본 논문 요약은 ['MDPI']에서 발행한 ['A Water-Soluble Core for Manufacturing Hollow Injection-Molded Products'] 논문을 기반으로 작성되었습니다.
1. 개요:
- 제목: 속이 빈 사출 성형 제품 제조를 위한 수용성 코어 (A Water-Soluble Core for Manufacturing Hollow Injection-Molded Products)
- 저자: Chung-Chih Lin, Chao-Long Yang
- 발행 연도: 2022년
- 발행 학술지/학회: Polymers
- 키워드: 사출 성형 (injection molding); 수용성 코어 (water-soluble core); 인서트 성형 (insert molding); 다구치 방법 (Taguchi method)
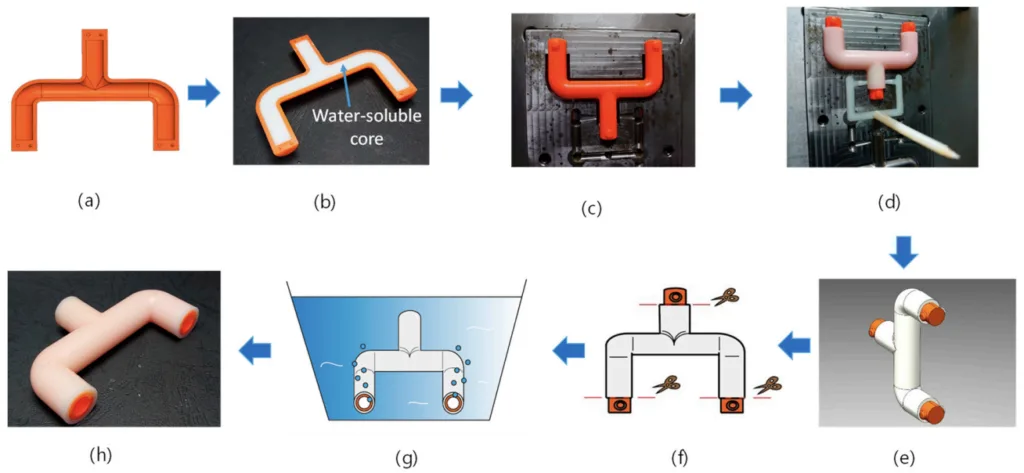
2. 초록 또는 서론
초록: 복잡한 속이 빈 제품을 조립 공정 없이 제조하는 것은, 예를 들어 플라스틱 흡기 매니폴드와 같이, 전통적인 사출 성형 방법으로는 어렵습니다. 희생 코어로서 저융점 합금을 사용하는 퓨저블 코어 (fusible-core) 기술은 이 문제를 해결하기 위해 개발되었지만, 제한적인 수지 종류 선택과 막대한 자본 투자로 인해 기술 확산이 더디게 진행되었습니다.
본 연구에서는 수지 종류의 제한 없이, 더 낮은 에너지 소비 공정으로 유사한 제품을 생산할 수 있는 새로운 방법을 확립합니다. 쉘 (shell)과 조립된 수용성 코어로 정의되는 엔벨로프드 코어 (enveloped core) 개념이 본 연구에서 제안됩니다. 이는 사출 성형 공정 중 압력에 저항하는 강성과 인성을 모두 제공합니다. 엔벨로프드 코어의 모양은 지정된 제품의 내부 윤곽과 동일합니다.
인서트 성형 공정이 엔벨로프드 코어를 스킨 층 (skin layer)으로 덮기 위해 도입되었습니다. 엔벨로프드 코어의 끝을 잘라내고 물에 담급니다. 쉘 내부의 수용성 코어가 용해되면 특수한 내부 윤곽을 가진 제품이 완성됩니다. 티-조인트 (tee-joint)를 통해 제안된 방법의 활용 방법을 시연합니다. 코어의 최적 성분과 공정 파라미터는 다구치 방법으로 결정됩니다.
결과는 코어의 압축 강도가 2 MPa보다 클 때 제안된 제품이 성공적으로 성형됨을 보여줍니다. 또한, 최적 샘플의 내부 윤곽의 편심 측정 결과 56% 개선되었으며, 코어 제거에 필요한 시간은 154초 미만입니다.
3. 연구 배경:
연구 주제 배경:
플라스틱 흡기 매니폴드와 같은 복잡한 속이 빈 제품을 전통적인 사출 성형 방법으로 제조하는 것은 상당한 어려움이 있습니다. 기존 방법은 종종 제품을 하위 부품으로 나누고, 기계적 체결 또는 접착제 접착과 같은 조립 공정을 거쳐야 합니다.
이러한 조립 단계는 제조 비용을 증가시키고, 치수 오차를 누적시키며 [5,6], 최종 제품에 취약점을 만들어 고압 또는 과부하 작동 시 고장을 유발할 수 있습니다. 더욱이, 접착 공정은 환경을 오염시키는 화학 용매를 사용할 수 있습니다.
기존 연구 현황:
속이 빈 제품 제조를 위한 기존 기술에는 금속 배기 매니폴드 주조용 샌드 코어 [7] 및 레진 트랜스퍼 몰딩 (RTM) 용 폴리옥시메틸렌 (POM) 또는 폴리스티렌 (PS) 폼과 같은 폴리머 코어와 같은 "제거 가능 또는 콜랩스 코어 기술 (removable or collapse core skill)"이 포함됩니다. 염 코어는 "물에 대한 우수한 용해도 (good solubility in water)" 때문에 사용되기도 합니다 [7-11].
그러나 "RTM 공정에 의해 유도되는 압력은 플라스틱 사출 공정의 압력보다 훨씬 낮기 때문에", 취성 염 코어는 사출 성형 중 균열 및 코어 이동에 취약합니다. 희생 코어로서 저융점 합금을 사용하는 "퓨저블 코어 기술 (fusible-core technique)" [12]은 이러한 방법을 개선했지만, "제한적인 수지 종류 선택과 막대한 자본 투자 (limited selection of resin type and the huge capital investment)"라는 단점이 있습니다.
"수용성 폴리비닐 알코올 (PVOH) 패턴 (water-soluble polyvinyl alcohol (PVOH) patterns)" [13]을 사용하는 또 다른 방법이 존재하지만, 몰드 캐비티 내 지지 메커니즘이 퓨저블 코어 기술과는 다릅니다.
