본 요약은 ['European Mechanical Science' 저널에 게재된 ['Aluminium High Pressure Die Casting Application on Rear Frame Rails'] 논문을 기반으로 작성되었습니다.
1. 개요:
- 제목: 리어 프레임 레일에 대한 알루미늄 고압 다이캐스팅 적용 (Aluminium High Pressure Die Casting Application on Rear Frame Rails)
- 저자: 이브라힘 오즈바이, 타메르 아이디너, ギュル칸 イル마즈오グル, 하피제 셀리크, 레벤트 악셀, 하룬 예니, 메테한 바이라모글루, 에르뎀 아이도무스 (Ibrahim Ozbay, Tamer Aydiner, Gürkan Yilmazoglu, Hafize Celik, Levent Aksel, Harun Yeni, Metehan Bayramoglu, Erdem Aydogmus)
- 발행 연도: 2019년
- 발행 저널/학술 단체: 유럽 기계 과학 (European Mechanical Science)
- 키워드: 리어 레일 강화 지지 브래킷 (Rear Rail Reinforcement Support Bracket), Al 합금 (Al Alloy), 고압 다이캐스팅 (High Pressure Die Casting), 차체 (Body In White, BIW)
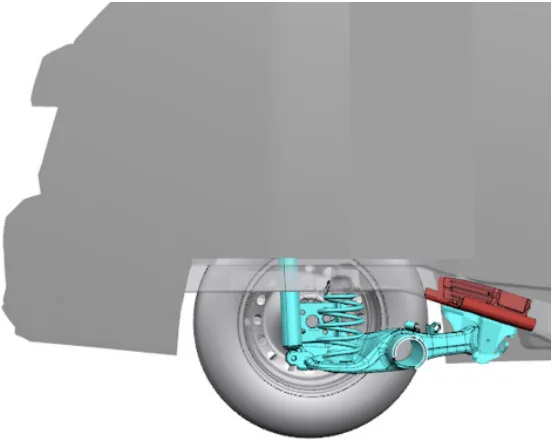
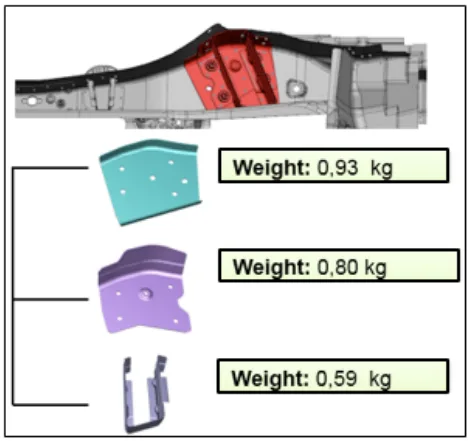
2. 초록 또는 서론
자동차 산업의 고도의 경쟁 환경과 환경 규제로 인해 자동차 제조업체는 기존의 강철과 같은 구조 재료 대신 더 높은 기계적 특성과 경량화 성능을 가진 재료를 사용하는 경향이 있습니다. 알루미늄 합금은 강철보다 3배 가볍기 때문에 이러한 적용의 좋은 예입니다. 알루미늄은 내구성능이 우수하기 때문에 차체 구조 설계에 사용이 제안되고 있으며, 적절한 형상과 열처리 적용 시 기계적 특성은 구조 부품에 유효합니다. 주조 공정은 토폴로지 최적화를 가능하게 하고, 판금 스탬핑에 비해 더 나은 강도와 더 적은 무게를 갖는 더 복잡한 형상을 만들 수 있습니다. 리어 레일 강화 지지 브래킷은 토폴로지 최적화된 알루미늄 다이캐스팅 부품을 적용할 수 있는 차체 구조 (Body In White) 의 가장 적합한 부품 중 하나입니다. 기존의 강화 지지 브래킷에서는 원하는 강성과 내구성을 확보하기 위해 여러 개의 강철 스탬핑 부품이 사용되어 설계, 성형성 및 조립 측면에서 훨씬 더 복잡한 구조를 초래합니다. 본 연구에서는 기존 솔루션과 동일한 성능을 얻기 위해 고압 주조 방식으로 설계 및 생산된 새로운 부품을 연구합니다. 또한 더 나은 기계적 특성을 얻기 위해 다양한 열처리를 테스트하고 최적의 열처리 사이클을 결정했습니다. 새로운 설계는 가상 검증 도구를 사용하여 기존 설계와 비교되었으며 비교 결과가 제시되었습니다.
