본 소개 자료는 [Publisher is not included in the paper]에서 발행된 ["Local stress/strain field analysis of die-casting Al alloys via 3D model simulation with realistic defect distribution and RVE modelling"] 논문의 연구 내용을 담고 있습니다.
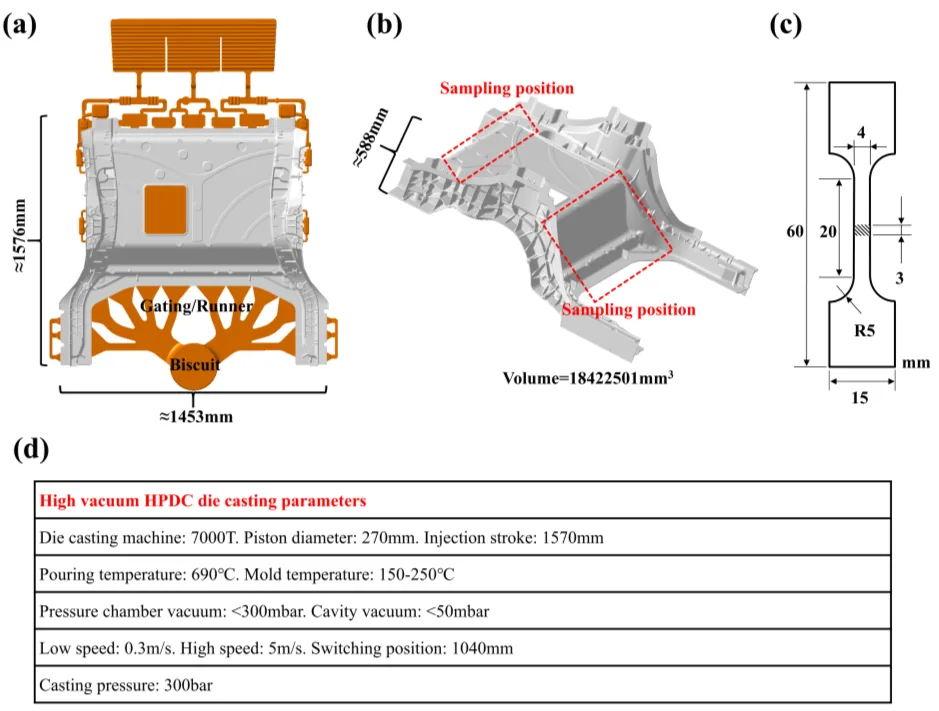
1. 개요:
- 제목: Local stress/strain field analysis of die-casting Al alloys via 3D model simulation with realistic defect distribution and RVE modelling (실제 결함 분포 및 RVE 모델링을 이용한 다이캐스팅 Al 합금의 국부 응력/변형률 필드 해석)
- 저자: Jian Yang, Bo Liu, Dongwei Shu, Qin Yang, Tiegang Hu
- 출판 연도: 2024
- 게재 저널/학회: 프리프린트.
- 키워드: Die-casting(다이캐스팅); Aluminium alloy(알루미늄 합금); Representative volume element(대표 체적 요소); X-ray computed tomography(X선 전산화 단층 촬영); Automotive lightweighting(자동차 경량화).
2. 초록
다이캐스팅 알루미늄(Al) 합금의 변형 및 파괴 거동은 매우 복잡합니다. 국부적인 특성 변화로 인해 재료의 미세 구조와 기계적 거동은 매우 이방성을 띕니다. 본 논문에서는 실험 및 유한 요소 계산 방법을 사용하여 고압 주조 Al 합금 부품의 결함 특성을 정량적으로 연구하고 국부 다공성 및 기공 크기가 소성에 미치는 영향을 분석했습니다. 실제 결함 분포를 가진 3차원 고체는 3D X선 전산화 단층 촬영을 사용하여 얻었으며 유한 요소 모델 구축을 위한 입력으로 사용되었습니다. 복합 응력 상태에서 주조 Al 합금의 손상 개시는 미세 규모에서 거시 규모까지 분석됩니다. 미세 다공성 응집의 두 가지 모드를 통해 균열 전파가 발생합니다. 응집된 기공은 내부 네킹 및 응력 집중으로 인해 균열을 생성합니다. 그런 다음 동일한 방향으로 확장되고 특정 방향으로 응집되어 결국 파괴됩니다. 그 후, 디지털 이미지 상관 측정을 통해 국부 응력/변형 거동을 얻어 다공성이 불균일성에 미치는 영향을 설명했습니다. 또한, 미세 구조의 탄소성 변형에 대한 이론적 프레임워크와 3D 대표 체적 요소 모델을 개발하여 재료의 주기적 경계 조건에서 변형 및 손상 프로세스를 시뮬레이션했습니다. 시뮬레이션 결과는 기공 주위의 국부 응력/변형이 변형에 따라 점진적으로 변화함을 보여줍니다. 다이캐스팅 공정 동안 이 방법은 Al 합금의 기계적 거동을 예측하는 능력을 보여줍니다.
3. 연구 배경:
연구 주제 배경:
다이캐스팅 알루미늄(Al) 합금은 자동차 및 항공 우주 산업에서 경량화를 위해 사용됩니다[1]. 고압 다이캐스팅(HPDC)은 Al 합금 부품의 핵심 제조 공정입니다[2, 3]. 그러나 다공성 유형 결함은 제품의 기계적 특성에 영향을 줄 수 있습니다[4, 5]. 다공성의 존재는 미세 구조적 불연속성을 초래하여 외부 하중이 가해질 때 국부적인 응력 집중 가능성을 증가시킵니다[6-8].
