본 논문 요약은 [ASME 2018 국제 제조 과학 및 엔지니어링 컨퍼런스]에서 발표된 논문 [An Automated System for Design for Manufacturability Analysis for Die-Casting]을 기반으로 작성되었습니다.
1. 개요:
- 제목: 다이캐스팅 공정의 제조 용이성 분석을 위한 자동화 시스템 (An Automated System for Design for Manufacturability Analysis for Die-Casting)
- 저자: 수닐 쿠마 (Sunil Kumar), 자틴더 마단 (Jatinder Madan)
- 발행 연도: 2018년 6월
- 발행 저널/학회: ASME 2018 국제 제조 과학 및 엔지니어링 컨퍼런스 (Proceedings of the ASME 2018 International Manufacturing Science and Engineering Conference)
- 키워드: 제조 용이성 설계 (Design for manufacturability), 다이캐스팅 (die-casting), 지식 기반 (knowledgebase), 특징 추출 (feature extraction), 모델 업데이트 (model updation)
![FIGURE 1: SCHEMATIC OF A DIE CASTING DIE [1]](https://castman.co.kr/wp-content/uploads/FIGURE-1-SCHEMATIC-OF-A-DIE-CASTING-DIE-1-1024x466.webp)
2. 연구 배경:
- 연구 주제의 사회적/학문적 맥락: 제조 용이성 설계 (DFM)는 설계 초기 단계에서 제조 가능성을 고려하는 데 중요한 개념입니다. 특히 설계와 제조가 서로 다른 팀, 종종 멀리 떨어진 팀에 의해 수행될 때 자동화된 DFM 도구 개발의 중요성이 커지고 있습니다.
- 기존 연구의 한계: 기존의 제조 용이성 확보 방식은 제조 전문가와의 반복적인 상담에 의존합니다. 이러한 반복 과정은 설계 리드 타임을 늘리고, 생산 비용을 증가시키며, 시장 출시 시간을 지연시켜 조직의 수익성에 부정적인 영향을 미칩니다. 기존의 다이캐스팅 DFM 시스템은 자동화된 분석 및 제조 용이성 조언 적용에 대한 요구를 완전히 해결하지 못했습니다. 특히 포괄적인 지식 기반, CAD 모델로부터의 효율적인 특징 추출, DFM 분석에 기반한 자동 모델 업데이트를 제공하는 시스템이 부족합니다.
- 연구의 필요성: 기존 DFM 및 기존 시스템의 한계를 극복하기 위해 다이캐스팅 공정을 위한 자동화된 DFM 시스템이 필요합니다. 이러한 시스템은 제조 용이성 조언을 생성하고 부품 설계를 자동으로 수정하여 설계 반복, 리드 타임 및 생산 비용을 줄일 수 있습니다.
3. 연구 목적 및 연구 질문:
- 연구 목적: 본 연구의 주요 목적은 특히 다이캐스팅 부품의 제조 용이성 분석을 위한 자동화 시스템을 제시하는 것입니다.
- 주요 연구 질문: 본 논문은 다음을 어떻게 해결할 수 있는지에 대해 다룹니다.
- 다이캐스팅 공정을 위한 DFM 지침의 지식 기반을 개발하는 방법
- 부품 CAD 모델로부터 다이캐스팅 특징을 추출하는 방법
- 다이캐스팅 부품 CAD 모델의 DFM 분석 및 모델 업데이트를 위한 자동화 시스템을 구축하는 방법
- 연구 가설: 명시적으로 가설로 제시되지는 않았지만, 본 연구는 자동화된 DFM 시스템이 다이캐스팅 부품 설계를 효과적으로 분석하고, 제조 용이성 조언을 제공하며, CAD 모델을 자동으로 업데이트하여 제조 용이성을 개선하고 재료 사용량을 줄일 수 있다는 전제하에 진행됩니다.
4. 연구 방법론:
- 연구 설계: 본 연구는 자동화된 DFM 시스템 개발을 포함합니다. 여기에는 DFM 지침의 지식 기반 구축, 특징 추출 방법론 개발, CAD 모델 분석 및 설계 수정 제안이 가능한 시스템으로 이러한 구성 요소를 통합하는 것이 포함됩니다.
- 자료 수집 방법: 시스템의 기능은 다이캐스팅 부품 CAD 모델에 적용하여 시연하고 검증합니다. 결과는 산업 전문가와의 상담을 통해 검증됩니다.
