본 소개 자료는 [NADCA]에서 발행한 ["알루미늄 고압 다이캐스팅에서 공정 변수와 품질 특성 간의 상관관계"] 논문의 연구 내용입니다.
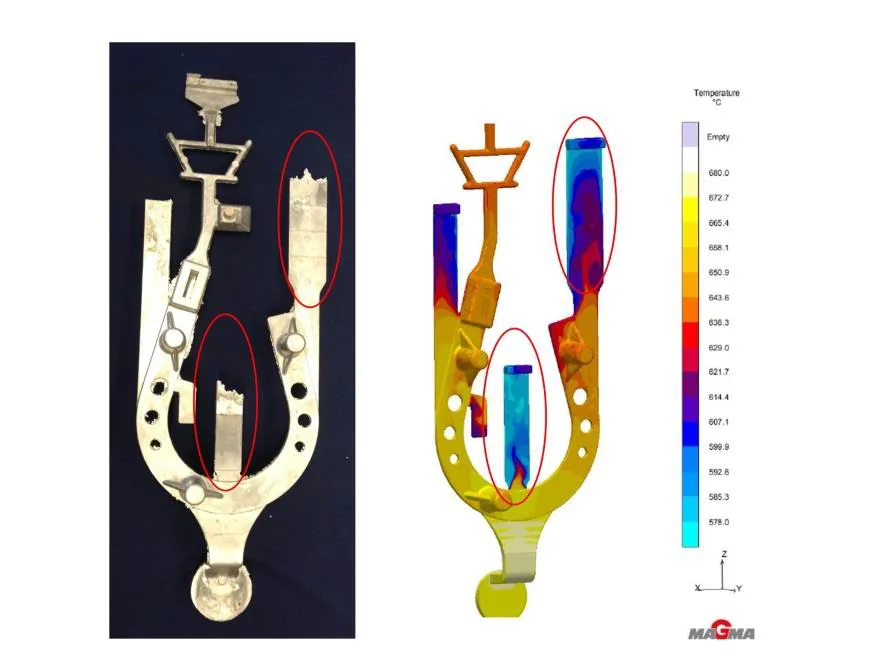
1. 개요:
- 제목: 알루미늄 고압 다이캐스팅에서 공정 변수와 품질 특성 간의 상관관계 (Correlation between process parameters and quality characteristics in aluminum high pressure die casting)
- 저자: M. Winkler, L. Kallien, T. Feyertag
- 출판 연도: 2015
- 발표 저널/학회: DIE CASTING CONGRESS & EXPOSITION, NORTH AMERICAN DIE CASTING ASSOCIATION
- 키워드: (논문에 명시적인 키워드가 없으므로, 제공된 문서 기반으로 이 섹션을 채울 수 없습니다.)
2. 초록
알루미늄 고압 다이캐스팅은 가장 생산적인 제조 공정 중 하나입니다. 부품의 복잡성이 증가하고 품질 요구 사항이 높아지고 있습니다. 고압 다이캐스팅의 과제는 수많은 품질 영향 공정 변수에도 불구하고 높은 품질 표준을 달성하는 것입니다. 모든 품질 영향 변수의 상호 작용은 최대 10-25%의 매우 높은 불량률로 이어집니다. 이러한 매개변수는 다이캐스팅 머신, 용광로, 온도 조절 시스템 등과 같은 공정의 다양한 시스템에 의해 중앙에서 모니터링되지 않습니다. 현재 공정에서 측정되는 일반적인 매개변수는 1단계 및 2단계의 피스톤 속도, 강화 압력 등입니다. 그러나 배기 공기의 습도와 같이 부품 품질을 제어하는 많은 매개변수가 있습니다.
유럽 연구 프로젝트 MUSIC(MUlti-layers control and cognitive System to drive metal and plastic production line for Injected Components)은 모든 품질 관리 매개변수를 고려하는 지능형 인지 시스템을 개발하여 고압 다이캐스팅의 불량률을 줄이는 것을 목표로 합니다. 이 프로젝트의 프레임워크에서는 수축 다공성, 콜드 셧 및 왜곡과 같은 여러 결함이 있는 부품 생산을 허용하는 특수 주조 형상이 개발되었습니다. 다이에는 샷 소리와 같이 현재까지 적용되지 않은 새로운 공정 매개변수를 모니터링하기 위해 많은 새롭고 혁신적인 센서가 장착되어 있습니다. 센서 데이터, 기계 및 주변 장치의 공정 매개변수는 주물의 품질 지수와 함께 하나의 공통 데이터베이스에 저장됩니다. 그러면 인지 네트워크는 측정된 센서 데이터를 기반으로 미래 부품의 품질 지수를 계산할 수 있습니다.
