본 소개 내용은 "[Elsevier B.V.]"에서 출판한 논문 "[Wear properties of a new Al80Mg10Si5Cu5 multicomponent alloy]"에 기반합니다.
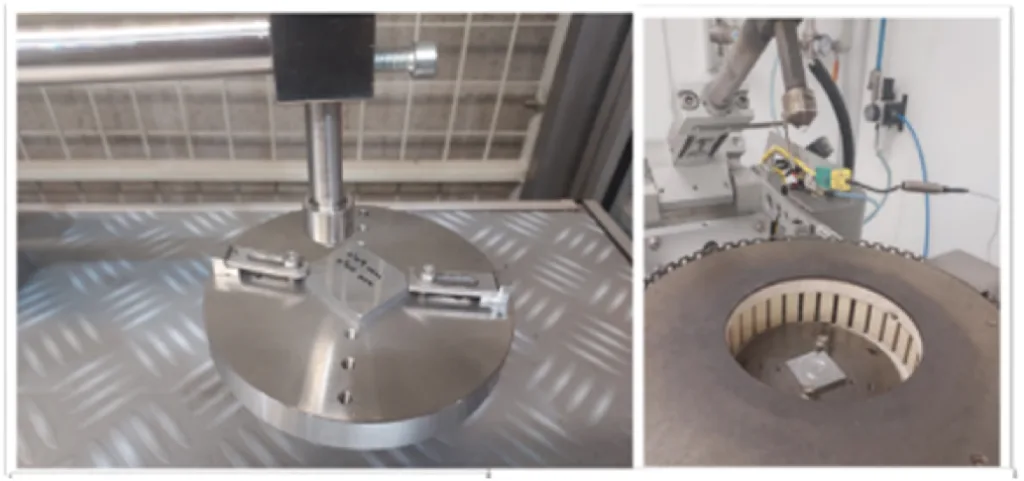
1. 개요:
- 논문 제목: Wear properties of a new Al80Mg10Si5Cu5 multicomponent alloy (새로운 Al80Mg10Si5Cu5 다성분 합금의 마모 특성)
- 저자: Ester Villanueva, Iban Vicario, Joseba Albizuri, Gurutze Arruebarrena, Teresa Guraya
- 발행 연도: 2024
- 발행 학술지/학회: Wear
- 키워드: Ball on disc, Friction, Wear, Aluminium multicomponent alloy, Abrasion (볼-온-디스크, 마찰, 마모, 알루미늄 다성분 합금, 연마 마모)
2. 초록:
본 연구는 경량 자동차 응용 분야, 특히 후륜 드럼 디스크용으로 새롭게 개발된 Al80Mg10Si5Cu5 시스템 기반의 다성분 알루미늄 경량 합금의 마모 관련 마찰학적 특성을 조사합니다. 샘플은 주조 합금 리턴 스크랩과 이차 알루미늄 잉곳을 사용하여 고압 다이캐스팅(HPDC)으로 제조되었으며, 상온(RT) 및 200 °C에서 시험되었습니다. A180Mg10Si5Cu5 합금은 상온에서, 특히 200 °C에서 기준 합금인 AlSi9Cu3보다 더 높은 경도와 내마모성(마모율 10배 감소)을 제공하는 것으로 관찰되었습니다. HPDC 주조 부품의 외부 표면층(스킨)을 유지하는 것의 영향이 볼-온-디스크 시험을 통해 연구되었으며, 이는 향상된 마찰학적 특성과 접촉면 가공 회피 가능성을 보여주었습니다. 표면층이 있는 주조 상태의 A180Mg10Si5Cu5 합금은 상온에서 5 × 10⁻⁴ mm³/N·m²의 마모율 계수를 보였으며, 이는 스킨이 없는 샘플보다 50% 낮은 값입니다. 표면층이 있는 용체화 처리 샘플(440 °C에서 72시간, 75 °C에서 수냉, 자연 시효)은 11 × 10⁻⁴ mm³/N·m²의 마모율 계수를 보였으며, 이는 표면층이 없는 샘플보다 약 20% 낮은 값입니다. AlSi9Cu3 합금의 마모율은 상온에서 스킨이 없는 샘플에서 50% 이상 감소했습니다. 200 °C에서는 표면층이 있는 샘플의 마모율 계수가 더 낮았습니다.
3. 서론:
다성분 개념에 기반한 알루미늄 다상 및 비등원자 고엔트로피 합금(HEA)은 단상 합금과 대조적으로 우수한 물리적 및 기계적 특성을 가지는 것으로 입증되었습니다[1]. 이러한 합금에서 강화된 단상 미세구조를 얻기 위한 급속 응고 공정의 효과는 최근 연구에서 수집되었습니다[2]. 다른 한편으로, 산업계에서 경량 차량에 대한 수요는 알루미늄 주조 부품의 제조, 특히 고압 다이캐스팅(HPDC)에 의한 GIGAPRESS 기술을 사용하는 전기 자동차에서 급격한 성장을 야기합니다[3]. 전기 자동차 시장은 지속적으로 성장하고 있으며, 차량 자율성을 높이기 위해 경량화가 중요합니다. 알루미늄 드럼 브레이크는 후륜 브레이크의 힘이 전륜 브레이크보다 낮고, 운동 에너지 회수 시스템(KERS)을 사용하여 제동력을 감소시키므로 경량 전기 자동차에 사용될 수 있습니다. 또한, 전륜 디스크 브레이크는 후륜 드럼 브레이크보다 먼저 작동하여 후륜 브레이크의 압력을 감소시킵니다[4]. 알루미늄 드럼은 철 드럼보다 가볍고, 방열성이 향상되었으며 페이드 현상이 감소되었고, 회주철 디스크의 부식 가능성과 디스크 고장을 피할 수 있습니다[5].