- 분석 방법: 시스템은 특징 매개변수를 추출하고 DFM 지식 기반과 비교하여 CAD 모델을 분석합니다. 시스템의 효과는 생성된 제조 용이성 조언, 자동화된 모델 업데이트 및 그에 따른 부품 무게 변화를 평가하여 평가합니다.
- 연구 대상 및 범위: 시스템은 특징 기반 모델링을 사용하여 생성되었으며 보스, 립, 구멍 및 드래프트와 같은 특징을 포함하는 다이캐스팅 부품의 CAD 모델에서 작동하도록 설계되었습니다.
5. 주요 연구 결과:
- 주요 연구 결과: 본 논문은 다이캐스팅 공정을 위한 자동화된 DFM 분석 시스템을 성공적으로 제시했습니다. 시스템은 다음을 포함합니다.
- DFM 지침의 지식 기반
- 부품 CAD 모델로부터의 다이캐스팅 특징 추출
- 자동화된 DFM 분석 및 모델 업데이트 시스템
시스템의 기능은 다이캐스팅 부품 CAD 모델에서 시연되었으며, 결과는 산업 전문가에 의해 검증되었습니다.
- 통계적/질적 분석 결과:
- 예시 부품에 시스템을 적용한 결과 상당한 재료 절감 효과가 나타났습니다. "부품 모델-1"의 경우 재료 절감률은 약 35%였습니다. "부품 모델-2"의 경우 재료 절감률은 약 37%였습니다. 이러한 절감은 주로 벽 두께를 줄이고 특징을 최적화하여 DFM 조언에 기반한 자동 재설계를 통해 달성되었습니다.
