본 논문 요약은 ['Saitama University']에서 발행한 ['Effects of Casting Defects on Mechanical Properties of Aluminum Alloy Die-Casts'] 논문을 기반으로 작성되었습니다.
1. 개요:
- 제목: 알루미늄 합금 다이캐스트의 기계적 성질에 미치는 주조 결함의 영향 (Effects of Casting Defects on Mechanical Properties of Aluminum Alloy Die-Casts)
- 저자: A.K.M. 아지즈 아하메드 (A.K.M. Aziz Ahamed)
- 발행 연도: 2008년 3월
- 발행 학술지/학회: 사이타마 대학교 대학원 이공학연구과 (Graduate School of Science and Engineering, Saitama University)
- 키워드: 논문에 명시되지 않음.
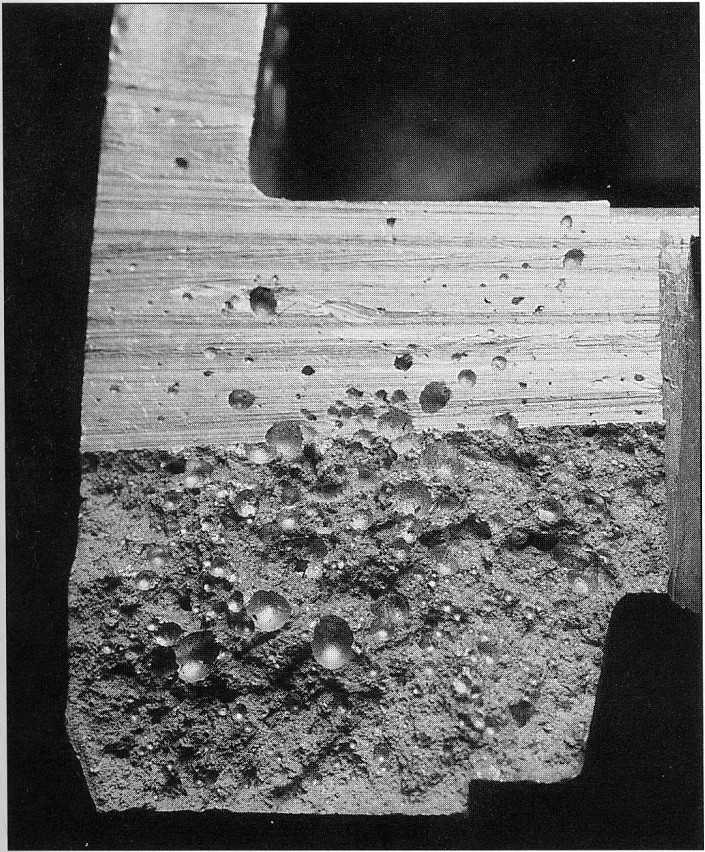
2. 초록 또는 서론
제1장은 다이캐스트 합금의 중요성과 결함, 음향 현미경 기술 개발, 비파괴 평가 및 본 논문의 목적을 소개합니다. 알루미늄 합금은 경량 특성으로 인해 자동차, 항공우주 및 운송 산업에서 인정받는 금속입니다. 고압 다이캐스팅은 최소한의 기계 가공으로 복잡한 형상을 생산하는 비용 효율적인 방법입니다. 자동차 산업은 자동차 변속기 하우징 및 실린더 헤드와 같은 부품 생산에 강력한 지역 알루미늄 다이캐스팅 산업을 활용합니다. 다이캐스팅은 높은 초기 설비 비용에도 불구하고 엄격한 공차와 빠른 생산 속도를 제공하는 고용량 정밀 주조에 가장 효율적인 공정입니다.
자동차 알루미늄 합금 주조의 결함은 제품 품질과 생산 비용에 대한 강조가 증가함에 따라 야금학자와 생산 엔지니어에게 지속적인 과제로 남아 있습니다. 알루미늄 합금 다이캐스트는 자동차 제품에서 반복적인 하중과 열 순환을 겪으며 사용됩니다. 따라서 신뢰성이 중요하며 기계적 성질에 영향을 미치는 요인을 인지하고 보장해야 합니다. 다공성 [1.1-1.7], 수축 공동 [1.8-1.9], 산화물 개재물 [1.10-1.12], 미세 조직 [1.13-1.15] 및 기타 주조 결함 [1.16-1.25]이 다이캐스트의 인장 및 피로 특성에 미치는 영향에 대한 연구가 수행되었습니다.
주조 결함 중 불규칙한 구조인 냉간 박편(cold flake) [1.21-1.25]의 영향에 관심이 집중되었습니다. 냉간 박편은 용융 금속을 샷 슬리브에 붓고 플런저로 밀어 넣을 때 초기 응고된 용융층이 주조 시 작은 조각으로 부서져 생성됩니다. 이러한 작은 조각을 냉간 박편이라고 하며 일반적으로 산화물 층으로 덮여 있습니다. 산화물 층은 종종 윤활제와 기공 [1.26]에 의해 오염되어 모재와의 습윤성을 감소시킵니다. 따라서 다이캐스트 합금의 기계적 성질과 신뢰성은 냉간 박편의 양에 따라 감소합니다 [1.27]. 냉간 박편을 제거하기 위한 많은 연구가 수행되었지만 생산 기술 [1.28]의 발전에도 불구하고 다이캐스트 제품에서 냉간 박편을 완전히 제거하는 데는 성공하지 못했습니다. 비파괴 평가는 주조 제품 [1.29]의 결함을 조사하는 데에도 사용됩니다.
3. 연구 배경:
연구 주제 배경:
알루미늄 합금 다이캐스트는 경량성과 복잡한 형상 생산의 비용 효율성으로 인해 자동차 부품에 널리 사용됩니다. 그러나 주조 결함, 특히 냉간 박편은 자동차 응용 분야에서 반복적인 하중과 열 순환을 받는 이러한 부품의 기계적 성질과 신뢰성에 상당한 영향을 미칩니다.
기존 연구 현황:
기존 연구는 다공성 [1.1-1.7], 수축 공동 [1.8-1.9], 산화물 개재물 [1.10-1.12], 미세 조직 [1.13-1.15] 및 기타 주조 결함 [1.16-1.25]과 같은 다양한 주조 결함과 이들이 다이캐스트의 인장 및 피로 특성에 미치는 영향에 초점을 맞추었습니다. 이러한 결함 중 냉간 박편 [1.21-1.25]은 중요한 결함으로 인식되고 있습니다. 비파괴 평가 방법은 이러한 결함을 감지하는 데 사용되지만 [1.29], 냉간 박편을 완전히 제거하는 것은 여전히 어려운 과제입니다 [1.28].
연구의 필요성:
주조 결함에 대한 수많은 연구에도 불구하고 알루미늄 다이캐스트의 기계적 성질에 미치는 냉간 박편의 영향, 특히 비파괴 검출 및 크기와 위치 평가와 관련된 영향은 추가 연구가 필요합니다. 특히 냉간 박편으로부터의 균열 시작 및 전파와 관련하여 다이캐스트 부품의 신뢰성을 보장하기 위한 효과적인 평가 방법이 필요합니다.
4. 연구 목적 및 연구 질문:
연구 목적:
본 논문의 목적은 주조 결함, 특히 냉간 박편이 알루미늄 합금 다이캐스트의 기계적 성질에 미치는 영향을 평가하는 것입니다. 여기에는 냉간 박편을 감지하고 특성화하기 위한 효과적인 초음파 방법 개발, 인장 및 피로 특성에 미치는 영향 조사, 이러한 결함으로부터의 균열 시작 및 전파 평가가 포함됩니다.
주요 연구 내용:
- 냉간 박편 조사를 통한 초음파 측정에 의한 균열 개방 감지 방법 개발.
- 냉간 박편의 크기와 위치에 따른 ADC12의 인장 특성 측정.
