이 기술 브리핑은 Trio Yonathan Teja Kusuma, Gunawan Budi Susilo, M Zulhan Iswanda가 REKAYASA, Journal of Science and Technology (2023)에 발표한 학술 논문 "Pengendalian Kualitas Produk Downlight dengan Implementasi Simulasi Die Casting"을 기반으로 합니다. HPDC 전문가를 위해 CASTMAN의 전문가들이 요약하고 분석했습니다.
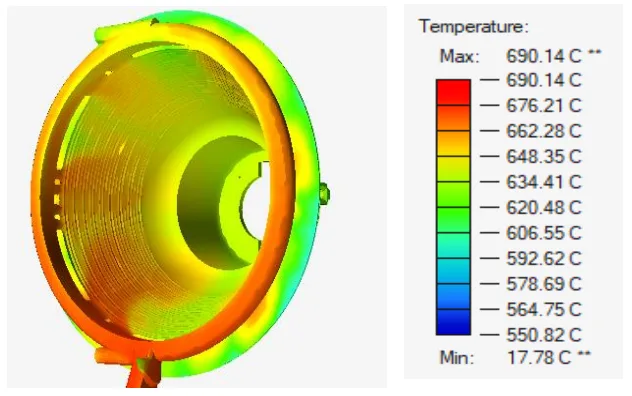
키워드
- 주요 키워드: 품질 관리를 위한 다이캐스팅 시뮬레이션
- 보조 키워드: HPDC 결함, 콜드 샷 결함, Inspire Cast 시뮬레이션, ADC12 알루미늄 주조, 주조 공정 최적화, 미세 기공 분석, 주조 시뮬레이션
핵심 요약
- 과제: ADC12 알루미늄 다운라이트 제품의 고압 다이캐스팅 공정에서 심각한 품질 문제가 발생했으며, 콜드 샷 결함이 전체 불량 부품의 52%를 차지하여 막대한 비용 낭비와 생산 지연을 초래했습니다.
- 방법: 연구원들은 Inspire Cast 시뮬레이션 소프트웨어를 사용하여 기존 사출 공정을 시각화하고 결함의 근본 원인을 파악한 후, 물리적 시험에 착수하기 전에 수학적으로 도출된 두 가지 새로운 공정 구성을 모델링했습니다.
- 핵심 돌파구: 시뮬레이션을 통해 콜드 샷 결함이 재결정 온도 이하에서 용탕 흐름이 만나면서 발생한다는 것을 시각적으로 확인했습니다. 최적화된 구성은 더 균일한 온도 프로파일을 보여주었고, 이는 결함 및 미세 기공 감소로 이어질 것으로 예측되었습니다.
- 결론: 다이캐스팅 시뮬레이션에 대한 투자는 물리적 시행착오와 관련된 비용과 시간을 대폭 줄여 가상 환경에서 공정 개선을 검증할 수 있게 함으로써 명확하고 신속한 투자 수익을 제공합니다.
과제: 이 연구가 HPDC 전문가에게 중요한 이유
고압 다이캐스팅에서 무결점 생산을 달성하는 것은 끊임없는 과제입니다. 콜드 샷, 수축, 기공, 균열과 같은 결함은 상당한 재정적 손실을 초래하고 제품 무결성을 손상시킬 수 있는 일반적인 장애물입니다. 이러한 문제는 종종 최적이 아닌 공정 변수나 금형 설계에서 비롯됩니다.
이 연구는 ADC12 알루미늄으로 다운라이트 부품(모델 NN511)을 생산하는 제조업체가 직면한 시급하고 실제적인 문제를 다룹니다. 해당 공정은 높은 불량률로 어려움을 겪었으며, 특히 콜드 샷이 전체 문제의 52%를 차지하는 가장 빈번한 원인이었습니다. 이는 업계의 많은 사람들에게 익숙한 시나리오입니다. 즉, 안정적인 공정 창을 찾기 위해 많은 비용과 시간이 소요되는 시행착오 접근법은 귀중한 시간과 자재를 소모합니다. 이 연구는 더 과학적이고 비용 효율적인 길을 제시합니다.
