본 요약은 ['Scientia Iranica' 저널에 게재된 'Design of Conformal Cooling Channels Using Numerical Methods in a Metal Mold and Calculating Exergy Destruction in Channels' 논문을 기반으로 작성되었습니다.]
1. 개요:
- 제목: 금속 몰드 내 컨포멀 냉각 채널의 수치적 방법 설계 및 채널 내 엑서지 파괴 계산 (Design of Conformal Cooling Channels Using Numerical Methods in a Metal Mold and Calculating Exergy Destruction in Channels)
- 저자: Ali BOLATTÜRK, Osman İPEK, Karani KURTULUŞ, Mehmet KAN
- 출판 연도: 2018년 8월
- 출판 저널/학술 단체: Scientia Iranica
- 키워드: 금속 몰드 (Metal Mold), 엑서지 파괴 (Exergy Destruction), 냉각 채널 설계 (Cooling Channel Design).
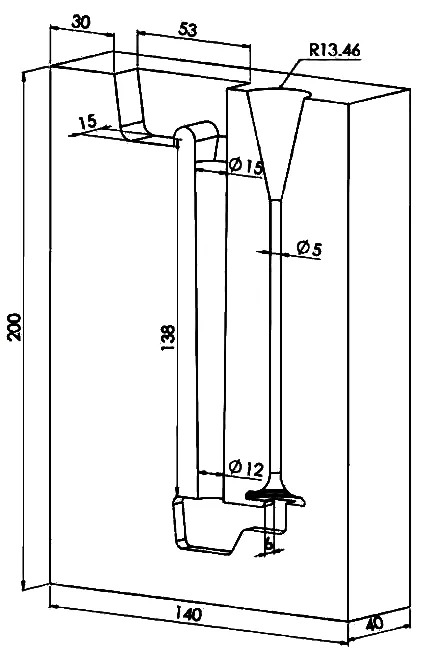
2. 초록 또는 서론
금속 몰드에서 더 빠른 냉각을 통해 사이클 시간을 단축하고 제품 품질을 향상하며 제품 손실을 줄일 수 있습니다. 그러나 기존 제조 방식으로는 몰드 냉각 채널을 선형 방향과 제한된 형태로만 제작할 수 있어 몰드 냉각 성능에 제약이 있습니다. 최근 개발된 적층 제조 기술은 복잡한 형상과 모노블록 3D 제품 제작이 가능합니다. 이 기술을 통해 다양한 형태의 컨포멀 냉각 채널을 갖춘 금속 몰드를 제작하여 우수한 냉각 성능을 확보할 수 있습니다. 본 연구에서는 모노블록 영구 몰드에서 최적의 냉각 성능을 달성하기 위해 컨포멀 냉각 채널을 설계했습니다. 본 연구에서는 설계된 컨포멀 냉각 채널과 기존 냉각 채널 몰드에 대해 정상 상태 조건에서 CFD (Computational Fluid Dynamics, 전산 유체 역학) 해석을 수행했습니다. 채널 내 유속 변화에 따른 압력 강하, 냉각 채널 출구 온도 및 엑서지 파괴를 계산했습니다. 수치 해석 결과, 컨포멀 냉각 채널이 기존 냉각 채널보다 약 5% 높은 냉각 성능을 달성할 수 있는 것으로 나타났습니다. 그러나 컨포멀 냉각 채널의 압력 강하는 기존 냉각 채널보다 더 높게 관찰되었습니다. 또한 컨포멀 냉각 채널의 엑서지 파괴는 기존 냉각 채널보다 약 12% 더 컸습니다.
