본 소개 자료는 "AIM / La Metallurgia Italiana"에서 발행한 "[The tool steel producer's contribution to successful die casting of structural components]" 논문을 기반으로 작성되었습니다.
![FIG. 1 Cast aluminium structural components (red) in the auto body of the AUDI A 8 [4]. Componenti strutturali di alluminio pressocolati (in rosso) nella carrozzeria della AUDI A 8 [4].](https://castman.co.kr/wp-content/uploads/image-1915-png.webp)
Componenti strutturali di alluminio pressocolati (in rosso) nella carrozzeria della AUDI A 8 [4].
1. 개요:
- 제목: 구조 부품의 성공적인 다이캐스팅을 위한 공구강 제조업체의 기여 (The tool steel producer's contribution to successful die casting of structural components)
- 저자: I. Schruff (Kind & Co., Edelstahlwerk, KG, Wiehl, Germany)
- 발행 연도: 2012
- 발행 학술지/학회: La Metallurgia Italiana - n. 9/2012 (AIM 주관 유럽 컨퍼런스 HTDC High Tech Die Casting, Vicenza 2012년 2월 9-11일 - Como 2011년 9월 21-23일 발표 논문)
- 키워드: 구조 부품, 자동차 산업, 열간 공구강, 특수 열간 공구강 등급, 기계적 특성, 히트 체킹 저항성, 열전도율, 열처리
2. 초록:
자동차 산업에서 다이캐스팅 구조 부품은 차량의 경량화에 크게 기여하여 연비 향상 및 CO2 배출량 감소에 중요한 역할을 하고 있습니다. 따라서 오늘날 다이캐스팅 알루미늄 A-, B-, C-필러, 쇼크 타워 또는 도어 부품이 기존의 강철 부품을 대체하는 경우가 매우 많습니다. 이러한 구조 부품은 종종 큰 치수와 복잡한 디자인이 특징입니다.
구조 부품용 다이캐스팅 금형은 인성, 고온 강도 및 열 피로 저항성 측면에서 최고의 요구 사항을 충족해야 합니다. 전통적으로 사용되는 1.2343 (AISI H 11), 1.2344 (Η 13) 또는 1.2367과 같은 열간 공구강은 이러한 요구 사항을 충족하지 못하는 경우가 많습니다. Kind & Co.는 TQ 1, HP 1, HTR이라는 세 가지 특수 열간 공구강을 개발하여 특성을 크게 개선했습니다.
본 보고서는 이러한 강재의 특성에 대한 개요뿐만 아니라 이들 등급으로 얻은 실제 경험에 대해서도 다룰 것입니다. 적절한 열처리는 금형의 성능에 필수적입니다. Kind & Co는 최근 세계에서 가장 크고 현대적인 진공 경화로 중 하나를 설치했으며, 이는 이러한 대형 다이캐스팅 금형에 중점을 둡니다. 본 보고서는 또한 현대적인 열처리 설비가 고급 구조 부품의 경제적인 다이캐스팅 공정에 기여하는 바를 보여줄 것입니다.
3. 서론:
국제 자동차 산업은 승용차의 CO2 배출을 대폭 제한하는 정치적 결정에 직면해 있으며, 유럽 연합은 자동차 산업에 대해 공격적인 목표(예: 130 g CO2/km 의무 감축 목표)를 설정했습니다. 경량화는 이러한 목표를 달성하기 위한 핵심 전략으로, 연비와 CO2 배출에 직접적인 영향을 미칩니다. 결과적으로 자동차 제조업체는 기존 강철 부품을 대체하는 다이캐스팅 알루미늄 구조 부품의 사용을 점점 더 늘리고 있습니다.
아우디는 이러한 접근 방식의 선구자였으며, 특히 AUDI A8(FIG. 1)에서 두드러졌고, 이러한 부품은 이제 도어 프레임(FIG. 2) 및 해치백 지지 프레임(FIG. 3)과 같은 응용 분야에서 흔히 볼 수 있습니다. 이러한 부품은 종종 큰 치수와 복잡한 디자인이 특징이며, 이는 다이캐스팅 공정과 금형 자체에 상당한 과제를 제기합니다. 금형은 긴 용탕 유동 경로를 처리해야 하며, 잠재적으로 더 높은 용탕 온도가 필요할 수 있어 국부적인 높은 열 부하와 열적 불균일성을 초래합니다. 리브와 같은 특징을 가진 복잡한 형상은 응력 집중을 유발하여 총 균열(gross cracking)의 위험을 증가시킬 수 있습니다.