접근법: 방법론 분석
이 과제를 해결하기 위해 연구원들은 공정 시뮬레이션에 주목했습니다. 이 연구는 강력한 시뮬레이션 소프트웨어인 Inspire Cast를 사용하여 다이캐스팅 공정을 분석하고 최적화하는 데 중점을 두었습니다.
방법론은 다음과 같은 몇 가지 주요 단계로 구성되었습니다:
- 기준선 분석: 팀은 먼저 샷 슬리브, 러너, 게이트 및 오버플로를 포함한 기존 금형의 3D CAD 모델을 만들었습니다. 이 모델을 Inspire Cast로 가져와 현재 문제가 있는 생산 공정의 시뮬레이션을 실행했습니다.
- 파라미터 계산: 임계 저속 샷 속도(Vcss)와 플런저의 1차 및 2차 단계 이동 거리를 포함한 새롭고 최적화된 사출 파라미터를 계산했습니다.
- 가상 테스트: 이러한 계산을 기반으로 "대안 1(Alternatif 1)"과 "대안 2(Alternatif 2)"라는 두 가지 새로운 구성을 개발했습니다. 그런 다음 이 대안 설정을 Inspire Cast에서 시뮬레이션하여 기계에 물리적 변경을 가하기 전에 금형 충전, 온도 분포 및 잠재적 미세 기공에 미치는 영향을 예측했습니다.
이러한 "시뮬레이션 우선" 접근법을 통해 연구원들은 새로운 공정 파라미터를 가상으로 검증하고 성능이 저조한 원래 설정과 직접 비교할 수 있었습니다.
핵심 돌파구: 주요 결과 및 데이터
시뮬레이션 결과는 결함의 원인과 제안된 해결책의 효과에 대한 명확하고 실행 가능한 통찰력을 제공했습니다.
- 결과 1: 근본 원인 파악: 기존 구성의 시뮬레이션(그림 1)은 금형 충전 중 온도 분포를 명확하게 시각화했습니다. 이는 다른 게이트에서 나온 용탕 흐름이 합금의 재결정 온도(<653°C) 이하에서 만나고 있음을 보여주었으며, 이는 콜드 샷 결함 형성의 전형적인 원인입니다.
- 결과 2: 더 나은 공정 검증: "파라미터 대안 1"에 대한 시뮬레이션은 상당한 개선을 보여주었습니다. 용융 알루미늄의 중요한 합류 지점에서의 온도가 더 균일하고 재결정 온도 이상으로 유지되어 더 나은 융합을 이끌었습니다(그림 2). 결과적으로 예측된 미세 기공은 제품 부피의 1.35% - 1.8% 범위로 감소했습니다(그림 3).
- 결과 3: 명확한 ROI 입증: 이 연구는 시뮬레이션에 대한 강력한 재정적 근거를 제공합니다. 논문에 따르면 최상의 구성을 찾기 위한 물리적 시험은 29%의 불량률과 상당한 비용을 초래했습니다. 반면, 단 두 번의 물리적 시험 대안만 포함된 시뮬레이션 주도 접근법은 초기 시험 비용의 일부(초기 시험 Rp 708,000 대비 Rp 240,000)로 더 낮은 22%의 불량률을 기록했습니다. 이는 비싸고 시간 소모적인 현장 실험을 줄이는 데 있어 시뮬레이션의 힘을 강조합니다.
귀사의 HPDC 제품에 대한 실질적 시사점
이 연구의 결과는 실제 제조 공정을 향상시키는 데 직접 적용할 수 있는 귀중한 교훈을 제공합니다.
- 공정 엔지니어에게: "데이터 처리(Pengolahan Data)" 섹션에 자세히 설명된 연구는 다단계 사출 프로파일을 계산하고 구현하기 위한 명확한 프레임워크를 제공합니다. 1단계(저속 샷) 속도와 이동 거리를 최적화함으로써 샷 슬리브 내의 공기 혼입을 효과적으로 최소화할 수 있습니다. 시뮬레이션 결과는 계산에 기반하여 이러한 파라미터를 조정하면 난류와 조기 냉각으로 인한 결함을 직접적으로 줄일 수 있음을 시사합니다.