3. 연구 배경:
연구 주제 배경:
금속 몰드에서 냉각 과정은 액체 금속의 응고에 중요한 요소 중 하나이며, 주조 제품 품질에 영향을 미칩니다. 냉각이 균일하지 않으면 핫 스팟 결함 및 변형과 같은 몰딩 결함이 발생합니다. 반대로, 적절하고 빠른 냉각은 제품 품질에 긍정적인 영향을 미칩니다. 기존 제조 방식으로는 몰드 냉각 채널을 선형 방향과 원형 단면으로만 제작할 수 있습니다. 이는 몰드 냉각 성능을 제한합니다 [1]. 적층 제조 방식으로 제작된 컨포멀 냉각 채널을 갖는 열간 압출 다이의 냉각 성능에 대한 연구가 있습니다 [2]. 컨포멀 냉각 채널 몰드를 사용했을 때 표준 냉각 채널 몰드에 비해 생산 속도가 최대 300% 증가하는 것으로 관찰되었습니다. 몰딩의 사이클 시간은 제품 비용과 품질에 영향을 미칩니다. 사이클 시간이 짧을수록 온도 분포가 더 균일하고 부품 변형이 적은 것으로 관찰되었습니다. 따라서 컨포멀 냉각 채널을 갖는 사출 금형에서 더 나은 제품 품질을 얻었습니다 [3-9]. 적층 제조 방식으로 제작된 금속 몰드의 생산 비용이 높다는 사실은 원하는 성능으로 컨포멀 냉각 채널 설계를 생산해야 할 필요성을 야기합니다. 유한 요소법을 사용하여 몰드 냉각 채널의 냉각 성능과 액체 금속의 응고 과정을 시뮬레이션할 수 있습니다. 수치 연구 결과, 컨포멀 냉각 채널을 통해 응고 시간을 줄여 냉각 성능을 향상시킬 수 있는 것으로 나타났습니다 [10-12]. 플라스틱 사출 금형용 컨포멀 냉각 채널이 설계되었습니다 [1]. 해당 연구는 수치적 및 실험적으로 수행되었습니다.
기존 연구 현황:
수치 및 실험 연구 결과, 컨포멀 냉각 채널을 사용했을 때 사이클 시간이 12.8% 단축되는 것으로 나타났습니다. 또한 Park and Dang [9]은 플라스틱 사출 금형용 컨포멀 냉각 채널을 개발했습니다. 연구 결과, 컨포멀 냉각 채널을 사용했을 때 사이클 시간이 30% 단축되는 것으로 나타났습니다.
마찰 손실, 온도 차이로 인한 열 전달, 급격한 팽창 및 압축은 시스템에서 엑서지 손실을 유발합니다 [13-15]. 용융 금속의 열은 냉각 채널을 통해 전달됩니다. 용융 금속과 냉각 채널 사이의 열 전달은 열교환기의 작동 원리와 유사합니다. 열교환기에서 엑서지 손실에 대한 많은 연구가 문헌에 존재합니다. 그러나 금속 몰드 냉각 채널에서 엑서지 손실에 대한 연구는 문헌에서 매우 드뭅니다. 열교환기 또는 열역학적 사이클의 최적 작동 조건을 결정하고 엑서지 파괴를 줄이기 위해 유체 속도, 압력 강하, 온도 분포와 같은 매개변수를 연구자들이 조사했습니다. 그들은 엑서지 파괴가 이러한 매개변수를 개선함으로써 감소된다는 점을 강조했습니다 [16-19].
최근 몇 년 동안 개발된 적층 제조 기술을 통해 복잡한 형상과 컴팩트한 구조로 제품을 제조할 수 있습니다. 본 연구에서는 기존 제조 방식으로 생산할 수 없는 다양한 형상의 금속 몰드 내 냉각 채널을 설계했습니다. 두 가지 다른 컨포멀 냉각 채널 몰드를 설계하고 정상 상태 조건에서 표준 냉각 채널 몰드와 수치적으로 비교했습니다. 각 채널에 대해 다양한 유량에서 열 전달률, 엑서지 파괴 및 압력 강하를 계산했습니다.
연구의 필요성:
적층 제조 방식으로 생산된 금속 몰드의 높은 생산 비용으로 인해 원하는 성능으로 컨포멀 냉각 채널 설계를 생산해야 할 필요성이 있습니다. 컨포멀 냉각 채널은 냉각 성능을 향상시킬 수 있지만, 압력 강하 및 엑서지 파괴 측면에서 기존 냉각 채널과 비교 분석이 필요합니다. 최적의 냉각 채널 설계를 위해서는 열 전달 성능뿐만 아니라 에너지 효율성을 고려한 엑서지 분석이 필수적입니다.
