본 페이지는 2018년 International Journal of Metalcasting에 게재된 연구 논문 "모듈러 설계 방식을 사용한 경량 다이캐스팅 금형의 초기 연구(AN INITIAL STUDY OF A LIGHTWEIGHT DIE CASTING DIE USING A MODULAR DESIGN APPROACH)"를 요약한 것입니다. 본 연구는 에너지 소비를 줄이고 고압 다이캐스팅(HPDC) 공정의 효율성을 향상시키기 위한 모듈러 경량 다이캐스팅 금형 설계의 잠재력을 조사합니다.
1. 개요:
- 제목: AN INITIAL STUDY OF A LIGHTWEIGHT DIE CASTING DIE USING A MODULAR DESIGN APPROACH (모듈러 설계 방식을 사용한 경량 다이캐스팅 금형의 초기 연구)
- 저자: Sebastian Müller, Klaus Dilger, Anke Müller, Felix Rothe, Klaus Dröder
- 발행 연도: 2018년
- 발행 저널/학술 단체: International Journal of Metalcasting, Volume 12, Issue 4
- 키워드: 다이캐스팅, 공정 모델링, 금형 변형, 경량 설계, 모듈러 컨셉, 에너지 절감 (die casting, process modeling, die deflections, lightweight design, modular concept, energy reduction)
2. 연구 배경:
- 연구 주제의 사회적/학문적 맥락:
고압 다이캐스팅(HPDC)은 특히 독일 생산량의 약 70%를 차지하는 자동차 산업에서 중요한 산업 공정입니다. HPDC는 기하학적으로 복잡한 부품을 대량 생산하는 데 선호됩니다. 그러나 기존의 HPDC 금형 설계 및 제조는 상당한 단점을 가지고 있습니다. 다이캐스팅 금형은 일반적으로 각 부품마다 맞춤 설계 및 절삭 가공 방식으로 제조되며 표준화가 부족합니다. 설계 개선은 설계자의 경험과 수치 해석 방법에 의해 점진적으로 발전해 왔습니다. 기존 방식은 주조 공정 중 높은 안정성을 확보하기 위해 금형을 대형으로 설계하는 것을 특징으로 합니다. - 기존 연구의 한계:
현재 다이캐스팅 금형 기술은 다음과 같은 여러 가지 한계에 직면해 있습니다.- 높은 투자 비용: 공정을 대량 생산에만 국한시키는 요인입니다.
- 높은 에너지 소비: 대형 금형 작동은 상당한 에너지 소비와 느린 금형 온도 제어를 초래합니다.
- 높은 총 중량: 견고하고 무거운 다이캐스팅 기계 및 구동 장치가 필요합니다.
- 에너지 집약적인 생산: 담금질 및 템퍼링된 공구강은 높은 CO₂ 배출량을 유발합니다.
- 재료 낭비: 다이캐스팅 금형, 특히 몰드 베이스는 사용 후 폐기되는 경우가 많아 재료 낭비에 기여합니다.
- 시간 및 재료 집약적인 가공: 공구강으로 성형 프레임을 제조하는 것은 시간과 비용이 많이 드는 공정입니다.
- 연구의 필요성:
본 연구는 기존 다이캐스팅 금형 설계 및 제조의 한계를 극복해야 할 필요성에 의해 동기 부여되었습니다. 다음과 같은 사항을 개선해야 할 필요성이 분명히 존재합니다.- 설계 및 제조 공정 간소화: 다이캐스팅 금형 제작과 관련된 시간과 비용을 절감합니다.
- 제품 변형의 신속한 구현: 개별화된 제품에 대한 수요 증가에 맞춰 주조 생산의 유연성을 높입니다.
- 에너지 효율성 향상: 금형 예열 및 작동 중 에너지 소비를 줄입니다.
- 재료 소비 감소: 경량 설계를 탐구하여 재료 사용량과 낭비를 최소화합니다.
3. 연구 목적 및 연구 질문:
- 연구 목적:
주요 연구 목적은 모듈러 설계 방식을 사용한 경량 다이캐스팅 금형에 대한 초기 연구를 수행하는 것입니다. 여기에는 이 새로운 금형 설계의 기본적인 열적 및 구조적 특성을 분석하여 타당성과 잠재적 이점을 평가하는 것이 포함됩니다. 궁극적인 목표는 설계 및 제조 시간과 비용을 절감하는 보다 효율적이고 유연한 다이캐스팅 금형 설계 원칙을 위한 길을 여는 것입니다. - 주요 연구 질문:
본 연구는 다음과 같은 주요 질문에 대한 답변을 구합니다.- 모듈러 경량 다이캐스팅 금형의 에너지 소비량은 예열 및 작동 중 기존 다이캐스팅 금형과 비교하여 어떻습니까?