연구의 필요성:
속이 빈 제품 제조를 위한 기존 방법에도 불구하고, 특히 사출 성형 분야에서 "특수한 속이 빈 제품 (special hollow product[s])"을 생산하기 위한 개선의 필요성이 있습니다. 퓨저블 코어 기술과 같은 현재 방법은 수지 호환성 및 비용에 제한이 있으며, 염 코어는 취성 때문에 사출 성형에 직접 사용하기 어렵습니다.
따라서 이러한 한계를 극복하고 사출 성형을 통해 복잡한 속이 빈 부품을 효율적이고 다용도로 제조할 수 있는 새로운 방법이 필요합니다.
4. 연구 목적 및 연구 질문:
연구 목적:
본 연구의 목적은 기존 기술의 한계를 해결하여 사출 성형을 사용하여 복잡한 속이 빈 제품을 제조하는 새로운 방법을 확립하는 것입니다. 제안된 방법은 "쉘 (shell)과 조립된 수용성 코어 (water-soluble core)로 정의되는 엔벨로프드 코어 (enveloped core)" 개념에 초점을 맞추어 "수지 종류의 제한 없이, 더 낮은 에너지 소비 공정 (without the limitation of resin type, as well as a lower-energy-consumption process)"으로 제품을 생산하는 것을 목표로 합니다.
이 방법은 "사출 성형 공정 중 압력에 저항하는 강성과 인성 (both rigidity and toughness to resist the pressure during the injection molding process)"을 가진 코어를 제공하는 것을 목표로 합니다.
핵심 연구 질문:
핵심 연구 질문은 다음과 같습니다:
- NaCl (염)과 트레할로스 설탕 (바인더)으로 구성된 수용성 코어 재료를 개발하고 특성화할 수 있는가?
- 수용성 코어와 플라스틱 쉘을 사용하여 "엔벨로프드 코어 (enveloped core)" 시스템을 설계하고 구현할 수 있는가?
- 다구치 방법 (Taguchi method)을 사용하여 적절한 코어 강도를 달성하기 위해 "코어의 성분과 공정 파라미터 (ingredient of the core and processing parameters)"를 최적화할 수 있는가?
- 복잡한 내부 윤곽을 가진 티-조인트 (tee-joint) 제품을 제조하여 제안된 방법의 타당성을 입증할 수 있는가?
- "바인더 함량, 가해지는 압력, 공정 온도 및 공정 시간이 코어 강도 및 성형 제품의 치수 정확도, 코어 제거율에 미치는 영향 (influence of the binder content, applied pressure, processing temperature, and processing time on the core strength and the dimension accuracy of the molded product, as well as the core removal rate)"을 평가할 수 있는가?
연구 가설:
연구 가설은 다음과 같습니다:
- 수용성 코어와 플라스틱 쉘로 구성된 엔벨로프드 코어 (enveloped core)는 노출된 수용성 코어와 달리 사출 성형 압력을 견딜 수 있을 것이다.
- 다구치 방법 (Taguchi method)을 사용하여 수용성 코어의 조성 (염 및 바인더 비율) 및 공정 파라미터 (압력, 온도, 시간)를 최적화하면 사출 성형에 충분한 압축 강도를 가진 코어를 얻을 수 있을 것이다.
- 제안된 엔벨로프드 코어 (enveloped core) 방법은 티-조인트 (tee-joint)와 같이 복잡한 내부 형상을 가진 속이 빈 제품을 향상된 치수 정확도와 효율적인 코어 제거로 제조할 수 있게 할 것이다.
5. 연구 방법론
연구 설계:
본 연구는 수용성 코어 배합 및 공정 파라미터를 최적화하기 위해 다구치 방법 (Taguchi method)에 기반한 실험 설계를 채택합니다. 이 연구는 다양한 조성과 다양한 공정 조건 하에서 수용성 코어를 제작하고, 기계적 테스트 및 결과 성형 제품 평가를 수행합니다. 티-조인트 (tee-joint) 제품은 제안된 방법의 시연을 위해 선택되었습니다.
자료 수집 방법:
자료는 다음 방법을 통해 수집되었습니다:
- 압축 시험 (Compression Test): 수용성 코어의 압축 강도는 ASTM D695-15 및 C473-15 표준에 따라 "HongTa testing machine (HT-2402, Taichung, Taiwan)"을 사용하여 측정되었습니다. 시편은 "직경 및 높이 35 mm × 35 mm"의 원통형으로 설계되었습니다.
- 치수 측정 (Dimensional Measurement): 성형된 티-조인트 (tee-joint) 제품의 기하학적 정확도는 "좌표 측정기 (coordinate measuring machine) (Brown & Sharpe Co., Ltd., Inspector classic, North Kingston, RI, USA)"를 사용하여 평가되었습니다. 치수 정확도를 정량화하기 위해 내부 윤곽의 편심률 (eccentricity)이 계산되었습니다.
- 코어 제거율 측정 (Core Removal Rate Measurement): 코어 제거율은 "전도도 측정기 (conductivity meter) (DFRobot SEN0244)", "TDS (총 용존 고형물) 프로브 (TDS (total dissolved solids) probe)", 및 "데이터 수집 보드 (data acquisition board) (DFRduino UNO R3)"를 사용하여 염 코어가 용해됨에 따라 수조의 전도도 변화를 측정하여 결정되었습니다.
자료 분석 방법:
수집된 자료는 다음 방법을 사용하여 분석되었습니다:
- 다구치 방법 (Taguchi Method): "L9(34) 직교 배열 (orthogonal array)"은 실험을 설계하고 코어 준비를 위한 최적 파라미터를 결정하는 데 사용되었습니다. "S/N 비 (S/N ratio)" 및 "ANOVA (분산 분석)"는 결과를 분석하고 중요한 요인을 식별하는 데 사용되었습니다.
- 편심률 계산 (Eccentricity Calculation): 편심률은 방정식 (2) 및 (3)을 사용하여 내부 윤곽이 완전한 원에서 벗어나는 정도를 정량화하기 위해 계산되었습니다.
- 코어 제거율 계산 (Core Removal Rate Calculation): 코어 제거율은 전도도 측정값을 기반으로 방정식 (4)를 사용하여 계산되었습니다.
