본 논문 요약은 ['Journal of Materials Engineering and Performance']에서 발행한 ['Low Solution Temperature Heat Treatment of AlSi9Cu3(Fe) High-Pressure Die-Casting Actual Automotive Components'] 논문을 기반으로 작성되었습니다.
1. 개요:
- 제목: 낮은 용액 온도 열처리된 AlSi9Cu3(Fe) 고압 다이캐스팅 실제 자동차 부품['Low Solution Temperature Heat Treatment of AlSi9Cu3(Fe) High-Pressure Die-Casting Actual Automotive Components']
- 저자: Silvia Cecchel, Andrea Panvini, Giovanna Cornacchia
- 발행 연도: 2018년
- 발행 학술지/학회: Journal of Materials Engineering and Performance, ASM International
- 키워드: 블리스터, 열처리, 고압 다이캐스팅, 비철 합금, 기공, 2차 알루미늄 합금


2. 초록 또는 서론
고압 다이캐스팅(HPDC) 부품은 일반적으로 표면 블리스터 발생으로 인해 고온에서 열처리할 수 없으며, 이는 표면 마감을 저해하고 기계적 물성을 감소시킬 수 있습니다. 이러한 맥락에서 본 논문의 목적은 HPDC AlSi9Cu3 합금에 대한 특수 저온 용체화 T6 열처리 효과를 분석하는 것입니다.
블리스터 발생을 방지하기 위해 매우 낮은 용체화 온도(< 450 °C, 165 °C 시효 후)를 일반적인 시간(1~16시간)과 조합하여 산업적 적용 가능성을 확보했습니다.
일반적인 생산에서 발생하는 전형적인 결함을 평가하기 위해 실제 주조품에서 추출한 시편에 대해 열처리를 수행했습니다. 물성은 외관 검사, 미세 조직 관찰, 이미지 분석, 경도, 인장 시험 및 파면 분석을 통해 분석했습니다. 그 결과 AlSi9Cu3 합금에서 현저한 블리스터링 없이 강화 효과를 얻기 위해 T6 열처리에서 수 시간 동안 450 °C 미만의 용체화 온도를 사용하는 것이 가능하다는 것을 보여주었습니다.
최적의 물성 조합은 430 °C에서 4시간 용체화 처리 후 165 °C에서 8시간 시효 처리하여 항복 강도가 약 50 MPa 증가하고 연성이 증가하며 최상의 품질 지수 값을 나타내는 조건에서 얻어졌습니다.
3. 연구 배경:
연구 주제 배경:
수송은 전 세계 대기 질에 큰 영향을 미치므로 자동차 배기가스 감소는 주요 관심사입니다. 이러한 맥락에서 주요 달성 가능한 해결책 중 하나는 수송 차량을 경량화하기 위해 알루미늄 합금(Ref 1, 2)과 같은 저밀도 재료를 사용하는 것입니다.
실제로 현재 기존의 강철 및 주철을 알루미늄 합금으로 대체하는 추세가 있습니다(Ref 3-5). 이러한 맥락에서 항상 기존 합금을 최적화해야 할 필요가 있다는 점에 주목할 가치가 있습니다. 왜냐하면 모든 응용 분야의 요구 사항을 충족하는 합금을 찾기가 어렵기 때문입니다.
또한 화학 조성은 광범위한 조성 범위에서 다양한 물성을 나타내는 특정 합금을 선택하는 데 있어 중요한 요소 중 하나입니다(Ref 6, 7). 제조 관점에서 고압 다이캐스팅(HPDC)은 높은 생산성(Ref 8, 9)으로 인해 경합금을 대량 생산하는 데 가장 널리 사용되는 방법입니다.
알루미늄 합금에 가장 다재다능한 기술로 인정받는 장점에도 불구하고 HPDC는 금속 다이 충전의 속도와 빠른 응고로 인해 주조품에 고압으로 공기가 갇히는 단점이 있습니다(Ref 10). 이러한 높은 수준의 기공은 다이캐스팅 부품에 열처리를 수행할 수 없는 이유입니다(Ref 11).
