본 논문 요약은 [논문 제목] "다이캐스트 알루미늄 합금의 기공 결함 진화에 대한 사출 속도의 영향 연구"를 기반으로 작성되었으며, [출판사] MDPI에 게재되었습니다.
1. 개요:
- 제목: 다이캐스트 알루미늄 합금의 기공 결함 진화에 대한 사출 속도의 영향 연구 (Study on the Influence of Injection Velocity on the Evolution of Hole Defects in Die-Cast Aluminum Alloy)
- 저자: 한쉐 차오 (Hanxue Cao), 치앙 장 (Qiang Zhang), 웨이카이 주 (Weikai Zhu), 쉥 추이 (Sheng Cui), 퀸 양 (Qin Yang), 지바이 왕 (Zhibai Wang), 빈 지앙 (Bin Jiang)
- 발행 연도: 2024년
- 출판 저널/학술 단체: Materials (MDPI)
- 키워드: 알루미늄 합금 다이캐스팅 (aluminum alloy die-casting); 가시화 (visualization); 사출 속도 (injection rate); 기공 결함 (hole defects)
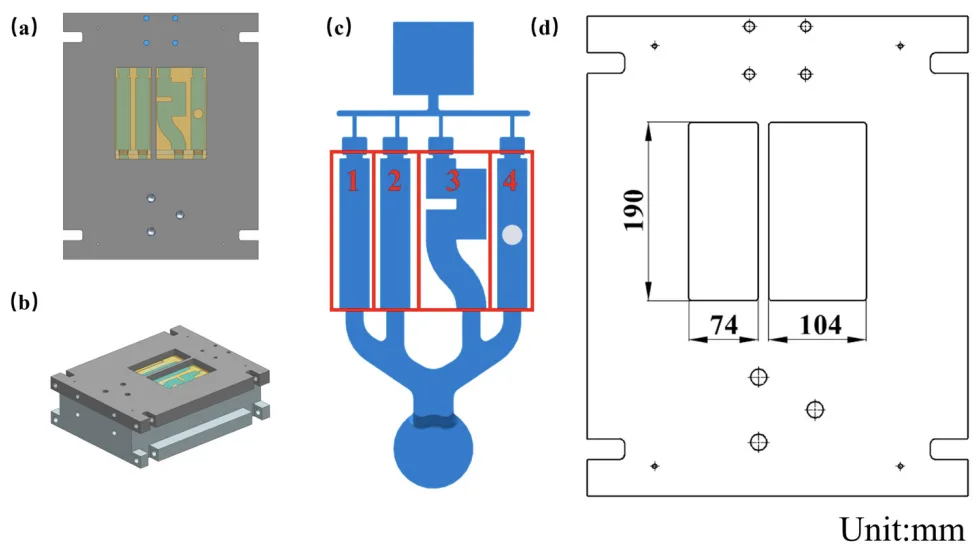
2. 연구 배경:
- 연구 주제의 사회적/학문적 맥락: 알루미늄 합금 다이캐스팅은 효율성과 치수 정확도로 인해 산업 전반에서 빠르게 발전하고 널리 사용되는 기술입니다. 그러나 기공 결함, 즉 홀 결함은 다이캐스팅에서 흔히 발생하는 문제로, 부품의 기계적 및 가공 특성에 부정적인 영향을 미칩니다. 이러한 결함을 이해하고 줄이는 것은 다이캐스트 제품의 품질과 신뢰성을 향상시키는 데 매우 중요합니다.
- 기존 연구의 한계: 기존 연구에서는 공정 변수와 금형 구조가 기공에 미치는 영향을 탐구했지만, 고압 다이캐스팅 중 금형 캐비티 내 용융 금속 흐름 거동을 직접 관찰하고 특성화하는 데는 한계가 있었습니다. 물 시뮬레이션 및 수치 시뮬레이션과 같은 기존 방법은 액체 금속 흐름의 복잡한 역학과 결함 형성을 정확하게 나타내는 데 한계가 있습니다.