연구 대상 및 범위:
본 연구는 다음 사항에 초점을 맞추었습니다:
- 재료 (Materials): "NaCl (염)" 및 "트레할로스 설탕 (바인더)"로 구성된 수용성 코어 재료, 쉘 및 스킨 층 (skin layer)을 위한 "아크릴로니트릴 부타디엔 스티렌 (ABS, POLYLAC PA-757, from CHIMEI Corp., Taipei, Taiwan)".
- 제품 (Product): "그림 3"에 표시된 특정 내부 윤곽을 가진 티-조인트 (tee-joint).
- 공정 파라미터 (Process Parameters): 코어 준비를 위한 바인더 함량, 가해지는 압력, 공정 시간 및 공정 온도, 그리고 "표 2"에 나열된 쉘 및 스킨 층 사출 성형을 위한 성형 파라미터.
6. 주요 연구 결과:
핵심 연구 결과:
- 최적 코어 파라미터 (Optimal Core Parameters): 다구치 방법 (Taguchi method)은 수용성 코어 준비를 위한 최적 파라미터를 "A3B3C2D3"로 식별했으며, 이는 특정 수준의 바인더 함량, 가해지는 압력, 공정 시간 및 공정 온도에 해당합니다.
- 압축 강도 (Compressive Strength): 최적 코어는 "3.2 MPa"의 압축 강도를 달성했으며, 이는 "표 3에 나열된 Exp. No. 5의 최대 강도에 비해 17.2% 향상 (17.2% improvement compared to the maximum strength of Exp. No. 5 listed in Table 3)"된 것입니다. 제안된 제품은 "코어의 압축 강도가 2 MPa보다 클 때 성공적으로 성형될 수 있습니다 (molded successfully when the compressive strength of the core is larger than 2 MPa)".
