본 논문 요약은 ['THE ANNALS OF "DUNAREA DE JOS" UNIVERSITY OF GALATI']에서 발행한 ['LEAN MANUFACTURING - PROCESS AUTOMATION AND ELIMINATION OF PRODUCTION LOSSES IN ROMANIAN AUTOMOTIVE INDUSTRY'] 논문을 기반으로 작성되었습니다.
1. 개요:
- 제목: LEAN MANUFACTURING - PROCESS AUTOMATION AND ELIMINATION OF PRODUCTION LOSSES IN ROMANIAN AUTOMOTIVE INDUSTRY (린 생산 방식 - 루마니아 자동차 산업의 공정 자동화 및 생산 손실 제거)
- 저자: Ovidiu AMBRUS
- 발행 연도: 2017년
- 발행 저널/학회: THE ANNALS OF "DUNAREA DE JOS" UNIVERSITY OF GALATI, FASCICLE IX. METALLURGY AND MATERIALS SCIENCE
- 키워드: 린 생산 방식, 자동차 산업, 공정 자동화
![Fig. 1. Lean Manufacturing pillars [1]](https://castman.co.kr/wp-content/uploads/image-732-png.webp)
2. 초록 또는 서론
본 논문은 제조 기업에 있어 가장 중요한 경영 방법론으로 자리매김한 린 생산 방식의 중요성을 다룹니다. "식스 시그마" 품질 도구와 함께 사용되는 린 생산 방식은 도요타 생산 시스템에 기반하며, 1995년 Womack과 Jones에 의해 서구 기업에 맞게 적용되어 기본적인 운영 역량을 강조합니다. 린 생산 방식은 유연한 조립 셀 또는 라인, 복잡한 작업, 숙련된 작업자, 우수한 제품 품질, 다양한 호환 부품, 필수적인 최고 품질, 생산 공정 개선을 통한 비용 절감, 국제 시장 및 글로벌 경쟁력을 포괄합니다 [2]. TRW Automotive는 가죽 제품 준비 분야에서 이러한 개념을 실제로 적용한 사례입니다.
본 논문은 린 생산 방식을 제조 시스템 내 낭비("Muda") 제거를 위한 체계적인 방법으로 소개하며, 과부하("Muri") 및 불균일한 작업 부하("Mura")로 인한 낭비 또한 고려합니다. 제품 또는 서비스를 소비하는 고객의 관점에서 "가치"는 고객이 기꺼이 비용을 지불하고자 하는 모든 행위 또는 공정으로 정의됩니다. 최소 비용으로 제조하는 생산 철학은 손실을 제거하여 고객 주문과 제품 인도 사이의 리드 타임을 단축하는 것을 목표로 합니다. LEAN 원칙의 구현은 오늘날 비용 절감이 시장의 현실인 생산 환경에서 중요한 생존 전략이 되었습니다. 린 생산 방식의 핵심 기둥은 그림 1에 간략하게 설명되어 있습니다.
3. 연구 배경:
연구 주제 배경:
린 생산 방식 또는 린 생산은 제조 시스템 내에서 낭비("Muda")를 제거하는 데 초점을 맞춘 체계적인 방법론으로 정의됩니다. 이는 과부하("Muri") 및 불균일한 작업 부하("Mura")로 인해 발생하는 낭비까지 포함합니다. 고객의 관점에서 "가치"는 고객이 지불할 의사가 있는 행위 또는 프로세스를 의미합니다. 최소한의 제조 비용으로 생산하는 핵심 철학은 낭비 제거를 통해 주문에서 배송까지의 사이클 시간을 단축하는 것을 목표로 합니다. LEAN 원칙의 구현은 비용 절감이 시장의 현실인 생산 환경에서 생존을 위한 필수 전략으로 진화했습니다.
기존 연구 현황:
본 방법론은 도요타 생산 시스템에 뿌리를 두고 있으며, Womack과 Jones [2]에 의해 서구 산업에 맞게 적용되었습니다. 본 논문은 Taichi Ohno의 7가지 생산 손실 분류 [3]를 참조하여 확립된 린 생산 방식 이론에 기반하고 있음을 나타냅니다. 이러한 손실에는 과잉 생산, 대기, 운송, 가공, 재고, 동작 및 수정이 포함됩니다.