- 전문가 검증은 시스템의 조언 및 모델 업데이트의 실제 관련성과 효과를 확인했습니다.
- 데이터 해석: 자동화된 DFM 시스템은 다이캐스팅 부품 설계에서 제조 용이성 문제를 효과적으로 식별하고 실행 가능한 조언을 제공하며, 이는 CAD 모델을 업데이트하는 데 자동으로 구현될 수 있습니다. 이는 제조 용이성 향상 및 재료 소비 감소로 이어집니다.
- 그림 목록:
- FIGURE 1: SCHEMATIC OF A DIE CASTING DIE [1] (다이캐스팅 금형의 개략도 [1])
- FIGURE 2: DIE-CASTING FEATURE TERMINOLOGY (다이캐스팅 특징 용어)
- FIGURE 3: FEATURE EXTRACTION (특징 추출)
- FIGURE 4: FEATURE PARAMETERS (특징 매개변수)
- FIGURE 5: THE PROPOSED DFM SYSTEM (제안된 DFM 시스템)
- FIGURE 6: FEATURE BASED PART MODELS (특징 기반 부품 모델)
- FIGURE 7: EXISTING AND REDESIGNED FEATURE BASED PART MODEL-1 (기존 및 재설계된 특징 기반 부품 모델-1)
- FIGURE 8: EXISTING AND REDESIGNED FEATURE BASED PART MODEL-2 (기존 및 재설계된 특징 기반 부품 모델-2)
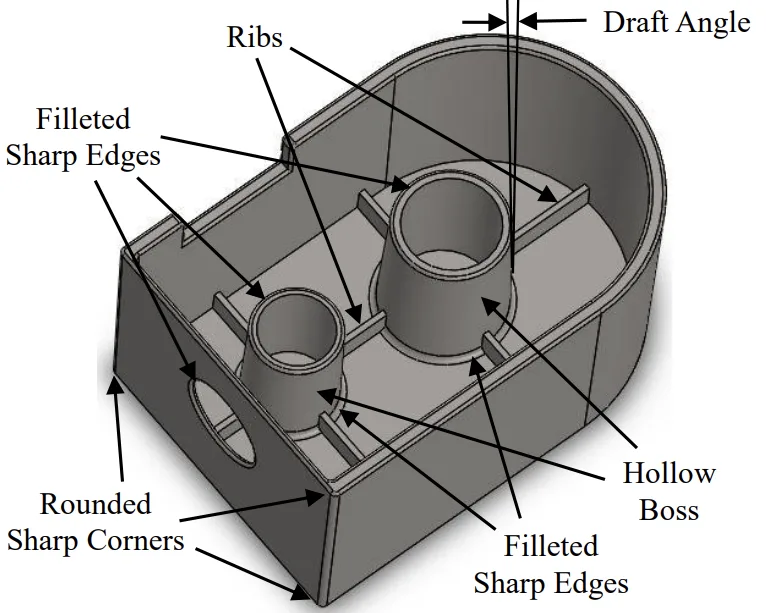
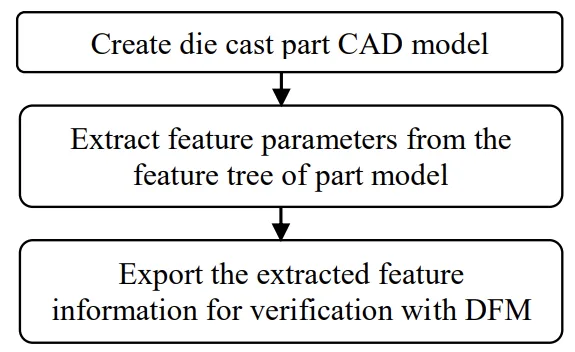
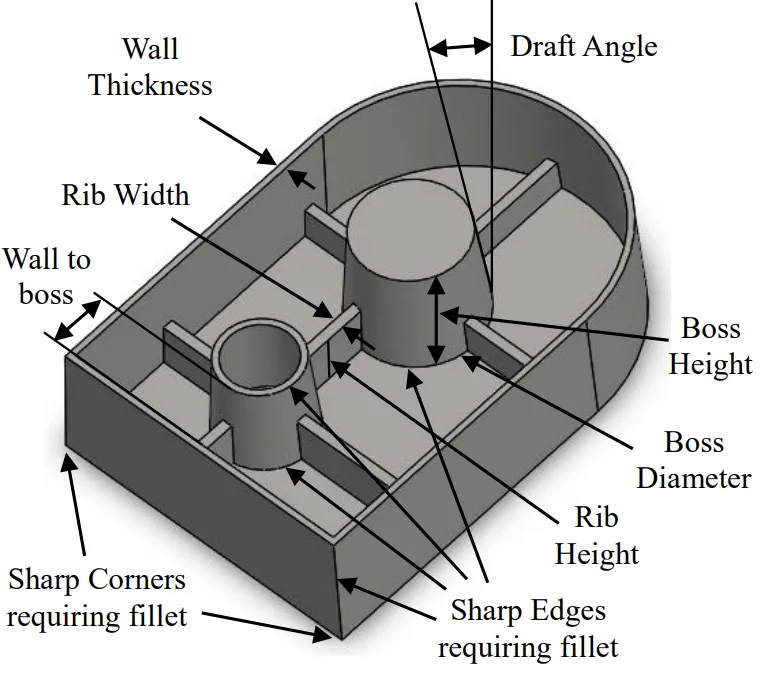
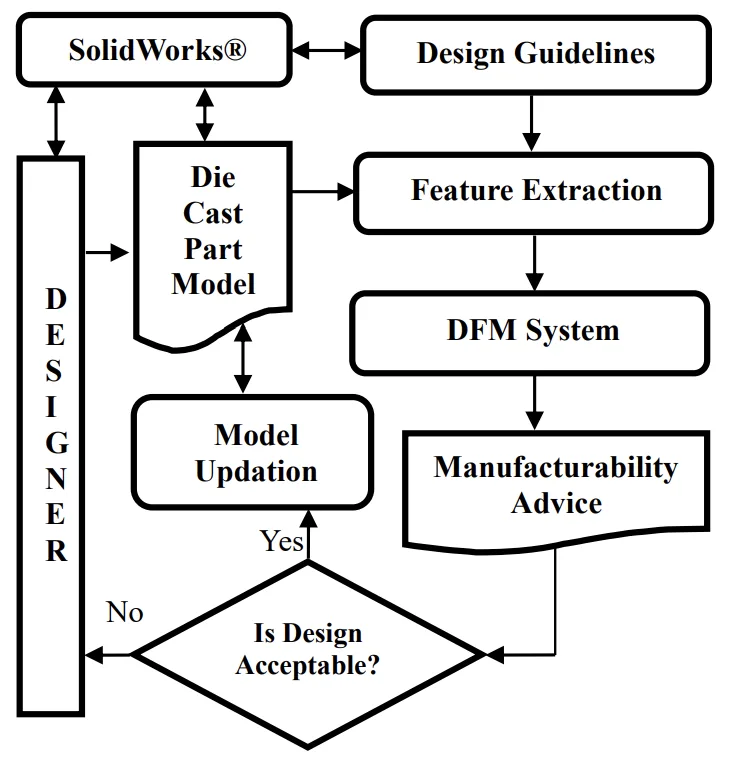
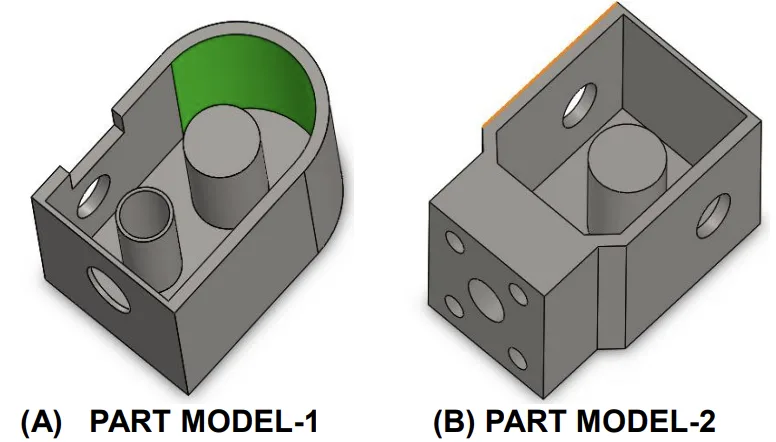
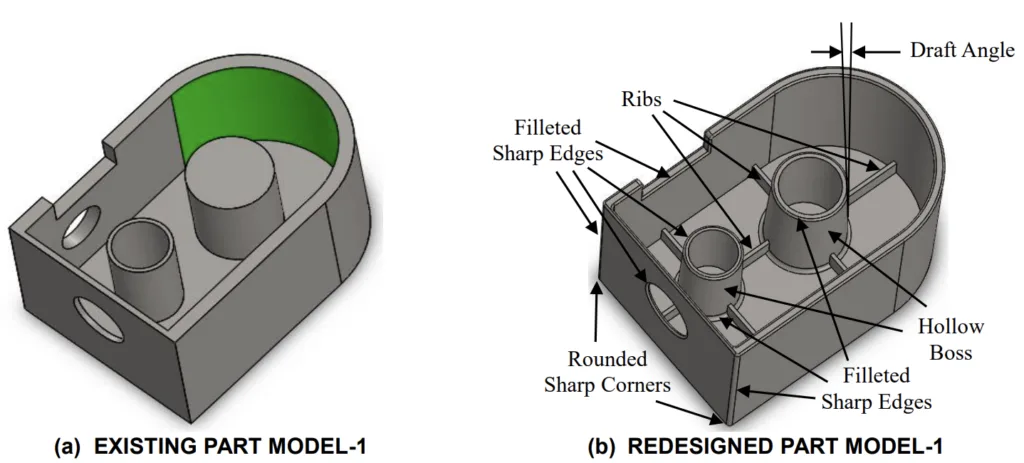
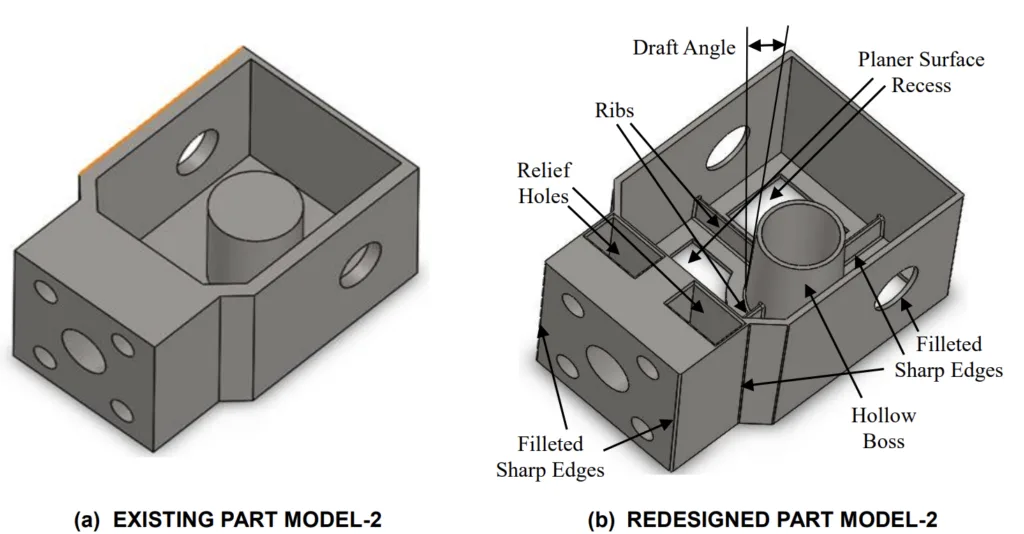
6. 결론 및 논의:
- 주요 결과 요약: 본 연구는 다이캐스팅 부품의 DFM 분석을 위한 자동화 시스템을 성공적으로 개발하고 시연했습니다. 시스템은 제조 용이성 평가 및 CAD 모델 수정 프로세스를 자동화하여 제조 용이성이 향상되고 재료 무게가 감소된 설계를 가능하게 합니다.