- 냉간 박편의 크기와 위치에 따른 ADC12의 피로 특성 조사.
- 음향 현미경 기술 및 국소 침수 초음파 방법을 이용한 결함 크기 및 위치 평가.
- 음향 현미경 및 초음파 측정을 이용한 냉간 박편으로부터의 균열 시작 관찰.
- 선형 탄성 파괴 역학적 접근법을 이용한 ADC12 합금의 파괴 기준 검토.
- 냉간 박편 영역, 크기, 형상 및 방향에 따른 피로 특성 조사 및 피로 시험 중 냉간 박편으로부터의 균열 시작 및 전파 결정 및 공정 중 초음파 측정을 이용한 불안정한 균열 전파 조사.
연구 가설:
논문에서 연구 가설이 명시적으로 언급되지는 않았습니다.
5. 연구 방법론
연구 설계:
본 연구에서는 다음과 같은 실험 설계를 채택했습니다.
- 초음파 시험 및 음향 현미경(SAM): 알루미늄 합금 다이캐스트 판재(ADC12)에서 냉간 박편을 감지하고 시각화합니다.
- 인장 시험: ADC12 합금의 인장 강도에 미치는 냉간 박편의 영향을 평가합니다.
- 굽힘 시험: 굽힘 조건에서 냉간 박편으로부터의 균열 시작 및 전파를 관찰합니다.
- 피로 시험: ADC12 합금의 피로 특성에 미치는 냉간 박편의 영향을 조사합니다.
- 공정 중 초음파 측정: 인장 및 피로 시험 중 냉간 박편으로부터의 균열 개방 및 전파를 모니터링합니다.
자료 수집 방법:
- 음향 현미경(SAM): 다이캐스트 판재 내부의 냉간 박편의 고해상도 이미지를 얻는 데 사용되었습니다. 이미지 획득 조건은 Gain- 60 dB, gate- 0.075 μm, F Trig- 50 %로 설정되었습니다.
- 초음파 측정: 20 MHz의 종파를 생성하는 트랜스듀서를 사용하여 냉간 박편 및 균열 전파를 감지하고 모니터링했습니다.
- 인장 시험: 인장 강도를 측정하기 위해 크로스헤드 속도 0.5 mm/min의 시험기를 사용하여 수행되었습니다. 파단 하중(Pf)과 초기 단면적(A0)을 기록했습니다.
- 피로 시험: S-N 곡선 및 피로 수명 데이터를 얻기 위해 응력비 R= 0.05(인장-인장 유형) 및 주파수 10 MHz에서 수행되었습니다.
- 파면 분석: 파단면을 광학 및 주사 전자 현미경(SEM)을 사용하여 관찰하여 균열 시작 위치 및 전파 경로를 분석했습니다.
분석 방법:
- 음향 이미지 분석: AVS 소프트웨어를 사용하여 3차원 냉간 박편 시각화를 위해 간격 음향 이미지를 결합했습니다.
- 응력 강도 계수 분석: 선형 탄성 파괴 역학적 접근법을 사용하여 Murakami et al. [3.12,3.13], Newman et al. [3.14,3.15] 및 Ishida et al. [3.16]의 방정식을 사용하여 파괴 시 임계 응력 강도 계수(Kc)를 평가했습니다.
- S-N 곡선 분석: 피로 시험 데이터를 사용하여 냉간 박편이 있는 ADC12 합금의 피로 수명을 평가하기 위해 S-N 곡선을 생성했습니다.
- 파면 분석: SEM 파단면 이미지를 분석하여 냉간 박편과 관련된 균열 시작점 및 전파 메커니즘을 식별했습니다.
연구 대상 및 범위:
- 재료: 알루미늄 합금 다이캐스트 판재 (ADC12, 공칭 조성 Al-11 mass% Si-2.5 mass% Cu).
- 결함: 냉간 박편, 크기, 위치(내재형, 노출형) 및 하중 방향에 대한 방향으로 특징지어짐.
- 시편: 인장, 굽힘 및 피로 시험을 위해 제어된 냉간 박편 크기 및 위치로 다이캐스트 판재에서 가공된 직사각형 시편.
- 범위: ADC12 합금의 인장 강도, 피로 수명 및 균열 전파에 미치는 냉간 박편 영향 조사. 냉간 박편의 비파괴 평가를 위한 초음파 및 음향 현미경 기술 개발 및 적용.
6. 주요 연구 결과:
주요 연구 결과:
- 균열 개방의 초음파 감지: 냉간 박편으로부터의 균열 개방을 감지하기 위해 워터백을 이용한 국소 침수 초음파 방법을 개발했습니다. 음향 현미경(SAM)은 냉간 박편을 밝은 부분으로 효과적으로 시각화했습니다. 인장 시험 중 공정 중 초음파 측정은 냉간 박편으로부터 반사된 파형의 위상 변화를 보여주어 균열 시작 및 전파를 나타냅니다.
- 주조 결함이 인장 강도에 미치는 영향: ADC12 합금의 인장 강도는 냉간 박편의 산화물 층 면적이 증가함에 따라 선형적으로 감소했습니다. 인장 방향에 수직인 노출된 냉간 박편은 내재형 냉간 박편에 비해 인장 강도를 현저히 감소시켰습니다. 인장 방향과 평행한 산화물 층은 최소한의 영향을 미쳤습니다. 임계 응력 강도 계수(Kc*)를 평가하여 산화물 층 면적에 대한 의존성을 보여주었습니다.
- 냉간 박편이 피로 특성에 미치는 영향: ADC12 합금의 피로 수명은 냉간 박편에 의해 크게 영향을 받았으며, 냉간 박편 크기와 위치의 차이로 인해 S-N 곡선에서 큰 분산을 보였습니다. 피로 수명은 냉간 박편 면적이 증가함에 따라 감소했습니다. 하중 방향에 수직인 노출된 냉간 박편은 내재형 냉간 박편보다 피로 수명에 더 해로웠습니다. 공정 중 초음파 측정은 피로 과정 중 냉간 박편의 분리를 확인하여 균열 형성을 유발했습니다. 피로 균열 크기로부터 평가된 최대 응력 강도 계수(KImax)는 인장 시험 결과와 일치했습니다.
제시된 데이터 분석:
- 인장 강도 감소: 냉간 박편, 특히 노출된 박편의 존재는 응력 집중부 역할을 하여 조기 파괴 및 인장 강도 감소를 유발합니다. 냉간 박편을 둘러싼 산화물 층의 크기는 인장 강도 감소 정도와 직접적인 상관 관계가 있습니다.
- 균열 시작 및 전파: 냉간 박편, 특히 산화물 층이 있는 냉간 박편은 인장 및 피로 하중 모두에서 균열 시작의 우선적인 위치 역할을 합니다. 초음파 측정은 이러한 결함으로부터의 균열 개방 및 전파를 효과적으로 추적했습니다.
- 피로 수명 저하: 냉간 박편은 피로 수명을 크게 단축시킵니다. S-N 곡선은 큰 분산을 나타내며, 이는 결함 특성의 가변성과 피로 성능에 미치는 영향을 강조합니다. 노출된 냉간 박편 구성은 내재형 냉간 박편보다 피로에 더 중요합니다.
- 파괴 역학 분석: 선형 탄성 파괴 역학은 응력 강도 계수 접근법을 사용하여 응력-변형률 곡선에서 관찰된 일부 비선형성에도 불구하고 냉간 박편을 포함하는 다이캐스트의 파괴 거동을 특성화하기 위한 합리적인 프레임워크를 제공합니다.