- 연구의 필요성: 홀 결함을 효과적으로 줄이거나 제거하려면 다이캐스팅 공정 중 가스 거동에 대한 더 깊은 이해가 필수적입니다. 본 연구는 실제 알루미늄 합금, 특히 널리 사용되는 ADC12의 다이캐스팅 공정 중 사출 속도가 합금 흐름 패턴과 가스 유발 결함에 미치는 영향을 실시간으로 직접 관찰하고 분석하는 방법의 필요성을 해결합니다.
3. 연구 목적 및 연구 질문:
- 연구 목적: 본 연구의 주요 목적은 충전 과정을 직접 가시화하여 다이캐스트 알루미늄 합금의 홀 결함 형성 및 진화에 대한 다양한 사출 속도의 영향을 조사하는 것입니다.
- 주요 연구 질문:
- 다이캐스팅 중 사출 속도 변화는 용융 알루미늄 합금의 흐름 패턴에 어떤 영향을 미치는가?
- 사출 속도와 가스 유발 홀 결함의 형성 및 진화 사이에는 어떤 관계가 있는가?
- 다양한 사출 속도에서 홀 결함 형성에 기여하는 메커니즘은 무엇인가?
- 연구 가설: 본 연구는 사출 속도를 높이면 용융 금속 흐름 패턴이 변경되어 공기 혼입이 증가하고 결과적으로 다이캐스트 알루미늄 합금 부품에서 더 높은 다공성 및 더 큰 홀 결함이 발생할 것이라는 가설을 세웠습니다.
4. 연구 방법론
- 연구 설계: 본 연구에서는 수평 냉간 챔버 다이캐스팅 기계 (DCC630M)에 장착된 유리창이 있는 특수 설계된 금형을 사용하여 혁신적인 동적 가시화 실험을 수행했습니다. 이 설정을 통해 알루미늄 합금 충전 과정을 직접 관찰할 수 있습니다.
- 데이터 수집 방법: 고속 카메라 (초당 1000 프레임, 1024 × 1024 해상도)를 사용하여 다양한 사출 속도 (1.0 m/s 및 1.5 m/s)에서 다이캐스팅 중 용융 금속 흐름을 기록했습니다. 주조 샘플을 제작하고 정수압법과 밀도 밸런스 (MH-110E)를 사용하여 다공성을 정량화했습니다.
- 분석 방법: 기록된 비디오를 분석하여 흐름 패턴과 결함 형성의 동적 진화를 특성화했습니다. Image-Pro Plus 소프트웨어를 사용하여 주조 샘플의 단면에서 홀 결함을 측정하고 분석했습니다. Anycasting 소프트웨어를 사용한 수치 시뮬레이션을 통해 실험 관찰 결과와 비교했습니다.
- 연구 대상 및 범위: 본 연구는 ADC12 알루미늄 합금 다이캐스팅에 중점을 둡니다. 이 연구에서는 카운터싱크 홀, 스텝 보스, 보우 및 관통 홀 구조의 4가지 일반적인 캐비티 구조를 가진 금형에서 홀 결함 형성에 대한 두 가지 다른 사출 속도 (1.0 m/s 및 1.5 m/s)의 영향을 조사합니다. 다공성 분석을 위해 이러한 캐비티 구조 내의 4개 위치 (S1, S2, S3, S4)에서 샘플을 채취했습니다.
5. 주요 연구 결과:
- 주요 연구 결과:
- 사출 속도를 1.0 m/s에서 1.5 m/s로 증가시키면 평균 다공성이 7.49%에서 9.57%로 증가했습니다. 이는 사출 속도가 증가함에 따라 기공의 수와 크기가 모두 크게 증가했음을 나타냅니다.
- 가시화 및 시뮬레이션 결과 1.5 m/s 사출 속도에서 흐름 전면이 1.0 m/s에 비해 더 심각한 파단 및 스플래싱을 나타냈습니다.
- 흐름 전면에서의 파단 스플래시 정도는 사출 속도가 높을수록 심각했으며, 이는 벽 부착 제트 효과 때문으로 분석되었습니다.