- 치수 정확도 개선 (Dimensional Accuracy Improvement): 최적 샘플의 내부 윤곽의 편심률 측정 결과, 최적이 아닌 파라미터로 제작된 샘플에 비해 "56% 개선 (56% improvement)"되었습니다. 편심률은 "26.3%에서 11.5%로 감소 (reduced from 26.3% to 11.5%)"했습니다.
- 코어 제거 시간 (Core Removal Time): 최적 코어의 코어 제거에 필요한 시간은 "154초 미만 (less than 154 s)"이었습니다.
제시된 자료 분석:
- 그림 7은 "설정 파라미터에 따른 염 코어의 압축 응력-변형률 곡선 (Compressive-stress-and-strain curves for salt core with respect to setting parameters)"을 나타내며, 다양한 파라미터 조합으로 준비된 코어의 압축 강도를 보여줍니다.
- 그림 9는 "샘플의 내부 윤곽의 편심률 측정 (The eccentricity measurement of internal contour of samples)"을 보여주며, 최적 샘플과 파괴된 샘플의 편심률을 5개 위치에서 비교합니다. 최적 샘플은 대부분의 위치에서 더 낮은 편심률 값을 나타냅니다.
- 그림 10은 "(a) 최저 강도 그룹의 코어 제거율 및 (b) 최고 강도 그룹의 코어 제거율 ((a) Core removal rate of the lowest strength group and (b) core removal rate of the highest strength group)"을 보여주며, 다양한 압축 강도를 가진 코어의 용해 속도를 보여줍니다. 강도가 높은 코어는 용해하는 데 시간이 더 오래 걸립니다.
