본 페이지는 Transactions of KSAE, Vol. 20, No. 4, pp.52-59 (2012)에 게재된 연구 논문 "고진공 다이캐스팅 공법 적용한 알루미늄 서브프레임 개발"을 요약합니다. 본 논문은 기존의 스틸 서브프레임 대비 무게를 줄이고 성능을 향상시키기 위해 고진공 다이캐스팅 공법을 사용하여 알루미늄 서브프레임을 개발하는 과정을 상세히 기술합니다.
1. 개요:
- 제목: 고진공 다이캐스팅 공법 적용한 알루미늄 서브프레임 개발 (Front Aluminum Subframe of High Level Vacuum Die-casting)
- 저자: 조영건, 임태성, 장상길, 조철환 (Younggun Cho, Taeseong Lim, Sang-gil Jang, Cheol-hwan Cho)
- 발행년도: 2012년
- 발행 학술지/학회: 한국자동차공학회 논문집 (Transactions of the Korean Society of Automotive Engineers, KSAE)
- 키워드: 고진공 다이캐스팅 (High level vacuum die-casting), 알루미늄 서브프레임 (Aluminum subframe), 리브 (Rib), 음향 수준 (Sound level), 롤 로드 (Roll rod)

2. 연구 배경:
- 연구 주제의 사회적/학문적 맥락:
- 유가 상승 및 탄소 배출 규제 강화로 인한 차량 경량화를 통한 연비 향상 요구 증대.
- 자동차 설계에서 경량 소재의 중요성 증가.
- 알루미늄은 높은 비강도와 다양한 성형 공정 가능성으로 엔진 부품뿐 아니라 서스펜션과 같은 구조 부품에 대한 적용이 확대되는 추세.
- 특히 대형차를 중심으로 알루미늄 서브프레임 적용이 세계적으로 확대되는 추세.
- 기존 연구의 한계:
- 기존 서브프레임은 주로 스탬핑된 강철 소재로 제조되어 무거움.
- 일반적인 알루미늄 다이캐스팅은 비용 효율적이지만, 제품 내 가스 함유량(10~30cc/100gAl)이 높아 기계적 물성이 낮고 열처리 및 용접이 어려워 고강도 구조 부품에 적용하기 어려움.
- 연구의 필요성:
- 연비 향상 요구를 충족하기 위한 경량 알루미늄 서브프레임 개발 필요.
- 기존 다이캐스팅의 한계를 극복하고 가스 함유량을 최소화하여 구조적 응용에 적합한 물성을 확보할 수 있는 고진공 다이캐스팅 공법 적용의 필요성.
- 공정 최적화를 통해 재료비 상승 효과를 최소화하면서 스틸 서브프레임 대비 무게를 절감하는 것을 목표로 함.
3. 연구 목적 및 연구 질문:
- 연구 목적:
- 고진공 다이캐스팅 기술을 적용한 알루미늄 전륜 서브프레임 개발.
- 스틸 서브프레임 대비 무게 절감 및 동등 이상의 구조 성능 확보.
- 재료 변경에 따른 비용 증가를 최소화하기 위한 설계 및 제조 공정 최적화.
- 주요 연구 질문:
- 고진공 다이캐스팅 공법이 가스 함유량을 줄이고 물성을 향상시켜 알루미늄 서브프레임 생산에 효과적인가?
- 고진공 다이캐스팅으로 제조된 알루미늄 서브프레임은 스틸 서브프레임 대비 얼마나 무게를 절감할 수 있는가?
- 개발된 알루미늄 서브프레임의 마운팅 강성, 소음 및 진동 (NVH), 내구 성능과 같은 구조 성능은 스틸 서브프레임과 비교하여 어떠한가?
- 알루미늄 서브프레임의 리브 설계가 NVH 성능과 구조적 무결성에 어떤 영향을 미치는가?
- 연구 가설:
- 고진공 다이캐스팅은 기존 다이캐스팅 방식보다 가스 함유량이 적고 기계적 물성이 우수한 알루미늄 서브프레임을 생산할 수 있을 것이다.
- 알루미늄 서브프레임은 스틸 서브프레임 대비 상당한 무게 절감을 달성할 것이다.