- 주조 공정 중 모듈러 경량 다이캐스팅 금형의 변형 및 응력 특성은 무엇이며, 기존 금형과 어떻게 비교됩니까?
- 모듈러 경량 설계는 일반적인 HPDC 공정 하중에서 충분한 구조적 무결성 및 치수 정확도를 유지할 수 있습니까?
- 에너지 효율성 및 구조적 성능 측면에서 모듈러 경량 다이캐스팅 금형 설계를 구현할 때 잠재적인 장점과 과제는 무엇입니까?
- 연구 가설:
경량 구조 및 모듈성의 설계 원칙에 따라 본 연구는 다음과 같은 가설 하에 진행됩니다.- 모듈러 경량 다이캐스팅 금형은 질량과 재료 감소로 인해 기존 금형에 비해 예열 및 작동 중 에너지 소비가 현저히 낮을 것입니다.
- 경량 설계에서 강성과 재료가 감소함에 따라 주조 공정 중 금형의 계산된 변형 및 응력은 기존 금형에 비해 상당히 높을 것입니다.
- 잠재적으로 더 높은 변형 및 응력에도 불구하고 모듈러 경량 다이캐스팅 금형은 HPDC 공정에 적합한 수준의 치수 정확도와 구조적 무결성을 유지하도록 설계될 수 있습니다.
4. 연구 방법론:
- 연구 설계:
본 연구는 유한 요소 해석(FEA)을 사용하여 경량 모듈러 다이캐스팅 금형 컨셉의 성능을 기존 다이캐스팅 금형과 비교 평가하는 비교 연구 설계를 채택합니다. 두 금형 설계 모두 동일한 4mm 판재 HPDC 부품에 대해 모델링하여 열적 및 구조적 거동을 직접 비교할 수 있도록 했습니다. - 자료 수집 방법:
자료는 ANSYS 소프트웨어를 사용하여 수행된 수치 시뮬레이션을 통해 수집되었습니다. 시뮬레이션 모델은 다음을 사용하여 구축되었습니다.- CAD 데이터: 경량 모듈러 다이캐스팅 금형과 기존 다이캐스팅 금형 모두에 대한 CAD 모델을 만들었습니다. BUEHLER SC B53 다이캐스팅 기계의 고정 및 이동 플래튼에 대한 CAD 데이터는 제조업체에서 제공했습니다.
- 경계 조건: 열 및 기계적 해석 모두에 대한 경계 조건은 실제 생산 공정 매개변수 및 관련 문헌을 기반으로 신중하게 정의되었습니다. 이러한 조건은 논문의 표 1과 표 2에 자세히 설명되어 있습니다.
- 분석 방법:
유한 요소법을 사용하여 결합된 과도 열 및 구조 해석을 수행했습니다. 이 접근 방식을 통해 열 전달과 구조 역학의 동시 시뮬레이션이 가능하여 주조 공정 중 열하중과 기계적 응력 간의 상호 작용을 포착할 수 있습니다. 분석에는 다음이 포함되었습니다.- 열 해석: 과도 열 시뮬레이션을 수행하여 금형 온도 변화, 냉각 채널의 열 출력 및 예열 및 주조 사이클 중 에너지 소비를 분석했습니다.
- 구조 해석: 정적 구조 시뮬레이션을 수행하여 기계적 하중(잠금력, 사출 압력) 및 열하중을 포함한 다양한 하중 조건에서 금형 변형, 벽 두께 편차 및 등가 폰 미세스 응력을 평가했습니다.
- 연구 대상 및 범위:
본 연구는 특정 HPDC 부품인 4mm 두께의 판재에 초점을 맞췄습니다. 이 형상을 선택한 이유는 다음과 같습니다.- 변형 분석이 용이합니다.
- 성능을 실제 다이캐스팅 금형과 비교할 수 있습니다.
- 캐비티가 이동 금형 절반에만 위치하여 설계 및 분석이 단순화됩니다.
- 하중이 금형 중앙에 집중되어 있어 중요한 응용 분야를 나타냅니다.
5. 주요 연구 결과:
- 주요 연구 결과:
유한 요소 계산 결과 다음과 같은 주요 결과가 나타났습니다.- 에너지 절감: 모듈러 경량 다이캐스팅 금형은 기존 금형에 비해 예열 및 작동 중 에너지 소비량이 현저히 적었습니다. 총 에너지 요구량은 주조 로트 크기에 관계없이 약 5.2배 감소했습니다(그림 5). 평균 캐비티 온도 200°C까지 예열하는 데 경량 금형은 4.2 MJ의 열이 필요했고, 기존 금형은 17.3 MJ의 열이 필요했습니다(그림 3).
