본 기술 자료 요약은 "[asting Characteristics of Aluminum Die Casting Alloys]" 논문을 기반으로 작성되었으며, "[미국 에너지부 산업 기술 사무국]"에서 발표되었습니다.
1. 개요:
- 제목: 알루미늄 다이캐스팅 합금의 주조 특성 (Casting Characteristics of Aluminum Die Casting Alloys)
- 저자: 마클루프 M. 마클루프 (Makhlouf M. Makhlouf), 디란 아펠리안 (Diran Apelian)
- 발행 연도: 2002년 2월 5일
- 발행 저널/학회: 미국 에너지부 산업 기술 사무국 (US Department of Energy, Office of Industrial Technologies)
- 키워드: 알루미늄 합금, 다이캐스팅, 주조 특성, 다이 솔더링, 슬러지 형성, 유동성 (Aluminum alloys, die casting, casting characteristics, die soldering, sludge formation, fluidity)

2. 연구 배경:
*연구 주제의 사회적/학문적 맥락:
본 연구는 "알루미늄 다이캐스팅 합금의 합금 - 미세 구조 - 성능 상호 작용 (Alloy - Microstructure - Performance Interactions in Aluminum Die Casting Alloys)"이라는 이전 프로그램의 후속 연구입니다. 이전 프로그램에서는 알루미늄 다이캐스팅 합금의 미세 구조 및 특성에 대한 10가지 원소와 일부 상호 작용의 효과를 조사했습니다. 이전 연구를 바탕으로 향상된 기계적 및 물리적 특성을 나타내는 합금의 최적 조성이 예측되었습니다. 이러한 예측된 합금은 우수한 기계적 또는 물리적 특성을 가질 수 있지만, 다이캐스팅이 용이할지는 불확실했습니다. 따라서 본 연구는 이러한 알루미늄 다이캐스팅 합금의 주조 특성을 조사하기 위해 시작되었습니다. 다이캐스팅은 중요한 제조 공정이며, 알루미늄 합금의 주조 특성을 이해하는 것은 고품질 부품 생산에 필수적입니다.
*기존 연구의 한계:
기존 연구는 알루미늄 다이캐스팅 합금의 기계적 및 물리적 특성 최적화에 초점을 맞추었으며, 주조 특성, 특히 다이 솔더링, 슬러지 형성, 유동성 및 피삭성을 충분히 평가하지 않았습니다. 슬러지 형성 및 다이 솔더링에 대한 기존 문헌은 일관성이 부족하고, 특히 높은 냉각 속도와 같은 다이캐스팅 특정 조건의 영향에 대한 포괄적인 이해가 부족했습니다. 또한 다이캐스팅 조건을 정확하게 시뮬레이션하는 보편적으로 인정되는 표준화된 유동성 테스트가 부족했습니다.
*연구의 필요성:
향상된 특성을 위한 합금 설계와 다이캐스팅을 통한 제조 가능성 사이의 격차를 해소하기 위해 본 연구가 시작되었습니다. 새롭게 개발된 알루미늄 다이캐스팅 합금의 주조 특성을 조사하여 효과적이고 효율적으로 다이캐스팅될 수 있도록 하는 것이 필요합니다. 다이 솔더링 및 슬러지 형성 문제의 이해와 완화는 다이캐스팅 산업의 생산성 및 비용 효율성에 매우 중요합니다. 유동성 및 피삭성 평가는 부품 품질 및 제조 효율성을 보장하는 데에도 중요합니다.
3. 연구 목적 및 연구 질문:
*연구 목적:
본 연구 프로그램의 목적은 다음과 같습니다.
- 선정된 알루미늄 다이캐스팅 합금의 주조 특성 평가.
- 알루미늄 다이캐스팅 합금의 주조 특성에 영향을 미치는 주요 요인 식별.
본 프로젝트는 우수한 특성을 갖도록 설계된 5가지 실험용 알루미늄 다이캐스팅 합금과 상용 A380.0 합금의 다이 솔더링 경향, 슬러지 형성 경향, 유동성 및 피삭성을 조사하고 비교하는 것을 목표로 합니다.
*주요 연구 질문:
- 선정된 알루미늄 다이캐스팅 합금의 다이 솔더링 경향은 무엇이며, 합금 화학 조성에 의해 어떻게 영향을 받는가?
- 이러한 합금의 슬러지 형성 경향은 다양한 유지 온도 및 냉각 속도에서 어떠하며, 합금 화학 조성 및 공정 변수가 슬러지 특성에 어떻게 영향을 미치는가?
- 다이캐스팅 조건에서 이러한 합금의 유동성은 어떠하며, 합금 화학 조성이 다이 충전 능력에 어떻게 영향을 미치는가?
- 이러한 합금의 피삭성 특성은 어떠하며, 슬러지 형성과 관련된 잠재적인 피삭성 문제가 있는가?