기존 연구 현황:
HPDC의 단점을 극복하기 위해 반용융 금속 및 레오캐스팅 공정과 같은 유망한 기술에 대한 다양한 연구가 제조 과정에서 더 높은 건전성을 제공합니다(Ref 12, 13). 기계적 및 구조적 관점에서 중력 주조 기술은 우수한 성능을 보장하지만 제조 사이클의 느림과 잠재적인 중량 감소를 제한하는 더 높은 부품 두께 요구 사항으로 인해 대량 생산에는 적합하지 않습니다(Ref 14-19).
오늘날 HPDC 기술은 여전히 품질과 비용 간의 최상의 절충안을 제공하기 때문에 가장 널리 사용됩니다. HPDC 부품의 가장 큰 불편함은 고온에서 열처리 수행의 복잡성입니다.
이는 인장 거동을 감소시키는 표면 블리스터링(고압 공기 포집으로 인해 발생) 형성 때문입니다(Ref 20). 최근 진공을 추가하는 기존 HPDC 공정의 업그레이드가 개발되었습니다.
이 새로운 기술은 가스 기공을 최소화하여(Ref 21) 주조품의 최종 품질을 크게 향상시킵니다. 매우 중요한 측면은 낮은 가스 함량 덕분에 진공 다이캐스팅 부품을 열처리할 수 있다는 것입니다(Ref 21).
반면에 진공 지원 없이 HPDC 기술로 2차 합금에 대한 높은 기계적 물성을 달성하는 것은 확실히 더 저렴한 솔루션으로 이어질 것입니다.
연구의 필요성:
사실 2차(스크랩에서 생산) AlSi9CuX 합금은 좋은 기계적 물성과 고온에서의 거동으로 인해 재활용 알루미늄의 높은 양에도 불구하고(Ref 22, 23) 실린더 헤드 및 엔진과 같은 광범위한 부품 생산을 위해 수송 분야에서 가장 많이 사용됩니다. 이러한 재처리된 2차 알루미늄 합금이 자동차 경량화의 환경적 이점을 개선하고 극대화하는 데 중요하다는 점에 주목할 가치가 있습니다(Ref 24-28).
이러한 합금의 사용을 더 무거운 응용 분야로 확장하기 위해 기존 HPDC 부품의 고온 열처리 한계를 극복하는 것이 큰 과제입니다. 본 연구를 더 잘 이해하기 위해 이 등급의 합금에 대한 몇 가지 세부 정보를 제공하는 것이 중요합니다. 이들의 기계적 물성은 특히 Mg 및 Cu 함량 측면에서 사용된 조성에 의해 크게 영향을 받으며, 표준 EN 1706:1998을 따릅니다.
특히 AlSi9Cu3은 공정 실리콘과 다양한 금속간 화합물로 채워진 1차 수지상 α-알루미늄 기질로 구성됩니다. Al-Si 합금에 구리를 첨가하면 열처리성이 증가하고 CuAl2 상 및 기타 금속간 화합물이 형성되어 주조 부품의 강도가 증가합니다(Ref 29-31). 구리 첨가는 합금의 융점과 공정 온도를 크게 감소시킵니다.
따라서 구리는 합금의 응고 범위를 확장하고(Ref 30, 32, 33) 기공 형성 조건을 용이하게 합니다(Ref 34). 고용체 열처리 없는 석출 경화 효과는 주로 주조 후 냉각 속도에 따라 달라지며, 벽 두께와 주조 변수에 영향을 받으므로 주조품에서 서로 다른 기계적 물성이 달성됩니다(Ref 35).
일반적으로 동일한 등급의 합금으로 만들어지고 다른 주조 기술로 생산된 부품의 경우 합금 균질화, 공정 실리콘의 구상화 및 기질 내 금속간 화합물의 용해를 개선하기 위해 비교적 높은 온도에서 용체화 처리가 채택됩니다(Ref 36). β-Mg2Si 및 θ-Al2Cu와 같은 입자는 π-Al8Mg3FeSi6, Q-Al5Cu2Mg8Si6 및 Al15(Fe, Mn)3Si2(Ref 36)와 같은 다른 입자보다 쉽게 용체화됩니다.
서로 다른 주조 Al-Si 합금의 미세 조직 및 기계적 물성에 대한 열처리 중 서로 다른 공정 변수(온도 및 시간)의 영향은 광범위하게 연구되었습니다(Ref 37-42). Cu가 없는 합금에 비해 Cu가 있는 Al 합금은 주조 미세 조직의 형태 때문에 균질화 시간이 연장된다는 점을 입증할 가치가 있습니다(Ref 17, 43).