3. 연구 배경:
연구 주제 배경:
혁신적인 자동차 차체 구조에서 고압 다이캐스팅 부품의 수가 증가하고 있습니다. 구조 요소로 알루미늄 부품을 적용하는 이유는 중량 감소입니다.
선행 연구 현황:
고압 다이캐스팅(HPDC)은 우수한 표면 품질, 높은 치수 정확도 및 높은 인장 강도를 가진 부품을 생산하는 생산적인 제조 방법입니다. 그러나 많은 매개변수가 부품 품질에 영향을 미칩니다. 기존 데이터 수집(그림 2)에는 피스톤 속도, 전환점, 강화 압력, 가열 오일 온도, 용광로 온도 및 분사 장치 매개변수와 같은 매개변수가 포함됩니다. 이들은 일반적으로 개별 장치에 의해 제어되고 측정됩니다. 다른 영향 매개변수(예: 습도, 배기 공기량, 플런저 가속도, 합금 조성 변화)는 일반적으로 측정되거나 저장되지 않습니다.
연구 필요성:
모든 품질 영향 변수 간의 상호 작용으로 인해 10-25%까지 높은 불량률이 발생합니다. 이 값은 다른 제조 공정의 불량률보다 10배 또는 1000배 초과합니다.
4. 연구 목적 및 연구 질문:
연구 목적:
유럽 연구 프로젝트 MUSIC (MUlti-layers control and cognitive System to drive metal and plastic production line for Injected Components)은 고압 다이 캐스팅에서 불량률을 줄이는 것을 목표로합니다.
핵심 연구:
모든 품질 관리 매개 변수를 고려한 지능형 인식 시스템을 개발하여 불량률을 줄입니다.
5. 연구 방법론
이 연구는 센서 네트워크와 인지 시스템을 활용합니다(그림 3). 고압 다이캐스팅 기계 및 주변 장치에는 센서가 장착되어 있습니다. 모든 장치는 하나의 공통 데이터베이스에 연결된 네트워크에 연결됩니다. 이 데이터베이스에는 모든 센서 데이터와 기계 및 주변 장치의 제어된 공정 매개변수가 저장됩니다.
결함(수축 다공성, 콜드 셧, 왜곡)을 의도적으로 생성하기 위해 특수 주조 형상(그림 4)이 설계되었습니다. 다이에는 다양한 공정 매개변수를 모니터링하기 위한 센서가 장착되어 있습니다.
주조 부품의 최종 설계를 검증하기 위해 MAGMA를 사용하여 충진 및 응고 시뮬레이션을 수행했습니다.
인지 모델의 훈련은 주조 결함을 예측하기 위한 초기 단계입니다. 이를 위한 അടിസ്ഥാന은 공정 및 품질 데이터의 가용성입니다. 데이터는 실험 계획법(DoE) 중에 수집됩니다.
모든 주물의 동일한 기준을 분석하기 위해 품질 관리 절차가 정의되었습니다.
6. 주요 연구 결과:
주요 연구 결과 및 제시된 데이터 분석:
- 다양한 캐비티 압력 신호의 비교가 그림 8에 나와 있습니다.
- 진공 시스템과 결합된 공기 질량 센서 신호가 제공됩니다. 그림 10은 일반적인 샷을 보여주고, 그림 11은 진공 채널에 누출이 있는 샷을 보여줍니다.
- 길고 짧은 분사 주기 후의 습도 센서 신호가 그림 12에 나와 있습니다.
- 매개변수, 센서 데이터 및 품질 결과 간의 종속성을 보여주기 위해 상관 행렬(표 1)이 생성되었습니다.
- Design-Expert® 소프트웨어에서 품질 지수, 온도 및 피스톤 속도 간의 상호 작용을 보여주는 3D 다이어그램의 예가 그림 13에 나와 있습니다.