- 최적화된 리브 설계를 통해 알루미늄 서브프레임은 강성과 NVH 성능이 향상되어 스틸 서브프레임과 동등하거나 더 나은 성능을 보일 것이다.
4. 연구 방법론:
- 연구 설계:
- 개발 및 비교 연구.
- 고진공 다이캐스팅 공법을 이용한 알루미늄 서브프레임 설계 및 제조.
- 알루미늄 서브프레임의 물성 및 성능을 스틸 서브프레임과 비교 평가.
- 자료 수집 방법:
- 재료 물성 시험: 고진공 다이캐스팅으로 생산된 알루미늄 합금의 기계적 물성 시험 (인장 강도, 항복 강도, 연신율). 알루미늄 합금의 화학 성분 분석.
- X-Ray 검사: 제조된 알루미늄 서브프레임의 기공 및 주조 품질 평가를 위한 X-Ray 검사.
- NVH 평가: 진동 및 소음 특성 평가를 위한 모달 분석 및 부밍 시험. 알루미늄 서브프레임이 장착된 차량의 음향 감도 측정.
- 내구 및 강도 시험: 다양한 하중 조건 (전후, 좌우, 상하) 하에서의 내구 시험. 정적 하중 하에서의 구조적 무결성 평가를 위한 강도 시험.
- 강성 분석: 롤 로드 마운팅 강성 측정.
- 분석 방법:
- 비교 분석: 알루미늄 서브프레임과 스틸 서브프레임의 재료 물성, 무게, 강성, NVH 성능 및 내구성을 비교 분석.
- 유한 요소 해석 (FEA): HyperWorks Pre 및 Radioss Solver 툴을 사용하여 다양한 리브 설계에 따른 NVH 성능을 모의 실험하기 위한 모달 분석.
- 통계 분석: 재료 물성 시험 결과의 평균값 계산 및 X-Ray 검사 등급 분석.
- 연구 대상 및 범위:
- 재료: 고진공 다이캐스팅으로 생산된 알루미늄 합금 (Silafont 36) 및 서브프레임용 스탬핑 강판.
- 부품: 자동차용 전륜 서브프레임.
- 제조 공정: 알루미늄 서브프레임의 고진공 다이캐스팅.
- 성능 평가: 마운팅 강성, NVH (소음, 진동), 내구성 및 강도.
5. 주요 연구 결과:
- 주요 연구 결과:
- 중량 절감: 알루미늄 서브프레임은 스틸 서브프레임 대비 4kg의 중량 절감을 달성함.
- 재료 물성: 고진공 다이캐스팅은 고급 알루미늄 합금과 견줄만한 기계적 물성을 가진 알루미늄을 생산함. 표 1은 스틸과 비교한 Silafont 36 알루미늄 합금의 기계적 물성을 보여줌:
- Silafont 36: 탄성 계수 71 GPa, 연신율 4.1%, 항복 강도 162 MPa, 인장 강도 247 MPa.
- 스틸: 탄성 계수 206 GPa, 연신율 32%, 항복 강도 343 MPa, 인장 강도 465 MPa.
- NVH 성능 향상: NVH 평가 결과 알루미늄 서브프레임 적용 시 140Hz (약 4,200rpm 엔진 속도) 대역에서 소음 수준이 8dB 감소함. 모달 분석 결과, 비틀림 모드를 제외하고 알루미늄 서브프레임의 주요 모드 주파수가 스틸 대비 증가함.
- 강성: 롤 로드 마운팅 강성이 알루미늄 서브프레임에서 향상되었으며, 특히 전후 방향 강성이 크게 증가함 (스틸 6,920 kgf/mm에서 알루미늄 8,405 kgf/mm로 증가). 알루미늄 서브프레임의 롤 로드 마운팅 수직 강성은 1,108 kgf/mm로 측정됨.
- 내구 및 강도: 알루미늄 서브프레임은 다양한 하중 조건 하에서 내구 시험을 성공적으로 통과했으며, 파손 (파단 또는 좌굴) 없이 강도 요구 사항을 충족함.
- 주조 품질: X-Ray 검사 결과 기공 수준이 대부분 3등급 이하 (일부 두꺼운 부분 제외)로 나타나 우수한 주조 품질을 보였으며, 이는 국제 자동차 부품 표준과 동등하거나 더 나은 수준임 (기공 수준 목표 < 4cc/100g, 달성 수준 ~2cc/100g).
