이 글은 [Computer-Aided Design & Applications]에서 발행한 ["Predicting Die Cracking in Die-Cast Products Using a Surrogate Model Based on Geometrical Features"] 의 논문 연구 내용을 소개하는 글 입니다.
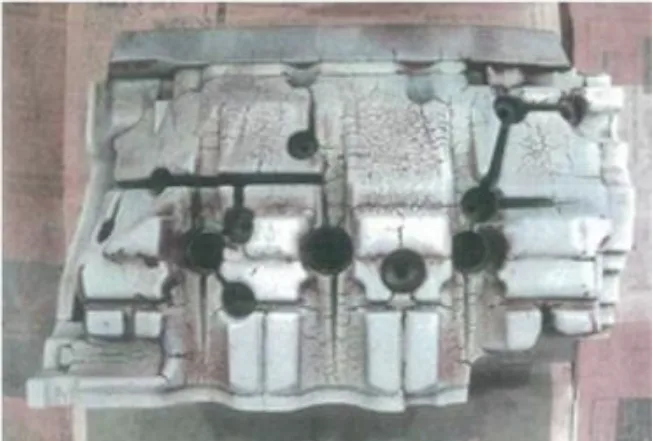
1. Overview:
- Title: Predicting Die Cracking in Die-Cast Products Using a Surrogate Model Based on Geometrical Features
- Author: Tomoya Yamazaki, Koh Hirokawa, Akira Murakami, Misato Baba, and Chisako Muramatsu
- Publication Year: 2025
- Publishing Journal/Academic Society: Computer-Aided Design & Applications, 22(2), 2025, 217-228
- Keywords: Die casting, Surrogate model, VAE, Neural network, Computer-aided design, die cracking, geometrical features, automotive industry, machine learning, defect prediction, 3D shape data
2. Abstracts or Introduction
본 논문은 제품 설계의 기하학적 특징에 초점을 맞추어 다이캐스팅 제품의 다이 크랙을 예측하기 위한 서 surrogate 모델의 개발 및 응용을 탐구합니다. 다이캐스팅은 복잡한 형상을 신속하게 대량 생산하는 효율성으로 유명하며, 특히 자동차 산업에서 차량 중량 및 부품 수 감소에 중요합니다.
그러나 제품 품질 보장 및 개발 리드 타임 최소화는 제품 설계 단계에서 복잡한 형상의 결함 예측의 어려움으로 인해 더욱 중요해진 과제입니다. 기존의 시뮬레이션 기술은 표준이지만 준비 및 실행 시간이 길어 효율적인 결함 예측을 위해 빅데이터 및 머신 러닝을 활용하는 방향으로 전환되고 있습니다.
본 연구에서는 다이캐스팅에서 중요한 문제인 다이 크랙 발생을 예측하기 위해 VAE(Variational Autoencoders)와 신경망을 사용하는 새로운 surrogate 모델을 소개합니다.
Toyota Motor Corporation의 엔진 블록 부품 및 트랜스액슬 케이스를 분석하여 모델은 높은 정확도로 다이 크랙을 예측하는 데 유망한 결과를 보여주며, 초기 결함 감지를 위한 제품 형상 데이터 활용을 통해 다이캐스팅 공정을 개선하기 위한 새로운 방향을 제시하여 제조 효율성 및 제품 품질을 향상시킵니다.
3. Research Background:
Background of the Research Topic:
다이캐스팅은 복잡한 형상의 제품을 고속으로 대량 생산하기 때문에 산업 생산, 특히 자동차 산업에서 널리 사용되며 차량 중량 감소 및 부품 수 감소의 관점에서 최근 몇 년 동안 다시 주목받고 있습니다. 산업 제품으로서 높은 경쟁력을 확보하려면 시장 트렌드를 정확하게 반영하는 제품을 적시에 공급하는 것이 필요하며, 이를 위해서는 제품 개발 리드 타임을 단축하는 것이 중요합니다.