그림 목록:
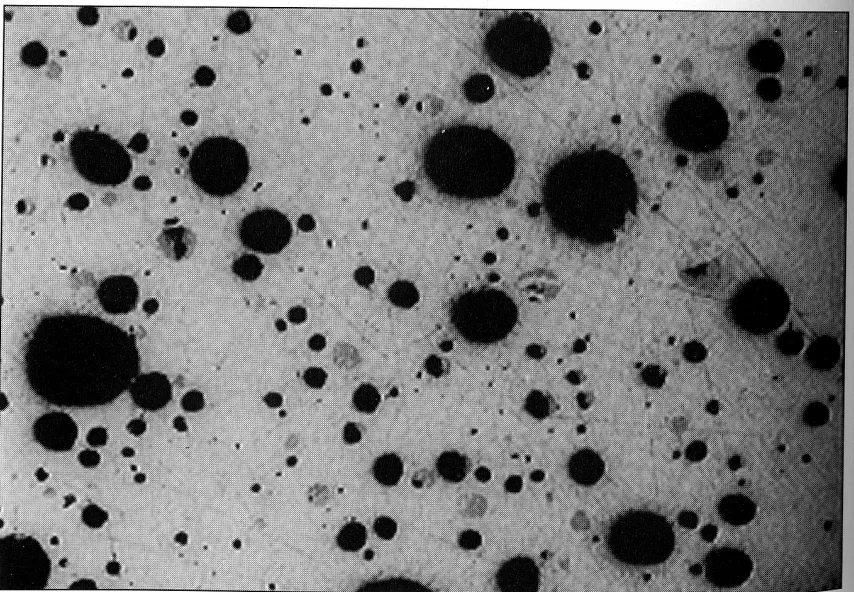
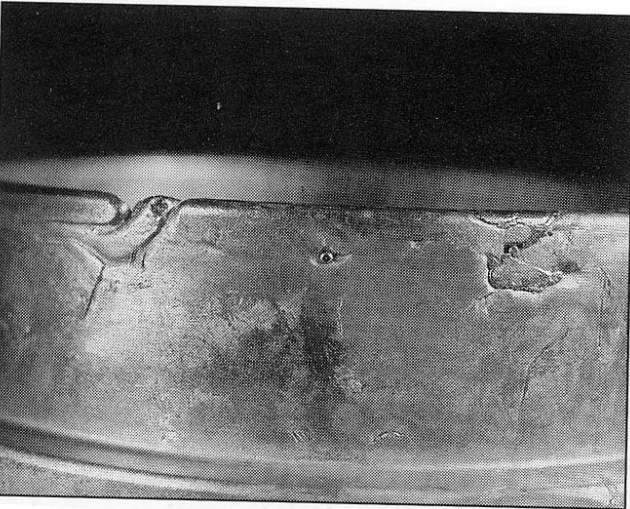
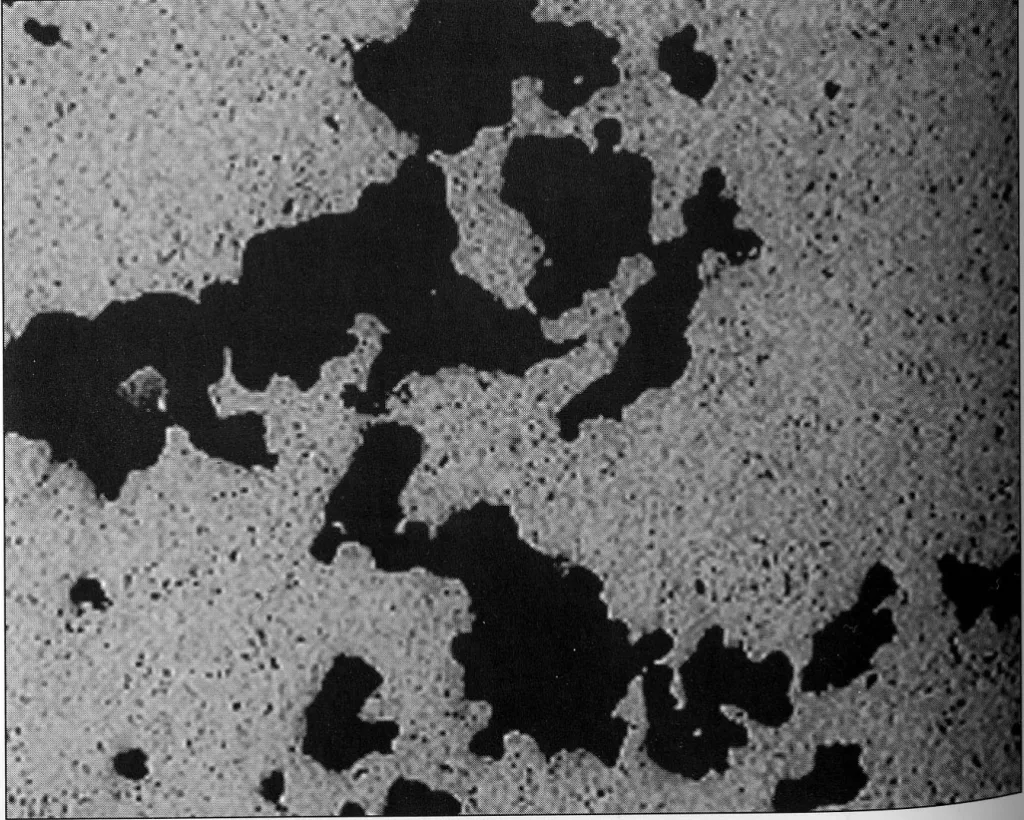
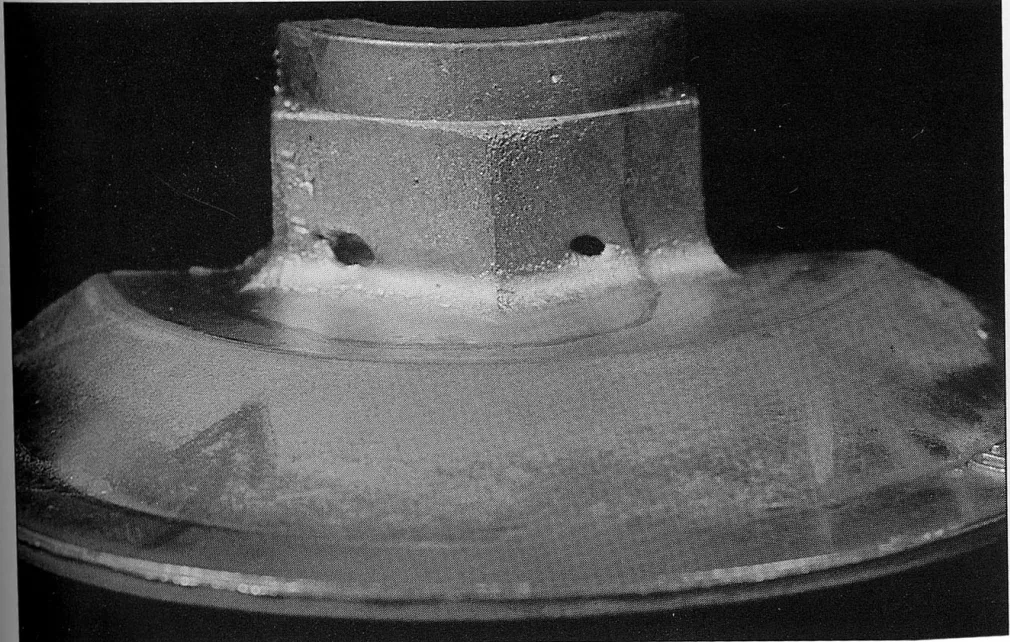
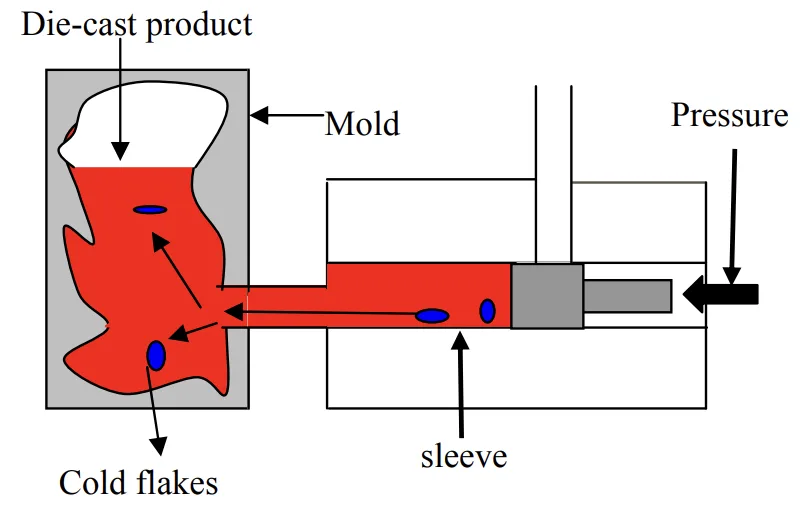
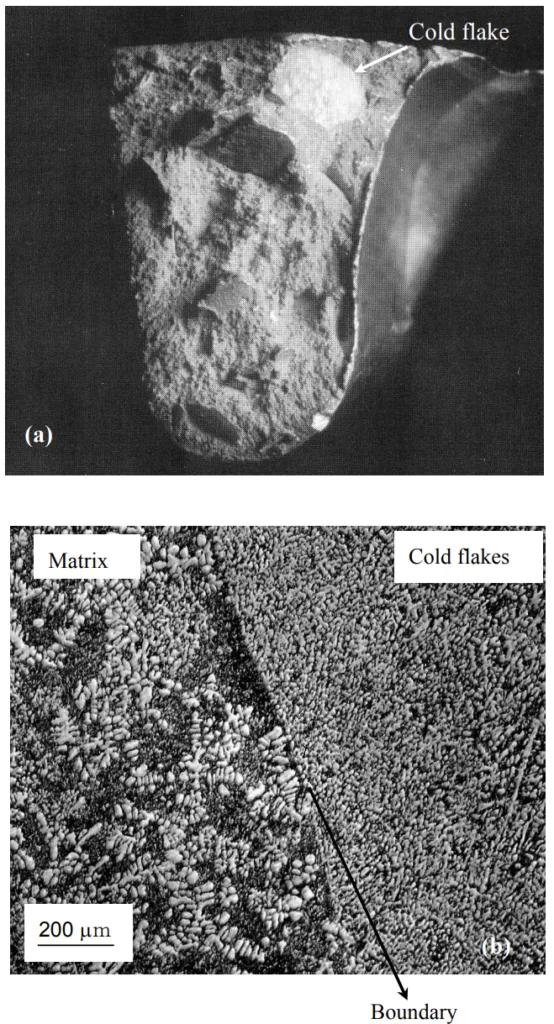
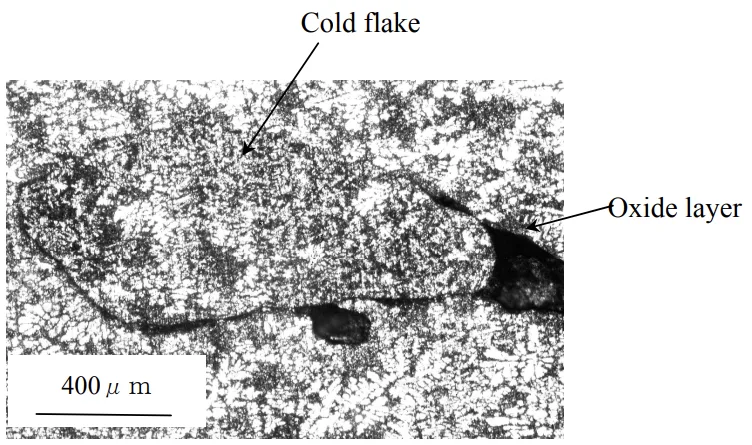

