 초점을 맞춰야 합니다. 주입 속도 프로파일 및 냉각 전략과 같은 다양한 공정 매개변수와 주조 품질에 대한 재료 변화의 영향에 대한 추가 연구가 필요합니다. - 추가 탐구가 필요한 영역
추가 탐구가 필요한 영역에는 본 연구에서 예측되었지만 광범위하게 실험적으로 검증되지는 않은 금형 침식 및 금형 고착 현상에 대한 보다 자세한 분석이 포함됩니다. 개발된 방법론을 더 넓은 범위의 복잡한 HPDC 부품과 다양한 알루미늄 합금에 적용하면 다용도성과 산업적 적용 가능성을 더욱 검증할 수 있을 것입니다.
8. 참고 문헌:
- [1] Doehler die-casting co (1916) Creating and industry. Brooklyn, New York
- [2] Jin CK, Bae JW, Kang CG (2014) Development of rheology vacuum low-pressure die casting with electromagnetic stirrer and vacuum system. Proc IMechE Part B J Eng Manuf 228(12):1599-1610
- [3] Zhang L, Wang R (2013) An intelligent system for low-pressure die-cast process parameters optimization. Int J Adv Manuf Technol 65:517-524
- [4] Hsu FY, Jolly MR, Campbell J (2009) A multiple-gate runner system for gravity casting. J Mater Process Technol 209:5736–5750
- [5] Jin CK, Kang CG (2011) Fabrication process analysis and experimental verification for aluminum bipolar plates in fuel cells by vacuum die-casting. J Power Sources 196:8241-8249
- [6] Kim ES, Lee KH, Moon YH (2000) A feasibility study of the partial squeeze and vacuum die casting process. J Mater Process Technol 105:42-48
- [7] Jin CK, Kang CG (2012) Fabrication by vacuum die casting and simulation of aluminum bipolar plates with micro-channels on both sides for proton exchange membrane (PEM) fuel cells. Int J Hydrog Energy 37:1661-1676
- [8] Chang QM, Chen CJ, Zhang SC, Schwam D, Wallace JF (2010) Effects of process parameters on quality of squeeze casting A356 alloy. Int J Cast Met Res 23:30-36
- [9] Hu BH, Tong KK, Niu XP, Pinwill I (2000) Design and optimisation of runner and gating systems for the die casting of thin-walled magnesium telecommunication parts through numerical simulation. J Mater Process Technol 105:128-133
- [10] Chen JH, Hwang WS, Wu CH, Lu SS (2011) Design of die casting process of top cover of automobile generator through numerical simulations and its experimental validation. Int J Cast Met Res 24:163-169
- [11] Jang JCH (1994) Casting plan of aluminum die castings. J Korean Foundry Soc 14(4):294-304
- [12] Kim ES, Lee KH (1998) High casting technology for aluminum alloy die casting (I). J Korean Foundry Soc 18(3):211-221
9. 저작권:
- 본 자료는 "정성일, 진철규, 서형윤, 김종덕, 강충길"의 논문: "고압 다이캐스팅을 이용한 알루미늄 자동차 클러치 하우징 제조를 위한 금형 구조 설계 및 주조 시뮬레이션"을 기반으로 작성되었습니다.
- 논문 출처: https://doi.org/10.1007/s00170-015-7566-4
본 자료는 상기 논문을 요약하여 작성되었으며, 상업적 목적으로 무단 사용하는 것을 금지합니다.
Copyright © 2025 CASTMAN. All rights reserved.