*연구 가설:
본 연구는 암묵적으로 다음과 같은 가설을 설정합니다.
- 합금 화학 조성, 특히 Fe, Mn, Ni, Cr 및 Si 함량은 다이 솔더링 및 슬러지 형성 경향에 상당한 영향을 미친다.
- 용융 온도, 다이 온도 및 냉각 속도와 같은 공정 변수는 주조 특성에 중요한 역할을 한다.
- 슬러지 계수가 높은 합금은 슬러지 형성 경향이 더 클 것이다.
- 합금 화학 조성 및 공정 변수 조정을 통해 다이 솔더링 및 슬러지 형성 문제를 완화하고 주조 특성을 최적화할 수 있다.
4. 연구 방법론
*연구 설계:
본 연구는 6가지 알루미늄 합금(5가지 실험용 및 1가지 상용 A380.0)의 주조 특성을 평가하기 위해 실험적 설계를 채택합니다. 다이 솔더링 및 유동성을 위한 물리적 시뮬레이션 테스트와 슬러지 형성을 위한 제어된 냉각 실험을 포함합니다. 피삭성은 직접 테스트가 불가능했기 때문에 슬러지 형성 및 문헌 검토에 대한 이해를 기반으로 평가됩니다.
*데이터 수집 방법:
- 다이 솔더링 경향: 제어된 조건(온도, 회전 속도, 시간)에서 용융 합금에 H-13 핀을 담그는 물리적 시뮬레이션 장치를 사용했습니다. 핀의 금속간 화합물 층 두께를 다이 솔더링 경향의 지표로 측정했습니다.
- 유동성: SPX Corporation에서 구불구불한 공동 몰드에 다이캐스팅하여 충전 길이를 유동성 지표로 측정했습니다. 테스트는 0.5mm 다이 공동 두께에서 2400ips의 게이트 속도로 수행되었습니다.
- 슬러지 형성 경향: 합금을 670°C 및 720°C에서 3시간 동안 유지하고 다양한 냉각 속도에서 응고했습니다: 도가니에서 느린 냉각, 영구 몰드에서 중간 냉각, 구리 쐐기 몰드에서 빠른 냉각. 미세 구조 분석을 수행하여 슬러지를 특성화했습니다.
- 피삭성: 시편 준비의 어려움으로 인해 직접적인 실험적 측정 없이 슬러지 형성 경향 및 문헌 검토로부터 피삭성을 추론했습니다.
*분석 방법:
- 다이 솔더링: 현미경을 사용하여 금속간 화합물 층 두께 측정.
- 유동성: 다이 공동에서 충전 길이 측정. 유동 길이 데이터의 통계 분석.
- 슬러지 형성: 광학 현미경, 주사 전자 현미경(SEM) 및 에너지 분산형 X선 분광기(EDX)를 사용하여 슬러지 양, 크기, 형태, 분포 및 화학 조성을 특성화했습니다. 슬러지 입자의 미세 경도 테스트도 수행했습니다.
- 피삭성: 슬러지 특성 및 문헌을 기반으로 한 질적 평가.
*연구 대상 및 범위:
연구 대상은 6가지 알루미늄 다이캐스팅 합금입니다: 향상된 특성을 위해 설계된 5가지 실험용 합금(#1~#5)과 상용 A380.0 합금. 연구 범위는 다이 솔더링 경향, 슬러지 형성 경향, 유동성 및 피삭성 평가로 제한됩니다. 본 연구는 모의 다이캐스팅 조건에서 이러한 주조 특성에 대한 합금 화학 조성 및 공정 변수의 영향에 초점을 맞춥니다.
5. 주요 연구 결과:
*주요 연구 결과:
- 다이 솔더링: "합금의 철 함량이 솔더링에 가장 큰 영향을 미친다." 합금 #1(1.84% Fe)은 솔더링을 나타내지 않았습니다. "Mn은 솔더링에 유익한 효과가 있다." "Ni는 솔더링에 해롭다." "Ti의 부족 또는 부재는 솔더링에 불리하다." 낮은 Fe 및 Mn과 Ni가 존재하는 합금 #4는 A380.0 합금보다 더 나쁜 가장 높은 다이 솔더링 경향을 나타냈습니다.
- 유동성: "모든 합금에서 데이터 분산이 넓어 합금 화학 조성 이외의 요인이 다이 공동을 채우는 합금 능력에 중요한 역할을 한다는 것을 의미합니다." "합금 화학 조성 측면에서 Fe, Mn, Cr 및 Mg와 같이 고온 화합물을 형성하는 원소의 양이 많을수록 합금의 유동성은 낮아집니다." 합금 383은 가장 높은 평균 유동 길이를 보였지만, Si 및 Cu 함량이 더 높음에도 불구하고 합금 #1 및 #3은 Fe, Mn, Cr 및 Mg의 총 함량이 더 높아 유동성이 더 낮은 것으로 나타났습니다.