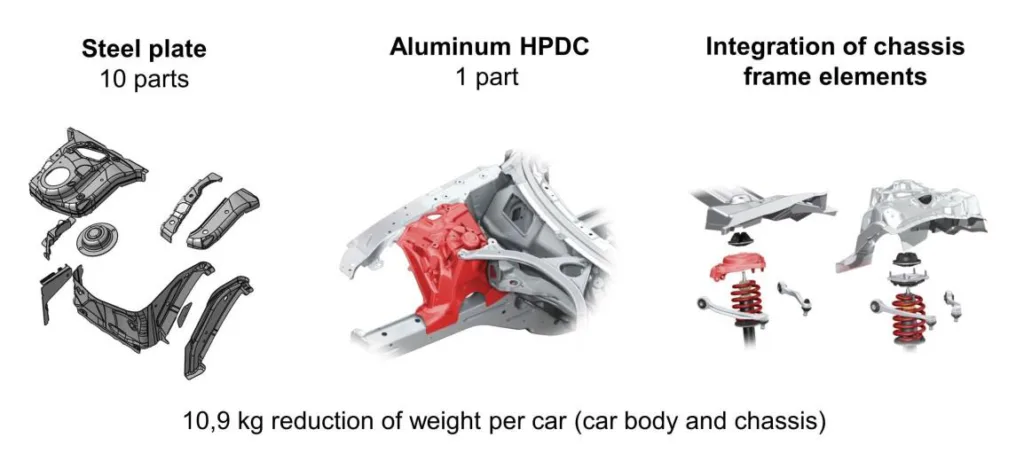
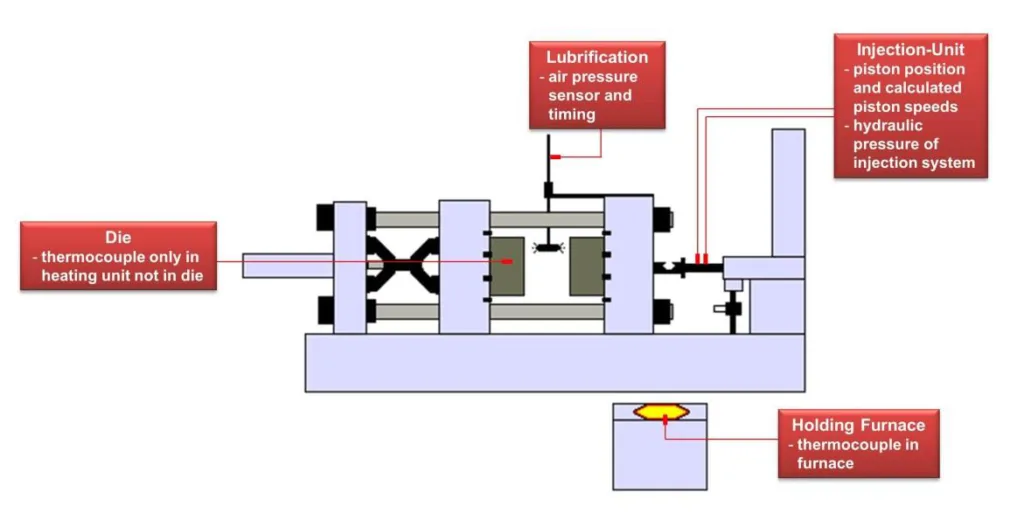

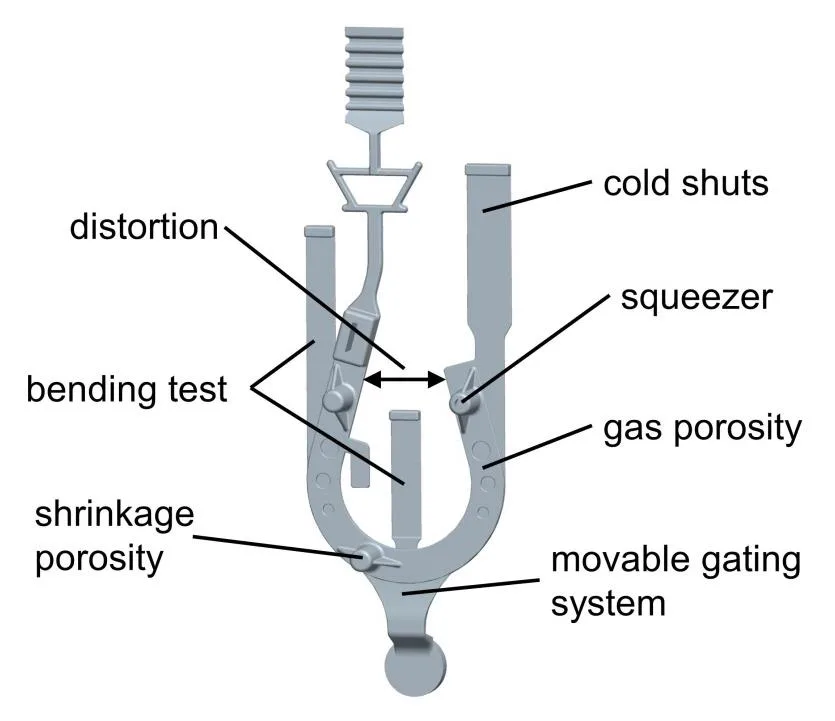
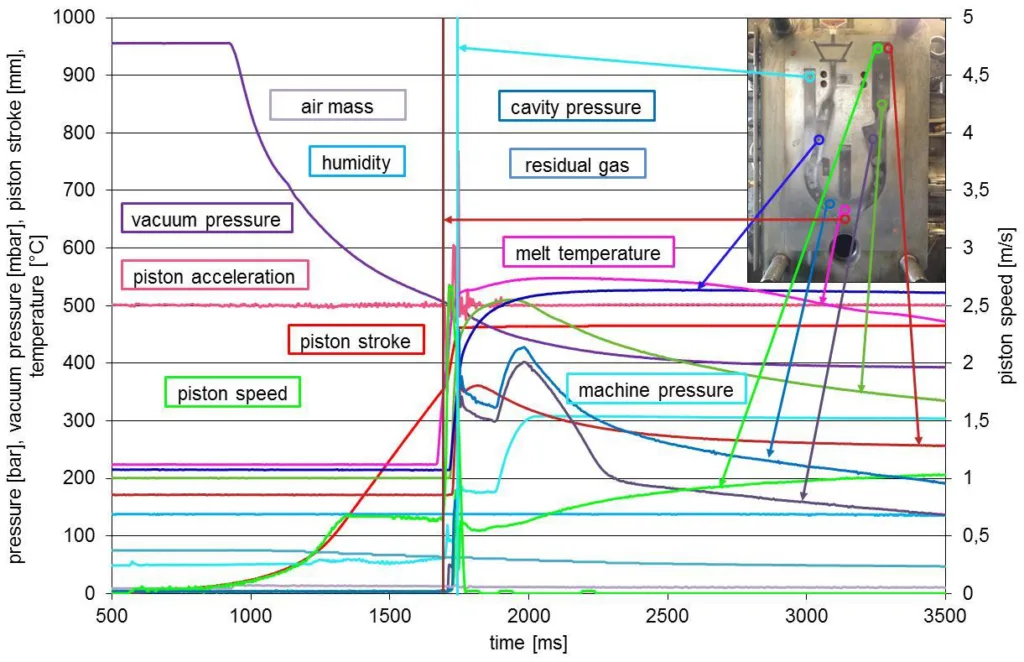
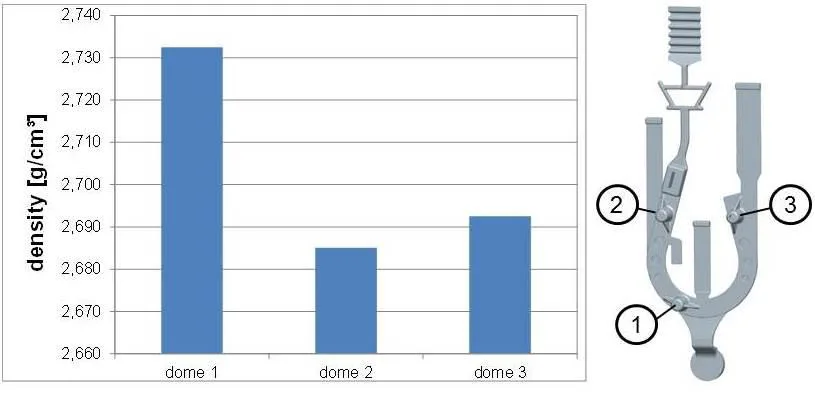
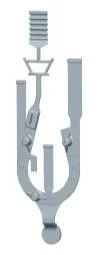
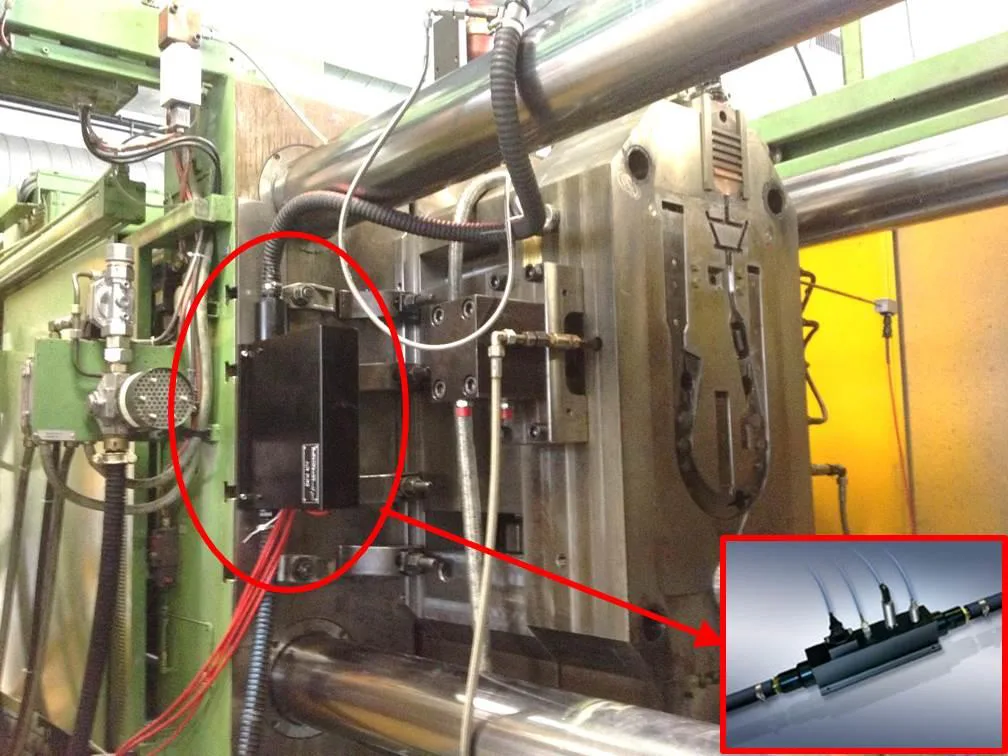
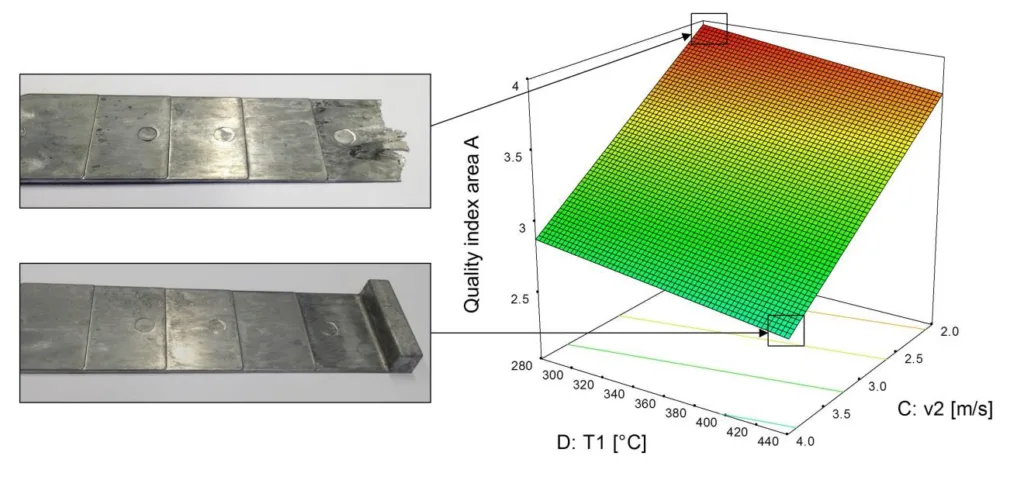
그림 이름 목록:
- 그림 1: 접합된 강철 부품 대신 구조용 알루미늄 고압 다이캐스팅 부품을 사용하여 중량 감소 [1]
- 그림 2: HPDC 공정 중 기존 데이터 수집
- 그림 3: 혁신적인 센서 네트워크 및 인지 시스템
- 그림 4: 결함을 생성하기 위한 특수 주조 형상
- 그림 5: 실제 주조 부품과 콜드 셧 관련 시뮬레이션 결과 비교 [2]