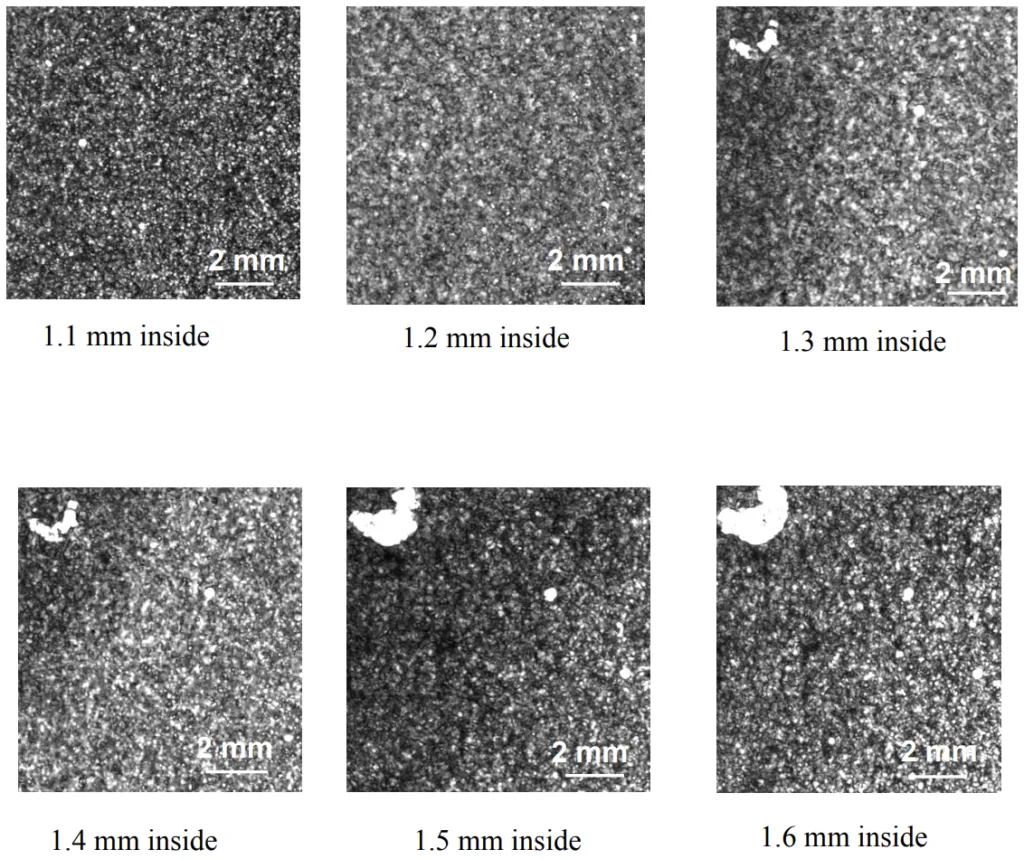
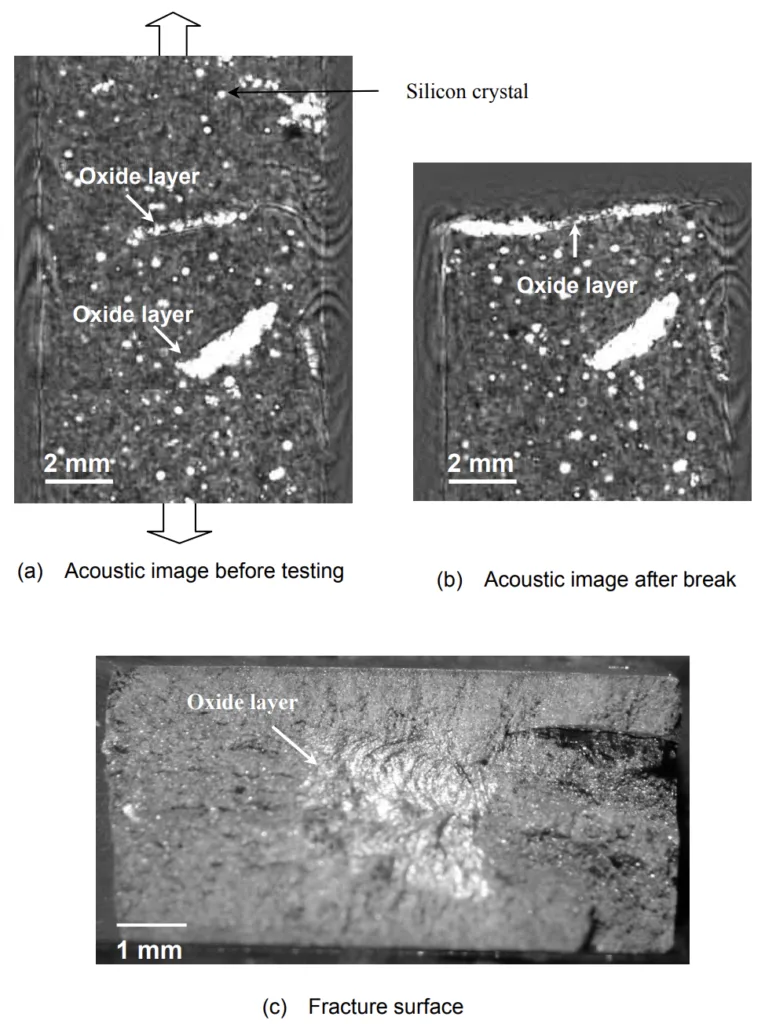
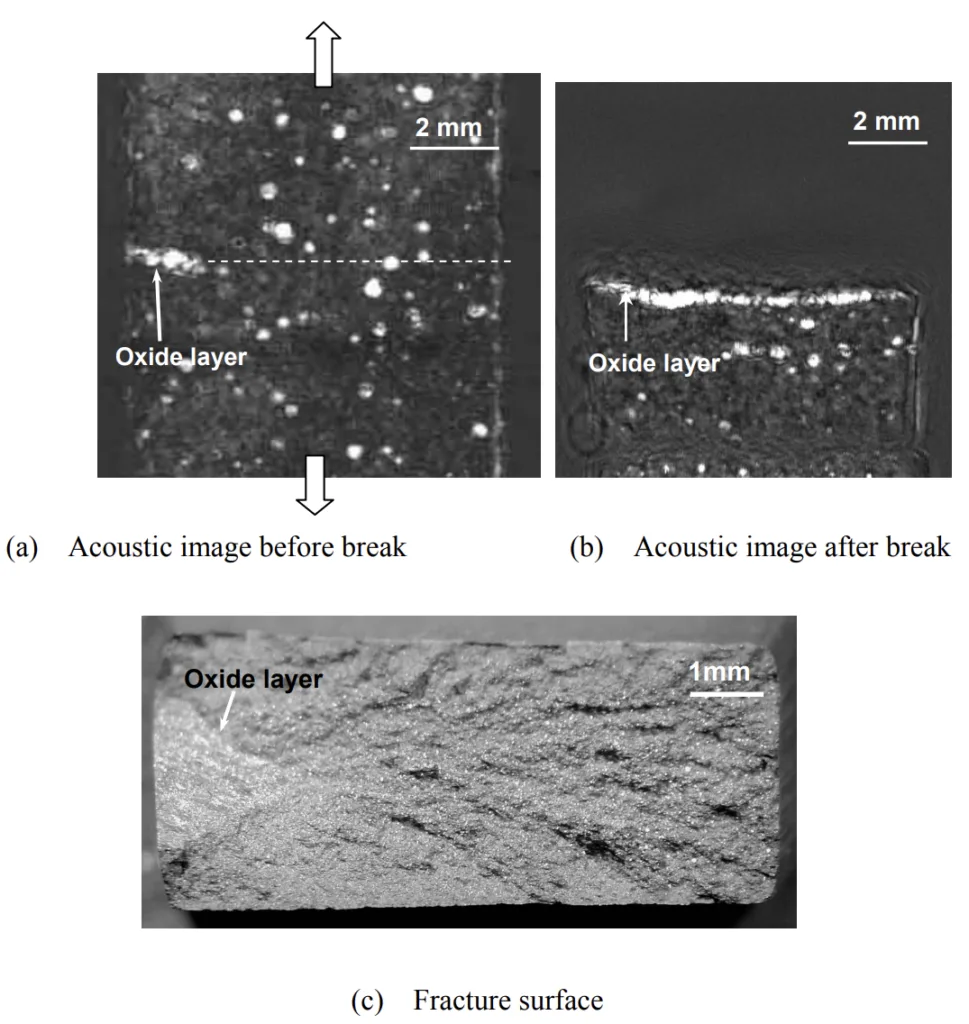
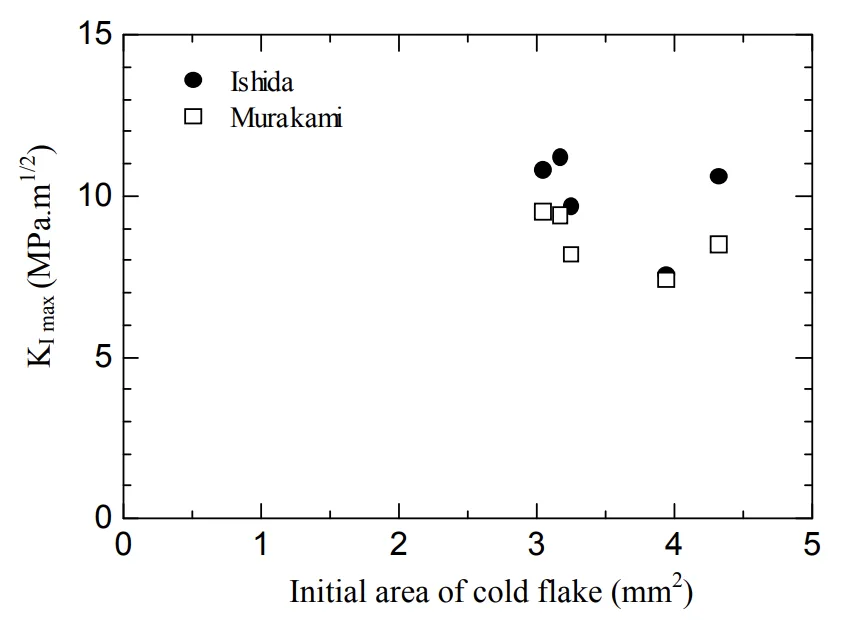
- Fig. 1.1 압력에 의해 평탄화된 기포가 있는 가스 기공.
- Fig. 1.2 주조 시 둥근 가스 기공의 현미경 사진.
- Fig. 1.3 냉간 유동 표면 결함의 일반적인 예
- Fig. 1.4 수축 기공의 일반적인 외관을 보여줍니다.
- Fig. 1.5 표면까지 확장되는 일반적인 유동 기공.
- Fig. 1.6 기계적 균열
- Fig. 1.7 일반적인 블리스터
- Fig. 1.8 포트 상단에서 나온 더 부드러운 산화물 찌꺼기
- Fig. 1.9 국자 딥 아웃 웰에서 드로스가 포함된 주조
- Fig. 1.10 다이캐스팅 기계 (a) 기존 다이캐스트 기계, (b) 슬리브 및 압력 시스템의 확장된 뷰
- Fig. 1.11 제품에 냉간 박편을 보여주는 다이캐스트 기계의 슬리브 및 압력 시스템.