- 변형: 실온에서 하중을 가했을 때 경량 금형의 계산된 변형이 기존 금형보다 높았습니다(그림 6). 그러나 최대 벽 두께 편차의 차이는 약 0.05mm로 비교적 작았습니다. 작동 온도에서 두 설계 컨셉 간의 편차는 판 중앙에서 약 0.05mm로 유지되었습니다(그림 7). 흥미롭게도 열 및 기계적 하중(설정 #III)을 결합한 조건에서 경량 설계는 기존 설계에 비해 벽 두께 편차가 더 적게 나타났습니다(그림 8).
- 응력: 등가 폰 미세스 응력 분석 결과, 경량 하중 지지 금속 구조 요소의 노치, 특히 주변 영역의 반경 부분에서 높은 응력 집중이 나타났습니다(그림 10b). 최적화된 3D 트러스로 구성된 공간 프레임에서도 국부적으로 높은 응력이 관찰되었습니다(그림 11).
- 시간-온도 곡선: 예열 및 주조 사이클 중 두 금형 설계의 시간-온도 곡선은 유사했습니다(그림 3 및 그림 4). 기존 금형은 경량 금형(1558초)에 비해 약간 빠른 가열 시간(200°C 도달 시간 965초)을 보였습니다. 이는 질량이 더 적음에도 불구하고 경량 금형의 냉각 채널 표면적이 더 작기 때문으로 분석되었습니다.
- 통계적/정성적 분석 결과:
- 정량적 에너지 절감: 시뮬레이션은 경량 모듈러 설계의 상당한 에너지 절감 잠재력을 정량적으로 입증했으며, 다양한 주조 로트 크기에 걸쳐 총 에너지 요구량에서 약 5.2배의 일관된 감소율을 보였습니다.
- 정성적 변형 거동: 변형 패턴에 대한 정성적 분석 결과, 경량 금형은 실온에서 기계적 하중 하에서 더 높은 변형을 보였지만 작동 온도에서는 거동이 바뀌었습니다. 결합된 열 및 기계적 하중 하에서 경량 설계는 기존 금형에 비해 벽 두께 편차가 감소했습니다.
- 응력 분포: 응력 분석은 경량 설계에서 응력 집중이 심한 영역, 특히 하중 지지 구조의 노치 및 반경 부분과 공간 프레임 내에서 정성적으로 식별했습니다.
- 자료 해석:
- 에너지 효율성: 결과는 모듈러 경량 다이캐스팅 금형이 HPDC 공정에서 에너지 소비를 크게 줄일 수 있다는 가설을 강력하게 뒷받침합니다. 이러한 감소는 주로 가열에 필요한 에너지가 적은 경량 설계의 낮은 질량에 기인합니다.
- 구조적 성능: 경량 금형이 특정 시나리오에서 더 높은 변형과 응력을 보였지만 전체 변형은 비교적 작고 기존 금형과 유사한 수준으로 유지되었습니다. 실제 주조 조건(설정 #III)에서 경량 설계는 변형 성능이 향상된 것으로 나타났습니다. 응력 분석은 신중한 재료 선택 및 구조 최적화가 필요한 영역을 강조했습니다.
- 모듈러 설계 타당성: 초기 시뮬레이션 결과는 모듈러 경량 설계 컨셉이 타당하며 다이캐스팅 금형의 효율성과 유연성을 향상시킬 수 있는 가능성이 있음을 시사합니다.
- 그림 목록:
- 그림 1. 경량 설계 금형의 단면도 (a) 및 등각 투영도 (b).
- 그림 2. 유한 요소 모델의 경계 조건 그림; (a) 기존 다이캐스팅 금형, (b) 경량 설계 다이캐스팅 금형; 1-8번 주석은 표 1 참조.
- 그림 3. 경량 및 기존 다이캐스팅 금형의 예열 중 냉각 채널의 계산된 과도 열 출력 및 평균 캐비티 온도.
- 그림 4. 20회 주조 사이클 후 계산된 과도 열 출력 및 평균 캐비티 온도.
- 그림 5. 세 가지 다른 주조 로트 크기에 대한 총 에너지 요구량.
- 그림 6. 경계 조건 I에 따른 벽 두께 편차의 그래프 표현 (표 3 참조).
- 그림 7. 경계 조건 II에 따른 벽 두께 편차의 그래프 표현 (표 3 참조).
- 그림 8. 경계 조건 II에 따른 벽 두께 편차의 그래프 표현 (표 3 참조).
- 그림 9. 기존 및 경량 다이캐스팅 금형을 장착한 고압 다이캐스팅 기계 기능 장치의 y 방향 계산된 변위; #Ill, 표 3에 따른 경계 조건; 40배 확대.
- 그림 10. 경량 설계 금형의 단면에서 등가 응력의 그래프 시각화.