따라서 금형 설계, 공구강 선택, 금형 제조 및 열처리는 신중하게 고려되어야 하며, 관련된 모든 당사자 간의 조기 협력이 필요합니다.
4. 연구 요약:
연구 주제의 배경:
연비 향상 및 CO2 배출량 감소를 위한 자동차 경량화 요구 증가는 크고 복잡한 다이캐스팅 알루미늄 구조 부품의 광범위한 채택으로 이어졌습니다.
이전 연구 현황:
이러한 대형 구조 부품 생산에 필요한 금형은 높은 열 부하, 온도 불균일성으로 인한 상당한 열 응력, 복잡한 형상으로 인한 높은 기계적 응력 등 극한 조건에 직면합니다. 1.2343 (H11), 1.2344 (H13), 1.2367과 같은 전통적인 열간 공구강은 이러한 까다로운 조건 하에서 인성, 고온 강도 및 열 피로(히트 체킹) 저항성 측면에서 종종 성능 한계에 도달합니다. 이러한 강재는 적절한 품질을 위해 ESR(Electro-Slag-Remelting) 공법으로 생산되어야 합니다.
연구 목적:
본 연구는 Kind & Co.에서 대형 구조 부품 다이캐스팅의 과제를 해결하기 위해 특별히 개발한 세 가지 특수 열간 공구강(TQ 1, HP 1, HTR)을 제시하는 것을 목표로 합니다. 표준 등급과 비교하여 개선된 특성을 상세히 설명하고 실제 경험을 논의합니다. 또한, 특히 대형 금형 인서트의 경우 최적의 금형 성능을 달성하는 데 있어 고급 열처리 공정 및 설비의 중요한 역할을 강조합니다.
핵심 연구:
연구의 핵심은 세 가지 특수 ESR 열간 공구강인 TQ 1, HP 1, HTR(화학 성분은 TAB. 1 참조)의 소개 및 특성 분석을 포함합니다. TQ 1은 높은 인성과 높은 고온 강도를 결합하도록 설계되었습니다. HP 1은 약간 수정된 조성으로 TQ 1의 경제적인 대안 역할을 합니다. HTR은 극한의 고온 강도와 열전도율을 위해 다르게 합금되었습니다(Cr 감소, W 추가). 본 연구는 이러한 특수강의 주요 기계적 특성을 표준 등급 1.2343, 1.2344, 1.2367과 비교합니다:
- 템퍼링 저항성 (FIG. 4)
- 고온 강도 (0.2% 항복 강도) (FIG. 5)
- 인성 (ISO-V 노치 충격 에너지) (FIG. 6)
- 히트 체킹 저항성 (실험실 시뮬레이션) (FIG. 7)
- 열전도율 (TAB. 3)
본 연구는 또한 적절한 열처리(권장 파라미터는 TAB. 2 참조)의 필요성을 강조하며, 경화, 템퍼링 및 완전한 마르텐사이트 변태를 달성하고 인성을 극대화하기 위해 충분한 퀜칭 속도를 달성하는 것의 중요성을 NADCA, Ford, GM 사양을 참조하여 논의합니다. 매우 큰 금형 인서트(예시는 FIG. 9, FIG. 10 참조)를 처리하고 높은 퀜칭 속도(FIG. 11)를 달성할 수 있는 새로운 대규모 진공 경화로(Ipsen Turbo Treater ST6672, FIG. 8)를 소개합니다. 열처리의 효과는 미세 구조 분석(FIG. 12)을 통해 입증됩니다. 대형 블록에 대한 적절한 단조 기술(3차원 단조)의 중요성도 언급됩니다.
5. 연구 방법론
연구 설계:
본 연구는 까다로운 다이캐스팅 응용 분야에 맞춰진 새로운 열간 공구강 조성(TQ 1, HP 1, HTR)의 개발을 포함했습니다. 비교 분석 방법론을 사용하여 이러한 새로운 등급의 특성을 기존 표준 강재(1.2343, 1.2344, 1.2367)와 비교 평가했습니다. 본 연구는 재료 과학 원리를 강재 생산(ESR, TQ 1/HP 1을 위한 특수 용해), 단조 기술(3차원 단조), 최첨단 열처리 기술을 포함한 실제 제조 고려 사항과 통합합니다.