- 통계적/정성적 분석 결과:
- 표 3은 다양한 리브 설계 (Rib A, Rib B, Rib C)에 대한 롤 로드 마운팅 강성을 보여줌. Rib C가 수직 강성 (Z 방향)에서 1,108 kgf/mm로 가장 높은 강성을 나타냄.
- 표 4는 스틸 및 알루미늄 서브프레임의 글로벌 모드 주파수를 나타냄. 알루미늄 서브프레임은 스틸 대비 굽힘 및 횡 굽힘 모드에서 더 높은 주파수를 보임.
- 표 6과 그림 8은 X-Ray 검사 결과를 보여주며, 기공이 대부분 3등급 이내로 허용 가능한 주조 품질임을 나타냄.
- 표 7은 주조된 알루미늄 합금의 측정된 재료 물성을 요약하며, 평균 항복 강도 235 MPa, 인장 강도 265 MPa, 연신율 5.6%를 나타냄.
- 그림 9는 알루미늄 및 스틸 서브프레임의 주파수 응답 함수를 비교하는 모달 시험 결과를 보여줌.
- 그림 10은 전방 좌석에서의 부밍 시험 결과를 보여주며, 알루미늄 서브프레임으로 NVH 성능이 향상되었음을 나타냄.
- 그림 12는 강도 시험 결과를 보여주며, 알루미늄 서브프레임의 구조적 무결성을 확인함.
- 자료 해석:
- 고진공 다이캐스팅 공법을 사용하여 구조적 및 NVH 성능이 향상된 경량 알루미늄 서브프레임 생산이 가능함.
- 최적화된 리브 설계 (Rib C)는 특히 수직 방향으로 강성 향상에 기여함.
- 알루미늄 서브프레임은 내구성과 강도 요구 사항을 충족하면서 상당한 무게 절감 및 NVH 성능 향상을 달성함.
- 고진공 다이캐스팅을 통해 달성된 주조 품질은 자동차 부품의 높은 기준에 부합함.
- 그림 목록:
- Fig. 1 고진공 다이캐스팅 (High level vacuum die-casting)
- Fig. 2 서브프레임 형상 (상면도) (Subframe shape (top view))
- Fig. 3 서브프레임 형상 (저면도) (Subframe shap (bottom view))
- Fig. 4 노멀 모드 해석 결과 (Results of normal mode analysis)
- Fig. 5 강도 해석 결과 (Results of strength analysis)
- Fig. 6 고진공 다이캐스팅 금형 구조 (Mold structure of high level vacuum die-casting)
- Fig. 7 제작된 서브프레임 사진 (Pography of manufactured subframe)
- Fig. 8 X-Ray 검사 (X-ray testing)
- Fig. 9 알루미늄 및 스틸 서브프레임의 모달 시험 (Modal testing of aluminium and steel subframe)
- Fig. 10 전방 좌석 부밍 시험 (Booming testing at front seat)
- Fig. 11 시험 설비 (Testing facilities)
- Fig. 12 강도 시험 결과 (Strength test results)

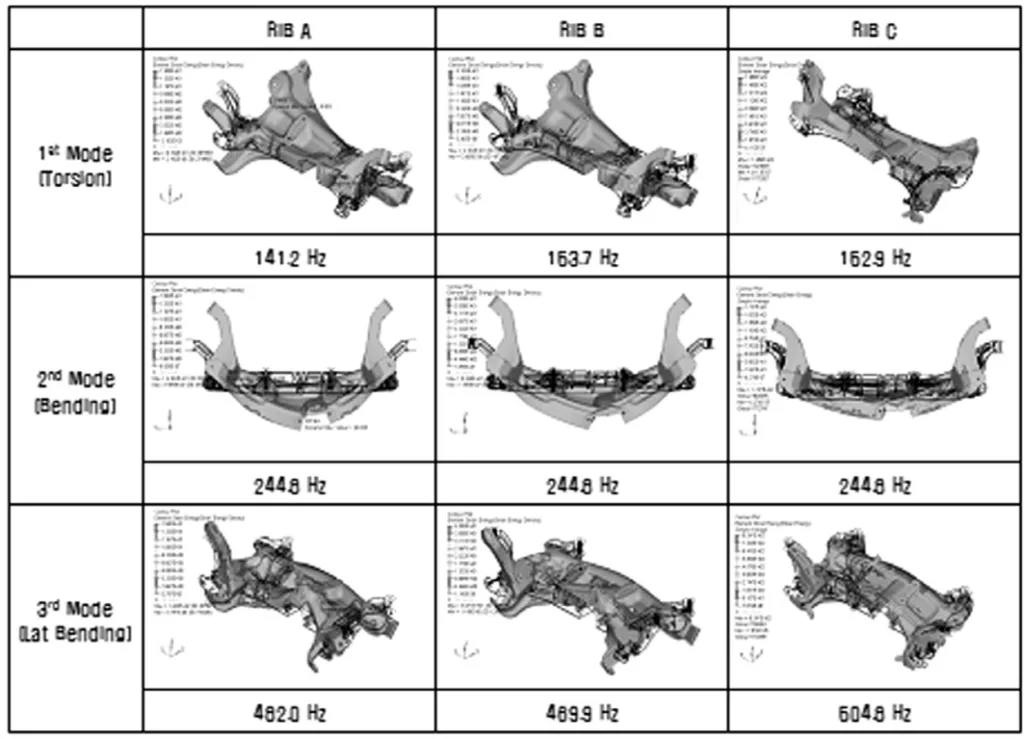
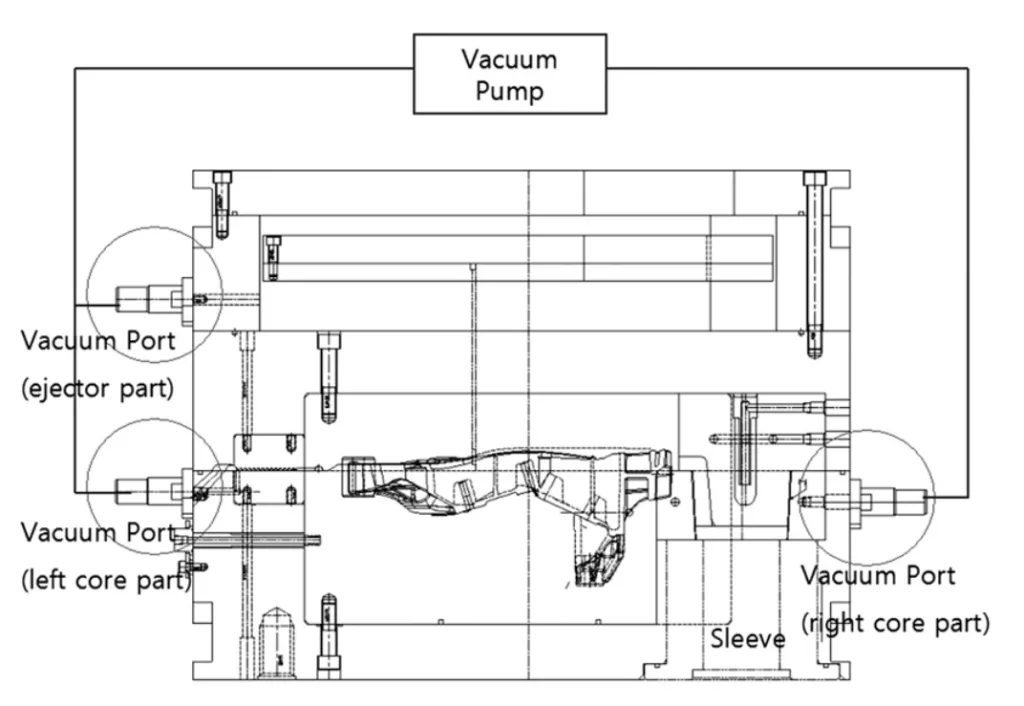
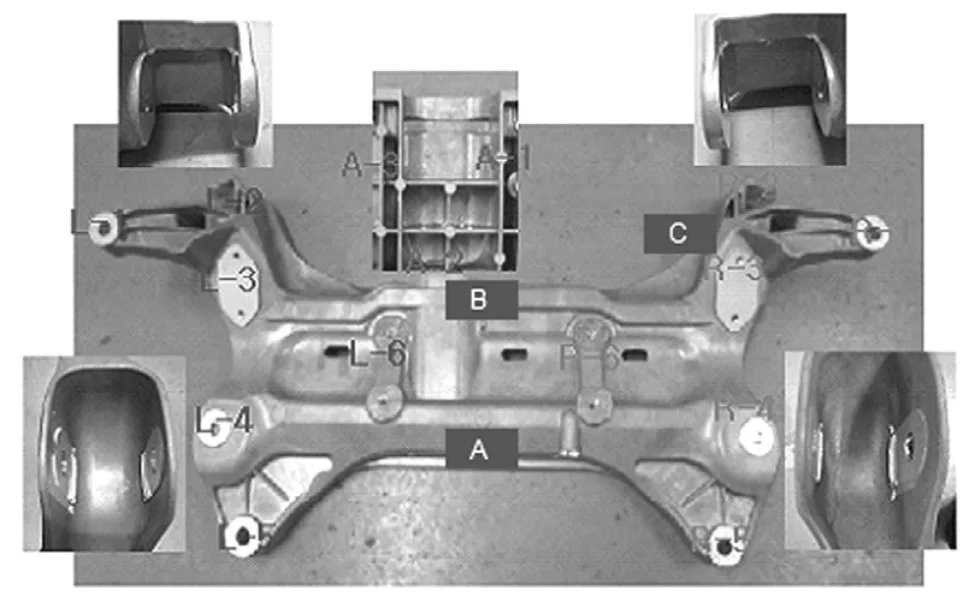
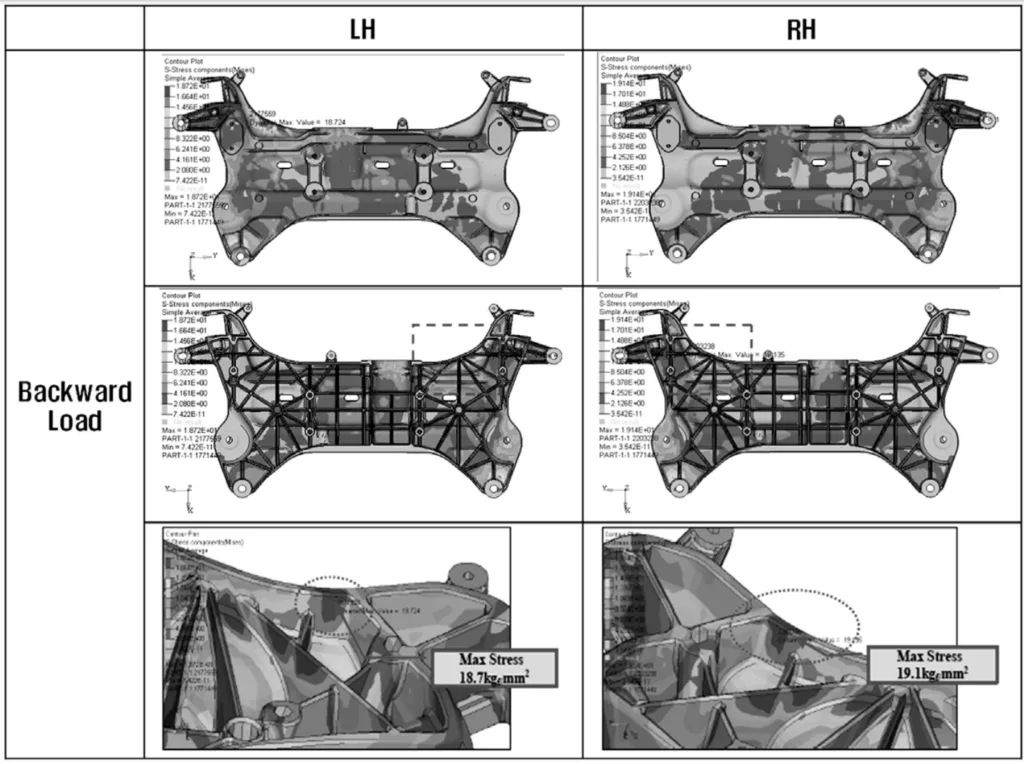
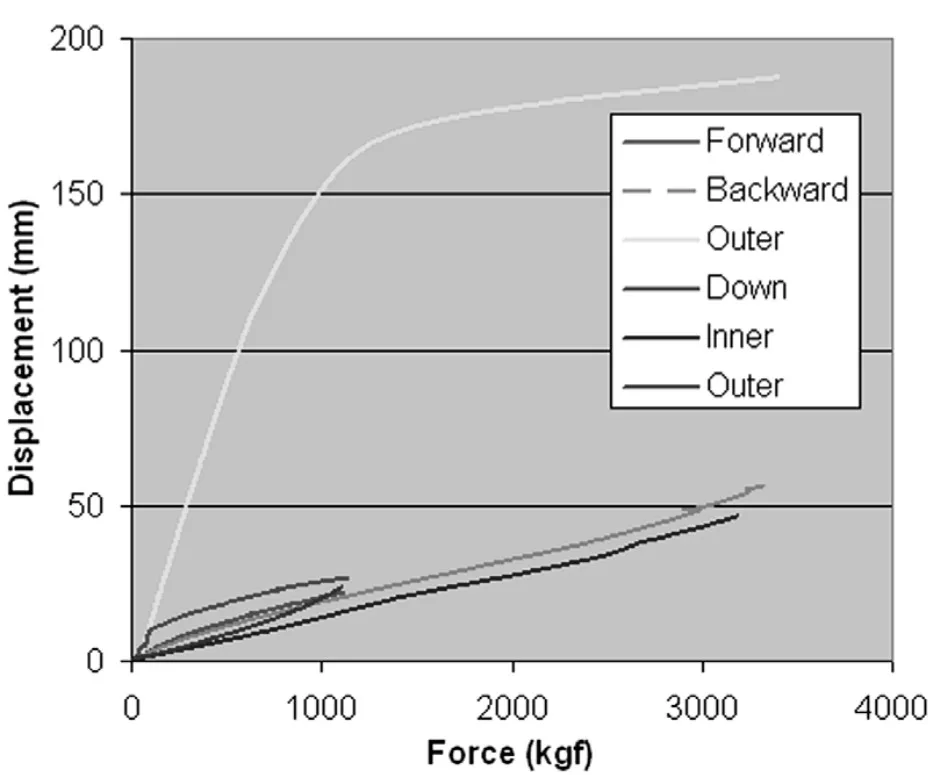
6. 결론 및 논의:
- 주요 결과 요약:
- 중량 절감 효과가 큰 고진공 다이캐스팅 공법을 국내 최초로 적용하여 차량 중요 안전 부품 중 하나인 전륜 서브프레임을 알루미늄 소재로 개발함.