- 그림 11. 경량 설계 금형의 공간 프레임에서 등가 응력의 그래프 시각화.
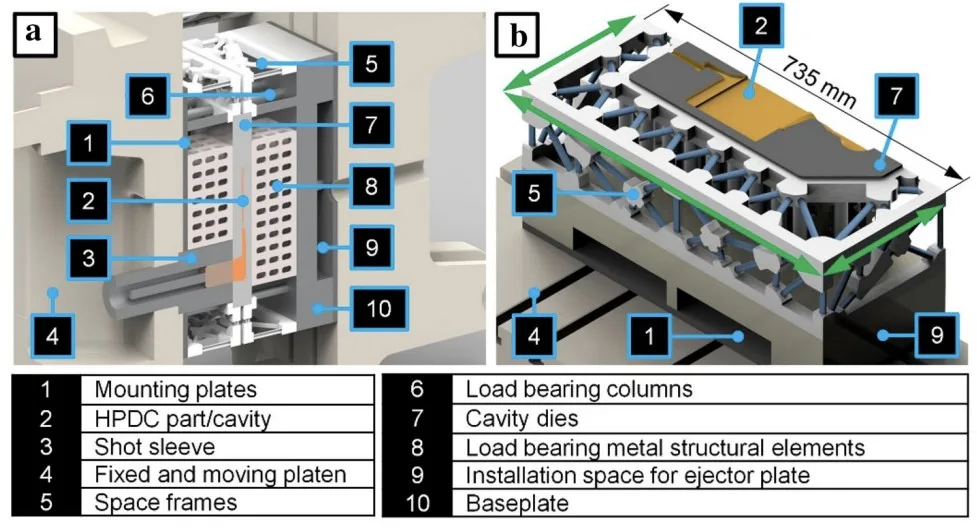
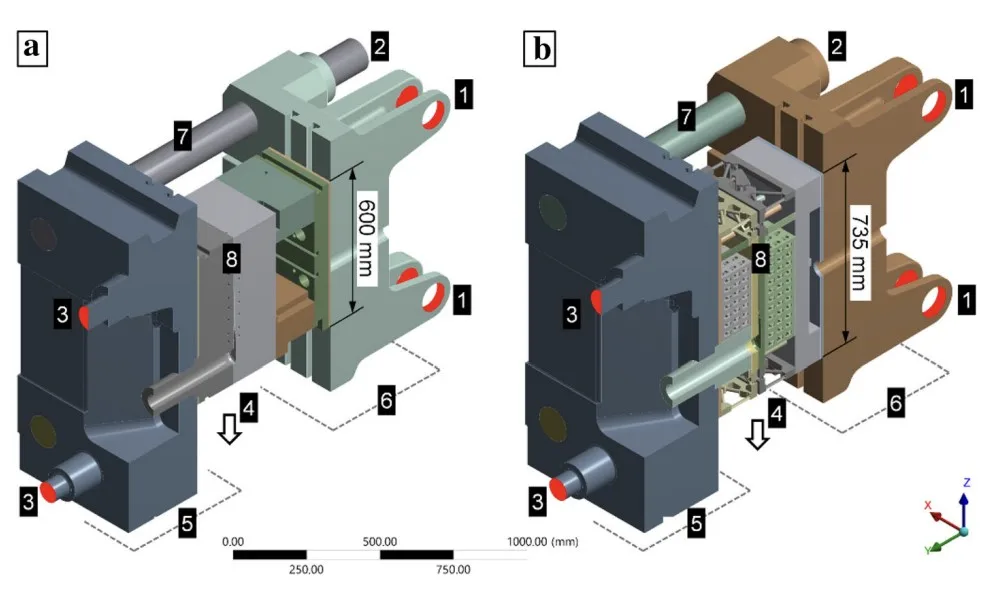
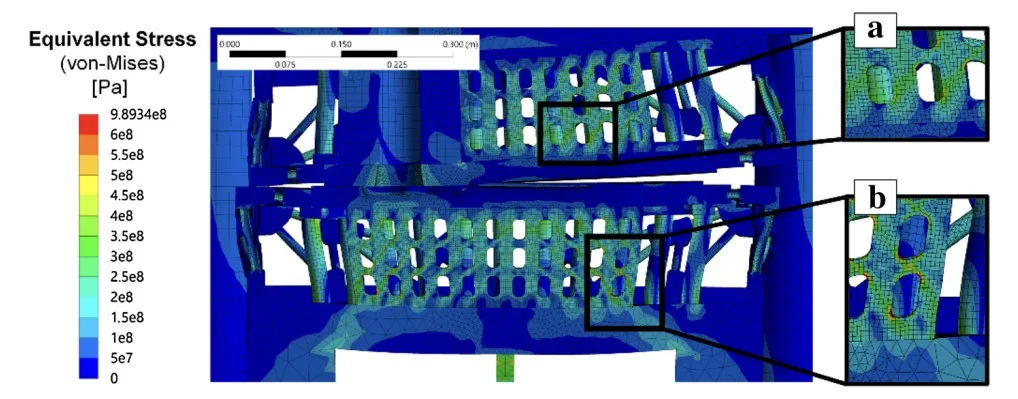
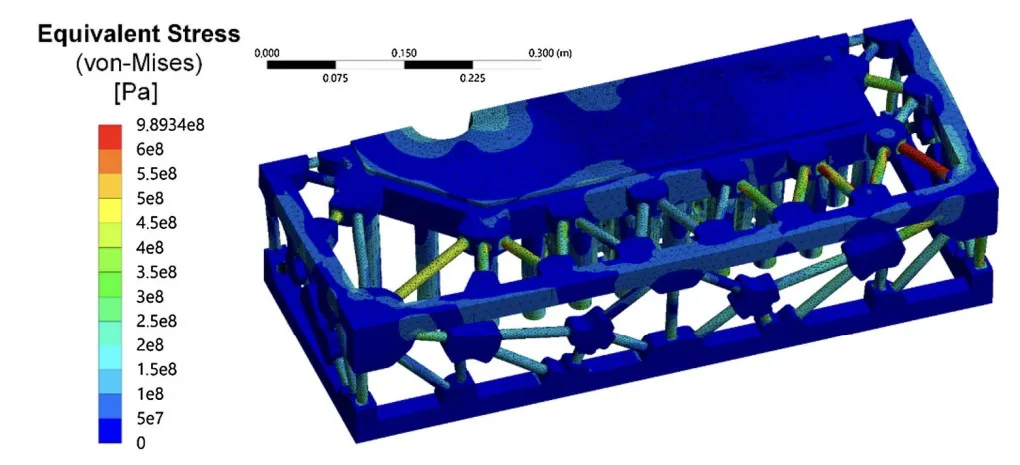
6. 결론 및 논의:
- 주요 결과 요약:
본 초기 연구는 모듈러 경량 다이캐스팅 금형 설계가 HPDC 공정에서 에너지 소비를 크게 줄일 수 있는 잠재력을 입증했습니다. 시뮬레이션 결과는 기존 금형에 비해 총 에너지 요구량이 약 5.2배 감소하는 것으로 나타났습니다. 계산된 변형 및 응력은 경량 설계에서 더 높았지만 관리 가능한 범위 내에 유지되었으며, 실제 주조 조건에서는 변형 성능이 향상되기도 했습니다. - 연구의 학문적 의의:
본 연구는 경량 모듈러 다이캐스팅 금형의 타당성 및 성능 특성에 대한 귀중한 초기 통찰력을 제공합니다. 에너지 효율성과 모듈성에 초점을 맞춘 새로운 접근 방식을 탐구함으로써 다이캐스팅 금형 설계에 대한 학문적 이해에 기여합니다. 본 연구는 HPDC 맥락에서 경량 설계 원칙의 잠재력을 강조하고 이 분야의 추가 연구 및 개발을 위한 토대를 제공합니다. - 실용적 의미:
본 연구 결과는 다이캐스팅 산업에 중요한 실용적 의미를 갖습니다.- 에너지 비용 절감: 경량 금형의 상당한 에너지 절감 잠재력은 특히 에너지 가격 상승과 환경 문제에 대한 우려가 커지는 상황에서 다이캐스팅 회사의 운영 비용을 크게 절감할 수 있습니다.
- 소량 로트 크기: 낮은 에너지 소비와 잠재적으로 감소된 금형 제조 비용은 HPDC를 소량 생산 로트 크기에 대해 경제적으로 더 타당하게 만들어 공정의 유연성과 적용 가능성을 높일 수 있습니다.
- 지속 가능한 제조: 에너지 소비 및 재료 사용량 감소는 보다 지속 가능하고 환경 친화적인 다이캐스팅 공정에 기여합니다.
- 낮은 전력 요구 사항: 경량 금형에서 냉각 채널의 열 출력이 감소하면 전력 요구 사항이 낮은 온도 제어 장치를 사용할 수 있음을 시사합니다.
- 연구의 한계:
본 연구는 초기 조사이며 다음과 같은 여러 가지 한계가 있습니다.- 시뮬레이션 기반 연구: 결과는 수치 시뮬레이션을 기반으로 하며 실제 주조 시나리오에서 정확성과 적용 가능성을 확인하려면 실험적 검증이 필요합니다.
- 특정 형상 및 공정 조건: 분석은 특정 4mm 판재 형상 및 공정 조건 세트에 대해 수행되었습니다. 다른 부품 형상 및 주조 매개변수에 대한 결과의 일반화 가능성은 추가 조사가 필요합니다.