- 슬러지 형성: "슬러지 계수(SF)¹는 합금의 슬러지 형성 경향과 형성되는 슬러지 양을 결정하는 데 가장 중요합니다." 높은 SF를 가진 합금 #1 및 #3은 상당한 슬러지를 형성했습니다. "슬러지 입자의 형태는 합금의 Fe:Mn:Cr 비율에 의해 영향을 받습니다." "냉각 속도는 슬러지 형성에 중요한 역할을 합니다. 느린 냉각은 슬러지 형성을 촉진합니다." "슬러지는 670°C 또는 720°C에서 유지하는 동안 테스트된 합금에서 형성되지 않습니다." 빠른 냉각 다이캐스팅 조건에서는 슬러지가 형성되지 않지만, 도가니에서 느린 냉각 조건에서는 형성될 수 있습니다.
- 피삭성: "합금은 적절한 가공 기술과 가공 매개변수를 사용하면 가공 문제가 없어야 합니다." 피삭성은 대부분의 테스트된 합금에서 다이캐스팅의 슬러지 형성이 과도하지 않으므로 적절한 매개변수 조정을 통해 관리할 수 있는 것으로 추론됩니다.
*통계적/질적 분석 결과:
- 다이 솔더링: 금속간 화합물 층 두께 측정(표 4)은 다이 솔더링 경향을 정량화하여 합금 #4가 가장 높은 값(44.5 µm)을 나타내고 합금 #1이 0 µm를 나타냈습니다.
- 유동성: 유동 길이 측정(표 6)은 데이터 분산이 커서 합금 화학 조성 외의 요인이 유동성에 영향을 미친다는 것을 나타냅니다. 합금 #1, #3 및 383에 대한 평균 유동 길이 및 범위가 제공됩니다.
- 슬러지 형성: 슬러지 계수(SF) 계산(표 7)은 관찰된 슬러지 형성과 상관 관계가 있습니다. 미세 경도 측정(표 8)은 다양한 슬러지 상의 경도를 정량화했습니다. 현미경 사진(그림 7-20)은 다양한 조건에서 슬러지 형태 및 분포를 질적으로 보여줍니다.
*데이터 해석:
- 합금 #1의 높은 Fe 함량은 Fe 포화로 인해 다이 솔더링을 최소화했습니다. Mn은 유익한 효과를 보였고, Ni와 Ti 부족은 해로운 것으로 나타났습니다.
- 유동성 테스트 결과는 높은 데이터 분산으로 인해 합금 화학 조성 효과에 대한 결정적인 결론을 내리기 어려웠으며, 공정 변이가 지배적인 것으로 나타났습니다. 그러나 고온 화합물 형성 원소(Fe, Mn, Cr, Mg)의 함량이 높을수록 유동성이 감소하는 것으로 보입니다.
- 슬러지 계수는 다이캐스팅 냉각 속도에서 슬러지 형성 경향을 효과적으로 예측했습니다. SF가 높은 합금은 상당한 슬러지를 형성했습니다. 냉각 속도와 합금 화학 조성은 슬러지 형태와 양에 상당한 영향을 미쳤습니다. 슬러지 형성은 느린 냉각 조건에서 더 두드러집니다.
- 피삭성은 대부분의 합금에서 다이캐스팅의 슬러지 형성이 심각하지 않으므로 적절한 가공 매개변수를 통해 관리할 수 있을 것으로 예상됩니다.
*그림 목록:
- 그림 1. 슬러지 계수 대 온도 [14, 16].
- 그림 2. 다이 솔더링 시뮬레이션 장치.
- 그림 3. 핀 표면의 금속간 화합물 층.
- 그림 4. 핀 표면의 금속간 화합물 층.
- 그림 5. 합금 383의 유동성 테스트 결과, 다이 공동 두께 1mm.
- 그림 6. 연구된 합금에 대한 온도 대 슬러지 계수.
- 그림 7. 합금 #3에서 천천히 냉각된 1차 Si에 둘러싸인 Fe-rich 침상 및 다면체 입자. S-1차 Si, P-다면체, N-침상(또는 판상).
- 그림 8. 합금 #1의 미세 구조, 용융물을 670°C에서 3시간 동안 유지하고 구리 쐐기 몰드에 0.17인치 벽 두께로 주조. T-별 모양, N-침상(또는 판상), S-1차 Si.
- 그림 9. 합금 #2의 미세 구조, 용융물을 670°C에서 3시간 동안 유지하고 구리 쐐기 몰드에 0.17인치 벽 두께로 주조. C-중국 문자형.
- 그림 10. 합금 #3의 미세 구조, 용융물을 670°C에서 3시간 동안 유지하고 구리 쐐기 몰드에 0.17인치 벽 두께로 주조. T-별 모양, S-1차 Si.