이러한 예 중 일부는 최근 Lumley 등의 연구입니다(Ref 10, 44-46). 이 연구에서는 HPDC Al-Si-X 합금 부품을 블리스터 발생 없이 열처리할 수 있는 실험실 규모 공정 변수 범위를 성공적으로 확립했습니다. 이 공정은 다른 기술을 사용하여 주조된 부품에 사용되는 것보다 낮은 용체화 온도(< 500 °C)와 짧은 시간(~ 15분)을 적용하는 것으로 구성됩니다.
Pabel 등(Ref 47)은 Al Si9Cu3(Fe)(Zn) 합금을 연구하여 서로 다른 열처리 조건의 영향을 조사했습니다. 특히 고압 다이캐스팅 시편은 주조 직후 급냉하고 이후 실온 또는 승온에서 보관했습니다. 자연 시효와 인공 시효의 조합도 테스트되었습니다. 그 결과 최적화된 두 처리의 조합으로 개선된 기계적 물성을 얻을 수 있음을 보여줍니다. 이러한 고려 사항은 본 논문의 맥락에 초점을 맞추었습니다.
실제로 본 연구의 목적은 일반적인 HPDC AlSi9Cu3 합금을 열처리할 가능성을 조사하는 것이며, 동시에 실제 산업 공정의 일반적인 제약 조건을 고려하는 것입니다. 이러한 방식으로 고려된 주요 요구 사항은 균일한 배치 조건을 보장하는 것이었으며, 이는 주조 공장에서 더 긴 처리 시간을 의미합니다. 특수 T6 열처리가 개발되었으며, AlSi9Cu3 합금에서 현저한 블리스터링 없이 강화 효과가 있는지 확인했습니다.
특히 매우 낮은 용체화 온도(< 450 °C, 165 °C 시효 후)를 일반적인 시간(1~16시간)과 조합하여 산업적 적용 가능성을 확보했습니다. 이러한 낮은 온도는 더 오랜 시간 동안 유지되더라도 공기 기공 팽창에 영향을 미치지 않는 것으로 가정됩니다. 또한 저온 열처리는 HPDC 부품 가열로 인해 발생하는 다른 일반적인 문제인 팽창 및 변형을 방지하고, 처리 시간을 연장하면 더 큰 균질화와 결과적으로 더 나은 시효 반응을 제공합니다.
일반적인 생산에서 발생하는 전형적인 결함을 평가하기 위해 실제 주조품에서 추출한 시편에 대해 열처리를 수행했습니다. 물성은 외관 검사, 미세 조직 관찰, 경도, 인장 시험 및 파면 분석을 통해 분석했습니다.
4. 연구 목적 및 연구 질문:
연구 목적:
본 연구의 주요 목적은 저온 용체화 T6 열처리가 일반적인 HPDC AlSi9Cu3 합금 부품의 기계적 물성을 향상시키는 데 효과적인지 평가하고, 특히 표면 블리스터링 완화에 초점을 맞추는 것입니다.
핵심 연구:
본 연구는 매우 낮은 용체화 온도(< 450 °C)를 산업적으로 적용 가능한 처리 시간(1~16시간) 및 후속 165 °C 시효 단계와 결합하여 현저한 블리스터링 없이 AlSi9Cu3 합금에서 상당한 강화를 달성할 수 있는지 여부에 중점을 둡니다. 본 연구는 기계적 물성을 극대화하기 위해 이러한 제약 조건 내에서 최적의 용체화 온도 및 시간 조합을 탐구합니다.
연구 가설:
중심 가설은 T6 열처리에서 450 °C 미만의 용체화 온도를 장시간 사용하여 AlSi9Cu3 합금에서 유해한 블리스터링을 유발하지 않고 강화를 달성하는 것이 가능하다는 것입니다. 또한 이러한 낮은 온도에서 용체화 처리 시간을 연장하면 균질화가 촉진되고 시효 반응이 개선되어 기계적 물성이 향상될 것이라는 가설을 세웠습니다.