일반적으로 자동차 산업의 제품 개발 프로세스는 "제품 설계"에서 "다이 설계", "생산성 시뮬레이션", "공정 설계", "기능 평가" 및 최종 "대량 생산"으로 이어지는 흐름을 따릅니다. 이 프로세스는 단방향이 아니라 반복적이며 각 단계의 반복적인 사이클을 통해 제품 설계의 완성도를 높입니다. 그러나 프로세스가 진행됨에 따라 사양이 더욱 복잡해지고 수정 또는 재작업이 증가하는 경향이 있습니다.
따라서 가능한 한 재작업을 최소화하면서 진행하는 것이 중요합니다. 재작업 횟수를 줄이고 제품 개발 리드 타임을 단축하려면 제품 형상뿐만 아니라 재료 선택 및 제품 설계 초기 단계부터 제조 계획 개발까지 고려하는 고품질 설계를 달성하는 것이 필수적입니다. Pahl과 Beitz [2]가 언급한 모범 사례에 따르면 제품 설계는 최종 제품이 필요한 모든 기준을 충족하도록 이러한 측면을 포괄해야 합니다.
그러나 초기 설계 단계에서 복잡한 형상의 제품에 대한 정확한 예측을 하는 것은 종종 어려우며, 이러한 요소를 설계 프로세스 초기에 적절하게 고려하지 않으면 재작업으로 이어질 수 있습니다. 이러한 맥락에서 "사전 예측"은 초기 설계 단계에서 잠재적인 결함을 예비적으로 추정하는 것을 의미합니다.
이는 후속 설계 단계에서 수행되는 상세 예측과는 다릅니다. 정확한 사전 예측은 복잡한 형상의 제품에 대해 어려우며, 이 단계에서의 부정확성은 재작업의 필요성에 기여할 수 있습니다.
Status of Existing Research:
시뮬레이션 기술은 제품을 제조하기 전에 기능을 예측하고 문제를 사전에 수정하기 위한 산업 제품 개발 프로세스에서 널리 채택되어 표준 기술이 되었습니다 [3, 4, 5, 6]. 정확도를 높이기 위한 노력도 계속되고 있으며, 예를 들어 주조 시뮬레이션에서는 전통적으로 용융 금속의 유체 분석에 초점을 맞추었지만 현재는 배압 영향과 스파우트에서의 튀는 거동에 대한 정확도를 개선하기 위해 주변 공기 압축 거동에 대한 계산도 통합하고 있습니다 [7].
또한 검토 사이클 속도를 높이기 위해 양자 컴퓨터를 사용하여 계산 시간을 줄이기 위한 연구가 진행 중입니다 [8]. 그러나 이러한 기술이 실제로 사용되더라도 시뮬레이션을 실행하려면 제조용 다이의 모델 정보를 준비해야 합니다. 수정 사항을 포함하여 시뮬레이션을 한 번 완료하는 데 며칠이 걸립니다.
따라서 시뮬레이션 정확도 및 시간 단축이 실현되더라도 시뮬레이션을 활용한 긴 예비 검토 시간 문제의 일부만 해결되어 제품 개발 초기 단계에서 쉬운 결함 예측이라는 과제가 해결되지 않은 채 남아 있습니다.
Necessity of the Research:
시뮬레이션 기술 발전의 한계점을 감안할 때, 과거 제조 제품의 결함 발생 정보와 축적된 시뮬레이션 결과를 분석 및 활용하여 패턴 인식을 현재 및 미래 생산성 예측에 대한 부가 가치로 전환하는 대안적 접근 방식이 적극적으로 추구되고 있습니다 [9]. 이러한 노력 중 surrogate 모델링이라는 기술은 상세한 시뮬레이션을 실행하는 대신 알려진 데이터에서 얻은 패턴을 사용하여 예측하는 머신 러닝 또는 기타 방법을 사용하여 계산 비용과 사전 필수 정보의 감소를 가능하게 하므로 주목을 받고 있습니다.