- 품질 관리팀에게: 시뮬레이션된 온도 프로파일(그림 1, 2, 4)과 콜드 샷 결함의 물리적 위치 사이의 강력한 상관관계는 강력한 예측 품질 도구를 제공합니다. 시뮬레이션을 사용하여 금형 설계의 "핫스팟" 또는 이 경우 "콜드스팟"을 식별하여 첫 번째 부품을 주조하기 전에 선제적으로 조정할 수 있습니다.
- 금형 설계팀에게: 이 연구는 사출 파라미터와 금형 설계가 본질적으로 어떻게 연결되어 있는지를 강조합니다. 연구는 사출 공정 최적화에 중점을 두었지만, 시뮬레이션 결과(2단계 분석)는 흐름이 러너 및 게이트 설계에 의해 어떻게 결정되는지를 명확하게 보여줍니다. 이는 금형 설계 초기 단계에서 시뮬레이션을 사용하는 것이 적절한 충전을 보장하고, 압력 요구 사항을 최소화하며, 게이트와 오버플로를 최대 효과를 위해 배치하는 데 중요하다는 것을 의미하며, 이는 논문의 전반적인 결과에 의해 뒷받침되는 결론입니다.
논문 상세 정보
Pengendalian Kualitas Produk Downlight dengan Implementasi Simulasi Die Casting
1. 개요:
- 제목: Pengendalian Kualitas Produk Downlight dengan Implementasi Simulasi Die Casting (다이캐스팅 시뮬레이션 구현을 통한 다운라이트 제품의 품질 관리)
- 저자: Trio Yonathan Teja Kusuma, Gunawan Budi Susilo, M Zulhan Iswanda
- 발행 연도: 2023
- 저널/학회: REKAYASA, Journal of Science and Technology
- 키워드: 다이캐스팅, 주조 결함, 주조 시뮬레이션
2. 초록:
다이캐스팅은 공압/유압 에너지로 구동되는 피스톤을 사용하여 용융된 금속을 금형에 사출하여 붓는 주조 공정입니다. 경우에 따라 구성이 정확하지 않으면 결함이 발생하여 결과물이 원하는 설계와 일치하지 않을 수 있습니다. 다이캐스팅 공정에서는 콜드 샷, 수축, 기포, 뒤틀림, 언더컷 등 여러 결함이 흔히 발생합니다. 컴퓨터의 도움으로 이러한 문제를 줄일 수 있을 것으로 기대됩니다. Inspire Cast를 사용하여 사출 공정을 시각화하면 다이캐스팅 공정 분석이 용이해집니다. 이 소프트웨어의 도움으로 더 나은 구성을 만들어 기계에 구현할 수 있습니다. 그러나 결과는 다릅니다. 소프트웨어 시뮬레이션에서는 다른 게이트에서 나오는 용탕 흐름이 재결정 온도인 665°C 이상이므로 두 용탕 흐름이 만날 때 더 잘 경화되고 융합되어야 한다고 합니다. 그러나 새로운 구성을 기계에 구현한 후에도 공정 결함은 기존 구성의 6%에 비해 구성 1의 경우 23%, 구성 2의 경우 13%로 여전히 높았습니다. 그럼에도 불구하고 이 소프트웨어를 구현하면 새로운 재료에 대한 새로운 구성을 찾기 위한 시행착오 과정의 비용을 줄일 수 있습니다.
3. 서론:
이 논문은 다이캐스팅을 다양한 금속 제품을 생산하는 주요 제조 공정으로 확립하는 것으로 시작합니다. 업계의 주요 과제는 콜드 샷, 수축, 블로우홀, 기공과 같은 결함이 빈번하게 발생한다는 점을 강조합니다. 이러한 결함은 종종 부적절한 금형 설계나 잘못된 사출 공정 구성으로 인해 발생합니다. 서론은 고압 다이캐스팅의 복잡한 유체 역학을 시각화하고 분석하기 위한 현대적인 해결책으로 컴퓨터 시뮬레이션을 제시하며, 이를 통해 엔지니어들이 이러한 일반적인 문제를 완화할 수 있도록 하는 연구의 배경을 설정합니다.