- 사출 속도가 증가하면 액체 파손으로 형성된 마이크로그룹 부피가 감소하여 공기 혼입 및 캐비티 결함이 증가했습니다.
- 통계적/정성적 분석 결과: 정량적 다공성 측정 결과 사출 속도가 높을수록 다공성이 통계적으로 유의미하게 증가하는 것으로 확인되었습니다. 정성적 가시화 비디오 분석 결과 더 높은 사출 속도에서 뚜렷한 흐름 패턴과 증가된 난류 및 스플래싱이 나타났습니다.
- 데이터 해석: 더 높은 사출 속도에서 다공성이 증가하는 것은 강화된 벽 부착 제트 효과 및 흐름 전면 파단 때문입니다. 이러한 현상으로 인해 후속 액체 금속이 초기 흐름과 융합하기 어려워 공기가 갇히고 캐비티 결함이 발생합니다.
- 그림 목록:
- 그림 5. 다양한 사출 속도에서의 흐름 특성 (Flow characteristics at different velocities of injection)
- 그림 6. 다양한 속도에서의 충전 흐름 시뮬레이션 결과 (Simulation results of filling flow at different speeds)
- 그림 7. 내부 게이트 두께 3.0 mm 및 사출 속도 1.0 m/s의 시편 단면 형태 (Cross-sectional morphology of specimens with an inner gate thickness of 3.0 mm and an injection velocity of 1.0 m/s)