AlSiCu는 HPDC에서 사용되는 가장 일반적인 알루미늄 합금이지만, 기계적 특성에 특정 제한이 있습니다[6]. AlSiMgCu 합금은 더 높은 내식성과 강도를 제공하며, 일반적으로 열처리를 통해 개선되어 우수한 내마모성과 마찰이 요구되는 다양한 자동차 부품에 적합합니다[7,8]. 불충분한 내마모성은 알루미늄 합금의 문제점이지만[9], 알루미늄 합금의 마찰학적 특성은 합금 원소의 종류와 양을 조절하거나, 외부 강화상을 도입하거나, 열처리를 통해 향상될 수 있습니다[10–12]. 주철 브레이크를 대체하고 차량 무게를 줄이기 위해 알루미늄 기반 금속 기지 복합재료(AMC) 브레이크 로터가 개발되었습니다. AMC는 알루미늄 합금보다 열전도율이 높고, 밀도가 낮으며, 비강도가 높습니다. AMC는 맞춤형 특성을 얻기 위해 Al2O3, SiC, SiO2와 같은 경질 세라믹 입자로 강화된 연성 알루미늄 기지를 특징으로 합니다[13].
그러나 AMC의 주요 단점은 생산 비용(특히 가공성 비용), 입자 크기 및 분포 제어의 어려움(마모 특성이 강화 입자의 부피와 크기에 크게 의존하기 때문에)[14], 복잡한 주조 공정, 그리고 주로 낮거나 어려운 리턴 스크랩의 재활용성입니다.
AMC가 아닌 주조 알루미늄 합금의 마모 특성을 향상시키는 가장 일반적인 방법은 실리콘 합금화입니다. Si 비율을 높이면 더 많은 경질 Si 결정이 생성되어 합금의 경도와 내마모성이 증가합니다. 마찰학적 응용 분야에서는 일반적으로 공정(eutectic) 상의 알루미늄과 결합된 초정(primary) 실리콘 상을 가진 과공정(hypereutectic) Al-Si 합금(Si > 13 wt%)이 사용됩니다. 실리콘 상의 유형, 형태, 크기 및 분포는 소성 변형된 알루미늄 기지 영역에서 하중의 중요한 부분을 지지하여 마찰 및 내마모성을 향상시키는 데 중요합니다[15–17]. 이 합금들에서 Si는 Mg와 결합하여 Mg2Si로 석출되는 경향이 있습니다. Mg 양의 증가는 내마모성 향상을 촉진합니다[18]. 복잡한 금속간 화합물상은 마모 메커니즘에서 접합 성장과 응착을 방지하는 데 핵심적입니다. 금속간 화합물상이 많은 합금은 마모율이 낮습니다[19]. 합금 내 구리 증가는 기계적 특성을 향상시키고, 내식성을 감소시키며, 기공을 증가시킬 수 있습니다[20,21]. AlSi7Mg 합금에서는 미세한 결정립을 촉진하고 경도와 내마모성을 증가시켜 마찰 계수를 낮추는 Al₂Cu 금속간 화합물상을 얻기 위해 최소 1 wt%의 Cu가 필요했습니다[22]. 알루미늄 주조 합금의 경도를 향상시키는 메커니즘은 Mg와 Al, 그리고 Cu와 Si의 반응에 의해서도 영향을 받아 합금의 강화를 담당하는 다양한 석출물을 촉진합니다. 다양한 상의 형성 및 거동 정의는 여러 상이 β (Mg2Si), θ (Al₂Cu), S (Al₂CuMg) 또는 Q (Al5Cu2Mg8Si6)와 같이 가깝거나 동시에 석출될 수 있기 때문에 복잡한 작업입니다[23]. 열처리 동안 용체화 온도, 냉각 속도 및 시간은 중요한 역할을 하여 여러 복잡한 상호 작용을 초래합니다. 최적 온도에서의 시효 처리는 강도와 연성을 감소시킬 수 있는 크고 비정합적인 입자의 석출을 피합니다. Fe, Mn, Cr과 같은 다른 원소의 소량 조합은 Al-Si 합금의 경도와 강도를 향상시켜 내마모성을 증가시킵니다[24].