- 그림 11. 합금 #4의 미세 구조, 용융물을 670°C에서 3시간 동안 유지하고 구리 쐐기 몰드에 0.17인치 벽 두께로 주조. N-침상(또는 판상).
- 그림 12. 합금 #5의 미세 구조, 용융물을 670°C에서 3시간 동안 유지하고 구리 쐐기 몰드에 0.17인치 벽 두께로 주조. C-중국 문자형.
- 그림 13. 합금 A380의 미세 구조, 용융물을 670°C에서 3시간 동안 유지하고 구리 쐐기 몰드에 0.17인치 벽 두께로 주조. B-블록형 입자.
- 그림 14. 합금 #2의 미세 구조, 용융물을 720°C에서 3시간 동안 유지하고 도가니에서 공랭 냉각. C-중국 문자형.
- 그림 15. 합금 #4의 미세 구조, 용융물을 720°C에서 3시간 동안 유지하고 도가니에서 공랭 냉각. P-다면체.
- 그림 16. 합금 A380의 미세 구조, 용융물을 720°C에서 3시간 동안 유지하고 도가니에서 공랭 냉각. C-중국 문자형, N-침상(또는 판상), P-다면체.
- 그림 17. 합금 #1의 미세 구조, 용융물을 670°C에서 3시간 동안 유지하고 도가니에서 공랭 냉각. S-1차 Si, N-침상(또는 판상), P-다면체.
- 그림 18. 합금 #3의 미세 구조, 용융물을 670°C에서 3시간 동안 유지하고 도가니에서 공랭 냉각. C-중국 문자형, B-블록형 입자.
- 그림 19. 합금 A380의 미세 구조, 용융물을 670°C에서 3시간 동안 유지하고 구리 쐐기 몰드에 0.36인치 벽 두께로 주조. T-별 모양, B-블록형 입자.
- 그림 20. 합금 A380의 미세 구조, 용융물을 720°C에서 3시간 동안 유지하고 구리 쐐기 몰드에 0.36인치 벽 두께로 주조. T-별 모양, B-블록형 입자.