4. 연구 목적 및 연구 질문:
연구 목적:
본 연구의 주요 목적은 금속 몰드에서 최적의 냉각 성능을 달성하기 위해 컨포멀 냉각 채널을 설계하고 수치적으로 분석하여 기존 냉각 채널 설계와 비교하는 것입니다. 본 연구는 열 전달, 압력 강하 및 엑서지 파괴 측면에서 성능 차이를 평가하는 것을 목표로 합니다.
핵심 연구 질문:
- 영구 몰드용 컨포멀 냉각 채널 설계는 어떻게 이루어지는가?
- 컨포멀 냉각 채널 (곡선 채널 (CC) 및 구형 핀 채널 (SFC)) 과 표준 채널 (SC) 의 금속 몰드 내 냉각 성능을 CFD를 사용하여 수치적으로 비교하면 어떤 결과가 나타나는가?
- 다양한 냉각 채널 설계에 대해 유속 변화에 따른 압력 강하, 냉각 채널 출구 온도 및 엑서지 파괴를 계산하고 비교하면 어떤 결과가 나타나는가?
연구 가설:
- 컨포멀 냉각 채널은 기존 냉각 채널보다 높은 냉각 성능을 나타낼 것이다.
- 컨포멀 냉각 채널의 압력 강하 및 엑서지 파괴는 기존 냉각 채널보다 높을 수 있다.
- 최적화된 컨포멀 냉각 채널 설계는 압력 강하 및 엑서지 파괴 증가 가능성에도 불구하고 냉각 효율성을 향상시킬 수 있다.
5. 연구 방법론
연구 설계:
본 연구는 수치 시뮬레이션 기반 연구 설계를 채택합니다. 표준 채널 (SC), 곡선 채널 (CC) 및 구형 핀 채널 (SFC) 의 세 가지 냉각 채널 구성을 설계했습니다. CFD 해석은 정상 상태 조건에서 수행하여 이러한 설계의 열적 및 유체 역학적 성능을 비교했습니다.
자료 수집 방법:
자료는 ANSYS-FLUENT 16.1 소프트웨어 [24] 를 사용한 CFD 시뮬레이션을 통해 수집되었습니다. 시뮬레이션은 다양한 냉각 오일 속도에서 각 채널 설계에 대한 압력 강하, 냉각 채널 출구 온도 및 열 전달률을 계산했습니다. 재료 속성 및 경계 조건은 문헌 및 실험 데이터를 기반으로 정의되었습니다.
분석 방법:
수집된 수치 데이터를 분석하여 다양한 냉각 채널 설계의 성능을 비교했습니다. 엑서지 파괴는 Engineering Equation Solver (EES) 소프트웨어 [25] 를 사용하여 계산되었습니다. 분석은 각 채널 유형에 대한 유속의 함수로서 열 전달률, 압력 강하, 출구 온도 및 엑서지 파괴를 평가하는 데 중점을 두었습니다. 수치 모델의 검증은 Imran et al. [23] 의 기존 실험 데이터와 결과를 비교하여 수행되었습니다.
연구 대상 및 범위:
연구 대상은 중력 다이캐스팅용 영구 몰드이며, 특히 가솔린 내연 기관의 배기 밸브용으로 모델링되었습니다 (Fig. 1). 연구 범위는 "Petro-therm" 브랜드 열 전달 오일을 냉매로 사용하고 GGG 50 연성 주철 (SC 용) 및 스테인리스강 316 L (CC 및 SFC 용) 을 몰드 재료로 사용하여 이 몰드 형상 내에서 세 가지 다른 냉각 채널 설계 (SC, CC, SFC) 의 수치 해석으로 제한됩니다.
6. 주요 연구 결과:
핵심 연구 결과:
- 냉각 성능: SFC는 기준 속도 1 m/s에서 SC보다 약 5% 높은 열 전달률을 나타냈습니다. SFC는 CC 및 SC보다 더 많은 열을 전달합니다 (Figure 7a).
- 압력 강하: SFC의 압력 강하 (약 50 kPa까지) 는 속도가 증가함에 따라 SC (1-4 kPa) 보다 훨씬 높았습니다.
- 엑서지 파괴: SFC의 엑서지 파괴는 SC보다 약 12% 더 컸습니다. SC 및 CC의 경우 엑서지 파괴는 속도가 증가함에 따라 처음에는 증가했다가 감소한 반면, SFC는 약 0.37 kW 주변에서 변동하는 엑서지 파괴를 보였습니다 (Figure 7b).