- Fig. 1. 12 일반적인 냉간 박편 (a) 시편의 냉간 박편 (b) 얇은 산화물 경계로 분리된 냉간 박편 및 모재
- Fig. 1.13 산화물 층을 갖는 일반적인 냉간 박편
- Fig. 1.14 음향 측정 (a) 음향 현미경, (b) 스캐너 (c) 물 속의 시편 및 프로브 거리, (d) 여러 세그먼트가 있는 전체 이미지 영역
- Fig. 1.15 주사 음향 현미경에 의한 C-스캔 측정 시스템의 개략도.
- Fig. 1.16 표면파 및 게이트 위치.
- Fig.2.1 시편 준비. (a) 인장 시편 선택을 위한 다이캐스트 판재. (b) 다이캐스트 판재 표면 아래 2mm에서의 음향 이미지. 밝은 부분이 냉간 박편입니다.
- Fig. 2.2 인장 시험용 시편의 형상 및 크기.
- Fig.2.3 선택된 냉간 박편을 갖는 굽힘 시험용 시편.
- Fig. 2.4 단조 하중을 가하여 이 장치로 음향 이미지를 촬영했습니다.
- Fig. 2.5 인장 시험용 실험 설정.
- Fig.2.6 초음파 측정을 위한 실험 설정
- Fig. 2.7 국소 침수 방법의 개략적 표현.
- Fig. 2.8 인장 시험 중 공정 중 초음파 측정을 위한 설정.
- Fig. 2.9 인장 시험 중 공정 중 초음파 측정을 위한 개략도.
- Fig.2.10 표면으로부터의 깊이가 다른 음향 이미지
- Fig. 2.11 AVS 소프트웨어로 2.9에서 가져온 이미지를 사용한 3차원 이미지.
- Fig.2.12 냉간 박편으로부터의 균열 시작을 보여주는 음향 이미지.
- Fig.2.13 냉간 박편으로부터의 균열 시작을 보여주는 음향 이미지.
- Fig. 2.14 인장 시험 전 시편의 음향 이미지.
- Fig. 2.15 침수법에 의한 인장 시험 전 Fig. 4의 냉간 박편의 산화물 층에서 반사된 초음파(RCF). S와 B는 각각 시편 표면과 바닥에서 반사된 에코입니다. (a) 표준 스케일 (b) 세로축 확대 스케일.
- Fig. 2.16 시편 표면, 바닥 및 냉간 박편에서 반사된 에코의 개략도.
- Fig. 2.17 냉간 박편과 모재 사이의 일반적인 경계.
- Fig. 2.18 인장 시험에서 얻은 두 가지 일반적인 곡선 (a) 기계 정지 없이, (b) 여러 단계에서 기계 정지.
- Fig. 2.19 조대한 냉간 박편을 포함하는 시편의 파단면.
- Fig. 2.20 인장 시험 중 냉간 박편의 산화물 층에서 반사된 에코의 변화.
- Fig. 2.21 냉간 박편의 산화물 층에서 반사된 초음파(RCF)의 일반적인 변화. S와 B는 표면과 바닥에서 반사된 에코를 보여줍니다.
- Fig. 2.22 인장 시험용 시편의 음향 이미지
- Fig. 2.23 Fig. 2.22의 표적 냉간 박편의 파단면
- Fig.2.24 워터백 방법으로 얻은 소형 냉간 박편으로부터의 파형 변화.
- Fig.2.25 소형 냉간 박편을 포함하는 시편의 파단면.
- Fig. 3.1 다이캐스트 판재의 음향 이미지 실험 설정 (a) 음향 현미경 (b) 이미지 선택 영역
- Fig. 3.2 인장 시편 준비를 위한 다이캐스트 판재의 음향 이미지. 밝은 부분과 점은 냉간 박편의 산화물 층을 나타내고 미세한 점은 모재의 실리콘 결정입니다.
- Fig. 3.3 인장 시험용 시편의 형상 및 치수.
- Fig. 3.4 인장 시험용 실험 설정.
- Fig. 3.5 냉간 박편 유무에 따른 시편의 일반적인 응력-변형률 곡선.
- Fig. 3.6 인장 방향에 수직으로 향하는 내재형 냉간 박편의 산화물 층을 갖는 시편의 음향 이미지와 파단면 비교.
- Fig. 3.7 내재형 냉간 박편에서 방사형 능선을 보여주는 파단면
- Fig. 3.8 표면에 노출되도록 배열된 냉간 박편의 산화물 층의 음향 이미지와 파단면 비교.
- Fig. 3.9 냉간 박편의 산화물 층 면적에 따른 공칭 인장 강도 변화.
- Fig. 3.10 냉간 박편의 산화물 층 면적에 따른 공칭 인장 강도 변화.
- Fig. 3.11 냉간 박편의 산화물 층 면적에 따른 유효 인장 강도 변화.
- Fig. 3.12 표면으로부터의 냉간 박편의 산화물 층 거리와 유효 인장 강도 관계.
- Fig. 3.13 노출된 길이가 다른 냉간 박편의 산화물 층을 갖는 시편의 파단면 비교.
- Fig. 3.14 냉간 박편의 노출된 표면 길이와 유효 인장 강도 관계.
- Fig. 3.15 Murakami(32) 및 Ishida(36) 방정식으로 계산한 내재형 냉간 박편을 갖는 시편의 겉보기 임계 응력 강도 계수 Kc* 비교.
- Fig. 3.16 Murakami(32) 및 Newman(34) 방정식으로 계산한 노출형 냉간 박편을 갖는 시편의 겉보기 임계 응력 강도 계수 Kc* 비교.
- Fig. 3.17 Murakami 방정식(32, 33)으로 계산한 내재형 및 노출형 냉간 박편을 갖는 시편의 겉보기 응력 강도 계수 Kc* 비교.
7. 결론:
주요 연구 결과 요약:
본 연구에서는 냉간 박편이 알루미늄 합금 다이캐스트(ADC12)의 기계적 성질에 상당한 영향을 미친다는 결론을 내렸습니다. 인장 강도는 냉간 박편과 관련된 산화물 층 면적이 증가함에 따라 선형적으로 감소합니다. 특히 인장 방향에 수직으로 배향된 노출된 냉간 박편은 내재형 냉간 박편에 비해 균열 시작에 더 취약하고 인장 강도 및 피로 수명을 더 크게 감소시킵니다. 공정 중 초음파 측정은 인장 및 피로 시험 모두에서 냉간 박편으로부터의 균열 시작 및 전파를 효과적으로 감지합니다. 선형 파괴 역학을 사용하여 평가된 임계 응력 강도 계수는 파괴 특성의 척도를 제공하며 냉간 박편의 크기와 위치에 영향을 받습니다. 피로 수명도 냉간 박편의 존재로 인해 감소하며, 노출된 박편이 더 심각한 영향을 미칩니다.
연구의 학문적 의의:
본 연구는 일반적인 주조 결함인 냉간 박편이 알루미늄 합금 다이캐스트의 기계적 거동에 미치는 영향에 대한 기본적인 이해에 기여합니다. 비파괴 초음파 기술과 음향 현미경이 이러한 결함을 감지하고 특성화하는 데 효과적임을 입증합니다. 본 연구는 냉간 박편 특성(크기, 위치)과 기계적 성질(인장 강도, 피로 수명) 간의 관계에 대한 정량적 데이터를 제공하며, 이는 재료 과학 및 다이캐스팅 엔지니어링에 유용합니다.
실제적 의미:
본 연구 결과는 다이캐스팅 산업에 실제적인 의미를 가지며, 부품 신뢰성을 향상시키기 위해 다이캐스팅 공정 중 냉간 박편 형성을 최소화하는 것의 중요성을 강조합니다. 개발된 초음파 측정 방법은 다이캐스트 부품의 품질 관리 및 비파괴 평가를 위한 귀중한 도구를 제공하여 냉간 박편과 같은 중요한 결함을 감지하고 기계적 성능에 미치는 영향을 예측할 수 있도록 합니다. 이는 공정 제어 개선, 불량률 감소 및 자동차 및 기타 응용 분야에서 알루미늄 다이캐스트 부품의 신뢰성 향상으로 이어질 수 있습니다.