- 그림 6: 추가 센서 신호가 있는 샷 곡선
- 그림 7: 돔 영역 밀도 비교
- 그림 8: 강화 압력(센서 신호의 주황색) 및 강화 압력 없음(센서 신호의 녹색)이 있는 캐비티 압력 센서 신호가 있는 샷 곡선
- 그림 9: Aalen의 파운드리 연구실의 750t 냉각 챔버 기계에 조립된 다중 공기 파이프 센서 시스템 [4]
- 그림 10: 진공 채널에 누출이 없는 진공 및 공기 질량 신호가 있는 샷 곡선
- 그림 11: 진공 채널에 누출이 있는 진공 및 공기 질량 신호가 있는 샷 곡선
- 그림 12: 길고(파란색) 짧은(노란색) 분사 주기 후에 측정된 진공 및 습도 센서 신호가 있는 샷 곡선
- 그림 13: 영역 'A'의 품질 지수, 2단계 피스톤 속도 및 온도 센서 신호 T1 간의 상호 관계
7. 결론:
주요 결과 요약:
캐비티 압력 센서는 주조의 বিভিন্ন 영역에서 압력을 모니터링합니다. 이들은 공급 효율성에 대한 정보를 제공하고 특히 주조 부품의 두꺼운 영역에서 밀도를 예측하는 데 도움이 됩니다.