연구의 필요성:
경쟁적인 시장 환경에서 지속적인 비용 절감은 필수적입니다. 본 논문은 기업이 경쟁력을 유지하기 위해 린 생산 방식을 채택해야 한다고 주장합니다. 또한, 인간 주도 공정 개선의 한계를 지적하며, 자동화를 통해 이러한 한계를 극복하고 인간의 능력을 뛰어넘는 효율성과 신뢰성을 향상시킬 수 있다고 제시합니다. 자동화는 일관된 결과를 달성하고 수동 작업과 관련된 본질적인 변동성을 해결하기 위한 해결책으로 제시됩니다.
4. 연구 목적 및 연구 질문:
연구 목적:
본 연구의 주요 목적은 루마니아 티미쇼아라에 위치한 TRW Automotive에서 린 생산 방식 프레임워크 내 자동화 구현을 조사하는 것입니다. 본 연구는 공정 자동화가 자동차 산업 환경에서 생산 손실 제거 및 제조 효율성 향상에 어떻게 기여할 수 있는지 입증하는 것을 목표로 합니다.
핵심 연구:
핵심 연구 초점은 TRW Automotive의 스티어링 휠 다이캐스팅 공정 자동화에 대한 사례 연구입니다. 여기에는 수동 공정 단계에서 자동화 공정 단계로의 전환을 분석하고 생산성, 품질, 비용 절감 및 안전 측면에서 예상되는 이점을 평가하는 것이 포함됩니다.
연구 가설:
암묵적인 연구 가설은 린 생산 방식 프레임워크 내에서 자동화 기술의 전략적 구현이 다음과 같은 주요 성과 지표의 상당한 개선으로 이어질 것이라는 것입니다.
- 생산성 및 생산량 증가.
- 일관된 공정 실행을 통한 제품 품질 향상.
- 인적 운영 시간 및 관련 인건비 감소.
- 특히 마그네슘과 같은 위험 물질을 취급할 때 작업자 안전 개선.
5. 연구 방법론
연구 설계:
본 연구는 TRW Automotive 티미쇼아라 공장의 다이캐스팅 공정 내 자동화 구현에 초점을 맞춘 사례 연구 설계를 채택합니다. 이 접근 방식을 통해 실제 산업 환경에서 린 생산 방식 원칙과 자동화 기술의 실제 적용에 대한 심층적인 조사가 가능합니다.
자료 수집 방법:
자료 수집은 TRW Automotive의 기존 수동 및 반자동 다이캐스팅 공정 분석을 기반으로 하며, 계획 및 구현된 자동화 공정과 대조됩니다. 여기에는 자동화 전후의 공정 단계를 관찰하고 문서화하는 것은 물론 예상되는 성과 지표를 수집하는 것이 포함됩니다.
분석 방법:
분석은 주로 질적이며, 수동 공정과 자동화 공정의 비교 평가를 포함합니다. 본 연구는 린 생산 방식 원칙의 맥락에서 자동화의 예상되는 이점을 평가하고, 7가지 낭비 제거에 초점을 맞춥니다. 표 (그림 7)는 자동화 구현으로 인한 변화와 이점을 체계적으로 분석하기 위해 제시됩니다.
연구 대상 및 범위:
연구 대상은 TRW Automotive 티미쇼아라 공장의 다이캐스팅 작업이며, 특히 스티어링 휠 생산에 초점을 맞춥니다. 범위는 이 다이캐스팅 작업 내 특정 공정 단계의 자동화와 생산성, 품질, 비용 및 안전에 미치는 영향으로 제한됩니다.
6. 주요 연구 결과:
핵심 연구 결과:
프로토타입 셀 구현을 기반으로 예상되는 주요 연구 결과는 다음과 같습니다.
- 더블 캐비티 장비에서 예상되는 생산성 (생산량) 30% 증가.
- 인간의 시각 검사의 변동성 제거 및 공정 일관성 향상을 통한 제품 품질 10% 향상 예상.
- 인적 운영 시간 40% 감소로 인한 인건비 절감.
- 특히 통제되지 않은 점화 위험이 자동화를 통해 완화되는 마그네슘 다이캐스팅과 관련된 인적 안전의 상당한 향상.
제시된 데이터 분석:
"다이캐스팅 프로토타입 셀의 자동화 공정 구현에 따른 제품 변화 및 이점 표"인 그림 7은 수동 공정에서 자동화 공정으로의 구체적인 변화를 자세히 설명합니다. 주요 변경 사항은 다음과 같습니다.
- 이형제 도포 방식: 수동에서 자동 마이크로 스프레이 (HERA)로 전환하여 일정하고 표준화된 도포 보장.
