주조 공정의 혁신: 700°C 알루미늄 용탕에 반도체 소자를 직접 삽입하는 기술
이 기술 브리프는 A. Ibragimov 외 저자들이 1st Joint International Symposium on System-Integrated Intelligence 2012: New Challenges for Product and Production Engineering (2012)에 발표한 논문 "[Micromachined Thermogenerator Directly Integrated into Metal Parts: Technological Aspects of the Embedding Process]"를 기반으로 하며, HPDC 전문가를 위해 CASTMAN의 전문가들이 요약 및 분석하였습니다.
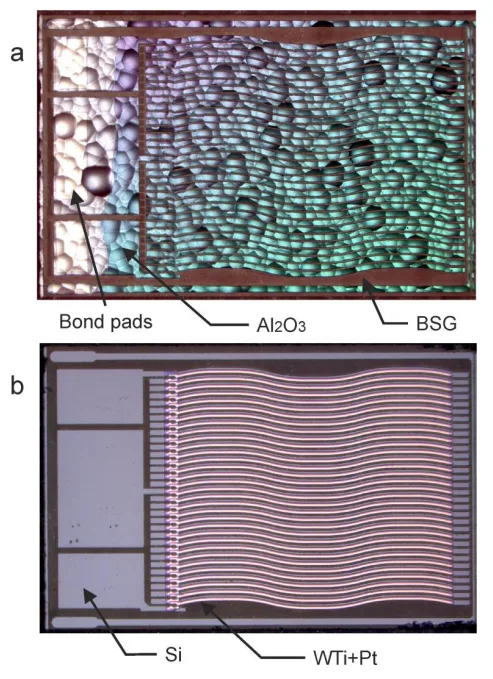
키워드
- Primary Keyword: 반도체 소자 임베딩 (Semiconductor Device Embedding)
- Secondary Keywords: 고압 다이캐스팅 (High-Pressure Die Casting, HPDC), 열전 발전기 (Thermogenerator, TG), 알루미늄 주조 (Aluminum Casting), 에너지 하베스팅 (Energy Harvesting), 금속-반도체 통합 (Metal-Semiconductor Integration), 주조 공정 안정성 (Casting Process Stability)
Executive Summary
- 도전 과제: 고온, 고압의 다이캐스팅 공정 중 섬세한 반도체 소자를 파손 없이 금속 부품에 직접 통합하는 것.
- 연구 방법: 열전 발전기(TG)를 보호용 폴리카보네이트 프레임워크에 고정한 후, 액체 알루미늄을 이용한 고압 다이캐스팅(HPDC) 공정을 통해 금속 부품 내부에 임베딩.
- 핵심 성과: 700°C의 알루미늄 용탕 속에서도 열전 발전기가 기능성을 유지하며 성공적으로 임베딩됨을 입증. 최종 수율 28% 달성.
- 결론: 반도체 소자의 금속 부품 직접 통합은 가능하며, 성공의 핵심은 주조 후 최종 부품의 기계적 변형을 제어하고 보호 프레임워크를 정교하게 설계하는 데 있음.
도전 과제: 왜 이 연구가 HPDC 전문가에게 중요한가
금속 부품에 센서나 전자 부품 같은 기능적 요소를 직접 통합하는 것은 수십 년간 엔지니어들의 목표였습니다. 이는 센서의 민감도를 극대화하고, 견고한 금속 케이싱으로 전자 부품을 외부 충격과 환경으로부터 보호할 수 있는 잠재력을 가지고 있기 때문입니다. 하지만 기존의 접근 방식에는 명확한 한계가 있었습니다. RFID 칩을 임베딩하려는 시도(Ref. [1-2])는 민감한 전자 장치를 보호하기 위해 상대적으로 두꺼운 보호층을 사용해야 했고, 이로 인해 센싱 요소로 사용하기에는 부적합했습니다. 또 다른 방법으로 박막 스트레인 센서를 강철 기판에 내장하는 연구(Ref. [3-4])도 있었지만, 이는 일반적인 반도체 기술과 호환되지 않아 적용 가능한 장치의 복잡성을 크게 제한했습니다. 본 연구는 이러한 한계를 극복하고, 일반적인 반도체(sc) 구조물을 용융 금속으로부터 부품을 형성하는 과정에서 직접 내장하는 가능성을 입증하는 것을 목표로 합니다.