그림 목록:
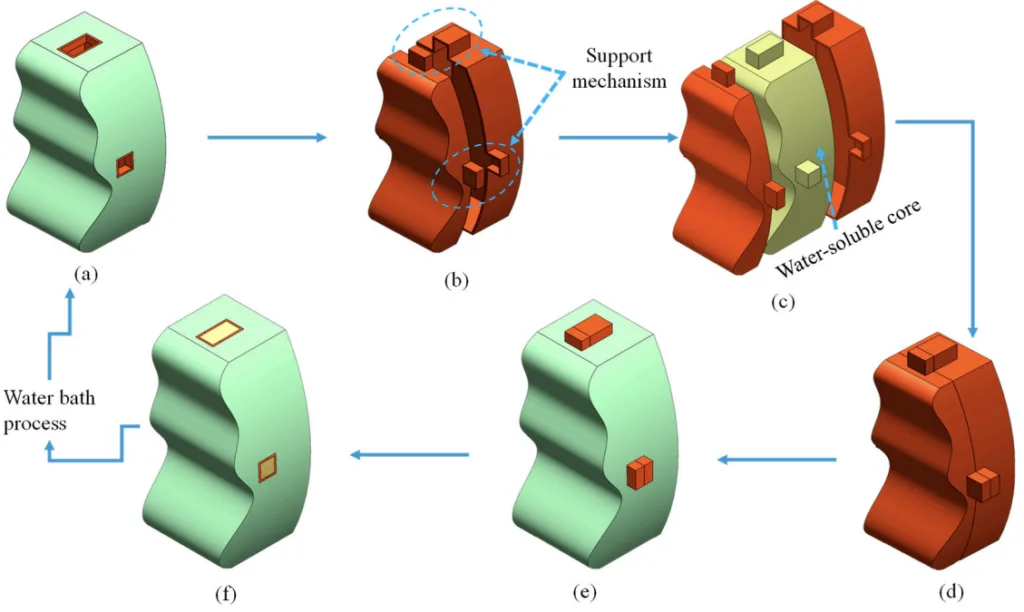
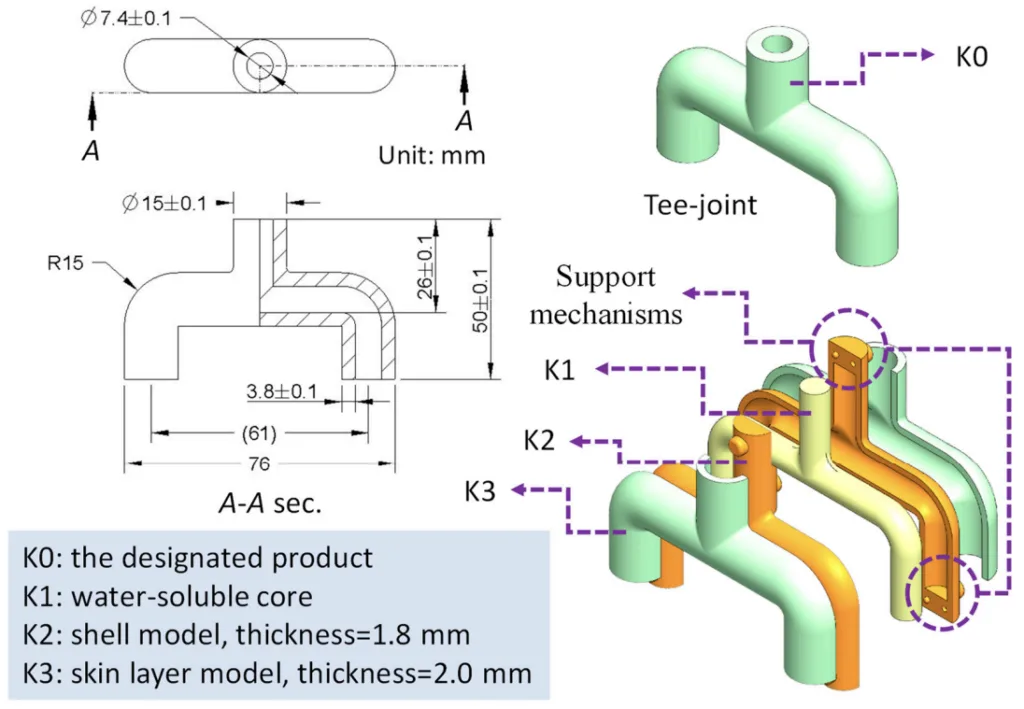
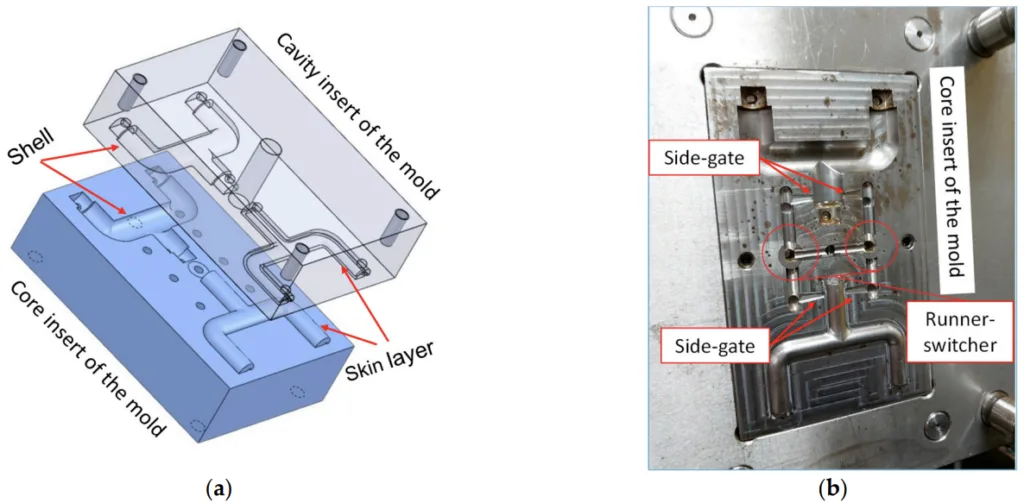
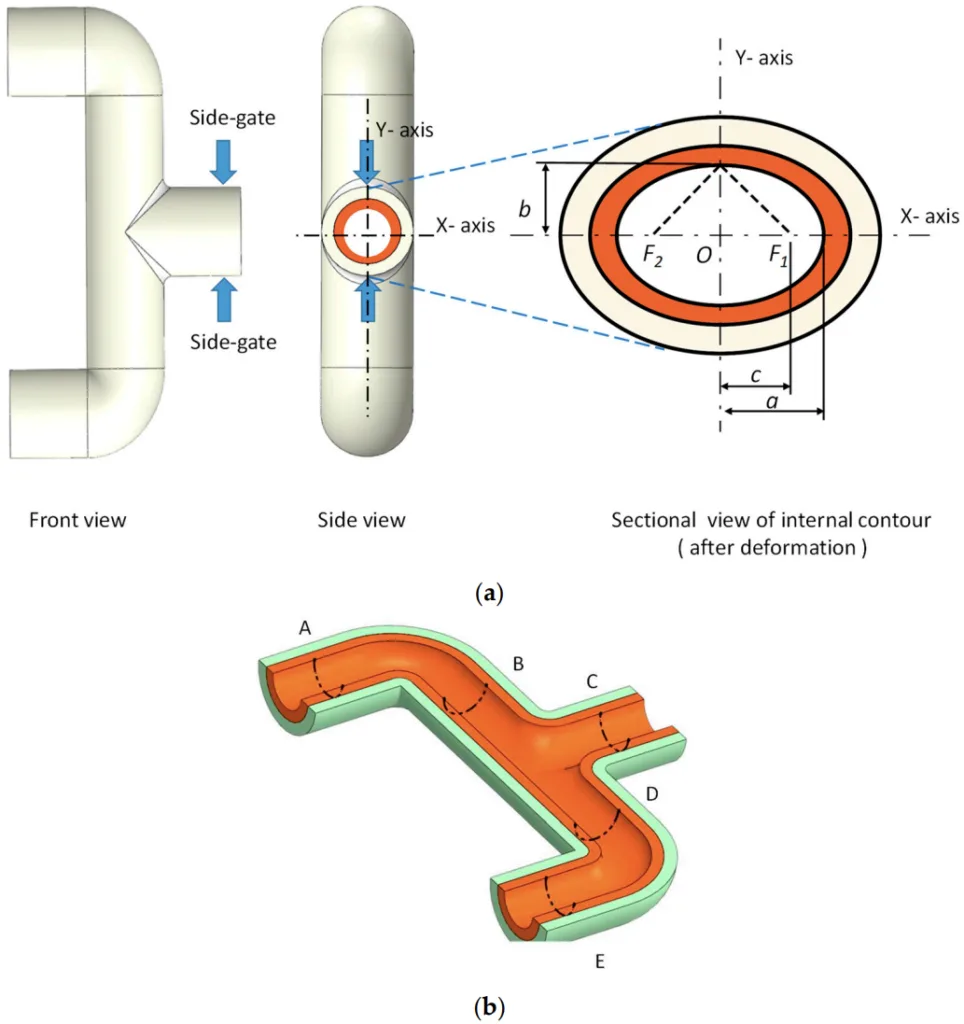
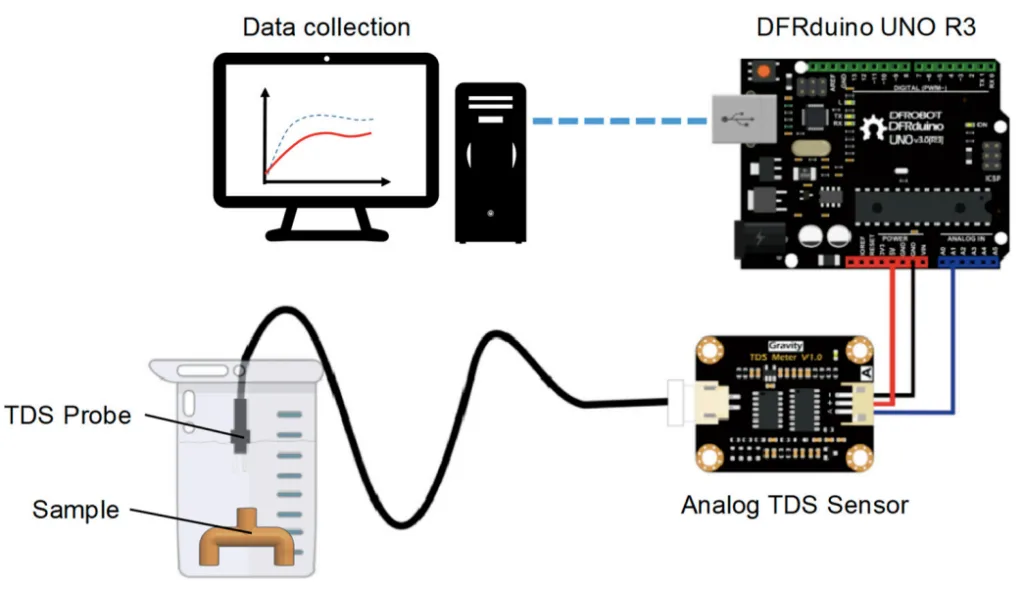
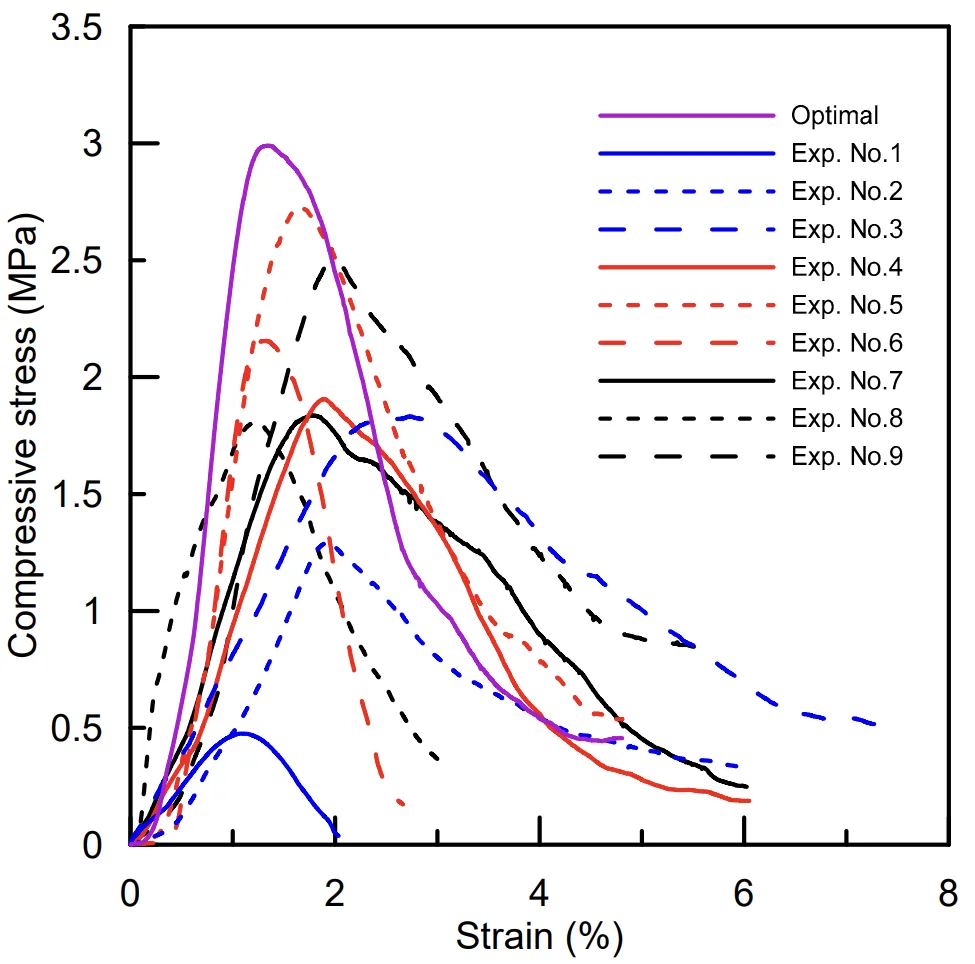
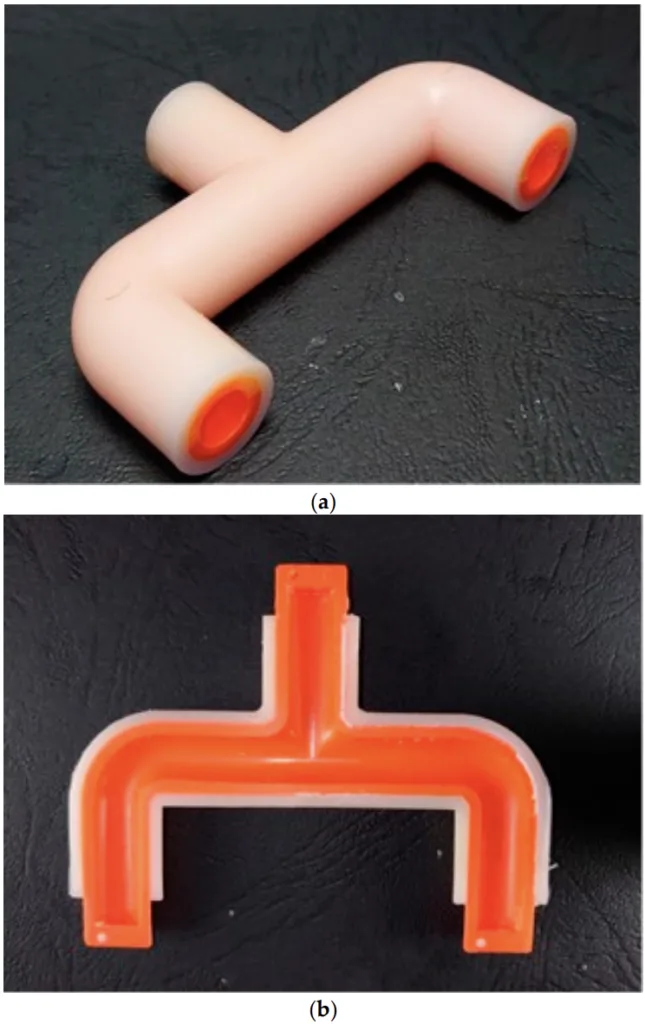
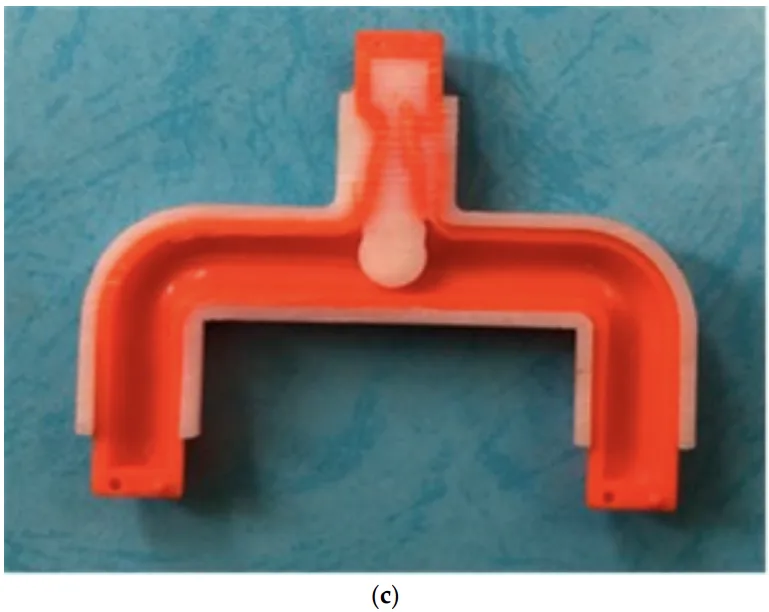
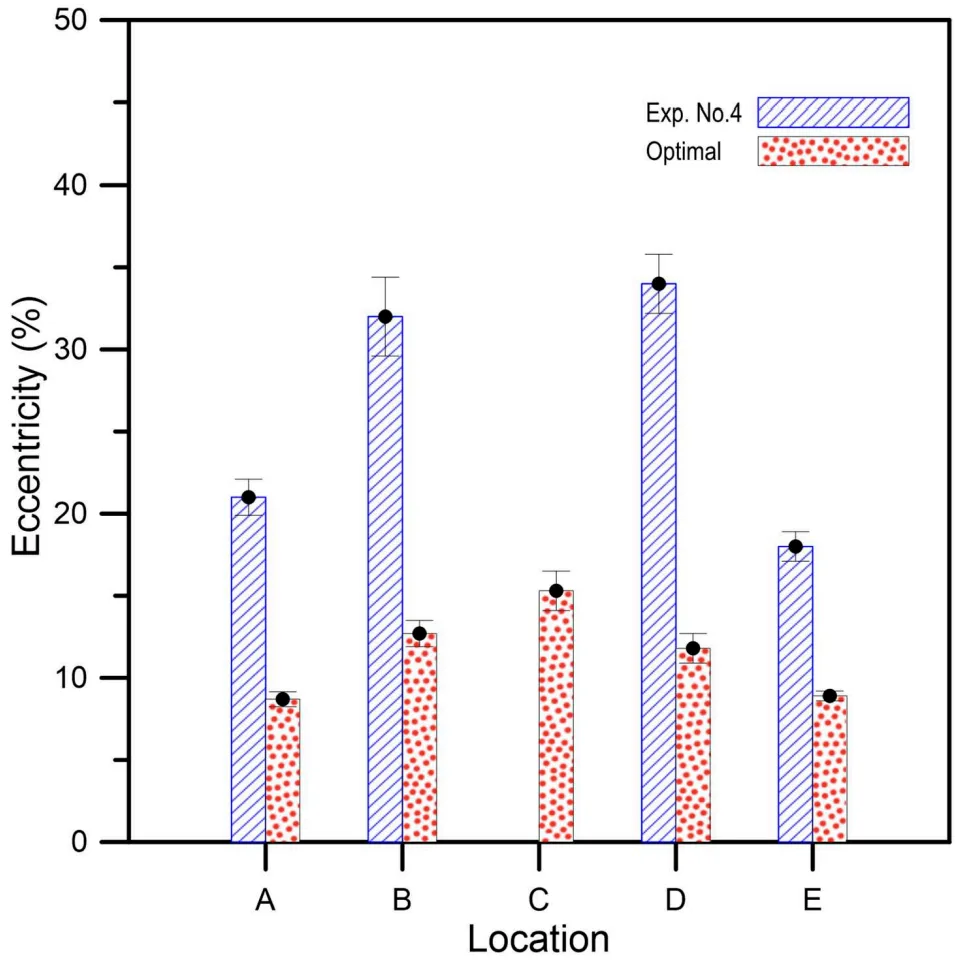
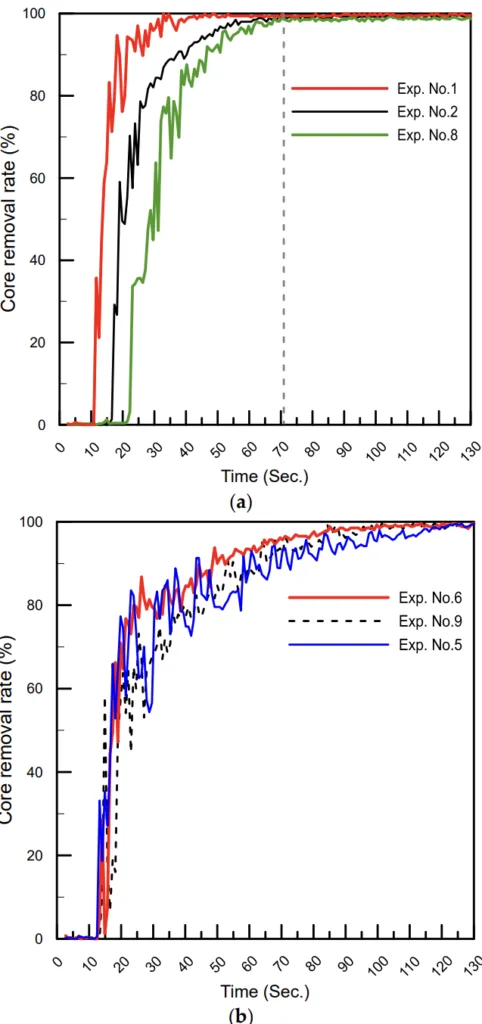
- 그림 1. 수용성 코어와 (a) 쉘 (shell)을 사용하여 속이 빈 제품을 생산하기 위한 준비 절차 (b): 쉘 (shell)이 있는 수용성 코어가 준비됨; (c) 엔벨로프드 코어 (enveloped core)는 두 개의 코어 쉘 (core shell)로 준비되고 몰드 캐비티 (mold cavity)에 위치함, (d) 스킨 층 (skin layer)이 성형됨, (e) 제품이 몰드에서 배출됨, (f) 엔벨로프드 코어 (enveloped core)의 끝이 잘림, (g) 제품이 수조에 담겨 코어가 용해됨, (h) 최종 제품이 얻어짐.