- 이형제 매체: 환경 및 안전 개선을 위해 오일에서 마이크로 스프레이 (HERA)로 전환.
- 인서트 공급: 일관되고 표준화된 공정을 위해 인서트 공급 자동화.
- 오버플로우 검사: 품질 관리를 개선하기 위한 자동 오버플로우 감지.
- 냉각: 수동 엘리베이터 딥 냉각을 대체하는 로봇 제어 딥 냉각 구현으로 표준화.
- 금속 인서트 검증: 수동 중량 스테이션 검사를 개선하는 오버플로우 감지 시 자동 검증.
- 중량 제어: 샷 간 변동성을 줄이기 위한 "First Off/Last Off" 중량 제어 구현.
- 레이저 마킹: 자동화된 레이저 마킹을 통한 단일 유닛 추적성 도입.
- 트림 프레스 청소: 일관되고 표준화된 유지 보수를 위한 트림 프레스 청소 자동화.
이러한 변화는 공정 표준화, 향상된 환경 및 안전 조건, 개선된 품질 관리, 감소된 공정 변동성 및 향상된 제품 추적성과 같은 이점을 가져올 것으로 예상됩니다.
그림 목록:

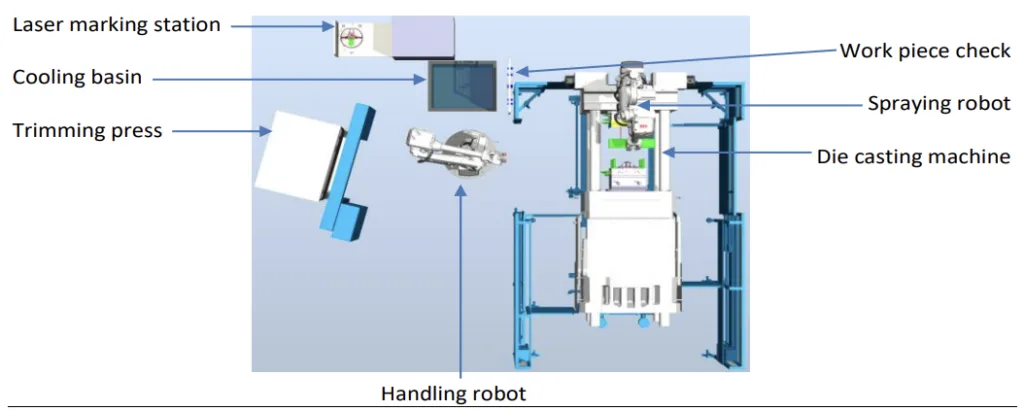
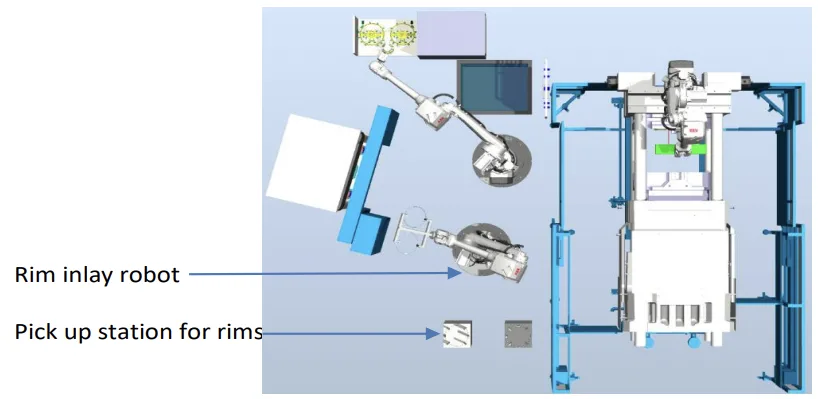
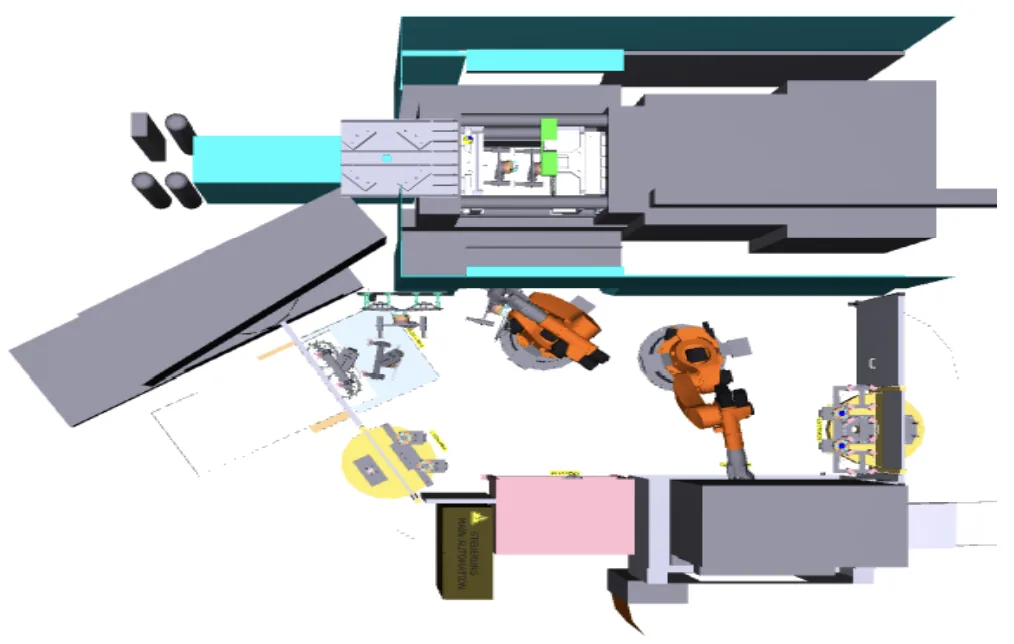
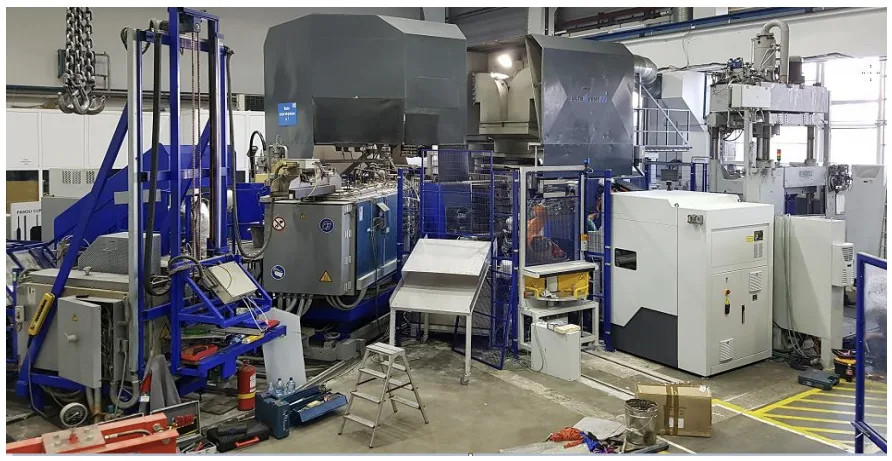
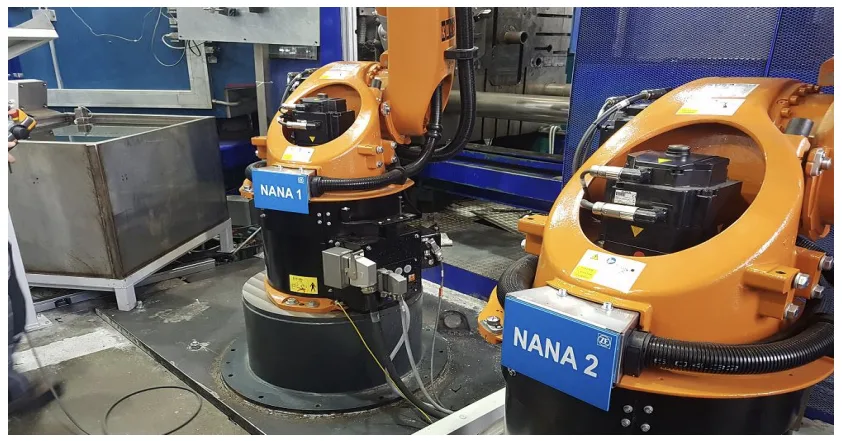
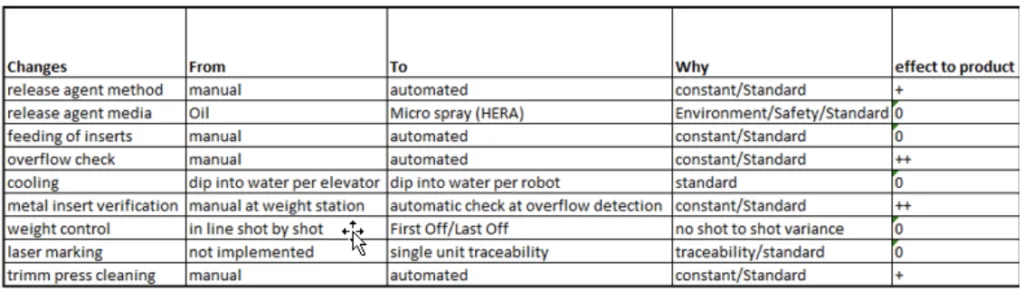
- Fig. 1. 린 생산 방식 기둥 [1]
- Fig. 2. 새로운 공정 단계 개요 - 첫 번째 핸들링 로봇 도입
- Fig. 3. 새로운 공정 단계 개요 - 두 번째 핸들링 로봇 도입
- Fig. 4. 자동화 구현 후 새로운 다이캐스팅 장비 레이아웃