4. 연구 요약:
연구 주제의 배경:
이 연구는 ADC12 알루미늄으로 제작된 다운라이트 제품(NN511) 생산에서 지속적인 품질 문제를 해결하기 위해 시작되었습니다. 기존 제조 공정은 높은 불량률을 초래했으며, 특히 콜드 샷이 전체 결함의 52%로 가장 중요한 문제였습니다.
이전 연구 현황:
이 논문은 콜드 샷(금속 흐름의 불완전한 융합) 및 기공(공기 혼입)과 같은 결함의 원인을 확립한 이전 연구를 인정합니다. 이 연구는 더 나은 기계 구성을 찾고 시행착오 비용을 줄이기 위해 특정하고 실용적인 산업 문제에 기존 시뮬레이션 기술(Inspire Cast)을 적용하는 것으로 자리매김합니다.
연구 목적:
주요 목표는 다이캐스팅 시뮬레이션을 사용하여 기존 공정을 분석하고, 높은 불량률의 근본 원인을 이해하며, 제품 품질을 개선하고 제조 비용을 절감하기 위해 새롭고 최적화된 사출 구성을 개발하고 테스트하는 것이었습니다.
핵심 연구:
연구의 핵심은 비교 분석이었습니다. 첫째, 기준선을 만들고 알려진 결함에 대해 시뮬레이션을 검증하기 위해 기존 공장 구성을 시뮬레이션했습니다. 둘째, 새로운 공정 파라미터를 계산하고 두 가지 대안 구성을 설계했습니다. 그런 다음 이 대안들을 Inspire Cast에서 시뮬레이션하여 용탕의 온도 흐름과 결과적인 미세 기공에 중점을 두어 분석했습니다. 시뮬레이션 결과는 가장 효과적인 구성을 결정하기 위해 기준선과 비교되었습니다.
5. 연구 방법론
연구 설계:
이 연구는 사전-사후 테스트 프레임워크를 사용하는 사례 연구로 설계되었습니다. "사전 테스트"는 기존의 결함 있는 생산 설정에 대한 분석이었고, "사후 테스트"는 두 가지 새롭고 최적화된 구성에 대한 분석이었습니다.
데이터 수집 및 분석 방법:
데이터는 먼저 CAD 및 Inspire Cast 소프트웨어에서 금형과 공정을 모델링하여 수집되었습니다. 분석은 시뮬레이션을 실행하고 시각적 결과물, 특히 2차 사출 단계 중의 온도 구배(그림 1, 2, 4)와 예측된 미세 기공 맵(그림 3, 5)을 검토하여 수행되었습니다. 이 연구는 또한 사전 시뮬레이션 유무에 따른 물리적 시험의 비용과 불량률을 비교했습니다.
연구 주제 및 범위:
이 연구는 특정 ADC12 알루미늄 다운라이트의 고압 다이캐스팅에 중점을 두었습니다. 범위는 주로 콜드 샷 및 미세 기공과 같은 결함을 줄이기 위해 사출 파라미터(여러 단계에서의 플런저 속도 및 위치)를 최적화하는 것으로 제한되었습니다. 금형 자체를 재설계하는 것은 포함되지 않았습니다.
6. 주요 결과:
주요 결과:
주요 결과는 시뮬레이션을 성공적으로 사용하여 콜드 샷의 원인을 식별하고 결함을 줄이는 새로운 공정을 검증한 것입니다. 초기 구성은 금속 흐름이 665°C 재결정 온도 이하에서 만나고 있음을 보여주었습니다. 제안된 "대안 1" 및 "대안 2" 구성은 이러한 합류 지점의 온도 프로파일을 개선했습니다. "대안 1"은 예측된 미세 기공을 1.35%-1.8%로 줄였고, "대안 2"는 1.35%-2.25% 범위를 보였습니다. 이 연구는 시뮬레이션이 물리적 시험 비용을 크게 절감한다고 결론지었습니다.