주조 알루미늄 합금의 마찰학 연구에 초점을 맞춘 연구에서는 AlSi 및 AlSiCuMg(X)와 같은 시스템[25–27]이 가장 많이 연구됩니다. 고 실리콘 알루미늄 합금에서는 일반적으로 하중 증가에 따라 연성 박리, 연마 마모, 취성 박리에서 홈파기 연마 마모로 마모 메커니즘이 변합니다[28]. 연마 마모와 산화는 경미한 마모 영역에서 지배적인 마모 현상이지만 항상 그런 것은 아닙니다. 박리, 응착 및 심각한 소성 변형은 AlSi9Cu3 HPDC 합금의 심각한 마모 영역에서 지배적입니다[23]. 박리는 표면층의 소성 변형을 통해 큰 마모 입자가 제거되는 것과 관련이 있으며, 이는 표면 아래 균열 핵 생성 후 균열 전파에 의해 발생합니다[29,30]. 이 메커니즘은 표면 아래 분리가 부착되어 마찰 계수를 증가시키는 전달층을 형성하는 고온에서 특히 분명합니다[31]. 또한, 고온에서의 마모율은 상온보다 10배 더 크다고 보고되었습니다[32]. 이러한 조건에서는 심각한 소성 변형, 재료 및 층 전달 및 축적을 포함하는 스커핑 메커니즘이 발생할 수 있습니다. 고온에서는 층 간의 접착력이 감소하여 박리를 촉진할 수 있습니다.
일부 연구에서는 마모 메커니즘이 온도에 따라 상온에서의 박리에서 부분적인 연마 마모로, 150 °C 이상에서는 소성 변형 및 산화 마모(소성 완화 메커니즘이 지배적)로 변화합니다[33–36]. AlSi9Cu3 합금에서는 다양한 상의 석출로 인해 경도 및 기계적, 마모 특성이 감소합니다[23,24]. 마모율은 150 °C보다 높은 온도에서 상온보다 훨씬 높지만, 온도와 선형적인 비례 관계는 없으며 약 200 °C에서 현저하게 증가합니다. AMC 및 알루미늄 합금에서 마모 시험 온도의 증가는 표면층의 더 높은 치밀도와 평균 저항을 촉진하여 입자 산화를 가속화합니다. 표면층 파괴 전에 표면층이 형성되면 마모율이 감소합니다[6]. 그러나 표면층이 치밀하지 않으면 표면 입자가 제거되고 표면이 손상되며 박리가 발생하여 마모율이 증가합니다[23].
경미한 마모에서 심각한 마모로의 전이 메커니즘은 적용된 하중, 상대편 볼 재료, 슬라이딩 속도 및 접촉면 온도와 같은 시험 변수의 조합에 의해 설명됩니다. 일반적으로 심각한 마모는 합금의 열 연화로 인한 대규모 소성 변형과 관련이 있으며, 조건에 따라 알루미늄 합금은 박리 마모를 제어하면서 심각하지 않은 마모 조건에서 작동할 수 있습니다[9]. AlSiCu(Fe) 주조 합금에서 경미한 마모 메커니즘을 얻기 위한 조건이 연구되었습니다[9,11,12,16, 37–39].
또한 마모 응용 분야에 코팅을 사용하는 것에 대한 관심이 증가하고 있다는 점도 주목됩니다[40,41].
볼-온-디스크(BOD) 시험은 재료의 마모 특성을 결정하는 데 가장 많이 사용되는 시험 중 하나입니다. 볼-온-디스크 시험 데이터를 분석하여 마모율 메커니즘은 세 가지 주요 단계 또는 국면으로 나눌 수 있습니다[42–45]. 첫 번째 국면은 표면 거칠기 변형 및 잔류 입자 수 증가로 인해 모재와 볼 사이의 최대 접착력으로 표면층을 제거하는 것에 해당합니다. 두 번째 국면은 일반적으로 보호적인 마찰화학적 표면층의 형성 또는 홈파기 및 거칠기 변형 과정의 감소와 관련이 있습니다. 핀 표면 온도의 상승이 슬라이딩 표면에 산화물 층을 형성하여 부드러운 기지 재료가 상대편 볼 표면에 노출되는 것을 방지하고 핀 표면의 마모율을 감소시키는 하위 국면이 있는 경우도 있습니다[46, 47]. 세 번째 국면은 마찰학적 조건의 계면 정상 상태를 특징으로 합니다.
마모율에 대한 적용 하중 효과는 합금에 따라 다르며, 일부 합금은 낮은 하중에서 약한 마모율을 보이다가 중간 하중에서 마모율 값이 크게 증가하고 높은 하중에서 점진적으로 증가합니다. 낮은 적용 압력은 일반적으로 마모로 인해 형성된 파편이 상대 표면의 골짜기에 갇히도록 촉진합니다. 파편이 골짜기에 갇히기 때문에 디스크의 돌출부에 의한 점 접촉이 접촉면으로 이동합니다. 접촉면으로의 이동과 샘플의 가공 경화는 정상 상태 마모로 이어졌습니다[48,49].
적용 압력의 증가는 온도 상승을 보여 산화물 층 제거로 이어졌습니다[48]. 파괴/분쇄된 산화물 층과 상대 표면의 마모 파편은 기계적으로 혼합된 층(MML) 또는 전달 필름(TF)의 형성을 유발할 수 있습니다. 적용 압력의 영향 하에서 전달 필름(TF)의 변형은 마모 파편의 변형 경화를 초래하여 TF의 경도를 증가시킵니다[48]. TF의 지속적인 형성과 제거는 금속 간 접촉을 방지하여 정상 상태 마모 영역에서 마모율이 일정하게 유지됩니다.