![Figure1. Sludge factor versus temperature [14, 16].](https://castman.co.kr/wp-content/uploads/Figure1.-Sludge-factor-versus-temperature-14-16.webp)
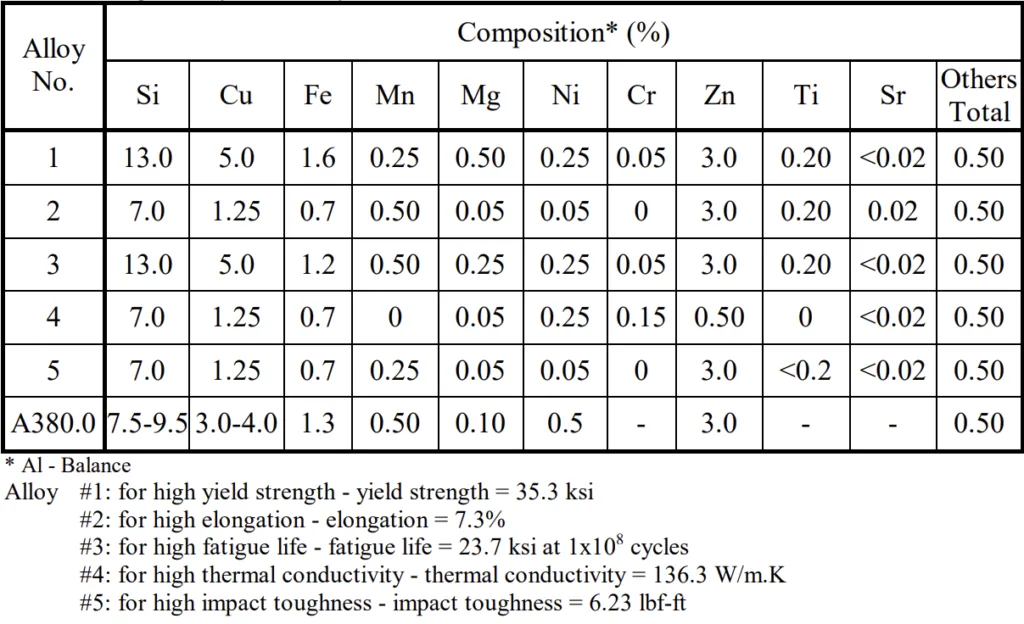
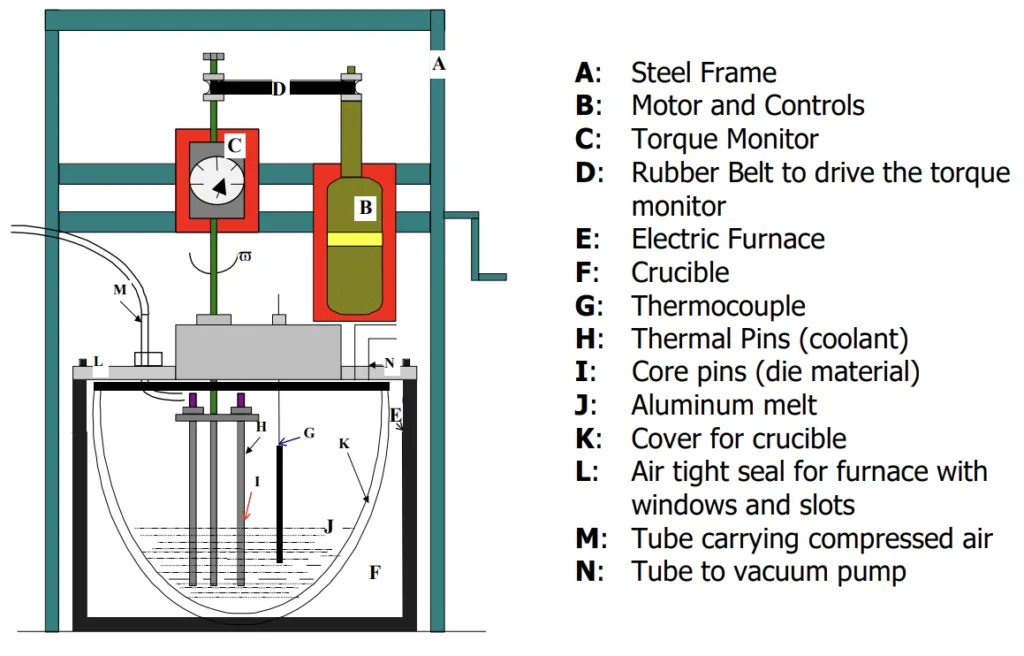
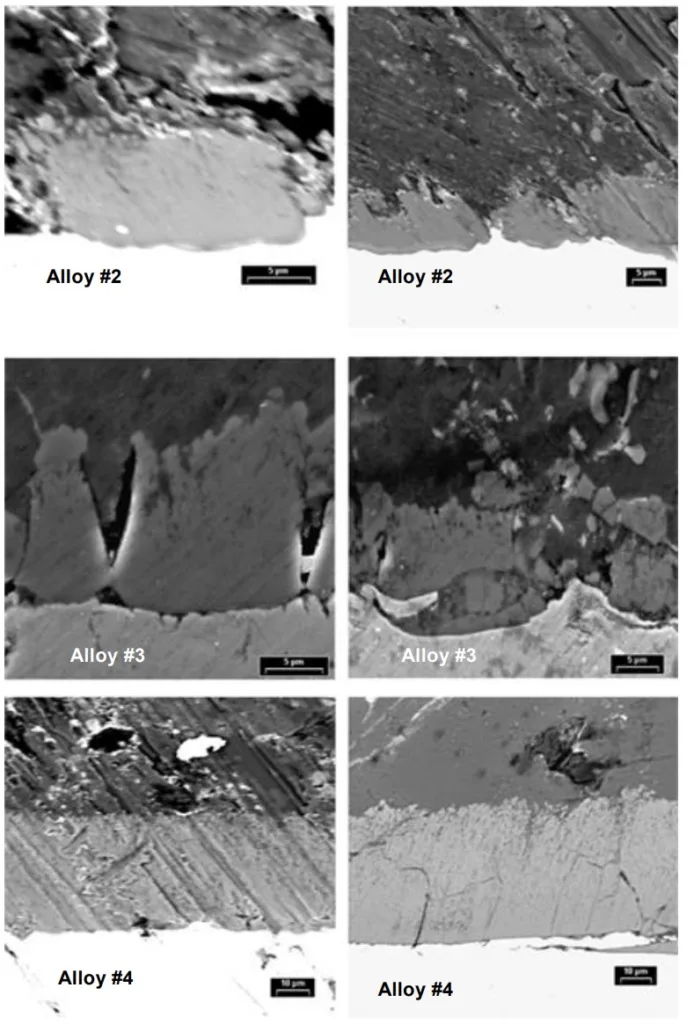
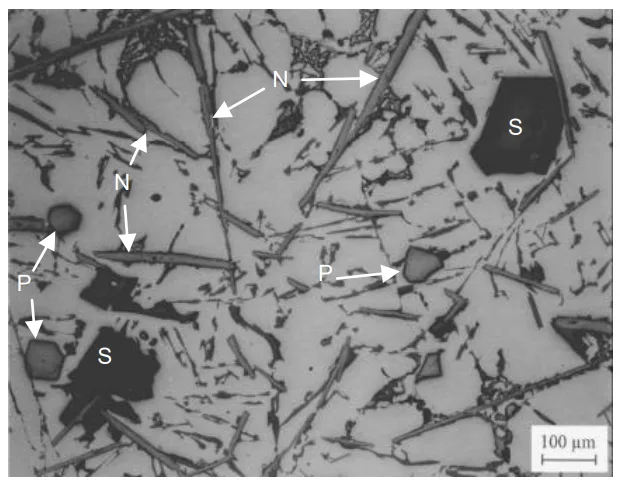
6. 결론 및 논의:
*주요 결과 요약:
본 연구는 향상된 기계적 특성을 위해 설계된 5가지 실험용 합금이 다이캐스팅 가능하다는 결론을 내렸습니다. 이들은 A380.0 합금과 비교하여 다이 솔더링, 슬러지 형성, 유동성 또는 피삭성 측면에서 주요 문제를 나타내지 않습니다. 구체적인 결과는 다음과 같습니다: Fe 함량은 다이 솔더링의 주요 요인이며, Mn은 유익한 효과가 있고, Ni는 해롭습니다. 슬러지 형성 경향은 슬러지 계수로 예측할 수 있으며, 합금 화학 조성 및 냉각 속도에 의해 영향을 받습니다. 유동성 데이터는 높은 가변성을 보여 공정 요인이 지배적임을 시사하지만, 고온 화합물 형성 원소(Fe, Mn, Cr, Mg)의 함량이 높을수록 유동성이 감소할 수 있습니다. 피삭성은 적절한 기술로 관리할 수 있을 것으로 예상됩니다.
*연구의 학문적 의의:
본 연구는 알루미늄 다이캐스팅 합금의 주조 특성, 특히 다이 솔더링 및 슬러지 형성에 대한 더 깊은 이해에 기여합니다. 다이캐스팅 조건에서 슬러지 경향을 예측하기 위한 슬러지 계수 개념의 실험적 검증을 제공합니다. 본 연구는 다이 솔더링에서 Fe, Mn, Ni, Cr 및 Ti의 역할과 슬러지 형태에 대한 냉각 속도의 영향을 명확히 합니다. 다이캐스팅에서 유동성 측정의 복잡성과 합금 화학 조성과 함께 공정 매개변수를 고려해야 할 필요성을 강조합니다.
*실용적 의미:
본 연구 결과는 알루미늄 다이캐스팅의 합금 설계 및 공정 최적화를 위한 실용적인 지침을 제공합니다.
- Fe 및 Mn 함량이 낮은 합금의 경우 다이 솔더링 문제에 주의해야 합니다. Mn 함량을 늘리고 Ni를 최소화하면 이를 완화할 수 있습니다. 예를 들어, 합금 #4의 경우 "합금 #4의 Mn 함량을 0.25 - 0.5%로 높이고 Ni 함량을 최소화해야 합니다."
- 슬러지 계수가 높은 합금, 특히 Fe가 높은 합금의 경우 하드스팟 형성을 방지하기 위해 "Fe 함량을 허용 가능한 최저 수준으로 유지하고 Mn 함량을 늘려야 합니다." 예를 들어, 합금 #1의 경우 "Fe를 1.6%로 줄이고 Mn을 0.5%로 늘릴 수 있습니다."
- 다이 충전 문제가 발생하면 합금 화학 조성을 변경하기 전에 공정 조정을 고려해야 합니다. 유동성을 개선하기 위해 합금 화학 조성에서 고온 화합물을 형성하는 원소를 최소화해야 합니다.
- 적절한 가공 기술과 매개변수는 이러한 합금에 매우 중요하며, 합금 유형 및 슬러지로 인한 잠재적인 하드스팟에 따라 조정이 필요할 수 있습니다.
*연구의 한계:
유동성 테스트는 데이터 분산이 커서 합금 화학 조성 효과에 대한 결정적인 결론을 내리기 어려웠습니다. 직접적인 피삭성 테스트는 수행되지 않았으며, 평가는 추론에 기반합니다. 본 연구는 제한된 합금 세트 및 공정 조건에 초점을 맞추었습니다. 슬러지 형성 연구는 유익하지만, 산업 다이캐스팅 작업의 복잡한 용융물 처리 및 냉각 조건을 완전히 재현하지 못할 수 있습니다.
7. 향후 후속 연구:
*후속 연구 방향:
- 다이캐스팅 합금에 대한 보다 강력한 유동성 측정 방법을 개발하기 위해 유동성 테스트에서 데이터 분산을 유발하는 요인에 대한 추가 조사.
- 피삭성 특성을 정량화하고 가공 매개변수를 최적화하기 위해 다양한 가공 조건에서 이러한 합금의 직접적인 피삭성 테스트.