- 그림 8. 내부 게이트 두께 3.0 mm 및 사출 속도 1.5 m/s의 시편 단면 형태 (Cross-sectional morphology of specimens with an inner gate thickness of 3.0 mm and an injection velocity of 1.5 m/s)
- 그림 9. 3.0 mm 내부 게이트에서 다양한 사출 속도에서의 다공성 (Porosity at different injection velocities at a 3.0 mm inner gate)
- 그림 10. 사출 속도 1.0 m/s에서 S2 위치의 액체 금속 흐름 패턴 (Flow pattern of liquid metal at S2 position at injection velocity of 1.0 m/s)
- 그림 11. 사출 속도 1.5 m/s에서 S2 위치의 액체 금속 흐름 패턴 (Flow pattern of liquid metal at S2 position at injection velocity of 1.5 m/s)
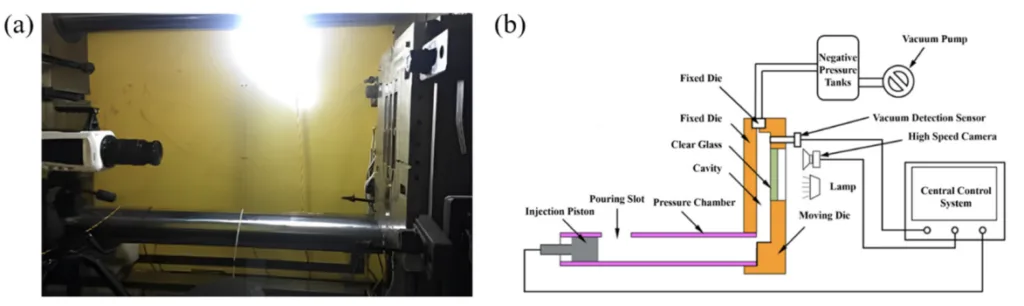
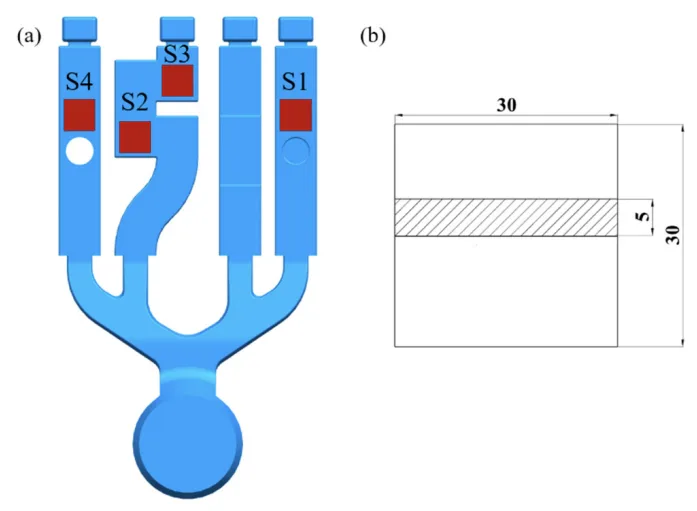