- 스틸 사양의 서브프레임 대비 4kg의 중량 절감 효과를 달성하여 차량 연비 개선 및 이산화탄소 절감에 기여함.
- 서브프레임 하단의 리브 구조 형상을 벌집 구조의 형상으로 최적 개발하여 1,108kgf/mm 수준 이상 수준의 롤 로드 마운팅부 상하 강성을 확보함. 또한 스틸 사양 서브프레임과 동등 이상의 글로벌 강성을 확보함. 그 결과 완성차량에서의 음향 감도 평가하여, 140Hz 대역에서 8dB 개선됨을 검증함.
- 시제품에 대한 기포 결함 수준은 2cc/100g 이하 수준으로 해외 경쟁차 수준 대비 크게 향상되었으며, 내구 및 정강도 시험 기준을 만족함을 확인하였다.
- 연구의 학문적 의의:
- 대형 구조 자동차 부품인 서브프레임 제조에 고진공 다이캐스팅 공법의 성공적인 적용을 입증함.
- 이 첨단 주조 방식으로 생산된 알루미늄 서브프레임의 재료 물성, 구조 성능 및 NVH 특성에 대한 귀중한 데이터를 제공함.
- 자동차 공학 분야의 경량화 전략에 대한 지식 기반을 확장함.
- 연구의 실용적 의미:
- 자동차 제조업체가 알루미늄 서브프레임 구현을 통해 차량 무게를 줄이고 연비를 향상시킬 수 있는 실행 가능한 솔루션을 제공함.