선행 연구 현황:
많은 연구자들이 미세 결함이 거시적 기계적 특성에 미치는 영향을 조사하기 위해 실험 및 유한 요소 시뮬레이션을 조합하여 사용했습니다[12].
- Sun[13]은 AM50 합금의 인장 특성 및 파괴 거동에 대한 미세 다공성의 영향을 조사했습니다.
- Jiang[14]은 HPDC AZ91 마그네슘 합금의 다공성과 기계적 특성 간의 관계를 조사했습니다.
- Zhang[7]은 실제 결함을 기반으로 3D 유한 요소 모델을 개발했습니다.
- Zhang[16]은 수치 시뮬레이션 및 DIC 테스트를 사용하여 불균일 구조의 변형 및 파괴 거동을 검증했습니다.
- Zhang[17]은 Al-10 Si-0.3 Mg 부품에서 다공성의 공간 분포 및 형태학적 특성과 소성에 미치는 영향을 조사했습니다.
- Sun[20]은 다양한 작업 조건에서 다공성, 기공 크기 및 분포가 손상 효과에 미치는 영향을 시뮬레이션했습니다.
- Ma[21]는 다이캐스팅 Al 합금의 구성 방정식을 확립했습니다.
- 수많은 연구에서 미세 구조 불균일성이 재료의 손상 개시 거동에 영향을 미치는 핵심 요소임을 보여주었습니다[22-26].
연구 필요성:
경계 조건 및 거시적 요인으로 인해 유한 요소 시뮬레이션의 정확도를 향상시킬 필요가 있습니다.
4. 연구 목적 및 연구 질문:
연구 목적:
본 연구는 복합 응력 상태에서 주조 Al 합금의 손상 개시 균열에 초점을 맞추고 실험 분석과 전산 모델링을 결합한 프레임워크를 제안합니다.
핵심 연구:
- X선 CT 기법을 사용하여 HPDC 부품 기공의 3차원 특성을 정량적으로 연구합니다.
- 국부 다공성, 기공 크기 및 위치가 소성에 미치는 영향을 분석합니다.
- X선 CT 기술로 캡처한 내부 기공 이미지를 기반으로 역 모델링을 수행합니다.
- 실제 결함 분포를 기반으로 한 모델의 수치 결과를 DIC 측정에서 얻은 국부 응력/변형 거동과 비교합니다.
- 3D 미세 구조의 탄소성 변형 및 RVE 모델의 이론적 프레임워크를 확립하여 주기적 경계 조건에서 변형 및 손상 프로세스를 시뮬레이션합니다.
5. 연구 방법
연구 프레임워크는 Fig. 1에 제시되어 있습니다. 연구는 세 가지 주요 부분으로 나뉩니다.
- 결함 분석: X선 CT 스캔을 사용하여 결함의 크기와 공간 분포를 정량적으로 분석합니다.
- 역 모델링 및 시뮬레이션: 내부 기공(X선 CT에서)의 3D 이미지를 사용하여 실제 결함 분포를 가진 솔리드 모델을 생성합니다. 결함과 기계적 특성 간의 관계는 시뮬레이션을 통해 탐구되어 파괴 메커니즘을 설명합니다.
- RVE 모델링: RVE 모델은 주기적 경계 조건에서 변형 및 손상 프로세스를 시뮬레이션하기 위해 구축되었습니다.
실험 방법:
- 재료 선택: 비열처리 다이캐스팅 Al 합금(Al-9Si, Al-7Si)이 선택되었습니다. 화학 조성은 유도 결합 플라즈마 방출 분광계(PerkinElmer Optima 8300)를 사용하여 결정되었습니다(Table 1).
- HPDC 실험: YIZUMI LEAP 7000T 수평 냉각 챔버 다이캐스팅 기계가 사용되었습니다. 공정 매개변수는 Fig. 2에 자세히 설명되어 있습니다.
- X선 CT 스캔 및 역 모델링: X선 CT(XPloreVista 2000 4D)는 ASTM E505, ASTM E2422 및 CASE 301-2023 표준에 따라 기공 크기, 형태 및 위치를 탐색하는 데 사용되었습니다. 역 모델링 프로세스는 AVIZO 및 ABAQUS 소프트웨어의 단계를 포함하여 Fig. 3에 설명되어 있습니다.
- 인장 시험 및 DIC 시험: 인장 시험은 MTS C45.305EEEY 기계를 사용하여 수행되었습니다. HAYTHAM DV 1200-32 시스템은 변위 측정에 사용되었습니다. 디지털 이미지 상관(DIC)은 변형 분포를 기공 변형과 연관시키는 데 사용되었습니다.
- 탄소성 재료 거동 법칙:
J2 등방성 탄소성 모델은 Al 매트릭스의 고유한 거동을 조사하는 데 사용되었습니다.
Eq. (1)에 따르면, n 값은 0.15이고 K 값은 356으로 맞춰질 수 있습니다.