- 출구 온도: 속도가 증가함에 따라 모든 채널의 출구 온도가 감소했습니다. 입구와 출구 사이의 온도 차이는 모든 채널에서 작았습니다 (4K).
제시된 데이터 분석:
수치 결과는 컨포멀 냉각 채널, 특히 SFC가 표준 채널에 비해 열 전달을 향상시킨다는 것을 나타냅니다. 그러나 이러한 성능 향상은 압력 강하 및 엑서지 파괴 증가라는 단점이 있습니다. SFC 설계는 가장 높은 열 전달률을 제공하지만, 가장 높은 압력 강하 및 엑서지 파괴를 나타냅니다. SFC에서 변동하는 엑서지 파괴는 구형 핀 구조 내의 복잡한 유동 역학을 시사합니다. 모든 채널에서 입구와 출구 사이의 작은 온도 차이는 효율적인 열 제거를 나타내지만, 엑서지 손실을 최소화하기 위한 채널 설계 최적화의 필요성을 강조합니다.
그림 목록:
- Figure 1. 금속 몰드 대칭 부품의 솔리드 모델
- Figure 2. 몰드 냉각 채널 열 전달 메커니즘의 가정
- Figure 3. 분석된 냉각 채널의 전산 영역
- Figure 4. 분석된 몰드 구성에 사용된 경계 조건
- Figure 5. Imran et al. [23] 및 현재 연구 결과의 기준 온도 비교
- Figure 6. Imran et al. [23] 및 현재 연구 결과의 압력 강하 비교
- Figure 7 a. 유량에 따른 SC, CC 및 SFC의 열 전달률 및 압력 강하 비교, b. 유량에 따른 SC, CC 및 SFC의 채널 출구 온도 및 엑서지 손실 비교
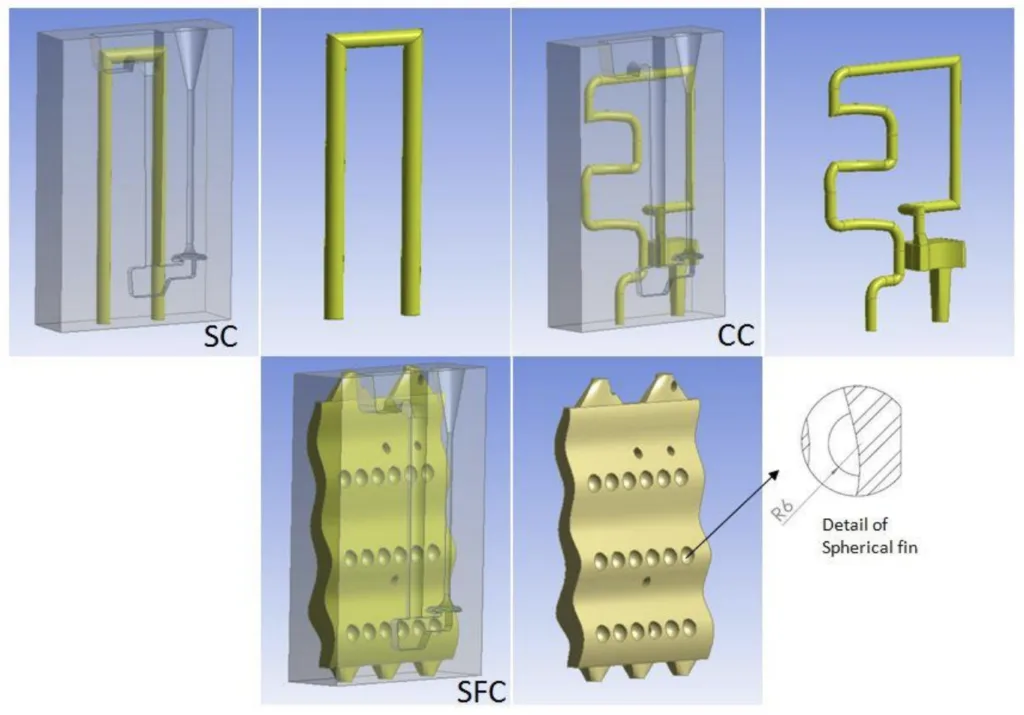