그림 이름 목록:
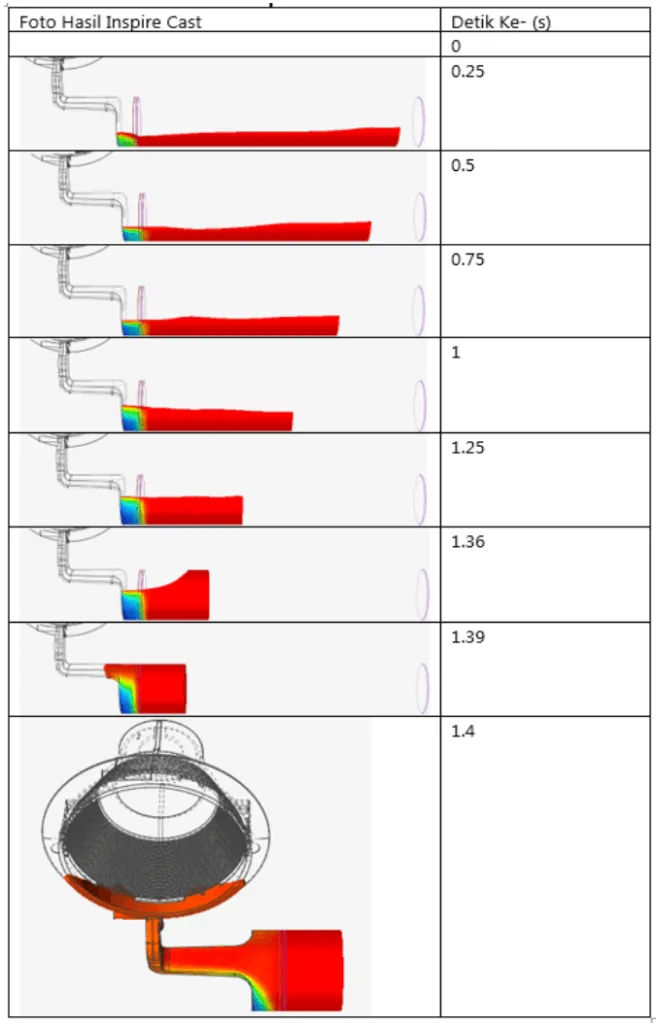
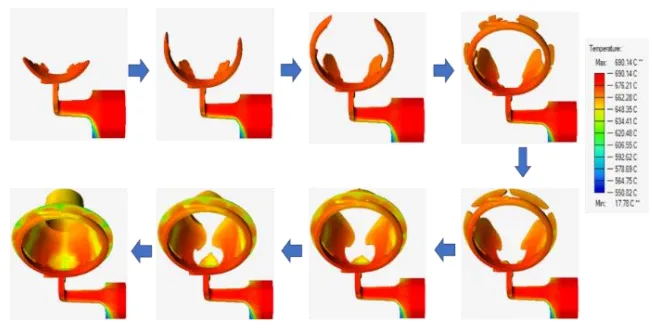
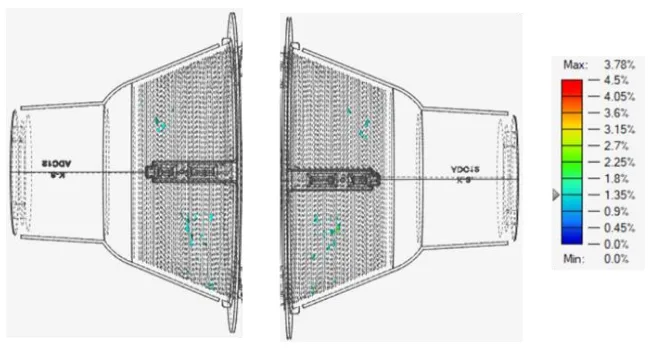
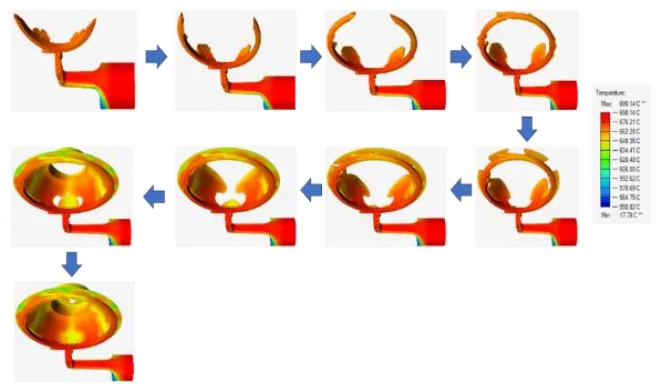
- 그림 1. 초기 구성에서의 주조 공정 시뮬레이션 결과
- 표 2. 파라미터 대안 1의 구성
- 표 3. 파라미터 대안 2의 구성
- 그림 2. Inspire Cast 시뮬레이션 결과: 2단계 파라미터 대안 1
- 그림 3. Inspire Cast 시뮬레이션 결과: 미세 기공 파라미터 대안 1
- 그림 4. Inspire Cast 시뮬레이션 결과: 2단계 파라미터 대안 2
- 그림 5. Inspire Cast 시뮬레이션 결과: 미세 기공 파라미터 대안 2
7. 결론:
이 논문은 네 가지 주요 결론을 도출합니다:
a. 가장 널리 퍼진 결함인 콜드 샷은 합류하는 알루미늄 흐름의 온도가 재결정 온도보다 낮아서 발생했습니다.
b. 시뮬레이션은 금형 내 알루미늄 흐름을 명확하게 묘사하여 생산 시작 전에 잠재적 결함을 분석할 수 있게 하여 시험과 관련된 비용을 줄이는 데 도움이 됩니다.
c. 공식을 사용하여 개발된 구성은 개선되었지만 완전히 최적화되지는 않을 수 있습니다. 시뮬레이션은 이러한 계산된 파라미터를 개선하여 더 나은 결과를 달성하고 물리적 시험 비용을 줄이는 데 도움이 됩니다.
d. 사출 구성의 변경은 최종 제품 품질에 직접적인 영향을 미칩니다.
8. 참고 문헌:
- Kwon & Kwon, 2019
- Shankar Kamble & Kadane, 2016
- Laukli, 2004