예를 들어 Amir Pouya는 신경망을 사용하여 레이저 용접 공정 매개변수를 학습하여 용접 풀의 단면 온도 분포를 예측할 수 있는 모델을 제안했습니다 [10]. 또한 Andres 등은 낮은 계산 비용으로 항공기 블레이드의 단면 형상을 추정하는 수단으로 SVM을 활용한 예측 모델의 효과를 보고했습니다 [11]. 따라서 알려진 데이터를 기반으로 감소된 원본 정보로 필요한 예측을 수행하는 surrogate 모델은 초기 개발 단계에서 제품 형상으로부터 제품 품질을 정확하게 예측하는 문제를 해결할 가능성이 높습니다.
그러나 지금까지 보고된 많은 사례는 3차원 현상을 2차원으로 축소하여 문제를 단순화했으며, 복잡한 3차원 형상이 예측 대상인 현상에 직접 적용할 수 있는지 여부를 명확히 해야 합니다. 또한 제품의 기하학적 정보를 기반으로 주조 공정에서 결함 발생에 대한 surrogate 모델의 효과에 대한 보고는 거의 없습니다. 실현 가능성이 입증되면 산업 제품 개발 프로세스에 큰 영향을 미칩니다.
4. Research Purpose and Research Questions:
Research Purpose:
본 연구의 목적은 제품 설계의 기하학적 특징을 활용하여 다이캐스팅 제품의 다이 크랙을 예측하기 위한 surrogate 모델을 개발하고 검증하는 것입니다. 목표는 제품 형상 데이터를 활용하여 초기 결함 감지를 개선하고 다이캐스팅 공정의 효율성을 향상시키는 것입니다.
Key Research:
- 다이 크랙 예측을 위해 VAE(Variational Autoencoders)와 신경망을 사용하는 새로운 surrogate 모델 개발.
- 기하학적 특징을 사용하여 Toyota Motor Corporation의 엔진 블록 부품 및 트랜스액슬 케이스의 다이 크랙 예측에 대한 모델의 정확도 평가.
- 다이캐스팅에서 초기 결함 감지를 위해 제품 형상 데이터 사용의 효과 조사.
- F1 점수를 사용하여 모델 성능 분석 및 다이 솔더링에 대한 이전 surrogate 모델과 비교.
5. Research Methodology
Research Design:
본 연구는 다이 크랙 예측을 위한 surrogate 모델을 개발하고 평가하는 양적 접근 방식을 사용합니다. 모델은 VAE와 신경망을 사용하여 구축되었으며 엔진 블록 부품 및 트랜스액슬 케이스 데이터 세트로 학습되었습니다. 모델의 예측 성능은 CAE 분석 결과와 비교하여 평가됩니다.
Data Collection Method:
데이터는 Toyota Motor Corporation에서 생산한 113가지 엔진 블록 부품과 130가지 트랜스액슬 케이스의 3D CAD 모델로 구성됩니다. SCSK Corporation의 Adventure 클러스터를 사용하여 계산된 최대 압축 변형률의 시뮬레이션 결과는 다이 크랙 예측의 목표 변수로 사용됩니다. CAD 모델은 특징 추출을 위해 복셀 기반 모델로 변환됩니다.
Analysis Method:
- Surrogate Model Construction: VAE는 복셀화된 3D 모델 표면에서 잘라낸 입방체 형상에서 특징 벡터를 추출하도록 학습됩니다. 그런 다음 신경망은 이러한 특징 벡터에서 시뮬레이션 결과(최대 압축 변형률)를 예측하도록 학습됩니다.
- Model Evaluation: F1 점수가 평가 지표로 사용됩니다. 예측된 결과와 CAE 분석 결과를 비교하기 위해 임계값 이상의 값을 갖는 영역을 결함 영역으로 정의합니다. F1 점수는 예측된 결함 영역과 실제 결함 영역 간의 겹침을 기반으로 계산됩니다. 부트스트랩 방법은 다이 솔더링에 대한 이전 surrogate 모델과의 성능을 비교하는 데 사용됩니다.