- 산업 다이캐스팅 공정(용융물 이송 및 샷 슬리브 냉각 포함)을 보다 밀접하게 시뮬레이션하는 조건에서 슬러지 형성에 대한 합금 화학 조성, 유지 온도 및 냉각 속도 간의 상호 작용에 대한 보다 상세한 연구.
- 슬러지 입자가 다이캐스팅 부품의 기계적 특성 및 성능에 미치는 장기적인 영향 조사.
- 이러한 합금의 다이 솔더링을 완화하는 데 있어 다양한 다이 코팅 및 윤활제의 효과 탐색.
*추가 탐색이 필요한 영역:
- Mn과 Ti가 다이 솔더링 경향에 영향을 미치는 정확한 메커니즘.
- 다이캐스팅 조건에서 다양한 합금 시스템에서 슬러지 형성을 유발하는 임계 냉각 속도 및 유지 온도.
- 미량 합금 원소 및 불순물이 알루미늄 다이캐스팅 합금의 주조 특성에 미치는 영향.
- 합금 화학 조성 및 공정 매개변수를 기반으로 한 다이 솔더링, 슬러지 형성 및 유동성에 대한 예측 모델 개발.
8. 참고 문헌:
- 1 M. M. Makhlouf, D. Apelian, and L. Wang, Microstructure and Properties of Aluminum Die Casting Alloys, NADCA, 1999.
- 2 Y. L. Chu, P. S. Cheng, and R. Shivpuri, “Soldering Phenomenon in Aluminum Die Casting: Possible Causes and Cures”, NADCA Transactions, 1993, pp361-371.
- 3 Y. L. Chu, P. S. Cheng, and R. Shivpuri, “A Study of Erosive Wear in Die Casting Dies: Surface Treatments and Coatings”, NADCA Transactions, 1993, pp199-208.
- 4 R. Shivpuri, S. I. Chang, Y. I. Chu, M. Kuthirakulathu, “An Evaluation of H-13 Die Steel, Surface Treatments and Coatings for Wear in Die Casting Dies”, NADCA Transactions, 1991, p.391-397.
- 5 K. Venkatesan, R. Shivpuri, “An Investigation of the Effect of Process Parameters on the Washout in Die Casting Dies”, NADCA Transactions, 1995, pp361-371.
- 6 W. Kajoch and A. Fajkiel, “Testing the Soldering Tendencies of Aluminum Die Casting Alloys”, NADCA Transactions, 1991, pp67-74.
- 7E. K. Holz, “Trouble-Shooting Aluminum Die Casting Quality Problems” Transactions of 7th. SDCE International Die Casting Congress, 1972, Paper No. 4372.
- 8 S. Shankar and D. Apelian, “DIE SOLDERING: Mechanism Of The Interface Reaction Between Molten Aluminum Alloy And Tool Steel – Part I, Submitted to Met Trans.
- 9 S. Shankar and D. Apelian, “DIE SOLDERING: Mechanism Of The Interface Reaction Between Molten Aluminum Alloy And Tool Steel – Part II, Submitted to Met Trans.
- 10 M. Yu, Y. L. Chu, and R. Shivpuri, Ohio State University, Columbus, OH, unpublished research, 1997.
- 11 A. C. Paladino, “Die Lubricant Research Meets Die Casters' Needs”, Die Casting Engineers, May-June 1991, pp. 16-18.
- 12 H. G. Munson, T. H. Camel, “Development of a Semi-Permanent Release Coating for Die Casting”, NADCA Transactions, 1991, pp351-354.
- 13 P. N. Crepeau, B. L. Tiwari, and K. M. Rahmoeller, “ Characterization of Oxide Sludge, Dross and Inclusions in Aluminum Melting and Holding Furnaces”, Proc. Of the 3rd International Conference on Molten Aluminum Processing, Orlando, Fl, November 1992, pp 51-57.
- 14 J. L. Jarstad, "Understanding Sludge", Proc. Of the 14th SDCE International Die Casting Congress and Exposition, Toronto, Ont, Canada, May 11-14, 1987, Paper No. G-T87-011.
- 15 D. E. Groteke, “Elimination Hard Spots from Aluminum Die Castings”, Die Casting Engineer, Vol. 29, No. 5, Sept/Oct. 1985, pp 16-18, 20, 22, 24.
- 16 J. Gobrecht, “Gravity-Segregation of Iron, Manganese and Chromium in an Aluminum-Silicon Casting, Part I”, Giesserei, Vol. 61, No. 10, 1975, pp 263-265.
- 17 S. G. Shabestari, and J. E. Druzleski, “The Effecet of Solidification Condition and Chemistry on the Formation and Morphology of Complex Intermetallic Compounds in Aluminum-Silicon Alloys”, Cast Metals, Vol. 6, No. 4, 1994, pp 217-224.