5. 연구 방법론
연구 설계:
본 연구는 T6 열처리 사이클 내에서 용체화 처리 변수를 체계적으로 변화시키는 실험 설계를 채택했습니다. 예비 저온 용체화 처리(< 450 °C)를 다양한 시간(1, 2, 4, 8, 16시간)으로 수행하여 경도 반응과 미세 조직 변화를 평가했습니다. 이러한 예비 결과를 바탕으로 선택된 용체화 온도(430, 450 및 490 °C)와 시간(4, 8 및 490 °C의 경우 0.25시간)을 165 °C에서 다양한 시간(1, 2, 4, 8, 16시간) 동안 일정한 인공 시효 처리와 결합하여 T6 열처리 세트를 설계했습니다.
데이터 수집 방법:
분석용 시편은 2차 AlSi9Cu3 합금(EN AC 46000)으로 만든 실제 HPDC 자동차 부품에서 추출했습니다. 데이터 수집에는 다음 방법이 사용되었습니다.
- 외관 검사: 용체화 처리 후 블리스터링을 감지하기 위해 외관 검사를 통해 표면 품질을 평가했습니다.
- 미세 조직 관찰: 광학 현미경을 사용하여 용체화 처리 전후의 미세 조직 변화를 조사하고, 실리콘 파편화 및 구상화에 초점을 맞췄습니다.
- 경도 시험: 비커스 경도 HV60 시험을 수행하여 ASTM E 18-03 절차(Ref 48)에 따라 열처리가 합금 경도에 미치는 영향을 정량화했습니다.
- 인장 시험: 원통형 다이캐스팅 인장 시편을 UNI EN ISO 6892-1:2009 표준에 따라 시험하여 항복 강도(σy), 인장 강도(σm) 및 연신율(A%)을 평가했습니다.
- 파면 분석: 주사 전자 현미경(SEM)을 사용하여 인장 시편의 파단면과 직교 단면을 조사하여 파괴 메커니즘과 미세 조직 특징을 분석했습니다.
- 에너지 분산 분광법(EDS): EDS를 사용한 반정량적 화학 분석을 수행하여 금속간 화합물을 특성화했습니다.
- 이미지 분석: LAS 4.0 소프트웨어를 사용하여 직교 단면에서 금속간 화합물 이미지 분석을 수행하여 금속간 화합물 부피, 크기, 원형도 및 기공도를 정량화했습니다.
분석 방법:
수집된 데이터를 분석하여 서로 다른 용체화 처리 변수가 AlSi9Cu3 합금의 기계적 물성 및 미세 조직에 미치는 영향을 결정했습니다. 경도-시간 곡선을 플로팅하여 용체화 처리의 동역학을 평가했습니다.
인장 시험 결과를 비교하여 기계적 물성 개선을 평가하고, 품질 지수(QI)(Ref 52)를 계산하여 전체 야금 품질을 비교했습니다.
미세 조직 이미지와 파면 분석을 분석하여 물성 변화와 미세 조직 진화(실리콘 구상화, 금속간 화합물 상 형태 변화), 기공 특성 간의 상관 관계를 분석했습니다. 이미지 분석은 금속간 화합물 및 기공 특징에 대한 정량적 데이터를 제공하여 질적 관찰을 뒷받침했습니다.
연구 대상 및 범위:
본 연구는 자동차 부품에 일반적으로 사용되는 2차 AlSi9Cu3 합금(EN AC 46000)에 초점을 맞췄습니다. 실제 생산 조건과의 관련성을 확보하기 위해 산업적으로 생산된 HPDC 자동차 주조품에서 시편을 추출했습니다.
본 연구의 범위는 저온 용체화 T6 열처리 및 블리스터링과 기계적 물성, 특히 항복 강도, 인장 강도, 연신율 및 경도에 미치는 영향 조사로 제한되었습니다.
6. 주요 연구 결과:
핵심 연구 결과:
본 연구는 450 °C 미만의 용체화 온도를 갖는 저온 용체화 T6 열처리를 HPDC AlSi9Cu3 합금 부품에 적용하여 현저한 블리스터링을 유발하지 않고 효과적으로 적용할 수 있음을 성공적으로 입증했습니다. 확인된 최적의 열처리 조건은 430 °C에서 4시간 용체화 처리 후 165 °C에서 8시간 시효 처리였습니다.