3. 연구 배경:
연구 주제 배경:
자동차 산업의 안전 기준 강화로 인해 차세대 차량의 차체 구조는 충돌 시 더 나은 구조적 무결성과 에너지 흡수 능력을 가져야 합니다. 동시에 새로운 환경 규제로 인해 탄소 배출량도 낮아져야 합니다. 엔진 및 변속기 효율, 차량 중량, 공기 역학 및 구름 저항은 탄소 배출량과 연료 소비에 영향을 미치는 주요 요인입니다. 차량 중량 100kg 감량은 km당 9g의 CO₂ 절감 효과를 가져올 수 있습니다. 따라서 차량 중량 감량은 CO₂ 배출량 감소를 위한 가장 효과적인 방법이며, 동시에 안전성, 주행 품질 및 전반적인 성능을 유지하는 데 필수적입니다. 자동차 구조는 전체 차량 중량의 약 40%를 차지하므로 차체 구조의 중량 감소는 연비 향상, 유해 배출 감소 및 원자재 절약을 달성하는 핵심 방법입니다.
기존 연구 현황:
차체 중량 감소를 위해 알루미늄, 마그네슘, 복합재료 등 다양한 설계 방법론과 혁신적인 재료 옵션이 모색되고 있습니다. 알루미늄은 비용 효율성, 가공성, 내식성, 재활용성 및 자동차 산업에서의 광범위한 사용으로 인해 차체 중량 감소에 가장 적합한 재료로 강조됩니다. 알루미늄 합금은 자동차 응용 분야에서 강철보다 다음과 같은 여러 가지 장점을 제공합니다: 낮은 밀도 (강철의 7.87 gr/cm³에 비해 2.7g/cm³), 단위 중량당 더 높은 충격 에너지 흡수, 그리고 라디에이터 코어 및 열교환기 응용 분야에 유용한 우수한 열전도율.
연구의 필요성:
현재 차량 설계에서 리어 서스펜션 지지 브래킷은 일반적으로 2.7kg 무게의 3개의 강판으로 구성됩니다. 이러한 부품은 수많은 스폿 용접과 구조용 접착제로 결합되어 차량 중량과 제조 비용 증가를 초래합니다. 성능과 안전성을 유지하거나 향상시키면서 중량과 비용을 줄이기 위한 대체 재료 및 제조 공정 탐색의 필요성이 있습니다.
4. 연구 목적 및 연구 질문:
연구 목적:
본 연구의 주요 목적은 구조적 성능과 안전성을 저하시키지 않으면서 중량 감소 및 비용 효율성을 달성하기 위해 알루미늄 합금과 고압 다이캐스팅을 사용하여 리어 레일 서스펜션 지지 브래킷을 재설계하는 것입니다.
핵심 연구:
핵심 연구는 다음 사항에 중점을 둡니다:
- 알루미늄 합금과 고압 다이캐스팅을 사용하여 단일 부품 리어 서스펜션 지지 브래킷 설계.
- 강성을 최대화하고 중량을 최소화하기 위한 토폴로지 최적화를 통한 설계 최적화.
- 원하는 기계적 특성을 얻기 위한 알루미늄 다이캐스팅 브래킷의 최적 열처리 결정.
- 새로운 알루미늄 다이캐스팅 브래킷의 성능을 가상 분석을 통해 검증하고, 충돌 안전성, 내구성 및 NVH (소음, 진동 및 불쾌감) 특성 측면에서 기존 강철 브래킷 솔루션과 비교.
연구 가설:
본 연구에서는 다음 가설을 설정합니다:
- 알루미늄 고압 다이캐스팅 리어 서스펜션 지지 브래킷은 기존의 다중 부품 강철 브래킷과 동등하거나 우수한 구조적 성능을 달성할 수 있다.
- 재설계된 알루미늄 브래킷은 강철 브래킷에 비해 상당한 중량 감소를 가져올 것이다.
- 최적화된 열처리는 알루미늄 다이캐스팅 브래킷의 기계적 특성을 향상시켜 구조용 자동차 응용 분야에 적합하게 만들 것이다.
5. 연구 방법론
연구 설계:
본 연구는 설계 및 검증 접근 방식을 채택합니다. 초기에는 서스펜션 연결 부위의 하중 조건을 기반으로 알루미늄 브래킷의 최적 설계를 생성하기 위해 토폴로지 최적화를 활용했습니다. 최적화를 위한 설계 공간은 U자형 크로스 멤버 내에서 정의되었습니다. 유한 요소법 (FEM) 은 서스펜션 조인트 지점에 X, Y, Z 방향으로 단위 하중을 가하여 토폴로지 최적화에 사용되었습니다.