접근 방식: 연구 방법론 분석
연구팀은 이 개념을 증명하기 위해 제베크 효과(Seebeck-effect) 기반의 열전 발전기(Thermogenerator, TG)를 시연용 소자로 선택했습니다(Ref. [5]). 이 TG는 주로 붕규산 유리(BSG) 몸체와 그 표면에 있는 Si-금속 열전퇴로 구성되어 있습니다(Figure 1). BSG 기판의 비정질 구조와 물결 모양의 열전퇴 형태는 주조 공정과 관련된 열-기계적 응력을 완화하는 역할을 합니다.
연구 과정은 다음과 같이 진행되었습니다.
- 초기 테스트: 먼저 녹는점이 232°C인 주석(tin) 용탕에 TG를 넣어 손상 없이 임베딩되는 것을 확인하며 개념의 신뢰성을 확보했습니다(Figure 2). 이 실험을 통해 TG의 Al2O3 절연층이 금속과의 단락을 효과적으로 방지함을 확인했습니다.
- 보호 프레임워크 개발: 알루미늄 고압 다이캐스팅(HPDC) 공정을 위해, TG의 일부(방열판 및 접촉 패드)는 노출시키고 중앙 부분만 금속에 묻히도록 특수 보호 장치가 필요했습니다(Figure 3). 폴리카보네이트로 제작된 프레임워크와 내열성 진공 고무 플러그를 사용하여 TG를 고정하는 방식이 최종적으로 채택되었습니다(Figure 5).
- HPDC 공정: 준비된 장치를 주조 금형에 넣고 'BÜHLER SCN/66' 주조기를 사용하여 HPDC 공정을 수행했습니다. 700°C의 AlSi9Cu3 알루미늄 합금을 사용했으며, 플런저 속도 0.6m/s, 재가압 300bar의 조건으로 주조했습니다.
- 후처리 및 분석: 주조 후, 아직 뜨거울 때 플라스틱 보호부를 기계적으로 제거하여 내장된 TG를 노출시키고(Figure 7) 기능성 테스트를 수행했습니다.
핵심 성과: 주요 발견 및 데이터
이 연구는 반도체 소자를 극한의 주조 환경에 통합하는 과정에서 중요한 통찰력을 제공했습니다.
- 성과 1: 성공적인 임베딩 및 기능성 확인 총 50개의 TG 중 14개가 임베딩 후에도 성공적으로 작동하여 28%의 수율을 보였습니다. 이는 700°C의 고온과 HPDC 공정의 높은 압력에도 불구하고 반도체 소자가 기능성을 유지할 수 있음을 실증적으로 보여준 중요한 결과입니다(Figure 6).
- 성과 2: 실패의 주된 원인 규명 실패 분석 결과, 파손의 주된 원인은 주조 공정의 열충격이 아니라, 주조 후 냉각 과정에서 발생하는 최종 알루미늄 부품의 '기계적 변형'이었습니다. 임베딩된 TG가 포함된 55mm 길이의 알루미늄 벽이 4mm 이상 구부러질 경우, 보호 조치의 종류와 상관없이 모든 TG가 파손되었습니다(Figure 8).
- 성과 3: 보호 프레임워크의 중요성 초기에는 플라스틱을 TG 주위에 직접 성형하려 했으나, 분리 과정에서 정렬 문제로 TG가 파손되었습니다. 최종적으로는 미리 성형된 플라스틱 부품에 구멍을 뚫고 TG를 고무 플러그로 고정하는 방식이 더 안정적임을 확인했습니다. 이는 임베딩 공정의 성공을 위해 소자를 고정하고 보호하는 프레임워크의 설계가 얼마나 중요한지를 보여줍니다.
귀사의 HPDC 운영을 위한 실질적 시사점
본 연구 결과는 실제 제조 환경에 다음과 같은 중요한 시사점을 제공합니다.