- 고진공 다이캐스팅은 품질과 성능이 향상된 복잡한 알루미늄 구조 부품의 대량 생산에 적용될 수 있음.
- 개발된 알루미늄 서브프레임 설계 및 제조 공정은 차량 생산에 직접 적용될 수 있음.
- 연구의 한계:
- 본 연구는 특정 전륜 서브프레임 설계 및 알루미늄 합금 (Silafont 36)에 초점을 맞춤.
- 실험실 시험 외에 실제 주행 조건에서의 장기 내구성 및 성능은 광범위하게 평가되지 않음.
- 스틸 서브프레임 제조와 비교하여 고진공 다이캐스팅을 사용한 대량 생산의 비용 효율성은 본 논문에서 명시적으로 자세히 분석되지 않음.
7. 향후 후속 연구:
- 후속 연구 방향:
- 성능 향상 및 무게 절감을 위한 알루미늄 서브프레임 설계 및 리브 구조의 추가 최적화.
- 잠재적으로 향상된 기계적 물성 또는 비용 효율성을 가진 고진공 다이캐스팅에 적합한 다른 알루미늄 합금 탐색.
- 알루미늄 서브프레임의 포괄적인 장기 내구성 시험 및 실제 차량 성능 평가.
- 고진공 다이캐스팅을 사용한 알루미늄 서브프레임 대량 생산을 위한 상세한 비용 분석 및 공정 최적화.
- 차량 조립 시 알루미늄 서브프레임의 접합 기술 연구.
- 추가 탐구가 필요한 영역:
- 기공을 더욱 최소화하고 주조 품질 일관성을 향상시키기 위한 주조 매개 변수 개선.
- 알루미늄 서브프레임의 피로 성능 및 충돌 안전성에 대한 상세 분석.
- 스틸 서브프레임과 비교한 알루미늄 서브프레임 생산 및 수명 주기의 환경 영향 평가.
8. 참고 문헌:
- 1) D. Triantos and M. Michaels, "Design and Fabrication of an Aluminum Engine Crandle for a General Motors Vehicle," SAE 1999-01-0659, 1999.
- 2) A. Mikuni, O. Itagaki and M. Suzuki, “Development of Aluminum Vacuum Die CastSub-frame," JSAE Autumn Conference, JSAE, 20045658, 2004.
- 3) T. Gakamoto, K. Kira and H. Kambe, “Development of Automotive Suspension Part by High Vacuum Die Casting," Journal of Japan Foundry Engineering Society, Vol.76, No.4, pp.283-288, 2004.
- 4) M. Tashiro, K. Kudoh, Y. Konno and K. Takagi, "Development of Nissan Innovative Casting System for Aluminum Casting Suspension Parts," Nissan Technical Review, No.49, 2001.
- 5) A. Mikuni, O. Itagaki and M. Suzuki, “Development of Aluminum Vacuum Die Cast Sub-frame," JSAE Annual Congress, JSAE, No.81-04, 2004.
- 6) G.-M. Yoon, D.-H. Kang, Y.-J. Ko and J.-D. Lim, "Application of High Level Vacuum Die-casting for the Automotive Parts,” Annual Conference Proceedings, KSAE, pp.1540-1546, 2009.
- 7) S.-Y. Park, D.-C. Park, K.-S. Yoon and M.-S. Lee, "A Study of Front Subframe System Optimization for Improving Vehicle NVH Performance," SAE 2009-01-2097, 2009.
- 8) M.-S. Kim, T.-S. Li, K.-M. Yoon, Y.-J. Ko, J.-M. Kim and K.-H. Kwak, “Development of Cast-forged Knuckle Using High Strength Aluminum Alloy,” Spring Conference Proceedings, KSAE, pp.1048-1055, 2010.
9. 저작권:
- 본 자료는 조영건, 임태성, 장상길, 조철환 님의 논문: 고진공 다이캐스팅 공법 적용한 알루미늄 서브프레임 개발을 기반으로 작성되었습니다.
- 논문 출처: DOI http://dx.doi.org/10.7467/KSAE.2012.20.4.052
본 자료는 상기 논문을 요약한 것으로, 상업적 목적의 무단 사용을 금지합니다.
Copyright © 2025 CASTMAN. All rights reserved.