자료 수집 방법:
본 연구는 주로 성능 평가를 위해 가상 검증 도구를 활용합니다. Silafont-36 알루미늄 합금의 재료 특성 및 다양한 열처리에 대한 실험 데이터를 사용하여 가상 시뮬레이션을 수행했습니다.
분석 방법:
다음과 같은 가상 분석 방법을 사용했습니다:
- 주조 분석: 금형 충전 및 응고 시뮬레이션을 수행하여 다공성 및 변형과 같은 잠재적인 주조 결함을 식별하고 게이팅 및 냉각 시스템 설계를 최적화했습니다.
- 가상 검증:
- 후방 충돌 성능 (TRIAS 33): TRIAS 33 후방 충돌 시나리오에 따라 시뮬레이션을 수행하여 강철 브래킷과 비교하여 알루미늄 브래킷의 구조적 무결성 및 변형 거동을 평가했습니다.
- 피로 성능: 반복적인 충격 하중 하에서 알루미늄 브래킷의 피로 수명을 평가하기 위해 피로 분석을 수행했습니다.
- 모달 분석 성능: 알루미늄 브래킷을 장착한 차량의 NVH 특성, 특히 고유 진동수 및 동적 강성을 평가하기 위해 모달 분석을 수행했습니다.
- 비틀림-굽힘 강성 성능: 알루미늄 브래킷을 장착한 차량의 비틀림 및 굽힘 강성을 평가하고 강철 브래킷과 비교했습니다.
연구 대상 및 범위:
본 연구는 승용차의 리어 서스펜션 지지 브래킷에 초점을 맞춥니다. 연구 대상 재료는 고압 다이캐스팅으로 가공된 Silafont-36 (AlSi10MnMg) 알루미늄 합금입니다. 범위는 설계, 재료 선택, 열처리 최적화 및 알루미늄 다이캐스팅 브래킷의 가상 검증을 포함합니다.
6. 주요 연구 결과:
핵심 연구 결과:
- 중량 감소: 알루미늄 다이캐스팅 리어 서스펜션 지지 브래킷은 강철 브래킷 조립품에 비해 차량당 약 3.0kg의 중량 감소를 달성했습니다.
- 스폿 용접 감소: 새로운 설계는 기존 강철 브래킷에 비해 약 35%의 스폿 용접 접합부를 제거했습니다.
- 재료 선택 및 열처리: Silafont-36 알루미늄 합금과 T6 열처리가 강도와 연신율의 균형을 제공하는 최적의 재료 및 열처리 조합으로 선택되었습니다. T6 열처리는 520°C에서 용체화 처리, 급냉 및 180°C에서 인공 시효 경화를 포함합니다.
- 주조 분석: 주조 시뮬레이션은 다공성 및 변형 위험을 완화하기 위한 설계 수정, 추가 냉각 라인 및 다중 게이트로 금형 설계를 최적화하는 데 기여했습니다.
- 가상 검증:
- 후방 충돌 성능 (TRIAS 33): TRIAS 33 시뮬레이션은 알루미늄 브래킷에 대한 만족스러운 후방 충돌 성능을 나타내었으며, 강철 브래킷에 비해 부정적인 결과가 나타나지 않았습니다 (FIG.11 Rear impact virtual analysis result - bottom view).
- 피로 성능: 피로 분석은 중요한 영역의 설계 최적화로 인해 알루미늄 브래킷의 피로 수명 성능이 향상되었음을 입증했습니다 (FIG.12 Fatigue Life Analysis).
- 모달 분석 성능: 모달 분석 결과 알루미늄 브래킷을 사용했을 때 차량의 비틀림 모드가 약간 증가 (~0.5 Hz) 하여 이 측면에서 NVH 특성이 향상되었음을 나타냅니다 (Fig.13 NVH analysis for suspension joint point).
- 비틀림-굽힘 강성 성능: 알루미늄 브래킷을 사용했을 때 차량의 비틀림 모드가 3-5% 증가하여 비틀림 강성이 향상되었음을 시사합니다.