이 처리로 인해 항복 강도가 약 50 MPa 증가하고, 연성이 2배 증가했으며, 최고 품질 지수 값이 나타났으며, 이는 주조 상태보다 50% 향상된 것입니다. 경도 측정 결과 430 °C와 450 °C 모두에서 용체화 시간이 증가함에 따라 경도가 점진적으로 감소하여 점진적인 금속간 화합물 용해 및 실리콘 파편화를 시사했습니다.
인장 시험 결과 주조 상태에 비해 모든 열처리된 시편에서 기계적 저항이 향상되었으며, 항복 강도와 인장 강도는 용체화 온도에 따라 증가했습니다.
제시된 데이터 분석:
- 경도-시간 곡선(그림 2 및 4): 용체화 시간이 증가함에 따라 경도가 감소하여 실리콘 구상화 및 금속간 화합물 용해를 나타냅니다. 시효 후 경도가 증가하여 시효 경화 반응을 확인했습니다.
- 광학 현미경(그림 3): 열처리 후 실리콘 상의 파편화 및 구상화, 합금의 균질화를 포함한 미세 조직 변화를 보여주었습니다.
- 인장 시험 곡선(그림 5): T6 처리 후 인장 물성이 개선되었으며, 용체화 온도에 따라 변동이 있었습니다.
- SEM 분석(그림 6 및 7): 파단면과 직교 단면을 보여주며, 금속간 화합물 상과 기공을 나타냅니다. 로제트 모양의 Fe-Mn 입자가 파단면에서 관찰되었습니다(표 4).
- EDS 분석(표 3 및 4): 금속간 화합물 상의 조성 데이터를 제공했습니다.
- 이미지 분석(표 5): 금속간 화합물 특징을 정량화하여 용체화 온도가 증가함에 따라 금속간 화합물 크기와 원형도가 감소하고, 열처리 후 기공 크기가 증가하는 것을 보여주었습니다.