6. 주요 연구 결과:
주요 연구 결과 및 제시된 데이터 분석:
- 다공성 특성화: X선 CT 스캔은 결함의 공간 분포와 형태를 보여주었습니다(Fig. 5). 결함은 부피와 구형도(Eq. 2)에 따라 가스 기공, 수축 기공, 가스-수축 기공으로 분류되었습니다[32-34]. 대부분의 결함은 가스 기공으로 확인되었습니다. 부피와 구형도, 부피와 투영 면적 간의 관계는 Fig. 6에 나와 있습니다.
- 실제 결함을 사용한 소성 변형 분석: 실제 기공 특성을 가진 체적 메쉬가 유한 요소 시뮬레이션에 사용되었습니다. Fig. 7은 시뮬레이션 흐름도와 결과를 보여줍니다. 시뮬레이션 모델은 매트릭스 취성 파괴 모드를 정확하게 예측했습니다.
- 시뮬레이션과 실험 비교: 시뮬레이션 및 실험 파괴 결과가 비교되었습니다(Table 2, Fig. 8). 실제 결함 분포를 가진 CAE 모델은 결함이 없는 모델에 비해 향상된 정확도를 보였습니다.
- 변형 및 미세 균열 형성 메커니즘: 가스 기공의 변형과 미세 균열 형성 메커니즘은 Fig. 9에 나와 있습니다. 균열 확장은 두 가지 모드의 미세 다공성 응집을 통해 발생합니다.
- 기공 특성과 국부 변형률 간의 관계: DIC 분석은 결함 분포와 상관관계가 있는 국부적인 고변형률 영역을 보여주었습니다(Fig. 10).
- 3D 미세 규모 RVE 모델 개발:
Digimat 소프트웨어를 사용하여 주조 Al 합금의 3D RVE 모델을 생성했습니다. RVE 모델의 설정 매개변수는 Fig. 11(a)에 나와 있습니다. - 대표 체적 요소 예측:
다양한 기공 체적 분율을 가진 RVE 모델과 시뮬레이션 결과는 Fig. 13에 나와 있습니다.
Fig. 14는 다양한 체적 다공성에서 기공 변형 및 손상의 개략도를 보여줍니다.