경미한 마모에서 심각한 마모 값으로의 전이는 적용된 하중에 따라 약 4~8N에서 최대 30N까지 다양할 수 있습니다[50]. 일반적으로 특정 마모율 값은 적용된 하중이 증가함에 따라 증가합니다.
상업용 브레이크 로터의 경우 마찰 계수(COF) 값은 0.45에서 0.69 사이입니다. 일부 저자에게는 하중 증가에 따른 COF 값의 선형적 증가가 없으며[51], 다른 저자에게는 예를 들어 Al-Al2O3 MMC 및 Al-SiC MMC 합금의 경우 브레이크 로터 응용 분야에서 0.30에서 0.60 사이의 안정적인 마찰 계수로 선형적 증가가 있습니다[52].
드럼 브레이크에서 경미한 또는 심각한 마모 상태를 정의하기 위해 보고된 마모율은 다양합니다. Al7.1Si 합금의 경우 k = 15 × 10⁻³ mm³/N·m[53], LM17 합금의 경우 6 × 10⁻³ mm³/N·m, 압력 및 속도(각각 0.2–1.0 N/mm ² 및 1.6 m/s)가 브레이크 로터의 제동 조건을 나타내는 알루미늄 복합재의 경우 7.5–10 × 10⁻³ mm³/N·m[54]으로 심각한 마모율이 보고되었습니다. 브레이크 로터 응용 분야용 루타일 및 실리마나이트 광물 하이브리드 AMC(HAMC)로 강화된 LM27 합금은 상업용 로터 재료의 경우 500m에서 약 16.5 × 10⁻³ mm³/N·m, HAMC의 경우 18 × 10⁻³ mm³/N·m의 마모율을 보였으며, 최종 정상 마모 값은 각각 약 6 및 7 × 10⁻³ mm³/N·m입니다. 0.37x10⁻⁴ ~ 2.37x10⁻⁴ mm³/N·m 사이의 값은 일반적으로 심각한 마모 영역 내에 있습니다[55]. 그러나 알루미늄 주조 합금의 경우, 15N 시험력에서 약 5 × 10⁻³ mm³/N·m입니다[56]. 시험 부하를 결정하기 위해, 시험된 합금에 따라 서지 정보 변동이 크기 때문에 알루미늄 브레이크에 대한 서지 정보와 결과를 비교하기 위해 15N이 선택되었습니다[56].
볼 재료 선택은 최종 결과를 수정할 수 있으므로 중요합니다. 알루미늄 합금의 경우, 강철 볼을 사용할 때 알루미늄과 강철의 친화력[55–57]으로 인해 시험 중 Al-Fe-O를 포함하는 MML 형성을 피하기 위해 알루미나가 종종 볼 재료로 사용되며, 최소한의 화학적 구동 접착으로 인해 접착 마모의 화학적 구동 측면을 최소화합니다. 따라서 알루미늄 합금이 마모 특성에 미치는 영향은 알루미나 상대 볼로 더 쉽게 판단할 수 있습니다[58].
새롭게 개발된 A180Mg10Si5Cu5 합금은 약 200 °C까지 특성을 유지하도록 설계되었으며, 합금 원소 선택은 Mg2Si 및 Al₂Cu 금속간 화합물상(내마모성을 증가시킴)을 얻되, 초정 Si는 존재하지 않도록(더 나은 기계적 특성과 연성을 얻기 위해) 신중하게 결정되었습니다. 새롭게 개발된 합금의 응용 분야는 알루미늄 드럼 브레이크, 특히 소형 전기 자동차의 후륜 브레이크일 수 있습니다.
최근, 스크랩 허용 Al65Cu10Mg10Si10Zn5 및 Al80Cu5Mg5Si5Zn5 HEA 알루미늄 합금이 연구되어 유망한 기계적 및 마모 특성을 보여주었지만[59], HEA 알루미늄 합금의 마모 특성에 대한 정보는 여전히 매우 적으며, 이차 알루미늄 합금 또는 스크랩 기반의 산업 공정으로 생산된 재료에 대한 정보는 더 적습니다. 이차 알루미늄 잉곳, 주조 알루미늄 리턴 스크랩, 마그네슘 스크랩을 전기 도가니로에서 용해하고 HPDC 공정을 사용하여 낮은 CO2 제조 가치를 얻었습니다[60].
따라서 본 연구에서는 개발된 합금을 상온 및 200 °C에서 연구하고, 주조 상태 및 열처리(TT) 상태에서 가장 표준적인 주조 합금(AlSi9Cu3 합금)과 비교할 것입니다.
병행하여, HPDC로 생산된 알루미늄 주조 부품은 외부 표면에 스킨 영역(또는 표면층)을 나타내며, 이는 결함이 거의 없고 기계적 특성이 향상되었습니다[61]. 그러나 볼-온-디스크(BOD) 시험에서 외부 표면층을 유지하는 것이 마모 특성에 미치는 영향은 연구되지 않았거나 매우 드물게 연구되었습니다[62].