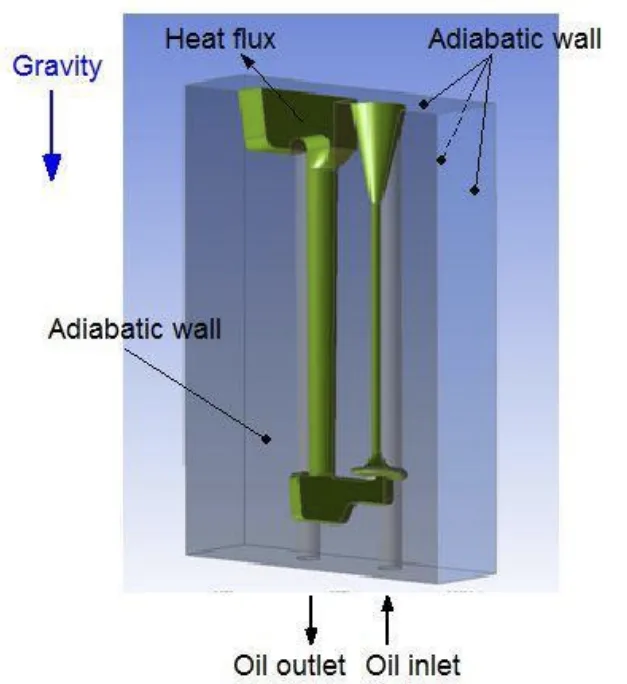
![Figure 5. Comparison of Imran et al. [23] and current study results for base temperature](https://castman.co.kr/wp-content/uploads/image-950-1024x707.webp)
![Figure 6. Comparison of Imran et al. [23] and current study results for pressure drop](https://castman.co.kr/wp-content/uploads/image-951-1024x699.webp)
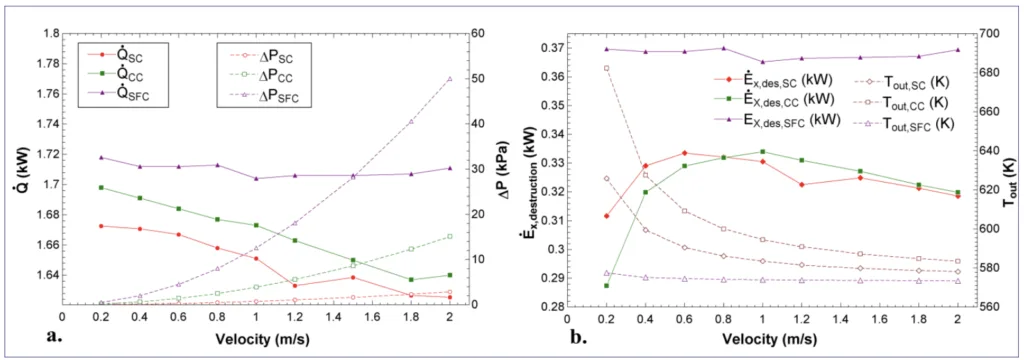
7. 결론:
주요 연구 결과 요약:
본 연구에서는 금속 몰드용 표준 (SC), 곡선 (CC) 및 구형 핀 (SFC) 컨포멀 냉각 채널을 수치적으로 비교했습니다. SFC는 기준 속도 1 m/s에서 SC보다 5% 더 높은 열 전달률을 보였지만, 압력 강하가 훨씬 높고 엑서지 파괴가 12% 더 컸습니다. 열 전달률은 사이클 시간이 감소함에 따라 증가합니다. 1m/s 속도에서 SC 및 SFC는 각각 0.157 W 및 11.7 W의 펌프 동력을 필요로 했습니다. SFC는 40W 더 많은 열 전달률을 달성했지만, 압력 강하는 SFC에서 가장 높았습니다. 유량이 감소함에 따라 출구와 입구 사이의 온도 차이는 SFC에 비해 SC 및 CC에서 더 높았습니다. SFC의 엑서지 파괴는 변동적이었고 SC보다 지속적으로 높았습니다.