제시된 데이터 분석:
그림과 차트에 제시된 데이터는 알루미늄 다이캐스팅 브래킷의 효과를 입증합니다. 그림 6은 다양한 열처리 조건에서 Silafont-36의 항복 강도와 연신율을 보여주며, T6 조건이 적합한 선택임을 강조합니다. 그림 7은 T6 열처리 사이클의 개략적인 표현을 보여줍니다. 그림 8과 9는 각각 다공성 및 변형 분석과 금형 충전 및 응고 분석을 보여주는 주조 분석 결과를 보여줍니다. 그림 11, 12, 13은 후방 충돌, 피로 수명 및 NVH 성능에 대한 가상 검증 결과를 제시하며, 알루미늄 브래킷이 강철 대응 부품에 비해 동등하거나 향상된 성능을 나타냄을 보여줍니다. 차트 1은 Silafont-36의 화학적 조성을 자세히 설명하고, 차트 2는 다양한 열처리에 대한 실험 연구 매개변수 및 결과를 요약합니다.
그림 목록:
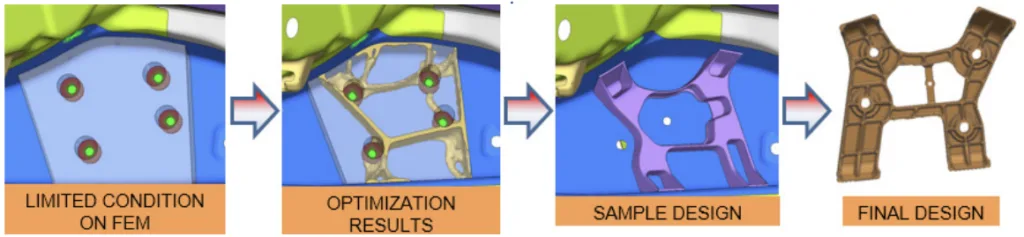
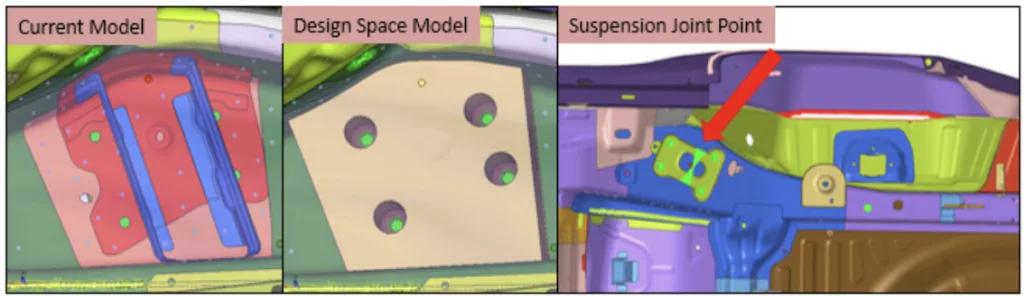
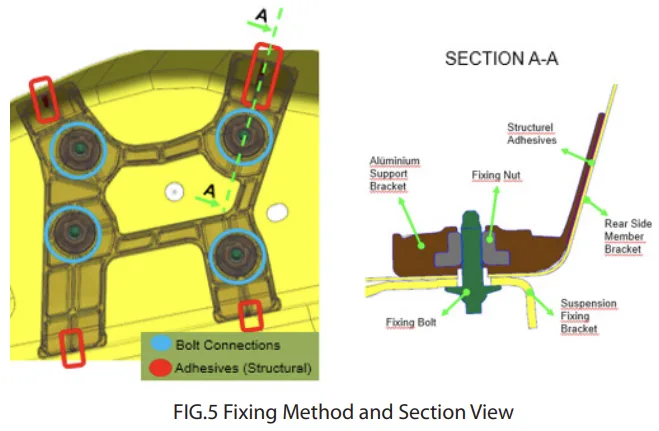
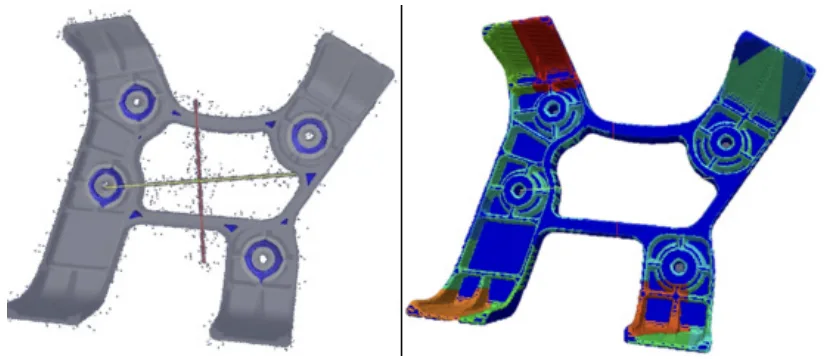
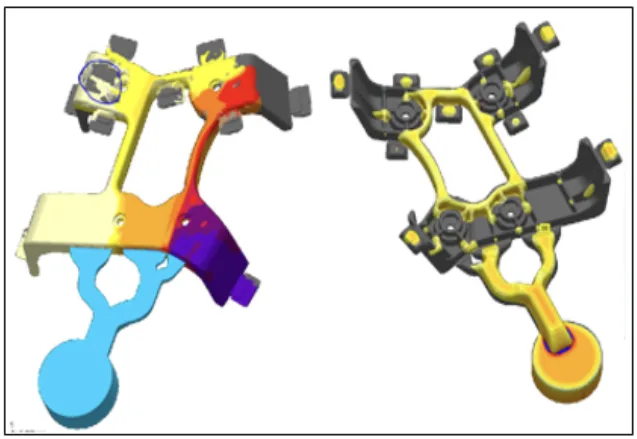
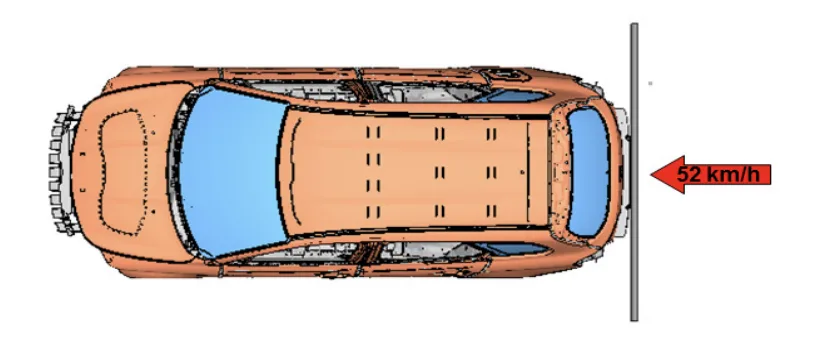
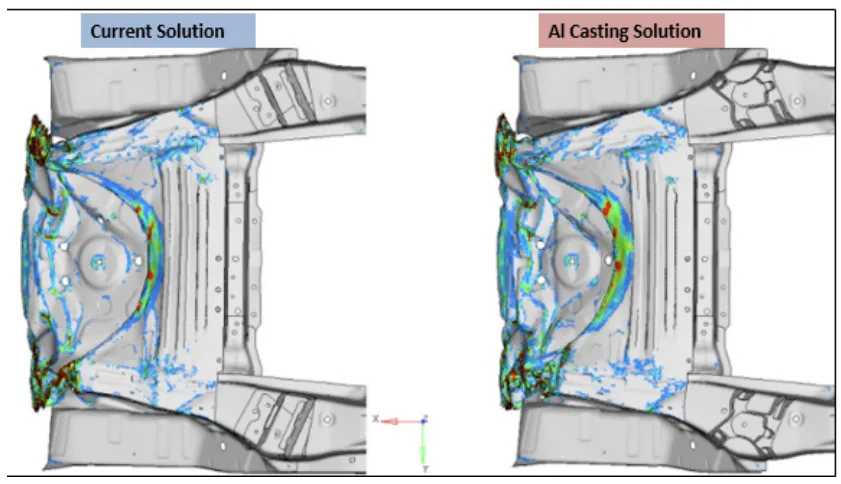
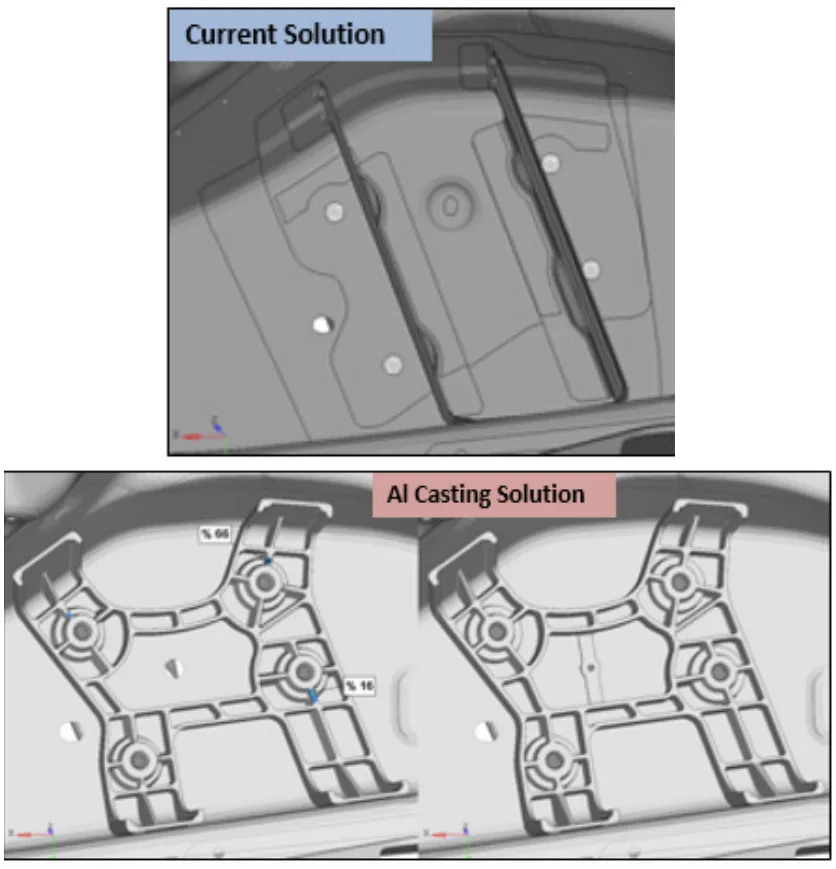
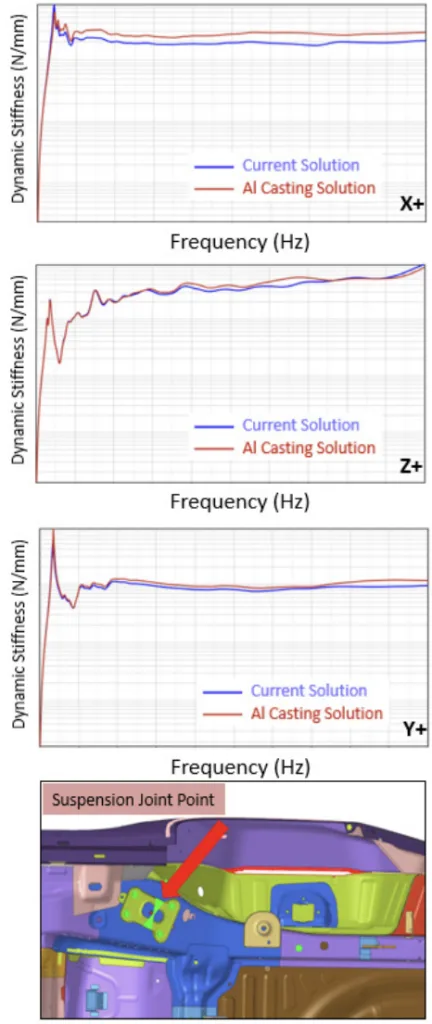
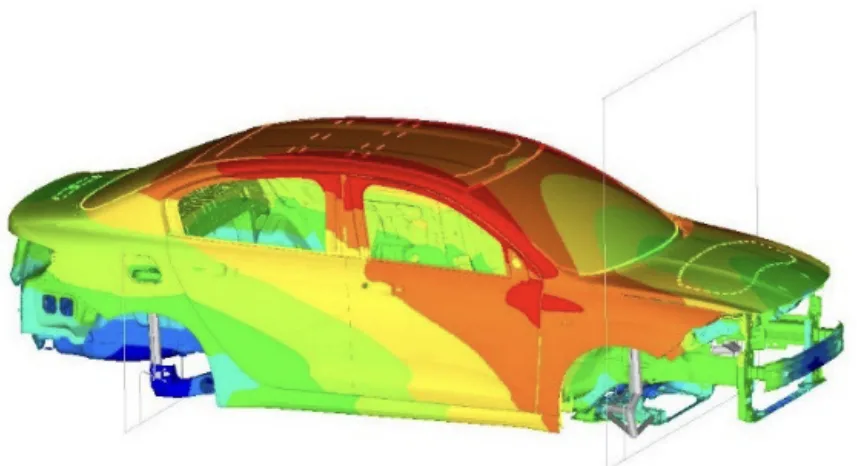
- FIG.1 리어 서스펜션과 차체 연결 실험 절차 (Connection of Rear Suspension to Body experimental procedure)
- FIG.2 리어 서스펜션 지지 브래킷 디스플레이 및 조립 세부 정보 (Rear Suspension Support Brackets Display and Assembling Details)
- FIG.3 토폴로지 최적화 및 최종 설계 (The Topology Optimization and Final Design)
- FIG.4 U자형 차체 암 및 서스펜션 조인트 지점의 현재 모델, 설계 공간 모델 (Current model, design space model in U-section body arm and Suspension Joint Point.)