- 단순화된 경계 조건: 인터페이스 열 전달 계수 및 슬라이딩에 대한 무마찰 가정과 같은 특정 경계 조건은 데이터 제한으로 인해 단순화되었습니다. 정확도 향상을 위해서는 보다 정교한 모델과 실험 데이터가 필요합니다.
- 유효 캐비티 압력 결합: 유효 캐비티 압력이 시뮬레이션에서 재료 응고와 동적으로 결합되지 않아 변형 및 응력 예측의 정확도에 영향을 미칠 수 있습니다.
- 변형을 넘어서는 부품 품질: 본 연구는 주로 금형 변형에 초점을 맞췄습니다. 다공성 및 기계적 특성과 같은 HPDC 부품 품질의 다른 측면은 직접 평가하지 않았습니다.
7. 향후 후속 연구:
- 후속 연구 방향:
향후 연구는 모듈러 경량 다이캐스팅 금형 컨셉을 더욱 발전시키고 검증하기 위해 다음과 같은 방향에 초점을 맞춰야 합니다.- 실험적 검증: 프로토타입 모듈러 경량 다이캐스팅 금형을 제조하고 실험적 주조 시험을 수행하여 시뮬레이션 결과를 검증하고 실제 생산 환경에서의 성능을 평가합니다.
- 구조 최적화: 응력 집중을 줄이고 변형을 최소화하기 위해 경량 구조, 특히 하중 지지 금속 구조 요소 및 공간 프레임을 추가로 최적화합니다.
- 고급 금형 재료: 열 관리 및 구조적 무결성을 더욱 향상시키기 위해 열전도율과 인장 강도가 더 높은 고급 금형 재료의 사용을 조사합니다.
- 고급 온도 제어: 금형 온도 균일성 및 사이클 시간을 최적화하기 위해 등각 냉각 채널과 같은 고급 금형 온도 제어 방법을 탐구하고 통합합니다.
- 제조 컨셉: 모듈러 경량 다이캐스팅 금형의 비용 효율적인 생산을 위한 제조 컨셉 및 전략을 개발하고, 설계의 특정 요구 사항을 고려합니다.
- 추가 탐구가 필요한 영역:
다음 영역에 대한 추가 탐구가 필요합니다.- 실제 다이캐스팅 금형 구현 및 테스트: 시뮬레이션을 넘어 실제 구현 및 테스트로 나아가는 것은 컨셉의 실제적인 타당성을 평가하는 데 매우 중요합니다.
- HPDC 부품 품질 평가: 치수 정확도, 표면 조도 및 기계적 특성을 포함하여 경량 금형을 사용하여 생산된 HPDC 부품 품질에 대한 포괄적인 평가.
- 슬라이더 및 복잡한 형상 고려: 산업 응용 분야에서 흔히 사용되는 슬라이더 및 언더컷이 있는 보다 복잡한 부품 형상을 수용하도록 설계 컨셉을 확장합니다.
- 제조 비용 분석: 모듈러 경량 금형의 생산 비용을 기존 금형과 비교하고 전반적인 경제적 이점을 평가하기 위해 자세한 제조 비용 분석을 수행합니다.
- 캐비티 압력 및 응고 결합: 변형 및 응력 예측의 정확도를 향상시키기 위해 캐비티 압력을 재료 응고와 동적으로 결합하는 보다 정교한 시뮬레이션 접근 방식을 구현합니다.