연구의 한계 및 향후 연구 분야:
본 연구에서는 특히 작은 냉간 박편을 갖는 시편의 경우 응력-변형률 곡선의 비선형성과 관련된 한계를 인정하며, 이는 임계 응력 강도 계수의 과소 평가로 이어질 수 있습니다. 향후 연구에서는 보다 포괄적인 분석을 위해 J-적분과 같은 비선형 파괴 역학적 접근법을 탐구할 수 있습니다. 또한 향후 연구에서는 냉간 박편 형상 및 방향의 영향을 보다 자세히 조사하고, 다이캐스팅 중 냉간 박편 형성을 완화하는 방법을 탐구하고, 조사를 다른 알루미늄 합금 및 다이캐스팅 공정으로 확장할 수 있습니다. 피로 균열 진행은 초음파 측정으로 확인되지 않았으며, 이는 향후 연구에서 개선할 수 있는 영역입니다.
8. 참고 문헌:
- [1.1] RL Edwards. CR Manning. JK Magor. Effects of porosity on Strength of Aluminum Die-castings. Foundry Management & Technology, 1981; 109(7): 84-91.
- [1.2] JA Eady. DM Smith. The effect of porosity on the Tensile Properties of Aluminum Casting. Materials Forum, 1986; 9(4): 217-223.
- [1.3] M Okayasu. K Kanazawa and N Nishi. Effects of Porosity and Microstructures on Tensile properties of Slow Filling Rate Die Castings. J. JFS 1999; 71: 301-306. (in Japanese)
- [1.4] H Mayer. M Papakyriacou. B Zettl. SE Stanzl-Tschegg. Influence of porosity on the fatigue limit of die cast magnesium and aluminium alloys. Int. J. Fatigue 2003; 25: 245-256.
- [1.5] JZ Yi. YX Gao. PD Lee. HM Flower and TC Lindley. Scatter in fatigue life due to effects of porocity in cast A356-T6 aluminum–silicon alloys. Metallurgical and Materials Transactions A 2003; 34A (9): 1879-1890.
- [1.6] J Linder. M Axelsson. H Nilsson. The influence of porocity on the fatigue life for sand and permanent mould cast aluminum. Int J of Fatigue 2006; 28(12): 1752-1758.
- [1.7] J Linder. A Arvidsson. J Kron. The influence of porosity on the fatigue strength of high-pressure die cast aluminum. Fatigue and Fracture of Engng Mat and Structures 2006; 29 (5): 357-363.
- [1.8] MJ Couper. AE Neeson. JR Griffiths. Casting defects and the fatigue behaviour of an aluminum casting alloy. Fatigue & Fracture of Engng Materials & Structure 1990; 13(3): 213-227
- [1.9] B. Skallerud. T Iveland. G Härkegård. Fatigue life assessment of aluminum-alloys with casting defects. Engng Fracture Mech 1993; 44(6): 857-874
- [1.10] X Cao. J Campbell. Oxide inclusion defects in Al-Si-Mg cast alloys. Canadian Metallurgical Quarterly. 2005; 44 (4): 435-447
- [1.11] X Dai. X Yang. J Campbell. J Wood. Influence of oxide film defects generated in filling on mechanical strength of aluminum alloy castings. Materials Science and Technology, 2004; 20(4): 505-513
- [1.12] X Cao. J Campbell. The solidification characteristics of Fe-Rich Intermetallics in Al-11.5Si-0.4Mg Cast Alloys. Metallurgical and Materials Transactions A, 2004; 35A(5):1425-1435
- [1.13] N Nishi. T Komazaki. Y Takahashi. Formation Mechanisms of Aluminum Die Castings Microstructures. IMONO 1991; 63(4): 347-352. (in Japanese)
- [1.14] T Komazaki. K. Matsuura. N Nishi. Influence of Microstructures on Mechanical Properties of ADC 10 Alloy Die Castings. IMONO 1993; 65(3): 191-196. (in Japanese)
- [1.15] JZ Yi. YX Gao. PD Lee. TC Lindley. Microstructure-based fatigue life prediction for cast A356-T6 aluminum–silicon alloys. Metallurgical and Maerials Transactions B 2006; 37 (2): 301-311
- [1.16 ] A Herrera. V Kondic. The effect of artificial flaws on the tensile properties of Al-Si12 alloy. Brit. Foundryman. 1984; 77(1): 31-34,
- [1.17] K Shiozawa. Y Tohda. SM Sun. Crack initiation and small fatigue crack growth behaviour of squeeze-cast Al-Si aluminum alloys. Fatigue & Fracture of Engng Mat and Structures 1997; 20 (2): 237-247
- [1.18] M Avalle. G Belingardi. MP Cavatorta. R Doglione. Casting defects and fatigue strength of a die cast aluminum alloy: a comparison between standard specimens and production components. Int. J. Fatigue 2002; 24: 1-9
- [1.19] YX Gao. JZ Yi. PD Lee. TC Lindley. A micro-cell model of the effect of microstructure and defects on fatigue resistance in cast aluminum alloys. Acta Materialia 2004; 52 (19): 5435-5449
- [1.20] A Shyam. JE Allison. JW Jones. A small fatigue crack growth relationship and its application to cast aluminum. Acta Materialia 2005; 53: 1499-1509
- [1.21] T Komazaki. Y Maruyama. N Nishi. Effects of Silicon Contents on Formation of Abnormal Structures of Aluminum Alloy Die Castings. IMONO 1995; 67: 258-264. (in Japanese)
- [1.22] H Iwahori. K Tozawa. Y Yamamoto. M Nakamura. Formation of scattered structures in aluminum alloy die-castings. J. Japan Inst. Light Metals 1984; 34: 389-394. (in Japanese)
- [1.23] H Nomura. E Kato. Y Maeda. S Okubo. Melt Cooling and Formation of Solidification Phase in Die Casting Sleeve. J. JFS 2001; 73(10): 656-661. (in Japanese)
- [1.24] H Iwahori. K Tozawa. Y Yamamoto. M Nakamura. Properties of scattered struecures included in aluminum die castings. J. Japan Inst. Light Metals 1984; 34 (9) 389-394. (in Japanese)
- [1.25] M Okayasu. K Kanazawa. N Nishi. Effects of Internal Defects on Tensile Properties of ADC10 Die Castings. J. JFS 1998; 70(11): 779-785. (in Japanese)
- [1.26] C H Caceres.B I Selling. Casting defects and the tensile properties of an Al-Si-Mg alloy. Materials Science and Engg A 1996; 220: 109-116
- [1.27] R Kimura. M Yoshida. G Sasaki. J Pan. H. Fukunaga. Influence of abnormal structure on the reliability of squeeze castings. Journal of Materials Processing Technology 2002; 130-131: 299-303
- [1.28] William G. Walkington. Causes and solutions die-casting defects, North American Die-casting Association Publication, p 155-158, 1997
- [1.29] H Kato. T Suzuki. Y Annou. K Kageyama. Nondestructive detection of Cold Flakes in Aluminum Alloy Die-Cast Plate with Ultrasonic Measurement. Mater. Trans. 2004; 45 (7): 2403-2409.