- 그림 2. 설계 흐름의 개략도 (Schematic illustration of design flow): (a) 지정된 제품, (b) 제품의 내부 윤곽에서 생성된 쉘 모델의 두 절반, (c) 쉘 (shell)로 조립된 코어의 스케치, (d) 엔벨로프드 코어 (enveloped core), (e) 스킨 모델 (skin model)이 코어를 전체적으로 덮음, (f) 지지 메커니즘 (support mechanism)을 잘라냄.
- 그림 3. 지정된 티-조인트 (tee-joint) (K0), 코어 (K1), 쉘 모델 (shell model) (K2) 및 스킨 층 모델 (skin layer model) (K3)의 개략도.
- 그림 4. (a) 코어 및 캐비티 인서트 (cavity insert)의 스케치, (b) 테스트 몰드의 절반 측면.
- 그림 5. (a) 성형 제품의 편심률 측정 (Eccentricity measurement) 및 (b) 각 샘플 측정에 대해 정의된 5개 위치.
- 그림 6. 코어 제거율 측정의 개략도.
- 그림 7. 설정 파라미터에 따른 염 코어의 압축 응력-변형률 곡선.
- 그림 8. 계속.
- 그림 9. 샘플의 내부 윤곽의 편심률 측정.
- 그림 10. (a) 최저 강도 그룹의 코어 제거율 및 (b) 최고 강도 그룹의 코어 제거율.
7. 결론:
주요 연구 결과 요약:
본 연구는 엔벨로프드 수용성 코어 (enveloped water-soluble core)를 사용하여 속이 빈 사출 성형 제품을 제조하는 새로운 방법을 성공적으로 시연했습니다. 