Research Subjects and Scope:
본 연구는 다이캐스팅을 사용하여 Toyota Motor Corporation에서 생산한 엔진 블록 부품 및 트랜스액슬 케이스의 다이 크랙 예측에 중점을 둡니다. 이러한 부품의 기하학적 특징은 surrogate 모델의 주요 입력입니다. 범위는 열 응력, 특히 저주기 피로로 인한 다이 크랙으로 제한됩니다.
6. Main Research Results:
Key Research Results:
- 기하학적 특징을 기반으로 VAE와 신경망을 사용하여 다이캐스팅 제품의 다이 크랙을 예측하기 위한 surrogate 모델이 성공적으로 개발되었습니다.
- 모델은 Toyota Motor Corporation의 엔진 블록 부품 및 트랜스액슬 케이스의 다이 크랙 예측에서 유망한 결과를 보여주었습니다.
- 엔진 블록 부품의 경우 모델은 약 0.62의 F1 점수를 달성했으며, 594개의 진양성(TP), 208개의 위음성(FN), 530개의 위양성(FP)이 있었습니다.
- 트랜스액슬 케이스 모델의 경우 F1 점수는 약 0.58이었으며, 174개의 TP, 73개의 FN, 178개의 FP가 있었습니다.
- 다이 크랙 예측 모델의 성능은 이전에 개발된 다이 솔더링용 surrogate 모델의 성능과 비슷합니다.
Analysis of presented data:
- Figure 6: VAE 및 신경망의 학습 곡선을 보여주며, 엔진 블록 및 트랜스액슬 케이스 모델 모두에 대해 적절한 학습 진행 상황을 나타냅니다.
- Figure 7: 결정 임계값이 변함에 따라 F1 점수의 전환을 보여주며, 두 모델 모두에서 비교적 높은 F1 점수를 달성할 수 있음을 보여줍니다.
- Figure 8: 부트스트랩 F1 점수 차이 분포를 제시하여 다이 크랙 예측 모델이 다이 솔더링 모델과 유사한 수준의 예측 정확도를 달성함을 시사합니다.
