1. 개요:
- 제목: 주조 결함 최소화 시뮬레이션 기술 리뷰 (A Review on Casting Defect Minimization Through Simulation)
- 저자: Mahipalsinh G. Jadeja, Manojkumar V. Sheladiya, Mayursinh Gohil
- 발행 연도: 2016년
- 발행 학술지/학회: IJSRD - International Journal for Scientific Research & Development, Vol. 3, Issue 11, 2016, ISSN (online): 2321-0613
- Keywords: Casting, Casting Defect, Shrinkage, Simulation
2. 연구 배경:
- 연구 주제의 사회적/학문적 맥락:
- 주조 공정은 완제품 생산 과정에서 실패 위험이 항상 존재하며, 결함 없는 제품 생산을 위한 조치가 필요합니다.
- 주조 결함은 주로 공정 변수와 관련되어 발생하며, 결함 없는 제품 생산을 위해서는 공정 변수 제어가 중요합니다.
- 효과적인 주입 시스템 설계는 고품질 주조품 생산에 필수적이며, 특히 새로운 주조품이나 높은 불량률을 보이는 주조품의 경우 주입 시스템 설계 개선이 중요합니다.
- 기존의 주입 시스템 수정은 수작업으로 진행되어 시간, 비용, 자원 소모가 컸습니다.
- 주조 시뮬레이션은 이러한 어려움을 효과적으로 극복하고 공정 예측을 위한 강력한 도구를 제공합니다.
- 기존 연구의 한계점:
- 논문에서 기존 연구의 한계점을 명시적으로 언급하지는 않았습니다. 하지만 수작업 기반의 주입 시스템 설계 수정 방식의 비효율성을 암시하며, 시뮬레이션 기술의 필요성을 강조합니다.
- 연구의 필요성:
- 주조 시뮬레이션은 기존 주입 시스템의 결함 발생 가능성이 높은 위치를 예측하고, 이를 바탕으로 주입 시스템 설계를 개선하여 불량률을 감소시킬 수 있습니다.
- 시뮬레이션 기반의 설계 개선은 수작업 방식에 비해 시간과 비용을 절약하고 효율성을 높일 수 있습니다.
3. 연구 목적 및 연구 질문:
- 연구 목적:
- 본 논문의 목적은 주조 공정에서 발생하는 결함을 파악하고, 특히 수축 결함의 원인을 분석하며, 수축 결함 개선 방안을 제시하여 주조 제품의 품질을 향상시키는 데 있습니다.
- 또한, SOFTCAST 소프트웨어를 이용한 시뮬레이션을 통해 수축 결함을 감지하고, 제시된 개선 방안을 적용하여 불량률을 감소시키는 방법을 제시하는 것을 목표로 합니다.
- 핵심 연구 질문:
- 주조 공정에서 발생하는 주요 결함은 무엇이며, 그 원인은 무엇인가?
- 특히 수축 결함의 발생 원인은 무엇이며, 이를 최소화하기 위한 효과적인 방법은 무엇인가?
- 주조 시뮬레이션은 주조 결함, 특히 수축 결함 예측 및 개선에 어떻게 활용될 수 있는가?
- 연구 가설:
- 본 논문은 리뷰 논문으로, 특정 연구 가설을 설정하고 검증하는 형태는 아닙니다. 하지만 시뮬레이션 기술을 활용한 주입 시스템 개선이 주조 결함, 특히 수축 결함 감소에 효과적일 것이라는 점을 암시적으로 제시합니다.
4. 연구 방법론:
- 연구 설계:
- 본 연구는 주조 결함, 특히 수축 결함과 관련된 기존 연구 문헌을 종합적으로 분석하는 리뷰 연구입니다.
- 다양한 주조 결함의 종류, 발생 원인, 개선 방안을 문헌 분석을 통해 정리하고, 시뮬레이션 기술의 활용 가능성을 탐색합니다.
- 데이터 수집 방법:
- 주조 공정 및 결함 관련 학술 논문, 기술 자료 등 문헌 자료를 수집하여 분석하였습니다.
- 특히, 주조 시뮬레이션 소프트웨어 활용 사례 및 효과 분석 관련 연구를 중점적으로 검토하였습니다.