데이터 수집 및 분석 방법:
재료 특성은 표준화된 시험 절차를 사용하여 정량화되었습니다:
- 화학 성분 분석 (결과는 TAB. 1).
- 다양한 온도에서 템퍼링 후 경도 측정(HRC)을 통해 템퍼링 곡선 생성 (FIG. 4).
- 고온 강도의 척도로서 0.2% 항복 강도(Rp0.2)를 결정하기 위한 고온 인장 시험 (FIG. 5).
- 45 HRC로 경화된 단조 바(약 320mm 직경)의 중심에서 횡방향으로 채취한 ISO-V 노치 시편을 사용한 충격 인성 시험 (FIG. 6).
- 600°C까지 가열 후 수냉하는 4,000 사이클을 포함하는 열 피로(히트 체킹) 실험실 시뮬레이션 및 후속 균열 평가 (FIG. 7).
- 경화 및 템퍼링된 시편(45 HRC)에서 다양한 온도(100°C, 400°C, 600°C)에서의 열전도율(λ) 측정 (TAB. 3).
- 연화 어닐링된 시편과 진공 열처리된 시편 모두에 대한 광학 현미경을 사용한 미세 구조 특성 분석 (FIG. 12). 결정립 크기는 Snyder-Graff 번호를 사용하여 평가되었습니다.
- 새로운 진공로의 퀜칭 압력 및 냉각 속도 능력을 산업 표준(NADCA #207-2008, Ford AMTD-DC2010, GM DC-9999-1)과 비교하여 성능 검증 (FIG. 11).
연구 주제 및 범위:
본 연구는 자동차 구조 부품용 대형 금형에 사용되는 열간 공구강에 구체적으로 초점을 맞췄습니다. 범위는 다음을 포함했습니다:
- 특수 강종(TQ 1, HP 1, HTR)의 개발 및 특성 분석.
- 주요 성능 특성의 비교 평가: 템퍼링 저항성, 고온 강도, 인성, 히트 체킹 저항성 및 열전도율.
- 강재 생산 방법(ESR, 청정도) 및 단조 기술(3차원 단조)이 재료 특성에 미치는 영향 조사.
- 오스테나이트화, 퀜칭 속도, 템퍼링 및 대형 금형 인서트(최대 5톤 이상) 처리에 필요한 능력을 포함한 진공 열처리의 중요한 역할 및 요구 사항 강조.
6. 주요 결과:
주요 결과:
- 표준 열간 공구강(1.2343, 1.2344, 1.2367)은 크고 복잡한 구조 부품 금형에 사용될 때 인성, 고온 강도 또는 열 피로 저항성에서 종종 한계를 보입니다.
- Kind & Co.는 최적화된 특성을 가진 세 가지 특수 ESR 열간 공구강을 개발했습니다:
- TQ 1: 높은 인성(1.2343 대비 약 25% 초과, FIG. 6)과 1.2367에 필적하는 높은 템퍼링 저항성/고온 강도(FIG. 4, FIG. 5)의 뛰어난 조합을 제공합니다. 표준 등급보다 개선된 히트 체킹 저항성을 보입니다(FIG. 7). 초청정 용해 공정이 필요합니다.
- HP 1: TQ 1과 유사한 높은 인성 및 히트 체킹 저항성 이점(FIG. 6, FIG. 7)을 제공하지만 약간 낮은 템퍼링 저항성 및 고온 강도를 가지며 보다 경제적인 대안 역할을 합니다. 또한 초청정 용해 공정이 필요합니다.
- HTR: 다른 합금 개념(W 합금, 낮은 Cr)을 특징으로 하며, 논의된 등급 중 가장 높은 고온 강도, 템퍼링 저항성 및 열전도율을 나타냅니다(FIG. 4, FIG. 5, TAB. 3). 최고의 히트 체킹 저항성을 제공하지만(FIG. 7) TQ 1 및 HP 1에 비해 인성이 낮습니다(FIG. 6). 극한의 열 부하에 노출되는 특정 인서트에 권장되며, 일반적으로 최대 43 HRC로 경화됩니다.