연구의 학문적 의의:
본 연구는 컨포멀 냉각 채널 설계에 대한 상세한 수치 해석을 제공하여 기존 설계와 비교하여 열적 및 유체 역학적 성능에 대한 이해를 높입니다. 본 연구는 컨포멀 냉각에서 향상된 열 전달과 증가된 압력 강하 및 엑서지 파괴 사이의 상충 관계를 강조하여 금속 몰드에서 냉각 채널 설계를 최적화하는 데 유용한 통찰력을 제공합니다.
실용적 의미:
연구 결과는 컨포멀 냉각 채널, 특히 SFC가 냉각 성능을 향상시키고 잠재적으로 사이클 시간을 단축할 수 있지만, 설계자는 증가된 압력 강하 및 엑서지 파괴를 고려해야 함을 시사합니다. 냉각 채널 설계 선택은 원하는 열 전달률, 허용 가능한 압력 강하 및 에너지 효율성 사이의 균형을 기반으로 해야 합니다. 열 전달을 극대화하는 것이 중요한 응용 분야의 경우 SFC가 에너지 소비가 더 높더라도 적합할 수 있습니다. 에너지 효율성을 우선시하는 응용 분야의 경우 SC 또는 CC 설계가 더 적합할 수 있습니다.
연구의 한계 및 향후 연구 분야:
본 연구는 수치 시뮬레이션에 국한되며, 조사된 특정 몰드 형상 및 채널 설계에 대한 실험적 검증을 포함하지 않습니다. 향후 연구에서는 이러한 수치적 결과에 대한 실험적 검증에 초점을 맞춰야 합니다. 높은 열 전달률을 유지하면서 컨포멀 냉각 채널 설계에서 엑서지 파괴를 최소화하기 위한 추가 최적화 연구가 필요합니다. 몰드 성능 및 주조 품질에 대한 다양한 컨포멀 냉각 채널 형상 및 유동 매개변수의 영향을 조사하는 것도 유익할 것입니다.
8. 참고 문헌:
- [1] Hsu, F.H. Wang, K. Huang, C.T. Chang, R.Y. “Investigation on conformal cooling system design in injection molding”, Advances in Production Engineering & Management., 8(2), pp.107-115 (2013).
- [2] Hölker, R. Haase, M. Khalifa, N.B. Takkaya, A. E. “Hot extrusion dies with conformal cooling channels produced by additive manufacturing”, Aluminum Two Thousand World Congress and International Conference on Extrusion and Benchmark ICEB, pp. 4838-4846 (2015).
- [3] Sachs, E. Wylonis, E. Allen, S. Cima, M. Guo, H. “Production of Injection Moulding Tooling With Conformal Cooling Channels Using the Three Dimensional Printing Process”, Polymer Engineering and Science., 40(5), (2000).
- [4] Eimsa-ard, K. and Wannisorn, K. “Conformal bubbler cooling for molds by metal deposition process”, Computer-Aided Design., 69, pp. 126-133 (2015).
- [5] Wang, Y. Yu, K. M. Wang, C. C. L. “Spiral and conformal cooling in plastic injection molding", Computer-Aided Design., 63, pp. 1-11 (2015).
- [6] Vojnová, E. "The benefits of a conforming cooling systems the molds in injection moulding process", Procedia Engineering., 149, pp. 535-543 (2016).
- [7] Venkatesh, G. Y. Ravi, K. Raghavendra, G. "Comparison of Straight Line to Conformal Cooling Channel in Injection Molding", Materials Today: Proceedings., 4(2), pp. 1167-1173 (2017).
- [8] Jahan, A.S. and Mounayri, H. "Optimal Conformal Cooling Channels in 3D Printed Dies for Plastic Injection Molding", Procedia Manufacturing., 5, pp. 888-900 (2016).
- [9] Park, H. Dang, X.P. "Development of a smart plastic injection mold with conformal cooling channels", Procedia Manufacturing., 10, pp. 48-59 (2017).
- [10] Wang, G. Zhao, G. Li, H. Guan, Y. “Multi-objective optimization design of the heating/cooling channels of the steam-heating rapid thermal response mold using particle swarm optimization”, Int. J. of Thermal Science., 50, pp. 790-802 (2011).