- 분석 방법:
- 수집된 문헌 자료를 바탕으로 주조 결함의 종류, 원인, 개선 방안을 분류하고 정리하였습니다.
- 시뮬레이션 기술의 주조 공정 적용 효과 및 결함 예측 능력을 분석하고, 실제 주조 현장에서의 활용 가능성을 평가하였습니다.
- SOFTCAST 소프트웨어의 수축 결함 예측 기능 및 개선 방안 적용 효과를 분석하였습니다.
- 연구 대상 및 범위:
- 본 연구는 주조 공정 전반에서 발생하는 다양한 결함을 대상으로 하지만, 특히 수축 결함에 초점을 맞추어 분석합니다.
- 연구 범위는 주조 결함의 발생 원인 분석, 개선 방안 제시, 시뮬레이션 기술 활용 방안 검토를 포함하며, 실제 주조 사례 및 시뮬레이션 결과를 분석하여 연구 결과를 뒷받침합니다.
5. 주요 연구 결과:
- 핵심 연구 결과:
- 주조 공정에서 발생하는 주요 결함으로 수축(Shrinkage), 블로우홀(Blowhole), 샌드 버닝(Sand Burning), 샌드 인클루전(Sand Inclusion), 콜드 랩 또는 콜드 셧(Cold Lap Or Cold Shut), 미스런(Misrun), 가스 기공(Gas Porosity), 미스매치(Mismatch), 균열 또는 찢어짐(Cracks Or Tears), 불완전 주조(Incomplete Casting) 등이 확인되었습니다.
- 각 결함의 발생 가능한 원인(Possible Causes)과 개선 방안(Remedies)을 상세히 제시하였습니다.
- 수축 (Shrinkage): 용융 금속의 밀도 변화, 부적절한 주입 시스템 설계 등이 원인이며, 개선 방안으로 액체 금속이 응고 수축을 보상하도록 압력을 유지하고, 적절한 주입 시스템 설계가 필요합니다.
- 블로우홀 (Blowhole): 코어 통기 불량, 코어 가스 과다 발생, 코어의 수분 흡수 등이 원인이며, 개선 방안으로 코어 통기 개선, 가스 발생량 감소, 코어 건조 및 보관 등이 필요합니다.
- 샌드 버닝 (Sand Burning): 높은 주형 온도, 주형재의 낮은 융점 등이 원인이며, 개선 방안으로 주형재 개선, 주입 온도 조절 등이 필요합니다.
- 콜드 랩 또는 콜드 셧 (Cold Lap Or Cold Shut): 용융 금속의 유동성 부족, 부적절한 주입 시스템 설계 등이 원인이며, 개선 방안으로 적절한 주입 온도, 주입 시스템 개선 등이 필요합니다.
- 미스런 (Misrun): 용융 금속이 주형 캐비티를 완전히 채우지 못하는 결함으로, 콜드 랩과 유사한 원인과 개선 방안을 가집니다.
- 가스 기공 (Gas Porosity): 갇힌 공기, 수소, 수분 등이 원인이며, 개선 방안으로 주입 온도 증가, 유동성 개선, 주입 속도 조절, 주형재 개선, 적절한 통기 등이 필요합니다.
- 미스매치 (Mismatch): 주형 이동으로 인한 단차 발생 결함으로, 주형 상하부 정렬 불량 등이 원인이며, 개선 방안으로 주형 정렬 핀 점검 및 수정, 주형 박스 및 클램핑 핀 사용 등이 필요합니다.
- 균열 또는 찢어짐 (Cracks Or Tears): 다이캐스팅에서 다양한 원인으로 발생하며, 수축, 다이 캐비티 손상, 불균일한 냉각 등이 원인이며, 개선 방안으로 건조 강도 감소, 주입 온도 감소, 급냉 방지, 피더 사용, 충분한 냉각 시간 확보 등이 필요합니다.
- 불완전 주조 (Incomplete Casting): 용탕 부족, 작업자 실수 등이 원인이며, 개선 방안으로 충분한 용탕 확보, 주입 시스템 점검, 작업자 교육 및 감독 강화 등이 필요합니다.
- SOFTCAST 소프트웨어를 이용한 시뮬레이션은 수축 결함 예측에 효과적이며, 시뮬레이션 결과를 바탕으로 주입 시스템을 개선하여 수축 결함을 최소화할 수 있음을 제시하였습니다.