그림 목록:
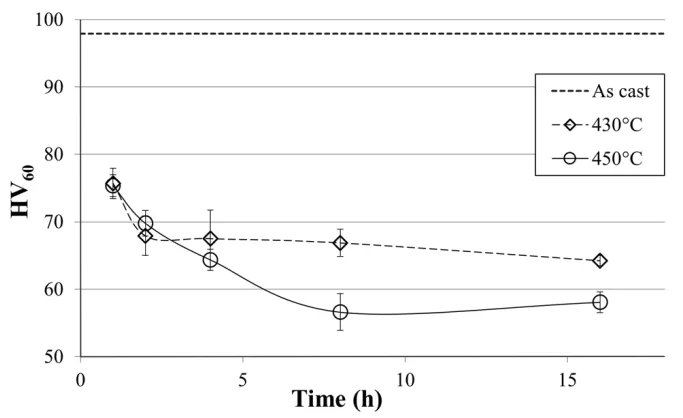
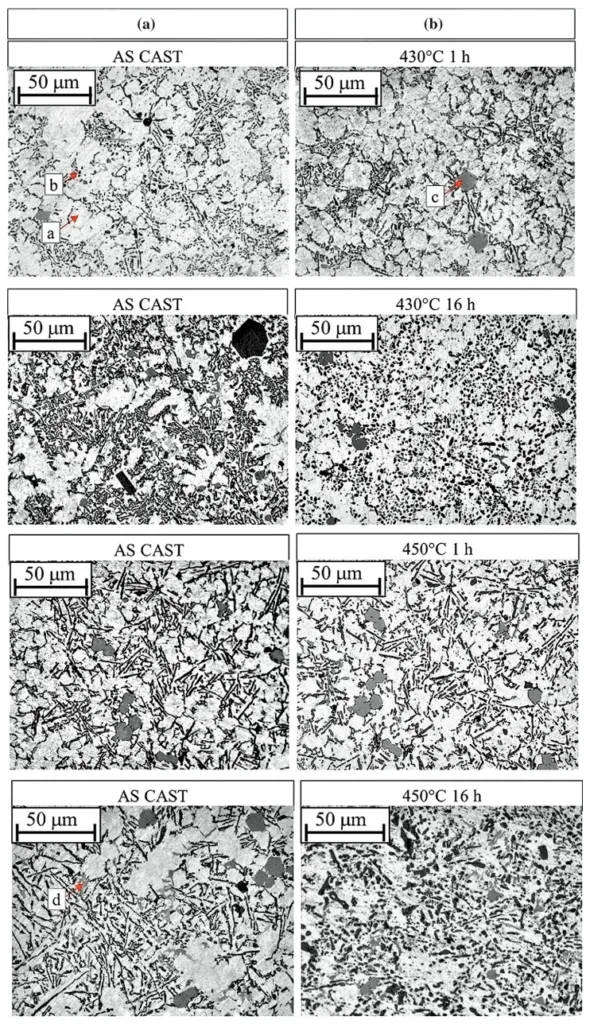
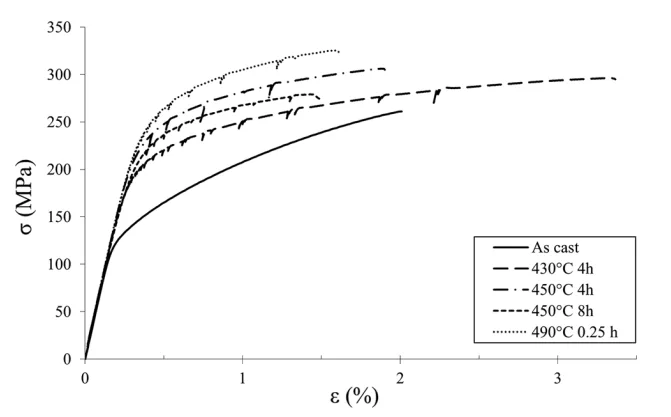
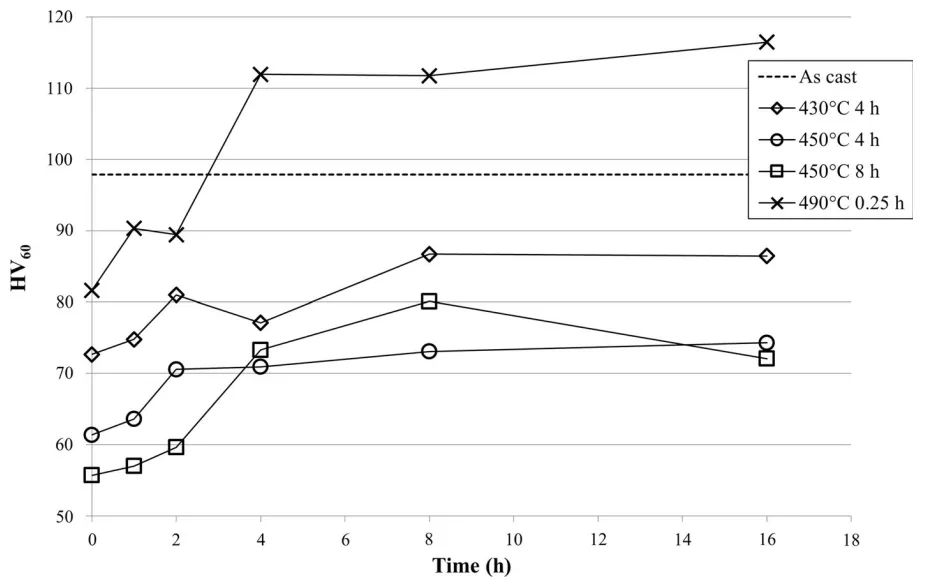
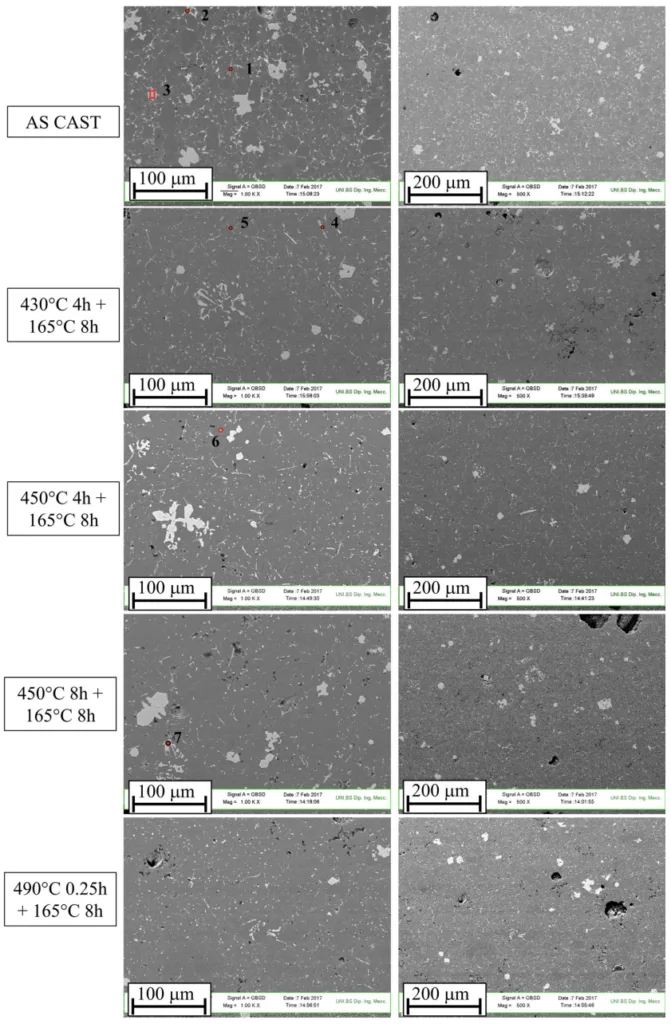
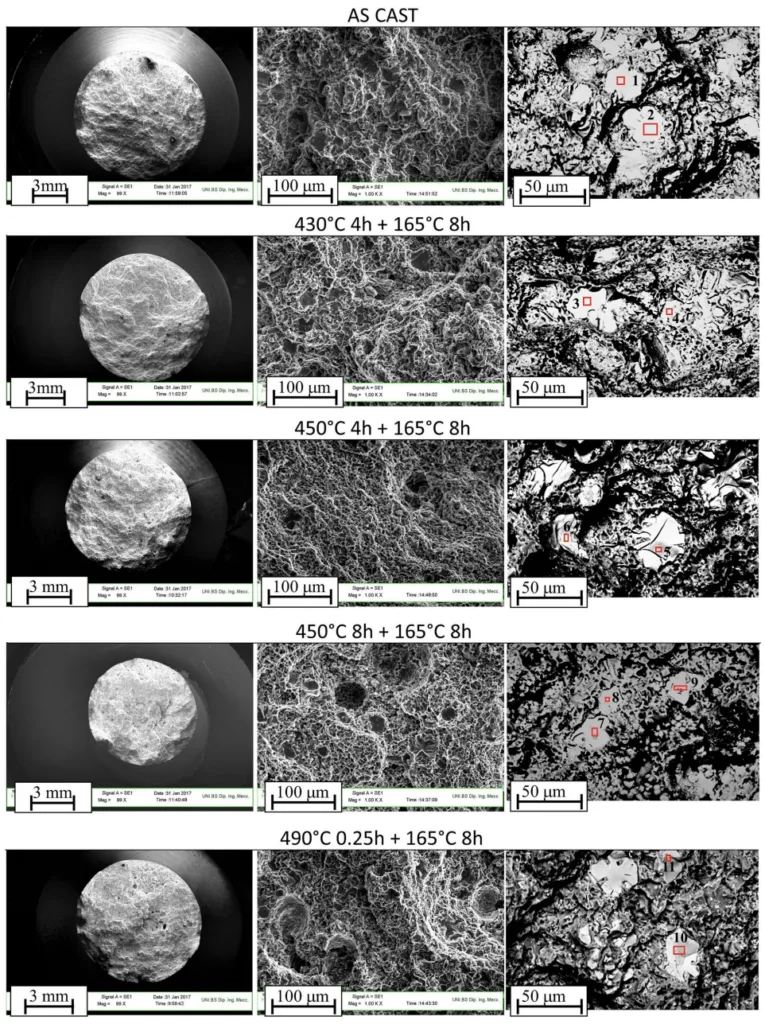
- 그림 1 실험적 용체화 처리 변수(좌) 및 실험적 T6 열처리 조건 선택(우)
- 그림 2 서로 다른 시간-온도 조건에서 용체화 처리된 합금 EN AC 46000의 경도-시간 곡선
- 그림 3 주조 상태(A) 및 430 및 450 °C(B)에서 용체화 처리된 EN AC 46000 시편의 동일 단면에 대한 광학 현미경 500배 배율. 상세 정보: α-Al-수지상 결정(a), Al-Si-Al2Cu-공정(b), 1차 Al15 (Mn, Fe,Cr)3Si2 (c) 및 Al₂Cu (d)
- 그림 4 165 °C에서 시효 처리된 합금 EN AC 46000의 경도-시간 곡선(서로 다른 용체화 처리 절차 후)
- 그림 5 서로 다른 용체화 처리 절차 후 165 °C에서 8시간 시효 처리된 합금 EN 46000의 인장 시험 곡선 비교
- 그림 6 인장 시편의 직교 단면에 대한 SEM