주요 연구 결과는 다음과 같습니다: (1) 수용성 코어와 쉘 (shell)을 결합한 엔벨로프드 코어 (enveloped core) 개념은 복잡한 속이 빈 부품의 사출 성형을 가능하게 합니다. (2) 다구치 방법 (Taguchi method)을 사용한 최적화는 코어 준비를 위한 최적 파라미터를 식별하여 압축 강도를 향상시켰습니다. (3) 제안된 방법은 치수 정확도를 크게 개선하여 편심률을 56% 감소시켰습니다. (4) 코어 제거 공정은 효율적이며, 최적 코어의 용해 시간은 154초 미만입니다.
연구의 학문적 의의:
본 연구는 엔벨로프드 수용성 코어 (enveloped water-soluble core) 개념을 도입하고 검증함으로써 사출 성형 분야에 기여합니다. 이는 수용성 코어의 적용 가능성을 저압에서 고압 성형 공정으로 확장합니다. 본 연구는 사출 성형 응용 분야에 최적화된 수용성 코어의 재료 조성 및 공정 파라미터에 대한 귀중한 통찰력을 제공합니다. 코어 최적화를 위한 다구치 방법 (Taguchi method)의 사용과 치수 정확도 및 코어 제거율에 대한 상세한 평가는 연구의 학문적 엄격성과 실제적 관련성을 더합니다.
실용적 의미:
제안된 방법은 복잡한 속이 빈 플라스틱 부품 제조를 위한 기존 기술에 대한 실용적인 대안을 제공합니다. 이는 수지 종류 제한 및 높은 자본 투자와 같은 퓨저블 코어 (fusible core)와 관련된 한계를 극복합니다. 코어에 쉽게 구할 수 있고 저렴한 재료 (염 및 설탕)를 사용하고, 낮은 에너지 소비와 쉬운 구현을 결합하여 이 방법은 산업적으로 매력적입니다. 흡기 매니폴드와 같이 특수한 내부 윤곽을 가진 제품을 비용 효율적이고 환경 친화적인 방식으로 제조하는 데 적용할 수 있습니다. 효율적인 코어 제거 공정은 실용적인 유용성을 더욱 향상시킵니다.