- ESR(Electro-Slag-Remelting)은 요구되는 균질성, 청정도 및 인성을 위해 필수적입니다. TQ 1 및 HP 1은 유해 미량 원소의 초저 농도를 위해 특수 야금 공정을 활용합니다.
- 대형 금형 블록에는 균일한 소성 변형을 보장하고 기계적 특성, 특히 인성을 향상시키기 위해 3차원 단조가 권장됩니다.
- 적절한 진공 열처리가 중요합니다. 퀜칭 중 높은 냉각 속도(NADCA, Ford, GM 최소 요구 사항 초과, 예: >28-30 °C/min)를 달성하는 것은 유해한 탄화물 석출을 억제하고 최적의 인성을 위한 미세한 마르텐사이트 미세 구조를 얻는 데 필수적입니다(FIG. 12).
- 높은 퀜칭 압력(예: 15 bar N2)과 용량(예: 5,500 kg 하중, 대형 챔버)을 갖춘 크고 강력한 진공 경화로(예: Ipsen Turbo Treater ST6672, FIG. 8)는 대형 금형 인서트(FIG. 9, FIG. 10)를 성공적으로 경화하고 부품 전체에 걸쳐 필요한 냉각 속도를 달성하는 데 필요합니다(FIG. 11).
- 대형 금형의 경우 목표 경도를 낮추면(예: 44-46 HRC 대신 40-42 HRC) 인성을 증가시켜 금형 수명에 유리할 수 있습니다.
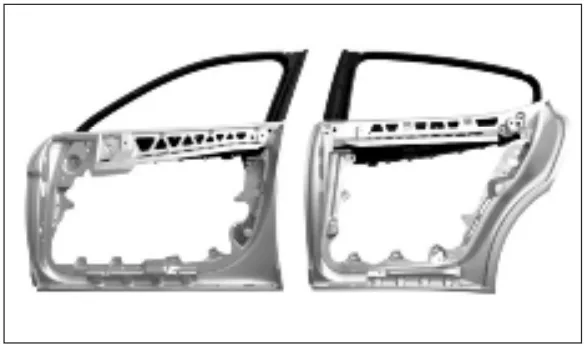
Telai di portiere e finestrini di un’automobile sportiva tedesca (Photo: Georg Fischer AG).
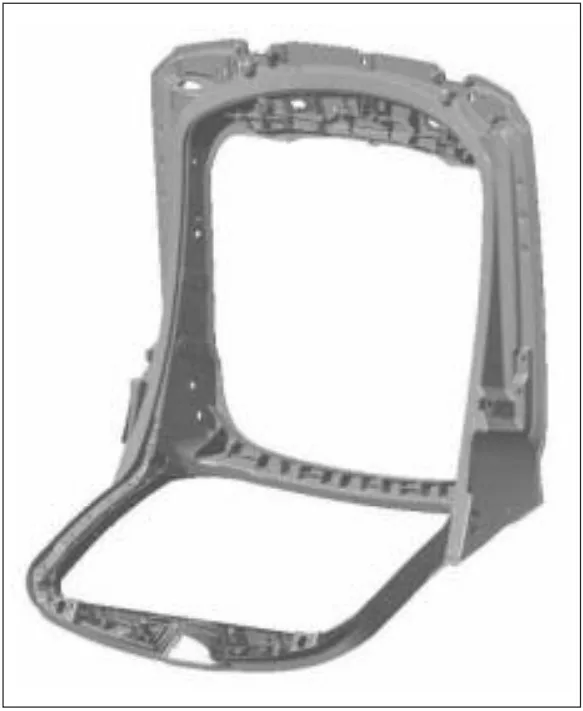
Telaio di supporto di un portellone posteriore pressocolato.
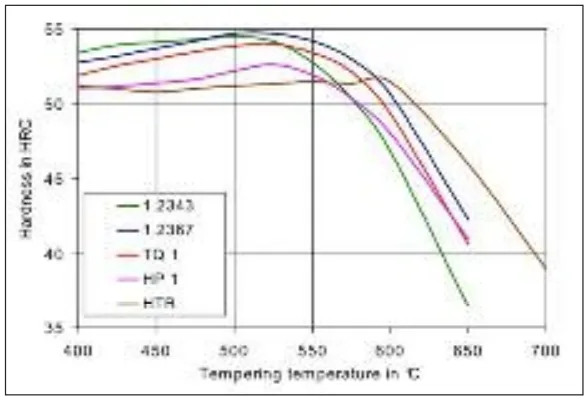
Diagramma di rinvenimento di acciai standard e acciai speciali da utensili per lavorazione a caldo per stampi da pressocolata.