- Rahimi, A.(2003). Introduction Of High Pressure Die-Casting And Common Defects In Die-Casting. Islamic Azad Univercity Of Saveh
- Krisbianto, D., Rahmalina, D., & Suwandi, A. (2019). Optimasi Desain Gating System Proses Die Casting Cold Chamber Menurunkan Cacat Produk. Jurnal Kajian Teknik Mesin, 4(2), 50-67.
전문가 Q&A: 가장 궁금한 질문에 대한 답변
Q1: 이 연구에서 다운라이트 제품의 품질을 개선하는 데 가장 중요한 단일 요인은 무엇이었습니까?
A1: 이 연구는 금형 충전 중 용융 알루미늄의 온도를 관리하기 위해 사출 구성을 최적화하는 것이 가장 중요한 요인이라고 결론지었습니다. 이는 금속 흐름이 융합되기 전에 재결정 온도 이하로 떨어지는 것을 방지하여 콜드 샷 결함의 주요 원인을 직접적으로 해결했습니다. (출처: "결론 및 제언(KESIMPULAN DAN SARAN)", "[논문 제목]")
Q2: 이 연구는 주조 결함을 해결하는 전통적인 방법과 어떻게 비교됩니까?
A2: 논문의 결론은 전통적인 방법이 물리적인 "시뮬레이션 없는 시험(Trial tanpa adanya simulasi)"에 의존한다고 강조합니다. 이 연구는 시뮬레이션 우선 접근법을 도입하여 최적화된 공정을 달성하는 데 필요한 시험 비용과 횟수를 크게 줄였음을 보여주었습니다. (출처: "결론 및 제언(KESIMPULAN DAN SARAN)", "[논문 제목]")
Q3: 이 결과는 모든 종류의 합금에 적용됩니까, 아니면 특정 합금에만 적용됩니까?