8. 참고 문헌:
- H. Lickfett, NE-Metallgießereien in Deutschland: Strukturentwicklung und Strategische Investitionen pro Standort Deutschland (Leichtbau in Guss, Saarbru¨cken, 2013)
- R. Scho¨ngrundner, W. Ecker, S. Marsoner et al., Development of a simulation aided design strategy for casting die frames. In: 9th International Tooling Conference, Leoben, Austria, (2012)
- C. Brecher, D. O¨ zdemir (eds.), Integrative Production Technology: theory and Applications (Springer, Cham, 2017)
- Y. Queudeville, T. Ivanov, C. Nußbaum et al., Decision and design methodologies for the lay-out of modular dies for high-pressure-die-cast-processes. in Materials Science Forum, (RWTH Aachen, Aachen, 2009), pp. 345–348
- B. Hummler-Schaufler, C. Schlumpberger, Produktentwicklung auf hohem Niveau. Druckgusspraxis 1, 39–42 (2004)
- Y. Queudeville, U. Vroomen, A. Bu¨hrig-Polaczek, Modularization methodology for high pressure die casting dies. Int. J. Adv. Manuf. Technol. 71(9–12), 1677–1686 (2014). https://doi.org/10.1007/s00170-013-5582-9
- O. Eitelwein, J. Weber, Unternehmenserfolg durch Modularisierung von Produkten, Prozessen und Supply Chains: WHU Benchmarking-Studie Modularisierung (Books on Demand, Norderstedt, 2011)
- J.H. Mikkola, O. Gassmann, Managing modularity of product architectures: toward an integrated theory. IEEE Trans. Eng. Manag. 50(2), 204–218 (2003). https://doi.org/10.1109/TEM.2003.810826
- H. Goehler, J. Meinert, T. Doll et al., Steel hollow sphere structures for energy efficient foaming tools. in Cellular Materials—CellMat (International Congress Center Dresden, Dresden, Germany, 2014)
- M.R. Barone, D.A. Caulk, A new method for thermal analysis of die casting. Trans. ASME J. Heat Transf. 115, 284–293 (1993)
- K. Hegde, H. Ahuett-Garza, G. Padiyar, NADCASponsored research: FEM analysis of die casting die deflections: Part I—modeling and simulation. in 18th International Die Casting Congress and Exposition, IN, USA, (1995)
- H. Ahuett-Garza, K. Hegde, R.A. Miller et al., NADCA-sponsored research: FEM analysis of die casting die deflections: Part ll—results. in 18th International Die Casting Congress and Exposition, IN, USA, (1995)
- H. Ahuett-Garza, R.A. Miller, The effects of heat released during fill on the deflections of die casting dies. J. Mater. Process. Technol. 142(3), 648–658 (2003). https://doi.org/10.1016/S0924-0136(03)00685-X
- A. Long, D. Thornhill, C. Armstrong et al., Stress correlation between instrumentation and simulation analysis of the die for high pressure die casting. Int. Metalcast 7(2), 27–41 (2013). https://doi.org/10.1007/BF03355551
- S.I. Jeong, C.K. Jin, H.Y. Seo et al., Mold structure design and casting simulation of the high-pressure die casting for aluminum automotive clutch housing manufacturing. Int. J. Adv. Manuf. Technol. 228(12), 1599 (2015). https://doi.org/10.1007/s00170-015-7566-4
- H. Yamagata, Y. Shigenaga, S. Tanikawa et al., Deflection simulation of a die installed in a highpressure die-casting machine. Trans. Jpn. Soc. Mech. Eng. 79(806), 3920–3929 (2013)
- C.V. Camp, M. Farshchin, Design of space trusses using modified teaching–learning based optimization. Eng. Struct. 62–63, 87–97 (2014). https://doi.org/10.1016/j.engstruct.2014.01.020
- M. Farshchin, C.V. Camp, M. Maniat, Multi-class teaching–learning-based optimization for truss design with frequency constraints. Eng. Struct. 106, 355–369 (2016). https://doi.org/10.1016/j.engstruct.2015.10.039
- B. Yalc¸in, M. Koru, O. Ipek et al., Effect of injection parameters and vacuum on the strength and porosity amount of die-casted A380 alloy. Int. Metalcast 11(2), 195–206 (2017). https://doi.org/10.1007/s40962-016-0046-2
- G. Dour, M. Dargusch, C. Davidson et al., Development of a non intrusive heat transfer coefficient gauge and its application to high pressure die casting. Metall. Sci. Technol. 22(1), 16–21 (2004)
- Y. Cao, Z. Guo, S. Xiong, Determination of the metal/ die interfacial heat transfer coefficient of high pressure die cast B390 alloy. IOP Conf. Ser.: Mater. Sci. Eng. 33, 12010 (2012). https://doi.org/10.1088/1757-899X/33/1/012010
- Z. Guo, S. Xiong, S. Cho et al., Interfacial heat transfer coefficient between metal and die during high pressure die casting process of aluminum alloy. Front. Mech. Eng. China 2(3), 283–287 (2007). https://doi.org/10.1007/s11465-007-0049-z