- FIG.5 고정 방법 및 단면도 (Fixing Method and Section View)
- FIG.6 다양한 열처리 상태에서 Silafont-36의 항복 강도 및 연신율 [6] (Silafont-36 Yield strength and elongation in various heat treatment states [6])
- FIG.7 T6 열처리 개략도 (온도 및 시간은 재료, 설계 및 요구 사항 유형에 따라 다를 수 있음) (T6 heat treatment schematic representation (temperatures and durations may vary depending on the type of material, design and requirements))
- FIG.8 다공성 및 변형 분석 및 설계 (Porosity and Distortion Analysis and of Design)
- FIG.9 금형 충전 및 응고 분석 및 설계 (Mold Filling and Solidification Analysis and of Design)
- FIG.10 TRIAS 33 검증을 위한 차량 후방 충돌 조건 (Rear Impact Condition of the Vehicle for TRIAS 33 Validation)
- FIG.11 후방 충돌 가상 분석 결과 - 하단 뷰 (Rear impact virtual analysis result - bottom view)
- FIG.12 피로 수명 분석 (Fatigue Life Analysis)
- FIG.13 서스펜션 조인트 지점 NVH 분석 (NVH analysis for suspension joint point)
- FIG. 14 BIW 모델의 비틀림-굽힘 강성 분석 (Torsional- Bending Stiffness Analysis in BIW model)
7. 결론:
주요 결과 요약:
본 연구는 자동차 BIW 구조의 리어 서스펜션 지지 브래킷 제조에 알루미늄 고압 다이캐스팅을 사용하는 것의 타당성을 성공적으로 입증했습니다. Silafont-36 합금으로 만들어지고 T6 열처리를 거친 재설계된 알루미늄 브래킷은 기존 강철 조립품에 비해 차량당 3.0kg의 상당한 중량 감소와 35%의 스폿 용접 감소를 달성했습니다. 가상 검증을 통해 알루미늄 브래킷이 충돌 안전성, 피로 수명 및 NVH 특성 측면에서 강철 브래킷의 성능을 충족하거나 능가하는 것으로 확인되었습니다.
연구의 학문적 의의:
본 연구는 자동차 공학의 경량화에 대한 지식 기반을 확장하는 데 기여하며, 특히 구조 부품에 대한 알루미늄 고압 다이캐스팅의 적용을 입증합니다. 고성능 다이캐스팅 부품을 설계하고 검증하는 데 토폴로지 최적화 및 가상 검증의 효과를 강조합니다. 또한 본 연구는 구조용 자동차 응용 분야에서 알루미늄 합금의 재료 선택 및 열처리 최적화에 대한 귀중한 통찰력을 제공합니다.
실용적 의미:
본 연구 결과는 자동차 산업에 상당한 실용적 의미를 갖습니다. 알루미늄 고압 다이캐스팅 리어 서스펜션 지지 브래킷의 성공적인 구현은 다음을 가져올 수 있습니다:
- 차량 중량 감소로 연비 향상 및 CO₂ 배출량 감소에 기여.
- 단일 부품 설계 및 스폿 용접 감소로 인한 조립 공정 단순화 및 제조 비용 절감.
- 향상된 차량 성능 및 NVH 특성.
- 자동차 구조에서 재활용 가능한 알루미늄 합금의 활용 증가로 지속 가능성 증진.
연구의 한계 및 향후 연구 분야:
본 연구는 주로 가상 검증에 의존합니다. 향후 연구에서는 실제 조건에서 알루미늄 다이캐스팅 브래킷의 성능을 추가로 검증하기 위해 물리적 프로토타입 제작 및 실험적 테스트를 포함해야 합니다. 설계 및 제조 공정을 더욱 최적화하기 위해 다양한 알루미늄 합금, 주조 공정 매개변수 및 접합 기술에 대한 추가 연구도 모색할 수 있습니다. 사용 조건에서 알루미늄 브래킷의 장기적인 내구성 및 내식성에 대한 추가 조사가 필요합니다.