- 공정 엔지니어: 이 연구는 주조 공정 중 센서 임베딩이 가능함을 보여줍니다. 하지만 28%의 수율은 주조 후 부품 변형을 최소화하기 위한 정밀한 공정 제어의 필요성을 강조합니다. CASTMAN의 주조 시뮬레이션 솔루션은 Figure 8에서 나타난 부품의 뒤틀림을 사전에 예측하고 금형 설계 및 공정 변수 최적화를 통해 이를 완화하는 데 기여할 수 있습니다.
- 품질 관리: 내장된 TG의 기능성 자체가 주조 공정의 품질 지표로 활용될 수 있습니다. 즉, TG가 정상 작동한다면 해당 부품이 과도한 기계적 응력이나 변형을 겪지 않았음을 의미하며, 이는 결함 조기 발견의 새로운 지표가 될 수 있습니다.
- 금형 설계: 본 연구는 최종 부품의 기계적 안정성이 내장된 전자 장치를 보호하는 데 결정적이라는 점을 명확히 합니다. 금형 설계 시 용탕의 흐름뿐만 아니라, 논문에서 제안된 바와 같이 최종 부품의 구조적 강성을 확보하기 위한 보강 설계(reinforcement)가 반드시 고려되어야 합니다.
Paper Details
Micromachined Thermogenerator Directly Integrated into Metal Parts: Technological Aspects of the Embedding Process
1. 개요:
- 제목: Micromachined Thermogenerator Directly Integrated into Metal Parts: Technological Aspects of the Embedding Process
- 저자: A. Ibragimov, H. Pleteit, C. Pille and W. Lang
- 발행 연도: 2012
- 학술지/학회: 1st Joint International Symposium on System-Integrated Intelligence 2012: New Challenges for Product and Production Engineering
- 키워드: Aluminum, Casting, Energy Harvesting
2. 초록:
본 연구의 목표는 반도체(sc) 소자를 용융 상태에서 성형되는 금속 가공품에 통합하는 것의 실현 가능성을 입증하는 것이다. sc 소자 자체의 기계적 및 열적 안정성과 더불어, 임베딩 공정을 위한 준비 과정이 전체 성공에 중요하다. 이 논문은 준비 단계에 초점을 맞추며, 적절한 프레임워크의 제조와 그 안에 sc 소자를 고정하는 것을 포함한다. 프레임워크는 폴리카보네이트로 제조되었고, 시연용으로 선택된 열전 발전기는 진공 고무 플러그를 사용하여 고정되었다. 이후 프레임워크는 주조 금형에 배치되었고, 액체 알루미늄을 사용한 고압 다이캐스팅 공정이 수행되었다. 보호용 플라스틱 커버와 플러그를 기계적으로 제거한 후, 열전 발전기가 노출되었다. 후속 기능성 테스트에서 28%의 수율을 보였다. 실패 분석 결과, 프레임워크의 추가 개발이 필요함을 보여준다.
3. 서론 요약:
기능적 요소를 금속 가공품에 직접 통합하는 것은 두 가지 이점을 가진다. 한편으로는 부하를 받는 기판과의 직접적인 접촉이 내장된 센서의 감도를 향상시키고, 다른 한편으로는 전자 부품을 견고한 금속 케이싱에 내장하는 것이 기계적 스트레스와 환경적 영향에 대한 보호 역할을 할 수 있다. 이전의 연구들은 RFID 칩을 두꺼운 보호층으로 감싸거나(Ref. [1-2]), 일반 반도체 기술과 호환되지 않는 강철 기판에 박막 센서를 사용하는(Ref. [3-4]) 등의 한계가 있었다. 이 연구의 주요 목표는 이러한 접근 방식들 사이의 격차를 해소하고, 용융 상태에서 성형되는 금속 가공품에 반도체 구조물을 내장할 가능성을 입증하는 것이다.
4. 연구 요약:
연구 주제의 배경:
금속 부품에 센서나 액추에이터와 같은 지능형 기능을 부여하려는 수요가 증가하고 있다. 특히 주조 공정 중에 이러한 기능 요소를 직접 통합하면 제조 공정을 단순화하고, 최종 제품의 성능과 신뢰성을 향상시킬 수 있다.
이전 연구 현황:
이전 연구들은 주로 민감한 전자 소자를 보호하기 위해 두꺼운 절연층을 사용하거나, 특정 기판(예: 강철)에만 적용 가능한 기술을 사용하여 적용 범위와 소자의 복잡성에 제한이 있었다.