4. 연구 요약:
연구 주제 배경:
자동차 산업, 특히 전기 자동차(EV) 분야에서 경량화 요구가 증가함에 따라 저밀도 알루미늄 합금에 대한 수요가 높아지고 있습니다. 고압 다이캐스팅(HPDC)은 이러한 부품을 생산하는 핵심 공정입니다. 일반적인 AlSiCu 합금은 한계가 있지만, 다성분 합금은 향상된 특성을 제공할 잠재력이 있습니다. 알루미늄 드럼 브레이크는 후륜 제동력이 낮고 주철보다 가볍기 때문에 EV에 고려되고 있습니다. 그러나 알루미늄 합금의 내마모성은 여전히 해결해야 할 과제입니다.
선행 연구 현황:
표준 AlSiCu 및 AlSiMgCu 합금은 HPDC에서 널리 사용되며, 종종 특성 향상을 위해 열처리가 필요합니다. 알루미늄 합금의 내마모성은 합금 원소(Si, Mg, Cu) 조절, 강화상 도입(알루미늄 매트릭스 복합재, AMC 등), 또는 열처리를 통해 개선될 수 있습니다. AMC는 우수한 특성을 제공하지만 높은 비용, 복잡한 공정, 낮은 재활용성이라는 단점이 있습니다. 비-AMC 합금의 경우, Si 함량은 경도를 증가시키고(Mg2Si 형성), Cu 첨가는 Al₂Cu를 형성하여 경도를 향상시키며, 다른 원소(Fe, Mn, Cr)도 기여합니다. 알루미늄 합금의 마모 메커니즘은 일반적으로 연마 마모, 산화, 박리를 포함하며, 온도(마모는 종종 150-200°C 이상에서 크게 증가)와 하중에 크게 영향을 받아 경미한 영역에서 심각한 영역으로 전이됩니다. 볼-온-디스크(BOD) 시험은 마찰학적 특성을 평가하는 일반적인 방법입니다. HPDC 부품은 미세한 입자의 표면 '스킨'을 특징으로 하며 향상된 특성을 가지지만, 마모에 미치는 영향은 거의 연구되지 않았습니다.
연구 목적:
본 연구는 200°C까지의 내마모성을 위해 설계된 새롭게 개발된 다성분 합금 Al80Mg10Si5Cu5의 마찰학적 특성(마찰 및 마모)을 조사하는 것을 목표로 했습니다. 이 연구는 이차 재료를 사용하여 HPDC로 생산된 이 합금을 표준 AlSi9Cu3 합금과 비교했습니다. 주요 목표는 상온(RT) 및 200°C에서의 성능을 평가하고, 특히 주조 상태의 외부 표면층(스킨)을 유지한 경우와 가공된 표면을 시험한 경우의 영향을 평가하는 것이었습니다. 목표 응용 분야는 자동차용 경량 알루미늄 드럼 브레이크입니다.
핵심 연구:
연구의 핵심은 새로운 Al80Mg10Si5Cu5 합금과 기준 AlSi9Cu3 합금의 시험 샘플을 이차 알루미늄을 사용하여 산업용 HPDC 공정으로 제조하는 것이었습니다. 일부 Al80Mg10Si5Cu5 샘플은 용체화 열처리(TT)를 받았습니다. 마찰학적 성능은 상온(RT) 및 200°C에서 알루미나 상대 볼에 대해 건식 슬라이딩 조건에서 볼-온-디스크(BOD) 마모 시험을 사용하여 평가되었습니다. 시험은 원래 HPDC 표면 스킨이 있는 샘플과 스킨이 제거된(연마된 표면) 샘플에 대해 수행되었습니다. 미세구조(광학 현미경, SEM/EDS), 상 조성(XRD), 경도(비커스, RT & 200°C)를 특성화했습니다. 이 연구는 새로운 합금과 표준 합금의 마찰 계수 및 비마모율을 비교하고, 표면 스킨의 영향, 열처리의 영향, 고온이 마모 거동 및 메커니즘에 미치는 영향을 분석했습니다.
5. 연구 방법론
연구 설계:
본 연구는 비교 실험 설계를 사용했습니다. 새롭게 개발된 Al80Mg10Si5Cu5 합금을 표준 기준 합금인 AlSi9Cu3과 비교했습니다. 두 합금 모두 HPDC를 사용하여 생산되었습니다. 실험 변수에는 합금 유형, 주조 상태 표면 스킨의 유무, 재료 상태(신규 합금의 경우 주조 상태 대 열처리 상태), 시험 온도(상온 대 200°C)가 포함되었습니다.
데이터 수집 및 분석 방법:
- 제조: 950톤 기계를 사용하여 고압 다이캐스팅(HPDC)으로 샘플 생산. 이차 알루미늄 합금 및 리턴 스크랩을 장입 재료로 사용. 일부 Al80Mg10Si5Cu5 샘플은 용체화 처리(440°C, 72시간) 후 수냉(75°C) 및 자연 시효(TT 조건) 처리됨.