8. 참고 문헌:
- [1] Hirsch, J. (2011). 혁신적인 경량 자동차 디자인의 알루미늄 (Aluminium in Innovative Light-Weight Car Design). 재료 트랜잭션 (Materials Transactions), 52(5): 818-824, DOI:10.2320/matertrans.L-MZ201132.
- [2] Altınok, E., Kayserili, H., Mert A., Altınel, S.A. (2017). 자동차 차체 개발의 경량 도어 링 솔루션 (Lightweight Door Ring Solution in Car Body Development). 자동차 및 기술 발전에 관한 국제 저널 (International Journal of Advances on Automotive and Technology), 1(3): 131-136, DOI: 10.15659/ijaat.17.07.529.
- [3] Başer, T. A. (2013). 알루미늄 합금 및 자동차 산업에서의 사용 (Alüminyum alaşımları ve otomotiv endüstrisinde kullanımı). 엔지니어 및 기계 (Mühendis ve Makina), 53(635): 51-58.
- [4] Mallick, P.K. (2010). 경량 차량용 재료, 설계 및 제조 (Materials, Design and Manufacturing for Lightweight Vehicles), 캠브리지, 영국: 우드헤드 출판 제한 (Cambrighe, UK: Woodhead Publishing Limited).
- [5] Wu, P., Ma, Q., Luo, Y., Tao, C. (2016). 자동차 엔진 브래킷의 토폴로지 최적화 설계 (Topology Optimization Design of Automotive Engine Bracket). 에너지 및 동력 공학 (Energy and Power Engineering), 8(4): 230-235, DOI: 10.4236/epe.2016.84021.
- [6] KG, 라인펠덴 알로이스 GmbH & Co., "압력 다이캐스팅용 1차 알루미늄 합금 (Primary Aluminium Alloys for Pressure Die Casting)," 알루미늄 라인펠덴 그룹의 회사 (A company of the Aluminium Rheinfelden Group), 프리드리히슈트라세 80 (Friedrichstraße 80).
- [7] Chaudhury, S.K., Apelian, D. (2006). 주조 Al-Si-Cu-Mg 합금의 유동층 열처리 (Fluidized Bed Heat Treatment of Cast Al-Si-Cu-Mg Alloys). 야금 및 재료 트랜잭션 A (Metallurgical and Materials Transactions A), 37A: 2295-2311.
- [8] M. Hartlieb, (2013). 구조용 다이캐스팅용 알루미늄 합금 (Aluminium Alloys For Structural Die Casting). 다이캐스팅 엔지니어 (Die Casting Engineer), 41.
- [9] Kurisu, F., Miyauchi, K. (2004). 파워트레인에 대한 ADAMS 메커니즘 분석 소프트웨어의 적용 (Application of ADAMS Mechanism Analysis Software To Powertrains). 마쓰다 기술 리뷰 (Mazda Technical Review), 22: 44-49.
- [10] Aksel, L., Efendioğlu, Ş., Yeni H., Bilge, Ç. (2016). 기존 HSS 또는 AHSS 응용 분야 대신 붕소 합금 열간 스탬핑 솔루션을 사용한 BIW의 중량 감소 연구 (Weight Reduction Study on BIW by Using Boron Alloyed Hot Stamping Solution of Front Frame Rail Instead Conventional HSS or AHSS Applications). 첨단 기술 및 과학에 관한 국제 회의 (International Conference on Advanced Technology & Sciences).
- [11] Joost, W. J., Krajewski, P.E. (2017). 고용량 자동차 응용 분야를 위한 마그네슘 합금 (Towards magnesium alloys for high-volume automotive applications). 스크립타 머티리얼리아 (Scripta Materialia), 128: 107-112, DOI: 10.1016/j.scriptamat.2016.07.035.
9. 저작권:
- 본 자료는 "이브라힘 오즈바이, 타메르 아이디너, ギュル칸 イル마즈오グル, 하피제 셀리크, 레벤트 악셀, 하룬 예니, 메테한 바이라모글루, 에르뎀 아이도무스"의 논문: "리어 프레임 레일에 대한 알루미늄 고압 다이캐스팅 적용"을 기반으로 합니다.
- 논문 출처: https://doi.org/10.26701/ems.422299
본 자료는 상기 논문을 요약한 것으로, 상업적 목적으로 무단 사용하는 것을 금지합니다.
Copyright © 2025 CASTMAN. All rights reserved.