- 연구의 학문적 의의: 본 연구는 자동화된 DFM 분야에 기여하며, 특히 다이캐스팅의 요구 사항을 해결합니다. 기존 시스템, 특히 다이캐스팅에서 부족했던 DFM 분석 및 모델 업데이트를 자동화하는 방법론을 제공합니다.
- 연구의 실제적 의미: 개발된 시스템은 다이캐스팅 산업에 상당한 실제적 이점을 제공합니다. DFM 분석 및 모델 업데이트를 자동화함으로써 설계 리드 타임을 크게 줄이고, 생산 비용을 낮추며, 재료 사용량을 최적화할 수 있습니다. 이는 제품 개발 주기를 단축하고 보다 비용 효율적이고 지속 가능한 제조 공정으로 이어질 수 있습니다.
- 연구의 한계: 현재 시스템에는 다음과 같은 특정 제한 사항이 있습니다.
- 특징 기반 CAD 모델용으로 설계되었으며 다른 모델링 방법을 사용하여 생성된 모델에는 직접 적용할 수 없습니다.
- 시스템의 특징 인식 및 DFM 조언은 현재 보스, 립, 구멍 및 드래프트와 같은 특정 특징으로 제한됩니다.
- 현재 형태의 시스템은 자동 재설계 과정에서 부품의 기능적 요구 사항을 명시적으로 고려하지 않습니다. 기능적 요구 사항을 고려하여 제안 사항을 수용하거나 거부하려면 여전히 설계자의 개입이 필요합니다.
7. 향후 후속 연구:
- 후속 연구 방향: 향후 연구는 다음 사항에 초점을 맞춰야 합니다.
- 더 넓은 범위의 다이캐스팅 특징과 더 복잡한 부품 형상을 처리할 수 있도록 시스템의 기능을 확장합니다.
- 부품 기능성을 유지하도록 기능적 요구 사항을 자동화된 DFM 분석 및 재설계 프로세스에 통합합니다.
- 수동 개입의 필요성을 더욱 줄이기 위해 시스템의 자동화 수준을 향상시킵니다.
- 시스템의 다른 다이캐스팅 합금 및 공정 변형에 대한 적용을 탐구합니다.
- 추가 탐구가 필요한 영역: 더 광범위한 산업 모범 사례 및 다이캐스팅 설계 지침을 통합하는 보다 포괄적인 DFM 지식 기반을 개발하는 데 추가 탐구가 필요합니다. 복잡한 다이캐스팅 부품에 대한 특징 추출 방법의 견고성과 효율성을 개선하는 것도 향후 연구 분야입니다.
8. 참고 문헌:
- [1]. Madan J., Rao P.V.M., Kundra T.K., 2007, “Computer aided manufacturability analysis of die cast parts", Computer Aided Design and Applications, 4 (1-4), pp. 147-158.
- [2]. Bralla, J. G., 1999, “Design for manufacturability handbook", McGraw-Hill Inc., New York. (2nd Ed.).
- [3]. Hui K.C., 1997, “Geometric aspects of the mouldability of parts", Computer Aided Design, 29 (3), pp. 197-208.
- [4]. O'Driscoll M., 2001, “Design for manufacture”, Journal of Materials Processing Technology, 122, pp. 318-321.
- [5]. Gupta S.K., Regli W.C., Das D., Nau D.S., 1997, "Automated manufacturability analysis: A survey, Res. Eng. Des., 9 (3), pp.168–190.
- [6]. Chen Y., Miller R.A., Sevenler K., 1995, “Knowledge based manufacturability assessment: an object oriented approach", Journal of Intelligent Manufacturing, 6, pp.321-337.
- [7]. Datar J.S., Ravi B., Pande S.S., 1992, "feature based modeler for the design of die cast components", IIF Transactions, 94-18, pp. 247-252.