- [1.30] J. Krautkramer and H. Krautkramer,” Ultrasonic Testing of Material, 4th edition, Springer Verlag, pp 13-14, New York, 1990
- [2.1] H. Iwahori, K. Tozawa, Y. Yamamoto and M. Nakamura : “ Formation of scattered structures in aluminum alloy die-castings”. J. Japan Inst. Light Metals 34 (1984) 389
- [2.2] N. Nishi, T. Komazaki and Y. Takahashi : “Formation mechanism of aluminum die-castings Microstructures” IMONO 63 (1991) 347
- [2.3] T. Komazaki, Y. Maruyama and N. Nishi : “ Effect of Silicon contents on formation of abnormal structures of aluminum alloy die-castings”. IMONO 67 (1995) 258
- [2.4] X Cao. J Campbell. Oxide inclusion defects in Al-Si-Mg cast alloys. Canadian Metallurgical Quarterly. 2005; 44 (4): 435-447
- [2.5] X Dai. X Yang. J Campbell. J Wood. Influence of oxide film defects generated in filling on mechanical strength of aluminum alloy castings. Materials Science and Technology, 2004; 20(4): 505-513
- [2.6] K. Konagaya, S. Aoyama, M. Tachikawa and K. Kanazawa : ”Effect of casting defects on fatigue life of aluminum alloy die-castings”. Japan Die Castings Cong. (1998) 171
- [2.7] M. Okayasu, K. Kanazawa and N. Nishi : “ Effects of internal defects on tensile properties of ADC 10 die-castings” J. JFS 70 (1998) 779
- [2.8] T. Komazaki, K. Matsuura and N. Nishi: “Influence of Microstructures on mechanical properties of ADC10 alloy die-castings” IMONO 65 (1993) 191
- [2.9] H. Iwahori, K. Tozawa, T. Asano,Y. Yamamoto, M. Nakamura, M. Hashimoto and S. Uenishi : J. Japan Inst. Light Metals 34 (1984) 525
- [2.10] Naomi Nishi : Material processing technical seminar ( Japan Material
- [2.11] William G. Walkington. Causes and solutions die-casting defects, North American Die-casting Association Publication, p 155-158, 1997
- [2.12] H. Kato, T. Suzuki, Y. Annou and K. Kageyama : “Nondestructive detection of Cold Flakes in Aluminum Alloy Die-Cast Plate with Ultrasonic Measurement”Mater. Trans. 45 (2004) 2403
- [2.13] J. Krautkrämer and H. Krautkrämer: Ultrasonic Testing of Materials, 4th ed. (Springer-Verlag) (1990) 16
- [2.14] X Cao. J Campbell. Oxide inclusion defects in Al-Si-Mg cast alloys. Canadian Metallurgical Quarterly. 2005; 44 (4): 435-447
- [3.1] X Cao. J Campbell. Oxide inclusion defects in Al-Si-Mg cast alloys. Canadian Metallurgical Quarterly. 2005; 44 (4): 435-447
- [3.2] X Dai. X Yang. J Campbell. J Wood. Influence of oxide film defects generated in filling on mechanical strength of aluminum alloy castings. Materials Science and Technology, 2004; 20(4): 505-513
- [3.3] X Cao. J Campbell. The solidification characteristics of Fe-Rich Intermetallics in Al-11.5Si-0.4Mg Cast Alloys. Metallurgical and Materials Transactions A, 2004; 35A(5):1425-1435
- [3.4] T Komazaki. Y Maruyama. N Nishi. Effects of Silicon Contents on Formation of Abnormal Structures of Aluminum Alloy Die Castings. IMONO 1995; 67: 258-264. (in Japanese)
- [3.5] H Iwahori. K Tozawa. Y Yamamoto. M Nakamura. Formation of scattered structures in aluminum alloy die-castings. J. Japan Inst. Light Metals 1984; 34: 389-394. (in Japanese)
- [3.6] H Nomura. E Kato. Y Maeda. S Okubo. Melt Cooling and Formation of Solidification Phase in Die Casting Sleeve. J. JFS 2001; 73(10): 656-661. (in Japanese)
- [3.7] H Iwahori. K Tozawa. Y Yamamoto. M Nakamura. Properties of scattered struecures included in aluminum die castings. J. Japan Inst. Light Metals 1984; 34 (9) 389-394. (in Japanese)
- [3.8] M Okayasu. K Kanazawa. N Nishi. Effects of Internal Defects on Tensile Properties of ADC10 Die Castings. J. JFS 1998; 70(11): 779-785. (in Japanese)
- [3.9] William G. Walkington. Causes and solutions die-casting defects, North American Die-casting Association Publication, p 155-158, 1997
- [3.10] H Kato. T Suzuki. Y Annou. K Kageyama. Nondestructive detection of Cold Flakes in Aluminum Alloy Die-Cast Plate with Ultrasonic Measurement. Mater. Trans. 2004; 45 (7): 2403-2409.
- [3.11] AKMA Ahamed. H Kato. K Kageyama. T Komazaki. Acoustic Visualization of Cold Flakes and Crack propagation in Aluminum Alloy Die-Cast Plate. Materials Science and Eng A 2006; 423: 313-323.
- [3.12] Y Murakami. H Usuki. Prediction of fatigue strength of high strength steels based on statistical evaluation of inclusion size. Japan Mech. Eng. Soc. 1989; 55 (510): 213-221. (in Japanese)
- [3.13] Y Murakami. Analysis of stress intensity factors of models Ι ΙΙ and ΙΙΙ for inclined surface cracks of arbitrary shape. Engng Fracture Mech. 1985; 22: 101-114.
- [3.14] JC Newman. Jr. IS Raju. An empirical Stress intensity factor equation for the surface crack. Eng. Frac. Mech. 1981; 15(1-2): 185-192.
- [3.15] Y Murakami. Stress Intensity Factor Handbook. Pergamon Press, oxford, 1987
- [3.16] M Ishida. H Noguchi. Tension of a plate containing an embedded elliptical crack. Eng. Frac. Mech. 1984; 20(3): 387-408.
- [3.17] TL Anderson. Fracture Mechanics fundamentals and applications. CRC press, 1995, p.117 p. 142 p. 541
- [3.18] K Kanazawa. K Chijiiwa. H Kubota. K Nakamura. Fracture toughness of Aluminum Alloy Die-Castings. Japan Die-Casting Association 1994; JD94-20: 170-177. (in Japanese)
- [3.19] JM McNaney. RM Cannon. RO Ritchie. Fracture and fatigue-crack growth along aluminum-alumina interfaces. Acta mater. 1996; 44(12): 4713-4728
- [4.1] K. Konagaya, S. Aoyama, M. Tachikawa, K. Kanazawa “ Effect of casting defects on fatigue life of aluminum alloy die-casting” Japan Die Cast Cong., JD98-27, pp 171-179
- [4.2] Y. Ninomiya, K. Kanazawa, K. Konagaya, S. Aoyama, H. Hirokawa, E. Soichi, “ Analytical prediction of fatigue life on aluminum alloy die-castings for high performance parts” Japan Die Cast Cong. JD04-30, pp. 175-180
- [4.3] K. Kanazawa, K. Chijiwa, T. Fukita,” Influence of casting method on properties of fatigue fracture in aluminum alloy die castings” Japan Die Cast Cong. JD92-20
- [4.4] Y. Murakami and H. Usuki: Trans. Japan Mech. Eng. Soc., 1989, 55, 213-221. (in Japanese)
- [4.5] M. Ishida and H. Noguchi: Eng. Frac. Mech., 1984, 20, 387-408.
- [4.6] K. Kanazawa, K. Chijiiwa, H. Kubota and K. Nakamura: Trans. 1994 Japan Die Cast. Cong., Dec. 1994, Japan Die Casting Association, 170-177. (In Japanese)
9. 저작권:
- 본 자료는 "[A.K.M. Aziz Ahamed]"의 논문: "[Effects of Casting Defects on Mechanical Properties of Aluminum Alloy Die-Casts]"를 기반으로 합니다.
- 논문 출처: (DOI URL은 논문에 없음)
본 자료는 상기 논문을 요약한 것으로, 상업적 목적으로 무단 사용하는 것을 금지합니다.
Copyright © 2025 CASTMAN. All rights reserved.