- Figure 9: 모델 수 증가에 따른 F1 점수의 추세를 보여주며, 데이터 세트가 커질수록 정확도 향상이 포화 상태에 도달하여 데이터 볼륨 증가보다는 아키텍처 변경의 필요성을 시사합니다.
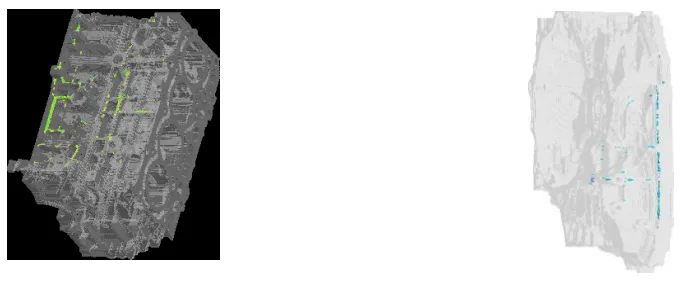
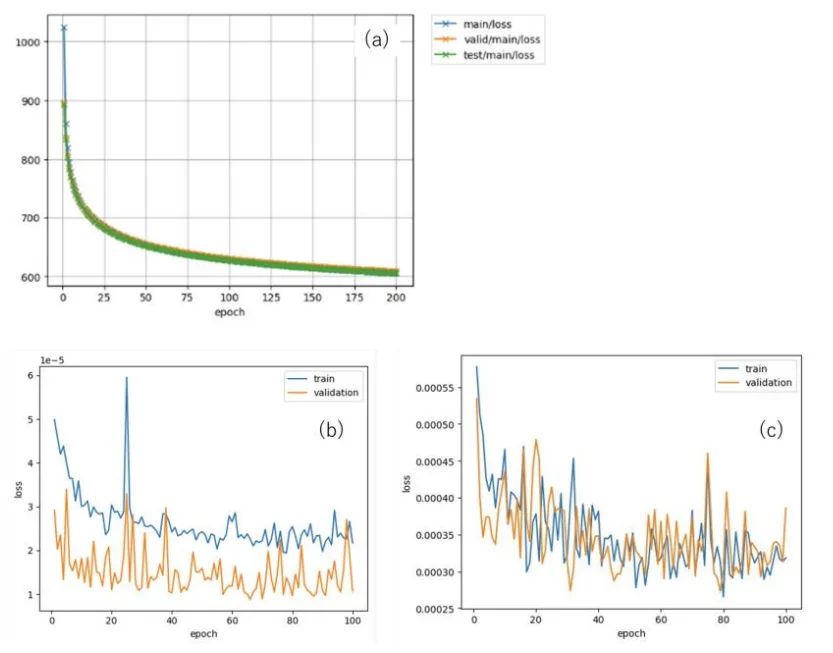
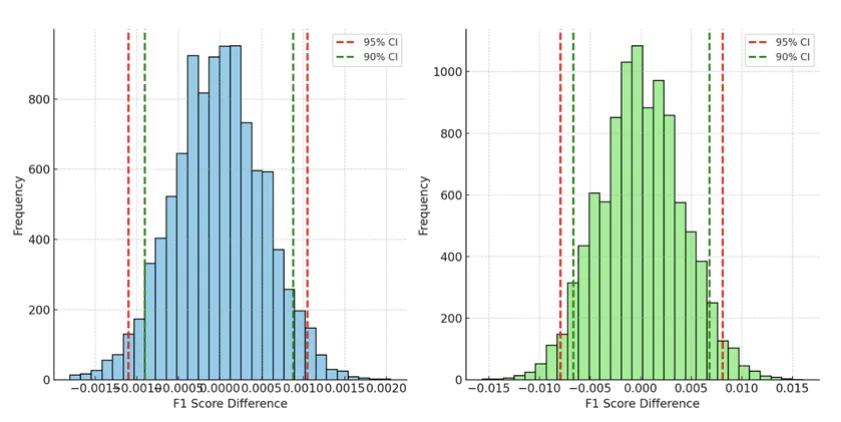
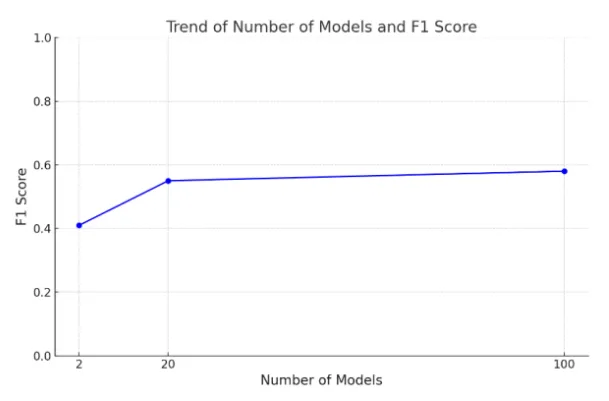
Figure Name List:
- Figure 1: Image of Die in the actual die-casting process, which has cracks (red lines) on the surface.
- Figure 2: Image of product shape (a)Engine block, (b)Trans axel case.
- Figure 3: Image of constructing the surrogate model.
- Figure 4: Image of evaluation method.
- Figure 5: Architecture of VAE and neural network.
- Figure 6: Train curve of a) VAE, b) Neural network for the engine block, and (c)Trans axel case.
- Figure 7: Transition of F1 score of a) Engine block's surrogate model and b) Trans axel case's surrogate model.
- Figure 8: Bootstrap distribution of F1 score difference between (a) Engine model and referenced model, and (b)Trans axel case model and referenced model.