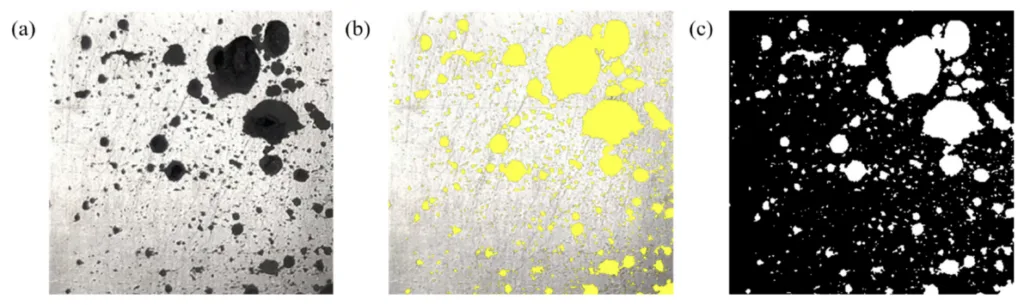
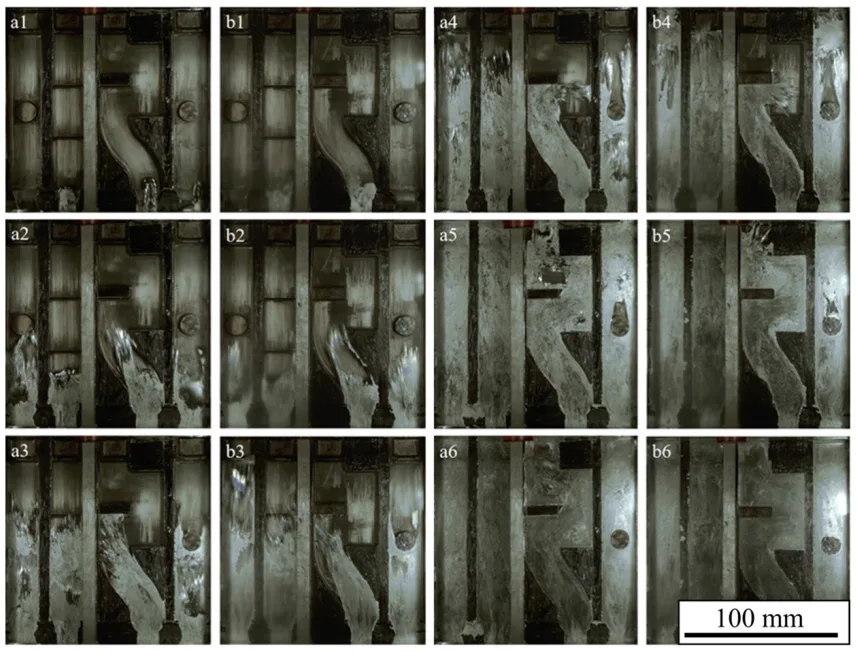
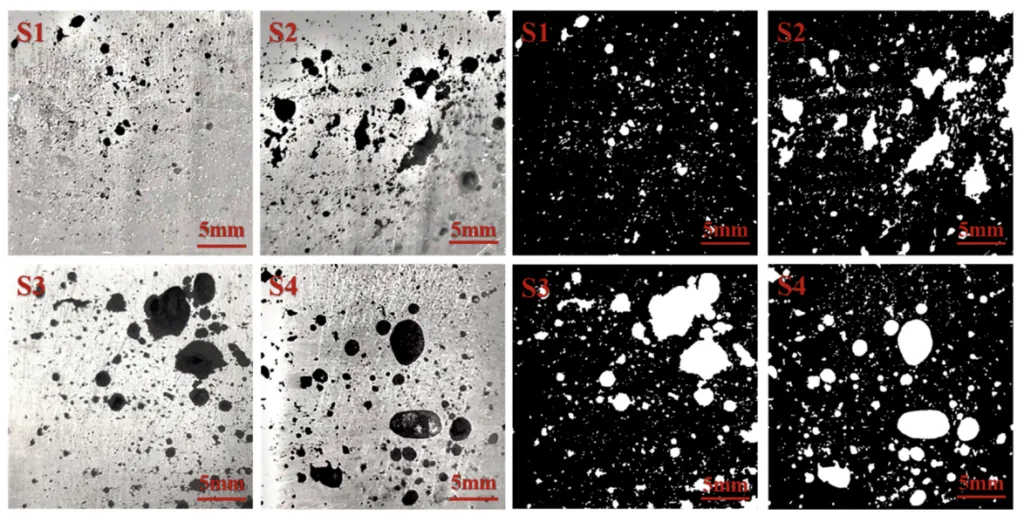
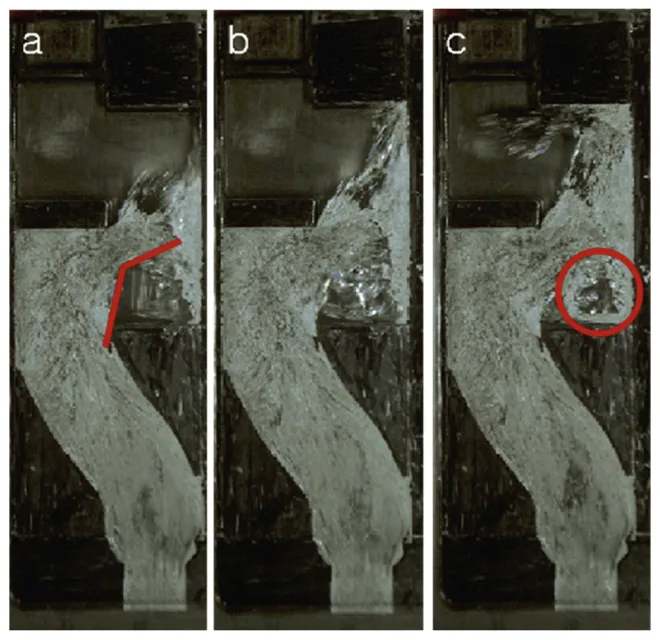
6. 결론 및 논의:
- 주요 결과 요약: 본 연구에서는 알루미늄 합금 다이캐스팅에서 사출 속도를 높이면 다공성 및 홀 결함이 크게 증가한다는 것을 입증했습니다. 이는 주로 더 높은 사출 속도로 인해 강화된 흐름 전면 파단, 벽 부착 제트 효과 및 공기 혼입 증가 때문입니다.
- 연구의 학문적 의의: 혁신적인 동적 가시화 방법은 다이캐스팅에서 용융 금속 흐름 거동 및 결함 형성을 직접 관찰하고 이해하는 데 유용한 도구를 제공합니다. 이 연구 결과는 가스 유발 결함의 메커니즘과 사출 속도의 영향에 대한 더 깊은 이해에 기여합니다.
- 실용적 의미: 본 연구는 다공성을 최소화하기 위한 금형 설계에 대한 실용적인 조치를 제시합니다.
- 흐름 방향을 변경하고 벽 제트 효과를 줄이기 위해 넓은 평면을 피하십시오.
- 넓은 평면이 필요한 경우 표면에 작은 돌출부 또는 함몰부를 추가하여 하부 용융 금속의 안정적인 흐름을 방해하고 금형 벽에 부착된 용융 금속의 통합을 촉진하십시오.