- 실제 주조 사례(EP20 부품)에 대한 시뮬레이션 분석을 통해 수축 결함 발생 위치를 예측하고, 주입 시스템 개선을 통해 불량률 감소 가능성을 확인하였습니다.
- 통계적/정성적 분석 결과:
- 본 논문은 리뷰 논문으로 통계적 분석 결과는 제시되지 않았습니다.
- 정성적 분석 결과로, 다양한 주조 결함의 종류, 원인, 개선 방안을 체계적으로 정리하고, 시뮬레이션 기술의 주조 결함 예측 및 개선 효과를 분석하였습니다.
- 데이터 해석:
- 주조 시뮬레이션은 주조 결함, 특히 수축 결함 예측 및 개선에 효과적인 도구이며, 실제 주조 현장에서 불량률 감소 및 품질 향상에 기여할 수 있습니다.
- SOFTCAST와 같은 FEM 기반 시뮬레이션 소프트웨어는 주조 공정 최적화 및 결함 최소화를 위한 강력한 솔루션을 제공합니다.
- Figure Name List:
- Fig. 1: Actual casting EP20
- Fig. 2: Monthly rejection rate of EP 20
- Fig. 3: Solid Model of Casting EP20
- Fig. 4: Simulation Result of the Casting EP 20.
- Fig. 5: Shrinkage porosity (macro-red, micro-orange).
- Fig. 6: Framework for feeder design and optimisation
- Fig. 7: Liquid-solid interface (solid lines) and feed-paths (dotted lines) inside stepped casting.
- Fig. 8: Distribution of Lower Bainite (volume fraction) (a) ideal case; (b) the case considering the results of casting.
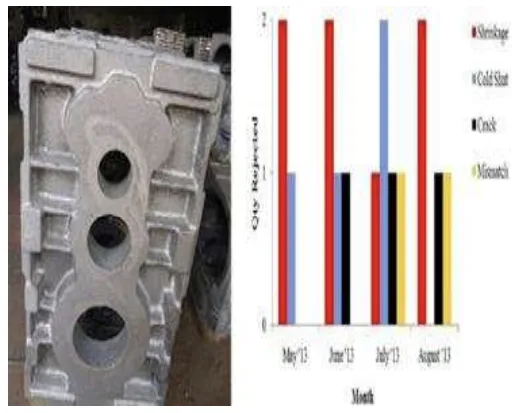
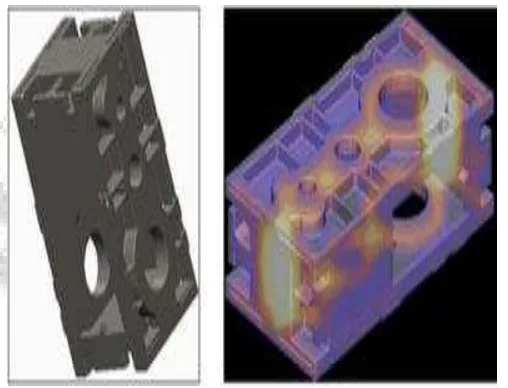
6. 결론 및 논의:
- 주요 결과 요약:
- 본 연구는 주조 공정에서 발생하는 다양한 결함과 그 원인, 개선 방안을 문헌 분석을 통해 종합적으로 검토하였습니다.
- 특히, 수축 결함은 주조 불량의 주요 원인이며, 시뮬레이션 기술을 활용한 주입 시스템 개선을 통해 효과적으로 감소시킬 수 있음을 제시하였습니다.
- SOFTCAST 소프트웨어 기반의 시뮬레이션은 수축 결함 예측 및 주조 공정 최적화에 유용한 도구임을 확인하였습니다.
- 연구의 학술적 의의:
- 본 연구는 주조 결함, 특히 수축 결함에 대한 체계적인 정보를 제공하고, 시뮬레이션 기술의 주조 공정 적용 가능성을 제시함으로써 학술적 가치를 지닙니다.
- 주조 공정 및 결함 관련 연구 분야의 발전에 기여하고, 향후 시뮬레이션 기반 주조 공정 연구의 기초 자료로 활용될 수 있습니다.