- Figure 9: Trends of the Number of Engine block models and F1 score
- Figure 10: Example of (a) rule-based prediction and (b) actual die model.
- Figure 11: Die architecture of the pertinent part
7. Conclusion:
Summary of Key Findings:
본 연구에서는 VAE 및 NN을 사용하여 제품 형상을 기반으로 다이캐스팅 다이의 다이 크랙을 예측하는 surrogate 모델을 성공적으로 구축하여 특정 수준의 정확도를 달성했습니다. 이 모델은 기하학적 특징을 활용하고 다이 솔더링 예측을 위한 이전 모델과 비슷한 성능을 보여줍니다. 그러나 모델은 냉각 회로와 같은 복잡한 내부 특징이 있는 영역에서 크랙을 정확하게 예측하는 데 한계가 있어 위양성이 발생합니다. 데이터 볼륨 증가로 인한 정확도 향상은 포화 상태에 도달하는 것으로 보이며, 표면 형상 외에 추가 요소를 통합하거나 보다 정교한 모델 아키텍처가 필요함을 시사합니다.
Academic Significance of the Study:
본 연구는 다이캐스팅에서 중요한 결함인 다이 크랙 예측에 기하학적 특징 기반 surrogate 모델을 사용하는 것의 타당성을 입증함으로써 해당 분야에 기여합니다. VAE와 신경망을 이 목적을 위해 사용하는 새로운 접근 방식을 소개하고 형상 데이터를 사용한 예측 정확도에 대한 벤치마크를 제공합니다. 본 연구는 다이캐스팅에서 형상 기반 결함 예측의 잠재력과 한계를 강조하여 이 분야의 추가 연구를 위한 길을 열었습니다.
Practical Implications:
개발된 surrogate 모델은 기존 시뮬레이션 기술에 비해 다이캐스팅에서 초기 결함 예측을 위한 더 빠르고 효율적인 방법을 제공합니다. 제품 형상 데이터를 활용하여 엔지니어는 초기 설계 단계에서 잠재적인 다이 크랙 위험을 식별하는 데 도움을 받아 제품 품질을 향상시키고 개발 리드 타임과 비용을 줄이기 위한 사전 예방적 설계 수정이 가능합니다.
Limitations of the Study and Areas for Future Research:
모델의 정확도는 열 응력 및 크랙에 큰 영향을 미치는 냉각 회로와 같은 내부 다이 특징을 무시하고 표면 형상 데이터에만 의존한다는 제한이 있습니다. 숨겨진 설계 요소가 있는 영역, 특히 위양성의 발생은 이러한 한계를 나타냅니다. 향후 연구에서는 예측 정확도를 개선하고 위양성을 줄이기 위해 냉각 회로 배열 및 다이 내부의 온도 분포와 같은 더 다양한 요소를 모델에 통합하는 데 중점을 두어야 합니다. 학습 아키텍처의 근본적인 변화를 탐구하고 모델 학습 데이터를 최적화하는 것도 추가적인 정확도 향상을 위해 제안됩니다.
8. References:
- [1] Czerwinski, F.: Current Trends in Automotive Lightweighting Strategies and Materials, Materials, 14(6631), 2024. http://doi.org/10.3390/ma14216631
- [2] Pahl, G.; Beitz, W.; Feldhusen, J.; Grote, K.-H.: Engineering Design: A Systematic Approach (3rd ed., Wallace, K.; Blessing, L., Trans. & Eds.), Springer, 2007.
- [3] Morgan, J. M.; Liker, J. K.: The Toyota Product Development System, Productivity Press, New York, NY, 2006.