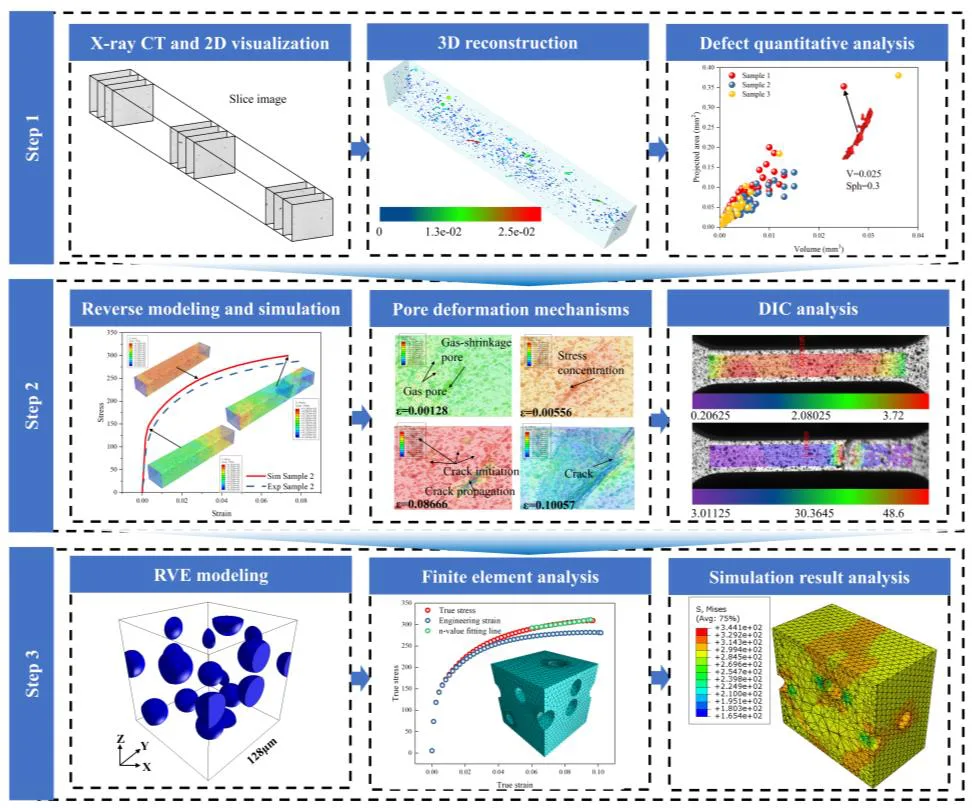
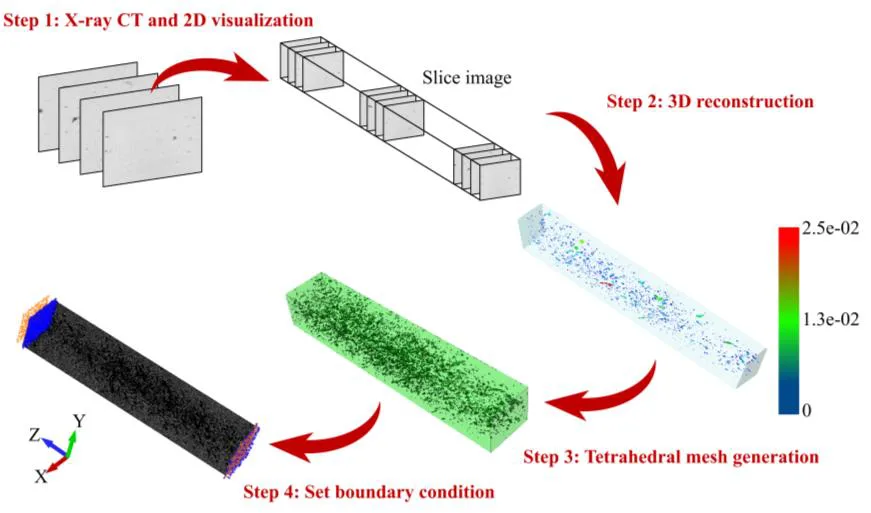
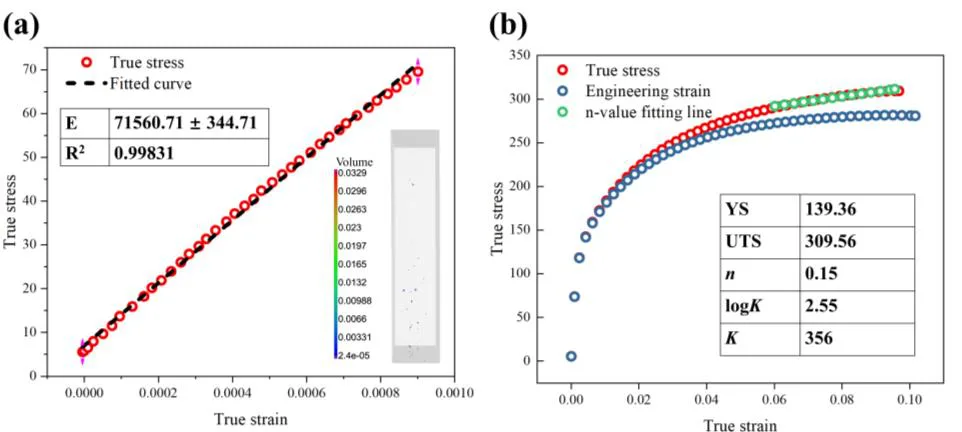
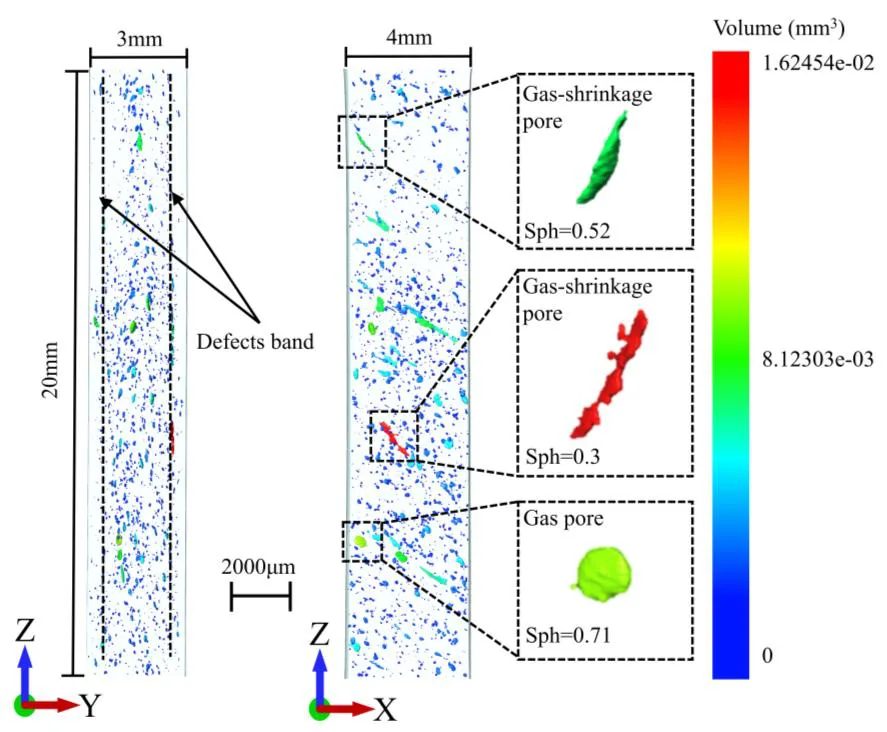
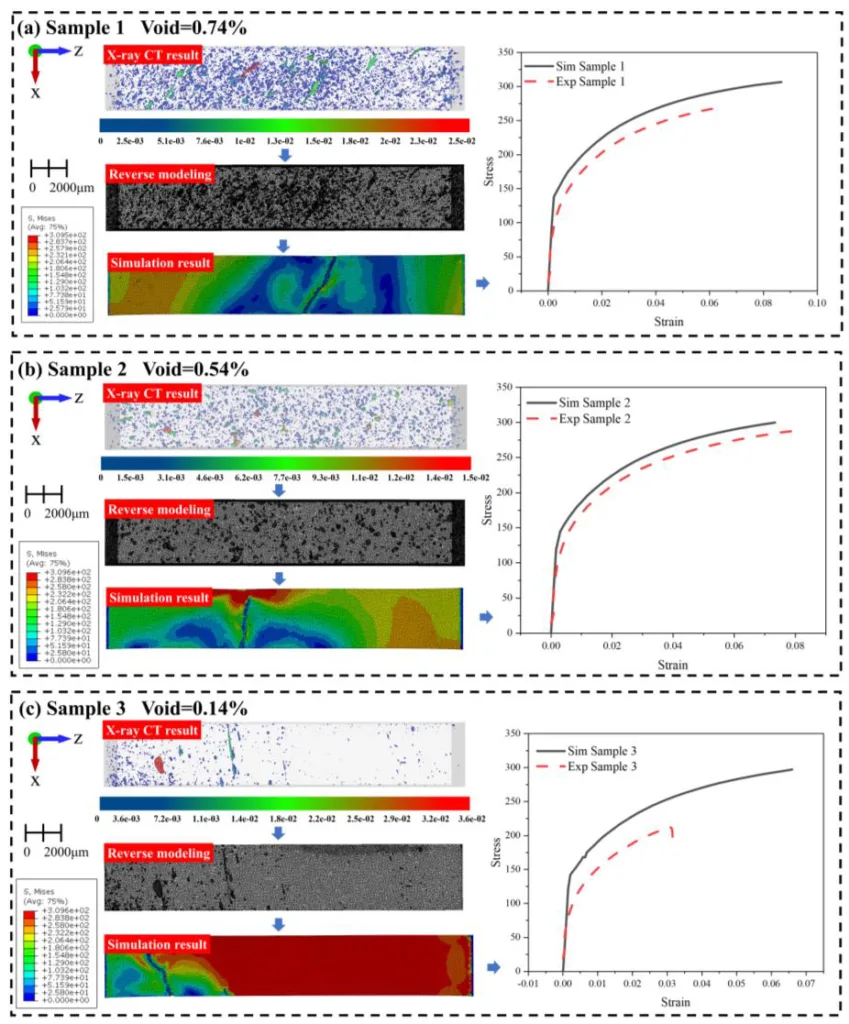
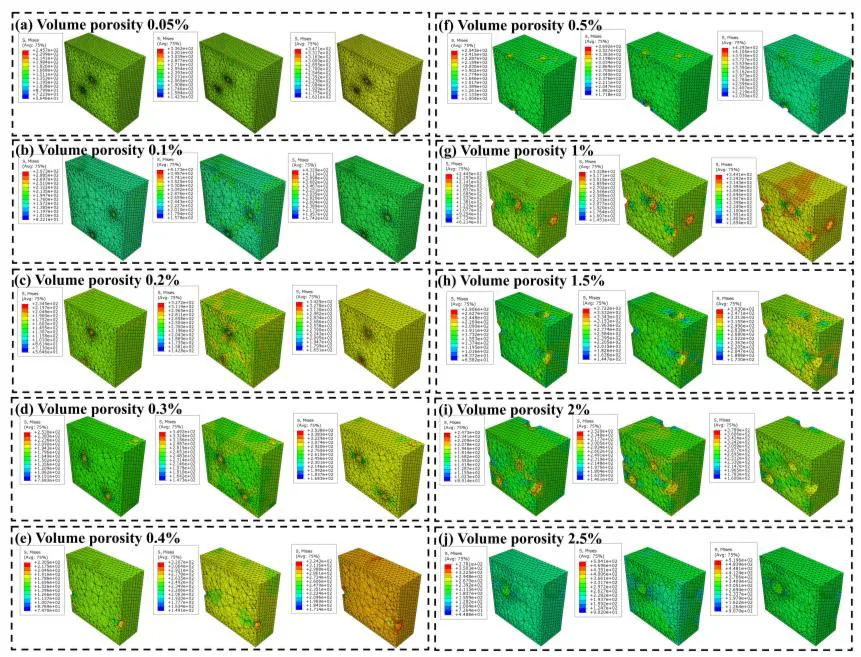
그림 이름 목록:
- Figure 1: Research idea framework for this study. (본 연구를 위한 연구 아이디어 프레임워크)
- Figure 2: Part structure, dimensions and process parameters. (부품 구조, 치수 및 공정 매개변수)
- Figure 3: Inverse modelling method for finite element volumetric meshing and method of setting boundary conditions. (유한 요소 체적 메싱을 위한 역 모델링 방법 및 경계 조건 설정 방법)
- Figure 4: Elastic-plastic material behavior law. (탄소성 재료 거동 법칙)
- Figure 5: Spatial distribution and morphological characteristics of defects (결함의 공간 분포 및 형태학적 특성)
- Figure 6: Quantitative statistical analysis of defects. (결함의 정량적 통계 분석)
- Figure 7: Inverse modelling steps and simulation analysis results. (역 모델링 단계 및 시뮬레이션 분석 결과)
- Figure 8: Mechanical property data and statistical results. (기계적 특성 데이터 및 통계 결과)
- Figure 9: Deformation and microcrack formation mechanism of gas pores. (가스 기공의 변형 및 미세 균열 형성 메커니즘)
- Figure 10: Simulation, tensile experiment and DIC analysis. (시뮬레이션, 인장 실험 및 DIC 분석)
- Figure 11: Setting parameters of the RVE model. (RVE 모델의 설정 매개변수)
- Figure 12: Schematic representation of the periodic boundary conditions. (주기적 경계 조건의 개략도)
- Figure 13: RVE models with different porosities and simulation results. (다양한 다공성을 가진 RVE 모델 및 시뮬레이션 결과)
- Figure 14: Schematic representation of porosity deformation and damage at different porosities. (다양한 다공성에서의 다공성 변형 및 손상 개략도)
7. 결론:
주요 결과 요약:
- X선 CT와 역 모델링을 사용하여 실제 기공 형태를 가진 3D 모델을 얻었습니다. 결함이 없는 모델에 비해 시뮬레이션 정확도가 크게 향상되었습니다.