- 화학 성분 분석: 광학 방출 분광법(OES) 사용.
- 미세구조 분석: 광학 현미경(MO) 및 에너지 분산형 X선 분광법(EDS)이 장착된 주사 전자 현미경(SEM)을 사용하여 특성화. 표준 금속 조직 준비 절차 따름.
- 상 식별: Cu-Kα 방사선을 사용한 X선 회절(XRD)로 수행.
- 경도 시험: UNE EN ISO 6507-1에 따라 상온 및 200°C에서 비커스 다이아몬드 압입(HV3)을 사용하여 측정.
- 마모 및 마찰 시험: ASTM G99-05에 따라 건식 슬라이딩, 왕복 운동 모드(구-평판 구성)의 볼-온-디스크 마찰계를 사용하여 수행. 상온 및 200°C에서 6mm 알루미나 볼 상대면, 15N 하중, 0.1m/s 슬라이딩 속도, 총 500m 슬라이딩 거리로 시험 수행. 마찰 계수(COF)는 연속적으로 기록됨.
- 마모율 측정: 3D 레이저 스캐닝 공초점 현미경을 사용하여 마모 트랙 부피 손실 결정. 비마모율(w)은 방정식 (1): w = V / (s x F)를 사용하여 계산됨.
- 마모 표면/표면하 분석: 마모 메커니즘을 결정하기 위해 SEM/EDS 및 OM을 통한 단면 분석 사용.
연구 주제 및 범위:
본 연구는 새로운 Al80Mg10Si5Cu5 다성분 합금의 마찰학적 특성(마찰 및 마모)을 기존 AlSi9Cu3 합금과 비교하는 데 중점을 두었습니다. 범위는 다음과 같습니다:
- HPDC 주조 상태 표면층(스킨)이 마모 및 마찰에 미치는 영향 평가.
- 특정 용체화 열처리(TT)가 Al80Mg10Si5Cu5 합금의 마찰학적 성능에 미치는 영향 평가.
- 고온(200°C)이 상온(RT)과 비교하여 마찰, 마모율 및 마모 메커니즘에 미치는 영향 조사.
- 다른 조건에서 합금의 미세구조, 상 및 경도 특성화.
- 시험은 특정 BOD 매개변수(15N 하중, 0.1m/s 속도, 알루미나 상대면)를 사용한 건식 슬라이딩 조건으로 제한됨.
6. 주요 결과:
주요 결과:
- 경도: 새로운 Al80Mg10Si5Cu5 합금은 주조 상태 및 열처리(TT) 상태 모두에서, 상온(RT) 및 200°C 모두에서 기준 AlSi9Cu3 합금보다 높은 경도를 보였습니다. 표면층(스킨)은 미세한 미세구조로 인해 내부 재료보다 지속적으로 약간 더 높은 경도를 나타냈습니다. TT 조건은 Al80Mg10Si5Cu5 합금의 주조 상태에 비해 낮은 경도를 초래했습니다.
- 마찰 (COF): 상온에서 두 합금(주조 상태)은 약 0.37-0.39의 유사한 정상 상태 COF 값을 보였습니다. 200°C에서는 상당한 차이가 나타났습니다: Al80Mg10Si5Cu5는 상대적으로 낮은 COF(주조 상태 약 0.41-0.42, TT 약 0.50-0.53)를 유지한 반면, AlSi9Cu3은 훨씬 높은 COF(스킨 포함 시 ~0.64, 스킨 없을 시 ~0.80)를 보였습니다. 표면 스킨의 존재는 일반적으로, 특히 초기 단계에서 약간 낮은 COF 값을 초래했습니다. TT-Al80Mg10Si5Cu5는 200°C에서 주조 상태 버전보다 높은 COF를 보였습니다. 모든 시험은 전형적인 3단계 마찰 곡선을 나타냈습니다(초기 안정화 단계가 억제된 200°C 제외).
- 마모율: Al80Mg10Si5Cu5 합금은 AlSi9Cu3보다 훨씬 우수한 내마모성을 보였습니다. 상온에서 스킨이 있는 주조 상태 Al80Mg10Si5Cu5가 가장 낮은 마모율(4.9 x 10⁻⁴ mm³/N·m)을 나타냈습니다. 스킨을 제거하면 주조 상태 Al80Mg10Si5Cu5의 경우 약 50%, AlSi9Cu3의 경우 약 57% 마모가 증가했습니다. 200°C에서 Al80Mg10Si5Cu5의 내마모성 이점은 더욱 두드러져, AlSi9Cu3보다 약 10배 낮은 마모율을 보였습니다(예: 스킨 없는 샘플의 경우 4.4 x 10⁻³ 대 44.8 x 10⁻³ mm³/N·m). 표면 스킨은 두 온도 모두에서 지속적으로 마모율을 감소시켰습니다. 특히, 열처리(TT)는 상온 및 200°C 모두에서 주조 상태와 비교하여 Al80Mg10Si5Cu5 합금의 마모율을 증가시켰습니다.