- [11] Franke, M. M. Hilbinger, R. M. Lohmüller, A. Singer, R. F. “The effect of liquid metal cooling on thermal gradients in directional solidification of super alloys: Thermal analysis”, Journal of Material Processing Technology., 213, pp. 2081-2088 (2013).
- [12] Furumoto, T. Ueda, T. Amino, T. Ksunoki, D. Hosokowa, A. Tanaka, T. “Finishing performance of cooling channel with face protuberance inside the molding die", Journal of Material Processing Technology., 212, pp. 2154-2160 (2012). DOI: 10.1016/j.jmatprotec.2012.05.016
- [13] Khairul, M. A. Alim, M. A. Mahbubul, I. M. Saidur, R. Hepbasli, A. Hossain, A. “Heat transfer performance and exergy analyses of a corrugated plate heat exchanger using metal oxide nanofluids", International Communications in Heat and Mass Transfer., 50, pp. 8–14 (2014).
- [14] Dizaji, H. S. Jafarmadar, S. Asaadi, S. “Experimental exergy analysis for shell and tube heat exchanger made of corrugated shell and corrugated tube”, Experimental Thermal and Fluid Science., 81, pp. 475-481 (2017).
- [15] Ipek, O. Kan, M. Gurel, B. “Examination of Different Heat Exchangers and the Thermal Activities of Different Designs”, Acta Physica Polonica A., 132(3), pp. 580-583 (2017).
- [16] Kan, M. Ipek, O. Gurel, B. "Plate Heat Exchangers as a Compact Design and Optimization of Different Channel Angles”, Acta Physica Polonica A., 128(2B), B-49 (2015).
- [17] Karaail, R. Öztürk, I. T. “Thermoeconomic Analyses of Steam Injected Gas Turbine Cogeneration Cycles", Acta Physica Polonica A., I, 128(2B), B-279 (2015).
- [18] Zehtabiyan, R. N. Damirci, D. S. Fazel, Z.M.H. Saffar, A. M. "Generalized heat transfer and entropy generation of stratified air-water flow in entrance of a mini-channel", Scientia Iranica B., 24(5), pp. 2406-2417 (2017).
- [19] Nouri, B. A. and Seyyed, H. M. H. "Numerical analysis of thermally developing turbulent flow in partially filled porous pipes", Scientia Iranica В., 22(3), pp. 835-843 (2015).
- [20]Altinsoy, İ. Çelebi Efe, G.F. Yener, T. Önder, K. G. Bindal, C. “Effect of Double Stage Nitriding on 34CrAlNi7-10 Nitriding Steel”, Acta Physica Polonica A., 132, pp. 663-666 (2017).
- [21] Arunkumar, S. Rao, K. S. Kumar, T. P. "Spatial variation of heat flux at the metal-mold interface due to mold filling effects in gravity die-casting", Int. J. of Heat and Mass Transfer., 51(11), pp. 2676-2685 (2008).
- [22] Hallam, C. P. and Griffiths, W. D. “A model of the interfacial heat-transfer coefficient for the aluminum gravity die-casting process”, Metallurgical and materials transactions B., 35(4), pp. 721-733 (2004).
- [23] Imran, A. A. Nabeel, S. M. Hayder, M. J. "Numerical and experimental investigation of heat transfer in liquid cooling serpentine mini-channel heat sink with different new configuration models" Thermal Science and Engineering Progress., 6, pp. 128-139 (2018).
- [24] Fluent, Version 16.1 User's Guide, Fluent Inc., Lebanon (NH) (2016).
- [25] Klein, S. A. “Engineering Equation Solver (EES)”, Academic Commercial V8.208.F-Chart Software, www.fChart.com (2008).
9. 저작권:
- 본 자료는 "Ali BOLATTÜRK, Osman İPEK, Karani KURTULUŞ, Mehmet KAN"의 논문 "Design of Conformal Cooling Channels Using Numerical Methods in a Metal Mold and Calculating Exergy Destruction in Channels"을 기반으로 요약되었습니다.
- 논문 출처: https://doi.org/10.24200/sci.2018.50090.1502
본 자료는 위 논문을 요약한 것으로, 상업적 목적으로 무단 사용하는 것을 금지합니다.
Copyright © 2025 CASTMAN. All rights reserved.