- 금형 내에 흐름 유도판 또는 튜브를 도입하여 유체 흐름 방향을 변경하여 벽 근처에서 더 균일한 흐름 패턴을 허용하십시오.
- 금형 설계 시 유체 흐름 특성을 고려하여 유선형 또는 곡선형 모양을 선택하여 벽 근처에서 유체 정체 및 불균일한 흐름을 최소화하십시오.
- 연구의 한계: 본 연구는 주로 사출 속도의 영향에 초점을 맞추었습니다. 논문에서는 온도 분포와 같은 요인도 흐름 및 기공 형성에 중요한 역할을 하지만, 본 연구의 주요 초점은 아니었다는 점을 인정합니다.
7. 향후 후속 연구:
- 후속 연구 방향: 향후 연구에서는 다이캐스팅에서 온도 분포가 용융 금속 흐름 및 기공 형성에 미치는 영향을 탐구해야 합니다.
- 추가 탐구가 필요한 영역: 시뮬레이션의 정확도를 높여 흐름 거동 및 결함 형성을 예측하기 위해 수치 시뮬레이션 경계 조건 최적화 및 보다 현실적인 물리적 모델 개발에 대한 추가 연구가 필요하며, 잠재적으로 온도 효과를 통합해야 합니다.
8. 참고 문헌:
- [1] Wang, G.G.; Weiler, J.P. Recent developments in high-pressure die-cast magnesium alloys for automotive and future applications. J. Magnes. Alloys 2023, 11, 78–87.
- [2] Yang, Y.-T.; Qiu, Z.-Y.; Zheng, Z.; Pu, L.-X.; Chen, D.-D.; Zheng, J.; Zhang, R.-J.; Zhang, B.; Huang, S.-Y. Al-enabled properties distribution prediction for high-pressure die casting Al-Si alloy. Adv. Manuf. 2024, 12, 591-602.
- [3] Cleary, P.; Ha, J.; Alguine, V.; Nguyen, T. Flow modelling in casting processes. Appl. Math. Model. 2002, 26, 171-190.
- [4] Kang, H.J.; Yoon, P.H.; Lee, G.H.; Park, J.Y.; Jung, B.J.; Lee, J.Y.; Lee, C.U.; Kim, E.S.; Choi, Y.S. Evaluation of the gas porosity and mechanical properties of vacuum assisted pore-free die-cast Al-Si-Cu alloy. Vacuum 2021, 184, 109917.
- [5] Hu, Q.; Guo, W.; Xiao, P.; Zhao, H. Effects of Fast Shot Speed and Wall Thickness on the Microstructures and Mechanical Properties of the High Pressure Die-casting 6061-SiC Composites. Metall. Mater. Trans. B-Process Metall. Mater. Process. Sci. 2021, 52, 2283–2293.
- [6] Ma, Y.-H.; Yu, W.-B.; Zhou, Y.-Q.; Xiong, S.-M. Influence of different high pressure die casting processes on 3D porosity distribution of Mg-3.0Nd-0.3Zn-0.6Zr alloy. China Foundry 2021, 18, 521–528.
- [7] Majerník, J.; Gašpár, S.; Husár, J.; Paško, J.; Kolínský, J. Research and Evaluation of the Influence of the Construction of the Gate and the Influence of the Piston Velocity on the Distribution of Gases into the Volume of the Casting. Materals 2021, 14, 2264.
- [8] Ibrahim, M.D.; Mohamad, M.R.; Roslan, L.; Sunami, Y.; Lam, S.S. High Pressure Die Casting Porosity Defect Analysis and Experimental Validation for Power Steering Columns and DVVTs. In Lecture Notes in Mechanical Engineering; Springer: Singapore, 2018; pp. 187–196.
- [9] Gautam, S.K.; Roy, H.; Lohar, A.K.; Samanta, S.K. Studies on Mold Filling Behavior of Al-10.5Si-1.7Cu Al Alloy during Rheo Pressure Die Casting System. Int. J. Met. 2023, 17, 2868–2877.