- Z. Guo, S. Xiong, B. Liu et al., Understanding of the influence of process parameters on the heat transfer behavior at the metal/die interface in high pressure die casting process. Sci. China Ser. E-Technol. Sci. 52(1), 172–175 (2009). https://doi.org/10.1007/s11431-008-0295-2
- Z.-P. Guo, S.-M. Xiong, B.-C. Liu et al., Effect of process parameters, casting thickness, and alloys on the interfacial heat-transfer coefficient in the highpressure die-casting process. Metall. Mater. Trans. A 39(12), 2896–2905 (2008). https://doi.org/10.1007/s11661-008-9640-0
- A. Hamasaiid, G. Dour, M.S. Dargusch et al., Heattransfer coefficient and in-cavity pressure at the casting-die interface during high-pressure die casting of the magnesium alloy AZ91D. Metall. Mater. Trans. A 39(4), 853–864 (2008). https://doi.org/10.1007/s11661-007-9452-7
- G. Zhi-peng, X. Shou-mei, L. Bai-cheng et al., Determination of the heat transfer coefficient at metal– die interface of high pressure die casting process of AM50 alloy. Int. J. Heat Mass Trans. 51(25–26), 6032–6038 (2008). https://doi.org/10.1016/ j.ijheatmasstransfer.2008.04.029
- M. Ciofalo, I. Di Piazza, V. Brucato, Investigation of the cooling of hot walls by liquid water sprays. Int. J. Heat Mass Trans. 42(7), 1157–1175 (1999). https://doi.org/10.1016/S0017-9310(98)00250-6
- G.W. Liu, Y.S. Morsi, B.R. Clayton, Characterisation of the spray cooling heat transfer involved in a high pressure die casting process. Int. J. Therm. Sci. 39(5), 582–591 (2000). https://doi.org/10.1016/S1290-0729(00)00207-6
- A.S. Sabau, R.B. Dinwiddie, Characterization of spray lubricants for the high pressure die casting processes. J. Mater. Process. Technol. 195(1–3), 267–274 (2008). https://doi.org/10.1016/j.jmatprotec.2007.05.021
- J.H. Hattel, P.N. Hansen, A 1-D analytical model for the thermally induced stresses in the mold surface during die casting. Appl. Math. Model. 18(10), 550–559 (1994). https://doi.org/10.1016/0307-904X(94)90140-6
- S. Mu¨ller, Ermittlung der Lebensdauer von Aluminium-Druckgießformen aufgrund thermischer Ermu¨dung. Zugl.: Braunschweig, Techn. Univ., Diss., 2015. Forschungsberichte des Instituts fu¨r Fu¨ge- und Schweißtechnik, Shaker, Aachen, 40 (2015)
- M. Ayabe, T. Nagaoka, K. Shibata et al., Effect of high thermal conductivity die steel in aluminum casting. Int. Metalcast 2(2), 47–55 (2008). https://doi.org/10.1007/BF03355427
- E. Kaschnitz, P. Hofer, W. Funk, Thermophysikalische Daten eines Warmarbeitsstahls mit hoher Wa¨rmeleitfahigkeit. GIESSEREI 97(9), 46–49 (2010)
- A. Armillotta, R. Baraggi, S. Fasoli, SLM tooling for die casting with conformal cooling channels. Int. J. Adv. Manuf. Technol. 71(1–4), 573–583 (2014). https://doi.org/10.1007/s00170-013-5523-7
- T. Kimura, H. Yamagata, S. Tanikawa, FEM stress analysis of the cooling hole of an HPDC die. IOP Conf. Ser.: Mater. Sci. Eng. 84, 12052 (2015). https://doi.org/10.1088/1757-899X/84/1/012052
- H. Hu, F. Chen, X. Chen et al., Effect of cooling water flow rates on local temperatures and heat transfer of casting dies. J. Mater. Process. Technol. 148(1), 57–67 (2004). https://doi.org/10.1016/j.jmatprotec.2004.01.040
- T. Kim, K. Jin, N. Kim et al., Numerical analysis and optimal design to reduce residual stresses and deformations of die casting baseplate after ejection. J. Mech. Sci. Technol. 29(7), 2949–2956 (2015). https://doi.org/10.1007/s12206-015-0625-9
- D. Klobcˇar, L. Kosec, B. Kosec et al., Thermo fatigue cracking of die casting dies. Eng. Fail. Anal. 20, 43–53 (2012). https://doi.org/10.1016/j.engfailanal.2011.10.005
- D. Klobcˇar, J. Tusˇek, B. Taljat, Thermal fatigue of materials for die-casting tooling. Mater. Sci. Eng. A 472(1–2), 198–207 (2008). https://doi.org/10.1016/j.msea.2007.03.025
- S. Naimi, S.M. Hosseini, Tool steels in die-casting utilization and increased mold life. Adv. Mech. Eng. 7(1), 286071 (2014). https://doi.org/10.1155/2014/286071
9. 저작권:
*본 자료는 Sebastian Müller, Klaus Dilger, Anke Müller, Felix Rothe, Klaus Dröder의 논문: AN INITIAL STUDY OF A LIGHTWEIGHT DIE CASTING DIE USING A MODULAR DESIGN APPROACH (모듈러 설계 방식을 사용한 경량 다이캐스팅 금형의 초기 연구)를 기반으로 합니다.
*논문 출처: https://doi.org/10.1007/s40962-018-0218-3
본 자료는 상기 논문을 기반으로 요약되었으며, 상업적 목적으로 무단 사용하는 것을 금지합니다.
Copyright © 2025 CASTMAN. All rights reserved.