연구 목적:
일반적인 반도체(sc) 소자를 고온의 용융 금속을 사용하는 주조 공정 중에 금속 부품 내부에 직접 통합하는 기술의 실현 가능성을 입증하고, 이 과정에서 발생하는 기술적 문제들을 파악하고 해결 방안을 모색하는 것이다.
핵심 연구:
제베크 효과 기반의 열전 발전기(TG)를 시연 소자로 사용하여, 보호 프레임워크 설계, 소자 고정 방법, 그리고 실제 고압 다이캐스팅(HPDC) 공정을 통한 알루미늄 부품 내 임베딩을 수행했다. 공정 후 기능성 테스트와 실패 분석을 통해 기술의 성공률과 주요 실패 원인을 규명했다.
5. 연구 방법론
연구 설계:
- 시연용 소자로 열-기계적 스트레스에 강한 TG를 선택.
- 저온 금속(주석)을 이용한 예비 실험으로 개념 검증.
- 고온/고압의 알루미늄 HPDC 공정을 위한 보호 프레임워크 설계 및 제작.
- 프레임워크에 TG를 고정한 후, 실제 HPDC 공정 수행.
- 주조 후 보호부 제거 및 TG의 기능성 평가.
데이터 수집 및 분석 방법:
임베딩 공정 후, TG의 전기적 특성(단락 여부, 발전 기능)을 테스트하여 성공 여부를 판단했다. 실패한 샘플에 대해서는 외관 검사를 통해 파손 원인(균열, 변형 등)을 분석했다.
연구 주제 및 범위:
연구는 반도체 소자를 용융 알루미늄을 이용한 HPDC 공정에 직접 통합하는 기술적 측면에 초점을 맞춘다. 특히, 소자를 보호하기 위한 프레임워크의 설계와 고정 방법, 그리고 최종 주조품의 기계적 안정성이 소자의 생존에 미치는 영향을 주요 범위로 다룬다.
6. 주요 결과:
주요 결과:
- 주석(232°C) 및 알루미늄(700°C) 용탕을 이용한 임베딩 공정에서 TG가 파괴되지 않고 기능성을 유지함을 입증했다.
- Al2O3 절연층은 금속과의 단락을 효과적으로 방지했다.
- 알루미늄 HPDC 공정에서 최종 수율은 28%였다.
- 실패의 주된 원인은 열충격이 아닌, 주조 후 냉각 과정에서 발생하는 최종 부품의 기계적 변형(굽힘)으로 밝혀졌다. 55mm 길이의 부품에서 4mm 이상의 굽힘이 발생했을 때 TG가 파손되었다.
- 임베딩 공정의 성공을 위해서는 소자 자체의 안정성뿐만 아니라, 보호 프레임워크의 설계와 최종 주조품의 기계적 안정성 확보가 매우 중요하다.
Figure 이름 목록:
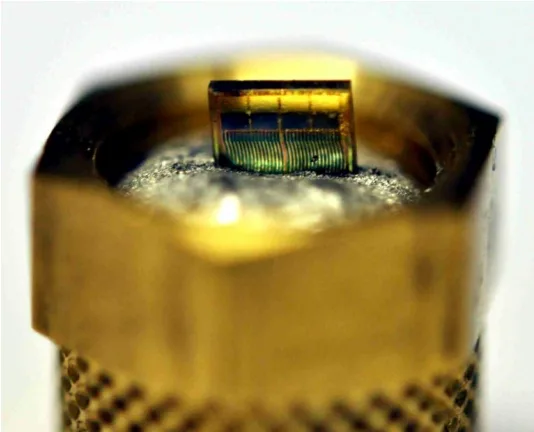

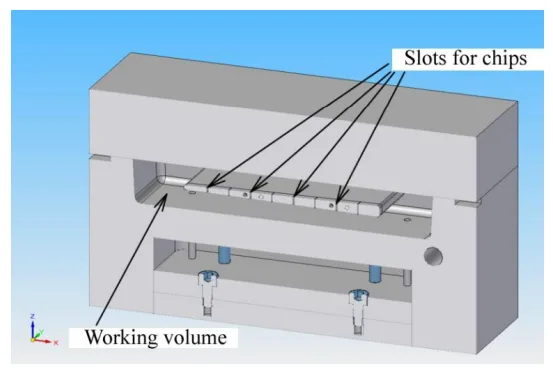
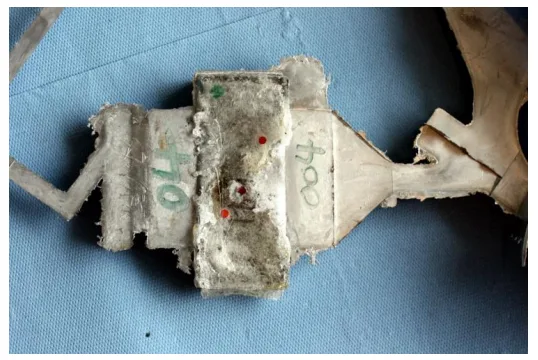
Figure 6. Mounting with three TG embedded in cast aluminium.