- [8]. Ramana K.V., Rao P.V.M., 2005, “Automated manufacturability evaluation system for sheet metal components in mass production”, International Journal of Production Research, 43 (18), pp. 3889–3913.
- [9]. Ramana K.V., Singh M., Gupta A., Dey R., Kapoor A., Rao P.V.M., 2006, “A manufacturability advisor for spun and roll formed sheet metal components", International Journal of Advances in Manufacturing Technology, 28, pp. 249-254.
- [10]. Venkatachalam A. R., Mellichamp J. M., Miller D. M., 1993, "A knowledge based approach to design for manufacturability", Journal of Intelligent Manufacturing, 4, pp. 355-366.
- [11]. Chen Y.M., Wen C.C., Ho C.T., 2003, “extraction of geometric characteristics for manufacturability assessment", Robotics and Computer Integrated Manufacturing, 19, pp. 371-385.
- [12]. Jacob D.V., Ramana K.V., Rao P.V.M., 2004, “Automated manufacturability assessment of rotational parts by grinding”, International Journal of Production Research, 42 (3), pp. 505-519.
- [13]. Das D., Gupta S. K., Nau D., 1996, “Generating redesign suggestions to reduce setup cost: a step towards automated redesign”, Computer Aided Design, 28 (10), pp. 763-782.
- [14]. Kumar S., Gupta A.K., Chandna P., 2012, "Optimization of process parameters of pressure die casting using Taguchi methodology", World Academy of Science, Engineering and Technology, 6, pp. 590-594.
- [15]. Bidkar R. A., McAdams D. A., 2010, "Methods for automated manufacturability analysis of injection-molded and die-cast parts", Research in Engineering Design, 21 (1), pp. 1-24.
- [16]. Shukor S.A., Axinte D.A., 2009, “Manufacturability analysis system: issues and future trends", International Journal of Production Research, 47 (5), pp. 1369-1390.
- [17]. Srikumaran S., Sivaloganathan S., 2005, “Proving manufacturability at the design stage using commercial modeling software", Computer Aided Design and Applications, 2, pp. 507-516.
- [18]. Madan J., Rao P.V.M., Kundra T.K., 2006, "System for early cost estimation of die-cast parts”, International Journal of Production Research, 45 (20), pp. 1-25.
- [19]. Poli C., 2001, “Design for manufacturing: A structured approach", Elsevier Science and Technology Books publishers.
- [20]. Chougule R. G., Ravi B., 2005, "Casting cost estimation in an integrated product and process design environment", International Journal of Computer Integrated Manufacturing, 19 (7), pp. 2-5.
- [21]. Chan D.S.K., 2003, "Expert system for product manufacturability and cost evaluation", Materials and Manufacturing Process, 18 (2), pp. 313-322.
- [22]. Hayes C.C., 1996, “Plan-based manufacturability analysis and generation of shape changing redesign suggestions", Journal of Intelligent Manufacturing, 7 (2), pp. 121-132.
- [23]. Korosec M., Balic J., Корас J., 2015, “Neural network based manufacturability evaluation of free form machining", International Journal of Machine Tools & Manufacturing, 45 (1), pp. 13-20.
- [24]. North American Die Casting Association, 2015, NADCA product specification standards for die casting, retrieved from https://www.diecasting.org/wcm/Technology/Standards/Die_Casting/wcm/Technology/Die_Casting_Standards.aspx?hkey=73d48de9-87ff-4e3.e-ace2-657a2cf33d99 (Assessed at 11am on 7-2-2018).
- [25]. Dhaliwal S., Gupta S. K., Huang J., Kumar M., 2002, "A step towards automated design of multi-piece sacrificial molds", ASME International Design Engineering Technical Conferences and Computers and Information in Engineering Conference, 3, pp. 337-347.
9. 저작권:
- 본 자료는 수닐 쿠마 (Sunil Kumar) 및 자틴더 마단 (Jatinder Madan)의 논문: 다이캐스팅 공정의 제조 용이성 분석을 위한 자동화 시스템 (An Automated System for Design for Manufacturability Analysis for Die-Casting)을 기반으로 합니다.
- 논문 출처: DOI: 10.1115/MSEC2018-6510
본 자료는 위 논문을 기반으로 요약되었으며, 상업적 목적으로 무단 사용하는 것을 금지합니다.
Copyright © 2025 CASTMAN. All rights reserved.