- [4] Khalilpourazary, S.; Dadvand, A.; Azdast, T.; Sadeghi, M. H.: Design and manufacturing of a straight bevel gear in hot precision forging process using finite volume method and CAD/CAE technology, International Journal of Advanced Manufacturing Technology, 56, 87-95. http://doi.org/10.1007/s00170-011-3159-z
- [5] Kwon, H.-J.; Kwon, H.-K.: Computer-aided engineering (CAE) simulation for the design optimization of gate system on high pressure die casting (HPDC) process, Robotics and Computer-Integrated Manufacturing, 55(Part B), 2019, 147-153. http://doi.org/10.1016/j.rcim.2018.01.003
- [6] Liu, J.; Ma, Y.; Fu, J.; Duke, K.: A novel CACD/CAD/CAE integrated design framework for fiber-reinforced plastic parts, Advances in Engineering Software, 87, 2015, 13-29. http://doi.org/10.1016/j.advengsoft.2015.04.013
- [7] Matsushita, S.; Aoki, T.: Gas-liquid two-phase flows simulation based on a weakly compressible scheme with interface-adapted AMR method, 2021.
- [8] Gaitan, F.: Finding Solutions of the Navier-Stokes Equations through Quantum Computing—Recent Progress, a Generalization, and Next Steps Forward, 2021.
- [9] Fei, T.; Jiangfeng, C.; Qinglin, Q.; Meng, Z.; He, Z.; Fangyuan, S.: Digital twin-driven product design, manufacturing and service with big data, International Journal of Advanced Manufacturing Technology, 94, 2018, 3563-3576.
- [10] Hemmasian, A. P.; Ogoke, F.; Akbari, P.; Malen, J.; Beuth, J.; Barati Farimani, A.: Surrogate Modeling of Melt Pool Temperature Field using Deep Learning, Additive Manufacturing Letters, 5, 2023
- [11] Paulete-Periáñez, C.; Andrés-Pérez, E.; Lozano, C.: Surrogate modelling for aerodynamic coefficients prediction in aeronautical configurations, Proceedings of the 8th European Conference for Aeronautics and Space Sciences (EUCASS), http://doi.org/10.13009/EUCASS2019-870.
- [12] Yamazaki, T.; Hirokawa, K.; Murakami, A.; Baba, M.; Muramatsu, C.: Predicting Soldering Failure in Die-Cast Products Using a Surrogate Model Based on Geometrical Features, CAD Journal, 21(4), 2024, 581-590. http://www.cad-journal.net/files/vol_21/CAD_21(4)_2024_581-590.pdf
- [13] Brock, A.; Lim, T.; Ritchie, J. M.; Weston, N.: Generative and Discriminative Voxel Modeling with Convolutional Neural Networks, arXiv preprint arXiv:1608.04236.
- [14] Klobčar, D.; Tušek, J.; Taljat, B.: Thermal fatigue of materials for die-casting tooling, Materials Science and Engineering: A, 472(1-2), 2008, 198-207. http://doi.org/10.1016/j.msea.2007.03.025
- [15] ADVENTURE PROJECT Seminar Materials: Material and Geometric Nonlinear Algorithms (ADV_Solid), Presented on May 15, 2001, University of Tokyo. Retrieved from: https://adventure.sys.t.u-tokyo.ac.jp/jp/pub/seminar20010515/adv_seminar_solver_algo/index.htm
- [16] Roger, L.: An Introduction to the Boostrap, 2021.
- [17] Namiki, K.; Kawano, M.; Schade, T.: High Thermal Conductivity Steel and its Application to Die Casting Tools, NADCA Die Casting Congress & Exposition, Transaction No. T12-071, 2012.
- [18] Morris Jr, J. W.; Guo, Z.; Krenn, C. R.; Kim, Y.-H.: The Limits of Strength and Toughness in Steel, ISIJ International, 41(6), 2001, 599-611.
9. Copyright:
- This material is "Tomoya Yamazaki"'s paper: Based on "Predicting Die Cracking in Die-Cast Products Using a Surrogate Model Based on Geometrical Features".
- Paper Source: https://doi.org/10.14733/cadaps.2025.217-228
This material was created to introduce the above paper, and unauthorized use for commercial purposes is prohibited.
Copyright © 2025 CASTMAN. All rights reserved.