- 시뮬레이션 모델은 인장 파괴 중 매트릭스 취성 파괴 모드를 정확하게 예측했습니다. 응집된 다공성은 내부 네킹 및 응력 집중으로 인해 균열을 생성합니다.
- 3D RVE 모델이 개발되어 유한 요소 탄소성 변형 프레임워크와 통합되었습니다. 다공성이 증가하면 국부 영역에 비정상적인 소성 변형 축적이 발생합니다.
- 이 방법은 기공 발생 메커니즘, 파괴 모드 및 다이캐스팅 Al 합금의 거시적 특성 예측 연구에 중요한 이점을 제공합니다.
8. 참고 문헌:
- [1] J. Allison, M. Li, C. Wolverton, and X. Su, "Virtual aluminum castings: an industrial application of ICME," Jom, vol. 58, pp. 28-35, 2006.
- [2] S. Dash, D. Li, X. Zeng, and D. Chen, "Heterogeneous microstructure and deformation behavior of an automotive grade aluminum alloy," Journal of Alloys and Compounds, vol. 870, p. 159413, 2021.
- [3] T. Li et al., "Progress and prospects in Mg-alloy super-sized high pressure die casting for automotive structural components," Journal of Magnesium and Alloys, 2023.
- [4] X. Hu and L. Xie, "FEA Simulations of Temperature Changes of Castings When Solidified and Cooled in Mould," in Advances in Computer Science and Education Applications: International Conference, CSE 2011, Qingdao, China, July 9-10, 2011. Proceedings, Part II, 2011: Springer, pp. 178-183.
- [5] Q. Pan, L. Zheng, Y. Sang, Y. Li, L. Zhou, and H. Zhang, "Effect of casting temperature on microstructure in a directionally solidified Ni-44Ti-5Al-2Nb-1Mo alloy," Rare Metals, vol. 30, pp. 349-353, 2011.
- [6] Y. Tijani, A. Heinrietz, T. Bruder, and H. Hanselka, "Quantitative evaluation of fatigue life of cast aluminum alloys by non-destructive testing and parameter model," International journal of fatigue, vol. 57, pp. 73-78, 2013.
- [7] Y. Zhang et al., "Analysis of local stress/strain fields in an HPDC AM60 plate containing pores with various characteristics," Engineering Failure Analysis, vol. 127, p. 105503, 2021.
- [8] G. Nicoletto, R. Konečná, and S. Fintova, "Characterization of microshrinkage casting defects of Al-Si alloys by X-ray computed tomography and metallography," International journal of fatigue, vol. 41, pp. 39-46, 2012.
- [9] Y. Zhang et al., "The gradient microstructure and deformation heterogeneity in HPDC AM60 alloy," Materials Science and Engineering: A, vol. 792, p. 139647, 2020.
- [10] J. H. Forsmark, J. W. Zindel, L. Godlewski, J. Zheng, J. E. Allison, and M. Li, "Using quality mapping to predict spatial variation in local properties and component performance in Mg alloy thin-walled high-pressure die castings: an ICME approach and case study," Integrating Materials and Manufacturing Innovation, vol. 4, pp. 81-118, 2015.
- [11] G. Hahn and A. Rosenfield, "Metallurgical factors affecting fracture toughness of aluminum alloys," Metallurgical Transactions A, vol. 6, pp. 653-668, 1975.
- [12] M. Luetje, M. Wicke, I. Bacaicoa, A. Brueckner-Foit, A. Geisert, and M. Fehlbier, "3D characterization of fatigue damage mechanisms in a cast aluminum alloy using X-ray tomography," International Journal of Fatigue, vol. 103, pp. 363-370, 2017.
- [13] X. Sun, Z. Cao, H. Liu, W. Jiang, and L. Liu, "Predicting the influence of microporosity on the mechanical properties and fracture behavior of high-pressure die-cast AM50 magnesium alloy," Applied Mechanics and Materials, vol. 670, pp. 90-94, 2014.
- [14] W. Jiang, Z. Cao, X. Sun, and H. Liu, "Three-dimensional microstructure reconstruction and finite element simulation of gas pores in the high-pressure die-casting AZ91 Mg alloy," Microscopy and Microanalysis, vol. 21, no. 6, pp. 1420-1425, 2015.
- [15] Y. Zhang et al., "Porosity quantification for ductility prediction in high pressure die casting AM60 alloy using 3D X-ray tomography," Materials Science and Engineering: A, vol. 772, p. 138781, 2020.
- [16] Y. Zhang et al., "Ductility prediction of HPDC aluminum alloy using a probabilistic ductile fracture model," Theoretical and Applied Fracture Mechanics, vol. 119, p. 103381, 2022.
- [17] Y. Zhang et al., "Quantitative analysis of 3D pore characteristics effect on the ductility of HPDC Al-10Si-0.3 Mg alloy through X-ray tomography," Journal of Materials Research and Technology, vol. 26, pp. 8079-8096, 2023.
- [18] S. Isavand and A. Assempour, "Strain localization and deformation behavior in ferrite-pearlite steel unraveled by high-resolution in-situ testing integrated with crystal plasticity simulations," International Journal of Mechanical Sciences, vol. 200, p. 106441, 2021.