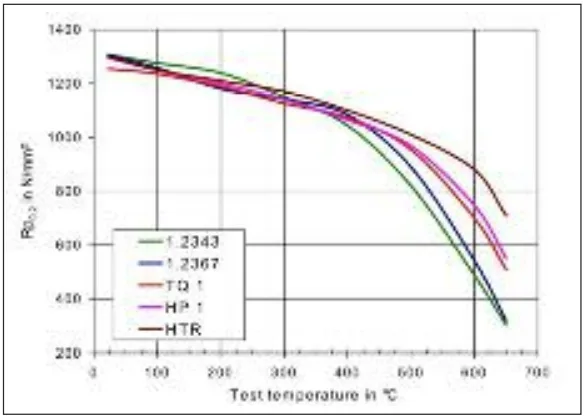
Resistenza meccanica alle temperature elevate di acciai standard e acciai speciali da utensili per lavorazione a caldo per stampi di pressocolata.
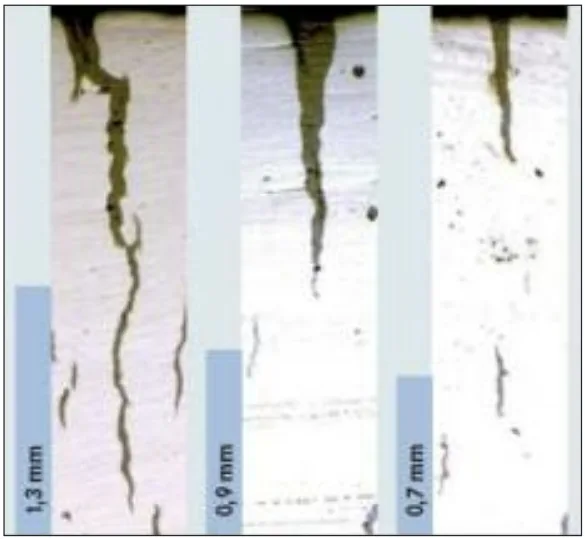
Aspetto delle cricche superficiali da fatica termica dopo 4.000 cicli a 600 °C / acqua - a): acciaio 1.2343; b): steel HP 1; c): acciaio HTR.
그림 및 표 목록:
- FIG. 1 AUDI A 8 차체의 주조 알루미늄 구조 부품(빨간색) [4].
- FIG. 2 독일 스포츠카의 도어 및 윈도우 프레임 (사진: Georg Fischer AG).
- FIG. 3 다이캐스팅 해치백 지지 프레임 (사진: BMW AG).
- FIG. 4 다이캐스팅 금형용 표준 및 특수 열간 공구강의 템퍼링 곡선.
- FIG. 5 다이캐스팅 금형용 표준 및 특수 열간 공구강의 고온 강도.
- FIG. 6 다이캐스팅 금형용 열간 공구강의 인성 (ISO-V 노치 시편, 횡방향, 단조 바 중심, 약 320mm 직경, 45 HRC).
- FIG. 7 4,000 사이클 600 °C / 수냉 후 히트 체킹 균열 외관 - a): 강재 1.2343; b): 강재 HP 1; c): 강재 HTR.
- FIG. 8 Kind & Co.의 새로운 진공 경화로 Ipsen Turbo Treater ST6672.
- FIG. 9 승용차 도어용 금형 인서트, 3,820 kg.
- FIG. 10 해치백 지지 프레임용 금형 인서트, 1,350 mm x 1,720 mm x 440 mm, 5,440 kg.
- FIG. 11 요구 사항과 비교한 로(furnace)의 특성.
- FIG. 12 USN ESR (1.2343 ESR)로 제작된 다이캐스팅 금형 인서트의 미세 구조, 3820 kg. a: 연화 어닐링된 미세 구조; b: 새로운 경화로에서 진공 열처리 후 미세 구조.