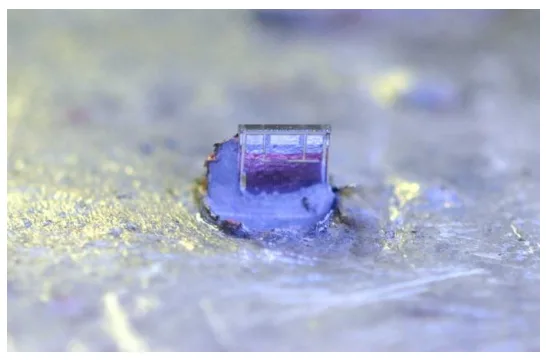
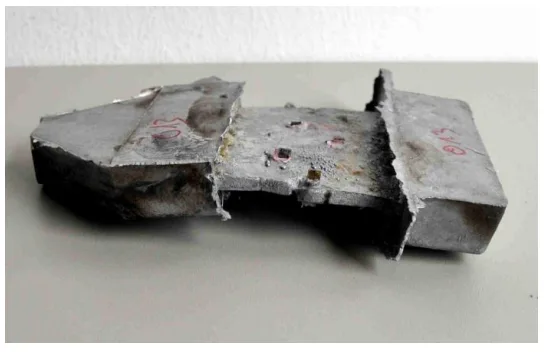
- Figure 1. Thermogenerator: (a) view from the structured side, (b) view through the transparent BSG-substrate.
- Figure 2. TG embedded into tin.
- Figure 3. Schematic of the embedding process with a removable plastic protection.
- Figure 4. Section of the puncheon for the initial embedding into the plastic component.
- Figure 5. Plastic mounting with three TGs fixed in it using resin plugs.
- Figure 6. Mounting with three TG embedded in cast aluminium.
- Figure 7. Half embedded TG after removing protective plastic.
- Figure 8. Deformation of an aluminum casting part.
7. 결론:
용융된 덩어리로부터 주조하는 동안 반도체 소자를 금속 구조 부품에 직접 통합하는 것의 실현 가능성이 입증되었다. 예시로 열전 발전기(TG)가 주석과 알루미늄에 내장되었다. 이 열적, 기계적으로 안정한 MEMS 구조는 700°C까지 테스트되었고 기능성을 잃지 않았다. 해당 프레임워크 제조 및 칩 고정을 포함한 임베딩 공정을 위한 TG의 준비 과정의 중요한 역할이 과소평가되어서는 안 된다. 실패 분석 결과, 향후 연구에서는 최종 알루미늄 부품의 기계적 안정성 문제를 해결하기 위해 개선된 프레임워크를 구현해야 함을 보여주었다.
8. 참고문헌:
- [1] Busse, M., Wöstmann, F.-J., Müller, T., Melz, T., Spies, P., 2006, Intelligente Gussteile – Einsatz adaptronischer Komponenten in Kombination mit Gussteilen. In: Giesserei 2006, 93/04:48-53.
- [2] Pille, C., 2010, In-Process-Embedding of Piezo Sensors and RFID Transponders into Cast Parts for Autonomous Manufacturing Logistics Gessner, T. (ed.): Smart Systems Integration.