- [19] S. Isavand and A. Assempour, "Effects of microstructural morphology on formability, strain localization, and damage of ferrite-pearlite steels: experimental and micromechanical approaches," Metallurgical and Materials Transactions A, vol. 52, pp. 711-725, 2021.
- [20] D. Z. Sun, Y. S. Ma, and F. Andrieux, "Modeling of the influence of pore morphology on damage behavior of an aluminum die casting alloy," in Materials Science Forum, 2014, vol. 794: Trans Tech Publ, pp. 319-324.
- [21] Y.-S. Ma, D.-Z. Sun, F. Andrieux, and K.-S. Zhang, "Influences of initial porosity, stress triaxiality and Lode parameter on plastic deformation and ductile fracture," acta mechanica solida sinica, vol. 30, pp. 493-506, 2017.
- [22] J. Lian, H. Yang, N. Vajragupta, S. Münstermann, and W. Bleck, "A method to quantitatively upscale the damage initiation of dual-phase steels under various stress states from microscale to macroscale," Computational materials science, vol. 94, pp. 245-257, 2014.
- [23] Y. Abdin, S. Lomov, A. Jain, G. Van Lenthe, and I. Verpoest, "Geometrical characterization and micro-structural modeling of short steel fiber composites," Composites Part A: Applied Science and Manufacturing, vol. 67, pp. 171-180, 2014.
- [24] S. A. H. Motaman, F. Roters, and C. Haase, "Anisotropic polycrystal plasticity due to microstructural heterogeneity: A multi-scale experimental and numerical study on additively manufactured metallic materials," Acta Materialia, vol. 185, pp. 340-369, 2020.
- [25] S. J. Wolff, S. Lin, E. J. Faierson, W. K. Liu, G. J. Wagner, and J. Cao, "A framework to link localized cooling and properties of directed energy deposition (DED)-processed Ti-6Al-4V," Acta Materialia, vol. 132, pp. 106-117, 2017.
- [26] S. Isavand, M. Kardan-Halvaei, and A. Assempour, "Crystal plasticity modeling and experimental characterization of strain localization and forming limits in ferrite-pearlite steels," International Journal of Solids and Structures, vol. 233, p. 111205, 2021.
- [27] R. Liu et al., "Influence of pore characteristics and eutectic particles on the tensile properties of Al-Si-Mn-Mg high pressure die casting alloy," Materials Science and Engineering: A, vol. 783, p. 139280, 2020.
- [28] T. Li et al., "Anisotropic cyclic deformation behavior of an extruded Mg-3Y alloy sheet with rare earth texture," Journal of Magnesium and Alloys, vol. 10, no. 6, pp. 1581-1597, 2022.
- [29] Y. Xia et al., "The ductility variation of high-pressure die-cast AE44 alloy: the role of inhomogeneous microstructure," Metallurgical and Materials Transactions A, vol. 52, pp. 2274-2286, 2021.
- [30] Z. Li et al., "Characterization on the formation of porosity and tensile properties prediction in die casting Mg alloys," Journal of Magnesium and Alloys, vol. 10, no. 7, pp. 1857-1867, 2022.
- [31] E. Fiorese, F. Bonollo, G. Timelli, L. Arnberg, and E. Gariboldi, "New classification of defects and imperfections for aluminum alloy castings," International Journal of Metalcasting, vol. 9, pp. 55-66, 2015.
- [32] D. Cocks, "A proposed simple qualitative classification for die-casting defects," in Proc. Diecasting Conference, Montreaux, 1996, p. 19.
- [33] J. Campbell, Castings. Elsevier, 2003.
- [34] W. G. Walkington, Die casting defects.. Causes and solutions. NADCA, 1997.
- [35] M. Avalle, G. Belingardi, M. P. Cavatorta, and R. Doglione, "Casting defects and fatigue strength of a die cast aluminium alloy: a comparison between standard specimens and production components," International journal of Fatigue, vol. 24, no. 1, pp. 1-9, 2002.
- [36] S. G. Lee and A. M. Gokhale, "Formation of gas induced shrinkage porosity in Mg-alloy high-pressure die-castings," Scripta Materialia, vol. 55, no. 4, pp. 387-390, 2006.
- [37] E. Lordan et al., "On the probabilistic nature of high-pressure die casting," Materials Science and Engineering: A, vol. 817, p. 141391, 2021.
- [38] Y.-T. Yang et al., "Al-enabled properties distribution prediction for high-pressure die casting Al-Si alloy," Advances in Manufacturing, pp. 1-12, 2024.
- [39] M. M. Thakur, N. A. Henningsson, J. Engqvist, P.-O. Autran, J. P. Wright, and R. C. Hurley, "On mesoscale modeling of concrete: Role of heterogeneities on local stresses, strains, and representative volume element," Cement and Concrete Research, vol. 163, p. 107031, 2023.
- [40] W. Zhang, H. Jing, L. Xu, L. Zhao, Y. Han, and C. Li, "Numerical investigation of creep crack initiation in P92 steel pipes with embedded spherical defects under internal pressure at 650° С," Engineering Fracture Mechanics, vol. 139, pp. 40-55, 2015.
- [41] V. Poroshin and A. Shlishevsky, "The forecasting of deformational and strength properties of metals with uniformly scattered defects in form of spherical hollows at single and cyclic loading," Materials Today: Proceedings, vol. 11, pp. 58-65, 2019.