- 마모 메커니즘: 주조 상태 Al80Mg10Si5Cu5의 경우, 상온 및 200°C 모두에서 연마 마모가 지배적인 마모 메커니즘이었으며, 이는 경미한 마모를 나타냅니다. TT-Al80Mg10Si5Cu5의 경우, 일부 연성 박리와 결합된 연마 마모가 관찰되었으며, 상온에서는 더 많은 균열을 동반한 경미한 마모로, 200°C에서는 경미-심각한 마모로 분류되었습니다. AlSi9Cu3 합금은 상온에서 연성 박리를 동반한 연마 마모(경미-심각한 징후)를 보였고, 200°C에서는 주로 심각한 연성 박리를 나타냈습니다. SEM/EDS 분석은 관찰된 마모 거동에서 미세구조(더 미세한 스킨), 상(Mg2Si, Al₂Cu, Al₂CuMg), 산화 및 파편 형성의 역할을 확인했습니다.
- 상대 볼 분석: 모든 시험에서 알루미나 상대 볼로의 재료 이동(응착)이 관찰되었으며, 이는 200°C에서, 특히 AlSi9Cu3 합금의 경우 더 중요했습니다.
그림 이름 목록 (Figure Name List):
- Fig. 1. Detail of tribometer employment and their components.
- Fig. 2. Detail of wearing surface topography.
- Fig. 3. XRD analysis of as-cast A180Mg10Si5Cu5 alloy.
- Fig. 4. XRD analysis of heat-treated A180Mg10Si5Cu5 alloy.
- Fig. 5. Analyzed phases in as-cast A180Mg10Si5Cu5 alloy.
- Fig. 6. Surface cast layer backscattered SEM images (x400 augmentation) of as-cast A180Mg10Si5Cu5 alloy.
- Fig. 7. Prepared sample backscattered SEM images (x400 augmentation) of as-cast A180Mg10Si5Cu5 alloy.
- Fig. 8. Surface cast layer sample SEM images (x400 augmentation) of the heat-treated A180Mg10Si5Cu5 alloy.
- Fig. 9. Inner region sample SEM images (x400 augmentation) of the heat-treated A180Mg10Si5Cu5 alloy.
- Fig. 10. Outside region optical microscopy images (x200 augmentation) of as-cast AlSi9Cu3 alloy.
- Fig. 11. Inner region optical microscopy images (x200 augmentation) of as-cast AlSi9Cu3 alloy.
- Fig. 12. Evolution of the coefficient of friction for the studied alloys at RT (0.1 m/s) with the surface layer.
- Fig. 13. Evolution of the coefficient of friction for the studied alloys at RT (0.1 m/s) without the surface layer.
- Fig. 14. Evolution of coefficient of friction for the experimental alloys at 200 °C (0,1 m/s) with the surface layer.
- Fig. 15. Evolution of coefficient of friction for the experimental alloys at 200 °C (0,1 m/s) without the surface layer.
- Fig. 16. Wear profiles at RT and 200 °C.
- Fig. 17. Material track area after BOD tests. (a) As-cast A180Mg10Si5Cu5 RT, (b) TT-A180Mg10Si5Cu5 RT, (c) As-cast AlSi9Cu3 RT, (d) As-cast A180Mg10Si5Cu5 200 °C, (e) TT-A180Mg10Si5Cu5 200 °C, (f) As-cast AlSi9Cu3 200 °C.
- Fig. 18. Material track thickness determination at RT: (a) As-cast A180Mg10Si5Cu5 RT, (b) TT-A180Mg10Si5Cu5 RT, (c) As-cast AlSi9Cu3 RT, and at 200 °C: (d) As-cast A180Mg10Si5Cu5, (e) TT-A180Mg10Si5Cu5, (f) As-cast AlSi9Cu3.
- Fig. 19. SEM images of worn surface tested at RT for as-cast A180Mg10Si5Cu5. (a), (b) and (c) = With surface layer at the magnification of×40, ×400 and x800. (d), (e) and (f) = Without surface layer at the magnification of×40, × 400 and x800.
- Fig. 20. SEM images of worn surface tested at RT for heat-treated A180Mg10Si5Cu5. (a), (b) and (c) = With surface layer at the magnification of×40, ×400 and x800. (d), (e) and (f) = Without surface layer at the magnification of×40, ×400 and x800.
- Fig. 21. SEM images of worn surface tested at RT for as-cast AlSi9Cu3. (a), (b) and (c) = With surface layer at the magnification of×40, ×400 and x800. (d), (e) and (f) = Without surface layer at the magnification of×40, × 400 and x800.
- Fig. 22. SEM images of worn surface for as-cast A180Mg10Si5Cu5. (a), (b) and (c) = With surface layer at the magnification of×40, ×400 and x800. (d), (e) and (f) = Without surface layer at the magnification of×40, ×400 and ×800 at 200 °C.
- Fig. 23. SEM images of worn surface for TT-A180Mg10Si5Cu5. (a), (b) and (c) = With surface layer at the magnification of×40, ×400 and x800. (d), (e) and (f) = Without surface layer at the magnification of×40, ×400 and ×800 at 200 °C.