공기 질량 센서를 사용하면 배기되는 공기의 양을 측정하고 진공 채널의 누출을 감지할 수 있습니다. 불량한 배기로 인해 갇힌 공기와 관련하여 주조 부품의 밀도를 예측하는 데 도움이 됩니다.
습도 센서를 사용하면 다이에 남아 있는 습도를 최소화하여 분사 주기를 개선할 수 있습니다.
상관 관계는 인지 모델을 훈련하고 품질 검사 없이 주조 부품의 품질을 예측하는 데 도움이 됩니다. 이는 품질 관리 노력을 줄이고 불량률을 줄일 수 있는 좋은 기회입니다.
OPC-UA를 통한 모든 장치 연결은 데이터 수집뿐만 아니라 HPDC 기계 및 주변 장치의 제어에 입력 변수를 보낼 수 있습니다. 즉, 시스템은 정의된 임계값 내에서 특정 품질 영향 매개변수를 조정하여 프로세스를 최적화할 수 있습니다.
8. 참고 문헌:
- [1] Wanke, P., Innovative Strukturgusskonzepte bei AUDI, AUDI AG, Gießereikolloquium Hochschule Aalen, (2012년 5월 9일)
- [2] Kallien, L., Winkler, M., Kognitives System zur Reduzierung der Ausschussrate im Druckguss, Horizonte, (2015년 4월/5월)
- [3] Bonollo, F., Gramegna, N., et al., The MUSIC guide to key-parameters in High Pressure Die Casting, MUSIC Consortium (2014)
- [4] http://www.electronics-gmbh.de/electronics/english/produkt_multisensor.htm
9. 저작권:
- 이 자료는 "[M. Winkler, L. Kallien, T. Feyertag]"의 "[알루미늄 고압 다이캐스팅에서 공정 변수와 품질 특성 간의 상관관계]" 논문을 기반으로 합니다.
- 논문 출처: [원래 문서에 DOI URL이 없습니다.]
본 자료는 위 논문을 소개하기 위해 작성되었으며, 상업적 목적으로 무단 사용하는 것을 금합니다. Copyright © 2025 CASTMAN. All rights reserved.