- 18 A. Flores, J. C. Escobedo, M. Mendez, and J. Mendez, “Kinetics of the Formation, Growth and Sedimentation of the Al15(Fe, Mn)3Si2 Phase in Al-Si-Cu Alloys”, Trans. of International Die Casting Congress and Exposition, Drtroit, Michigan, USA, Sept. 30 – Oct. 3, 1991, pp 293-297.
- 19 M. R. Ghomashchi, “Intermetallic Compounds in an Al-Si Alloy Used in High Pressure Die-Casting”, Z Metallkunde, 78 (1987), 11, pp 784-787.
- 20 G. Gustafsson, T. Thorvaldsson, and G. L. Dunlop, “The Influence of Fe and Cr on the Microstructure of Cast Al-Si_Mg Alloys”, Met. Trans. A. 17A (1986), pp 45-52.
- 21 M. C. Flemings, “Solidification Processing", McGraw., London, 1974.
- 22 L. Arnberg, L. Backerud, and A. Dahle, “Castability of Aluminum Foundry Alloys”, An AFS Research Report, AFS, 1999, pp24-31.
- 23 J. Campbell, “Review of Fluidity Concepts in Casting”, Cast Metals, Vol. 7, No. 4, 1995, pp227-237.
- 24 M. Tiryakioglu, D. R. Askeland, and C. W. Ramsay, “Fluidity of 319 and A356: An Experimental Design Approach”, AFS Trans. Vol. 102, 1994, pp17-25.
- 25 M. C. Flemings, E. F. Niiyama, and H. F. Taylor, “Fluidity of Aluminum: An Experimental and Quantitative Evaluation”, AFS Trans. Vol. 69, 1961, pp625-635.
- 26 M. C. Flemings, F. R. Mollard, E. F. Niiyama, and H. F. Taylor, “Fluidity of Aluminum: Surface Tension, Vibration and Heat Losses in Runner Systems Effect”, AFS Trans. Vol. 70, 1962, pp1029-1039.
- 27 S. Floreen and D. V. Ragone, “The Fluidity of Some Aluminum Alloys”, AFS Trans. Vol. 65, 1957, pp391-393.
- 28 M. R. Sheshradri and A. Ramachandran, “Casting Fluidity and Fluidity of Aluminum and its Alloys”, AFS Trans. Vol. 73, 1965, pp292-304.
- 29 E. N. Pan and J. F. Hu, “Study on Fluidity of Al-Si Alloys”, AFS Trans. Vol. 105, 1997, pp413-418.
- 30 G. W. P. Rengstorff and T. R. Baruch, “Surface Energy Effect on Flow of Molten Metal in Thin Section”, AFS Trans. Vol. 70, 1962, pp920-923.
- 31 P. Bastien, J. C. Armbruster, and P. Azou, “Flowability and Viscosity”, AFS Trans. Vol. 70, 1962, pp400-409.
- 32 J. L. Jorstad, “Machinability of 380 Alloy: Effect of Minor Elements and Impurities", 10th SDCE International Die Casting Exposition & Congress, March 19-22, 1979, St. Louis, Missouri, Paper No. G-T79-072.
- 33 J. L. Jorstad, “Influence of Aluminum Casting Alloy Metallurgical Factor on Machinability", Modern Casting, December 1980, pp47-51.
- 34 R. C. Lemon, “Metallurgical Factor Related to Machining Aluminum Castings”, SAE Congress and Exposition, January 1967, Paper No. 607465.
- 35 D. L. Colwell, “Zinc in Aluminum Casting Alloys”, AFS Trans. Vol. 60, 1952, pp517-524.
- 36 R. C. Lemon, “Free Machining Aluminum Casting Alloys X310 and X335”, AFS Trans. Vol. 71, 1963, pp315-318.
- 37 C. A. Queener and W. L. Witchell, “Effect of Iron Content and Sodium Modification on the Machinability of Aluminum Alloy Die Castings”, AFS Trans. Vol. 73, 1965, pp14-19.
- 38 J. M. Fox, “Aluminum Alloy Casting Inclusions”, AFS Trans. Vol. 69, 1961, pp737-742.
- 39 G. L. Armstrong, “Metallurgical Defects Encountered in Machining Aluminum Die Castings", Trans. of the Society of Die Casting Engineers, March 1975, Paper No. G-T75-011.
9. 저작권:
*본 자료는 마클루프 M. 마클루프 (Makhlouf M. Makhlouf)와 디란 아펠리안 (Diran Apelian)의 논문: "알루미늄 다이캐스팅 합금의 주조 특성 (Casting Characteristics of Aluminum Die Casting Alloys)"을 기반으로 작성되었습니다.
*논문 출처: (DOI URL은 문서에 제공되지 않았습니다. )
본 자료는 상기 논문을 기반으로 요약되었으며, 상업적 목적으로 무단 사용하는 것을 금지합니다.
Copyright © 2025 CASTMAN. All rights reserved.