- [42] F. Klein and P. Wimmer, "Experimental Determination of the Influence of Casting Conditions on the Solidifaction of Zinc Die Castings," in Materials Science Forum, 1996, vol. 215: Trans Tech Publ, pp. 409-414.
- [43] J. Weiler and J. Wood, "Modeling the tensile failure of cast magnesium alloys," Journal of alloys and compounds, vol. 537, pp. 133-140, 2012.
- [44] S. Mohd, Y. Mutoh, Y. Otsuka, Y. Miyashita, T. Koike, and T. Suzuki, "Scatter analysis of fatigue life and pore size data of die-cast AM60B magnesium alloy," Engineering Failure Analysis, vol. 22, pp. 64-72, 2012.
- [45] F. Nichols, "Plastic instabilities and uniaxial tensile ductilities," Acta metallurgica, vol. 28, no. 6, pp. 663-673, 1980.
- [46] J. Lian and J. Chen, "Plastic instability and strain to fracture for damaged materials," Materials Science and Engineering: A, vol. 131, no. 1, pp. 9-15, 1991.
- [47] C. Hamilton, "Superplasticity," in Strength of Metals and Alloys (ICSMA 7): Elsevier, 1986, pp. 1831-1857.
- [48] I. Serrano-Munoz, J.-Y. Buffiere, C. Verdu, Y. Gaillard, P. Mu, and Y. Nadot, "Influence of surface and internal casting defects on the fatigue behaviour of A357-T6 cast aluminium alloy," International Journal of Fatigue, vol. 82, pp. 361-370, 2016.
- [49] Z. Xu, W. Wen, and T. Zhai, "Effects of pore position in depth on stress/strain concentration and fatigue crack initiation," Metallurgical and Materials Transactions A, vol. 43, pp. 2763-2770, 2012.
- [50] Y. Zhang et al., "Microstructure-property relationships in HPDC Aural-2 alloy: Experimental and CP modeling approaches," Materials Science and Engineering: A, vol. 848, p. 143364, 2022.
- [51] P. M. Carneiro, P. V. Gamboa, C. Baudín, and A. P. Silva, "Modelling of elastic modulus of a biphasic ceramic microstructure using 3D representative volume elements," Journal of the European Ceramic Society, vol. 40, no. 3, pp. 901-910, 2020.
- [52] G. Chen, A. Bezold, and C. Broeckmann, "Influence of the size and boundary conditions on the predicted effective strengths of particulate reinforced metal matrix composites (PRMMCs)," Composite Structures, vol. 189, pp. 330-339, 2018.
- [53] Q. Sun, S. Asqardoust, A. Sarmah, and M. K. Jain, "Elastoplastic analysis of AA7075-0 aluminum sheet by hybrid micro-scale representative volume element modeling with really-distributed particles and in-situ SEM experimental testing," Journal of Materials Science & Technology, vol. 123, pp. 201-221, 2022.
- [54] A. Moumen, M. Jammoukh, L. Zahiri, and K. Mansouri, "Numerical modeling of the thermo mechanical behavior of a polymer reinforced by horn fibers," Int. J, vol. 9, no. 4, 2020.
- [55] V. Felli, B. Noris, and R. Ognibene, "Eigenvalues of the Laplacian with moving mixed boundary conditions: the case of disappearing Dirichlet region," Calculus of Variations and Partial Differential Equations, vol. 60, pp. 1-33, 2021.
- [56] E. Totry, C. González, and J. LLorca, "Failure locus of fiber-reinforced composites under transverse compression and out-of-plane shear," Composites Science and Technology, vol. 68, no. 3-4, pp. 829-839, 2008.
- [57] Q. Sun et al., "Failure criteria of unidirectional carbon fiber reinforced polymer composites informed by a computational micromechanics model," Composites Science and Technology, vol. 172, pp. 81-95, 2019.
- [58] S. L. Kramer et al., "The third Sandia Fracture Challenge: predictions of ductile fracture in additively manufactured metal," International Journal of Fracture, vol. 218, pp. 5-61, 2019.
- [59] D. P. Naragani, J.-S. Park, P. Kenesei, and M. D. Sangid, "Void coalescence and ductile failure in IN718 investigated via high-energy synchrotron X-ray tomography and diffraction," Journal of the Mechanics and Physics of Solids, vol. 145, p. 104155, 2020.
- [60] O. West, J. Lian, S. Münstermann, and W. Bleck, "Numerical determination of the damage parameters of a dual-phase sheet steel," ISIJ international, vol. 52, no. 4, pp. 743-752, 2012.
- [61] V. Brinnel, J. Langenberg, F. Kordtomeikel, Y. Di, and S. Münstermann, "Numerical derivation of strain-based criteria for ductile failure: Discussions on sensitivity and validity," Engineering Fracture Mechanics, vol. 148, pp. 421-440, 2015.
9. 저작권:
- 본 자료는 "Jian Yang, Bo Liu, Dongwei Shu, Qin Yang, Tiegang Hu"의 논문 "Local stress/strain field analysis of die-casting Al alloys via 3D model simulation with realistic defect distribution and RVE modelling"을 기반으로 합니다.
- 논문 출처: https://ssrn.com/abstract=4968855
본 자료는 위 논문을 소개하기 위해 작성되었으며, 상업적 목적으로 무단 사용하는 것을 금합니다. Copyright © 2025 CASTMAN. All rights reserved.