- [10] Haghniaz, F.; Delbergue, D.; Côté, R.; Demers, V. Mold filling behaviour of LPIM feedstocks using numerical simulations and real-scale injections. Powder Metall. 2023, 66, 436-449.
- [11] Hu, M.Y.; Cai, J.J.; Li, N.; Yu, H.L.; Zhang, Y.; Sun, B.; Sun, W.L. Flow Modeling in High-Pressure Die-Casting Processes Using SPH Model. Int. J. Met. 2018, 12, 97-105.
- [12] Ren, M.; Gu, J.; Li, Z.; Ruan, S.; Shen, C. Simulation of Polymer Melt Injection Molding Filling Flow Based on an Improved SPH Method with Modified Low-Dissipation Riemann Solver. Macromol. Theory Simul. 2022, 31, 2100029.
- [13] Niu, X.F.; Zhao, J.Y.; Wang, B.J. Application of smooth particle hydrodynamics (SPH) method in gravity casting shrinkage cavity prediction. Comput. Part. Mech. 2019, 6, 803–810.
- [14] Zarbini Seydani, M.; Krimi, A.; Bedel, M.; Khelladi, S.; El Mansori, M. A 2D filling and solidification benchmark test: Validating smoothed particle hydrodynamics (SPH) simulations for sand gravity casting. Int. J. Adv. Manuf. Technol. 2023, 128, 801–821.
- [15] Saeedipour, M.; Schneiderbauer, S.; Pirker, S.; Bozorgi, S. A Numerical and Experimental Study of Flow Behavior in High Pressure Die Casting. In Magnesium Technology, Proceedings of the 2014—TMS 2014 143rd Annual Meeting and Exhibition, San Diego, CA, USA, 16–20 February 2014; Springer: Berlin/Heidelberg, Germany, 2014.
- [16] Kulasegaram, S.; Bonet, J.; Lewis, R.W.; Profit, M. High pressure die casting simulation using a Lagrangian particle method. Commun. Numer. Methods Eng. 2003, 19, 679-687.
- [17] Homayonifar, P.; Babaei, R.; Attar, E.; Shahinfar, S.; Davami, P. Numerical modeling of splashing and air entrapment in high-pressure die casting. Int. J. Adv. Manuf. Technol. 2008, 39, 219-228.
- [18] Bi, C.; Xiong, S. Development of a Full PLIC-VOF Method for Mold Filling Simulation of High Pressure Die Casting Process. In Proceedings of the 8th Pacific Rim International Congress on Advanced Materials and Processing, Waikoloa, HI, USA, 4–9 August 2013; Marquis, F., Ed.; Springer International Publishing: Cham, Switzerland, 2016; pp. 2867–2874.
- [19] Sakuragi, T. Mould filling simulation with consideration of surface tension and its application to a practical casting problem. Cast Metals 2013, 18, 202-208.
- [20] Niida, A.; Maeda, Y. Observation of Air Entrapment during Mold Filling of Die Casting Using Water Model Experiment for Mold Filling Simulation. Mater. Trans. 2020, 61, 1364-1368.
- [21] Liu, J.; Zhou, P.; Zuo, X.; Wu, D.; Wu, D. Optimization of the Liquid Steel Flow Behavior in the Tundish through Water Model Experiment, Numerical Simulation and Industrial Trial. Metals 2022, 12, 1480.
- [22] Lin, S.P.; Reitz, R.D. Drop and spray formation from a liquid jet. Annu. Rev. Fluid Mech. 1998, 30, 85–105.
9. 저작권:
본 자료는 한쉐 차오 외 저자의 논문: "다이캐스트 알루미늄 합금의 기공 결함 진화에 대한 사출 속도의 영향 연구"를 기반으로 작성되었습니다.
논문 출처: https://doi.org/10.3390/ma17204990
본 자료는 상기 논문을 기반으로 요약되었으며, 상업적 목적의 무단 사용을 금지합니다.
Copyright © 2025 CASTMAN. All rights reserved.