- Fig. 5. TRW Automotive의 첫 번째/프로토타입 셀에서 자동화 공정 구현 관련 활동
- Fig. 6. TRW Automotive의 첫 번째/프로토타입 셀에서 자동화 공정 구현 관련 활동
- Fig. 7. 다이캐스팅 프로토타입 셀의 자동화 공정 구현에 따른 제품 변화 및 이점 표
7. 결론:
주요 결과 요약:
본 연구는 TRW Automotive에서 린 생산 방식 프레임워크 내 자동화 구현이 매우 성공적일 것으로 예상된다는 결론을 내립니다. 프로토타입 셀의 예비 결과는 생산성, 품질, 운영 시간 단축 및 안전 측면에서 상당한 개선 가능성을 시사합니다. 자동화 이니셔티브는 작업 그룹 구성원이 작업량 균형을 위한 복잡한 시간 연구 없이 서로 보조를 맞출 수 있도록 하여 생산 유연성을 향상시킬 것으로 예상됩니다.
연구의 학문적 의의:
본 연구는 자동차 산업 내에서 린 생산 방식 원칙과 첨단 자동화 기술을 성공적으로 통합한 실제 사례를 제공합니다. 이는 실제 제조 환경에서 이러한 통합 접근 방식의 실질적인 이점을 입증함으로써 운영 우수성에 대한 지식 체계에 기여합니다.
실용적 의미:
본 연구 결과는 제조 공정 개선 전략으로 자동화를 고려하는 자동차 제조업체 및 기타 산업에 귀중한 통찰력을 제공합니다. TRW Automotive의 사례 연구는 운영 개선, 생산 손실 감소 및 제품 품질 향상을 위해 린 프레임워크 내에서 자동화를 구현하는 모델 역할을 합니다.
연구의 한계 및 향후 연구 분야:
본 연구는 결과가 예비적이며 프로토타입 셀을 기반으로 한다는 점을 인정합니다. 결과는 아직 전체 생산 라인에 대해 확정적이지 않습니다. 향후 연구는 TRW Automotive의 전체 다이캐스팅 생산 라인에서 자동화 구현의 장기적인 영향과 확장성을 평가하는 데 초점을 맞춰야 합니다. 다른 제조 환경 및 산업에서 이러한 결과의 광범위한 적용 가능성에 대한 추가 조사도 권장됩니다.
8. 참고 문헌:
- [1]. Allen J., Robinson C., Stewart D., Lean Manufacturing - a plant floor guide, Society.
- [2]. ***, Lean manufacturing - Methods for reducing costs, Pilot Project.
- [3]. Womack J. P., Jones D. T., Roos D., The Machine that Changed the World: How Lean Production Revolutionized the Global Car Wars, S. & Schuster, London, 1990.
- [4]. ***, Lean manufacturing - Methods for cost reduction, Pilot Project TRW Automotive.
9. 저작권:
- 본 자료는 "Ovidiu AMBRUS"의 논문: "LEAN MANUFACTURING - PROCESS AUTOMATION AND ELIMINATION OF PRODUCTION LOSSES IN ROMANIAN AUTOMOTIVE INDUSTRY"를 기반으로 합니다.
- 논문 출처: [THE ANNALS OF "DUNAREA DE JOS" UNIVERSITY OF GALATI, FASCICLE IX. METALLURGY AND MATERIALS SCIENCE, Nº. 1 - 2017, ISSN 1453-083X]
본 자료는 상기 논문을 요약한 것으로, 상업적 목적으로 무단 사용하는 것을 금지합니다.
Copyright © 2025 CASTMAN. All rights reserved.