- [3] Kobliska, J. et al., 2005, Rapid fabrication of smart tooling with embedded sensors by casting in molds made by three dimensional printing, Proceedings of the SFF Symposium.
- [4] Cheng, X. et al., 2007, Study on embedding and integration of microsensors into metal structures for manufacturing applications, J. Manuf. Sci. Eng., 129:416.
- [5] Ibragimov, A., Pleteit, H., Pille, C., and Lang, W., 2012, IEEE Electron Device Lett., 33/2:233-235.
결론 및 다음 단계
이 연구는 주조 공정을 통해 지능형 금속 부품을 제조하는 데 있어 중요한 기술적 로드맵을 제공합니다. 연구 결과는 품질을 개선하고, 결함을 줄이며, 생산을 최적화하기 위한 명확하고 데이터 기반의 경로를 제시합니다.
CASTMAN은 고객의 가장 어려운 기술적 문제를 해결하기 위해 최첨단 산업 연구를 적용하는 데 전념하고 있습니다. 이 백서에서 논의된 문제가 귀사의 연구 목표와 일치한다면, 저희 엔지니어링 팀에 연락하여 이러한 고급 원칙을 귀사의 연구에 적용하는 방법에 대해 논의해 주시기 바랍니다.
전문가 Q&A:
- Q1: 이 연구의 주된 목표는 무엇이었나요? A1: 이 연구의 주된 목표는 용융 상태의 금속으로부터 부품을 성형하는 과정에서 반도체 소자를 직접 통합하는 기술의 실현 가능성을 입증하는 것이었습니다. (출처: "Micromachined Thermogenerator Directly Integrated into Metal Parts" 논문의 Summary 섹션)
- Q2: 시연용으로 어떤 종류의 소자가 사용되었고 그 이유는 무엇인가요? A2: 제베크 효과 기반의 열전 발전기(TG)가 사용되었습니다. 그 이유는 TG의 구조(비정질 BSG 기판, 물결 모양 열전퇴)가 주조 공정의 열-기계적 스트레스를 견딜 만큼 충분히 견고하고, 그 기능성이 향후 더 복잡한 2세대 장치에 유용하게 사용될 수 있기 때문입니다. (출처: 논문의 Section 1, "Requirements and demonstrator's choice")
- Q3: 알루미늄 임베딩 공정의 성공률은 얼마였으며, 주된 실패 원인은 무엇이었나요? A3: 기능적 수율은 28%(50개 중 14개 성공)였습니다. 주된 실패 원인은 고온의 열충격이 아니라, 주조 후 냉각 과정에서 발생한 최종 알루미늄 부품의 기계적 변형(굽힘)이었습니다. Figure 8에서 볼 수 있듯이, 부품이 4mm 이상 구부러지면 TG가 파손되었습니다. (출처: 논문의 Section 2 후반부 및 Section 3)
- Q4: 알루미늄 고압 다이캐스팅(HPDC)의 핵심 공정 조건은 무엇이었나요? A4: AlSi9Cu3 합금을 700°C의 온도로 사용했으며, 플런저 속도는 0.6m/s, 재가압 압력은 300bar였습니다. (출처: 논문의 Section 2, "Technological aspects of the embedding process")
- Q5: 섬세한 반도체 소자는 주조 공정 중에 어떻게 보호되었나요? A5: 폴리카보네이트로 만든 특수 프레임워크를 사용했습니다. TG는 진공 고무 플러그를 사용하여 이 프레임워크 내부에 고정되었고, 전체 조립품이 주조 금형에 배치되었습니다. 주조 후 프레임워크는 기계적으로 제거되었습니다. 이 과정은 Figure 5와 Figure 6에 묘사되어 있습니다. (출처: 논문의 Section 2)
저작권
- 이 자료는 A. Ibragimov 외 저자의 논문 "[Micromachined Thermogenerator Directly Integrated into Metal Parts: Technological Aspects of the Embedding Process]"를 분석한 것입니다.
- 논문 출처: 1st Joint International Symposium on System-Integrated Intelligence 2012: New Challenges for Product and Production Engineering
- 본 자료는 정보 제공 목적으로만 사용됩니다. 무단 상업적 사용을 금지합니다.
- Copyright © 2025 CASTMAN. All rights reserved.