- TAB. 1 다이캐스팅 금형용 열간 공구강의 화학 성분.
- TAB. 2 다이캐스팅 금형용 열간 공구강의 권장 경화 파라미터.
- TAB. 3 열간 공구강의 열전도율 λ (W / (m * K)).
7. 결론:
다이캐스팅 알루미늄 구조 부품의 사용은 자동차 경량화, 연비 감소 및 CO2 배출량 저감에 중요한 기여를 합니다. 그러나 이러한 부품은 종종 가용성 및 생산성의 한계에 가까운 크고 복잡한 금형 인서트를 필요로 합니다. 특정 형상은 종종 불균일한 온도 분포와 높은 열 응력을 유발하여 1.2343 및 1.2344와 같은 표준 열간 공구강의 적용 가능성에 도전합니다. TQ 1, HP 1, HTR과 같이 특별히 개발된 ESR 열간 공구강은 개선된 고온 강도, 템퍼링 저항성, 인성 및 히트 체킹 저항성을 포함한 최적화된 특성을 제공합니다. 현저히 개선된 고온 특성 및 열전도율을 가지지만 인성이 낮은 HTR은 일반적으로 43 HRC 미만으로 사용되며 극한의 열 부하를 받는 부분 인서트에 가장 적합합니다. 이러한 강재, 특히 대형 치수에서의 성공적인 적용은 고급 열처리에 결정적으로 달려 있습니다. 새로운 진공 경화로(IPSEN Super Turbo ST6672)는 매우 큰 금형 인서트(5톤 이상)를 경화하는 데 필요한 용량과 높은 퀜칭 능력을 제공하여 바람직하지 않은 탄화물 석출을 억제하고 미세한 마르텐사이트 미세 구조를 달성합니다. 이는 대형 금형에서도 우수한 인성 값을 보장합니다. 현대적인 맞춤형 열간 공구강과 최첨단 열처리 설비의 조합은 복잡하고 고급스러운 구조 부품의 성공적이고 경제적인 다이캐스팅을 위한 최적의 기반을 제공합니다.
8. 참고 문헌:
- [1] Decision No 1753/2000/EC of the European Parliament and of the Council of 22 June 2000 establishing a scheme to monitor the average specific emissions of CO2 from new passenger cars. www.europa.eu
- [2] Communication from the Commission to the Council of the European Parliament - A community strategy to reduce CO2 emissions from passenger cars and improve fuel economy. www.europa.eu
- [3] Communication from the Commission to the Council and the European Parliament - 6 Results of the review of the Community Strategy to reduce CO2 emissions from passenger cars and light commercial vehicles. www.europa.eu
- [4] G. BRANNER and P. WANKE: The Role of High Pressure Die Casting in the AUDI Lightweight Strategy, Proc. International Forum on Structural Components by HPDC, Vicenza, September 2011, AIM
- [5] NADCA DIE MATERIALS COMMITTEE: Special Quality Die Steel & Heat Treatment Acceptance Criteria for Die Casting Dies. NADCA #207-2008, North American Die Casting Association (2008)
- [6] FORD MOTOR COMPANY: Die Insert Material and Heat Treatment Performance Requirements, General Applications. Specification No. AMTD-DC2010, Rev. L (1999)
- [7] GM POWERTRAIN GROUP: Standard Specification. Die Insert Material and Heat Treating Specification. Specification No. DC-9999-1, Rev. 18 (2005)
- [8] H. BERNS, E. HABERLING, and F. WENDL: Influence of the Annealed Microstructure on the Toughness of Hot-work Tool Steels. Thyssen Edelst. Techn. Ber., Special Issue 1990, pp. 45 – 52
- [9] H. BERNS: Die Bedeutung der t10/7-Zeit für die Wärmebehandlung hochlegierter Stähle. HTM J. Heat Treatm. Mat. 65 (2010) 4, pp. 182 – 188
9. 저작권:
- 본 자료는 "I. Schruff"의 논문입니다. "[The tool steel producer's contribution to successful die casting of structural components]"를 기반으로 합니다.
- 논문 출처: La Metallurgia Italiana - n. 9/2012, pp. 37-43
본 자료는 상기 논문을 바탕으로 요약되었으며, 상업적 목적의 무단 사용을 금합니다.
Copyright © 2025 CASTMAN. All rights reserved.