A3: "본 연구에서는(Pada penelitian ini)" 섹션에 설명된 바와 같이, 이 연구는 특별히 ADC12 알루미늄을 사용하여 수행되었습니다. 이 논문은 이러한 특정 온도 값이나 파라미터가 다른 합금에 직접 적용될 수 있다는 주장을 하지 않으며, 이는 추가 조사가 필요합니다.
Q4: 연구원들은 이 결론에 도달하기 위해 어떤 특정 측정 또는 시뮬레이션 기술을 사용했습니까?
A4: 연구원들은 "Inspire Cast 소프트웨어"를 사용하여 사출 공정의 시각적 시뮬레이션을 만들었습니다. 이 소프트웨어를 통해 용탕 흐름의 온도를 분석하고 미세 기공 영역을 예측할 수 있었으며, 이는 "연구 방법론(Metode Penelitian)" 및 "결과 및 토의(Hasil Pembahasan)" 섹션에 설명되어 있습니다.
Q5: 논문에 따르면, 주요 한계점이나 향후 연구 분야는 무엇입니까?
A5: 저자들은 "결론(Kesimpulan)"에서 수학 공식만으로 개발된 구성은 시뮬레이션으로 개선된 구성에 비해 여전히 "최적이 아니다(kurang optimal)"라고 말합니다. "제언(Saran)" 섹션에서는 최상의 결과를 얻기 위해 계산된 구성을 기계에 직접 적용하기보다는 항상 시뮬레이션의 입력으로 사용해야 한다고 권장합니다.
Q6: 이 논문이 다이캐스팅 시설에 주는 직접적이고 실용적인 교훈은 무엇입니까?
A6: 핵심 교훈은 Inspire Cast와 같은 시뮬레이션 소프트웨어를 사용하여 물리적 시험을 수행하기 전에 사출 파라미터를 모델링하고 최적화함으로써 콜드 샷과 같은 결함 문제를 해결하는 데 필요한 비용과 시간을 크게 줄일 수 있다는 것이며, 이는 "Pengendalian Kualitas Produk Downlight dengan Implementasi Simulasi Die Casting" 논문의 전반적인 결과에 의해 강력하게 뒷받침되는 결론입니다.
결론 및 다음 단계
이 연구는 HPDC 공정의 품질 관리를 향상시키기 위한 귀중한 로드맵을 제공합니다. 반응적이고 시행착오적인 접근 방식에서 벗어나 선제적이고 시뮬레이션 중심적인 방법론으로 전환함으로써 제조업체는 복잡한 주조 공정을 정밀하게 제어할 수 있습니다. 이 연구 결과는 품질을 개선하고, 콜드 샷과 같은 결함을 줄이며, 궁극적으로 생산 비용을 최적화하는 명확하고 데이터 기반의 길을 제시합니다.
CASTMAN은 고객의 가장 어려운 다이캐스팅 문제를 해결하기 위해 최신 산업 연구를 적용하는 데 전념하고 있습니다. 이 논문에서 논의된 문제가 귀사의 운영 목표와 공감대를 형성한다면, 저희 엔지니어링 팀에 연락하여 귀사의 부품에 이러한 고급 원칙을 구현하는 방법을 논의하십시오.
저작권
- 이 자료는 "Trio Yonathan Teja Kusuma, Gunawan Budi Susilo, M Zulhan Iswanda"의 논문입니다. "Pengendalian Kualitas Produk Downlight dengan Implementasi Simulasi Die Casting"을 기반으로 합니다.
- 논문 출처: https://doi.org/10.21107/rekayasa.v16i1.18839
이 자료는 정보 제공 목적으로만 사용됩니다. 무단 상업적 사용을 금지합니다.
Copyright © 2025 CASTMAN. All rights reserved.