- 실무적 시사점:
- 본 연구 결과는 주조 현장에서 시뮬레이션 기술을 활용하여 주조 결함을 예측하고, 주입 시스템을 개선함으로써 불량률을 감소시키고 생산성을 향상시키는 데 기여할 수 있습니다.
- 특히, SOFTCAST와 같은 시뮬레이션 소프트웨어는 주조 기술자들에게 실질적인 도움을 줄 수 있는 유용한 도구입니다.
- 연구의 한계점:
- 본 연구는 문헌 리뷰 연구로, 특정 시뮬레이션 소프트웨어(SOFTCAST)에 대한 분석에 집중되어 있어, 다양한 시뮬레이션 기술 및 주조 조건에 대한 일반화에는 한계가 있을 수 있습니다.
- 실제 주조 실험을 통한 검증 연구가 부족하며, 향후 다양한 주조 조건 및 시뮬레이션 소프트웨어를 활용한 추가 연구가 필요합니다.
7. 향후 후속 연구:
- 후속 연구 방향:
- 다양한 시뮬레이션 소프트웨어 및 주조 조건에서의 수축 결함 예측 정확도 및 개선 효과 검증 연구가 필요합니다.
- 실제 주조 실험을 통해 시뮬레이션 예측 결과의 타당성을 검증하고, 시뮬레이션 기반 주입 시스템 설계 최적화 방법론 개발 연구가 필요합니다.
- 수축 결함 외 다른 주조 결함에 대한 시뮬레이션 예측 및 개선 연구 확대가 필요합니다.
- 추가 탐구가 필요한 영역:
- 인공지능(AI) 및 머신러닝(ML) 기술을 활용한 주조 결함 예측 및 자동 개선 시스템 개발 연구
- 주조 공정 변수와 결함 발생 간의 상관관계 분석 및 데이터 기반 결함 예측 모델 개발 연구
- 3D 프린팅 기술을 활용한 주조 주형 제작 및 시뮬레이션 연동 연구
8. 참고문헌:
- [1] Harshil Bhatta, Rakesh Barota, Kamlesh Bhatta, Hardik Beravalaa, Jay Shah "Design Optimization of Feeding System and Solidification Simulation for Cast Iron" 2nd International Conference on Innovations in Automation and Mechatronics Engineering, ICIAME 2014 Elsevier volume 14 (2014) 357 – 364
- [2] C. M. Choudhari, B. E. Narkhede, S. K. Mahajan "Methoding and Simulation of LM 6 Sand Casting for Defect Minimization with its Experimental Validation" 12th Global Congress On Manufacturing And Management, GCMM 2014 Elsevier volume 97 (2014) 1145-1154
- [3] Dr. B Ravi, Durgesh Joshi "Feedability Analysis and Optimisation Driven by Casting Simulation” Technical paper submitted to the Indian Foundry Journal Indian Foundry Journal April 2007
- [4] Mayur Sutaria, Vinesh H. Gada, Atul Sharma, B. Ravi "Computation of feed-paths for casting solidification using level-set-method” Journal of Materials Processing Technology Elsevier volume 212 (2012) 1236-1249
- [5] Χ. Sua, G. Wang, Y.T. Zhang,J.F.Li, Y.M.Rong "Modeling on stress evolution of step part for casting-heat treatment processes" International Federation for Heat Treatment and Surface Engineering 20th Congress Beijing Elsevier volume 50 (2013) 360 – 367
- [6] E. Anglada, A. Meléndez, L.Maestro, I. Domiguez "Adjustment of Numerical Simulation Model to the Investment Casting Process” The Manufacturing Engineering Society International Conference, MESIC 2013 Elsevier volume 63 (2013) 75 – 83
- [7] F. J. Bradley, M. Samonds "A comparison of source term and enthalpy approaches to the numerical simulation of the solidification of ductile irons" Applied mathematics modeling, volume 16, (1992).
9. Copyright:
*본 자료는 Mahipalsinh G. Jadeja, Manojkumar V. Sheladiya, Mayursinh Gohil의 논문: A Review on Casting Defect Minimization Through Simulation을 기반으로 작성되었습니다.
본 자료는 위 논문을 바탕으로 요약 작성되었으며, 상업적 목적으로 무단 사용이 금지됩니다.
Copyright © 2025 CASTMAN. All rights reserved.