연구의 한계 및 향후 연구 분야:
본 논문은 결론 섹션에서 명시적으로 한계 또는 향후 연구 분야를 언급하지 않습니다. 그러나 연구에 따르면 잠재적인 한계 및 향후 연구 방향은 다음과 같습니다:
- 쉘 (shell) 및 스킨 층 (skin layer)에 적용 가능한 폴리머 범위에 대한 추가 연구. 본 연구에서는 ABS가 사용되었지만, 다른 엔지니어링 플라스틱과의 호환성을 탐색하면 방법의 적용 가능성이 확대될 것입니다.
- 대량 생산을 위한 공정의 확장성 탐색. 현재 연구는 실험실 규모에서 타당성을 입증합니다. 대량 생산을 위해 공정을 최적화하기 위한 추가 연구가 필요합니다.
- 환경 지속 가능성을 더욱 향상시키기 위해 쉘 (shell) 재료의 재사용 및 재활용, 폐수에서 염 및 설탕 회수 가능성 조사.
- 엔벨로프드 코어 (enveloped core) 방법의 다용도성을 완전히 입증하기 위해 티-조인트 (tee-joint)를 넘어 더 복잡한 제품 형상 탐색.
- 용해 시간 및 물 소비량을 줄이기 위한 코어 제거 공정의 추가 최적화.
8. 참고 문헌:
- [1] Dorp, E.R.; Blume, C.; Haedecke, T.; Pata, V.; Reith, D.; Bruch, O.; Möginger, B.; Hausnerova, B. Process-dependent structural and deformation properties of extrusion blow molding parts. Polym. Test. 2019, 77, 105903.
- [2] Rodríguez-Castellanos, W.; Martínez-Bustos, F.; Rodrigue, D.; Trujillo-Barragán, M. Extrusion blow molding of a starch-gelatin polymer matrix reinforced with cellulose. Eur. Polym. J. 2015, 73, 335–343.
- [3] Mikhail Katsevman, M.; Pavlov, A.; Kruglov, P. Production of thermoplastic compound materials for processing by injection molding, blow molding and extrusion. Reinf. Plast. 2018, 62, 318–321.
- [4] Stevenson, J.F. Innovation in Polymer Processing: Molding; Carl Hanser Verlag: Munich, Germany, 1996.
- [5] Yaagoubi, M.E.; Haas, S.; Schwegler, D. The magnetic orientation of hard ferrites rubber bonded permanent magnets using the injection moulding. Sens. Actuators A Phys. 2021, 230, 112571.
- [6] Klein, R. Laser Welding of Plastics: Materials, Processes and Industrial Applications; John Wiley & Sons: Hoboken, NJ, USA, 2012.
- [7] Ettemeyer, F.; Schweinefuß, M.; Lechner, P.; Stahl, J.; Greß, T.; Kaindl, J.; Durach, L.; Volk, W.; Günther, D. Characterisation of the decoring behaviour of inorganically bound cast-in sand cores for light metal casting. J. Mater. Process. Technol. 2021, 296, 117201.
- [8] Kohlstädt, S.; Vynnycky, M.; Goeke, S. On the CFD Modelling of Slamming of the Metal Melt in High-Pressure Die Casting Involving Lost Cores. Metals 2021, 11, 78.
- [9] Jelínek, P.; Adámková, E. Lost cores for high-pressure die casting. Arch. Foundry Eng. 2014, 14, 101–104.
- [10] Kaerger, J.; Atz, L. Water soluble mandrels for lost core applications in manufacturing of hollow composite structures. In Proceedings of the SAMPE Europe Conference Nantes, Nantes, France, 17-19 September 2019.
- [11] Xiao, Z.; Harper, L.T.; Kennedy, A.R.; Warrior, N.A. A water-soluble core material for manufacturing hollow composite sections. Compos. Struct. 2017, 182, 380–390.
- [12] Osswald, T.A.; Turng, L.-S.; Gramann, P. Injection Molding Handbook; Carl Hanser Verlag: Munich, Germany, 2008.
- [13] McNulty, J.D.; Kharbas, H.; Thompson, C.; Ashton, R.S.; Turng, L.S. A method to create internal geometries within injection molded parts using water soluble Polyvinyl alcohol (PVOH) inserts. In Proceedings of the ANTEC Conference Orlando, Orlando, FL, USA, 23-25 March 2015.
- [14] Salzmann, M.; Blößl, Y.; Todorovic, A.; Schledjewski, R. Usage of Near-Infrared Spectroscopy for Inline Monitoring the Degree of Curing in RTM Processes. Polymers 2021, 13, 3145.
- [15] Bhudolia, S.K.; Perrotey, P.; Gohel, G.; Joshi, S.C.; Gerard, P.; Leong, K.F. Optimizing Bladder Resin Transfer Molding Process to Manufacture Complex, Thin-Ply Thermoplastic Tubular Composite Structures: An Experimental Case Study. Polymers 2021, 13, 4093.
- [16] Bargaoui, H.; Azzouz, F.; Thibault, D.; Cailletaud, G. Thermomechanical behavior of resin bonded foundry sand cores during casting. J. Mater. Process. Technol. 2017, 246, 30-41.
- [17] Sussich, F.; Urbani, R.; Princivalle, F.; Cesàro, A. Polymorphic amorphous and crystalline forms of trehalose. J. Am. Chem. Soc. 1998, 120, 7893-7899.
- [18] Kan, Z.; Yan, X.; Ma, J. Conformation dynamics and polarization effect of α, α-Trehalose in a vacuum and in aqueous and salt solutions. J. Phys. Chem. A 2015, 119, 1573–1589.
- [19] Yanykin, D.V.; Khorobrykh, A.A.; Semenov, A.Y.; Mamedov, M.D. Effect of Trehalose on the Functional Properties of Photosystem II. In Allakhverdiev, Photosynthesis: Molecular Approaches to Solar Energy Conversion, Proceedings of the Advances in Photosynthesis and Respiration; Shen, J.R., Satoh, K., Eds.; Springer: Cham, Switzerland, 2021; Volume 47.
9. 저작권:
- 본 자료는 "Chung-Chih Lin, Chao-Long Yang"의 논문: "A Water-Soluble Core for Manufacturing Hollow Injection-Molded Products"를 기반으로 합니다.
- 논문 출처: https://doi.org/10.3390/polym14112185
본 자료는 상기 논문을 기반으로 요약되었으며, 상업적 목적으로 무단 사용하는 것을 금지합니다.
Copyright © 2025 CASTMAN. All rights reserved.