- 그림 7 인장 시편의 파단면에 대한 SEM
- 그림 8 축에 직교하는 단면에 대한 SEM 조사에서 금속간 화합물 매핑 결과
7. 결론:
주요 결과 요약:
본 연구는 HPDC 2차 AlSi9Cu3 합금에 저온 용체화 T6 열처리를 적용하는 것이 가능하다는 것을 결정적으로 입증합니다. 450 °C 미만의 용체화 온도를 산업적으로 관련된 시간과 결합하여 현저한 블리스터링을 유발하지 않고 합금을 효과적으로 강화했습니다. 최적으로 확인된 T6 처리는 430 °C/4시간 용체화 및 165 °C/8시간 시효를 포함하며, 항복 강도(약 50 MPa 증가), 연성(2배 증가) 및 전체 품질 지수(약 50% 증가)에서 상당한 개선을 가져왔습니다.
연구의 학문적 의의:
본 연구는 HPDC 알루미늄 합금, 특히 2차 합금의 열처리 반응에 대한 과학적 이해에 기여합니다. 기존에 사용되던 것보다 낮은 용체화 온도에서 효과적인 강화를 달성할 수 있음을 입증하여 열처리 가능한 HPDC 부품의 가공 범위를 확장합니다. 본 연구는 저온 용체화 처리 변수, 미세 조직 진화(실리콘 구상화, 금속간 화합물 상 변형) 및 결과적인 기계적 물성 간의 관계에 대한 귀중한 통찰력을 제공합니다.
실용적 의미:
본 연구 결과는 HPDC 2차 AlSi9Cu3 합금 부품을 열처리하는 실용적으로 실행 가능하고 더 저렴한 접근 방식을 제공합니다. 진공 보조 HPDC 또는 고온 용체화 처리의 필요성을 없앰으로써 이 저온 T6 공정은 기존 주조 환경에서 쉽게 구현될 수 있으며, 기계적 성능을 향상시키고 HPDC 알루미늄 부품, 특히 자동차 분야에서의 응용 범위를 확장할 수 있습니다.
연구의 한계 및 향후 연구 분야:
본 연구는 중요한 통찰력을 제공하지만 다양한 HPDC 부품 형상 및 합금 조성에 대해 저온 T6 처리를 최적화하기 위한 추가 연구가 필요합니다. 최적화된 변수로 처리된 부품의 피로 및 크리프 거동을 포함한 장기 성능 평가가 권장됩니다. 저온 용체화 처리 중 금속간 화합물 상 변형 및 기공 진화의 정확한 메커니즘에 대한 추가 조사도 유익할 것입니다.
8. 참고 문헌:
- [참고 문헌 목록은 원본 요약의 8번 참고 문헌 목록과 동일]
9. 저작권:
- 본 자료는 "[Silvia Cecchel, Andrea Panvini, and Giovanna Cornacchia]"의 논문: "[Low Solution Temperature Heat Treatment of AlSi9Cu3(Fe) High-Pressure Die-Casting Actual Automotive Components]"을 기반으로 합니다.
- 논문 출처: https://doi.org/10.1007/s11665-018-3478-4
본 자료는 위 논문을 기반으로 요약되었으며, 상업적 목적으로 무단 사용하는 것을 금지합니다.
Copyright © 2025 CASTMAN. All rights reserved.