- Fig. 24. SEM images of worn surface for as-cast AlSi9Cu3. (a), (b) and (c) = With skin at the magnification of×40, ×400 and x800. (d), (e) and (f) = Without skin at the magnification of×40, × 400, ×800 at 200 °C.
- Fig. 25. OM cross-section micrographs of the wear tracks tested at RT for as-cast A180Mg10Si5Cu5 at x100 (a), x200 (b), and ×500 (c) and as-cast AlSi9Cu3 at x100 (d), x200 (e) and ×500 (f).
- Fig. 26. OM cross-section micrographs of the wear tracks tested at 200 °C for as-cast A180Mg10Si5Cu5 at x100 (a), x200 (b), x500 (c), as-cast AlSi9Cu3 at ×100 (d), x200 (e) and ×500 (f).
7. 결론:
본 논문은 새로운 A180Mg10Si5Cu5 주조 합금의 마찰 및 마모 특성을 포괄적으로 조사하고, 상온 및 200°C에서 주조 상태 및 열처리 상태에서 AlSi9Cu3 주조 합금과 비교하였으며, 다이캐스팅 부품의 외부 스킨 효과를 포함하여 분석했습니다. 결론은 다음과 같습니다:
(1) →HPDC용으로 개발된 새로운 A180Mg10Si5Cu5 합금은 상온에서 표준 AlSi9Cu3 합금에 비해 향상된 내마모성(마모율 50% 이상 감소)을 특징으로 합니다. 이러한 개선은 표면 및 표면하 경도뿐만 아니라, 새로운 합금의 미세구조 유형 및 형태에 기인하며, 연마 마모가 주된 마모 메커니즘입니다. AlSi9Cu3 합금은 일부 연성 박리를 동반한 연마 마모를 보이며 더 높은 비마모율을 나타냈습니다. 상온에서 A180Mg10Si5Cu5 합금은 경미한 마모율을 보였고, AlSi9Cu3은 일부 심각한 마모 징후를 동반한 경미한 마모를 보였습니다.
(2) →200°C에서는 마모율과 COF 값이 더 높습니다. 표면층이 있는 주조 상태의 A180Mg10Si5Cu5 합금은 연마 마모를 보이며 다시 한번 가장 낮은 마모율을 나타냈고, 경미한 마모를 보였습니다. TT-A180Mg10Si5Cu5 합금은 주조 상태 A180Mg10Si5Cu5 합금과 비교하여 우세한 이차 연성 박리 마모 메커니즘과 함께 연마 마모를 나타냈으며, 일부 심각한 마모 징후를 동반한 경미한 마모를 보였습니다. 주조 상태 AlSi9Cu3 합금은 가장 높은 마모율(마모율 10배 감소)을 나타냈고 주로 연성 박리 메커니즘을 보여 심각한 마모를 나타냈습니다.
(3) →표면층이 있는 샘플은 더 높은 경도, 더 나은 미세구조 및 감소된 품질 결함으로 인해 낮은 COF 값과 비마모율을 나타냈습니다. HPDC 주조 부품의 가공을 피하는 것은 마모 조건 하에서 사용 중 성능을 향상시킬 수 있습니다.
(4) → 새롭게 개발된 합금은 알루미늄 드럼 브레이크를 위한 비용 효율적이고 낮은 CO2 대안으로서의 가능성을 보여줍니다. 이차 알루미늄 합금으로부터 얻어진 성능 특성으로 인해 이점을 제공하며, 이는 또한 철보다 가벼워 잠재적으로 연비를 향상시킬 수 있습니다. 또한, 생산에 사용된 HPDC 공정은 다른 장점들 중에서도 사이클 타임을 단축시키는 결과를 가져옵니다.
8. 참고문헌 (References):
- [References] - (참고 문헌 목록은 원문 그대로 유지합니다.)
- [1] P. Sharma, V.K. Dwivedi, S.P. Dwivedi, Development of high entropy alloys: a review, Mater. Today: Proc. 43 (1) (2021) 502–509, https://doi.org/10.1016/j.matpr.2020.12.023.
- [2] S. Salifu, P.A. Olubambi, Effects of fabrication techniques on the mechanical properties of high entropy alloys: a review, Int. J. Lightweight Mater Manufact (2023) 13–53, https://doi.org/10.1016/j.ijlmm.2023.08.001.
- … (이하 모든 참고 문헌은 원문과 동일하게 유지) …
- [96] G. Plasensia, A.T. Utigard, High temperature oxidation mechanism of dilute copper aluminium alloys, Corrosion Sci. 47 (2005) 1149–1163, https://doi.org/10.1016/j.corsci.2004.06.031.
9. 저작권:
- 본 자료는 "Ester Villanueva, Iban Vicario, Joseba Albizuri, Gurutze Arruebarrena, Teresa Guraya"의 논문입니다. "[Wear properties of a new Al80Mg10Si5Cu5 multicomponent alloy]" 논문을 기반으로 합니다.
- 논문 출처: https://doi.org/10.1016/j.wear.2024.205585
본 자료는 상기 논문을 기반으로 요약되었으며, 상업적 목적의 무단 사용을 금지합니다.
Copyright © 2025 CASTMAN. All rights reserved.